Сейчас ваша корзина пуста!
О влиянии соотношения твердости бандажной рельсовой сталей на интенсивность изнашивания рельсов
Цикл статей:
Введение
Глава 1 – Анализ процессов в зоне фрикционного контакта колеса с рельсом
Глава 2 – Методика экспериментальных наблюдений и обработка данных
Глава 3 – Основные результаты наблюдений
Глава 4 – Исследование неравномерности износа рельсов по длине звена
Глава 5 – О влиянии соотношения твердости бандажной рельсовой сталей на интенсивность изнашивания рельсов
Глава 6 – Влияние нагруженности локомотивов на интенсивность износа рельсов
Регрессионные зависимости износа рельсов от наработки тоннажа и радиуса кривой на подъеме четного пути
Химико-термические методы упрочнения металлов путем увеличения поверхностной твердости весьма эффективны для повышения сопротивления абразивному изнашиванию [133].
Проблема повышения твердости рельсовой и бандажной сталей как методу повышения их износостойкости посвящена обширная литература [18, 23, 87,121,128,134 – 144] и др.
В связи с введением новых технологий повышения твердости бандажной стали _ вопрос об оптимальном соотношении твердости рельсовой и бандажной сталей приобретает большое значение.
Д.т.н. Т.В. Ларин [135, 136] на основании испытаний образцов из рельсовой и бандажной сталей пришел к выводу, что твердость бандажной стали должна быть в 1,2-1,4 раза выше твердости рельсовой стали.
В статье А.Н. Вихровой, Т.В. Ларина и др. [137] утверждается, что увеличение твердости колесной стали от 250 до 400 НВ практически не влияет на износостойкость и контактную долговечность рельсовой стали.
Д.А. Курасов [18] приходит к аналогичным выводам.
Э.А. Томило [141] получил расчетным путем, что износ рельса
пропорционален квадрату отношения (НВ§/НВр)2 и обратно пропорционален НВр. Износ бандажа пропорционален (НВр/НВ§) и обратно пропорционален НВ5.
Существуют и другие мнения. В статье Горского A.B. и др.[142] со ссылкой на исследования И.И. Домбровского утверждается, что минимальный износ бандажей и рельсов достигается при соотношении твердости бандажа НВ§ и рельсов НВр в пределах НВ§/ НВр=1-И,05.
В.М. Богданов [19] считает необходимым пересмотреть этот вопрос. Исследования Е.А. Шура, например, показывают, что наименьший суммарный износ металлов получается при одинаковой твердости контактирующих поверхностей.
Необходимо учесть, что Т.В. Ларин, делая заключение о необходимости более высокой твердости бандажа по сравнению с рельсом на основании опытов с ршками из бандажной и рельсовой сталей, предупреждал, что выводы могут быть распространены на работу пары рельс- бандаж при условиях наличия трения качения с проскальзыванием, отсутствие между поверхностями разделяющего слоя в виде песка, влаги и масла, которые изменяют природу взаимодействия поверхностей в контакте.
Реальный контакт гребня колеса с рельсом отличается именно тем, что имеем трение скольжения и разделяющий слой в виде песка, влаги, масла и продуктов износа рельсов и бандажей.
Т.В. Ларин указывал, что по условиям обработки твердость бандажей до HB 350 надо считать приемлемой и превышать её без надобности.
Прямое отношение к рассматриваемому вопросу имеет статья X. Гюнтера и Д. Бессера [95] из которой следует, что относительный износ изнашиваемого материала при постоянной твердости минеральных частиц резко уменьшается при твердости металла 340-350 кгс/мм2 и при дальнейшем увеличении твердости металла уменьшение износа происходит медленно. Это исследование подтверждает необходимость увеличения твердости бандажной стали до HB 3433 Н/мм2 (350кгс/мм2).
В последнее время проблема оптимальной твердости получила развитие в трудах Д.П. Маркова [145-148]. Считается[148],что преимущественными видами изнашивания являются сглаживание микронеровностей, усталостное и заедание. При этом наиболее опасный вид изнашивания (заедание) возникает при больших проскальзываниях и определяется величиной проскальзывания и твердостью тел. В [148] содержится вывод, что суммарная износостойкость колес и рельсов увеличивается при увеличении одного из элементов, тогда как при средних величинах проскальзываний суммарная износостойкость увеличивается, если увеличиваются твердости обоих элементов. Определена [146] и минимальная твердость закаленного слоя в гребнях (600 HV или 520 ЕВ) по условию невозникновения в них усталостных трещин. Во избежание возникновения заедания необходимо закаливать гребни колес и боковые поверхности рельсов на твердость свыше 400 НУ («380 НВ).
Необходимо остановится на понятиях схватывания и заедания поверхностей при трении. Согласно Гаркунову Д.Н. [22] «схватывание- явление прочного соединения металлов в результате взаимного трения или совместного деформирования ниже температуры рекристаллизации. Считается, что для образования прочных связей между металлами в холодном состоянии необходимо отсутствие на соприкосающихся поверхностях пленок и загрязнений. При этом сближение трущихся поверхностей должно быть на межатомное расстояние [22,23].
По Б.И. Костецкому [23] «Изнашивание схватыванием первого рода – это процесс интенсивного разрушения поверхности деталей машин при трении, выражающийся в пластической деформации поверхностных слоев, возникновении местных металлических связей на трущихся поверхностях и разрушении их с отделением частиц металла или налипания их на поверхностях трения».
По ГОСТ 23.002-78 [24] изнашивание при заедании определяется как изнашивание в результате схватывания, глубинного вырывания материала, переноса его с одной поверхности трения на другую и воздействия возникших неровностей на сопряженную поверхность.
Не отрицая в принципе возможность возникновения схватывания металлов гребня бандажа и рельса и последующего разрушения металлических связей, обратим внимание на следующие явления. Первое – в зоне контакта гребня колеса и рельса существует третье тело из пленок окислов (разрушение которых при пластическом деформировании металла может обеспечить металлический контакт на ювенильных поверхностях), смазочных материалов, измельченного песка и продуктов износа рельсов и бандажей.
С нашей точки зрения достаточно плотная и распределенная по всей длине рельса пленка из продуктов износа рельсов и бандажей препятствует образованию металлических связей и, следовательно, изнашиванию в форме заедания. Этому же препятствует и наличие песка, масла и других загрязнений на поверхности рельсов.
Второе важное наблюдение заключается в том, что вид изношенной поверхности рельсов не соответствует изнашиванию при заедании (рис. 4.20). Согласно ГОСТ 23.002-78 такой вид повреждений, какой мы наблюдаем на рисунке, может быть отнесен к задиру.
При свежих повреждениях рельсов кромки задиров и царапин острые, длина и направление их говорят о направлении скольжения в зоне контакта выкружки бандажа с рельсом и о продолжительности контакта.
Происхождение задиров и царапин можно объяснить внедрением соответствующих глубине и ширине борозд на рельсе неровностей на поверхности более твердого тела-бандажа.
О влиянии твердости бандажной стали износ рельсов на перевальном участке ВСЖД
С 1995 года в локомотивном депо Иркутск-Сортировочный введена установка плазменного поверхностного упрочнения бандажей локомотивных колес.
Способ упрочнения заключается в сверхскоростном нагреве металла до температуры закалки с последующим охлаждением за счет теплопроводности металла бандажа. Способ реализуется при использовании в качестве концентрированного источника нагрева плазменной струи.
Режим плазменного упрочнения был следующий: мощность плазменной струи-40 кВт, частота вращения колесной пары-0,8 об/мин, расход плазмообразующего газа-12 л/мин, шаг смещения плазматрона 10мм.
Обследовано десять электровозов ВЛ80Т, обращавшихся на участке Иркутск-Слюдянка. Измерение твердости произведено прибором ТЕМП-1. В связи со значительным разбросом показаний прибора при измерениях в различных точках ограниченной области гребня бандажа или поверхности катания количество измерений было не менее 6-8, при этом отчеты, на много отличающиеся от некоторого среднего значения в этой области, отбрасывались. Для примера в таблице 4. приведены данные по твердости шести осей электровоза №1332.
