Сейчас ваша корзина пуста!
Материлы и методы исследования
Цикл статей:
Глава 1 – Формирование структуры и свойств при плазменной наплавке износостойких покрытий на медь и высокоуглеродистую, марганцовистую стали
Глава 2 – Материлы и методы исследования
Глава 3 – Разработка конструкции плазмотрона с расширяющимся каналом сопла для плазменной наплавки
Глава 4 – Плазменное нанесение жароизносостойкого покрытия на медную основу
Материалы и требования к ним
Материал кристаллизаторов непрерывной разливки должен быть достаточно теплопроводным и жаропрочным, химически неактивным по отношению к расплаву, достаточно твердым и износостойким, выдерживать длительные термосмены в диапазоне рабочих температур разливки, обладать стабильностью свойств.
Традиционным материалом для кристаллизаторов является медь (табл. 2.1). Но она в какой-то мере взаимодействует с расплавом, имеет довольно низкую твердость (НВ 0,8-1,0 ГПа), а также довольно существенно разупрочняется в интервале температур (250 -300 °С) вследствие собирательной рекристаллизации.
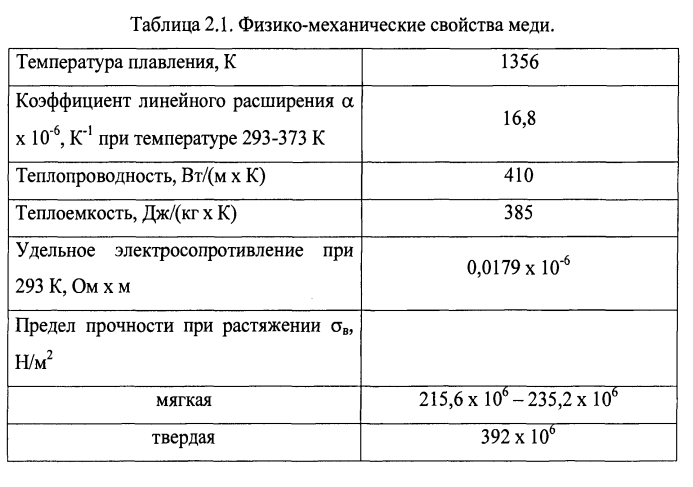
Железнодорожная крестовина.
Отливки для тяжелонагруженных деталей, работающих под действием статических и высоких динамических нагрузок и от которых требуется высокая, износоустойчивость, относится к аустенитному классу, фазовый состав которой представляет собой аустенит (у – твердый раствор легирующих элементов в железе) и карбидная фаза переменного состава (Ре,Мп)3С.
Литая высокомарганцовистая сталь 110Г13Л (сталь Гатфильда) получила широкое применение для изготовления деталей, эксплуатируемых в условиях интенсивных ударных нагрузок и абразивного изнашивания благодаря способности высокомарганцовистого аустенита подвергаться наклепу и приобретать твердую износоустойчивую поверхность без изменения вязкости изделия в целом.
Высокомарганцовистая литая сталь Г13Л, имеет в своем составе – 0,9 – 1,4% углерода; 11,5 – 15 % марганца; 0,8 – 1,0 % кремния; хрома и никеля не более 1,0% и фосфора не более 0,12 % (ГОСТ 2176-77).
После закалки на аустенит сталь Г13Л имеет следующие средние значения механических свойств при испытании образцов на растяжение (табл. 2.2.) [54].
