Сейчас ваша корзина пуста!
Модернизация буксы с целью повышения ресурса подшипников
Цикл статей:
Глава 1 – Повышение ресурса буксовых подшипников грузовых вагонов
Глава 2 – Исследование влияния динамической нагруженности на ресурс буксового подшипника
Глава 3 – Модернизация буксы с целью повышения ресурса подшипников
Скорректированный ресурс буксовых подшипников и пути его повышения
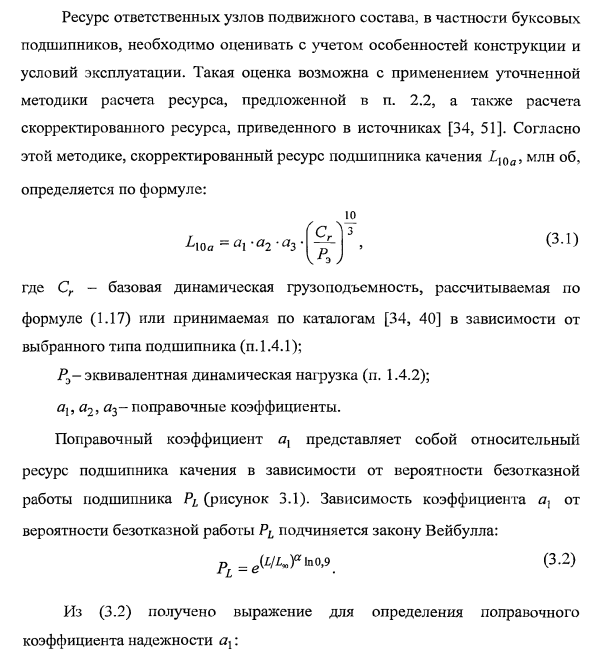
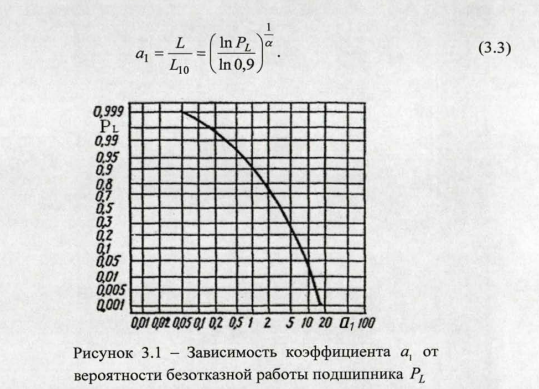
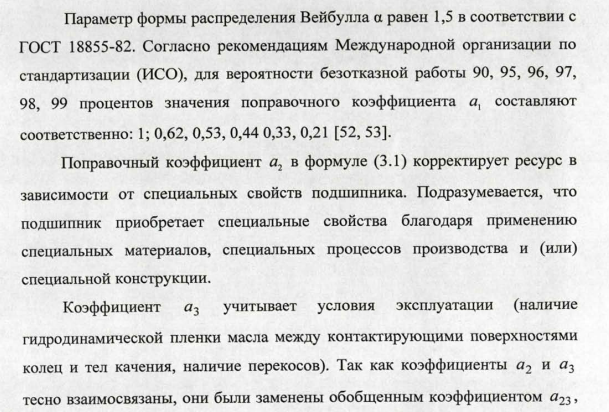
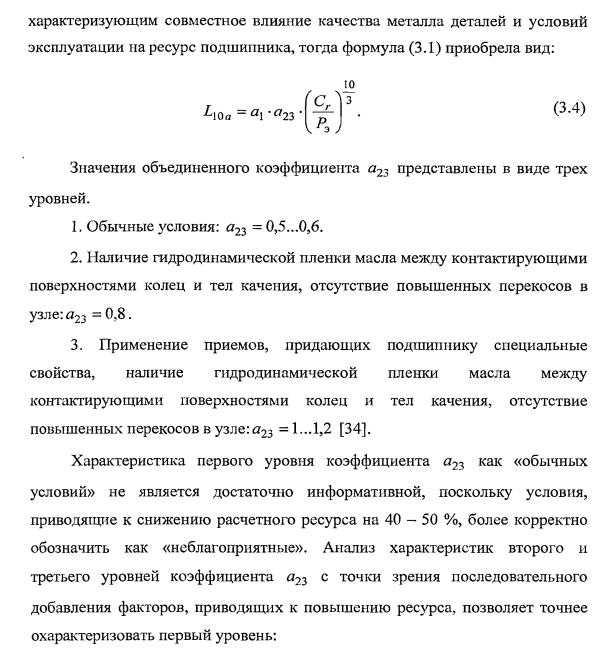
- наличием перекосов в узле,
- неудовлетворительными условиями смазывания,
- отсутствием приемов, придающих подшипнику специальные свойства.
