Сейчас ваша корзина пуста!
Разработка новых скреплений для железобетонных шпал
Цикл статей:
Глава 1 – Обзор исследований, посвященных работе промежуточных рельсовых скреплений в пути с железобетонными шпалами
Глава 2 – Упругие шайбы
Глава 3 – Упругие элементы рельсовых скреплений
Глава 4 – Исследования новых типов рельсовых скреплений
Глава 5 – Разработка новых скреплений для железобетонных шпал
Нераздельное рельсовое скрепление КН-65
СГУПСом совместно с Горновским заводом «Спецжелезобетона» разработано нераздельное подкладочное рельсовое скрепление КН-65 (рис. 4.1), на которое подана совместная заявка на изобретение № 99115566 «Рельсовое скрепление для пути на железобетонном основании» с приоритетом от 13 июля 1999г.
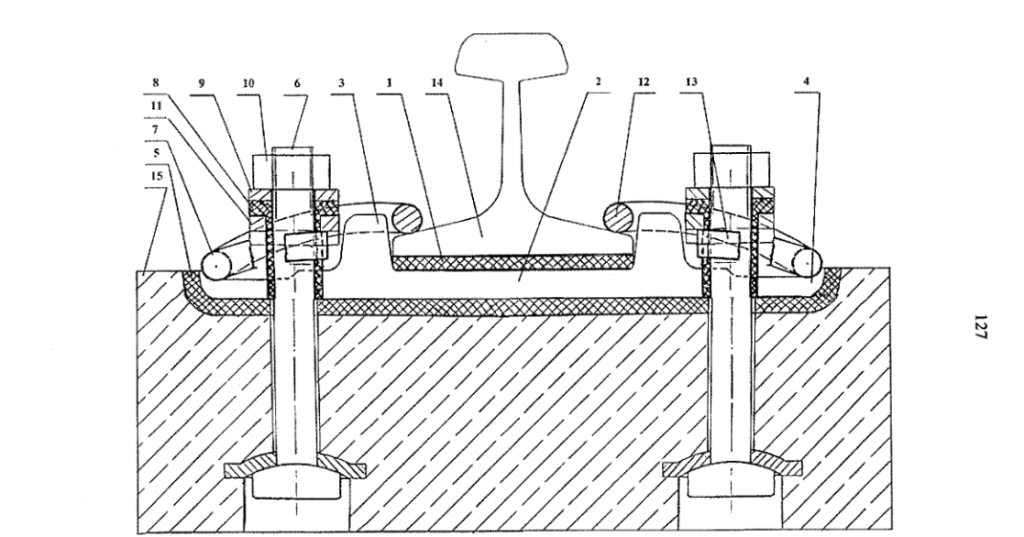
Рис 4.1 Промежуточное рельсовое скрепление КН-65
Бесподкладочное рельсовое скрепление БАРС
В связи с тем, что актуальной задачей в настоящее время является создание экономичных бесподкладочных скреплений для железобетонных шпал, которые могут найти свою сферу применения, специалистами СГУПСа и Горнов- ского завода «Спецжелезобетона» было разработано бесподкладочное скрепление БАРС (рис. 4.2), на которое подана совместная заявка на изобретение № 99119615 «Крепление рельса к Железобетонному основанию» с приоритетом от 17 Сентября 1999г.
Крепление рельса 1 к железобетонному основанию 2 содержит криволинейный анкер-болт 3, выполненный в виде скобы и жестко замоноличенный в железобетонное основание 2, пружинные клеммы 4, каждая из которых соединена с соответствующим концом анкера болта 3 через регулятор напряжения клеммы, включающей в себя шайбу 5 и гайку 6, при этом одна ветвь клеммы установлена с возможностью взаимодействия с рельсом 1, а другая – с упорной металлической подклеммной подкладкой 7, выполненной в виде криволинейной пластины, с загибом 8, для упора ветвей пружинной клеммы 4 и жестко соединенной с подклеммной частью 9 криволинейной выемки железобетонного основания 2, и приваренной к анкеру 1, при этом упорная подклеммная подкладка 7 имеет изгиб 10 в подрельсовой части 11 криволинейной выемки железобетонного основания 2, который контактирует с изолирующей прокладкой. 12, выполненной в виде уголка с фиксатором 13 и установленной между пружинной клеммой 4 и подошвой рельса 1, амортизирующую подрельсовую прокладку 14 установленную в подрельсовой части 11 криволинейной выемки железобетонного основания 2.
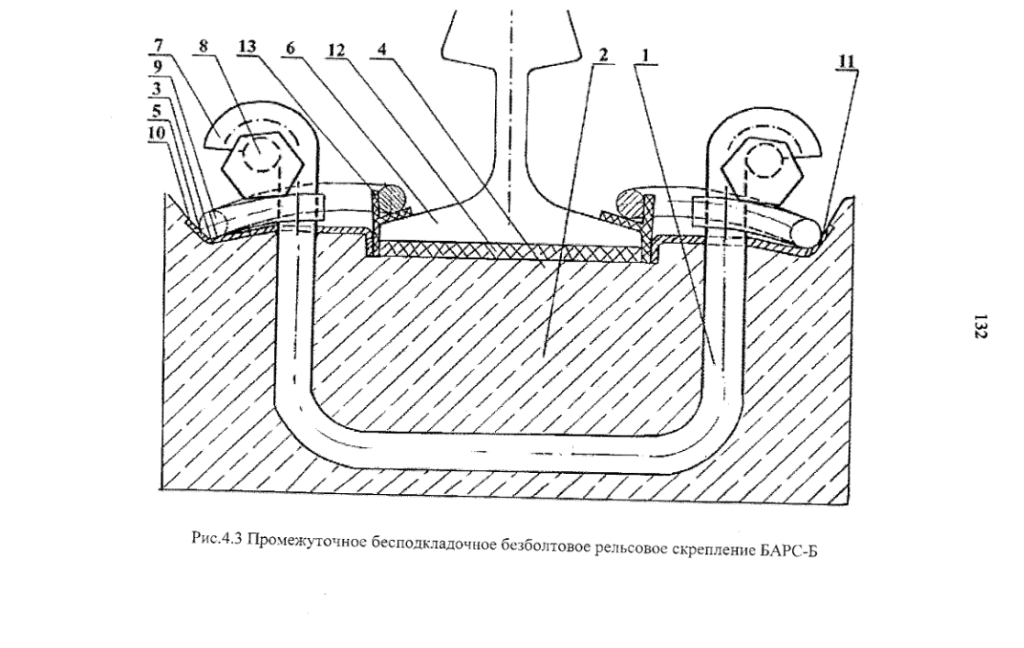
Устройство работает следующим образом:
При действии нагрузки на рельс 1 он совершает сложные пространственные перемещения, при этом его подошва воздействует на подрельсовую амортизирующую прокладку 14 и изолирующие прокладки 12, и стремиться сместиться относительно их, чему препятствуют силы трения, возникающие на поверхности контакта элементов скрепления за счет усилий, вызванных прижатием пружинных клемм 4 через шайбы 5 гайками 6 регуляторов напряжения. Усилия, передающиеся от подошвы рельса 1 на подрельсовую амортизирующую прокладку 14, стремятся выдавить ее со своего места, чему препятствуют силы трения по контакту с подрельсовой частью 11 криволинейной выемки железобетонного основания 2 и изолирующей прокладки 12, контактирующей с загибами 10 упорных подрельсовых прокладок 8. Усилия, передающиеся от подошвы рельса 1 на изолирующие прокладки 12, стремятся сместить их относительно клемм 4, чему препятствуют фиксаторы 13. Усилия, передающиеся от изолирующих прокладок 12 на пружинные клеммы 4, стремятся сместить и повернуть их относительно упорных подклеммных подкладок 7, чему препятствуют силы, передающиеся на клеммы 4 от шайб 5 и гаек 6 регуляторов напряжения и загибы 8 в этих подкладках. Усилия от упорных подклеммных подкладок 7 передаются на поверхность подклеммной части 9 криволинейной выемки в железобетонном основании 2 и на анкер 3, который препятствует неупругим смещениям этих подкладок 7 относительно железобетонного основания 2. Анкер 3 передает усилия на железобетонное основание 2 по контакту замоноли- ченной в него части своей поверхности.
Предлагаемое скрепление исключает неупругие взаимные смещения его деталей, что обеспечивает равномерную и стабильную передачу усилий от рельса на основание и повышает его эксплуатационную надежность.
Бесподкладочное безболтовое анкерное рельсовое скрепление БАРС-Б
На экспериментальном кольце ВНИИЖТа в течение продолжительного времени испытывается безболтовое анкерное скрепление АРС, разработанное МИИТом. Однако это скрепление недостаточно технологично в изготовлении, так как имеет анкер, изготавливаемый с помощью литья. Поэтому специалисты Горновского завода «Спецжелезобетона» и СГУПСа разработали более технологичное бесподкладочное безболтовое анкерное рельсовое скрепление БАРС- Б (рис. 4.3.), на которое подана совместная заявка на изобретение № 99119614 «Промежуточное рельсовое скрепление для железобетонных шпал» с приоритетом от 17 сентября 1999г.Промежуточное рельсовое скрепление для железобетонных шпал содержит криволинейный анкер 1, выполненный из двух стержней круглого поперечного сечения, жестко соединенных между собой сваркой и жестко заделанных в железобетонную шпалу 2, выполненной с криволинейной выемкой 3 в зоне скрепления, состоящей из подрельсовой части 4, выполненной на расчетную глубину, и двух подклеммных частей 5; при этом концы анкера разнесены вдоль подошвы рельса 6 и имеют крюкообразные загибы 7, охватывающие ось регулятора 8 напряжения клемм 9, при этом одна ветвь каждой клеммы установлена с возможностью взаимодействия с подошвой рельса 6, а другая – с упорной подклеммной подкладкой 10, выполненной в виде криволинейной пла
стины с загибом 11 для упора клеммы и жестко закрепленной в подклеммной части выемки 5 шпалы 2 и приваренной к анкеру 1, причем упорная подклемм- ная подкладка 10 контактирует посредством изгиба с амортизирующей подкладкой 12, установленной в подрельсовую часть 4 выемки 3 и с изолирующей подкладкой 13, между клеммой 9 и подошвой рельса 6, выполненной в виде уголка с выступом.
Устройство работает следующим образом:
При нагрузке на рельс 6 он совершает сложные пространственные перемещения, при этом его подошва воздействует на подрельсовую амортизирующую прокладку 12 и изолирующие прокладки 13, и стремиться сместиться относительно их чему препятствуют силы трения, возникающие на поверхностях контактирования элементов скрепления за счет усилий вызванных прижатием пружинных клемм 9 регуляторами напряжений 8. Усилия, передающиеся от подошвы рельса на подрельсовую амортизирующую прокладку 12, стремятся выдавить ее с места расположения. Этому препятствуют силы трения амортизирующей подрельсовой прокладки по контакту с подрельсовой частью 4 криволинейной выемки 3 в шпале 2 и загиб упорной подклеммной подкладки 10, находящейся в подрельсовой части 4 выемки 3. Усилия, передающиеся от изолирующих прокладок 13 на пружинные клеммы 9 стремятся сместить и повернуть их относительно упорных подклеммных подкладок 10, чему препятствуют силы, передающиеся на клеммы 9 от регуляторов напряжения 8 и загибы 11 в этих подкладках. Усилия от упорных подклеммных подкладок 10 передаются на поверхность подклеммной части 5 криволинейной выемки 3 в железобетонной шпале 2 и на анкер 1, который передает усилия на железобетонную шпалу 2 по контакту части своей поверхности, замоноличенной в шпалу 2.
Предлагаемое скрепление исключает поворот и заклинивание клеммы, обеспечивает более равномерную и стабильную передачу усилий от подошвы рельса на шпалу, что повышает эксплуатационную надежность скрепления, упрощает его конструкцию и повышает технологичность изготовления.