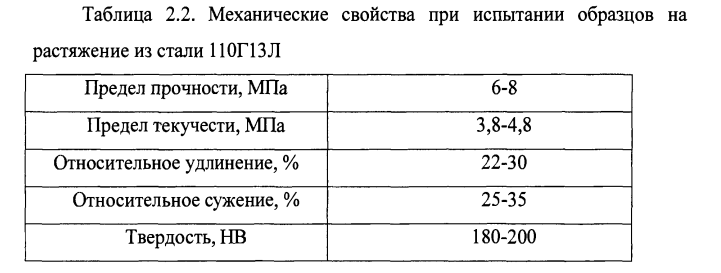
Свое ценное свойство подвергаться наклепу и получать износостойкую поверхность сталь Г13Л приобретает только в закаленном состоянии с чисто аустенитной структурой. Одновременно сталь Г13Л имеет ряд существенных недостатков, которые необходимо учитывать как при изготовлении и эксплуатации деталей, так и при наплавке:
- низкая изначальная твердость (НВ = 180 – 200 ) поэтому на первой стадии эксплуатации деталей происходит значительное смятие металла, осадка которого может достигать приблизительно 30% допустимого износа с одновременным деформационным упрочнением поверхности. После достижения определенной степени упрочнения поверхность детали подвергается в основном истиранию; в дальнейшем смятие продолжается, однако протекает значительно медленнее [72]. При холодном наклепе марганцовистая сталь может повышать твердость до НВ=300 – 500. Для получения максимальной твердости НВ.С>50 нужно применять ударную силу свыше 752 кг /см2 [54].
- недостаточная структурная устойчивость высокомарганцовистого аустенита против распада при нагреве и охлаждении при сварке или наплавке с образованием твердых и хрупких структур, отличающихся малой вязкостью. По мнению многих исследователей [54] это снижает пластичность наплавленного слоя и может вызвать появление трещин, отколы и выкрашивание металла. Согласно диаграмме изотермического распада, приведенной в работе [73] распад аустенита происходит в интервале температур 350 – 750 °С при выдержке более 4 минут: в первую очередь происходит выпадение карбидов по границам зерен, при длительных выдержках происходят также выпадение карбидов внутри зерен. И, наконец, в области средних температур (400 – 550°С) при очень длительных выдержках выпадение карбидов сопровождается образованием перлита вокруг карбидов – твердость при этом повышается, ударная вязкость падает, а сталь становится магнитной.
- неблагоприятное для нагревов сочетание теплофизических свойств низкой теплопроводности и высокого коэффициента термического расширения, что делает сталь Г13Л очень чувствительной к образованию термических трещин [73].
В работе [54] приводятся следующие значения теплопроводности при 49 температуре от О °С до 1000° С (табл. 2.3):
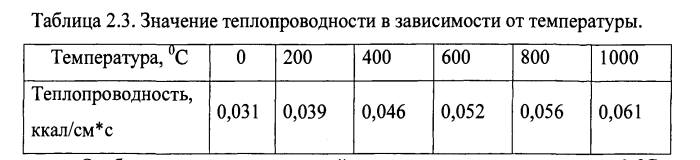
Особенно опасен ускоренный нагрев при температуре от 0 °С до 700 °С, то есть в области, где теплопроводность слишком низка. Известно, что теплопроводность стали резко уменьшается с возрастанием в ней марганца и углерода. Так, например, теплопроводность марганцовистой аустенитной стали, содержащей 1,2% углерода и 12% марганца, в 3,5 раза меньше, чем углеродистой [54]. В других исследованиях имеются указания на еще большую разницу в теплопроводности углеродистой и марганцовистой стали.
Коэффициент линейного расширения марганцовистой стали вдвое больше, чем углеродистой и колеблется в пределах от 18×10′6 1/град до 23×10′61/град в зависимости от температуры.
Рельс.
На железных дорогах, применяют рельсы из стали, имеющие высокое содержание углерода (0,65-0,82%) и перлитную или близкую к перлитной структуру. В таблице 2.4. приведен химический состав рельсовой стали.
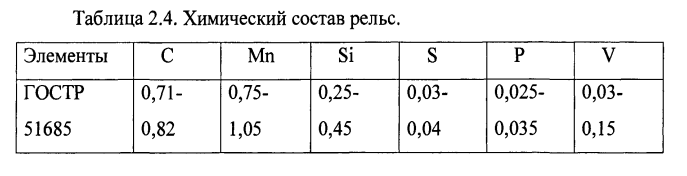
В работе использовался объемнозакаленный рельс. Объемнозакаленный рельс получают следующим образом. Полноразмерные рельсы нагревают в печи до 830 °С, закаливают в масле и затем повторно нагревают и отпускают при 500 °С. При такой технологии удается получить мелкодисперсную перлитную структуру по всему сечению рельса [74].
В табл. 2.5. представлены механические свойства рельсов.