Характеристике первого уровня коэффициента а23 вполне соответствуют условия работы и конструктивные особенности двух радиальных роликовых подшипников в буксах железнодорожного подвижного состава, в частности, грузовых вагонов. Два однорядных роликоподшипника, последовательно монтируемых на шейку оси, работают под комбинированной нагрузкой, горизонтальная составляющая которой приводит к перекосу тел качения в двух плоскостях, нарушению равномерного распределения давления вдоль образующих и резкому ухудшению условий смазывания. Уточненный расчет ресурса подшипников с учетом перекоса тел качения в вертикальной плоскости показал снижение ресурса от 35 до 43 % (п. 2.2), что соответствует первому уровню коэффициента а23, равному 0,5…0,6.
Существенным аргументом в пользу принятия такого значения является допущение, что динамическая грузоподъемность тандема из двух цилиндрических роликоподшипников, работающих в одном узле, приравнивается к динамической грузоподъемности двухрядного подшипника (подразумевается идеальное качество изготовления и установки). В действительности имеют место недостаточная точность, разноразмерность и отклонения в геометрии колец и тел качения, наличие двух отдельных посадок поверхностей внутренних колец и погрешности торцевой затяжки. Существенные отклонения от идеальных условий для развития максимальной грузоподъемности наряду с неравномерным распределением нагрузки между подшипниками, подтверждают правомерность применения первого уровня коэффициента а2 3, равного 0,5… 0,6, при расчете
скорректированного ресурса буксовых подшипников.
Пути повышения скорректированного ресурса буксовых подшипников грузовых вагонов, согласно критериям, определяющим значение коэффициента а23, состоят в следующем.
1. Принятие мер для исключения перекосов в узле с соответствующим улучшением условий смазывания (позволяют принимать значение коэффициента а23, равное 0,8). В качестве такого решения предлагается раздельное восприятие радиальной нагрузки и рамной силы путем введения в конструкцию буксы шарового подпятника (п. 3.2). Модернизация буксы путем введения шарового подпятника позволяет исключить воздействие рамной силы на буксовые подшипники. При этом расчет скорректированного ресурса с учетом только радиальной нагрузки становится объективным и отражающим реальные условия эксплуатации.
2. Применение приемов, способствующих приобретению подшипником специальных свойств: специальных материалов, специальных процессов производства, специальной конструкции при условии отсутствия перекосов (позволяет принимать значение коэффициента а23, равное 1… 1,2).
К применению специальных материалов относятся, в частности, электрошлаковый и вакуумно-дуговой переплавы подшипниковой стали, введение в ее состав различных легирующих элементов, а также химико- термическая обработка [54, 55, 56].
Под применением специальных процессов производства и специальной конструкции можно понимать конструктивное совершенствование подшипникового узла с целью обеспечения возможностей для повышения точности изготовления и монтажа, улучшения условий работы и обеспечения оптимальной динамической нагруженности элементов. Применительно к повышению скорректированного ресурса буксовых подшипников введение в буксу шарового подпятника дает возможность дальнейшей модернизации буксы путем применения двухрядного роликового подшипника с безбортовыми кольцами (п.3.3). Последовательная реализация двух предложенных уровней модернизации буксы грузового вагона приведет к повышению значения скорректированного ресурса, отражающего конкретные условия работы и особенности конструкции подшипникового узла.
Первый уровень модернизации буксы: введение шарового подпятника
Введение шарового подпятника в буксу грузового вагона представляет собой результат построения опоры комбинированного нагружения с раздельным восприятием радиальной и горизонтальной поперечной нагрузки, принципиальная схема представлена на рисунке 3.2.
В типовую конструкцию буксы предлагается ввести шаровой подпятник 4 [57], состоящий из шара, размещенного между опорами. Назначение подпятника — воспринимать рамную силу, которая в применяемой буксе действует на торцевые поверхности бортов роликовых подшипников. При отсутствии рамной силы удержание шара в нерабочем положении на определенном расстоянии от опоры осуществляется посредством упругого элемента 5.
