Сейчас ваша корзина пуста!
Исследование неравномерности износа рельсов по длине звена
Цикл статей:
Введение
Глава 1 – Анализ процессов в зоне фрикционного контакта колеса с рельсом
Глава 2 – Методика экспериментальных наблюдений и обработка данных
Глава 3 – Основные результаты наблюдений
Глава 4 – Исследование неравномерности износа рельсов по длине звена
Глава 5 – О влиянии соотношения твердости бандажной рельсовой сталей на интенсивность изнашивания рельсов
Глава 6 – Влияние нагруженности локомотивов на интенсивность износа рельсов
Регрессионные зависимости износа рельсов от наработки тоннажа и радиуса кривой на подъеме четного пути
Износ рельсов по длине звена носит неравномерный характер. На неравномерность износа рельсов обращали внимание исследователи и раньше, например, [76]. Л.П. Мелентьев [77] считает, что при наличии начальных неровностей на рельсе будет резко проявляться влияние жесткости подрельсового основания, тогда как для рельсов правильного очертания жесткость подрельсового основания влияет слабо. Для изучения особенностей этого явления проведены измерения вертикального и бокового износа в 49 точках звена. Обследовано 202 звена: 117 на подъеме и 85 на спуске четного пути. Большинство рельсов имело износ, близкий к допускаемому или превышающий его по правилам технической эксплуатации.
На рис. 4.8 показаны графики изменения бокового износа в кривой радиуса 300 м (через 1 м), показывающие, что по длине звена имеется несколько локальных максимумов бокового износа. Зарождение мест повышенного износа происходит в первые месяцы эксплуатации. Расположение максимумов износа по длине звена может быть обусловлено характером динамического воздействия подвижного состава на путь и неправильностью очертания рельса, вызванного либо непрямолинейностью рельса при прокате, либо отступлением рельса в плане от радиальной кривой. Этот вопрос требует детальной проработки. Но величина максимумов износа на принимающем и отдающем концах рельса зависит от угла в стыке.
Для уменьшения влияния угла в стыке на износ рельсов Кармазиным А.И. предлагается применять предварительно изогнутые рельсы [78].
Основное значение имеет главный максимумом по длине рельса, в большинстве случаев являющийся общим для вертикального и бокового износа. Его амплитуда почти в 2 раза больше остальных локальных максимумов. Анализ обследованных звеньев показал следующее: 4% звеньев не имеют четко выраженного максимума; 11,8% звеньев имеют главный максимум ближе к середине или отдающему концу рельса; 84,2% звеньев максимально изношены на принимающем конце.
Значения износа по длине рельса
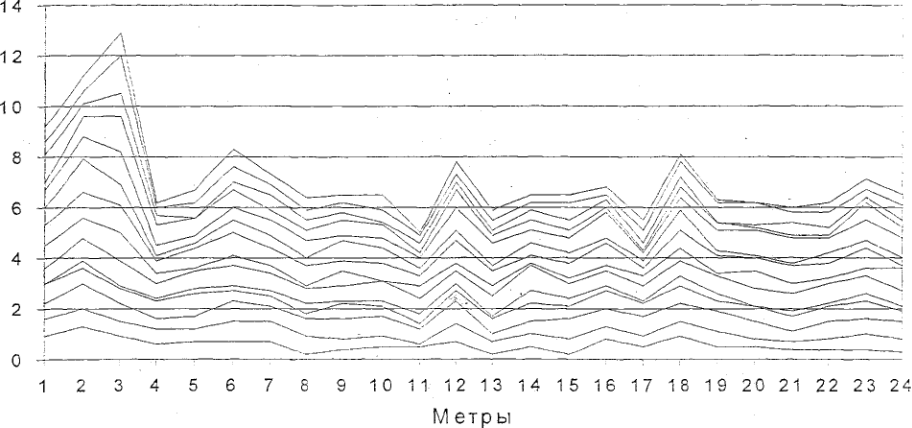
Отметим, что замеры износа рельсов по методике, описанный в главе 3, происходили в фиксированных точках, не совпадающих, как правило, с максимумом износа.
Возникают две задачи в связи с вышесказанным. Во-первых, т.к. замена рельсов назначается по максимальному износу на звене, то необходим переход от прогнозируемого по регрессионным зависимостям износа к максимальному. Во-вторых, для анализа интенсивности износа рельсов на сети дорог желательно производить замеры по единой методике. Учитывая трудоёмкость замеров, необходимо определить минимально необходимое число точек на звене, замеры износа в которых с заданной вероятностью характеризовали бы среднюю величину износа на звене и его максимальное значение.
Первая задача решалась следующим образом.
Для определения реальных сроков службы рельсов нами исследовано превышение максимального износа на звене по сравнению со средним по измерению в трех фиксированных ранее точках. В этом случае по каждому звену вычислены поправочные коэффициенты К:
К = ^ (4.13)
- к
- где /гтах – максимальное измеренное на данном звене значение износа;
- ¡г – среднее из трех значений износа, измеренных на данном звене в фиксированных точках.
Коэффициенты вычислены отдельно для вертикального, бокового и приведенного износа.
На рис. 4.9 приведены гистограммы распределения полученных коэффициентов отдельно на подъеме и на спуске, величина т – количество звеньев с поправочным коэффициентом, попавшим в интервал.
Поправочные коэффициенты
Средневзвешенные значения коэффициентов указаны в таблице 4.12. Эти значения коэффициентов использованы для определения тоннажа, после пропуска которого необходимо назначить сплошную смену рельсов.
Таблица 4.12 Участок | Поправочный коэффициент к износу, рассчитанному по регрессионному уравнению | ||
К | К | Кр | |
Подъем | 1,5 | 1,6 | 1,5 |
Спуск | 1,3 | 1,6 | 1,4 |
В ходе исследования были построены гистограммы распределения поправочных коэффициентов для различных интервалов радиусов кривых.
Однако предельные значения коэффициентов, определяющие максимальный износ на значительной части звеньев, совпали со значениями, указанными в табл. 4.12.
По временной методике, предложенной нами и утвержденной управлением ВСЖД для анализа интенсивности износа рельсов и определения эффективности рельсосмазывания износ рельсов в дистанциях пути измерялся в 16 точках звена. Для уменьшения затрат времени на замеры износа поставлена задача определения минимально необходимого количества точек на звене, по износу рельсов в которых можно было бы с вероятностью не ниже 0,9 вычислить величину среднего значения износа на звене, а при помощи эмпирических коэффициентов определить величину максимального износа.
Износ рельсов, как уже было сказано, имеет значительный разброс (рис.4.10)
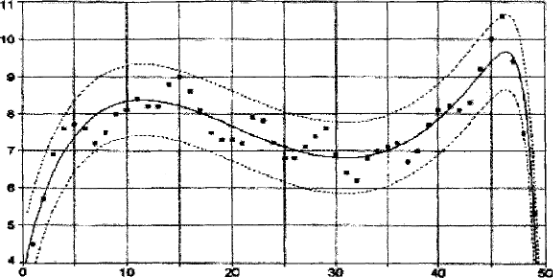
Главной задачей было отыскание точек, в которых следует измерять износ рельсов. Были найдены номера шпал, на каждом звене, в которых находятся величины отличные от математического ожидания на 10%. После анализа построили график частоты попадания значений М+10%,М-10% на каждую точку (рис.4.12).