Таблица 4.18
Дата: 22.03.96 | Локомотив ВЛ 80 т | 1332 | ||||||
Но мер | Средний отчет по ТЕМП-1 | Твердость по Бринеллю (кгс/мм2) | ||||||
оси | Поверх, катания | Гребень | Поверх. | катания | Гребень | |||
левое | правое | левое | правое | левое | правое | левое | Правое | |
1 | 600 | 571 | 590 | 592 | 376 | 347 | 366 | 368 |
2 | 608 | 619 | 746 | 644 | 384 | 396 | 535 | 420 |
3 | 566 | 572 | 755 | 767 | 342 | 348 | 540 | 560 |
4 | 580 | 555 | 601 | 754 | 356 | 328 | 377 | 540 |
5 | 580 | 55 | 642 | 587 | 356 | 331 | 420 | 363 |
6 | 576 | 574 | 728 | 610 | 352 | 350 | 511 | 386 |
Анализ замеров твердости термоупрочненных бандажей показал, что абсолютная величина твердости гребней достигает НВ5700 МПа (580кгс/мм2), разница твердости колес одной колесной пары достигала на
поверхности катания 9% и гребней 27-43%, разброс твердости гребней по комплекту колебался от НВ3787 до НВ5494 МПа (от НВ 386 до НВ560 кгс/мм2).
Инструкцией [149] допускается разность твердости бандажей на одной колесной паре НВ24. В процентах это означает допустимая разность твердости равна 6,8% при твердости НВ350 и 4,8% при твердости НВ500.
Особое значение приобретает вопрос о шероховатости поверхности бандажа при обточке. В настоящее время после обточки не производится чистовой обработки поверхности катания и гребня. Не применяются какие- либо иные методы уменьшения шероховатости бандажа после обточки, например предусмотренная инструкцией ЦТ/329 [149] накатка роликом обработанной поверхности бандажей по кругу катания. Требование, чтобы
шероховатость поверхности катания не превышала 80мкм, не выполняется. При этом инструкцией не предусматриваются также требования к чистоте поверхности гребня бандажа.
Существующее представление о том, что конечная установившаяся шероховатость трущихся тел не зависит от исходной шероховатости этих тел [1, 4], приводит к неправильному выводу, что при обточке колесных пар чистота обработки поверхности не имеет существенного значения. Особенность трения в зоне контакта гребня колеса с рельсом является нестационарность режима трения. Нестационарность режима трения обусловлена следующими факторами: большим разбросом в величинах твердости колесных пар подвижного состава (как тягового, так и вагонов), динамическим характером сил взаимодействия, различиями в профиле колес, различиями физико-механических свойств поверхностного слоя бандажей колес, различия в степени изношенности колес подвижного состава, подачей песка из песочниц локомотивов для увеличения коэффициента сцепления, различием осевых нагрузок от колесных пар, величины скольжений, неравномерностью износа рельсов по длине, неправильностью очертания гребня колеса по длине обода и т.д.. Нестационарность режима трения относится как к рельсу, так и колесам подвижного состава, которые при движении вступают во взаимодействие с рельсами различного профиля из-за неравномерности их износа, различной твердости и химического состава.
Нестационарность режима трения приводит к тому, что рельсы и колеса подвижного состава находятся как бы в режиме приработки, и процесс не переходит в установившуюся стадию минимальной интенсивности износа. Режим приработки и интенсивность изнашивания в этом режиме существенно зависят не только от шероховатости колес и рельсов, но и от процесса обточки. Дело в том, что одна и та же шероховатость может быть достигнута при различной скорости точения и глубине подачи резца. В процессе приработки износоустойчивость поверхности при данной шероховатости будут зависеть от величины остаточных напряжений, полученных при обточке.
Но режим приработки не может быть регулируемым в условиях взаимодействия подвижного состава и пути и происходит при максимальных нагрузках. Известно и то, что интенсивность изнашивания в стадии приработки в очень сильной степени зависит от шероховатости поверхности [150]. И чем больше шероховатость, тем больше интенсивность износа из-за возрастания механической составляющей износа. Уменьшение шероховатости в принципе увеличивает вероятность схватывания, но в условиях взаимодействия колеса и рельса при наличии смазки, продуктов износа, частиц минерального происхождения и т.д. не может принять существенного значения.
Вне зависимости от того, зависит или не зависит величина установившейся шероховатости от исходной, время приработки и приработочный износ зависит от исходной шероховатости поверхностей пар трения [151].
Перечисленные причины нестационарности процесса трения в зоне выкружки колеса и гребня с рельсом и вытекающего из этого режима приработки требуют принятия соответствующих мер для уменьшения интенсивности износа бандажей и рельсов: повышение качества обработки поверхностей бандажей и вагонных колес при обточке, обеспечение максимально достижимой одинаковости твердости по окружности гребня и бандажа, обточка бандажей тягового подвижного состава « по копиру» с целью выдержанности профиля бандажа, профильная шлифовка рельсов по поверхности катания и по боковой поверхности.
Наблюдения показывают, что на боковой поверхности рельсов образуются царапины глубиной до 8-ми мм, являющиеся следствием внедрения в материал рельса более твердого материала (рис. 4.20), а направление царапин свидетельствует о направлении скольжения гребня колеса относительно рельса. Глубокие повреждения боковой поверхности не могут быть произведены продуктами износа рельсов и бандажей и частицами минерального происхождения. Следы резания и пропахивания поверхности рельса образуются внедрением выступов на гребне бандажа, появившихся в результате грубой обработки поверхности бандажа при обточке [152].
Таким образом, источником абразивного характера износа рельсов являются три фактора: внедрение с пропахиванием в боковую поверхность рельса прошедших упрочнение выступов на поверхности гребня, образовавшихся при обточке бандажей; наличие в зоне контакта гребня бандажа с боковой поверхностью рельса продуктов износа и удерживаемых на поверхности рельса силами магнитного притяжения; наличие в контакте колеса с рельсом продуктов минерального происхождения, в основном кварцевого песка.
В связи с абразивным характером изнашивания рельсов и бандажей необходимо отметить следующее: во-первых, смазывание поверхностей трения не может решить проблему уменьшения износа рельсов и бандажей полностью. Во-вторых, условия открытого контакта могут обеспечить только граничное смазывание. Это означает, что обеспечить целостность смазывающей пленки по всей длине рельсов и бандажей невозможно, что приводит в местах нарушения целостности смазывающей пленки к адгезионным связям и, возможно, схватыванию поверхностей трения с последующим разрушением связи. В-третьих, по причине значительной шероховатости поверхностей трения рельсов и бандажей на площадках контакта происходит взаимное внедрение поверхностей и при наличии целостной смазочной пленки. В условиях трения скольжения гребня бандажа по боковой поверхности рельсов происходит задир поверхностей внедрившимися объемами с пластическим оттеснением материала и разрушением его. Образование продуктов износа рельсов и бандажей приводит к интенсивному износу и самой смазочной пленки, т.к. масло адсорбируется на частицах износа и уносится с поверхностей трения.
Поэтому повышение чистоты обработки поверхности гребней бандажей при обточке могло бы существенно уменьшить взаимное внедрение контактирующих поверхностей бандажей и рельсов и, следовательно, уменьшить их износ.
На необходимость повышения гладкости поверхностей и повышение их твердости, удалении абразивных частиц из зоны контакта с целью уменьшения интенсивности абразивного изнашивания указывалось в [153] (стр.16).
В-четвертых, скольжение гребня бандажа по рельсу в сочетании с высокими удельными давлениями вызывают повышение температуры в зоне контакта, что приводит к разрушению смазочной пленки.
Обследование обточенных колесных пар показало, что качество чистоты обработки поверхности бандажа при обточке неудовлетворительно. Чистовая обработка резаньем может обеспечить чистоту поверхности по шестому классу по действовавшему ранее ГОСТ 2789-73. По СТ СЭВ 63877 показатели шероховатости должны быть равны Яа 08,-3,2 мкм; Кт, -свыше 1,6 мкм и до 12,5 мкм [154], где Яа-среднее арифметическое отклонение профиля, Ят -наибольшая высота неровностей профиля (расстояние между линией выступов и линий впадин профиля в пределах базовой длины), Я2 -высота неровностей профиля по десяти точкам.Известно, что при такой обработки поверхностей неровности нельзя различить на ощупь и нужны специальные приборы для определения класса.