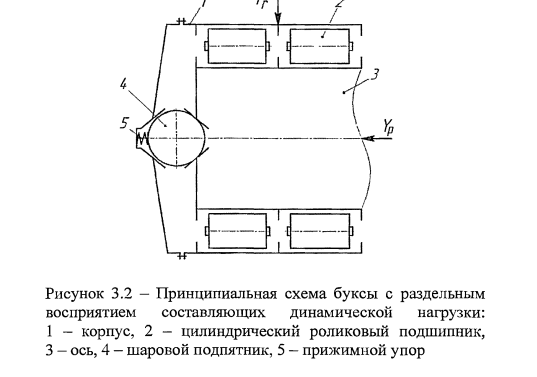
С целью сведения к минимуму затрат на модернизацию конструкции буксы, целесообразно сохранить без изменений конструкцию торцевого крепления подшипников, в частности, тарельчатой шайбы, применяемой в настоящее время. Диаметр отверстия в шайбе согласно ГОСТ 22780-93 составляет 53 мм. При выборе в качестве шара тела качения из стандартной номенклатуры свободных деталей для шарикоподшипников, его максимальный стандартный диаметр не должен превышать 50,8 мм (2 дюйма).
Предлагаемый шаровой подпятник работает по принципу упорных подшипников скольжения. Описание и расчет подпятников скольжения приведены в источниках [46, 58, 59, 60,]. В работе [59] среди упорных подшипников скольжения выделен особый вид подшипников, воспринимающих нагрузку путем упора в сферу с центром по оси вращения вала. Несущая способность таких подшипников определяется контактными напряжениями, которые зависят от формы соприкасающихся поверхностей. Наиболее высокие напряжения возникают при контакте двух сфер, меньшие – при контакте плоской поверхности со сферой и наиболее низкие — при контакте сферы со сферической вогнутой поверхностью радиусом, равным 1,01 — 1,02 от радиуса сферы. Во всех случаях напряжения уменьшаются с увеличением диаметра сфер. Опорные тела рекомендуется изготавливать из шарикоподшипниковых сталей типа ШХ15, ШХ15СГ и подвергать термической обработке до твердости 62 – 65 НЯС [61]. Подчеркивается, что из всех вариантов подпятников со сферическими опорными поверхностями наиболее предпочтительна конструкция с полным шаром. Такая схема обладает тем преимуществом, что шар вследствие практически всегда имеющейся несоосности опорных поверхностей, проворачивается при работе, и износ равномерно распределяется по его поверхности.
Для подбора материала и оптимальных геометрических параметров шара и опор аналитически определены напряжения в местах контактирования сопряженных поверхностей на основе нормальной задачи Герца о сжатии двух упругих тел [62], которая нашла широкое применение для инженерных расчетов контактной прочности деталей машин. Кроме того, выполнено моделирование напряженно-деформированного состояния элементов подпятника методом конечных элементов.
Согласно теории Герца, если поверхности тел описываются уравнениями второго порядка, пятно контакта имеет эллиптическую форму и закон распределения контактных давлений, соответствующий такой форме пятна, должен быть эллипсоидальным.
Теории упругости и решению контактных задач посвящены работы И. А. Биргера [63], Ю. Е. Власенко [64], Л. А. Галина [65], И. Г. Горячевой[66], Д. Гудьера [67], Н. Б. Демкина [68, 69], К. Джонсона [70], А. Н. Динника [71], Б. С. Ковальского [72, 73], В. С. Коссова [74], С. П. Новикова [75], В. В. Новожилова [76], А. А. Ольшевского [77], В. И. Сакало, [74], Р. В. Саусвелла [78], Ю. П. Подлеснова [79], Э. В. Рыжова [69, 79, 80], С. П. Тимошенко [67], А. П. Филина [81].
Для выбора оптимальной конструкции шарового подпятника необходимо оценить максимальные напряжения в контакте шара с опорными поверхностями и сравнить с предварительно назначенными допускаемыми напряжениями.