Подкладочное раздельное рельсовое скрепление КБ-65 с упругими прутковыми клеммами ОП-Ю5
В настоящее время повсеместное использование промежуточного скрепления КБ-65 с П – образными жесткими клеммами не удовлетворяет новым требованиям для ведения скоростного движения по высокой жесткости и малой упругости пути, а также по большой трудоемкости обслуживания. Поэтому специалистами СГУПС, совместно со специалистами Горновского завода «Спецжелезобетона» и «Новосибирского Стрелочного завода» проведены исследования скрепления КБ-65 с упругими клеммами ОП-Ю5 (рис 4.4).
Промежуточное раздельное рельсовое скрепление состоит из нашпальной прокладки 1, установленной на железобетонную шпалу 2. На прокладку 1 установлена подкладка 3 прикрепленная к шпале 2 при помощи двух закладных болтов 4. В качестве изолятора используют полимерную втулку 5, установленную между подкладкой 3 и закладным болтом 4. Нагрузка на втулку 5 передается от гайки 6 закладного болта 4 через двухвитковую пружинную шайбу 7 и плоскую шайбу 8. Рельс 9, через подрельсовую резиновую прокладку 10, устанавливается на подкладку 3 между ребордами 11 подкладки 3. Закрепление рельса 9 к подкладке 3 происходит при помощи упругих прутковых пружинных клемм ОП-Ю5 12, надетых на реборду 11, при этом передние концы клемм 12 упираются в рельс 9, а задние концы в подкладку 3. Нагрузка на клемму 12 передается от закладного болта 13, установленного в пазу реборды 11 подкладки 3, через шайбу 14 от гайки 15 закладного болта 13.
Бесподкладочное анкерное рельсовое скрепление ГС-1
Совместно разработанное специалистами СГУПС и Горновского завода «Спецжелезобетон» скрепление ГС-1 рис.4.5 предназначено для более надежной фиксации рельса при максимальном удешевлении производства с использованием стандартных деталей скреплений.Крепление рельса к железобетонному основанию содержит подрельсовую амортизирующую прокладку 3, расположенную в выемке основания, тонкую усилительную пластину 2, которая повторяет очертание выемки и замоноличена в ней, причем усилительная пластина 2 имеет в средней части выштампованные отгибы, замоноличенные в основание, а по краям – загибы, усилительная пластина имеет два прямоугольных отверстия, через которые проходят анкеры 1, каждый из которых выполнен в форме параллелепипеда, имеющего в нижней части выступы в форме «ласточкиного хвоста». В средней части анкера 1 находится круглое сквозное отверстие, а в верхней части расположен вырез, повторяющий очертание выступа, в который вставлена головка клеммного болта 8, на стержень которого надеты гайка 7 и прижимная шайба 6, опирающаяся на охватывающие боковые поверхности анкера 1 концы клеммы 5, выполненной из прутка круглого поперечного сечения, имеющей симметричную П- образную форму с двумя упорами в загиб усилительной пластины 2, и полкой, опирающейся на электроизолирующую прокладку 4, выполненную в виде уголка, одна полка которого расположена на верхней грани подошвы рельса, а вторая – между анкером 1 и боковой гранью подошвы рельса, причем электроизолирующая прокладка имеет фиксаторы.
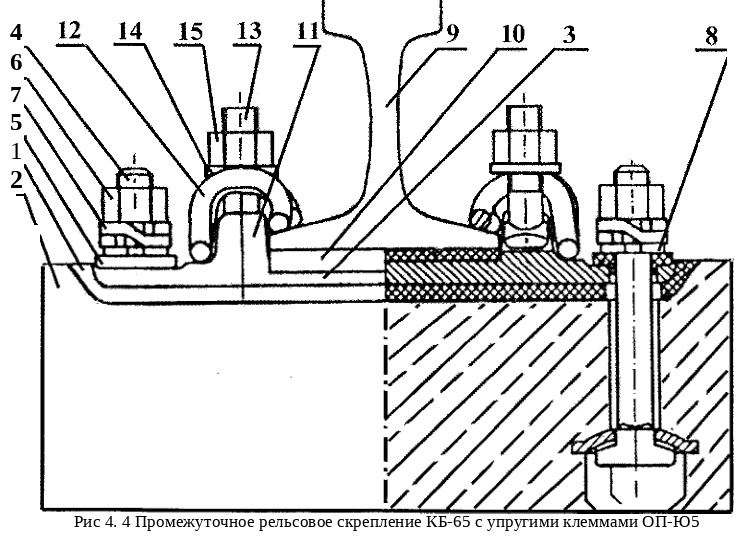
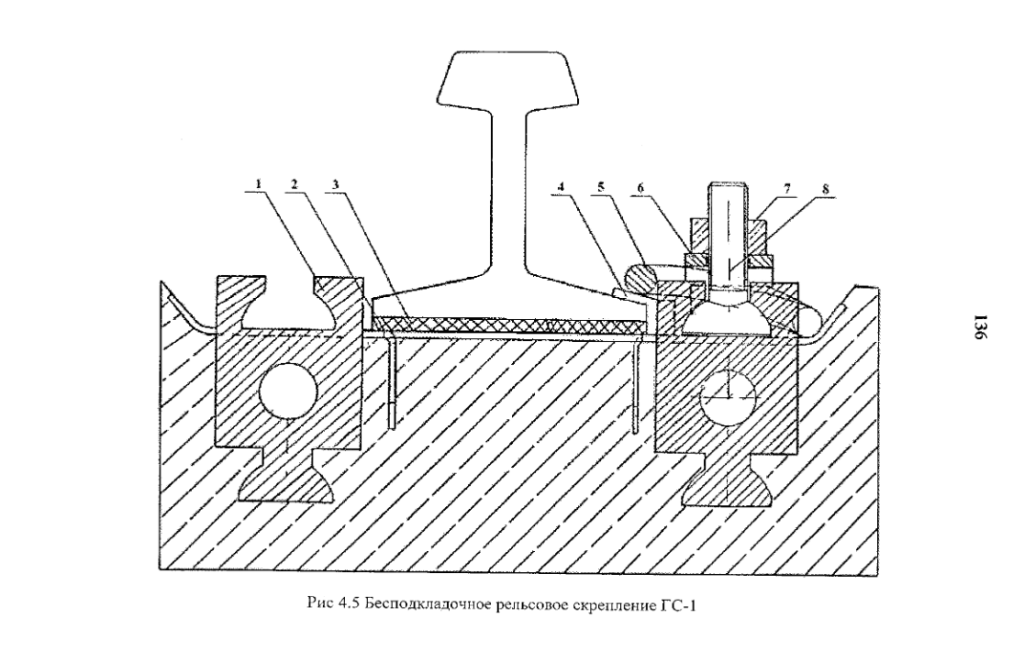
Устройство работает следующим образом:
При действии нагрузки на рельс он совершает сложные пространственные перемещения, при этом его подошва воздействует на подрельсовую амортизирующую прокладку 3 и изолирующие прокладки 4 и стремится сместиться относительно их, чему препятствуют силы трения, возникающие на поверхностях контактирования элементов крепления за счет усилий, созданных прижатием пружинных клемм 5 через прижимные шайбы 6 гайками 7.
Усилия, передающиеся от подошвы рельса на подрельсовую амортизирующую прокладку 3, стремятся выдавить ее со своего места, чему препятствуют силы трения по контакту прокладки 3 с тонкой усилительной пластиной 2, замоноличенной в основание и вертикальная полка электроизолирующей прокладки 4, контактирующей с анкером 1. Усилия, передающиеся от подошвы рельса на верхнюю полку изолирующей прокладки 4, стремятся сместить их относительно полки клеммы 5, чему препятствуют фиксаторы. Усилия, передающиеся от верхней полки изолирующих прокладок 4 на полку пружинных клемм 5 стремятся сместить и повернуть их относительно анкеров 1, чему препятствуют взаимодействующие с концами клемм 5 прижимная шайба 6 и гайка 7, надетые на клеммный болт 8 и загибы усилительной пластины. Клеммный болт 7 под действием сил, передающихся от концов клемм 5 стремится сместиться относительно анкера, чему препятствует поверхность выреза анкера 1 в форме «ласточкиного хвоста», который охватывает головку клеммного болта 8.
Усилия от головки клеммного болта 8 и усилия от вертикальной полки электроизолирующей прокладки 4 стремятся сместить анкер 1 относительно основания, чему препятствуют силы сцепления по поверхности анкера 1 и выступа в форме «ласточкиного хвоста» и по поверхности круглого отверстия, заполненного бетоном основания, а также и усилительная пластина 2, имеющая в средней части выштампованные отгибы, которая жестко соединена с анкером 1 и замоноличена по всей поверхности, контактирующей с основанием.
Предлагаемое крепление исключает возможность взаимных неупругих смещений элементов крепления и, вследствие этого, ослабление крепления, что обеспечивает равномерную и стабильную передачу усилий от рельса на основание и повышает эксплуатационную надежность крепления рельса к железобетонному основанию.
Другие типы рельсовых скреплений
В настоящее время специалистами СГУПС и Горновского завода «Спецжелезобетона» разработаны и проведены лабораторные исследования следующих типов рельсовых скреплений: подкладочного КБ-65И, и бесподкладочного ГС-2. Данные скрепления находятся в стадии патентования, поэтому рисунки и описания данных скреплений в этой работе не приводится, а результаты исследований будут описаны ниже.
Схема приложения нагрузки и метод расчета основных характеристик
Для проведения испытаний темплетов рельсовых скреплений специалистами СГУПС было разработано и изготовлено специальное устройство для размещения и жесткой фиксации в нем железобетонного (деревянного) блока с собранным узлом рельсового скрепления. Устройство жестко закрепляется на гидравлическом прессе и позволяет произвести испытания блока любого рельсового скрепления независимо от типа шпал и рельсов.
Устройство изготовлено таким образом, что угол наклона дна короба, на которое укладывается своей нижней постелью шпала, составляет 25 градусов, а с учетом того, что для всех типов шал, использующих подуклонку подошвы рельса внутрь колеи равную 1/20, угол наклона нагружающей силы относительно вертикальной оси симметрии рельса, составил 22 градуса 8 минут (22.14 градуса).
Условно принимаем плоскость нижней постели шпалы – горизонтальной и вводим следующие условные обозначения: Р – величина наклонной силы, кН; Рг – горизонтальная проекция силы Р на ось параллельную плоскости нижней постели и продольной оси шпалы, проходящая через точку приложения силы Р, кН; Рв – величина вертикальной проекции силы Р на ось перпендикулярную плоскости нижней постели шпалы и проходящую через точку приложения силы Р, кН; И1- индикатор фиксирующий горизонтальное смещение головки рельса под действием наклонной силы Р, мм; И2 – индикатор фиксирующий горизонтальное смещение подошвы рельса под действием наклонной силы Р, мм; ИЗ и И4 – индикаторы фиксирующие вертикальное смещение внутреннего и внешнего края подошвы рельса под действием силы Р, мм; Ив – величина вертикального смещения центра подошвы рельса от приложения наклонной силы Р, мм.
Схема приложения нагрузки к темплету рельсового скрепления и расстановка индикаторов приведена на рис. 4.6.
Расчет основных показателей темплетов рельсовых скреплений возможен по следующим вариантам:
- оценка угловых и жесткостных характеристик нарастающим итогом, рассчитывающихся для нагрузки от 0 до заданной;
- интервальная пошаговая оценка угловых и жесткостных характеристик, измеряющихся с определенным шагом приращения нагрузки;
- интервальная оценка жесткостных и угловых характеристик, измеряющихся для определенного диапазона нагрузки.