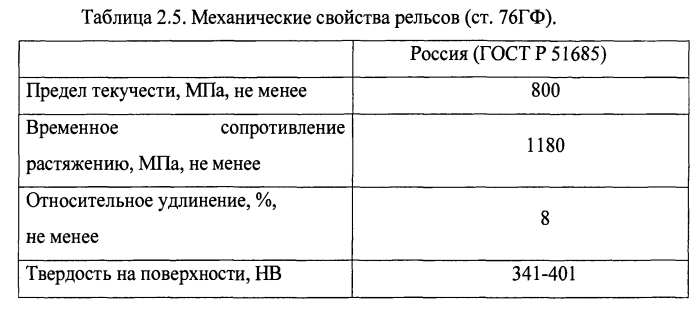
Вязкость разрушения для рельсовых сталей может быть оценена показателем ударной вязкости. В соответствии с Российским стандартом ГОСТ Р 51685 . 2000 ударная вязкость должна быть не менее 25 Дж/см2 при температуре +20 °С.
Наплавочные материалы.
При наплавке на медь в качестве материала покрытия использовали металлический порошок из жароизносостойкого сплава Б02 марки ПРИТУХ 15СЗР2, химический состав которого следующий: № – 77%, Сг – 15 %, С – 0,5%, 81 – 3,2%, В – 2% и Ре – до 5% (см. раздел 1.5).
При наплавке на рельсовую сталь и сталь Гатфильда в качестве наплавочного материала применяли – металлический порошковый сплав ПР – 65Х25ПЗНЗ (с условным названием «ИЗ»), соответствующий химическому составу электродам ЦНИИН-4 и изготовленный по спецзаказу на заводе “Тулачермет” (химический состав по заводскому сертификату качества: основа – железо, 25,25% хрома, 13,26% марганца, 3,5% никеля, 0,8% кремния, 0,8% углерода и 0,024% фосфора).
Методы исследования.
При проведении исследования химического и фазового составов, микроструктуры и механических свойств после плазменного нанесения хромоникелевого порошка использовали современные методы.
Для проведения исследования распределения макроструктуры и твердости по сечению покрытия и медной основы из образца наплавки вырезались поперечные темплеты размером ~ 20×30 мм, захватывающие зоны металла наплавки и основного металла Си. Травление осуществлялось «нитале» (3 % НЫОз) при комнатной температуре.
Твердость по глубине наплавленного слоя определялась по методу Роквелла шариком при нагрузке 100 кг в соответствии методикой ГОСТ 9013.
Замеры микротвердости по глубине наплавленного слоя проводились на приборе ПМТ-3 с нагрузкой 0,981 Н.
Для определения прочности покрытия проводили испытания на растяжение образцов, вырезанных из поверхности наплавленного металла. Испытания проводили на машине “ИНСТРОН” со скоростью деформации 1,1 *10′3 сек’1 на плоских образцах длиной 30 мм.
Испытания на срез, моделирующие напряжения в поверхностном слое стенки кристаллизатора, возникающие в процессе эксплуатации, проводили на машине «ИНСТРОН» со скоростью движения траверсы 0,2 см/мин с записью диаграммы нагрузка-деформация. Схема нагружения представлена на рис. 2.1. Поперечные образцы имели сечение 10×3,5 мм. Испытывали металл наплавки, переходной зоны и медную подложку.
Исследования износостойкости металла покрытия проводили методом нанесения непрерывной царапины на поперечном шлифе образца с покрытием. Царапина наносилась алмазной пирамидкой при постоянная нагрузке 50 г. При увеличении х470 проводили замер лунки через каждые 0,05 мм. Износ оценивали, как величину пропорциональную квадрату ширины лунки, поскольку именно эта величина отражает потери материала при нанесении царапины конусом пирамиды.
Микроструктура наплавленной зоны исследовалась на поперечных и косых шлифах, протравленных в 3% растворе НМО3.
Рентгеноструктурным методом оценивали уровень остаточных микронапряжений (по ширине рентгеновских интерференций (311) металла). Рентгенографировали образцы с наплавкой как с поверхности наплавки, так и по сечению образца, в том числе и медной подложки, на рентгеновском дифрактометре ДРОН-3 в Ре – излучении в режиме записи дифрактограмм, в диапазоне углов Вульфа – Брегга от 52-146°. Угловая скорость счетчиков импульсов 1°/мин, скорость движения диаграммной ленты 2400мм/час, щели гониометра 1×0,5 мм. Отметка углов через 0,1°.