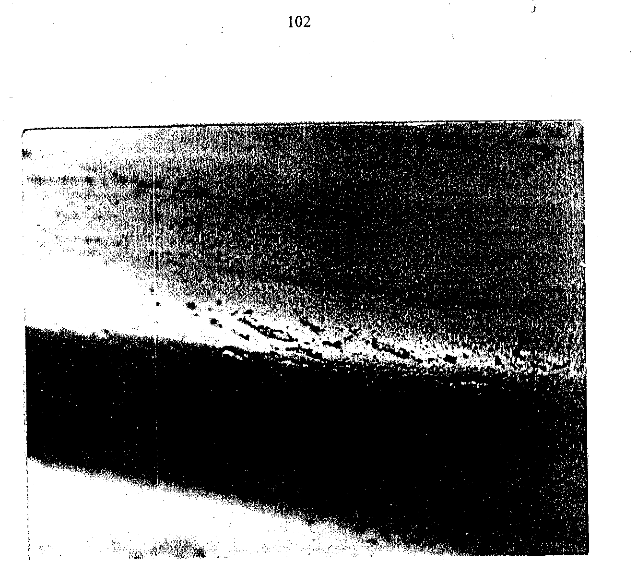
Выводы
- Боковая поверхность рельсов в условиях ВСЖД испытывает главным образом абразивное изнашивание, а по поверхности катания – усталостное изнашивание в условиях пластического оттеснения материала, переформирования и наклепа.
- Абразивное изнашивание рельсов вызывается прежде всего частицами износа рельсов и бандажей, внедрение более твердых по сравнению с рельсом выступов и неровностей на поверхности гребня бандажа, образовавшихся в результате периодических обточек колесных пар ТПС.
- Минимальная эффективность от смазок РС-6 и др. при нанесении их рельсосмазывателями конструкции ВНИИЖТа объясняется присутствием в зоне фрикционного контакта продуктов износа рельсов и бандажей, абразива минерального происхождения.
- Плазменное упрочнение бандажей колесных пар ТПС является перспективным способом увеличения ресурса бандажей. Вместе с тем твердость бандажей в области гребня является завышенной по отношению к твердости рельсов, что приводит к увеличению интенсивности изнашивания рельсов.
- Необходимо перед плазменным упрочнением бандажей производить чистовую обработку поверхности бандажа и уменьшить шероховатость ее до Rz 20.
Влияние температуры в зоне фрикционного контакта на износ
Исследование влияния температуры на процессы, происходящие в контакте колесо-рельс, имеет очень большое значение. В конечном счете от абсолютного значения температуры зависит устойчивость смазочного слоя, образование тех или иных химических соединений, величина коэффициента трения и интенсивность износа как рельсов, так и бандажей.
В статье [155] (Чичинадзе A.B. и др.) указывается, что исследования позволили обосновать и подтвердить основную гипотезу, по которой коэффициент трения и интенсивность износа фрикционных пар – однозначные функции максимальной температуры поверхности трения, которая является интегральным фактором, отражающим совместное влияние нагрузки, скорости, фрикционных свойств, а также теплофизических свойств материалов пары и конструктивных размеров фрикционных элементов.
Влияние скорости скольжения проявляется также в первую очередь через температуру трения [14, 95].
Изменение температуры в зоне контакта колеса с рельсом имеет несколько последствий: разрушение смазочного слоя в результате нагревания поверхностного слоя; изменение глубины относительного внедрения трущихся тел; изменение коэффициента трения; образование так называемого черного налета на рельсах, состоящего из льда, мелкодисперсных продуктов, смазки и изгари.
Величина относительного внедрения, по исследованиям A.B. Чичи- надзе [156],для данной конфигурации неровностей зависит от температурного поля, т.к. при изменении температуры изменяются механические свойства материалов. В тоже время величина относительного внедрения зависит и от нагрузки, но в значительно меньшей степени, т.к. увеличение нагрузки приводит к увеличению числа фактических пятен контакта при незначительном увеличении глубины внедрения.
Исследования трения стали 22ХНМ [155] со смазками “ЦИАТИМ – 203” и “Литол” показали, что при увеличении температуры от 50 до 200°С коэффициент трения увеличивается в 2 – 4 раза, достигая 0,24 – 0,39.
В статье Ю.М. Лужнова [157] утверждается, что расчет средней в зоне контакта температуры нагрева поверхности трения показал, что она может достигать 12-15°С, что во многом может определять условие фазового перехода льда в воду и фрикционные свойства рельсового пути. Именно поэтому происходит образование “черного налета” на рельсах при температуре воздуха ниже -15 – 20°С. При этом адгезия “черного налета” к рельсу часто повышает его когезионную прочность, что затрудняет удаление “черного налета” с рельсов.
По другим исследованиям (Т. Борзо, [158]), при прохождении поезда температура рельса может повышаться на 11°С.
Важно отметить [158], что температура гребня колеса может повыситься до 150°С и даже до 290°С во время динамического торможения.
В книге C.B. Алехина и Н.С. Продана [159] приводятся результаты замеров температуры бандажей при торможении поезда из двух локомотивов ЧС2М и трех вагонов. Температура бандажей измерялась инфракрасными датчиками, установленными на расстоянии 25 мм от поверхности бандажа. В результате торможения при падении скорости движения с 200 до 160 км/ч температура достигала 300°С.
И.В. Крагельский в работе [160] указал на то, что при трении скольжения возникновение высокой температуры изменяет механические свойства трущихся материалов и характер пленок. Сила трения меняется со скоростью скольжения через изменение свойств материала при изменении температуры.
С.И. Косиков [119] установил, что после длительного температурного воздействия происходят необратимые структурные изменения смазочной пленки (из мазута и цилиндрового масла). При охлаждении смазывающее действие пленки не восстанавливается. Опыты проводились на образцах из рельсовой стали.
По исследованиям Ф.П. Лроудена и Д. Тейбора [14, 161], высокая температура в пятнах касания повышает химическую активность поверхностей трения и частиц износа по отношению к окружающей атмосфере или смазке. Относительно быстрый нагрев и охлаждение (как это имеет место в контакте колесо-рельс) горячих пятен могут вызывать структурные изменения в металле и существенно облегчить диффузию и образование сплава на поверхности.
Ф.П. Броуден и Д. Тейбор [161] показали, что даже при наличии смазочных пленок на поверхности могут развиваться очень высокие температуры, достигающие нескольких сот градусов при сравнительно небольших нагрузках и скорости скольжения. Эти высокие температуры локализуются в точках фактического контакта.
С другой стороны, при повышении температуры до 130 – 150°С, возникает дезориентация молекулярного слоя вследствие теплового движения, и защитная роль смазок нарушается [1].
Лейн Т.Б. [162], исследуя условия заедания трущихся поверхностей при граничной смазке, приводит мнение Блока, что для каждого сочетания трущейся пары и смазки существует своя местная температура на поверхности контакта, при которой смазочная пленка разрушается и начинается усиленный износ.
Существует и некоторая осреднённая оценка влияния низких температур на износ рельсов. Г.М. Шахунянц и др. [128] по наблюдениям за износом рельсов на ВСЖД считают, что влияние низких температур(ниже
« -25° С) на повышение удельного износа рельсов находится в границах (0,3-2)%. В тоже время влияние низких температур зависит от степени использования тяговых возможностей локомотивов, от движения во время буранов и гололеда. При движении на пределе тяговых возможностей локомотивов во время метелей и гололеда износ рельсов резко увеличивается.
В статье Г.Г. Поляковой, Ю.Н. Ликратова и др. [163] указывается на более интенсивный износ рельсов и бандажей в зимнее время, чем в летнее.