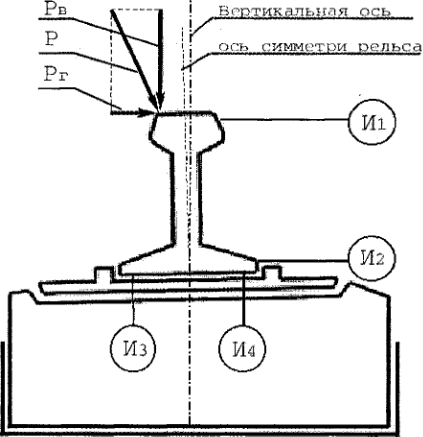
Рис. 4.6 Схема приложения нагрузки к темплету рельсового скрепления и расстановка индикаторов
В настоящее время наиболее распространенным считается третий вариант определения общей жесткости скрепления для интервала вертикальных нагрузок от 40 до 80 кН или от 20 до 80 кН. Недостатком этого варианта является условное принятие приращения перемещения точек измерения на данном интервале происходящее по линейному закону, что абсолютно не отражает действительной ситуации перемещения, происходящей по нелинейному закону.
В связи с вышеизложенным, можно утверждать, что данный способ оценки является малопригодным для отражения результатов проведенных исследований, и наиболее рациональными способами можно считать способы анализа нарастающим итогом или пошагового сравнения. При этом наиболее благоприятные условия для сравнительного анализа скреплений можно считать интервальную пошаговую оценку, которая в наименьшей степени подвержена ошибкам и неточностям при установке и сборке скреплений, особенно в начальный этап нагружения, когда происходит выбор зазоров между элементами скреплений, и позволяет более точно оценить реальное перемещение скрепления под нагрузкой.
В дальнейшем характеристики скреплений будем сравнивать по вышеприведенной интервальной пошаговой методике, а также использования в некоторых случаях измерения нарастающим итогом.
Ниже приводятся расчетные зависимости для вычисления угловых и же- сктостных характеристик методом по нарастанию нагрузки и интервальным пошаговым методом.
Угол поворота подошвы рельса относительно первоначально положения для нагрузки в интервале от 0 до п, где п – величина нагрузки Р в момент снятия показания, и меняющаяся от 10 до 100 кН с шагом 10 кН, определяется следующим выражением:
ап={и,п-Щп)/Н
где: И4п и И3п – показания индикаторов соответственно И4 и ИЗ в момент измерения перемещения при нагрузки п, мм, Н – расстояние по горизонтали между индикаторами.Интервальный угол поворота подошвы рельса относительно первоначального положения для нагрузки в интервале от п-1 до п, где п-1 – предыдущее показание индикатора, определяется следующим выражением, где: И4п.1 и И3т_1 – показания индикаторов соответственно И4 и ИЗ в момент измерения перемещения при нагрузки п-1, мм.
Принимаем для дальнейших расчетов и испытаний рельс типа Р-65.
Проведя предварительный просмотр и оценку результатов испытаний пришли к следующему выводу:
- при использовании общих показателей от 0 до п, наиболее точно можно оценить угол поворота подошвы рельса относительно первоначального положения и жесткость рельса на кручение, так как оценить эту жесткость поинтер- вально практически невозможно;
- при использовании интервальных пошаговых показателей, как наиболее точного метода, оценивается угол поворота рельса относительно первоначального положения, горизонтальная жесткость по головке и подошве рельса и вертикальная жесткость по подошве рельса;
- при использовании жесткого интервала (диапазон наклонной силы от 40 до 90 кН, при этом вертикальная нагрузка составит 36.25 – 81.57 кН, а горизонтальная – 16.90 – 38.04 кН, что приблизительно соответствует диапазону нагрузок от 40 до 80 кН, приведенным в литературе), оценивается угол поворота, жесткости на кручение, а так же горизонтальная жесткость по головке и подошве рельса и вертикальная жесткость по подошве рельса.
По большинству данных показателей ниже будут оценены скрепления приведенные в пунктах 4.3.1.- 4.3.5 данной работы.
4.5. Статические испытания под действием наклонной силы темплетов новых типов рельсовых скреплений
4.5.1. Сравнительные исследования подкладочных рельсовых скреплений: Д-0, КБ-65, КБ-65и, КБ-650П, КН-65 и КН-65у
Для возможности сопоставления результатов исследований новых типов рельсовых скреплений, первоначально были испытаны узлы скреплений КБ-65 (рис 4.7) и Д-0, а результаты данных испытаний принимались как эталонные для дальнейшего сравнения и оценки скреплений.
Испытания проводились в соответствии с пунктом 4.1.2.9 данной работы. Величина наклонной силы изменялась от 0 до 100 кН. Угол наклона прилагаемой силы относительно оси перпендикулярной нижней подошве шпалы, составил 25 градусов, при этом вертикальная составляющая от наклонной силы ЮОкН равнялась 90.63 кН, а горизонтальная – 42,26 кН, что сопоставимо с максимальными значениями в кривой от действия подвижного состава.
В качестве экспериментальных образцов были исследованы следующие типы подкладочных промежуточных рельсовых скреплений: КБ-65и, КБ-650П (рис. 4.8), КН-65 (рис. 4.9) и КН-65у.
Результаты измерений перемещений головки и подошвы темплетов рельсовых скреплений Д-0, КБ-65, КБ-65и, КБ-650П, КН-65 и КН-65у, а также рассчитанные по нарастающей о 0 до 100 кН угол поворота подошвы рельса и жесткость на кручение, последовательно поинтервально рассчитанные угол поворота рельса, горизонтальная жесткость по головке и подошве рельса и вертикальная жесткость по подошве рельса приведены в табл. 4.2 – 4.7.
Для сравнения всех вышеперечисленных типов рельсовых скреплений приведены следующие диаграммы.
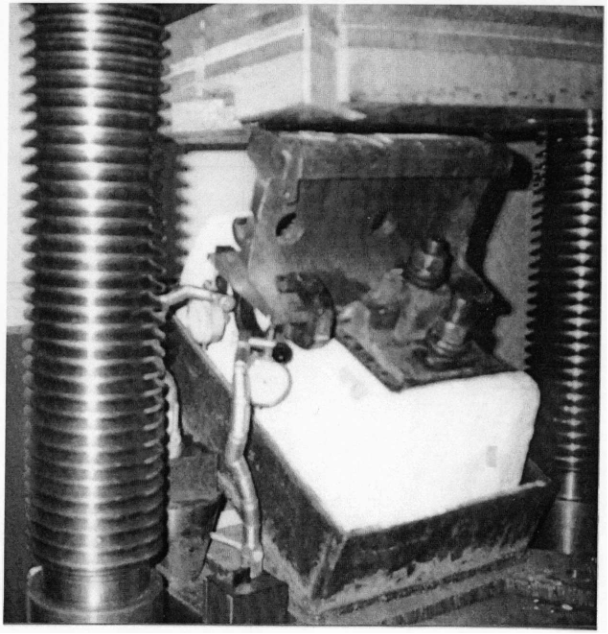
Рис 4.7 Статические испытания на наклонную нагрузку рельсового скрепления КБ-65
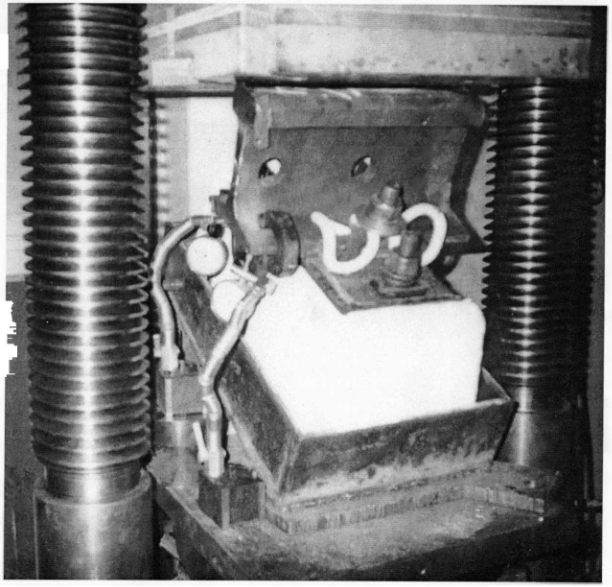
Рис 4.8 Статические испытания на наклонную нагрузку рельсового скрепления КБ-650П
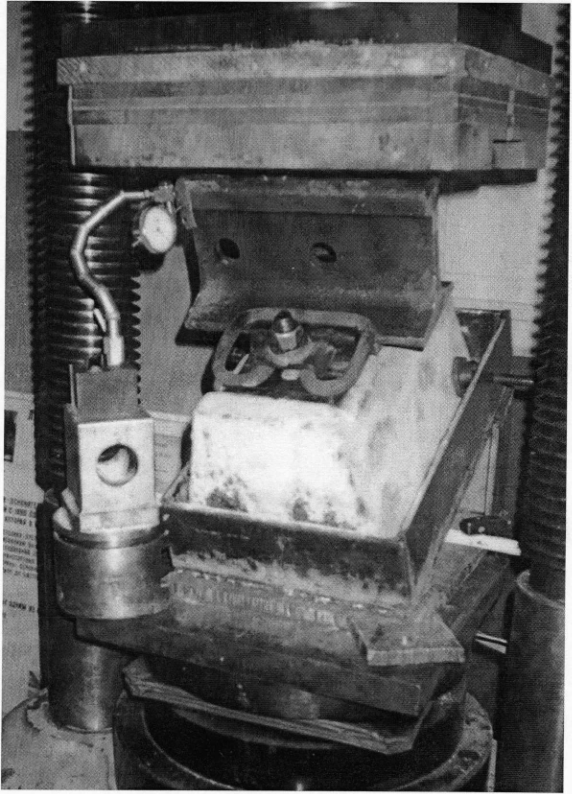
Рис 4.9 Статические испытания на наклонную нагрузку рельсового скрепления КН-65
Нагрузка, кН | Показания индикаторов, мм | Общие показатели | Интервальные показатели | ||||||||||
угол поворота, радиан 10″3 | жесткость на кручение кН*м рад | угол поворота, 5радиан 10″3 | Жесткость | ||||||||||
Р | Рг | Рв | т | И2 | ИЗ | И4 | Ив | гор. гол., кН/мм | гор. под., кН/мм | верт. под., кН/мм | |||
0 | 0.00 | 0.00 | 0.00 | 0.00 | 0.00 | 0.00 | 0.00 | 0.000 | 0.00 | 0.000 | 0.00 | 0.00 | 0.00 |
10 | 4.23 | 9.06 | 1.43 | 0.62 | 0.26 | 1.29 | 0.78 | 7.923 | 29.79 | 7.923 | 2.96 | 6.82 | 11.69 |
20 | 8.45 | 18.13 | 3.02 | 1.64 | 0.64 | 1.94 | 1.29 | 10.000 | 47.20 | 2.077 | 2.66 | 4.14 | 17.60 |
30 | 12.68 | 27.19 | 3.55 | 2.09 | 1.06 | 2.46 | 1.76 | 10.769 | 65.75 | 0.769 | 7.97 | 9.39 | 19.28 |
40 | 16.90 | 36.25 | 3.98 | 2.42 | 1.31 | 2.78 | 2.05 | 11.307 | 83.49 | 0.538 | 9.83 | 12.81 | 31.80 |
50 | 21.13 | 45.32 | 4.35 | 2.72 | 1.56 | 3.06 | 2.31 | 11.538 | 102.27 | 0.231 | 11.42 | 14.09 | 34.20 |
60 | 25.36 | 54.38 | 4.67 | 2.96 | 1.80 | 3.34 | 2.57 | 11.846 | 119.54 | 0.308 | 13.21 | 17.61 | 34.86 |
70 | 29.58 | 63.44 | 4.92 | 3.15 | 2.03 | 3.61 | 2.82 | 12.153 | 135.93 | 0.308 | 16.90 | 22.24 | 36.25 |
80 | 33.81 | 72.50 | 5.18 | 3.36 | 2.25 | 3.84 | 3.05 | 12.230 | 154.37 | 0.077 | 16.25 | 20.12 | 40.28 |
90 | 38.04 | 81.57 | 5.38 | 3.51 | 2.41 | 4.02 | 3.22 | 12.384 | 171.51 | 0.154 | 21.13 | 28.17 | 53.31 |
100 | 42.26 | 90.63 | 5.63 | 3.71 | 2.65 | 4.30 | 3.48 | 12.692 | 185.95 | 0.308 | 16.90 | 21.13 | 34.86 |
Нагрузка, кН | Показания индикаторов, мм | Общие показатели | Интервальные показатели | ||||||||||
угол поворота радиан* 10″ | жесткость на кручение кН*м рад | угол поворота, радиан 10″ | Жесткость | ||||||||||
Р | Рг | Рв | И1 | И2 | ИЗ | И4 | Ив | гор. гол., кН/мм | гор. под., кН/мм | верт. под., кН/ мм | |||
0 | 0.00 | 0.00 | 0.00 | 0.00 | 0.01 | 0.00 | 0.01 | 0.000 | 0.00 | 0.000 | 0.00 | 0.00 | 0.00 |
10 | 4.23 | 9.06 | 0.55 | 0.33 | -0.10 | 0.16 | 0.03 | 2.000 | 118.00 | 2.077 | 7.68 | 12.81 | 362.52 |
20 | 8.45 | 18.13 | 1.97 | 1.49 | -0.27 | 0.56 | 0.15 | 6.385 | 73.93 | 4.385 | 2.98 | 3.64 | 78.81 |
30 | 12.68 | 27.19 | 2.57 | 1.88 | 0.07 | 1.08 | 0.58 | 7.769 | 91.13 | 1.385 | 7.04 | 10.84 | 21.08 |
40 | 16.90 | 36.25 | 3.03 | 2.16 | 0.27 | 1.41 | 0.84 | 8.769 | 107.65 | 1.000 | 9.19 | 15.09 | 34.20 |
50 | 21.13 | 45.32 | 3.42 | 2.39 | 0.46 | 1.65 | 1.06 | 9.154 | 128.91 | 0.385 | 10.84 | 18.37 | 42.15 |
60 | 25.36 | 54.38 | 3.73 | 2.59 | 0.65 | 1.86 | 1.26 | 9.307 | 152.14 | 0.154 | 13.63 | 21.13 | 45.32 |
70 | 29.58 | 63.44 | 4.01 | 2.80 | 0.79 | 2.01 | 1.40 | 9.384 | 176.04 | 0.077 | 15.09 | 20.12 | 62.50 |
80 | 33.81 | 72.50 | 4.24 | 2.98 | 0.94 | 2.13 | 1.54 | 9.154 | 206.26 | -0.231 | 18.37 | 23.48 | 67.13 |
90 | 38.04 | 81.57 | 4.49 | 3.24 | 1.06 | 2.24 | 1.65 | 9.077 | 234.01 | -0.077 | 16.90 | 16.25 | 78.81 |
100 | 42.26 | 90.63 | 4.76 | 3.44 | 1.15 | 2.31 | 1.73 | 8.923 | 264.49 | -0.154 | 15.65 | 21.13 | 113.29 |
Расчет: угла поворота, вертикальной
Горизонтальное перемещение головки рельса для максимального значения наклонной силы 100 кН выглядело следующим образом: наибольшее перемещение головки рельса показало скрепление КН-65у, превысив показатель скрепления КБ-65 на 28%, скрепление Д-0 показало превышение на 18%, далее с превышением всего на 5 % следовало скрепление КБ-65И. Показатели скрепления КН-65 соответствовали КБ-65, а перемещение головки рельса скрепления КБ-650П показало всего 61% от величины КБ-65.
