Сейчас ваша корзина пуста!
Причины и факторы изнашивания бандажей колес локомотивов
Цикл статей:
Глава 1 – Повышение ресурса колесных пар локомотивов с тележками поводкового типа
Глава 2 – Причины и факторы изнашивания бандажей колес локомотивов
Глава 4 – Конструкторское и технологическое совершенствование буксового поводка
Глава 5 – Экспериментальные исследования шарниров буксовых поводков
Глава 6 – Технология и функционально-стоимостный анализ эффективности модернизации буксовых поводков
В 70-80-е годы XX столетия отечественное локомотивостроение постепенно перешло на бесчелюстные рамы тележек, у которых тяговые и тормозные усилия от КМБ к тележке передаются посредством БП с обрезиненными шарнирами. Такой упругой связью рам тележек с буксовыми узлами был оборудован практически весь парк ТПС, тепловозы: ТЭП60, ТЭП70БС, ТЭ109, 3(2)ТЭ10В (М, У, МК), 2ТЭ116, 2ТЭ121, 2ТЭ136; электровозы: ВЛ10, ВЛ80, ВЛ82, ВЛ60, ВЛ41, ЧС4.
Анализ эксплуатационных данных показывает, что упрощенное заимствование конструкции бесчелюстной тележки и ее буксовых связей с КМБ, без фундаментальных исследований механики работы оборудования экипажной части (в зависимости от типа локомотива), обеспечило на длительный период проблему ресурса бандажей [67]. Конструкторские и технологические нормативы обрезиненных шарниров устанавливались аналитическими методами для общего машиностроения [19, 68-71]:
- продольное перемещение буксовых узлов относительно рамы тележки в горизонтальной плоскости (не более 0,2 мм), в режиме тяги и торможения;
- вертикальное перемещение рамы тележки относительно буксы при индивидуальном рессорном подвешивания (не более 40 мм);
- поперечное перемещение средней оси трехосной тележки 14 мм.
Характерные неисправности буксовых поводков
Типичные неисправности элементов буксовых поводков и колесных пар в условиях эксплуатации приведены на рисунках 2.1-2.7
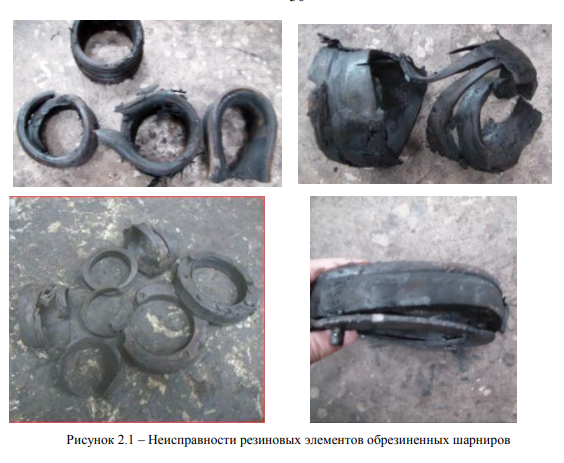
Неисправность (деформация) корпуса БП, в соответствии с рисунком 2.2, как следствие динамических нагрузок. Известно, что отклонение длины хотя бы одного поводка из четырех КМБ от альбомных размеров (320±0,2 мм) создает условия для постоянного перекоса оси колесной пары в тележке и продолжительного взаимодействия гребней бандажей с боковыми гранями головок рельсов. Такое состояние связей тележки с буксами колесно-моторного блока: снижает тяговые возможности локомотива; повышает сопротивление движению, расход топливно-энергетических ресурсов (ТЭР) на тягу поездов и эксплуатационные затраты. Неустойчивое движение колесных пар сопровождается огромными амплитудами силовых динамических нагрузок, воздействующих на слабые конструктивные элементы, разрушая их и буксовые поводки до непригодного и невосстанавливаемого состояния в соответствии с рисунками 2.3-2.5.