Взаимодействие колеса и рельса происходит на выступах неровностей поверхностей. Неровности поверхностей являются источниками концентрации напряжений. Понижение тмпературы, приводящее к охрупчи- ванию стали, должно было бы привести к существенному увеличению интенсивности износа рельсов в зимних условиях.
По исследованиям ВНИИЖТа [164], критическая температура перехода незакаленных рельсов в хрупкое состояние находится в пределах до – 20 С, а закаленных до -30°С. Микролегирование стали позволило повысить низкотемпературную надежность рельсов и снизить верхний порог хладноломкости до -80°С. К сожалению, мы не знаем критерий, которым пользовались авторы статьи [164], при определении критической температуры.
Существенное влияние на величину критической температуры, при которой происходит переход в хрупкое состояние, имеют структура стали (крупно – или мелкозернистая) и наличие концентраторов напряжений [139,140]. В книге С.П. Тимощенко [165] со ссылкой на исследования H.H.
Давиденкова показано, что критическая температура для крупнозернистой
среднеуглеродистой стали (0,23% углерода) равна « -95°С, в то время как
в случае мелкозернистой была равна « -160° С . Концентратор напряжений в форме выточки привел к увеличению критической температуры приблизительно до +40 и 0 °С соответственно для крупнозернистой и мелкозернистой сталей, а интервал температуры, при котором происходит переход от хрупкого к пластическому разрушению, гораздо больше в случае образцов с надрезами.
Поверхностный слой металлов рельса и бандажа имеет сложное строение. В работе В.Н. Кащеева [166] отмечалось, что над первичной объемной структурой металла располагается зона деформированного металла, обычно возникающая после механической обработки, затем следует слой окислов, химически связанный с металлом, адсорбционный слой газа, слой воды и адсорбционный слой полярных молекул смазки и органических веществ. При этом измененный поверхностный слой при обточке может быть толщиной от 0,25 до 2,0 мм [166].
Трение в контакте колесо – рельс способствует усилению адсорбции и разрыхлению поверхностного слоя.
Поставщиком водорода, адсорбируемого стальными поверхностями, могут быть смазки, пластмассы и т.д.
При насыщении поверхностных слоев металла водородом происходит его охрупчивание, уменьшением способности поглощать энергию при деформации и, следовательно, ускорению процесса разрушения. Характерно то, что охрупчивание стали под влиянием водорода происходит в интервале температур от -100 до +100°С. Наибольшая степень охрупчива- ния наблюдается при комнатной температуре или несколько более низкой температуре.
Сталь особенно склонна к водородной хрупкости в закаленном состоянии и в результате наклепа [4, 166,167].
Имеется ряд гипотез, объясняющих механизм водородной хрупкости, наиболее распространенная из которых объясняет уменьшение прочности стали снижением уровня поверхностной энергии металла при адсорбции водорода в вершине развивающейся трещины. Стальные поверхности рельсов склонны к атмосферной коррозии. Это явление мы наблюдаем постоянно. Уже через несколько суток снятые с пути рельсы покрываются слоем ржавчины. Этот процесс в рельсах происходит постоянно и в действующем пути. В процессе атмосферной коррозии происходит интенсивное наводораживание стальных поверхностей, усиливающейся с увеличением влажности воздуха.
Часть водорода попадает в пространственные дефекты металла, создает большие давления, доводящие металл до разрушения вблизи поверхности.
Наблюдение за износом рельсов в зависимости температуры на ВСЖД
Для оценки влияния температуры вычислим интенсивность износа рельсов в зимний и летний периоды (табл. 4.19).
Таблица 4.19№ | Км | R, | Период | Ahs, | Ahb, | А Г, | Ah/AT | |||
п.п | M | наблю | мм | мм | млн т | Боковой | Вертикальный | |||
дений | Зима | Лето | Зима | Лето | ||||||
1 | 5241/42 | 295 | 28.11.814.02.82 | 1.56 | 1.06 | 19.184 | 0.081 | 0.055 | ||
30.04.82- | 1.83 | 0.67 | 28.698 | 0,064 | 0,029 | |||||
6.08.82 | ||||||||||
2 | 5240/41 | 297 | 29.11.8227.02.83 | 1.43 | 0.74 | 25.060 | 0.057 | 0,03 | ||
26.04.81- | 1.44 | 0.44 | 27.461 | 0.052 | 0.016 | |||||
31.08.81 | ||||||||||
3 | 5237 | 350 | 5.11.8229.01.83 | 1.27 | 0.43 | 22.448 | 0.056 | 0.019 | ||
02.05.82- | 1.29 | 0.97 | 28.673 | 0.045 | 0.034 | |||||
03.08.82 | ||||||||||
4 | 5238/39 | 306 | 31.10.814.02.82 | 1.59 | 1.56 | 26.120 | 0.061 | 0.06 | ||
30.04.82- | 1.55 | 1.21 | 31.486 | 0.049 | 0.038 | |||||
11.08.82 | ||||||||||
5 | 5279 | 300 | 01.11.8125.02.82 | 1.96 | 2.04 | 29.935 | 0.064 | 0.068 | ||
04.05.83- | 1.63 | 1.11 | 26.170 | 0.062 | 0.042 | |||||
02.08.83 | ||||||||||
6 | 5279/80 | 536 | 01.11.8102.02.82 | 1.4 | 1.78 | 24.731 | 0.057 | 0.072 | ||
03.06.82- | 1.09 | 1.02 | 24.503 | 0.044 | 0.042 | |||||
02.09.82 | ||||||||||
7 | 5277/78 | 302 | 29.11.8125.04.82 | 1.76 | 1.88 | 39.008 | 0.045 | 0.048 | ||
25.04.82- | 1.66 | 1.72 | 44.542 | 0.037 | 0.039 | |||||
29.09.82 | ||||||||||
8 | 5279 | 300 | 30.12.8205.04.83 | 2,04 | 1.53 | 29.977 | 0.068 | 0.051 | ||
03.06.82- | 1.56 | 1.04 | 24.849 | 0.063 | 0.042 | |||||
02.09.82 |
Различие износов в зимний период по сравнению с летним (в %) в таблице 4.20.
Таблица 4.20
№ п.п. | Км | Я | Боковой износ | Вертикальный износ |
1 | 5241/42 | 295 | >26,6 | >139,0 |
2 | 5240/41 | 297 | >9,6 | >87,5 |
3 | 5237 | 350 | >24,4 | <44,0 |
4 | 52338/39 | 306 | >24,5 | >57,9 |
5 | 5279 | 300 | >3,2 | >62,0 |
6 | 5279/80 | 536 | >29,5 | >71,4 |
7 | 5277/78 | 302 | >21,6 | >23,1 |
8 | 5279 | 300 | >7,9 | >21,4 |
9 | 5276 | 297 | >50,0 | >117,4 |
10 | 5241 | 295 | >10,0 | >154,0 |
Средние значения износа в табл. 4.16 определены для шести звеньев в каждой кривой.
На подъеме (позиция 1-4) и на спуске (позиция 5-9) и вертикальный, и боковой износ рельсов в зимний период по сравнению с летним больше в 1,09-2,2 раза.
Более интенсивное изнашивание рельсов в зимний период связано, возможно, с более интенсивной подачей песка для увеличения сцепления колес ТПС с рельсами. Отметим, что весовые нормы поездов в зимних условиях не уменьшаются, хотя эта возможность предусмотрена правилами тяговых расчетов [168].
О влиянии ширины колеи на износ рельсов
В связи с увеличением интенсивности бокового износа рельсов и гребней колес подвижного состава на сети дорог вопрос о рациональной ширине колеи вновь стал актуальным. Ещё большее значение эта проблема может иметь в случае унификации ширины колеи 1520 мм для кривых радиусом 300м и более. Мнения как научных исследователей, так и практических работников железнодорожного транспорта по этому вопросу часто противоположны. Существуют убедительные аргументы у сторонников той точки зрения, что уменьшение ширины колеи положительно сказывается на уменьшении уровня динамического воздействия подвижного состава на путь, на уменьшении предельно возможного угла набегания колес подвижного состава на рельс, обеспечивает более плавное движение поездов [109, 169 – 171]. По другой точке зрения [172] переход на колею 1520 мм прогнозируемый ресурс у рельсов уменьшился на 30%, а бандажей колесных пар на 20,2%.