Назначение допускаемых напряжений
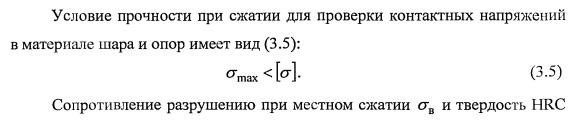
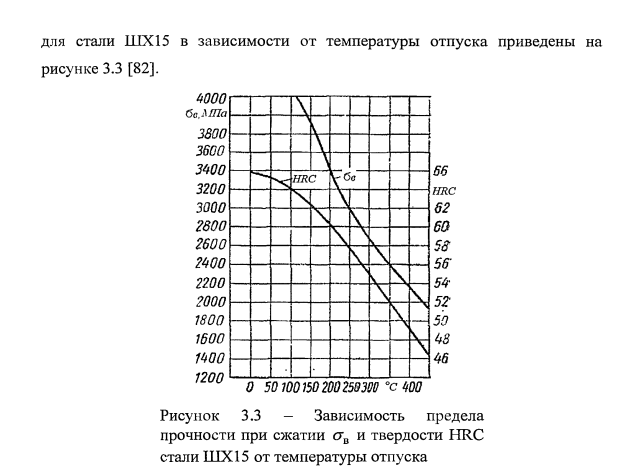
При выборе размеров и материала для элементов шарового подпятника необходимо обеспечить запас против разрушения или остаточных деформаций. Если принять в качестве материала для опор сталь ШХ15 твердостью 62 НЯС, предел прочности при сжатии которой составляет 3000 МПа, то материал шара выбирается несколько тверже, например, сталь ШХ15 твердостью 64 НRС (предел прочности при сжатии 3200 МПа).
Для гарантированного предотвращения разрушения вследствие избыточных контактных давлений в элементах можно допускать напряжения, составляющие по величине только часть от предела прочности материала, то есть с учетом коэффициента запаса прочности.
Коэффициент запаса должен быть выбран с тем расчетом, чтобы был обеспечен запас против появления опасного состояния материала. При воздействии нагрузки на элементы из пластичных материалов опасное состояние характеризуется появлением больших остаточных деформаций (явление текучести). Допускаемое напряжение, превышение которого приводит к наступлению опасного состояния для пластичных материалов определяется по формуле [ (83)]:
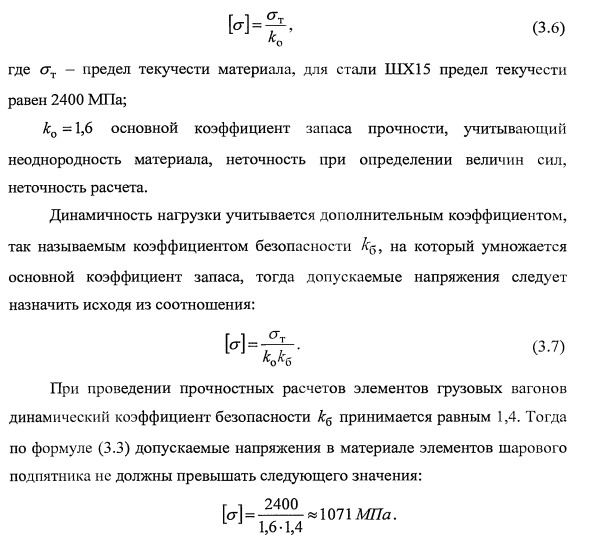
Расчет контактных напряжений в деталях подпятника
С целью обеспечения минимальных контактных напряжений выбраны опорные поверхности для шара, имеющие форму вогнутой сферы (рисунок 3.4). Максимальное значение контактных напряжений при сжатии шара радиусом Яу с вогнутой сферической опорой радиусом Я2 силой Е определяется по формуле [84]:
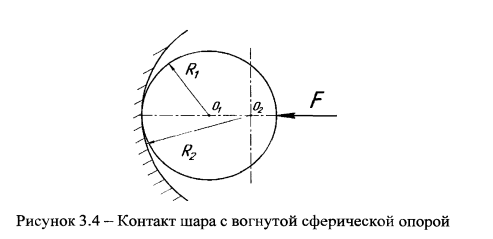
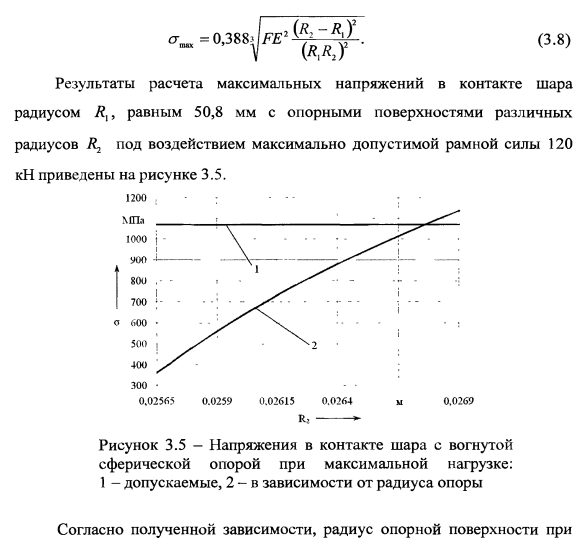
назначенной величине допускаемых контактных напряжений 1071 МПа должен находиться в пределах 25,4 — 26,7 мм. Этот интервал полностью согласуется с рекомендациями [59], в соответствии с которыми для дальнейших расчетов был принят радиус опоры Л,, равный 25,65 мм, что составляет 1,01 от В^. Результаты расчета контактных напряжений в зависимости от приложенной нагрузки при взаимодействии шара радиусом 25,4 мм из стали ШХ15 с вогнутой сферической опорой радиусом 25,65 мм из того же материала приведены на рисунке 3.6.