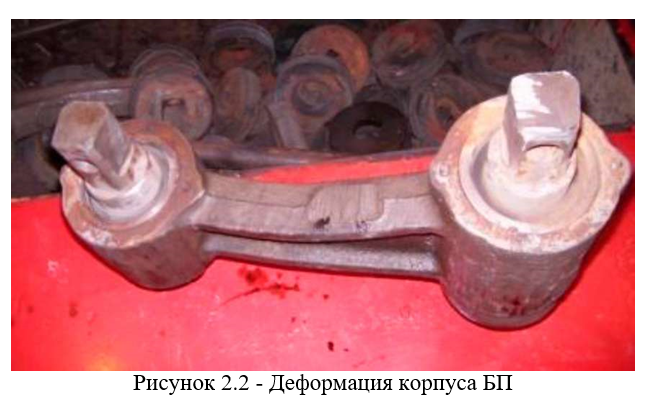
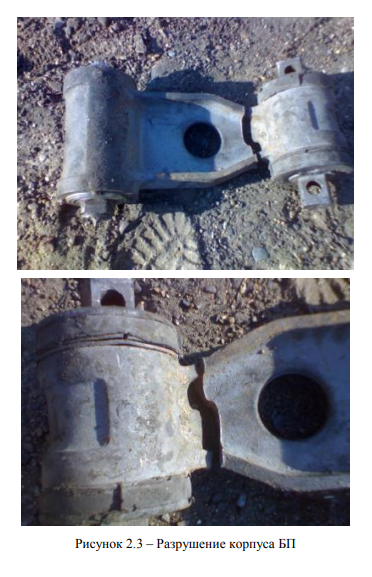
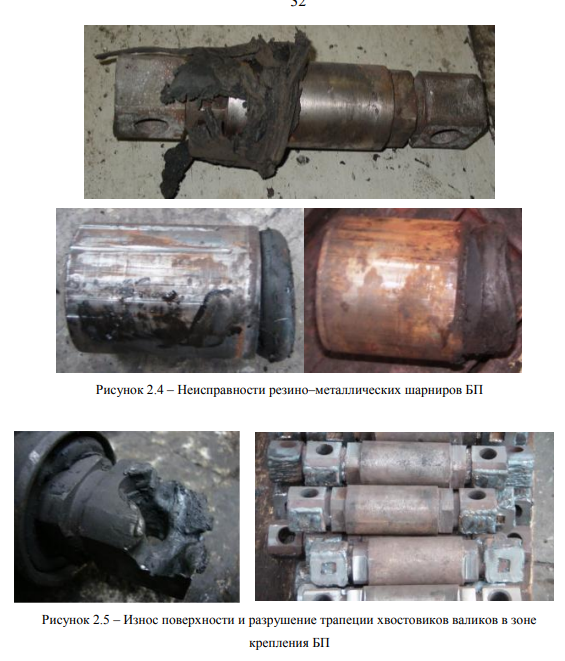
По результатам мониторинга состояния и неисправностей корпуса поводка установлено, что при пробеге тепловоза более 300 тыс. км отверстия малых головок имеют овальность 4-5 мм, а больших головок 2-3 мм в соответствии с рисунком 2.6. Повысить прочность головок поводка можно известным технологическим методом за счет применения полезных самонапряжений. Тогда головка поводка приобретает повышенную прочность при вводе в нее дополнительной втулки с натягом (до 0,07 мм на 10 мм диаметра вводимой втулки). В инструкции ТИ175 рекомендуют запрессовывать металлическую втулку обрезиненного шарнира в головку поводка с натягом от 0,06 до 0,16 мм [72], что позволяет уменьшить значения напряжений с возрастанием нагрузки. Однако необходимо учитывать реальные условия работы конструкции, при которых значение коэффициента концентрации не является постоянным для каждой головки поводка, а зависит от состояния резины и характера нагрузки. Перекос колесной пары в тележке, горизонтальное поперечное ее перемещение, увеличивают максимальные напряжения в головке поводка. На выносливость стальных головок и обрезиненных шарниров значительное влияние оказывает амплитуда пульсирующей нагрузки.
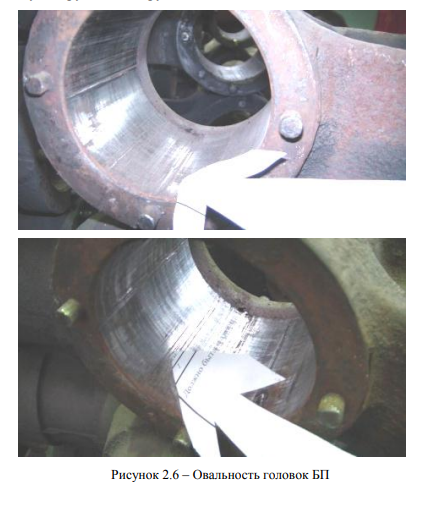
Виды поверхностей тормозных колодок «с наварами» металла бандажа представлены на рисунке 2.7. Металл срезается, в основном, с гребня бандажа при перекосе оси колесной пары в тележке. В процессе торможения тормозная колодка не попадает на профиль бандажа. Выступ тормозной колодки касается поверхности гребня и стружка приваривается к корпусу колодки.