Проанализировав построенный график, выделили точки, в которых частота попадания максимальная, и нашли частоту попадания математического ожидания в эти точки.
Анализ различных вариантов подсчета среднего значения бокового износа показал, что с вероятностью не менее 0.9 достаточно измерять износ в пяти-шести точках звена. Выбранные точки должны иметь частоты, близкие к максимальным, и среднее значение износа в этих точках должно дать значение математического ожидания. Сравнение истинного математического ожидания и среднего из пяти точек показало правильность этого вывода. Соответствие между ними в среднем составляет 93%. В этих пяти точках и следует измерять износ, а именно в точках 9, 10, И, 16, 19 (рис. 4.13) [79].
Далее были найдены максимальные значения износа и отличие этих значений от среднего значения износа. Коэффициент приведения среднего износа к максимальному составляет 1,44.
Подобным образом могут быть уточнены значения коэффициентов перехода от средних значений к максимальному для различных условий эксплуатации. Следует ожидать, что по причине различных схем формирования поездов, режимов вождения, осевых нагрузок, тормозных режимов будут и различия в коэффициентах.
Полученные зависимости износа рельсов по длине звена представляют собой траектории движения колёсных пар подвижного состава и дают возможность исследовать характер динамического воздействия подвижного состава на путь в зависимости от скорости движения и расчётной модели.
Сравнительный график средних найденных в 5 точках, в 49 точках и мах значений
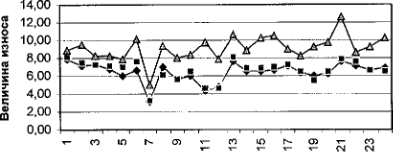
Рис.4.13
Вероятность нахождения математического ожидания в одной из этих пяти точек составило 0,877.
При этом необходимо иметь в виду, что предложенная аппроксимация износа по длине звена не описывает имеющиеся локальные максимумы, т.е. более короткие неровности, которые могут быть заданы той или иной функцией и наложены на основную кривую износа.
Определение периодичности сплошной смены рельсов наружной нити в кривых
Если в аналитическую зависимость износа от различных факторов подставить предельно допустимое по правилам технической эксплуатации значение износа [Ь], то значение пропущенного тоннажа, соответствующее данной величине износа, будет являться нормативом на период между сплошными сменами рельсов. Учитывая, что максимальный износ на звеньях в к раз больше (табл. 4.12), чем определённый по полученным зависимостям, выражение для предельного износа принимает вид.
Исследование 1984-87, 1994-97 годов показали, что изменения в грузовой работе и по воздействию подвижного состава на путь могут изменить интенсивность изнашивания рельсов в несколько раз. В связи с этим целесообразно показать как разнятся нормативы на сплошную смену рельсов на затяжных спусках и подъёмах, тогда как рекомендация на нормативы имеет смысл при устоявшихся и мало изменяющихся условиях эксплуатации пути.
Необходимость введения дифференцированных нормативов обсуждалась в [80]. На рисунке 4.14 показано отношение нормативного до сплошной смены рельсов тоннажа на подъёме к соответствующей величине на спуске в условиях применения рекуперативного торможения.
Отношение нормативного тонажа на подъеме Тнп к соответствующей величине на спускеТнс
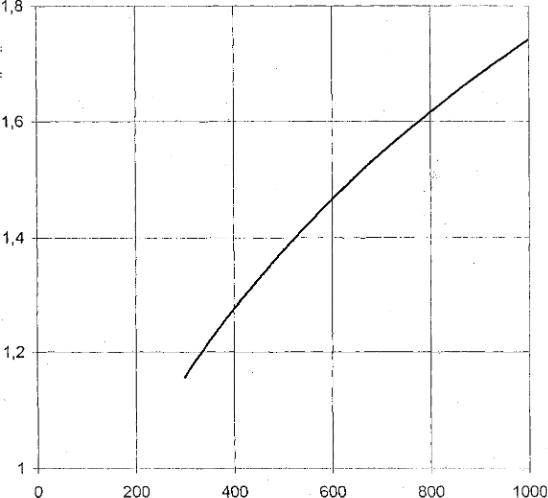
Влияние возвышения наружного рельса в кривых участках пути на износ рельсов
Вошедшая в [81] формула определения возвышения наружного рельса в кривых , где V – средневзвешенная скорость, км/ч., ^-радиус кривой, м., получена из условия равенства вертикальных давлений, а следовательно, вертикального износа рельсов, лежащих на наружной и внутренних нитях.
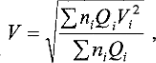
Средневзвешенная скорость должна определяться по формуле
История вопроса изложена в [82]. Там же приведены эмпирические формулы определения возвышения наружной нити, предложенные в различных странах. Необходимо отметить, что эти формулы дают результаты, значительно отличающиеся друг от друга.
Попытка определить возвышение с позицией обеспечения равенства суммарного (вертикального и бокового) износа рельсов наружной и внутренней нитей не увенчалось успехом, т.к. в этом случае пришлось бы увеличить возвышение более чем в два раза по сравнению с расчетом по формуле (4.18). Кроме экономического критерия определения возвышения (по формуле 4.18) существуют [82] критерий обеспечения комфорта для пассажиров в скорых поездах и критерий обеспечения прочности и устойчивости пути и безопасности движения скорых поездов. По второму критерию поперечное ускорение, возникающее при движении экипажа в кривой, не должно превосходить допускаемой величины:
По критерию обеспечения прочности и устойчивости пути и безопасности движения скорых поездов необходимо, чтобы:
- максимальное напряжение в наружной кромке наружного рельса не превышало допускаемого значения,
- центробежная сила не превышала допускаемого значения,
- степень разгрузки внутреннего колеса не должна превышать 30% статического вертикального давления на ось,
- отношение бокового давления наружного направляющего колеса к статическому вертикальному давлению должно быть не более единицы,
- коэффициент устойчивости экипажа в кривой должен быть не меньше заданного числа и меньше единицы.
Поперечное ускорение ат складывается из непогашенного ускорения и добавочных ускорений, зависящих от наличия горизонтальных неровностей (а ) и виляния экипажа (авил).
Ускорением, возникающим при вилянии экипажа, в кривых участка* пути обычно пренебрегают.
Ускорение, возникающее от неровности пути, может достигать значительной величины: (0,25-4- 0,5)м/с2 для пассажирских вагонов (0,5^-0,75) м/с для грузовых полувагонов [82]. По предложению М.Ф. Ве- риго адо6 может быть принято равным 0,18 м/с , которое возникает даже при хорошем ходе экипажа.