Вопрос о ширине колеи сводится к выяснению влияния зазора между рабочей гранью головки рельса и гребней колес на боковые силы [173]. Расчеты показывают [173], что уменьшение зазора лишь при растягивающих продольных силах снижает боковые поперечные силы.
Из последних публикаций обратим внимание на докторскую диссертацию Королькова Е.П. [174] и книгу Вериго М.Ф. [175]. Корольков Е.П. приходит к выводу, что “радикальным методом уменьшения износа гребней колес и сопротивления движению является восстановление уширений и расстояния между рельсами 1524 мм”, что “установленный в настоящее время зазор между колесными парами и рельсами вызывает интенсивный износ гребней колес и боковых поверхностей рельсов и вызывает дополнительные силы сопротивления движению”.
М.Ф. Вериго [175] ставит вопрос о постановке широких опытов в натуре по возможности использования унифицированной ширины колеи 1520 мм с радиусами 300 м и более. Основанием для таких опытов являются результаты исследований на имитационных моделях, заключающиеся в том, что направляющие, боковые, рамные силы и фактор износа при движении вагона по кривым радиуса 350 м и 200 м даже с максимальным непогашенным поперечным ускорением а=0,7 м/кв.с не только не увеличиваются, но за счет снижения уровня скоростей даже уменьшаются. Аргументами в пользу исследования возможности использования ширины колеи 1520 мм при радиусах круговых кривых R>300 м являются: отсутствие ранее обращавшихся на сети длиннобазных двух – и трехосных вагонов, мощных паровозов с большой жесткой базой, «учет реально используемых допусков содержания пути по направлению (рихтовке) может существенно изменить наше отношение к значению минимального радиуса, при котором ещё можно применять унифицированную ширину колеи 1520».
О необходимости увеличить граничный радиус кривой «унифицированной колеи» с 350 метров до 650 метров и установить большие минимальные значения ширины колеи в кривых, в том числе 1530 мм при радиусе меньше 350 м предлагалось в статье В.С.Плоткина и др.[176].
Для установления влияния ширины колеи на износ рельсов требуется тщательно поставленный эксперимент. Для того, чтобы выделить из множества факторов, влияющих на интенсивность износа, влияние ширины колеи, необходимо уложить рельсы одной партии в одной и той же кривой, но при различной ширине колеи в различных участках этой кривой. При этом должно быть выдержано возвышение наружного рельса на всей части круговой кривой, необходимо тщательное содержание кривой в плане и, как минимум, произвести измерение твердости рельсовой стали всех наблюдаемых звеньев. Сравнение данных износа рельсов, уложенных даже в кривые одинакового радиуса при одинаковом возвышении наружного рельса, проблематично. Практика показывает, что двух одинаковых кривых по условиям эксплуатации не существует, так как могут отличаться в этих кривых продольные уклоны пути, режимы вождения поездов и их скорости, длины кривых, модуль упругости рельсового основания, температурные условия и т.д. Несоблюдение эксплутационных условий приводит к изменению интенсивности износа рельсов. Однако в нашем распоряжении есть данные наблюдений, сравнение которых возможно.
В тексте и таблицах будем придерживаться следующих обозначений: 8, А 8 – ширина колеи и её приращение, мм; , – боковой износ рельсов и его приращение, мм; Ы – радиус круговой кривой, м; Ы§- интенсивность бокового износа рельсов, мм/млн.т брутто груза; Т – наработка тоннажа, млн.т брутто груза; 8о – ширина колеи на начало наблюдений, мм.
Проследим за интенсивностью износа рельсов в кривой радиуса 300м с условным номером 4 (на подъеме четного пути перевального участка ВСЖД). Замеры износа относятся к различным рельсам, но наблюдения велись с момента укладки рельсов. При этом возвышение рельса при сплошной смене не менялось, твердость рельсов в среднем была одинакова, рельсы объемно закаленные Р65 производства КМК. Первый период наблюдений с 03.04.82 по 11.08.82, второй период – с 02.10.82 по 27.03.83. Измерение износа проводилось одним исполнителем и одним инструментом, в одних и тех же фиксированных точках на звене. Данные наблюдения сведены в таблицы [4.21,4.22].
Таблица 4.21 Изменения 8 и в кривой N 403.04.82 | 11.08.82 | Д5> | Щ | дт | к’5 | |||
Звено | 80 | К | 8 | к5 | ||||
2 | 1520,5 | 0,5 | 1529,8 | 3,2 | 9,3 | 2,7 | ||
3 | 1521,5 | 0,7 | 1530,5 | 3,7 | 9,0 | 3,0 | 36,873 | 0,079 |
4 | 1522,5 | 0,3 | 1531,8 | 3,5 | 9,3 | 3,2 | ||
5 | 1522,0 | 0,5 | 1533,2 | 3,4 | 11,2 | 2,9 | ||
6 | 1523,5 | 0,4 | 1532,0 | зд | 8,5 | 2,7| |
В среднем для пяти звеньев ширина колеи увеличилась на А 8=9,5 мм, боковой износ в среднем увеличился на =2,9 мм.
Таким образом, из-за износа рельсов ширина колеи увеличилась на 2,9 мм, а из-за необратимой деформации шпал, разработки костыльных отверстии в подкладках на – =6,6 мм.
Увеличение ширины колеи из-за необратимой деформации шпал и разработки костыльных отверстий – в подкладках в 2,3 раза больше увеличения ширины колеи из-за бокового износа рельсов.
Таблица 4.22 звено | 02.10.82 | 27.03.83 | ||||||
во» | 8, | щ, | ЛТ, | |||||
мм | мм | мм | мм | мм | мм | мм | мм | |
1 | 1535,0 | 1,0 | 1540,7 | 4,0 | 5,7 | 3,0 | ||
2 | 1534,3 | 1,5 | 1540,5 | 4,4 | 6,2 | 2,9 | ||
3 | 1535,3 | 1,0 | 1541,7 | 4,5 | 6,4 | 3,5 | 51,298 | 0,058 |
4 | 1535,5 | 1,0 | 1541,0 | 4,0 | 5,5 | 3,0 | ||
5 | 1534,7 | 1,5 | 1540,0 | 4,6 | 5,3 | 3,1 | ||
6 | 1535,0 | 1,0 | 1540,3 | 4,1 | 5,3 | 3,1 | ||
7 | 1537,3 | 1,0 | 1542,8 | 3,6 | 5,5 | 2,6 |
Среднее приращение ширины колеи А!? =5,7 мм, среднее приращение бокового износа А/г^ =3,0 мм. В этом цикле наблюдений по причине износа рельсов ширина колеи увеличилась на 3 мм, из-за деформации шпал и разработки костыльных отверстой; на 2,7 мм.
Таким образом, при большей начальной ширине колеи (в среднем 1535,2 мм по сравнению с 1521.7 мм в первом цикле наблюдений) общее увеличение ширины колеи уменьшилось на 40%, из-за деформации шпал и подкладок увеличение ширины колеи уменьшилось в 2,4 раза, интенсивность бокового износа рельсов уменьшилось в 1,36 раза (или на 36%).
Аналогичные наблюдения за износом рельсов и шириной колеи приведены в таблице 4.23 .Данные наблюдений относятся к кривой N 8, расположенной на спуске четного пути. Характеристика пути: радиус кривой – 302м, длина круговой кривой – 70м, продольный уклон пути – 14,8-
17,9°/00..