Горизонтальное перемещение головки рельса в интервале наклонных нагрузок 40-90 кН составило: превышение по сравнению с КБ-65 на 29% у скрепления КН-65у; примерно близкими к КБ-65 скрепления Д-0 и КН-65 показав соответственно на 4 и 6 % меньшую величину; скрепление КБ-650П на 22 % меньшую величину и на 40 % меньшую величину показало скрепление КБ-65И.
Горизонтальное перемещение подошвы при величине наклонной нагрузки 100 кН. Максимальное значение показало скрепление КН-65у, превысив показатель КБ-65 на 44%, далее следовало скрепление КБ-65И с превышением на 21%, Д-0 оказало результат на 8 % больше чем КБ, а КН-65 на 5 % меньше чем у КБ. Наименьший результат показало скрепление КБ-650П со значением на 45% меньше чем у КБ-65.
Горизонтальное перемещение подошвы рельса в интервале наклонной силы 40-90 кН: максимальное значение показало скрепление КН-65у, превысившее показатель КБ на 72%, далее КН-65 с 28% превышением; скрепление Д-0 показало результат равный КБ, и примерно равные результаты показали скрепления КБ-65и и КБ-650П на 17-19 % ниже, чем у КБ.
Вертикальное перемещение центра подошвы рельса при величине наклонной нагрузки 100 кН: максимальное перемещение показало скрепление Д-0, показав в 2 раза большее перемещение, чем КБ-65; на 75% большее перемещение показало скрепление КБ-65и; скрепление КН-65 показало на результат на 22% большие, КН-65у на 11% меньше, а КБ-650П показало результат равный КБ-65.
Вертикальное перемещение центра подошвы рельса в интервале наклонной силы 40-90 кН: скрепления Д-0 и КБ-65и показали результат на соответственно на 44 и 26 % больше, чем КБ-65, а КН-65, КБ-650П и КН-65у соответственно на 6, 12 и 29% меньше, чем у КБ-65.
Далее проводим анализ жесткостных характеристик и углов поворота.
Результаты расчетов угла поворота показаны на графике (прил. 2 рис. 4). Увеличение угла поворота растет не линейно. Основные изменения угла поворота подошвы рельса относительно первоначального положения происходят при нагружении темплета скрепления наклонной силой до 30-40 кН, а при дальнейшем увеличении нагрузки угол поворота практически не изменяется или его изменения незначительны, и происходят по линейному закону не превышая суммарной величины 10″3 радиана.
Для наклонной нагрузки в 100 кН максимальный угол поворота подошвы рельса относительно первоначального положения показало скрепление Д-0, превысив угол поворота КБ-65 на 42%, далее довольно близко по характеристике к КБ-65 показало скрепление КН-65у, превысив всего на 11%, несколько меньший угол поворота, с превышением на 21%, показало скрепление КН-65, а минимальные углы поворота показали скрепления КБ-65И и КБ-65ОП, составив всего 37%) от угла поворота подошвы рельса у КБ-65.
Жесткость на кручение при величине наклонной нагрузки 100 кН: для скреплений КБ-65и и КБ-650П оказалась в 2.7 раза выше, чем у КБ-65, у КН-65 на 25% выше, а у Д-0 и КН-65у соответственно на 30 и 11 % меньше показателя КБ-65.
Горизонтальная жесткость по головке рельса при величине наклонной нагрузки 100 кН: для скрепления КБ-650П оказалась на 60% выше, чем у КБ-65, скрепления КН-65 и КБ-65и показали жесткость равную КБ-65, а Д-0 и КН-65у соответственно на 15 и 22% меньшую, чем КБ-65.
При поинтервальном исследовании горизонтальной жесткости по головке рельса наибольшую величину показало скрепление КБ-65И, несколько меньшую КБ-65 ОП, приблизительно равной скреплению КБ показали Д-0 и КН65, а наименьшую величину показало скрепление КН-65у.
Горизонтальная жесткость по подошве при величине наклонной силы 100 кН у скрепление КБ-650П составила величину на 81% большую, чем у КБ-65, у скреплений Д-0, КН-65 и КБ-65И величина жесткости составила соответственно на 8 и 17%) большую, а у КН-65у на 51% меньшую, чем у КБ-65.
При интервальном пошаговом рассмотрении горизонтальной жесткости по подошве рельса, (прил.2 рис. 6) можно выделить некоторое повышение жесткости по сравнению с КБ-65 и Д-0 у скреплений КБ-65И и КБ-650П и несколько меньшую жесткость у скрепления КН-65у. Такая же картина получилась при рассмотрении интервала наклонной силы 40-90 кН.
Вертикальная жесткость по подошве рельса при величине наклонной силы 100 кН для скрепления КН-65у составила величина на 13% превышающая жесткость КБ, КБ-650П показало жесткость примерно равную КБ-65, а скрепления КН-65, КБ-65И и Д-0 показали жесткость на 18, 43 и 50% меньшую, чем КБ.
При рассмотрении интервальной пошаговой вертикальной жесткость по подошве рельса (прил. 2 рис. 7), несколько большую, чем у КБ-65 жесткость показали скрепления КН-65 и КБ-650П, равную КБ скрепление КН-65 и несколько меньшую КБ-65И и КН-65у.
4.5.2. Сравнительные исследования бесподкладочных рельсовых скреплений: БАРС, БАРС-Б, ГС-1, ГС-2 и скреплений Д-0 и КБ-65
Для возможности сопоставления результатов исследований новых типов рельсовых скреплений, первоначально были испытаны узлы скреплений КБ-65 и Д-0, а результаты данных испытаний принимались как эталонные для дальнейшего сравнения и оценки скреплений.
Испытания проводились в соответствии с пунктом 4.1.2.9 данной работы. Величина наклонной силы изменялась от 0 до 100 кН. Угол наклона прилагаемой силы относительно оси перпендикулярной нижней подошве шпалы, составил 25 градусов, при этом вертикальная составляющая от величины наклонной силы 100 кН равнялась 90.63 кН, а горизонтальная – 42,26 кН, что сопоставимо с максимальными значениями в кривой от действия подвижного состава.
В качестве экспериментальных образцов были исследованы следующие типы бесподкладочных рельсовых скреплений: БАРС (рис.4.10), БАРС-Б (рис.4.11), ГС-1, ГС-2.
Результаты измерений перемещений головки и подошвы темплетов рельсовых скреплений БАРС, БАРС-Б, ГС-1, ГС-2, а также рассчитанные по нарастающей о 0 до 100 кН угол поворота подошвы рельса и жесткость на кручение, последовательно поинтервально рассчитанные угол поворота рельса, горизонтальная жесткость по головке и подошве рельса и вертикальная жесткость по подошве рельса приведены в табл. 4.8 – 4.11.