Как видно из рисунка 3.6, под воздействием максимально допустимой рамной силы контактные напряжения в сопряженных элементах подпятника достигают не более трети назначенного допускаемого значения.
Конструкция и принцип работы шарового подпятника
Шаровой подпятник буксы грузового вагона [57] представлен на рисунке 3.7. Разработанная конструкция содержит пяту 1 с вогнутой сферической поверхностью, собственно подпятник в виде шара 2, осевую опору 3 с вогнутой сферической поверхностью, ось 4, корпус 5 осевой опоры 3. Пята 1 выполнена с конусом 6, между торцовыми поверхностями пяты 1 и оси 4 размещена регулировочная шайба 7. Осевая опора 3 установлена с гарантированным натягом в корпусе 5. На цилиндрической поверхности опоры 3 с зазором установлен упор 8 с конической поверхностью 9.
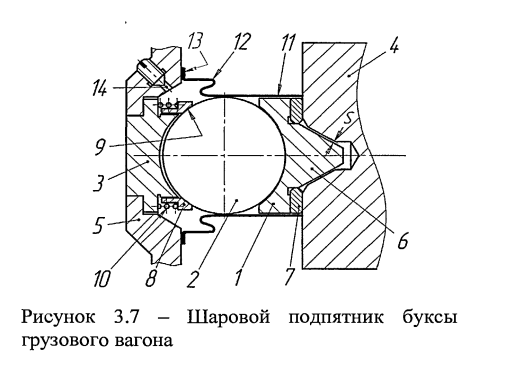
Упор 8 посредством упругого элемента 10 отжимает подпятник 2 от вогнутой сферической поверхности опоры 3. На подпятник 2 установлена герметизирующая втулка 11 с упругим элементом 12, обеспечивающим постоянный контакт фланца 13 втулки 11с корпусом 5 осевой опоры 3. Для заполнения рабочей полости подшипника смазочным материалом в корпусе 5 выполнено отверстие 14.
При сборке подшипника требуемый зазор между коническими поверхностями пяты 1 и центрового отверстия оси 4 устанавливают с помощью регулировочной шайбы 7 путем изменения ее толщины. Равенство диаметров втулки 11 и подпятника 2 обеспечивает предварительное центрирование и удержание подпятника 2 во втулке 11 перед установкой корпуса 5 с осевой опорой 3, упором 8 и упругим элементом 10.