Наибольший интерес у практических работников пути вызываем возможность уменьшить боковой износ наружной нити установлением из быточного по сравнению с расчетным возвышения наружной нити.
Анализ эксплуатационных данных о работе пути привел авторов ра боты [83] к выводу, что интенсивность бокового износа рельсов очень ела бо связана с величиной возвышения наружного рельса (стр.179). Указыва ется, что “боковой износ наружного рельса, помимо грузонапряженности плана и профиля пути, существенным образом зависит от рода и режим; движения поездов”.
Аналогичный вывод содержится в[84], где констатируется, что изно’ рельсов внутренней и наружной нитей не является прямой функцией воз вышения наружной нити.
В работе [64] отмечается, что увеличение возвышения наружного рельса приводит к уменьшению направляющих сил, но увеличивается уго. набегания колес на рельсы. Поэтому увеличение возвышения на 20 ми приводит к снижению бокового износа всего на 3-5%.
Такой же вывод в работах [85, 86]. В ряде исследований указываете на желательность установления избыточного возвышения, что позволи выравнять интенсивности износа рельсов наружной и внутренней ните: [87,65].
X. Балух [57] считает, что рационально принятое возвышение дол» но обеспечивать возможно более равномерное распределение нагрузок н обе рельсовые нити, что достигается вычислением возвышения по средне взвешенной скорости.
В основу более точного расчета возвышения наружной нити положен учет влияния силы тяги и сопротивления движению поезда, эксцентриситетов расположения колесных пар в колее из-за наличия зазоров между гребнями колес и рельсами, силы ветра [47].
Были предложены и иные критерии установления возвышения наружного рельса. Так, Г.И. Хархута [88] предложил рассчитывать возвышение наружного рельса по грузонапряженности.
В последние годы предпринята попытка определения возвышения наружного рельса, минимизирующего время хода поездопотока по кривой [89].
В работе С.М. Андриевского [17] обращается внимание на то, что увеличение возвышения наружного рельса при неизменной скорости движения, уменьшая боковое давление направляющих колес подвижного состава, несколько увеличивает углы их набегания на наружный рельс кривой и соответственно увеличивает скольжение гребней колес или выкружек гребней по скруглению рельсовой головки, в результате чего интенсивность бокового износа рельсов изменяется незначительно. Следовательно, увеличение возвышения не может быть эффективным средством для ликвидации или существенного уменьшения интенсивности бокового износа рельсов.
Несоответствие между возвышением наружного рельса и скоростью движения в кривых приводит к снижению коэффициента сцепления со многими последствиями. Это обстоятельство имеет наиболее существенное значение и на него указывается в книге Л.А. Мугинштейна и А.Л. Лисицына [6].
Определение оптимального возвышения наружного рельса и возможное повышение скоростей движения пассажирских и грузовых поездов рассматривается в статье Н.И. Карпущенко и А.Н. Шлейнинга [90].
Рациональный диапазон значений непогашенных ускорений грузовых поездов с точки зрения устранения несоответствия скоростей возвышению и снижение интенсивности бокового износа рельсов в кривых дан в работах [91, 92]. Для устранения перекосного положения тележек, уменьшения углов набегания колесных пар на рельсы необходимо, чтобы непогашенное ускорение находилось в диапазоне от 0 до +0,1 м/с . Рациональный диапазон значений непогашенных ускорений грузовых поездов должен быть от +0,3м/с2 до -0,3м/с2.
Исследование влияния возвышения упорной нити в кривых на износ рельсов на перевальном участке ВСЖД
Попытка включить в расчет возвышение наружного рельса в качестве четвертого независимого фактора, в дополнение к исследованным выше, дала отрицательный результат. Причина этого в том, что радиус кривой и юзвышение зависят друг от друга, а включение зависимых факторов в »асчет по методу Брандона недопустимо.
Поэтому, учитывая, что между радиусом кривизны и возвышением тюрной нити в кривой существует обратная пропорция, вместо двух факторов в модель включен один.
Оценки точности регрессионных уравнений Участок | Виды | Среднее откло | Средняя от | Корреляци |
износа | нение расчетных | носительная | онное отно | |
значений от | ошибка ап | шение | ||
фактических,мм | проксимации | |||
Подъем | Вертикальный | 0,143 | 0,416 | 0,930 |
Боковой | 0,178 | 0,442 | 0,926 | |
Приведенный | 0,048 | 0,238 | 0,956 | |
Спуск | Вертикальный | 0,015 | 0,127 | 0,912 |
Боковой | 0,068 | 0,296 | 0,730 | |
Приведенный | 0,024 | 0,173 | 0,862 |
Отметим, что ошибка данной аппроксимации несколько больше, чем в предыдущих. Кроме того, значительно изменились показатели степени при уклоне пути. Следовательно, хотя в целом уравнения правильно описывают динамику износа, но о влиянии уклона пути по ним судить уже нельзя.
Учитывая, что натурные съемки уклона к кривых проведены по рабочей грани упорной нити, величины уклона и возвышения также могут быть зависимы друг от друга.
Действительный характер связи между радиусом, возвышением и уклоном по указанным причинам должен быть другим и требует отдельного исследования.
Для качественной оценки влияния возвышения наружной нити на износ рассчитаем по полученным регрессионными зависимостями относительное уменьшение износа при увеличении возвышения на 5 мм.
Расчет сведен в табл. 4.14
Относительное уменьшение износа в процентах при увеличении возвышения на 5мм
Возвышение наружного рельса | Расчетная величина АИ % по участкам и видам износа | |||||
Подъем | Спуск | |||||
Вер- тик. | Боковой | Привед. | Вертик. | Боковой | Привед. | |
40 | 1,4 | 20,4 | 10,2 | 5,1 | 8.9 | 6,8 |
60 | 0,9 | 14,4 | 7,1 | 3,5 | 6,2 | 4,7 |
80 | 0,7 | 11Д | 5,4 | 2,7 | 4,7 | 3,6 |
100 | 0,6 | 9,0 | 4,4 | 2,2 | 3,8 | 2,9 |
120 | 0,5 | 7,6 | 3,7 | 1,8 | 3,2 | 2,4 |
140 | 0,4 | 6,6 | 3,2 | 1,6 | 2,8 | 2,1 |
На подъеме вертикальный износ практически не зависит от возвышения. Боковой износ наиболее существенно зависит от положения рельсовых нитей по уровню. Расчеты показывают, что только в кривых большого радиуса на подъеме увеличение возвышения наружного рельса на 1012% приводит к уменьшению бокового износа на 15-20%. В кривых малого радиуса (< 350 м) на подъемах и на спусках увеличение возвышения против расчетного из условия равной загруженности вертикальными силами рельсов внутренней и наружной нитей не приводит к заметному уменьшению бокового износа рельсов, но влечёт за собой увеличение выхода рельсов нижней нити по вертикальному износу и дефектам контактно- усталостного происхождения.
Следовательно, увеличение возвышения наружной нити в кривых не может являться действенным средством уменьшения бокового износа рельсов [61]. Аналогичный вывод сделал Л.П.Мелентьев [93].