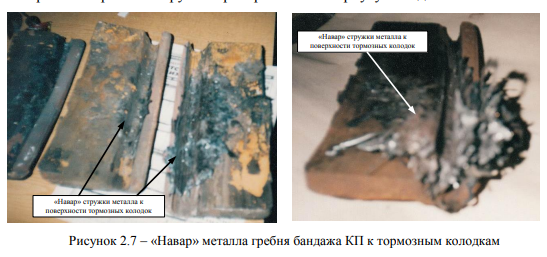
Типичная неисправность поверхности катания колеса представлена рисунке 2.8, а неисправность поверхности катания головок рельсов, в виде температурных раковин представлена на рисунке 2.9.
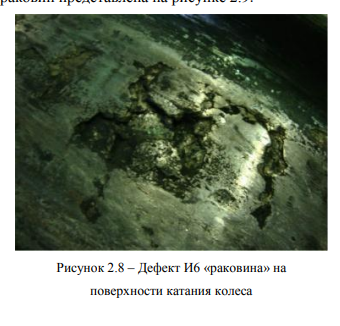
Раковины на рабочей поверхности головок рельсов наблюдается повсеместно в кривых участках рельсовой колеи и на внутреннем рельсе. На поверхности катания колеса раковины формируются при прохождении кривых в режиме тяги, когда колесо катится по малому диаметру (с визгом), проскальзывая.
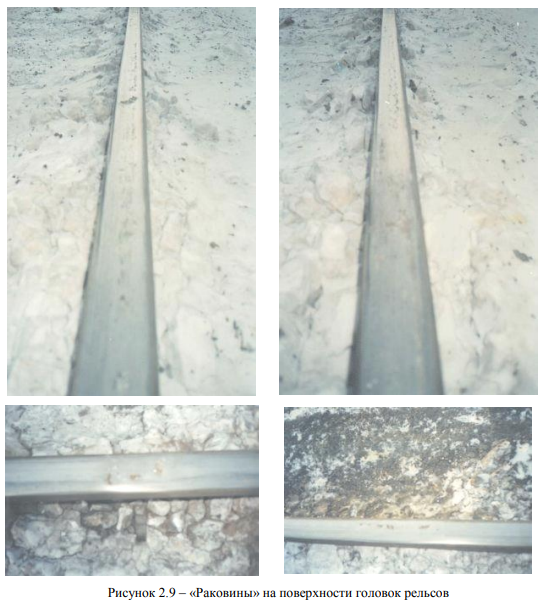
Анализ работоспособности элементов буксового поводка
Подвижное соединение при помощи ушка с болтом или шарнир с валиком является обычным элементом различных соединительных конструкций в машиностроении, которое обладает, как правило, поразительно низкой долговечностью. На долговечность и работоспособность соединения всецело влияет цикличность динамических нагрузок. Долговечность такого соединения часто определяет эффективность самой машины, стоимость которой несоизмерима со стоимостью элементов соединения. Подобное соотношение в полной мере относится к обрезиненным шарнирам буксовых поводков.
Модели механизма работы обрезиненных шарниров обстоятельно рассмотрены в работах [66, 70, 73]. Большие силовые и динамические составляющие, повышенные деформации резиновых втулок, создают условия интенсивного изменения их физических и технических характеристик. Незначительный износ резины резко изменяет степень ее начального поджатия, появляются зазоры между металлом и резиной. Наличие зазора в подобном соединении является дополнительным концентратором напряжений в металле головки поводка. Можно предположить, что при разработке шарниров конструкторы принимали резину как конструкционный материал, способный сохранять параметры связей между буксовыми узлами и бесчелюстной рамой тележки на протяжении нормативных межремонтных пробегов локомотивов. Типичное состояние буксовых соединений в условиях эксплуатации, в соответствии с рисунками 2.1-2.5, свидетельствуют о необходимости дальнейших исследований работоспособности обрезиненных шарниров прочностным, конструкторским и технологическим критериям. Их долговечность в типичных условиях эксплуатации не соответствует научными аспектами [74-76] и требует своего нового осмысления. Анализ показывает, что конструкция наиболее повреждаемой малой головки поводка выполнена без учета:
- соответствия физических и технологических свойств резиновых элементов шарнира, которые должны обеспечивать межремонтный эксплуатационный период;
- теоретического обоснования гарантированного срока службы корпуса поводка и других металлических деталей шарнира;
- физических зависимостей по предельным коэффициентам концентрации напряжений и числу циклов до разрушения элементов шарнира.