Для сравнения всех вышеперечисленных типов рельсовых скреплений приведены следующие диаграммы:
– горизонтальное перемещение головки рельса под действием наклонной силы прил. 2 рис. 8;
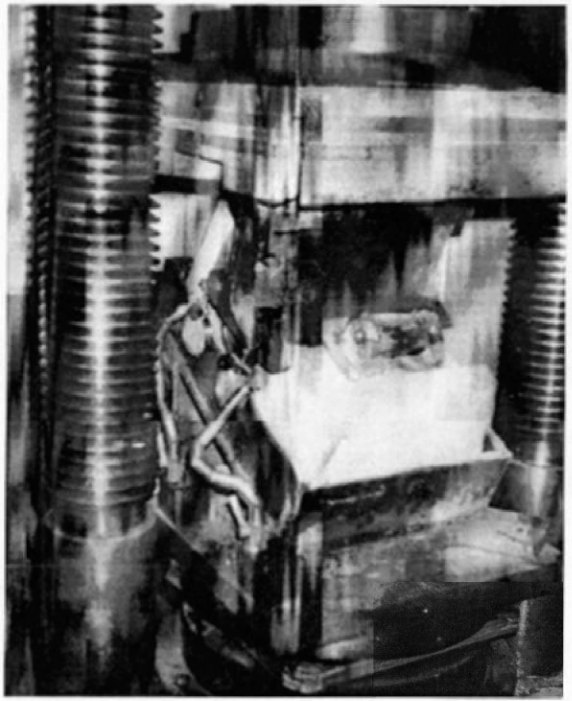
Рис 4.11 Статические испытания на наклонную нагрузку анкерного безболтового рельсового скрепления БАРС-Б
Нагрузка, кН | Показания индикаторов, мм | Общие показатели | Интервальные показатели | ||||||||||
угол поворота, 5радиан 10* | жесткость на кручение кН*м/ рад | угол поворота, радиан* 10″3 | Жесткость | ||||||||||
Р | Рг | Рв | т | И2 | ИЗ | И4 | Ив | гор. гол., кН/мм | гор. под., кН/ мм | верт. под., кН/ мм | |||
0 | 0.00 | 0.00 | 0.00 | 0.00 | 0.00 | 0.00 | 0.00 | 0.000 | 0.00 | 0.000 | 0.00 | 0.00 | 0.00 |
10 | 4.23 | 9.06 | 0.60 | 0.38 | -0.26 | -0.01 | -0.14 | 1.923 | 122.72 | 1.923 | 7.04 | 11.12 | -67.13 |
20 | 8.45 | 18.13 | 1.21 | 0.43 | -0.24 | 0.33 | 0.05 | 4.385 | 107.65 | 2.462 | 6.93 | 84.52 | 50.35 |
30 | 12.68 | 27.19 | 1.53 | 0.46 | 0.07 | 0.77 | 0.42 | 5.385 | 131.49 | 1.000 | 13.21 | 140.87 | 24.17 |
40 | 16.90 | 36.25 | 1.84 | 0.60 | 0.32 | 1.05 | 0.69 | 5.615 | 168.11 | 0.231 | 13.63 | 30.19 | 34.20 |
50 | 21.13 | 45.32 | 2.27 | 0.99 | 0.56 | 1.21 | 0.89 | 5.000 | 236.00 | -0.615 | 9.83 | 10.84 | 45.32 |
60 | 25.36 | 54.38 | 2.62 | 1.36 | 0.83 | 1.33 | 1.08 | 3.846 | 368.16 | -1.154 | 12.07 | 11.42 | 46.48 |
70 | 29.58 | 63.44 | 2.88 | 1.64 | 1.04 | 1.40 | 1.22 | 2.769 | 596.56 | -1.077 | 16.25 | 15.09 | 64.74 |
80 | 33.81 | 72.50 | 3.08 | 1.86 | 1.22 | 1.46 | 1.34 | 1.846 | 1022.67 | -0.923 | 21.13 | 19.21 | 75.53 |
90 | 38.04 | 81.57 | 3.25 | 2.05 | 1.39 | 1.52 | 1.46 | 1.000 | 2124.00 | -0.846 | 24.86 | 22.24 | 78.81 |
100 | 42.26 | 90.63 | 3.41 | 2.23 | 1.54 | 1.58 | 1.56 | 0.308 | 7670.00 | -0.692 | 26.41 | 23.48 | 86.31 |
Результаты статических испытаний темплета скрепления ГС-2. Расчет: угла поворота, вертикальной жесткости по головке, горизонтальной жесткости по головке и подошве рельса и жесткость на кручение.
горизонтальное перемещение подошвы рельса под действием наклонной силы прил. 2 рис. 9;вертикальное перемещение центра подошвы рельса под действием наклонной силы прил. 2 рис. 10;полный угол поворота подошвы рельса относительно первоначального положения под действием наклонной силы прил. 2 рис. 11;интервальная горизонтальная жесткость по головке рельса от действия наклонной силы прил. 2 рис. 12;интервальная горизонтальная жесткость по подошве рельса от действия наклонной силы прил. 2 рис. 13;интервальная вертикальная жесткость по подошве рельса от действия наклонной силы прил. 2 рис. 14.Горизонтальное перемещение головки рельса для максимального значения наклонной силы 100 кН выглядело следующим образом: наибольшее перемещение головки рельса показало скрепление БАРС-Б, превысив показатель скрепления КБ-65 на 56%, скрепление Д-0 показало превышение на 18%, далее с превышением всего на 13 % следовало скрепление ГС-1. Показатели скрепления ГС-2уступали на 7% КБ-65, а перемещение головки рельса скрепления БАРС показало всего 71% от величины КБ-65.
Горизонтальное перемещение головки рельса в интервале наклонных нагрузок 40-90 кН составило: превышение по сравнению с КБ-65 на 72% у скрепления БАРС-Б; примерно близкими к КБ-65 скрепления Д-0 и БАРС, показав соответственно на 4 и 3% меньшую величину; скрепление ГС-1 на 24 % меньшую величину и на 49 % меньшую величину показало скрепление ГС-2.
Горизонтальное перемещение подошвы при величине наклонной нагрузки 100 кН. Максимальное значение показало скрепление БАРС-Б, превысив показатель КБ-65 на 40%, Д-0 показало результат на 8 % больше, чем КБ-65, а ГС-1 равный КБ. Наименьший результат показали скрепления ГС-1 и БАРС со значениями соответственно на 29 и 35% меньше, чем у КБ-65.
Горизонтальное перемещение подошвы рельса в интервале наклонной силы 40-90 кН: максимальное значение показало скрепление БАРС-Б, превысившее показатель КБ на 114%, далее БАРС с 34% превышением; скрепление Д-0 показало результат равный КБ, а скрепления ГС-1 и ГС-2 на 28 и 51% ниже, чем у КБ.
Вертикальное перемещение центра подошвы рельса при величине наклонной нагрузки 100 кН: максимальное перемещение показало скрепление Д-0, показав в 2 раза большее перемещение, чем КБ-65; на 19% большее перемещение показало скрепление ГС-1; скрепление БАРС-Б показало результат на 4% большие, БАРС на 10%) меньше, а ГС-2 показало результат равный КБ-65.
Вертикальное перемещение центра подошвы рельса в интервале наклонной силы 40-90 кН: скрепление Д-0 показало результат на 44% больше, чем КБ- 65, а БАРС, ЮАРС-Б, ГС-2 и ГС-1 соответственно на 5, 7 36 и 37% меньше, чем у КБ-65.
Далее проводим анализ жесткостных характеристик и углов поворота.
Результаты расчетов угла поворота показаны на графике (прил. 2 рис. 11). Увеличение угла поворота растет не линейно. Основные изменения угла поворота подошвы рельса относительно первоначального положения происходят при нагружении темплета скрепления наклонной силой до 30-40 кН, а при дальнейшем увеличении нагрузки угол поворота практически не изменяется или его изменения незначительны, и происходят по линейному закону не превышая суммарной величины 2*10″ радиана.
Исключением является скрепление БАРС, у которого при нагрузке более 40 кН угол поворота подошвы рельса стал уменьшаться и уже при нагрузке в 100 кН угол достиг практически первоначальной величины.
Для наклонной нагрузки в 100 кН максимальный угол поворота подошвы рельса относительно первоначального положения показали скрепления Д-0 и ГС-2, превысив угол поворота КБ-65 на 42 и 48%, далее по характеристикам следовало скрепление БАРС-Б, превысив на 11%, а минимальный угол поворота показало скрепление БАРС, из-за обратного поворота подошвы после нагрузки 40 кН, составив всего 3% от угла поворота подошвы рельса у КБ-65.
Жесткость на кручение при величине наклонной нагрузки 100 кН: для скреплений Д-0, БАРС-Б, ГС-1 и ГС-2 соответственно на 30, 16, 22 и 11 % меньше показателя КБ-65.
Горизонтальная жесткость по головке рельса при величине наклонной нагрузки 100 кН: для скрепления БАРС оказалась на 40% выше, чем у КБ-65, скрепление ГС-1 показало жесткость на 7% больше КБ-65, а Д-0 и ГС-2 и БАРС-Б соответственно на 15, 12 и 35% меньшую, чем КБ-65.
При поинтервальном исследовании горизонтальной жесткости по головке рельса наибольшую величину показало скрепление ГС-2, несколько меньшую ГС-1, приблизительно равной скреплению КБ показали Д-0 и БАРС, а наименьшую величину показало скрепление БАРС-Б.
Горизонтальная жесткость по подошве рельса при величине наклонной силы 100 кН у скреплений БАРС и ГС-1 составила соответственно величину на 54 и 40% большую, чем у КБ-65, у скреплений Д-0, БАРС-Б величина жесткости составила соответственно на 8 и 28% большую, а у ГС-1, равную КБ-65.
При интервальном пошаговом рассмотрении горизонтальной жесткости по подошве рельса (прил. 2 рис. 13) можно выделить некоторое повышение жесткости по сравнению с КБ-65 и Д-0 у скрепления ГС-1, сильное повышение у ГС-2 и несколько меньшую жесткость у скреплений БАРС и БАРС-Б.
Вертикальная жесткость по подошве рельса при величине наклонной силы 100 кН для скрепления БАРС составила величина на 11% превышающая жесткость КБ-65, ГС-2 показало жесткость равную КБ-65, а скрепления БАРС-Б, ГС-1 и Д-0 показали жесткость на 4, 16 и 50% меньшую, чем КБ.
При рассмотрении интервальной пошаговой вертикальной жесткости по подошве рельса (прил. 2 рис. 14), несколько большую, чем у КБ-65 жесткость показали скрепления ГС-1, ГС-2 и БАРС-Б, равную КБ, а скрепление БАРС несколько меньшую Д-0.
Статические испытания рельсовых скреплений на продольный сдвиг
При исследовании новых типов рельсовых скреплений одной из важнейших задач, кроме определения жесткостных характеристик, является определение сопротивления рельсового скрепления от угона пути, то есть определение удерживающей способности скрепления на продольный сдвиг вдоль оси рельса.
Для определения вышеприведенных характеристик скреплений на Горнов- ском заводе «Спецжелезобетона» была сконструирована и изготовлена специальная установка (рис. 4.12), позволяющая проводить испытания на продольный сдвиг рельсовой рубки закрепленной на одной, двух или на трех шпалах одновременно, имеющих жесткое крепление к основанию.
Испытаниям подверглись скрепления КБ-65, КН-65 и КН-65у, с различными вариантами затяжки клеммных болтов. По техническим причинам произвести испытания других типов рельсовых скреплений на данной установке не удалось.Рельсовые скрепления, предназначенные для использования в бесстыковом пути, согласно «Техническим требованиям к промежуточным рельсовым скреплениям ЦП 1-86» должны обеспечивать погонное сопротивление рельсовой нити не менее 25 кН/м, что соответствует продольной нагрузке на узел при срыве рельса не менее 12.5 кН, без вертикального пригруза, а по источнику [4] на основании теоретических и многочисленных экспериментальных исследований сделан вывод, о том, что для предотвращения угона и недопустимого раскрытия трещин при изломе рельса необходимо погонное сопротивление бесстыкового пути должно быть не менее 10 деление КН-65 и КН-65у несколько уступают скреплению КБ-65 по усилию срыва рельса со шпалы. При стандартном монтажном усилии 150 Нм, рельсовое скрепление КБ-65 показало усилие, при котором происходит срыв и равномерное движение рельса равное 14.30 кН, а КН-65у – 11.62 кН, несколько уступив норме ЦП 1-86 равной 12.5 кН. При увеличении монтажных усилий до 180 Нм (120% от нормативной), рельсовые скрепления КБ-65, КН-65 и КН-65у показали соответственно 14.92 кН, 15 кН и 13.06 кН, что полностью удовлетворяет условиям ЦП 1-86.
При ослаблении монтажных усилий до 75 Нм (50% от нормативной затяжки), все три скрепления не удовлетворяют требованиям ЦП 1-86.
Но в соответствии с условиями, полученными в монографии [4], данные скрепления даже при ослаблении монтажных усилий до 75 Нм (минимально допустимой величиной считают затяжку 70 Нм [77]), имеют достаточную удерживающую способность и удовлетворяют условиям надежной эксплуатации пути.