Влияние смазки на износ рельсов и бандажей колесных пар
Смазка трущихся поверхностей является основным способом уменьшения интенсивности их износа. Этому вопросу посвящена обширная литература.
В классической работе Д. Мура даны теоретические основы смазки, виды смазочных материалов и сферы применения смазки.
В работе О.П. Ершкова [82], опубликованной в 1959 г., приводятся следующие данные: лубрикация рельсов уменьшает сопротивление движению на 50%, срок службы рельсов увеличивается в 1,5-2 раза; количество сменяемых по износу гребня бандажей уменьшается в 4-5 раз.
Наличие абразивного материала (главным образом кварцевого песка, подаваемого в зону контакта колеса с рельсом из песочниц локомотивов для увеличения сцепления колес тягового подвижного состава с рельсами) существенно снижает антифрикционные действия смазок и вызывает сомнения у работников железных дорог в необходимом нанесении смазок одновременно с применением песка.
Остановимся на нескольких работах, посвященных этому вопросу [94-98].
Абразивность твердых частиц характеризует их способность разрушать поверхностный слой трущихся тел [97]. Кварцевые песчаники отнесены к пятому классу, т.е. абразивность выше средней (по шкале оценок
Ямпольский Г .Я. и Крагельский И.В. [94] утверждают, что абразивная частица может производить деформации микрорезания и пластического передеформирования металла. Преобладание того или иного вида деформации зависит от соотношения твердости абразивной частицы, металла, давлении в контакте, вида смазочного материала. Величина износа зависит, кроме того, от концентрации абразивных частиц б”0‘667. Если внешние давления в контакте вызывают дробление частиц, то износ металла от нагрузки слабо завиеитуг.к. внедрение абразивных частиц в металл конечно и определяется их механической прочностью при дроблении. Поэтому любая большая нагрузка, чем приводящая к дроблению, уже не может увеличить глубину внедрения и пропорциональный ей износ.
Существенным для анализа износа рельсов и бандажей колесных пар является вывод [94] , что для смазанных поверхностей микрорезание возможно при 0,3 < с < 0,4 ,а для несмазанных поверхностей микрорезание возможно при 0,1 < с < 0,7 (с — к/Я, где: к – глубина внедрения, Я – объемный радиус частицы). Это означает, что вероятность микрорезания на смазанной поверхности уменьшается в шесть раз.
Другой важный вывод состоит в том, что скольжение увеличивает абразивный износ.
В [99] на основании опыта смазки на американских железных дорогах приводятся следующие данные: эффект лубрикации, выраженный отношением удельного износа рельсов с лубрикацией к удельному износу рельсов без лубрикации изменялся в пределах от 1: 8 до 1: 34,8 для кривых различной протяженности и находящихся на различном расстоянии от лубрикатора. При этом один лубрикатор может обслуживать до 1500 м кривой.
Применение лубрикации на Северной железной дороге [100] в кривой радиуса 920 м на рельсах Р43 уменьшило интенсивность бокового износа рельсов в три раза. Эффект от одного рельсосмазывателя конструкции
П.И. Васильева прослеживался на расстоянии нескольких километров. В качестве смазки применялся солидол.
В докладе Калусек Дж. На семинаре Американской железнодорожной ассоциации [101] сообщалось, что скорость изнашивания ряда материалов при смазывании смазкой с песком снижается в среднем в 20 раз, а при смазывании чистой смазкой в 100-200 раз. При этом на конечных этапах развития контактной усталости образуются участки растрескивания поверхности на наружном рельсе или участки отслаивания на внутреннем рельсе. Также отмечалось, что смазка уменьшает силы, действующие на рельс и колесо в зоне контакта и уменьшает пластическое течение. Рекомендовано было не делать перерывов в смазывании рельсов.
Влияние избыточного количества смазки исследовали Питере Э.Дж., Роунд К.К. [102]. Боковые силы, действующие на наружный рельс, увеличиваются на 20-4-40 %, если на верхнюю и внутреннюю поверхности головки наружного рельса наносится избыток смазочного материала, а внутренний рельс остается несмазанным. В случае адекватного смазывания наружного рельса на кривых обеспечивается снижение скорости изнашивания внутренней поверхности головки рельса в 80 раз, а гребней колес в 20 раз. В этой работе делаются и другие важные выводы: благодаря смазыванию наружного рельса на кривых среднее сопротивление поезда уменьшается на 50 % на кривых при отсутствии уклона, но не влияет на составляющую сопротивления, обусловленную уклоном; благодаря смазыванию на горизонтальных прямых участках можно уменьшить сопротивление движению на 30 % ; загрязнение тормозных колодок смазкой не уменьшает коэффициент трения между колодками и поверхностью качения колеса, т.к. смазочный материал выгорает; смазочный материал на поверхности катания мешает ультразвуковой дефектоскопии рельсов.
В [103,104] обращается внимание на то, что наличие смазки на поверхности катания наружных рельсов в кривой приводит к увеличению поперечных сил от колеса ведущей оси локомотива в среднем на 40%, а при избыточной смазке более чем на 80%. Поперечные силы от ведомой оси были меньше по абсолютной величине, чем от ведущей, но их относительный рост был выше.
Реальные данные о продлении срока службы рельсов при смазке их боковой грани сообщается в [105] со ссылкой на американские источники: срок службы рельсов повышается в 1,5-2 раза, а количество сменяемых бандажей по износу гребней сократилось в 4-5 раз.
Результаты наблюдений за износом рельсов при применении смазки носят часто противоречивый характер. В статье [64] указывалось, что в
местах установки лубрикаторов износ рельсов не только не уменьшался, а зачастую даже увеличивался.
В [106-107] по результатам наблюдений в четырех кривых радиусом 300 м и при уклоне 15% на основании замеров бокового износа указывается на низкую эффективность жидкой смазки, подаваемой на рельс от путевого лубрикатора. Наблюдения показали, что на первых звеньях от рельсо- смазывателя износ уменьшился в 3 раза, а за пределами шестого-восьмого звеньев разницы в интенсивности рельсов со смазкой и без нее почти не было.
В работах Л.П. Мелентьева [23, 108-110] при применении смазки отмечалось уменьшение износа рельсов в 2-3 раза, а также снижение уровня боковых динамических сил, снижение сопротивления движению на 50 %.
В конечном итоге срок службы рельсов нельзя увеличить пропорционально уменьшению интенсивности их износа при применении смазки из-за зарождения и роста контактных усталостных трещин, образующих на поверхности сетку и приводящих к увеличению волнистой неровности поверхности катания [111]. Для ликвидации и предупреждения развития поверхностных усталостных трещин необходима переодическая шлифовка рельсов после пропуска приблизительно каждые 5 млн. т. брутто груза.
Преимущества смазки рельсов и гребней колес не исчерпывается уменьшением интенсивности износа. Смазка позволяет уменьшить сопротивление движению поезда в кривых и прямых участках пути и достичь существенной экономии топлива на перевозку груза (на 9-15 %), повысить скорости движения поездов. I – VIII класса).