В процессе проектирования шарового подпятника буксы грузового вагона с учетом предполагаемых габаритов в качестве упругого элемента выбрана витая пружина из круглой проволоки (рисунок 3.8) со следующими параметрами [46, 85]:
диаметр сечения витка (диаметр проволоки): d = 3,8 мм,
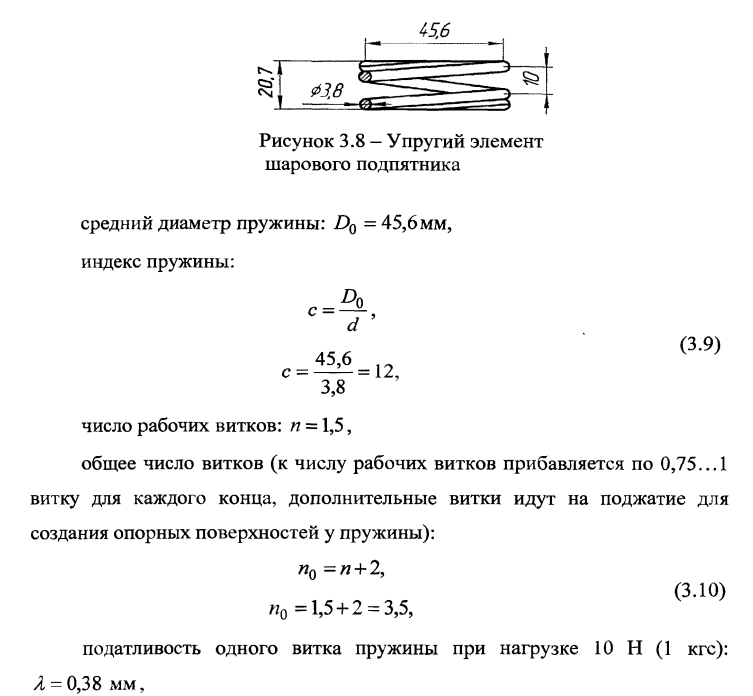
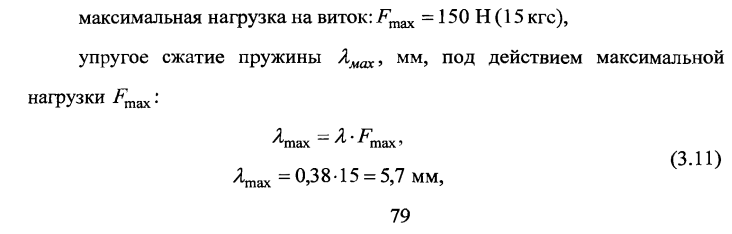
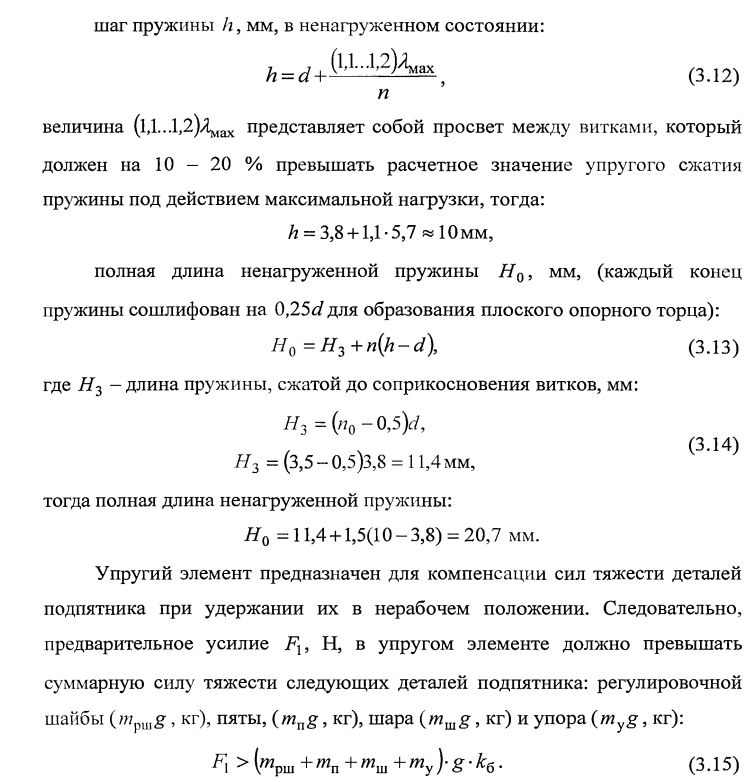
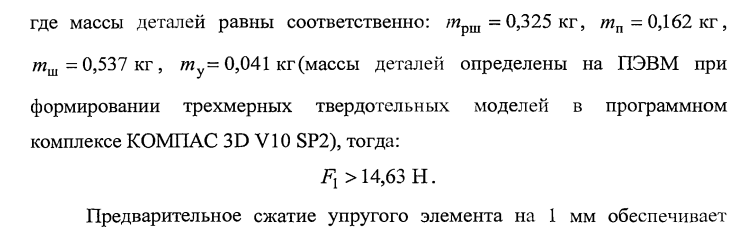

Подпятник работает следующим образом. Под воздействием боковой силы на ось колесной пары пята 1 упирается в сферическую поверхность подпятника 2 и далее усилие воспринимает сферическая поверхность опоры 3, при этом коническая поверхность 9 упора 8 прижимается к сферической поверхности подпятника 2, а торцевые поверхности втулки 11 — к торцевым поверхностям корпуса осевой опоры 5 и оси. Вращение оси передается подпятнику, который опирается на вогнутые сферические поверхности пяты 1 и опоры 3 большего радиуса. Наличие смазочного материала в рабочей полости подпятника и, соответственно, в зазорах подвижных сферических соединений обеспечивает высокую работоспособность подпятника. Следует заметить, что шар при взаимодействии с конической поверхностью упора вследствие всегда имеющейся несоосности опорных поверхностей проворачивается при работе и износ распределяется равномерно по его поверхности. Изменение положения оси под нагрузкой сопровождается радиальными и угловыми смещениями ее торцевой поверхности. Наличие зазора 5 между коническими поверхностями пяты и центрового отверстия оси, определяемого значениями величин этих смещений и получаемого путем изменения толщины регулировочной шайбы, обеспечивает самоцентрирование сферической поверхности пяты.