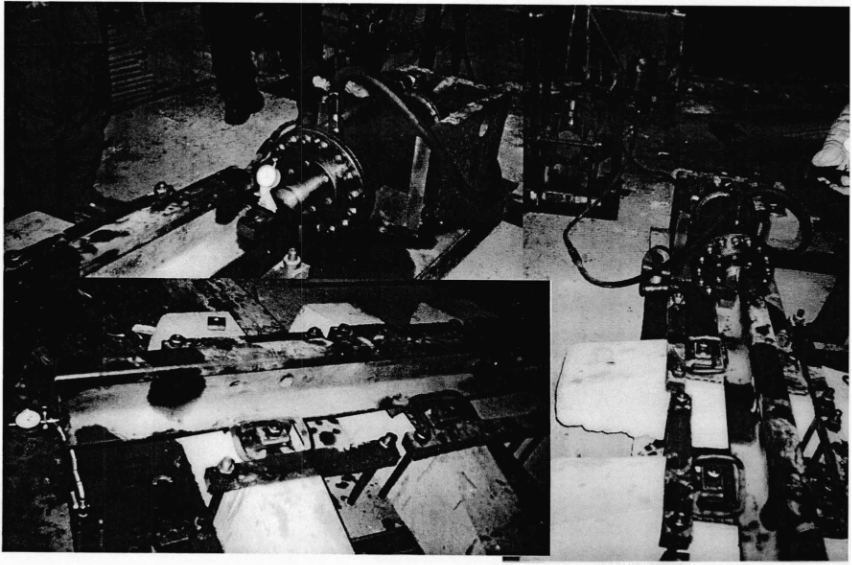
Рис 4.12 Испытания на продольный сдвиг скреплений КН-65
Динамические испытания темплетов рельсовых скреплений
Для проведения динамических испытаний темплетов рельсовых скреплений специалистами СГУПС было разработано и изготовлено два одинаковых специальных устройства для размещения и жесткой фиксации в них железобетонных (деревянных) блоков с собранным узлом рельсового скрепления. Устройства жестко закрепляются на испытательной машине и позволяют производить испытания одновременно двух блоков любых рельсовых скреплений независимо от типа шпал и рельсов.
Устройства изготовлены таким образом, что угол наклона дна короба, на которое укладывается своей нижней постелью шпала, составляет 25 градусов, относительно основания короба.
Испытания проводились в соответствии с пунктом 4-1.2.11 данной работы, на гидравлическом пульсаторе ГРМ-1 № 132, поверенном 4.11.1999 свидетельство о поверке № 1990.
Каждое скрепление подвергалось нагружениям в 2 млн. циклов со следующими параметрами: максимальное усилие 60 кН, минимальное усилие 20 кН. Испытания проводились с постоянной частотой 10 Гц (600 цикл/мин). Все клеммные болты были затянуты на 150 Нм. Через каждые 300 тыс. циклов на- гружения производился тщательный осмотр конструкции, измерялась затяжка болтов, электрическое сопротивление и проверялось состояние изоляторов.
Испытаниям были подвергнуты следующие типы рельсовых скреплений: КН-65, КБ-65И, ГС-1 и ГС-2.
Скрепление КБ-65И в результате испытаний видимых разрушений не обнаружено, затяжка болтов в норме, изоляционные втулки не разрушены.
Скрепление КН-65 в результате испытаний видимых разрушений не обнаружено, затяжка болтов в норме, изоляционные втулки не разрушены, электрическое сопротивление закладной болт-рельс после 600 тыс. циклов стабилизировалось и составило в среднем 50 кОм.
Скрепления ГС-1 и ГС-2 в результате испытаний видимых разрушений не обнаружено, затяжка болтов в норме. Результаты испытаний ГС-1 и ГС-2 приведены в табл. 4.13.
Число циклов нагружения, тыс. цикл | Затяжка болтов, Нм | |||
Скрепление ГС-1 | Скрепление ГС-2 | |||
Наружный болт | Внутренний болт | Наружный болт | Внутренний болт | |
0 | 150 | 150 | 150 | 150 |
480 | 110 | 124 | 106 | 115 |
822 | – | – | – | – |
1164 | 97 | 129 | 110 | 115 |
1506 | 87 | 129 | 101 | 110 |
1866 | 87 | 129 | 97 | 106 |
1974 | 92 | 129 | 101 | 110 |
2001 | 97 | 129 | 101 | 115 |
Оценка экономической эффективности внедрения нового рельсового скрепления КН-65
Протяжение бесстыкового пути на железобетонных шпалах составляет более 56 тыс.км. Серийным скреплением такого типа является скрепление КБ- 65 с жесткими клеммами и двухвитковыми пружинными шайбами. Ежегодная укладка бесстыкового пути с рельсовым скреплением КБ-65 на железобетонных шпалах составляет около 5 тыс.км. Скрепление КБ-65 принято за базовый вариант скрепления. Пружинные клеммы рельсового скрепления КН-65 обуславливают повышение эксплуатационной стойкости его элементов и позволяют уменьшить в два раза число подтягиваний гаек болтов по сравнению со скреплением КБ-65.
Технико-экономические показатели скреплений КБ-65 и КН-65
В табл. 4.14 приведены основные технико-экономические показатели скреплений КБ-65 и КН-65.
Таблица 4.14 | Показатели узла скрепления | КБ-65 | КН-65 |
1 | Количество деталей, шт. | 21 | 15 |
2 | Масса металла, кг. | 11,3 | 9,7 |
3 | Количество болтов, шт. | 4 | 2 |
4 | Количество пружинных элементов, шт. | 4 | 2 |
5 | Жесткость пружинного металлического элемента кН/мм, | ||
в рабочем диапазоне нагрузок 10-20 кН | 13,2 | 7,5 | |
6 | Период между сплошной подтяжкой болтов млн.т брутто | ||
пропущенного груз | 40-50 | 70-90 | |
7 | Удельный выход прокладок, процентов на 100 млн.т, груза | 4 | 2 |
8 | Отношение срока службы скрепления к сроку службы рельсов | 1 | 1 |
Основной объем капитального ремонта бесстыкового пути проводится на участках с грузонапряженностью 50-80 млн.т.км/км брутто в год. Рельсы – тер- моупрочненные, кривые участки пути составляют примерно 25%. При этом средняя эпюра шпал составит 1880 шт./км. Между капитальными ремонтами проводятся средние и подъемочные ремонты. Стоимость капитального ремонта новой и базовой техники откорректирована с учетом ее оптовой цены.
Расчет экономического эффекта
Единовременные затраты. Элементы рельсовых скреплений, выпускаемые промышленностью, приобретаются по оптовым ценам, которые характеризуют капитальные вложения железнодорожного транспорта, связанные с производством этой техники. Поэтому при расчете экономического эффекта можно пользоваться оптовыми ценами.
В табл. 4.15 приведены оптовые цены на 01.03.2000 года. Цена узла скрепления КБ-65 составляет 188,40 руб., а КН-65 – 179,98 руб. Стоимость скрепления КБ-65, приходящаяся на 1 км бесстыкового пути, равна 354192,00 руб., стоимость скрепления КН – 338362,40 руб. В результате чего затраты на закупку скреплений приходящиеся на 1 км пути снижены на 15829,60 руб. Сопутствующие капитальные вложения потребителя и производства приняты для скреплений КБ-65 и КН-65 одинаковыми.
Текущие затраты. Эксплуатационные расходы и текущие затраты железнодорожного транспорта складываются из стоимости ремонтов, которые необходимы за период эксплуатации бесстыкового пути со скреплением КБ-65 и КН-65.
В расчете учитывались эксплуатационные издержки железнодорожного транспорта, на сплошную затяжку болтов.
В соответствии с табл. 4.16 экономия эксплуатационных расходов за весь период эксплуатации составит 15624,00 руб/км..
Общий эффект. С учетом экономии на оптовой стоимости скреплений и на текущее содержание получаем экономию за межремонтный период 31453,6 руб/км
Наименование элементов | КБ-65 | КН-65 | Отклонение, руб | ||||
Кол-во, шт. | Цена, руб | Сумма, руб | Кол-во, шт | Цена, руб | Сумма, руб | ||
1. Подкладка металлическая | 2 | 40,95 | 81,90 | 2 | 33,40 | 66,80 | -15,10 |
2. Прокладка нашпальная стандартная ЦП-328 | 2 | 6,68 | 13,36 | 2 | 6,68 | 13,36 | 0,00 |
3. Прокладка подрельсовая стандартная ЦП-143 | 2 | 2,89 | 5,78 | 2 | 2.89 | 5,78 | 0,00 |
4. Болт закладной с гайкой | 4 | 6,15 | 24,60 | 4 | 6,15 | 24,60 | 0,00 |
5. Болт клеммный с гайкой | 4 | 4,78 | 19,12 | – | – | – | -19,12 |
6. Шайба 2-х витковая | 8 | 1,98 | 15,84 | – | – | – | -15,84 |
7. Изолирующая втулка | 4 | 1,92 | 7,68 | 4 | 1,92 | 7,68 | 0,00 |
8. Клемма жесткая (пружинная для КН-65) | 4 | 4,13 | 16,52 | 4 | 12,43 | 49,72 | +33,20 |
9. Скоба | 4 | 0,90 | 3,60 | – | – | – | -3,60 |
10. Шайба круглая | – | – | – | 4 | 1,17 | 4,68 | +4,68 |
11. Планка прижимная | – | – | – | 4 | 1,84 | 7,36 | +7,36 |
Итого на один комплект (1 шпала): | 188,40 | 179,98 | -8,42 | ||||
На 1 км пути (1880 шт/км): | 354192,00 | 338362,40 | -15829,60 |
Варианты | ||||||
№ | Наименование данных | Базовый КБ-65 | Новый КН-65 | Отклонение | ||
На единицу | На весь период | На единицу | На весь период | |||
1 | Количество шпал на 1 км пути | 1880 | 1880 | |||
2 | Количество ремонтов пути за период эксплуатации:капитальныхсредних | 1 1 | 11 | – | ||
– подъемочных | 2 | 2 | – | |||
– сплошная подтяжка гаек | 4 | 2 | 2 | |||
3 | Стоимость ремонтов: | |||||
– капитальный, тыс. руб/км | 1182,000 | 1182,000 | 1182,000 | 1182,000 | 0,000 | |
– средний со сплошной сменой рельсов, | 289,000 | 289,000 | 289,000 | 289,000 | 0,000 | |
тыс. руб/км | • | |||||
– подъемочный без сплошной смены | 44,000 | 88,000 | 44,000 | 88,000 | 0,000 | |
рельсов, руб/км | ||||||
– сплошная подтяжка гаек, руб/км | 5,208 | 20,832 | 2,604 | 5,208 | – 15,624 | |
4 | Оптовая цена скрепления, тыс. руб./км | 354,192 | 354,192 | 338,3624 | 338,3624 | – 15,8296 |
Итого экономия тыс.руб/км | -31,4536 |
Выводы
- Сравнительный анализ характеристик узлов рельсовых скреплений, измеренных при максимальном значении наклонной силы равной 100 кН, и рассчитанные для интервала от 0 до 100 кН, а также их процентное отношение, приведены в табл. 4.17. Анализ характеристик узлов рельсовых скреплений, измеренных и рассчитанных для интервала наклонной силы 40-90 кН, приведен в табл. 4.18.
Скрепление КБ-65И показало: горизонтальное перемещение по головке рельса несколько больше, чем у КБ-65, но меньше Д-0; горизонтальное перемещение подошвы было выше, чем у КБ-65 и Д-0; вертикальное перемещение центра подошвы среднее между КБ и Д-0, при этом угол поворота значительно уступал КБ и Д-0; а по жесткостным характеристикам скрепление показало промежуточный результат, между КБ и Д-0.
Скрепление КБ-65И, с изолированным закладным болтом и круглым отверстием в подкладке, разрабатывалось как более технологичное скрепление, позволяющее освоить его полное производство на Горновском заводе «Спецжелезобетона» со значительным упрощением производства шпал для данного скрепления, и местным изготовлением изоляторов.
Значительным недостатком скрепления КБ-65И является установка закладного болта снизу шпалы, что делает невозможным смену вышедшего из строя болта без извлечения шпалы из пути, при этом трудозатраты на замену вышедшего из строя закладного болта, по сравнению с КБ-65, увеличатся в 22.8 раза для перегона, а для станции в 25 раз [105], что является экономически неэффективным.