На основе мониторинга состояния буксовых поводков и их элементов, определены корректирующие задачи совершенствования связей между рамой тележки и буксами. Для успешного решения этих задач необходимо исключить из шарнира резину, выбрать и обосновать физические и механические характеристики конструкционного материала, пригодного для работы в условиях и режимах нагрузок, действующих на элементы конструкции буксовых поводков.
Специфика работы резиновых деталей в конструкциях экипажной части локомотивов
Применению в локомотивостроении резино-технических изделий (РТИ), испытывающих воздействие сложных нагрузок, неизбежно предшествовали многочисленные теоретические и экспериментальные исследования. Методы и результаты исследований изделий общего машиностроения с достаточной полнотой изложены в работах [71, 74-76] и других отечественных изданиях.
Анализ показывает, что применявшиеся в исследованиях методы основаны как на простой форме записи эмпирических данных, так и на применении достижений к тому времени теории упругости. Наибольшее распространение получили методы расчета резиновых деталей при малых деформациях, основанные на применении формул сопротивления материалов. Однако для расчета цилиндрических амортизаторов обрезиненных шарниров буксовых поводков конструкторы использовали конечные формулы, предложенные в работе [74-76].
Экспериментальные исследования по оценке работоспособности РТИ выполнены в сопоставлении прочности и механики разрушения резины в наиболее общих примерах, не имеющих отношения к конкретным деталям и локомотивам. Опыт практики подтверждает, что при проектировании и формировании обрезиненных шарниров буксовых поводков недостаточно учтен ряд факторов: параметры нагрузок; климатические условия; фазы «отдыха» и продолжительность нагрузки; частота и амплитуда силового воздействия; масштабный фактор деформации резины до ее разрушения; наличие концентраторов напряжений; немеханические факторы (молекулярный вес, плотность, прочность молекулярных связей, наполнители).
Для современных локомотивов конструкторам, технологам и эксплуатационникам целесообразно придерживаться инновационных научных и проверенных практическим опытом положений:
- резина является практически несжимаемым материалом и изделия должны иметь возможность изменять формы при нагрузке;
- необходимо избегать конструкций, в которых резина работает на растяжение и изгиб;
- необходимо добиваться равномерного распределения напряжений по всему объему РТИ;
- если используется несколько однотипных РТИ, то следует добиваться идентичности их характеристик и равномерной нагрузки;
- несущая способность и жесткость резиновых конструкций должна быть достигнута не в ущерб ее долговечности;
- резиновые детали необходимо выбирать по физическим и механическим свойствам и допустимым изменениям их характеристик во времени и по условиям эксплуатации.
Изучение и систематизация эксплуатационного состояния обрезиненных шарниров буксовых поводков свидетельствуют о том, что машиностроители изначально не всегда учитывают ограничивающие требования резиновых деталей по предстоящим особенностям условий и режимов их работы.
Параметры технологического изнашивания бандажей
Обобщенные данные неисправностей бандажей колес по сети дорог ОАО «РЖД» свидетельствуют о том, что 60-80 % из них составляют «износ гребня» и «остроконечный накат». Эти неисправности относят к разряду самых высоких факторов риска по безопасности движения, и чтобы их снизить, эксплуатационники вынуждены преждевременно восстанавливать профиль бандажа обточкой колес или выполнять замену КМБ и колесной пары. Технологические операции по обточке колесных пар отнесены к техническому обслуживанию ТО-4. Отсутствие эффективных методов мониторинга состояния и неисправностей колесных пар не позволяет проконтролировать и установить достоверные численные критерии «технологического изнашивания» (глубина снятого металла) в зависимости от износа гребня или проката, ползунов, температурных раковин, что усложняет расчет ресурса бандажей. Чтобы выработать подходы к решению задач «управления» ресурсом бандажей, необходимо разработать математическую модель идентификации технологического их изнашивания по критериям: глубина резания и масса снимаемого металла. Зависимость глубины резания для восстановления нормативных параметров толщины гребня достигшего 26 мм, приведена на рисунке 2.10.