Шаровой подпятник представляет собой кинематическое соединение первого класса с пятью подвижностями для передачи горизонтальной поперечной нагрузки от торца шейки оси к опоре. Соединение состоит из последовательно соединенных кинематических пар «шайба-пята», «пята- шар» и «шар-опора». Нагрузка в кинематическом соединении первого класса воспринимается поверхностями звеньев, что обеспечивает меньшие значения контактных напряжений в сравнении с кинематическими парами первого класса с точечным или линейным контактом. Плоскостная кинематическая пара «шайба-пята» обладает тремя подвижностями в пределах зазора. Две поступательные подвижности служат для компенсации радиальных смещений шейки оси, вращательная подвижность является местной, безвредной для соединения. Сферическая кинематическая пара «пята-шар» обладает тремя вращательными подвижностями для компенсации угловых смещений шейки оси. Сферическая кинематическая пара «шар-опора» также обладает тремя вращательными подвижностями, которые являются местными и обеспечивают равномерный износ кинематических пар [86].
Введение смазочного материала в рабочую полость подпятника, удержание его в зонах трения сферических поверхностей, самоцентрирование пяты при радиальном и угловом смещениях торцевой поверхности оси обеспечивают значительное повышение ресурса подпятника, по сравнению с известными подшипниками со сферическими упорными поверхностями. Реализация первого уровня модернизации буксы путем применения шарового подпятника исключает воздействие рамной силы на подшипники, следовательно, предотвращает перекосы тел качения и нарушение условий смазывания. Тогда при расчете скорректированного ресурса L10а, млн об, по формуле (3.4) коэффициент а23 принимается равным 0,8 (п. 3.1). Это приводит к повышению ресурса:
по методике расчета скорректированного ресурса на 33 %; по предложенной уточненной методике расчета ресурса: на 35 — 43 % в зависимости от скорости движения.
Второй уровень модернизации буксы: совершенствование подшипникового узла
Разноразмерность и отклонения в геометрии посадочных поверхностей колец двух цилиндрических роликовых подшипников приводят к неравномерному распределению радиальной нагрузки, что вызывает перекос осей роликов, снижает быстроходность и нагрузочную способность подшипников, ухудшает условия их работы и существенно снижает ресурс.
Для исключения перечисленных последствий неравномерной нагрузки на подшипники предлагается двухрядный роликоподшипник с безбортовыми кольцами (рисунок 3.9) [87].
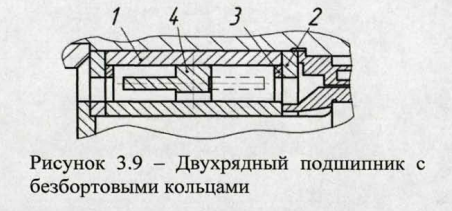
Для повышения быстроходности и нагрузочной способности подшипников наружное кольцо двухрядного радиального подшипника 1 с короткими цилиндрическими роликами предлагается выполнить в виде втулки без бортов с приставными кольцами 2 и направляющими кольцами 3, а сепаратор подшипника – с центрирующим пояском 4, контактирующим с внутренней поверхностью кольца. Наружное кольцо обеспечивает минимальные отклонения от цилиндрической формы посадочной поверхности, взаимодействующей с опорной поверхностью корпуса буксы. Цилиндрические поверхности внутреннего кольца позволяют исключить разноразмерность и отклонения форм дорожек качения для роликов. Это способствует более равномерному распределению нагрузки на тела качения. Расположение роликов в шахматном порядке обеспечивает возможность дополнительного нагружения ролика при двухрядном исполнении.
При этом торцевые поверхности пояска сепаратора и направляющих колец определяют симметричное расположение роликов подшипника
относительно торцов кольца. Сепаратор и направляющие кольца можно выполнять из антифрикционного материала или из легированной стали с антифрикционным покрытием.