В целом, по результатам статических и динамических испытаний, скрепление КБ-65И показало себя работоспособным с характеристиками удовлетворяющими требованиям эксплуатации.Скрепление КБ-650П с клеммами ОП-Ю5; горизонтальное перемещение по головке рельса значительно меньше, чем у КБ-65 и Д-0; горизонтальное перемещение подошвы было меньше, чем у КБ-65 и Д-0; вертикальное перемещение центра подошвы соответствовало КБ, при этом угол поворота значительно уступал КБ и Д-0; а по жесткостным характеристикам, кроме вертикальной жесткости по подошве, скрепление оказалось значительно жестче КБ и Д-0.
Скрепление КБ-65ОП разработано на базе КБ-65, в котором заменили жесткую П-образную клемму, на упругую прутковую клемму ОП-Ю5, которая показала хорошие результаты при испытаниях, но само скрепление по результатам испытаний оказалось жестче прототипа. В результате наблюдений за установленными в пути клеммами и при лабораторных исследованиях, был замечен существенный недостаток данной конструкции: при установке клеммы ОП-Ю5 и нагружения конструкции наблюдалось сползание клеммы по наклонной верхней поверхности подошвы рельса и перекрытия клеммой образовавшегося зазора между ребордой подкладки и подошвой рельса. Поэтому при нагружении клемма своими острыми кромками расклинивала рельс с подкладкой, давая при этом очень малое перемещение рельса, фактически не выполняя свою роль упругого элемента. Данный недостаток легко устраним, при изменении формы подкладки, добавив в нее дополнительный выступ (реборду), препятствующий перемещению клеммы назад.
При эксплуатации в пути поступили замечания о невозможности установки данного скрепления в районе стыка.
Скрепление КБ-650П прошло успешные испытания и при удалении вышеперечисленных недостатков рекомендуется для применения в бесстыковом пути.
3. Скрепление КН-65; горизонтальное перемещение по головке соответствует КБ-65; горизонтальное перемещение подошвы незначительно меньше, чем у КБ-65 и Д-0; вертикальное перемещение центра подошвы находится между показаниями для КБ и Д-0, при этом угол поворота уступал КБ и Д-0, а по жесткостным характеристикам, близкое к жесткости КБ, но больше чем Д-0.
Скрепление КН-65у: горизонтальное перемещение по головке и подошве больше чем у КБ-65 и Д-0; вертикальное перемещение центра подошвы меньше показателей для КБ и Д-0, при этом угол поворота был между значениями для КБ и Д-0, а по жееткостным характеристикам, за исключением вертикальной жесткости по подошве уступал КБ и Д-0.
Скрепления КН-65 и КН-65у разрабатывались как более простые, малодетальные, упругие образцы подкладочных скреплений взамен КБ-65 с максимальным использованием имеющейся производственной базы и минимальной переделкой оборудования.
Скрепления КН-65 и КН-65у успешно прошли статические и динамические испытания. В настоящее время изготовлена опытная промышленная партия и планируется укладка 1 км пути со скреплением КН-65у, с перспективой дальнейшего использования в бесстыковом пути.
4. Скрепление БАРС: горизонтальное перемещение по головке и подошве рельса, а также вертикальное перемещение центра подошвы меньше показателей для КБ и Д-0, при этом угол поворота оказался значительно меньше, чем у КБ и Д-0, а по жесткостным характеристикам оказалось жестче КБ и Д-0.
Скрепление БАРС разрабатывалось как анкерное бесподкладочное скрепление, обладающее высокой технологичностью изготовления, минимальным расходом материалов, и минимальным количеством деталей, при этом обеспечивающим низкую стоимость и простоту сборки. К недостаткам данного скрепления можно отнести – возможность повреждения резьбы, приводящее к замене шпалы. При использовании высокоулеродных сортов стали уменьшается возможность повреждения резьбы, а при оснащении путевых бригад средствами восстановления резьбы (насадки с лерками для электроинструмента), можно свести к минимуму замену шпал, вышедших из строя. Данная конструкция является перспективной, и экономически выгодной как для использования в сети железных дорог, так и для применения в метро и для городского железнодорожного транспорта. Скрепление успешно прошло лабораторные испытания и при незначительной технической доработке может быть запущено в мелкосерийное производство, для проведения путевых испытаний.
Скрепление БАРС-Б: горизонтальное перемещение по головке и подошве рельса, а также вертикальное перемещение центра подошвы больше показателей для КБ и Д-0, при этом угол поворота оказался больше чем у КБ, а по жест- костным характеристикам оказалось значительно менее жестким, чем КБ и Д-0.
Скрепление БАРС-Б разрабатывалось как бесподкладочное, безрезьбовое, анкерное рельсовое скрепление, обладающее высокой технологичностью, ма- лодетальностью, простотой в сборке и обслуживании, а также низкой стоимостью производства.
В результате испытаний скрепление показало большие перемещения из-за невысокой точности изготовления экспериментального образца, и невозможности регулировки передачи усилия от эксцентрика на клемму, связанное с недостатком конструкции эксцентрика. Кроме того, для данного типа рельсового скрепления рекомендуется произвести заглубление опорной площадки под подошвой рельса.
Успешно пройдя испытания, скрепление БАРС-Б показало простоту сборки и неприхотливость. Скрепление требует технологической доработки и, по мнению специалистов СГУПС, является самым перспективным из малооб- служиваемых скреплений.
5. Скрепления ГС-1 с полимерным изолятором по своим упругим характеристикам является промежуточным между КБ и Д-0.
Скрепление ГС-2 с изоляционным покрытием анкера показало несколько большую жесткость, чем КБ и Д-0, и соответственно меньшее перемещение.
Скрепления ГС-1 и ГС-2 являются однотипными бесподкладочными анкерными скреплениями, соответственно с полимерным изолятором и изоляционным покрытием анкера. Изоляционное покрытие анкера скрепления ГС-2 оказалось ненадежным, и проведение дальнейших испытаний этого скрепления было прекращено. Скрепление ГС-1 является малодетальным, имеет простую сборку и низкую стоимость при высоком использовании стандартных деталей, находящихся в производстве.
Скрепление ГС-1, успешно пройдя статические и динамические испытания, оказалось дешевле, экономичнее и технологичнее скрепления КБ-65, не уступая ему в характеристиках и выигрывая в эксплуатационных расходах. В настоящее время ставится вопрос о производстве опытной партии для укладки в путь.
Заключение
Автором диссертационной работы поставлена и решена задача совершенствования новых типов малообслужваемых рельсовых скреплений с упругими элементами для железобетонных шпал, проведенных в соответствии с временной методикой испытаний утвержденной в ЦП МПС.
На основании выполненных теоретических и экспериментальных исследований, а также по результатам полигонных испытаний сделаны следующие основные выводы:
- Выполнен анализ состояния и тенденций развития современных рельсовых скреплений, который показал, что все работы в области повышения надежности пути можно разделить на несколько групп:
- модернизация использующегося скрепления КБ-65 путем замены упругих шайб или постановкой новых пружинных клемм взамен жестких П-образных;
- переход на новые подкладочные скрепления с упругими клеммами;
- переход на новые типы малообслуживаемых бесподкладочных рельсовых скреплений, в том числе и безболтовых, содержащих малое количество деталей высокого качества, обладающих повышенной надежностью и долговечностью;
- Теоретические расчеты показали, что в качестве упругих пружин под гайки стыковых болтов могут быть использованы типовые тарельчатые шайбы или гофрированные шайбы, в основу которых положены типовые.
В качестве упругих пружин под гайки стыковых болтов разработаны тарельчатые гофрированные шайбы из стали 60С2А толщиной 5 мм, внешним диаметром 70 мм и внутренним – 28 мм. Высота таких шайб 10 мм.
Лабораторные исследования показали, что жесткость гофрированных шайб составляет 19 кН/мм, что соответствует техническим требованиям.
В качестве упругих пружин под гайки клеммных и закладных болтов разработаны тарельчатые гофрированные шайбы из стали 60С2А толщиной 3 мм, внешним диаметром 50 мм и внутренним – 23 мм. Высота волны таких шайб должна быть 1,5 мм.
Лабораторные исследования данных шайб показали, что одиночные шайбы обеспечивают жесткость 12 кН/мм, а сдвоенные 8 кН/мм и удовлетворяют техническим требованиям.
Динамические испытания на пульсаторе тарельчатых гофрированных шайб показали положительные результаты.
Эксплуатационные испытания гофрированных шайб на двух уравнительных пролетах бесстыкового пути после пропуска 6,3 млн. тонн брутто груза показали высокую эксплуатационную надежность и стабильность натяжения ботов.
- Анализ результатов лабораторных исследований показал, что клемма ОП- 105, по сравнению с двухвитковой пружинной шайбой, в рабочем диапазоне нагрузок 10-20 кН имеет в 4-5 раз большую длину хода при завинчивании гайки и соответственно позволит увеличить промежуток времени между подтяжкой болтов при использовании в скреплении КБ-65, в 2 раза, что соответственно уменьшит расходы на текущее содержание пути.
Анализ результатов исследования упругих прутковых клемм для скреплений КН-65 и ЖБР-3 показал, что данные клеммы обладают малыми остаточными деформациями, значительной упругостью (7,5 кН/мм и 5,6 кН/мм) и стабильностью результатов испытаний. При этом создаются более благоприятные условия для эксплуатации верхнего строения пути, уменьшаются динамические нагрузки на элементы.
- Проведенный анализ интервальной жесткости по результатам лабораторных исследований стандартных резиновых упругих элементов выявил следующее: наиболее упругой можно считать прокладку скрепления ЖБР-3-65 толщиной 14 мм ЦП-204, далее примерно равными нашпальную скрепления КБ-65 ЦП-328 и совместно подрельсовую ЦП-143 с нашпальной скрепления КБ-65 ЦП-328, более жесткими подрельсовую скрепления КБ-65 толщиной 8 мм ЦП- 143 и чрезмерно жесткой гладкую подрельсовую прокладку толщиной 8 мм скрепления КБ-65 ОП-318.
В результате испытаний все прокладки, за исключением ОП-318, показали стабильные результаты, малые колебания и плавное возрастание жесткости, поэтому они рекомендуются для дальнейшего применения как в действующих скреплениях, так и в новых типах рельсовых скреплений.
5. Для достижения поставленной в диссертационной работы цели предложено произвести унификацию испытаний выпускаемых в настоящее время, как стандартных рельсовых скреплений, так и новых экспериментальных образцов подкладочных и бесподкладочных скреплений.
Целью унификации является проведение исследований на одном и том же оборудовании, при одних и тех же условиях, по одной и той же установленной схеме испытаний для получения наибольшей достоверности результатов с последующим их анализом.
Для проведения испытаний узлов рельсовых скреплений на действие наклонной силы было разработано и изготовлено специальное устройство для размещения и жесткой фиксации в нем железобетонного (деревянного) блока с собранным узлом рельсового скрепления. Устройство изготовлено таким образом, что угол наклона дна короба, на которое укладывается своей нижней постелью шпала, составил 25 градусов, а с учетом того, что для всех типов шал, использующих подуклонку подошвы рельса внутрь колеи равную 1/20, угол наклона нагружающей силы относительно вертикальной оси симметрии рельса, составил 22 градуса 8 минут (22.14 градуса).
В настоящее время наиболее распространенным считается способ определения угловых и жесткостных характеристик для интервала вертикальных нагрузок от 40 до 80 кН или от 20 до 80 кН. Недостатком этого метода является условное принятие приращения перемещения точек измерения на данном интервале, происходящее по линейному закону, что абсолютно не отражает действительной ситуации перемещения, происходящей по нелинейному закону. В связи с вышеизложенным, можно утверждать, что данный способ оценки является малопригодным для отражения результатов проведенных исследований, и, по предложению автора работы, наиболее рациональными способами можно
считать способы анализа назрастающим итогом или пошагового сравнения. При этом наиболее благоприятные условия для сравнительного анализа скреплений даст интервальная пошаговая оценка, которая в наименьшей степени подвержена ошибкам и неточностям при установке и сборке скреплений, особенно в начальный этап нагружения, когда происходит выбор зазоров между элементами скреплений и позволяет более точно оценить реальную работу скрепления под нагрузкой.