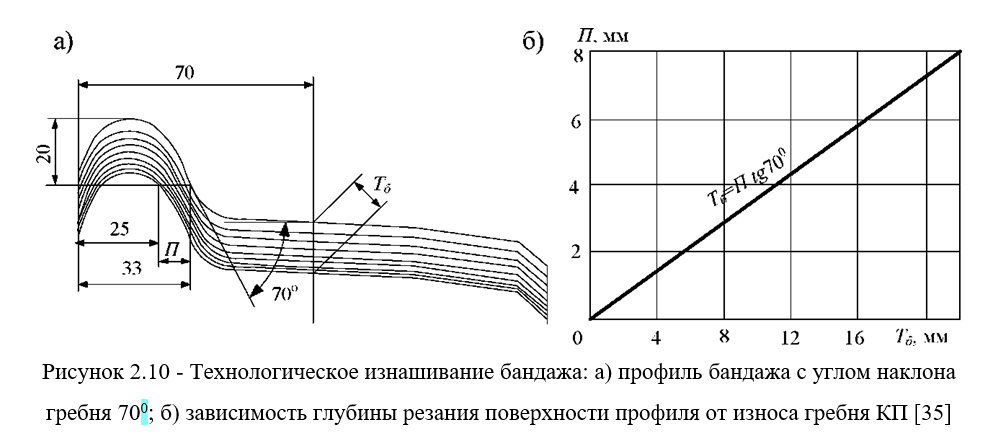
По апостериорным эксплуатационным данным, в соответствии с рисунком 2.10, а, использованием интерполяционного метода Лагранжа [77] для равноотстоящих узлов интерполирования, уточнена зависимость, в соответствии с рисунком 2.10.6, которая хорошо согласуется с результатами работы [35]


В связи с тем, что бандаж является телом вращения, то количество снимаемого металла, целесообразно оценивать объемом и массой. Эти зависимости можно достоверно определять по интегральному критерию технологического изнашивания Ит поверхностей сложного профиля бандажей колесных пар подвижного состава. Формальное определение интересующего нас критерия можно получить, рассматривая интеграл

где подынтегральная функция F зависит от х, так как включает функцию и ее первую производную. Пределы интегрирования х1 и х2 считаются фиксированными по сечениям проекции профиля бандажа (О – g) на вертикальную ось в соответствии с рисунком 2.11. Параметр глубины резания, как подынтегральная функция у (х) явно не зависит от х, а от графика профиля, тогда уравнение интегрального критерия изнашивания по объему и массе снятого металла М, позволяет обоснованно прогнозировать ресурс бандажей с учетом износа гребня, проката, ползунов и температурных раковин: V = y2dx.
Объем снимаемого металла V, м , находим по интегральным поверхностям параллельных сечений профиля бандажа колесной пары [78].

где V и V – объемы металла, соответственно до и после обточки, м ;
у = / (х) – функция, есть кривая вращения вокруг оси Ох, образующая
поверхность искомого тела вращения;
О, а, Ь, с, d, е, g – пределы интегрирования.
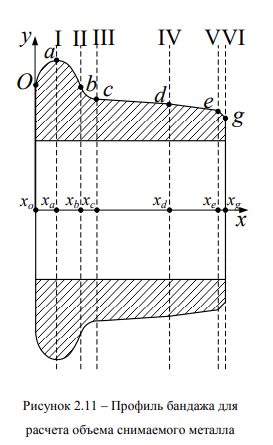
Тело вращения делится секущими плоскостями (О-VI) на участки, проекции которых на вертикальную плоскость имеют явно выраженные линейные и нелинейные формы по оси Ох.
V = V – v2 = |
Участки О—I и I-II могут иметь форму параболы, гиперболы или конуса. Участок II—III определяется радиусом R = 13,5 мм или R = 15 мм. Участки III—IV, IV—V, V-VI – преимущественно – произвольные кривые, характеризующие прокат, наличие ползуна, раковин и т.д. Необходимо у1 и у]– выразить на интегралах (х0-хё), по ^а – угла наклона к оси Ох.