Ямпольский Г .Я. и Крагельский И.В. [94] утверждают, что абразивная частица может производить деформации микрорезания и пластического передеформирования металла. Преобладание того или иного вида деформации зависит от соотношения твердости абразивной частицы, металла, давлении в контакте, вида смазочного материала. Величина износа зависит, кроме того, от концентрации абразивных частиц б”0‘667. Если внешние давления в контакте вызывают дробление частиц, то износ металла от нагрузки слабо завиеитуг.к. внедрение абразивных частиц в металл конечно и определяется их механической прочностью при дроблении. Поэтому любая большая нагрузка, чем приводящая к дроблению, уже не может увеличить глубину внедрения и пропорциональный ей износ.
Существенным для анализа износа рельсов и бандажей колесных пар является вывод [94] , что для смазанных поверхностей микрорезание возможно при 0,3 < с < 0,4 ,а для несмазанных поверхностей микрорезание возможно при 0,1 < с < 0,7 (с — к/Я, где: к – глубина внедрения, Я – объемный радиус частицы). Это означает, что вероятность микрорезания на смазанной поверхности уменьшается в шесть раз.
Другой важный вывод состоит в том, что скольжение увеличивает абразивный износ.
В [99] на основании опыта смазки на американских железных дорогах приводятся следующие данные: эффект лубрикации, выраженный отношением удельного износа рельсов с лубрикацией к удельному износу рельсов без лубрикации изменялся в пределах от 1: 8 до 1: 34,8 для кривых различной протяженности и находящихся на различном расстоянии от лубрикатора. При этом один лубрикатор может обслуживать до 1500 м кривой.
Применение лубрикации на Северной железной дороге [100] в кривой радиуса 920 м на рельсах Р43 уменьшило интенсивность бокового износа рельсов в три раза. Эффект от одного рельсосмазывателя конструкции П.И. Васильева прослеживался на расстоянии нескольких километров. В качестве смазки применялся солидол.
В докладе Калусек Дж. На семинаре Американской железнодорожной ассоциации [101] сообщалось, что скорость изнашивания ряда материалов при смазывании смазкой с песком снижается в среднем в 20 раз, а при смазывании чистой смазкой в 100-200 раз. При этом на конечных этапах развития контактной усталости образуются участки растрескивания поверхности на наружном рельсе или участки отслаивания на внутреннем рельсе. Также отмечалось, что смазка уменьшает силы, действующие на рельс и колесо в зоне контакта и уменьшает пластическое течение. Рекомендовано было не делать перерывов в смазывании рельсов.
Влияние избыточного количества смазки исследовали Питере Э.Дж., Роунд К.К. [102]. Боковые силы, действующие на наружный рельс, увеличиваются на 20-4-40 %, если на верхнюю и внутреннюю поверхности головки наружного рельса наносится избыток смазочного материала, а внутренний рельс остается несмазанным. В случае адекватного смазывания наружного рельса на кривых обеспечивается снижение скорости изнашивания внутренней поверхности головки рельса в 80 раз, а гребней колес в 20 раз. В этой работе делаются и другие важные выводы: благодаря смазыванию наружного рельса на кривых среднее сопротивление поезда уменьшается на 50 % на кривых при отсутствии уклона, но не влияет на составляющую сопротивления, обусловленную уклоном; благодаря смазыванию на горизонтальных прямых участках можно уменьшить сопротивление движению на 30 % ; загрязнение тормозных колодок смазкой не уменьшает коэффициент трения между колодками и поверхностью качения колеса, т.к. смазочный материал выгорает; смазочный материал на поверхности катания мешает ультразвуковой дефектоскопии рельсов.
В [103,104] обращается внимание на то, что наличие смазки на поверхности катания наружных рельсов в кривой приводит к увеличению поперечных сил от колеса ведущей оси локомотива в среднем на 40%, а при избыточной смазке более чем на 80%. Поперечные силы от ведомой оси были меньше по абсолютной величине, чем от ведущей, но их относительный рост был выше.
Реальные данные о продлении срока службы рельсов при смазке их боковой грани сообщается в [105] со ссылкой на американские источники: срок службы рельсов повышается в 1,5-2 раза, а количество сменяемых бандажей по износу гребней сократилось в 4-5 раз.
Результаты наблюдений за износом рельсов при применении смазки носят часто противоречивый характер. В статье [64] указывалось, что в местах установки лубрикаторов износ рельсов не только не уменьшался, а зачастую даже увеличивался.
В [106-107] по результатам наблюдений в четырех кривых радиусом 300 м и при уклоне 15% на основании замеров бокового износа указывается на низкую эффективность жидкой смазки, подаваемой на рельс от путевого лубрикатора. Наблюдения показали, что на первых звеньях от рельсо- смазывателя износ уменьшился в 3 раза, а за пределами шестого-восьмого звеньев разницы в интенсивности рельсов со смазкой и без нее почти не было.
В работах Л.П. Мелентьева [23, 108-110] при применении смазки отмечалось уменьшение износа рельсов в 2-3 раза, а также снижение уровня боковых динамических сил, снижение сопротивления движению на 50 %.
В конечном итоге срок службы рельсов нельзя увеличить пропорционально уменьшению интенсивности их износа при применении смазки из-за зарождения и роста контактных усталостных трещин, образующих на поверхности сетку и приводящих к увеличению волнистой неровности поверхности катания [111]. Для ликвидации и предупреждения развития поверхностных усталостных трещин необходима переодическая шлифовка рельсов после пропуска приблизительно каждые 5 млн. т. брутто груза.
Преимущества смазки рельсов и гребней колес не исчерпывается уменьшением интенсивности износа. Смазка позволяет уменьшить сопротивление движению поезда в кривых и прямых участках пути и достичь существенной экономии топлива на перевозку груза (на 9-15 %), повысить скорости движения поездов.
Исследование влияния смазки на износ рельсов на перевальном участке Восточно-Сибирской железной дороги
В 1996году нами исследовались смазки РС-6 на графитовой основе и опытная смазка РСМ производства Иркутского завода “Радиан”.
Испытания проведены в июле-августе по четному пути на подъеме с продольным уклоном пути 170/00 в кривой радиуса 301 м, на 5232 км. Четное направление является грузовым в отличие от нечетного пути, по которому пропускается значительное количество поездов с порожними вагонами.
Характеристика рельсов в опытных кривых отражена в таблице 4.15.