6. Для возможности сопоставления результатов исследований новых типов рельсовых скреплений первоначально были испытаны узлы скреплений КБ-65 и Д-0, а результаты данных испытаний принимались как эталонные для дальнейшего сравнения и оценки скреплений. В качестве экспериментальных образцов были исследованы нижеприведенные типы рельсовых скреплений. Подкладочные:
- КБ-65И (разработано на базе скрепления КБ-65 с изоляционным покрытием канала в шпале под закладной болт, имеющий шестигранную головку);
- КБ-650П (разработано на базе скрепления КБ-65 с заменой стандартной П-образной клеммы на упругую прутковую клемму ОП-Ю5);
- КН-65 и КН-65у (разработаны на базе скрепления КБ-65 с упразднением клеммного болта и П-образной клеммы, а в качестве упругого элемента используется прутковая клемма КН-65 закрепленная непосредственно на закладной болт).
Бесподкладочные:
- БАРС (скрепление с замоноличенным прутковым анкером на поверхность соторого нанесена резьба и надета прутковая клемма скрепления ЖБР-3-65);
- БАРС-Б (безболтовое безрезьбовое анкерное рельсовое скрепление в котором нагрузка на клемму от скрепления ЖБР-3-65 передается через эксцентрик, опирающийся в анкер);
- ГС-1 и ГС-2 (анкерные скрепления, в которых нагрузка на клемму от скреп- тения ЖБР-3-65 передается через стандартный клеммный болт скрепления КБ-65, остановленный в паз анкера).
- Проведя анализ результатов статических испытаний скреплений, автор пришел к следующему выводу:
- при использовании общих показателей наклонной силы от 0 до п, где п – изменяется от 10 до 100 кН с шагом в 10 кН, наиболее точно можно оценить угол поворота подошвы рельса относительно первоначального положения и жесткость угла на кручение, так как оценить эту жесткость поинтервально практически невозможно;
- при использовании интервальных пошаговых показателей, как наиболее точного метода, оценивается угол поворота рельса относительно первоначального положения, горизонтальная жесткость по головке и подошве рельса и вертикальная жесткость по подошве рельса;
- при использовании жесткого интервала (для наиболее часто распространенного в литературе интервала вертикальных нагрузок на узел скрепления от 40 до 80 кН) принимаем диапазон наклонной силы от 40 до 90 кН, при этом вертикальная составляющая этих сил представлена диапазоном вертикальных нагрузок 36.25 – 81.57 кН, и горизонтальных нагрузок для данного диапазона 16.90 – 38.04 кН, что приблизительно соответствует диапазону нагрузок приведенным в литературе. При этом определяется угол поворота, жесткости на кручение, а также горизонтальная жесткость по головке и подошве рельса и вертикальная жесткость по подошве рельса.
- По результатам статических испытаний узлов скреплений под воздействием наклонной нагрузки установлено, что вертикальная их жесткость формируется в основном за счет толщины и формы резиновых прокладок. Горизонтальная жесткость скреплений по головке рельса и на кручение определяется жесткостью клемм и в значительной мере жесткостью подрельсовых прокладок. Горизонтальная жесткость скреплений по подошве рельса определяется конструкцией скреплений, а у подкладочных скреплений, кроме того, толщиной нашпальных прокладок.
9. Для анализа результатов испытаний узлов скреплений выберем интервал изменения наклонной силы, равный 40-90 кН. Для этого интервала нагружения сделаем оценку жесткости наиболее распространенных скреплений.
Вертикальная жесткость узлов скреплений Д-0 по сравнению со скреплением КБ-65, имевшим подрельсовую прокладку толщиной 8 мм и нашпальную толщиной 10 мм, оказалась на 30% меньше.
Вертикальная жесткость скреплений КН-65 и КБ-650П оказались соответственно на 7 и 16 % больше, чем у скрепления КБ-65.
Вертикальная жесткость скрепления ГС-1, имевшего подрельсовую прокладку толщиной 14 мм, оказалась на 60% выше, чем у скрепления КБ-65.
Горизонтальная жесткость скреплений по их подошве оказалась для Д-0 равной КБ-65. Для подкладочных скреплений КН-65 и КБ-650П оказались соответственно на 28 % ниже и на 18 % выше, чем у КБ-65. Горизонтальная жесткость анкерного скрепления ГС-2 оказалась на 52%» выше, чем у скрепления КБ-65.
Горизонтальная жесткость скреплений, измеренная по головке рельса в интервале 17-38 кН горизонтальной нагрузки, для скрепления Д-0 оказалась примерно равной жесткости типового скрепления КБ-65, а у КН-65 на 12% меньше.
У скрепления КБ-650П, имевших прутковые клеммы ОП-Ю5, горизонтальная жесткость по головке рельса оказалась на 20% выше чем у КБ-65. Объяснить это можно большой жесткостью подрельсовой прокладки и заклиниванием клеммы ОП-Ю5 между кромкой подошвы рельса и ребордой подкладки.
Горизонтальная жесткость по головке рельса анкерного скрепления ГС-1 оказалась на 38% выше чем у скрепления КБ-65. Объясняется это незначительным перемещением подошвы рельса относительно анкеров.
10. Определение удерживающей способности скреплений КБ-65, КН-65 и КН-65у на продольный сдвиг вдоль оси рельса с различными вариантами затяжки клеммных болтов осуществлялось на специально сконструированной и изготовленной установке, позволяющей проводить сдвиг рельсовой рубки, закрепленной на одной, двух или на трех шпалах одновременно, имеющих жесткое крепление к основанию.
Проанализировав результаты испытаний, установили, что рельсовое скрепление КН-65 и КН-65у незначительно уступают скреплению КБ-65 по усилию срыва рельса со шпалы. В соответствии требованиями Технических условий на укладку и эксплуатацию бесстыкового пути, данные скрепления даже при ослаблении монтажных усилий до 50% имеют достаточную удерживающую способность и удовлетворяют условиям надежной эксплуатации пути.
11. Динамические испытания темилетов рельсовых скреплений КН-65, КБ- 65И, ГС-1 и ГС-2 на действие циклической наклонной нагрузки, при угле передачи нагрузки равным 25 градусов с максимальным усилием 60 кН, минимальным усилием 20 кН, частотой 10 Гц в объеме 2 млн. циклов показали, что в результате испытаний у всех вышеприведенных скреплений видимых разрушений не обнаружено, затяжка болтов в норме, изоляционные втулки и прокладки не разрушены, что свидетельствует о работоспособности скреплений и пригодности для укладки в путь.
На основе выполненной диссертационной работы автором предлагается следующее:
- Использовать утвержденную методику, как для разработки новых технических требований на проектирование промежуточных рельсовых скреплений, так и для провидения испытаний рельсовых скреплений, определяя при этом их пригодности к новым условиям эксплуатации.
- Расширить существующие полигоны укладки разработанных новых типов гофрированных шайб для скрепления КБ-65 на бесстыковом пути с железобетонными шпалами, что позволит значительно увеличить эксплуатационную надежность всех элементов путевой решетки и пути в целом.
- Увеличить протяженность экспериментально уложенного участка пути со скреплением КН-65 протяженностью 250 м, до 5 км для возможности получения наиболее точной информации, по поведению нового типа малообслужи- ваемого рельсового скрепления с упругими прутковыми клеммами с целью выработки рекомендаций по текущему содержанию и ремонту пути и с возможностью последующего перехода на выпуск данного типа скреплений на Горнов- ском заводе «Спецжелезобетон».
- Уложить опытные участки с анкерным скреплением ГС-1 для его эксплуатационной проверки.
- Принять для последующих исследований новых типов рельсовых скреплений на действие наклонной силы следующие способы оценки основных параметров:
- оценку угла поворота рельса относительно первоначального положения, горизонтальной жесткости по головке и подошве рельса и вертикальной жесткости по подошве рельса производить при использовании интервальных пошаговых показателей, от 0 до 100 кН с шагом в 10 кН;
- оценку угла поворота, жесткости на кручение, а так же горизонтальную жесткость по головке и подошве рельса и вертикальную жесткость по подошве рельса, для возможности сравнения с литературными данными, можно оценивать при использовании общепринятого интервала нагружения.
- В процессе проведения исследований и наблюдений в пути автором работы были обнаружены нижеприведенные недостатки скреплений и предложены следующие меры по их устранению:
- Неустранимым недостатком скрепления КБ-65И является установка закладного болта снизу шпалы, что делает невозможным смену вышедшего из строя болта без извлечения шпалы из пути при этом трудозатраты на замену вышедшего из строя закладного болта по сравнению с КБ-65 увеличатся в 22.8 раза для перегона, а для станции в 25 раз [105], что является экономически неэффективным.
- В скреплении КБ-650П в результате наблюдений за установленными в пути клеммами и при лабораторных исследованиях был выявлен существенный недостаток данной конструкции: при нагружения конструкции наблюдалось сползание клеммы по наклонной поверхности подошвы рельса и перекрытия клеммой образовавшегося зазора между ребордой подкладки и подошвой рельса. При нагружении клемма своими острыми кромками расклинивала рельс с подкладкой, препятствуя его перемещению, фактически не выполняя роль упругого элемента. Автором предлагается устранить данный недостаток, изменением формы подкладки, добавив в нее дополнительный выступ (реборду), препятствующий перемещению клеммы назад.
- К недостаткам скрепления БАРС относится возможность повреждения резьбы анкерных стержней, приводящее к замене шпалы. Предлагается для уменьшается возможности повреждения резьбы и сведению к минимуму количество вышедших из строя шпал использовать для производства анкера высокоуглеродистые сорта стали, и произвести оснащение путевых бригад средствами восстановления резьбы (насадки с лерками для электроинструмента).
- Скрепление БАРС-Б показало большие перемещения из-за низкого качества изготовления экспериментального образца и невозможности регулировки передачи усилия от эксцентрика на клемму, связанное с недостатком конструкции эксцентрика. Предлагается для данного типа рельсового скрепления произвести заглубление опорной площадки под подошвой рельса, произвести разработку надежных электроизоляторов и усовершенствовать конструкцию эксцентрика и анкера, для возможности регулировки передачи усилия от клеммы на рельс.
- Изоляционное покрытие анкера скрепления ГС-2 оказалось ненадежным, и проведение дальнейших испытаний этого скрепления было прекращено.
Список Литературы
- Зензииов H.A. Рыжак С.А. Выдающиеся инженеры и ученые железнодорожного транспорта. М.: Транспорт. 1990 – С. 17.
- Основные направления экономического и социального развития СССР на 1986-1990 годы и на период до 2000 года // Правда . – 1986. 9 марта. – С. 1-6.
- Лынев Р.Н. Критический путь экономики // Известия 1986. – 18 января.
- Карпущенко Н.И. Надежность связей рельсов с основанием. М. 1986. 150с.
- Альбрехт В. Г. Виноградов Н.П. Проблеммы бесстыкового пути // Путь и путевое хозяйство. – 1985. – №1. – С. 28-30.
- Бесстыковой путь / Под ред. Альбрехта В.Г. и Бромберга Е.М. – М.: Транспорт 1982. – 193 с.
- Белорусов А И , Колосов А.П. Влияние уровня монтажных усилий на вибрационное ускорение балласта // Сб. Науч. тр. / ХИИТ. – 1988. – Вып. 5. – С. 38-45.
- Шахунянц Г.М. Железнодорожный путь. М. Транспорт, 1987.
- Технические указания по устройству, укладке и содержанию бесстыкового пути / ЦП МПС РФ. М.: Транспорт, 1992 г. 72 с.
- Крейнис 3.JT. Бесстыковой путь. – М.: Знание 1967. – 48 с.
- Вериго М.Ф. Методика проектирования промежуточных рельсовых скреплений и расчеты параметров к ней: Рукопись ЦНИИ МПС, 1954. – 84 с.