звено | 05.04.81 | 03.07.81 | ||||||
8, | 8, | ДГ, | Ъ’д | |||||
мм | мм | мм | мм | мм | мм | млн.т | мм/млн.т | |
5 | 1512,2 | 0,8 | 1521,7 | 3,5 | 9,5 | 2,7 | ||
6 | 1517 | 0,7 | 1526,7 | ЗД | 9,7 | 2,4 | 25,034 | 0,101 |
7 | 1510,3 | 0,5 | 1571,8 | 3,0 | 7,5 | 2,5 |
Средняя ширина колеи на звеньях 5-7 в момент начала наблюдений равна 1513,2 мм при среднем боковом износе 0,67 мм. В период с 05.04 по 03.07.81 ширина колеи увеличилась в среднем на 8,9 мм при увеличении бокового износа в среднем на 2,53 мм Т.е. увеличение ширины колеи за счет деформаций шпал и подкладок превышало боковой износ рельсов в 2,56 раза.
Второй цикл наблюдений относится к рельсам, уложенным во время капитального ремонта пути (таблица 4.24).
звено | 30.09.81 | 29.11.81 | ||||||
$0, | 8, | ЛЯ | Ак6, | ЛГ, | к’5 | |||
мм | мм | мм | мм | мм | мм | млн.т | мм/млн.т | |
5 | 1524,2 | 1,3 | 1526,8 | 2,0 | 2,6 | 0,7 | ||
6 | 1529,2 | 1,3 | 1530,8 | 2,0 | 1,6 | 0,7 | 15,997 | 0,039 |
7 | 1530,0 | 1,1 | 1532,8 | 1,6 | 2,8 | 0,5 |
В начале наблюдений средняя ширина колеи равна 80=1527,8 мм. За первые 2 месяца эксплуатации приращение износа составило 0,63 мм в среднем. Приращение износа из-за деформаций шпал и подкладок равно 1,7 мм и в 2,7 раза больше приращения бокового износа. При начальном ширине колеи 1513,2 мм (05.04.81) за первые два месяца эксплуатации ширина колеи из-за деформаций шпал и подкладок увеличилась на 4,27 мм, что в 2,5 раза больше увеличения ширины колеи при её начальном значении 1527,8 мм. Интенсивность износа рельсов в этих двух циклах наблюдений уменьшилась с 0,101 мм/млн.т брутто до 0,039 мм/млн.т брутто, т.е. уменьшилась в 2,6 раза.
Изменение £и в кривой №1 звено | 13.07.97 | 01.11.97 | |||||||
Точ | 8, | 8, | А*, | щ | А Г, | Ь’З | |||
ки | мм | мм | мм | мм | мм | ,мм | млн.т | мм/млн. т | |
31 | 4 | 1525 | 0,4 | 1532 | 3,2 | 7,0 | 2,8 | ||
6 | 1525,5 | 0,5 | 1532,5 | 3,4 | 7,0 | 2,9 | |||
8 | 1525 | 0,5 | 1531,5 | 3,1 | 6,5 | 2,6 | 15,26 | 0,189 | |
10 | 1525,5 | 0,5 | 1530,5 | 2,7 | 5,0 | 2,2 | |||
25 | 1524,5 | 0,3 | 1530,5 | 3,3 | 6,0 | 3,0 | |||
42 | 1526 | од | 1532 | 3,6 | 6,0 | 3,5 | |||
44 | 1524 | 0,3 | 1531,5 | 3,5 | 7,5 | 3,2 | |||
32 | 4 | 1528,5 | 0,4 | 1532,5 | 2,6 | 4,0 | 2,2 | ||
6 | 1527,5 | 0,3 | 1532 | 2,9 | 4,5 | 2,6 | |||
8 | 1525 | 0,5 | 1530 | 2,9 | 5,0 | 2,4 | |||
10 | 1527,5 | 0,2 | 1531,5 | 2,3 | 4,5 | 2,1 | 15,26 | 0,157 | |
25 | 1529 | 0,7 | 1536 | 3,3 | 7,0 | 2,6 | |||
42 | 1526,5 | 0,6 | 1532 | ЗД | 5,5 | 2,5 | |||
44 | 1526,5 | 0,5 | 1532 | 2,9 | 5,5 | 2,4 |
На звене 31 в кривой радиуса 288м средняя ширина колеи после 14 дней эксплуатации пути в среднем по 25 точкам равна 1525,5 мм.
Согласно приказу МПС 6Ц от 06.03.96г ширина колеи при укладке должна быть 1535 мм (при допуске на сужение-4 мм). На звене 32 средняя ширина колеи-1527,1 мм.
Среднее приращение ширины и бокового износа рельсов для этих звеньев равны: 6,43мм и 2,88мм для звена 31;5,14мм и 2,4мм для звена 32.
Ширина колеи меньше номинального размера на звене 31 на 9,5мм, на звене 32 на 7,9мм. При одинаковой наработке тоннажа интенсивность износа на звене 31 больше интенсивности износа на звене 31 в 1,2 раза. Увеличение ширины колеи из-за деформации шпал больше приращения бокового износа в 1,23 и 1,14 раза соответственно на звеньях 31 и 32.Назовем интенсивностью увеличение ширины колеи (Уб) отношение приращения колеи А 8 к наработке тоннажа за соответствующий этому увеличению ширины колеи период времени.
Результаты наблюдений доказывают, что стремление отдалить во времени ремонтные работы по перешивке пути по причине уширения колеи уменьшением её ширины по отношению к номинальным размерам при капитальном ремонте и сплошной смене рельсов приводит к увеличению интенсивности износа рельсов и интенсивности изменения ширины колеи.
В таблице 4.27 представлены результаты наблюдений за износом рельсов и шириной колеи после капитального ремонта по четному пути на 5230-5237 км. Эти наблюдения относятся к новым во многом изменившимся условиям эксплуатации, заключающимся в смене тягового подвижного состава в связи с переводом участка Зима – Слюдянка на переменный ток (на смену локомотивам ВЛ10, ВЛ10У пришли локомотивы ВЛ85, ВЛ80 различных модификаций, ВЛ65), изменении весовых норм поездов и загруженности локомотивов, плазменном упрочнении бандажей тягового подвижного состава, увеличении объема восстановления наплавкой вагонных колес, изменением допусков на толщину гребня локомотивных колес и т.д.
№ | Км | К | Звенья | 80 | 8 | А | |
3 | 5232 | 301 | 10-12 | 1524,7 | 1531,5 | 6,8 | 3,4 |
9 | 5234 | 303 | 31-33 | 1524,5 | 1536,4 | 11,9 | 2,97 |
31 | 5237 | 346 | 18-20 | 1523,2 | 1535,7 | 12,5 | 3,75 |
Продолжение таблицы 4.27
А Т | А5 А Т | А£-А Ъ§ А Т | Щ | Период наблюдений |
16,666 | 0,343 | 0,209 | 0,206 | (04.07.-01.11)1997г 3 месяца 27 дней |
16,475 | 0,830 | 0,63 | 0,203 | (07.07.-01.11)1997г 3 месяца 24 дня |
15,585 | 0,802 | 0,561 | 0,241 | (11.07.-01.11)1997г 3 месяца 20 дней |
По данным таблицы 4.27 изменение ширины колеи, вызванное деформацией шпал, превышает боковой износ рельсов в 2-3 раза. При соблюдении установленных норм содержания рельсовой колеи можно было бы уменьшить и интенсивность бокового износа рельсов, и интенсивность накопления деформаций элементов верхнего строения пути (шпал, подкладок), и отдалить во времени перешивку пути по причине его уширения.
В таблицах 4.25-4.27 содержатся данные об износе рельсов и ширине колеи новых рельсов.
Представляет интерес проследить за интенсивностью износа рельсов и увеличения ширины колеи в промежутках между перешивками рельсов на различных этапах их эксплуатации.
В таблицах 4.28 представлены данные, относящиеся к кривой №4 (И=297м) на подъёме по четному пути.
Между 01.06.81. и 01.07.81 проведена перешивка пути. Наблюдения показывают, что при ширине колеи 1523,6 мм по сравнению с начальной шириной колеи 1536,1 мм интенсивность износа рельсов увеличилась в 1,3 раза, интенсивность увеличения ширины колеи в 3,6 раза, в т.ч. за счет деформации шпал и износа подкладок в 1,8 раза.
Средняя начальная ширина колеи после перешивки составила 1534,6 мм, среднее приращение бокового износа равно 0,58мм и среднее приращение колеи-2,12мм. Между 01.06.81. и 01.07.81 проведена перешивка пути. Данные нового цикла наблюдений приведены в таблице 4.29.