Твердость рельсовТип | Кило | Звено | Твердость | Номер плавки |
рельсов | метр | НВ, Мпа | ||
Р65 | 5232 | 4 | 3320 | ХФР2612 |
КМК | 5 | 3402 | ХФ621Г10 | |
6 | 3360 | ХФ621Г10 | ||
7 | 3541 | ХФ02612 | ||
8 | 3198 | ХФЕ2610 | ||
9 | 3384 | ХФ748С5 | ||
10 | 3453 | ХФЕ2610 | ||
11 | 3365 | ХФ2610Е1 | ||
12 | 3708 | ХФР2612 | ||
13 | 3218 | ХФЕ2610 | ||
14 | 3159 | ХФТ2609 | ||
15 | 3178 | ХФТ2609 | ||
16 | 3350 | ХФ622Е16 | ||
17 | 3364 | ХФ622Е22 |
На момент испытания смазки рельсы имели боковой износ до 13 мм. Звенья 4-10 не смазывались и служили в качестве контрольных. Смазывалась боковая поверхность наружного рельса кривой вручную на протяжении всей длины рельсов втиранием смазки плотным тампоном.
В начале и конце эксперимента боковой износ рельсов измерялся в восьми точках каждого звена (за 2,4,6,8,10,25,42,44 шпалами по ходу движения поездов) с точностью + 0,1 мм.
Была измерена твердость рельсов методом Бринелля вдавливанием шарика диаметром 10 мм усилием 29430 Н (3000 кгс) прибором ТШП-4 в трех точках каждого звена. В таблице 4.15 приведены средние значения твердости для каждого звена. Диаметры отпечатков измерялись микроскопом МПБ-3 с точностью + 0,1 мм. Прибор ТШП-4 градуировался на образцовых мерах твердости. Ошибка измерения твердости рельсов составляла (1-1,5) %.
Средняя твердость контрольных несмазываемых рельсов составила НВ 3379 МПа, а смазываемых – НВ 3334 МПа, т.е. была приблизительно одинакова, т.к. различие в твердости составило 1,3 % (в пределах точности измерений).Погодные условия были благоприятными для испытаний: стояла сухая, солнечная погода, дневные температуры превышали +25°С.
Результаты испытаний смазки РСМ-96
Консистентная смазка РСМ-96 испытывалась в июле 1996 г. Смазка наносилась три раза в сутки в период с 9 до 18 часов. В ночное время рельсы не смазывались, что снижало эффективность смазки.
Средние величины приращений бокового износа рельсов характеризовались смазывающими данными (таблица 4.16).
Таблица 4.16Звено | Среднее приращение бокового износа | Звено | Среднее приращение бокового износа, мм |
4 | 0,92 | 11 | 0,64 |
5 | 0,87 | 12 | 0,56 |
6 | 0,84 | 13 | 0,68 |
7 | 0,84 | 14 | 0,73 |
8 | 0,97 | 15 | 0,63 |
9 | 0,92 | 16 | 0,54 |
10 | 0,77 | 17 | 0,67 |
Средняя величина приращения бокового износа контрольных рельсов равнялась 0,88 мм, смазываемых – 0,64 мм. Смазка позволила уменьшить боковой износ рельсов □ на 28 %.
Смазке без длительных ночных перерывов уменьшение износа рельсов можно прогнозировать минимум на 40 % по сравнению с износом несмазываемых рельсов.
Смазка РСМ хорошо разносится колесами подвижного состава. Наличие смазки РСМ наблюдалась на расстоянии нескольких сот метров по ходу поезда, т.е. смазка разносится на расстоянии, в несколько раз превышающее смазанный участок. Кроме того, необходимо учесть то обстоятельство, что по условиям эксперимента к экспериментальному участку поезда подходили по несмазанным рельсам. Поэтому смазка интенсивно уносилась с рельсов колесами подвижного состава и ее хватало для пропуска 8-10 грузовых поездов.
Во время эксперимента ограничение на подачу песка под колеса локомотивами не вводилось и песок подавался в обычном режиме.
К недостаткам смазки РСМ следует отнести то, что она вбирает в себя песок, пыль, что снижает ее эффективность.
Удельный расход смазки в эксперименте был равен 300-350 г/км смазываемого пути и являлся завышенным из-за указанного выше того обстоятельства, что подвижной состав подходил к экспериментальному участку с несмазанными, сухими колесами и смазка интенсивно уносилась ими.
Смазка РСМ должна наноситься только на не смоченные водой рельсы. К влажным и мокрым рельсам смазка не прилипает и интенсивно смывается с рельсов.
Абразивный характер изнашивания боковой поверхности рельсов и гребней бандажей колесных пар
Изнашивание боковой поверхности рельсов в кривых участках пути носит преимущественно абразивный характер. Абразивное изнашивание обусловлено тремя главными причинами: попадание в зону контакта колеса с рельсом кварцевого песка из песочниц локомотивов, продуктов износа колес и рельсов и внедрением выступов термоупрочнённых бандажей в материал более мягкого рельса и играющих роль закреплённых абразивных частиц.
Противоюзовое устройство
На железнодорожных экипажах отечественного производства (ВЛО, ВЛ15, ВЛ80 и т.д.) применяется форсунка песочницы, имеющая две горловины для подвода и отвода песка, полость для разрыхления песка, а также каналы для подачи сжатого воздуха на разрыхление и подачу песка в зону подсыпки. Система пескоподачи с помощью этой форсунки в качестве сигнализатора появления юза использует реле защиты от юза, срабатывающее при возникновении разности потенциалов между тяговыми двигателями. При этом обеспечивается управление подсыпкой как автоматическое, так и по команде машиниста.
Традиционными недостатками из этой системы пескоподачи являются:
- ненадежность работы форсунки, обусловленная возможностью смерзания и окускованием песка в полости для разрыхления;
- инерционность системы, выражающая в запаздывании подачи песка и обусловленная необходимостью выполнения действия по разрыхлению песка после появления управляющего сигнала от реле защиты от юза, а также наличием остаточного количества песка в подсыпном рукаве после выключения реле защиты; в режиме управления подсыпкой по команде машиниста этот недостаток значительно усиливается;
- большой расход песка.
Частично перечисленные недостатки устраняются в техническом решении по авторскому свидетельству России № 1801827, М. кл. 5В61С 15/08 [125] «Форсунка песочницы локомотива», которая совершенствует систему пескоподачи серийного производства, входящую в комплект механической части вышеперечисленных электровозов, выполнением в корпусе форсунки дополнительного канала, сообщенного с каналом подачи воздуха и составляющего острый угол с осью сопла, располагаемого под горловиной отвода песка, при этом устройство для регулирования подачи воздуха содержит сумматор, регулирующий потребное количественное соотношение расходов воздуха и песка.
Однако в этой конструкции сохраняется возможность смерзания или окускования песка в полости разрыхления, что является предпосылкой ненадежности работы системы пескоподачи.
Кроме того, общим недостатком известных технических решений является способ осуществления конечной фазы пескоподачи: песок по рукаву отводного канала поступает на головку рельса самотеком за счет массовых сил, практически равномерно распределяясь по поверхности головки рельса в ее сечении. Попавший в результате этого в зону контакта гребня колеса с боковой поверхностью головки рельса песок выполняет роль абразива, интенсифицирующего износ этих поверхностей.