Тогда масса снятого металла бандажа М кг, будет определяться по выражению (2.5)

Например, объем снимаемого металла V и его масса М при глубине резания равной 5 и 10 мм для профиля бандажа локомотива по ГОСТ 11018-87 [79], в соответствии с рисунком 2.12 и таблицей 2.1, с диаметром 1050 мм и гребнем толщиной 33 мм, приведен в таблице 2.2. Глубина резания примерная. В эксплуатационных условиях толщина бандажей может сокращаться от 20 до 25 мм, после одной обточки [70].
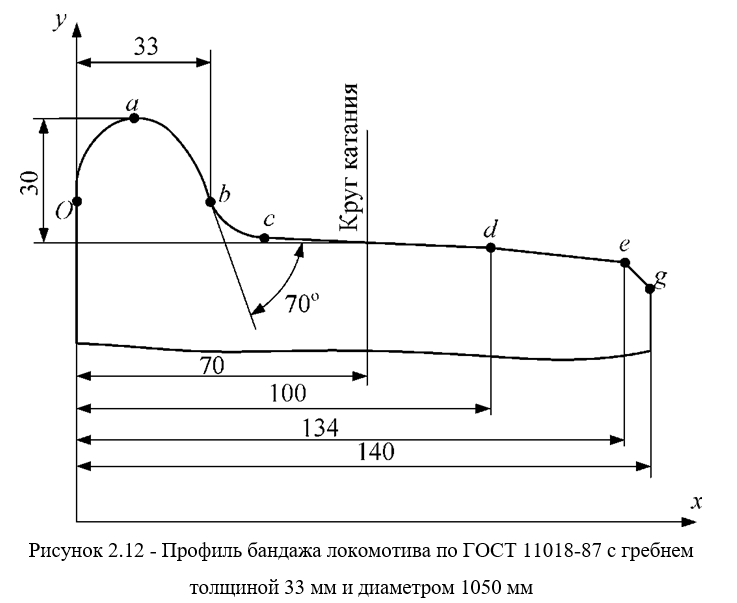
Геометрические координаты профиля бандажа локомотива по ГОСТ 11018-87 с гребнем толщиной 33 мм представлены в таблице 2.1.
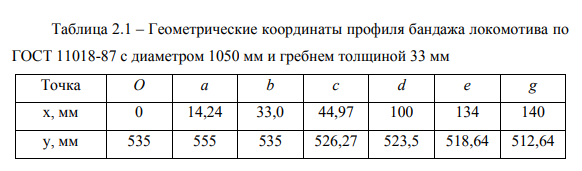
Расчетами установлено, что при глубине резания бандажа , равной 5 мм с первоначальным диаметром по кругу катания 1050 мм, объем снимаемого металла -5
(1.5), будет равен V « 2341,2 см , а масса снятого металла с одного бандажа (1.6), будет равна м = 4 кг. Для двух бандажей одной КП масса составит примерно 8 кг.
В таблице 2.2 приведены массы снятого металла при различной глубине резания и различном диаметре колес локомотива.
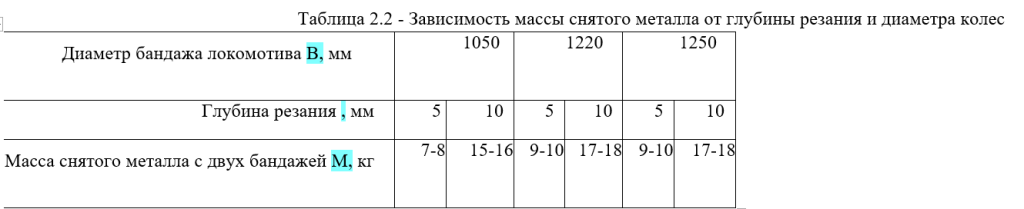
Выводы
Характер неисправностей обрезиненных шарниров и их металлических деталей создает, в межремонтный период эксплуатации локомотивов, несоответствие нормативных параметров (320±0,2 мм) четырех буксовых поводков каждого КМБ, следствием которого является перекос оси колесной пары в раме тележки тепловоза от 2 до 14 мм. 2. Шарниры буксовых поводков необходимо изготовлять из износостойких конструкционных материалов.