При проведении комплексного исследования состава, структуры и механических свойств после плазменной наплавки хромомарганцового порошкового сплава 65Х25Г13НЗ на рельсовую сталь и сталь Гатфильда использовали следующие методы.
Химический состав определяли спектральным методом на приборе 8РЕКТВО «БАВ 8».
Твердость по глубине наплавленного слоя определялась по методу Роквелла шариком при нагрузке 100 кг в соответствии методикой ГОСТ 9013.
Испытания на растяжения проводили на универсальной испытательной машине «ИНСТРОН» с записью диаграмм растяжения. Скорость деформации составляла 1 х 10′3 сек.’1.
Испытания на ударную вязкость проводили при комнатной температуре +20 °С на образцах основного металла (ОМ) и наплавленного металла (НМ) размером 10x8x55 мм с круглым надрезом вырезанных на расстоянии 0 мм и 10 мм от границы наплавки.
Испытания на статический изгиб также осуществляли на универсальной испытательной машине «ИНСТРОН» при скорости нагружения 0,2 см/мин. с записью диаграммы нагрузка-деформация. Испытания проводили на образцах с круглым надрезом, а также на образцах без надреза.
Поверхность разрушения исследовали на сканирующем электронном микроскопе «НОК1ВА» с микроанализатором «Ыпк РХ 2000» при увеличении х 35-500.
Исследование микроструктуры проводили на поперечных и продольных шлифах. Выявление микроструктуры основного металла проводили путем травления в 10 % НС1, а металла наплавки в 3% НМО3.
Рентгеносъемки проводили на дифрактометре ДРОН-3 в Ре-излучении на продольном и поперечном шлифах в направлении по глубине наплавки края шлифа, что означало соответствующее расстояние от поверхности наплавки. В том числе рентгенографировался участок границы наплавки.
Дифрактограммы записывали в Ре-излучении в области углов 20 Вульфа-Бреггов 20=44-136°. Щели гониометра 1×0,5 мм. Угловая скорость перемещения счетчика импульсов 1°/мин. Фазовый состав определяли по межплоскостным расстояниям б. Напряженное состояние – по ширине интерференционных линий аустенита (311) и (111).
Локальную концентрацию микронапряжений оценивали из доли площади «хвостов» дифрактограмм к общей интенсивности (площади) дифрактограмм.
Список литературы
26. Югансон Э.Ю. Исследование процессов соединения меди и ее сплавов со сталью и чугуном струей перегретого металла. Труды института металлургии им. Байкова, вып. 2,1957.
27. Тысовская С.Е. Новый способ наплавки бронз на чугун и сталь. ЛДНТП, №90,1958.
28. Вайнерман А.Е., Красулин Ю.Л., Шоршоров М.Х. Плазменная наплавка меди и бронз на сталь плазменной струей. – «Автоматическая сварка», 1966.
29. Лахтин Ю.М. Металловедение и термическая обработка металлов. М.: Металлургия, 1984. 360 с.
30. Дудко Д.А., Лакиза С.П. О новых возможностях сварки высокотемпературной дугой, сжатой газовым потоком. «Автоматическая сварка», 1960, № 11.
31. Каленский В.К. и др. Исследование и разработка способа автоматической наплавки клапанов автомобилей. «Автоматическая сварка», 1963, №1.
32. Красулин Ю.Л.., Кулагин И.Д. Регулирование температуры сварочной ванны при наплавке плазменной струей – «Автоматическая сварка», 1966, №9.
33. Гладкий П.В., Фрумин И.И., Плазменная наплавка с присадкой порошков. Резка, наплавка и сварка сжатой дугой. М., ЦИНТИхимнефтемаш, 1968.
34. Л.А.Арцимович, Элементарная физика плазмы, Госатомиздат,1963.
35. Финкельбург В., Меккер Г. Электрические дуги и термическая плазма. Иностранная литература, Москва, 1961.