Нами предлагаемое противоюзовое устройство, которое решает задачу повышения надежности процесса пескоподачи при соблюдении возможности строгой дозировки и количественного соответствия расходов воздуха и песка и исключении инерционности системы за счет мгновенного исполнения команд управляющей системы.
Поставленная задача решается тем, что в противоюзовом устройстве, содержащем корпус с горловинами подачи и отвода песка, сообщающимся с магистралью и каналами подачи сжатого воздуха и связанный со средствами автоматического включения пескоподачи, в комплект которых входят датчики юза и преобразователи электрических сигналов, отличием является то, что исполнительный орган устройства выполнен в виде расширяющегося книзу прямоточного канала подачи песка, соединенного верхней горловиной с емкостью, содержащей запас песка, снабженного пневматическим запорным устройством и размещенного внутри последовательно расположенных, разделенных перегородкой пневматических камер, верхняя из которых выполнена как корпус запорного устройства, а нижняя – как эжектор, оканчивающийся патрубком, снабженным на нижнем своем конце отражателем с возможностью уменьшения попадания песка в зону контакта гребня колеса с рельсом; при этом командный орган – блок автоматического управления, связанный с исполнительным посредством электропневматического крана, содержит блоки сравнения и информации об опорных и рабочих частотах прохождения сигналов от датчиков юза, выполненных в виде сочетания источника и приемника светового излучения, установленных с обеих сторон круговых дисков, которые имеют окна на своей поверхности и выполнены с возможностью синхронного вращения с колесными парами.
Предлагаемое устройство представлено на рисунках 4.15-4.18. На рис. 4.15 изображена укрупненная блок-схема системы пескоподачи; на рис. 4.16 – полумонтажная схема исполнительного органа; на рис. 4.17 – вариант исполнения запорного устройства; на рис. 4.18- расходный патрубок 23 с отражателем 25.
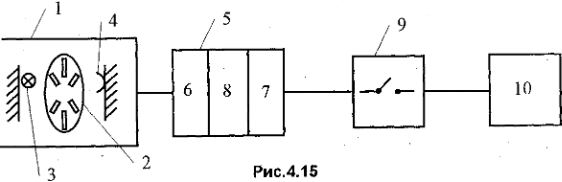
Обозначения и пояснения к схемам: 1 – датчик юза, включающий в себя диск 2, источник излучения 3 и приемник излучения 4, выполненные, например, в виде фотодиодов; 5 – блок автоматического управления пескоподачи
Таким образом, противоюзовое устройство содержит корпус с горло- инами подачи и отвода песка, сообщающийся с магистралью и каналами подачи сжатого воздуха и связанный со средствами автоматического вклю- [ения пескоподачи, в комплект которых входят датчики юза и преобразователи электрических сигналов. Отличительной особенностью противогазового устройство является то, что исполнительный орган устройства выполнен в виде расширяющегося книзу прямоточного канала подачи песка, соединенного верхней горловиной с емкостью, содержащей запас песка, снабженного пневматическим запорным устройством и размещенного внутри последовательно расположенных, разделенных перегородкой пневматических камер, верхняя из которых выполнена как корпус запорного устройства, а нижняя – как эжектор, оканчивающийся патрубком, снабжен- [ым на нижнем своем конце отражателем с возможностью уменьшения [опадания песка в зону контакта гребня колеса с рельсом; при этом командный орган – блок автоматического управления, связанный с исполни- ельным посредством электропневматического крана, содержит блоки равнения и информации об опорных и рабочих частотах прохождения сигналов от датчиков юза, выполненных в виде сочетания источника и приемника светового излучения, установленных с обеих сторон круговых [исков, которые имеют окна на своей поверхности и выполнены с возможностью синхронного вращения с колесными парами.
Конструкция позволит уменьшить количество подаваемого песка на юльсы, что уменьшит степень абразивного износа рельсов и бандажей, меныпит сопротивление движению поезда, повысит коэффициент сцепле- [ия колес ТПС с рельсами, меньше будут и затраты, связанные с расходом [еска, затратами на текущее содержание пути.
Нами подана заявка на изобретение (приоритет от 24.07.97, заявка 97113438/28(013565), в соавторстве с А.И. Миловановым).
Новый способ лубрикации рельсов
Было показано, что на поверхности рельсов имеются металлические абразивные частицы-продукты износа рельсов и колес, которые удерживаются на рельсе силами магнитного притяжения и резко снижают эффективность рельсосмазывания. Такую же негативную роль играют частицы кварцевого песка [126,129].
Известен электроискровой способ очистки поверхности рельсов [18], но для удаления металлических частиц с поверхности рельсов этот способ неэффективен.
Известен способ нанесения с помощью управляемого механического средства смазки на боковую поверхность головки рельса, реализованный, например, в устройствах по а.с. России №№2059492 [130], 2067939 [131], м. кл. 6В61КЗ/02, или на гребень колеса железнодорожного транспорта средства (см., например, а.с. СССР №1791233 [132], м. кл. 5В61КЗ/02), с целью снижения коэффициента трения гребня колеса о боковую поверхность головки рельса и, таким образом, снижения их износов, однако на участках пути, где по условиям движения железнодорожного транспортного средства требуется осуществлять подсыпку песка в зону контакта колеса с рельсом, смазка, нанесенная на поверхность рельса или колеса , оказывается связующим , удерживающим абразивные частицы на взаимодействующих поверхностях ,чем интенсифицируется подрез гребней колес и боковой износ рельсов.
Предлагаемый нами способ решает задачу снижения интенсивности износа боковой поверхности рельсов и гребней колес и за счет этого обеспечивает улучшение эксплуатационных качеств железнодорожных транспортных средств.
Эта задача решается тем, что предлагаемый способ уменьшения интенсивности износа боковой поверхности рельсов и гребней колес железнодорожного транспортного средства заключается в подаче, при помощи управляемых механических средств, химического агента на боковую поверхность рельса или на гребень колеса для снижения коэффициента трения в их контакте. При этом контактирующие поверхности рельса или колеса вначале подвергают воздействию магнитного поля, затем механической очистке, после чего на них подается охлаждающий химический агент (или смазка).
Воздействием магнитного поля устраняются металлические частицы с поверхности рельса, средство механической очистки устраняет неметаллические абразивные частицы, осевший на поверхности рельса и колеса конденсат (изморозь), полученный от охлаждения окружающего воздуха, выполняет роль смазки.
Магнитное поле может быть создано электромагнитом, закрепленным на вышеупомянутом техническом средстве. В качестве охлаждающего химического агента может применяться жидкий азот. Таким образом предлагаемый способ обладает следующими существенными достоинствами:
- Удаление металлического абразива обеспечивается воздействием магнитного поля.
- Удаление неметаллического абразива обеспечивается механической очисткой.
- Образование изморози в качестве смазки обеспечивается конденсированием влаги, содержащейся в воздухе , вблизи контактируемых поверхностей, за счет резкого охлаждения этих поверхностей подаваемым на них хладоагентом.
- Вместо конденсирующейся на охлажденном рельсе влаги можно применять обычные смазки, например РС-6.