Средняя начальная ширина колеи после перешивки пути составила 1523,6мм, среднее приращение бокового износа и ширины колеи составили 1,5 и 7,5мм соответственно.
При начальной ширине колеи 1523,6мм по сравнению с начальной шириной колеи 1534,6мм интенсивность износа рельсов возросла в 1,24 раза, интенсивность увеличения ширины колеи: общая-1,7 раза, за счет деформации шпал и подкладок в 1,8 раза.
Рассмотрим изменение Р^и в кривой радиуса 536м (№10) на
спуске по четному пути. Особенностью эксплуатации рельсов в этой кривой является то, что перешивка рельсов не производилась. Результаты наблюдений в таблице 4.30.
Изменение £ и в кривой N 10Дата за | М, | А Т, | V* | к’з | ||||
мера | мм | мм | мм | мм | мм | А^ – А/г | ||
А Т | А Т | |||||||
30.09.81 | 1521,4 | 0,14 | ||||||
25.02.82 | 1525,9 | 1,98 | 4,5 | 1,84 | 38,545 | 0,117 | 0,069 | 0,048 |
04.07.82 | 1528,0 | 3,35 | 2,1 | 1,37 | 37,829 | 0,056 | 0,019 | 0,036 |
30.12.82 | 1535,2 | 5,1 | 7,2 | 1,75 | 49,275 | 0,146 | 0,111 | 0,036 |
В кривой Я = 536 м интенсивность износа на первом этапе (при 8о =1521,4мм) была в 1,33 больше интенсивности износа на втором этапе (при 8о = 1525,9м), а затем оставалась постоянной.
Во всех исследованных случаях установлена зависимость интенсивности износа рельсов и накопления остаточных деформаций в других элементах верхнего строения пути от начальной ширины колеи.
Наблюдения показывают, что для звеньевого пути на деревянных шпалах и костыльном скреплении унификация ширины колеи 1520 мм вплоть до радиуса 300м приведет к увеличению интенсивности накопления остаточных деформаций в элементах верхнего строения пути и увеличению расходов на содержание пути.
Постановка экспериментов по изучению влияния ширины колеи и возможности унифицирования её должна быть связана с изменением конструкции промежуточных скреплений на пути с деревянными шпалами, с переходом на железобетонные шпалы, а не только и не столько с изучением влияния только ширины колеи.
При всей важности вопроса влияния ширины колеи на износ рельсов, накопление остаточных деформаций в других элементах верхнего строения пути и унификации ширины колеи необходимо отметить, что периодические увеличения интенсивности износа рельсов на ВСЖД происходили после перехода на колею 1520 мм и связаны с изменившимися эксплуатационными условиями (введение тяжеловесных поездов, увеличение загруженности локомотивов, упрочнение бандажей колес локомотивов, смена вида тяги при переходе на переменный ток и др.), в то время как стремление практических работников пути уменьшить ширину колеи при капитальном ремонте и сплошных сменах рельсов с целью отдалить во времени межремонтные сроки явилось реакцией на резкое увеличение интенсивности уширения колеи вследствие изменения условий эксплуатации.
Выводы:
- Ширина колеи существенно влияет на интенсивность износа рельсов.
- При капитальном ремонте звеньевого пути на деревянных шпалах нецелесообразно укладывать рельсо-шпальную решетку с шириной колеи менее номинальных размеров, указанных в приказе МПС N 6Ц от 6 марта 1996г., т.е. при Я>350м – 1520мм, 300<Я<349 м 1530мм, при Б1<299м – 1535 мм.
- Исследование влияния ширины колеи на боковой износ рельсов и гребней колес и установления оптимальных размеров ширины колеи должно быть увязано с типом тягового подвижного состава, обращающегося на том или ином участке сети дорог, загруженностью локомотивов, скоростями движения поездов, типом верхнего строения пути, возвышением наружного рельса в кривых.
Используемая Литература
- Войцик М. Эволюция продолжается. – В «Progressive railroading, July, 1987 (Wiycik M. The evolution continues)
- Каменев H.H. Эффективное использование песка для тяги поездов. – Труды ВНИИЖТа. Вып. 366, М., 1968, 86 стр.
- Зобел Ф.Г.Р. Разработка способов повышения сцепления. – Железные дороги мира, 1976, № 6, стр. 68-77.
- Кожевников Н.Ф., Никитин Е.В. Износ рельсов на некоторых пескозаносимых участках. – В трудах ТАШИИТа «Анализ строительства дорог в условиях Средней Азии и Казахстана». Вып. 141, 1977, стр. 22-28.
- 3акиров P.C., Кожевников Н.Ф., Иванов А.В. Износ незакалённых рельсов типа Р50 на пескозаносимых участках железных дорог. – В межвуз. сб. научных трудов МИИТа. Вып. 607, 1979, стр. 27-31.
- Пб.Шлюнеггер X. Использование коэффициента сцепления. – Железные дороги мира, 1990, № 9, стр. 15-21.
- Лужнов Ю.М., Черепашенец Р.Г. Механизм действия и расход песка на увлажнённых рельсах. – В трудах МИИТа «Физико-химическая механика сцепления». Вып. 455, 1973, стр. 121-129.
- Лисунов В.Н., Бабич В.М. Особенности использования песка на локомотивах с жёсткими характеристиками. – В межвузовском сб. научных трудов ОМИИТа. «Исследование работы электрооборудования и вопросы прочности электроподвижного состава», 1979, стр. 17-21.
И9.Косиков С.И. Фрикционные свойства железнодорожных рельсов. М., «Наука», 1967, 112 стр. - Лисунов В.Н. Особенности работы пути при электрическом приложении. Железнодорожный транспорт, 1980, № 10, стр.62-64.
- Исаев И.П., Лужнов Ю.М. Проблемы сцепления колёс локомотивов с рельсами. М., «Машиностроение», 1983, 238 стр.
- Гребенюк П.Т., Первушин В.М. О сопротивлении троганию с места движению подвижного состава колеи 1067 мм – Вестник ВНИИЖТ, 1985, №8, стр. 27-31.
- Исаев И.П., Самме Г.В. Пути повышения использования силы сцепления колёс локомотивов с рельсами. – В сб. научных трудов ВЗИИТа «Вопросы повышения сцепления колёс электрических локомотивов с рельсами». Вып. 88, стр. 5-13.
- Вербек Г. Современное представление о сцеплении и его использование. – Железные дороги мира, 1974, № 4, стр. 23-53.
- A.c. № 1801827 М.кл. 5В61С15/10 Форсунка песочницы локомотива. Н.И. Горбунов, Е.В. Михайлов, А.Л. Кашура, П.И. Кудла, А.Л. Го- лубенко, В.И.Могила. 1996.
- Коротаев Б.В. Об одном способе уменьшения бокового износа рельсов и гребней колёс подвижного состава. – Тезисы докладов научно- практической конференции «Транспортные проблемы Восточной Сибири». Иркутск, 1998, с. 43.
- Порошин В.Л., Мирза А.Н. Определение геометрических параметров слоя металла, удаляемого при механической обработке головки рельсов. – Вестник ВНИИЖТ, 1983, № з, Стр. 45-48.
- Шахунянц Г.М., Никонов А.М., Смирнова М.Б., Глазкова Л.В. Экспериментальные исследования химического состава, макро- и микроструктуры и износа рельсов. – В сб. н. тр. МИИТа «Физико-химическая реакция сцепления». Вып. 445. М., 1973, стр. 130-136.
- Милованов А.И., Коротаев Б.В., Милованов A.A. О возможности уменьшения бокового износа рельсов и подреза гребней колёс за счёт внесения изменений в механическую часть транспортного средства и применения новой методики лубрикации. – Материалы межвузовской научно- технической конференции «Железнодорожный транспорт Сибири: проблемы и перспективы». Омск, 1998, с. 36.
- A.c. № 2059492 М.кл. 6В61КЗ/02 Устройство для нанесения смазки на рельсы. Чирков а.В., Зайков В.Н., Кирилов С.А. 1996.