Предполагаемый способ лубрикации рельсов особенно будет полезен при шлифовке рельсов с целью устранения неровностей на поверхности катания и на боковой поверхности рельсов, при котором образуется большое количество металлической пыли.
Используемая Литература
- Смирнов В.И. Срок службы рельсов типа Р65 при обращениии вагонов с осевой нагрузкой 250 кН на перевальных участках. Автореферат диссертации на соискание учёной степени кандидата технических наук. Ленинград, 1984, 18 страниц.
- Мелентьев Л.П. Особенности работы рельсов в тяжёлых условиях эксплуатации. – В трудах ЦНИИ МПС «Рельсы повышенной прочности для особо тяжёлых условий эксплуатации». Вып. 428. М., «Транспорт», 1970, стр. 108-140.
- Кармазин А.И. Повышение долговечности колёс грузовых вагонов и рельсов. Автореферат диссертации на соискание учёной степени д.т.н. Ростов-на-Дону, 1997, 105 с.
- Коротаев Б.В., Болотов A.C. Анализ изменения бокового износа рельсов по длине звена и разработка методики измерения износа рельсов. – В сборнике научных трудов ИрИИТа «Транспортные проблемы Сибирского региона», выпуск 2, Иркутск, 1998, с. 25-28.
- Путь и безопасность движения поездов. Под ред. д.т.н. В.Я.Шульги. М., «Транспорт», 1983, с. 94.
81 .Инструкция по текущему содержанию железнодорожного пути, ЦП/2913. М., «Транспорт», 1974. - Ершков О.П. Вопросы подготовки железнодорожного пути к высоким скоростям движения. Труды ВНИИЖТ. Вып. 176, 1959.
- Ершков О.П., Мелентьев Л.П., Яхов М.С. Расчёты железнодорожного пути в кривых и нормы его устройства. Труды ВНИИЖТ. Вып. 192, 1960.
- Марков Ю.Н. Возвышение наружной нити и износ рельсов. – В межвузовском сборнике научных трудов «Вопросы проектирования и содержания железнодорожного пути в условия Урала и Сибири». УрэМИИТ. Вып. 57. Свердловск, 1978, стр. 49-57.
- Гречук B.C. К вопросу о боковом износе рельсов в кривых при движении электросекции. – В сборнике «Исследование контактной прочности рельсов». ЛИИЖТ. Вып. 187. Ленинград, 1962, стр. 108-124.
- Мелентьев Л.П. Результаты наблюдений за развитием бокового износа рельсов в различных условиях эксплуатации. – В сборнике научных трудов ВНИИЖТа «Исследование рельсов тяжёлых типов». Вып. 220. Трансжелдориздат. Москва, 1961, 144 стр.
- Мелентьев Л.П. Исследование основных причин, влияющих на боковой износ рельсов в кривых. – Автореферат на соискание учёной степени кандидата технических наук. М., ВНИИЖТ, 1954, 12 стр.
- Хархута Т.И. Расчёт возвышения наружного рельса по грузонапряжённости. – Путь и путевое хозяйство, 1962, № 3.
- Гавриленков А.В., Ершков О.П., Иванов Г.Г., Митин Н.Ф. Определение возвышения наружного рельса, минимизирующего время хода по- ездопотока по кривой. – Вестник ВНИИЖТ, 1991, № 1, стр. 16-19.
- Карпущенко Н.И., Шлейнинг А.И. Возвышение наружного рельса и скорость движения. – Путь и путевое хозяйство, 1999, № 1, с. 22-24.
- Певзнер В.О., Редькин В.И., Карцев В .Я., Космин А.В. Возвышение рельса при смешанном движении. – Путь и путевое хозяйство, 1997, № 5, с. 33-34.
- Космин А.В. Параметры пути в кривых при смешанном движении поездов. – Автореферат диссертации на соискание учёной степени к.т.н. М., 1998, 30 с.
- Мелентьев Л.П. Как использовать рельсы Р65К. – Путь и путевое хозяйство, 1992, № 4, с. 10-11.
- Ямпольский Г.Я., Крагельский И.В. Исследование абразивного износа элементов пар трения качения. Москва, «Наука», 1973, 63 стр.
- Гюнтер X., Бессер Д. О влиянии частиц минерального происхождения на характер износа. – В кн. «Теоретические и прикладные задачи трения, износа и смазки машин». М., «Наука», 1982, стр. 227-237.
- Ямпольский Г.Я. Статистическая оценка износа абразивными частицами элементов трения качения с проскальзыванием. – В сборнике «Моделирование трения и износа». М., ИМАШ, 1970, стр. 114-121
- Тененбаум М.М. Износостойкость конструкционных материалов и деталей мшин при абразивном изнашивании. М., «Машиностроение», 1966, 332 стр.
- Биллитт М. Индустриальные смазочные материалы. М., «Машиностроение», 1982, 136 стр.
- Баулин И.С. Лубрикация рельсов на железнодорожных кривых. М., Трансжелдориздат, 1945, 35 стр.
- Линёв С.А. Эффективность смазывания рельсов для уменьшения бокового износа их в кривых. – Техника железных дорог, 1956, № 4, страница 26.
- Kalousek J. Laboratory studies of rail wheel lubrication (доклад на семинаре Американской железнодорожной ассоциации). Chicago, 1985.
- Peters and Kenneth С. Rownd. Wheel-rail lubrication research. «Transportation Test Center».
Влияние избыточной смазки рельсов на величины поперечных сил от четырёхосного локомотива (США). – Экспресс-информация «Железнодорожный транспорт за рубежом». Серия IV. Путь и путевое хозяйство. Проектирование и строительство. М., 1992, выпуск 3, стр. 14-19.
Лубрикация рельсов на железных дорогах США. – Железно дорожный транспорт, 1988, № 12, стр. 72-73. - Мелентьев Л.П. Совершенствование профилей рельсов. – В кн.: Улучшение использования железнодорожных рельсов. Труды ВНИИЖТ, вып. 334. М., «Транспорт», 1967,144 стр.
- Полякова Г.Г. О смазке рельсов на перевальном участке. – В межвузовском сборнике научных трудов «Надёжность и эффективность работы железнодорожного пути в условиях Сибири», под редакцией Л.М.Дановского. Новосибирск, 1980, стр. 82-85.
- Ядрошникова Г.Г. Интенсивность износа и сроки службы рельсов в кривых при рекуперативном торможении поездов. – Автореферат диссертации на соискание учёной степени кандидата технических наук. Новосибирск, 1988, 20 страниц.
- Мелентьев Л.П. Исследование причин бокового износа рельсов в кри-вых. – В сб. научных трудов ЦНИИ МПС. Вып. 154, «Трансжелдор- издат», 1958.
- Мелентьев Л.П. Эксплуатационная стойкость рельсов. – Железно доррожный транспорт, 1974, № 8, стр. 61-64.
- Ю.Мелентьев Л.П. Смазывание рельсов на кривых участах пути. М., «Транспорт», 1962, 36 стр.