- A.c. № 2067939 М.кл. 6В61 КЗ/02 Бортовой рельсовый лубрикатор. Шаповлов В.В., Фендриков А.И., Богданов В.М., Клим Я.Я., Щербак П.Н., Озябкин АЛ. 1996.
- A.c. № 1791233 М.кл. 5В61КЗ/02 Способ смазки реборд ходовых колёс. Серобабин Ю.А., Анисимов Г.Н.
- Дроздов Ю.Н. Состояние и перспективы развития трибологии механических систем. – В книге «Научные проблемы машиностроения».
М., « Наука», 1988, с. 102-111. - Альбрехт В.Г. Технико-экономическое сравнение различных типов железнодорожного пути. – Железные дороги мира, 1979, № 5, стр. 340.
- Ларин Т.В. Износ и пути продления срока службы бандажей железнодорожных колёс. Труды ВНИИЖТа. Вып. 165, Трансжелдориздат, 1958.
- Ларин Т.В. Об оптимальной твёрдости элементов пары трения «Колесо-рельс». – Вестник ВНИИЖТ, 1965, № 3, стр. 5-9.
- Вихрова А.М., Ларин Т.В., Парышев Ю.М., Хургин Л.С. О соотношении твёрдости рельсовой и колёсной стали. – Вестник ВНИИЖТ, 1983, №6, стр. 34-38.
- Крысанов Л.Г. На рельсовой комиссии. – Путь и путевое хозяйство, 1992, № 4, стр. 15.
- Альбрехт В.Г., Крысанов Л.Г. Факторы, определяющие сроки службы рельсов и методы продления их эксплуатации в пути. – Экспресс- информация ЦНИИТЭИ МПС «Железнодорожный транспорт». Серия «Путь и путевое хозяйство». М., 1994, вып. 2, стр. 26-45.
- Ядрошникова Г.Г. К вопросу о сроках службы рельсов по износу. – В сб. научных трудов НИИЖТа «Повышение надёжности и эффективности железнодорожного пути». Новосибирск, 1991, стр.83-86.
- Томило Э.А. Исследование контактного взаимодействия и износа цилиндрических пар качения. – Проблемы машиностроения и надёжности машин. М., 1995, № 6, стр. 48-50.
- Горский A.B., Буйносов А.П., Боярских Г.С., Лавров В.А. Бандажи и рельсы. Опыт Свердловской дороги. – Электрическая и тепловозная тяга, 1992, № 4, стр. 26-27.
- Мелентьев Л.П., Порошин В.П., Фадеев Е.И. Содержание и ремонт рельсов. М., «Транспорт», 1984, 232 стр.
- Термически упрочнённые рельсы. Под ред. д.т.н., проф. А.Ф. Золотарского. М., «Транспорт», 1976, 264 стр.
- Марков Д.П. Повышение твёрдости колёс подвижного состава. – Вестник ВНИИЖТ, 1995, № 3, стр. 10-17.
- Марков Д.П. Триботехнические свойства поверхностей колёс- но-рельсовой пары. – Вестник ВНИИЖТ, 1995, № 5, стр. 30-35.
- Марков Д.П. Закалка гребней колёс подвижного состава на высокую твёрдость для снижения бокового износа. – Вестник ВНИИЖТ, 1997, № 1, стр. 36-42.
- Марков Д.П. Трибологические аспекты повышения износостойкости и контактно-усталостной выносливости колёс подвижного состава. – Автореферат диссертации на соискание учёной степени доктора технических наук. М., 1997, 31 стр.
- Инструкция по формированию, ремонту и содержанию колёсных пар тягового подвижного состава железных дорог колеи 1520 мм № ЦТ/329, 1995 г.
- 3орин В.А. Основы долговечности строительных и дорожных машин. М., Машиностроение, 1986, 246 стр.
- Комбалов B.C. Состояние и перспективы развития методов расчёта на базе молекулярно-механической теории трения и усталостной теории износа твёрдых тел (сухое и граничное трение). – В книге «Научные проблемы машиностроения». Издательство «Наука», М., 1988, стр. 142160.
- Коротаев Б.В. Влияние веса поезда на износ рельсов в криволинейных участках пути. – Материалы межвузовской научно-технической конференции «Железнодорожный транспорт: проблемы и перспективы». Омск, 1998, с. 68-69.
- Дроздов Ю.Н., Павлов В.Г., Пучков В.Н. Трение и износ в экстремальных условиях. М., Машиностроение, 1986, 224 стр.
- Рубанов А.Д. Изобретателю о системе допусков и посадок. JL, «Лен-издат», 1983, 136 стр.
- Чичинадзе А.В., Браун Э.Д., Гинзбург А.Г., Игнатьева З.В. Тепловая динамика и моделирование трения и изнашивания в машинах, приборах и аппаратах. – В кн. «Научные проблемы машиностроения». М., «Наука», 1988, стр. 119-141.
- Чичинадзе А.В. Современные задачи внешнего трения и моделирования. – В кн: «Моделирование трения и износа». М., 1970, стр. 6-22.
- Лужнов Ю.М. Особенности трения на рельсах в зимних условиях. – В сб. н. тр. МИИТа «Физико-химическая механика сцепления». Вып. 445. М., 1973, стр.130-136.
- Г.Борзо. Преимущества смазывания поверхности контакта колесо-рельс, выбор смазок и способов их нанесения. – В «Modern railroads, September, 1986».
- Алёхин С.В., Продан Н.С. Надёжность механической части подвижного состава. М., «Транспорт», 1969,176 стр.
- Крагельский И.В. Трение и износ. М., Машгиз, 1962,383 стр.
- Боуден Ф.П., Тейбор Д. Температура поверхности трущихся тел. – В книге «Трение и граничная смазка» под ред. И.В.Крагельского. Издательство иностранной литературы. М., 1953, стр. 231-254.
- Лейн Т.Б. Температура заедания граничных смазочных плёнок. – В книге «Трение и граничная смазка». М., «Издательство иностранной литературы», 1953, стр. 265-272.
- Полякова Г.Г., Ликратов Ю.Н., Сорокин В.П., Гришина Г.Г. Об интенсивности бокового износа рельсов и бандажей колёсных пар. – В межв. сб. научных трудов «Надёжность и эффективность работы железнодорожного пути в условиях Сибири», Новосибирск, 1980, стр. 100-108.
- Скворцов О.С., Рейхарт В.А., Дьяконов В.Н. Рельсы «для зимы». – Путь и путевое хозяйство, 1992, № 3, стр. 17-18.
- Тимошенко С.П. Сопротивление материалов. М., «Наука», т.2, 480 стр.
- Кащеев В.Н. Процессы в зоне фрикционного контакта металлов. М., «Машиностроение», 1978, 214 стр.
- Гаркунов Д.Н., Поляков A.A. Повышение износостойкости деталей конструкций самолётов. М., «Машиностроение», 1974, 200 стр.
- Правила тяговых расчётов для поездной работы. М., «Транспорт», 1985, 287 стр.
- Золотарский А.Ф., Вершинский C.B., Ершков О.П., Иващенко Г.И., Шестаков В.Н., Чернышев М.А. Железнодорожный путь и подвижной состав для высоких скоростей движения. М., «транспорт», 1964.
- Яхов М.С., Ершков О.П. Унификация ширины колеи в прямых и кривых участках железнодорожного пути. Труды ВНИИЖТ, в. 192, I960, стр. 102-149.
- Вершинский C.B., Данилов В.Н., Хусидов В.Д. Динамика вагона. М.: Транспорт, 1991, 360 стр.
- Буйносов А.П., Клинский B.C. Об износе бандажей электровозов ЧС2 и ЧС7. – Железнодорожный транспорт, 1992, № 5, стр. 45-46.
- Карпущенко H.H., Николаенко A.A., Ядрошникова Г.Г., Юрчен- ко Г.Г. Влияние подуклонки и ширины колеи на износ рельсов. – Путь и путевое хозяйство, 1997, № 3, стр. 18-20.