Повышению точности размещения роликов между внутренним и наружным кольцами, уменьшению перекоса осей роликов при вращении способствуют центрирование сепаратора по наружному кольцу и осевое размещение роликов между точно ориентированными торцовыми поверхностями пояска сепаратора и направляющих колец. Отсутствие горизонтальной поперечной нагрузки на торцовые поверхности роликов, окружная подвижность опорных поверхностей направляющих колец позволяют увеличить быстроходность подшипника, а повышенная точность опорных поверхностей дорожек роликов – его нагрузочную способность.
Разработка отдельных конструктивных элементов на основе предложенной принципиальной схемы [108, 109, 110] позволила сформировать конструкции букс грузовых вагонов с двухуровневой модернизацией (Таблица 3.1).
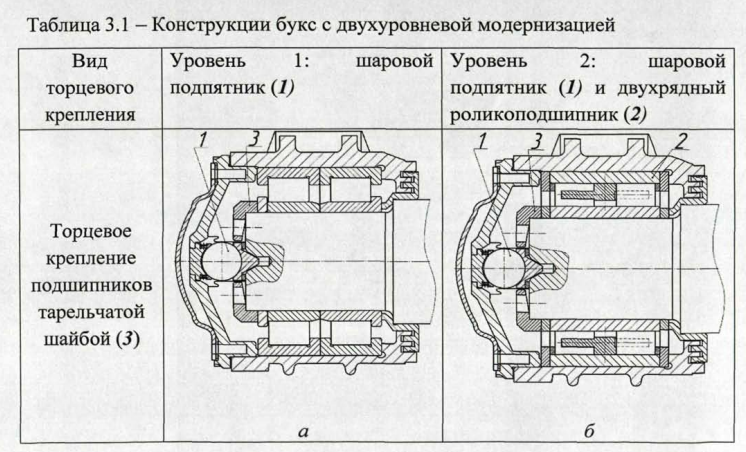
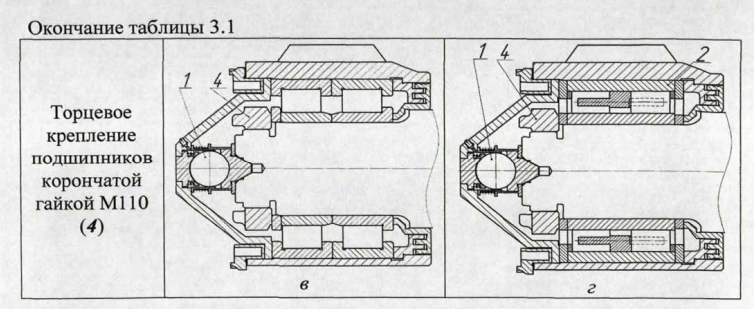
Последовательная реализация двух предложенных уровней модернизации буксы приводит к существенному повышению скорректированного расчетного ресурса подшипников модернизированной буксы в сравнении с ресурсом подшипников в буксе без модернизации. Результаты расчета скорректированного ресурса подшипников в буксах с различными уровнями модернизации приведены в таблице 3.2.
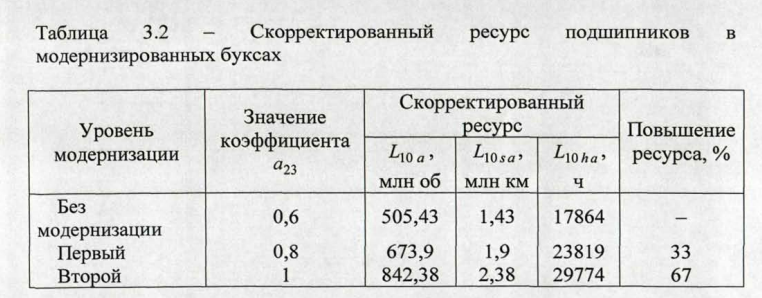
Моделирование напряженно-деформированного состояния деталей модернизированной буксы
При модернизации буксы в ее конструкцию вводится ряд дополнительных деталей, при этом изменяется схема передачи рамной силы на элементы торцевого крепления. Вместо торцевой поверхности наружного кольца подшипника нагрузка передается крепительной крышке через разработанный корпус опоры, в центральной части которого по неподвижной посадке смонтирована опора шарового подпятника. Такое изменение схемы передачи нагрузки потребовало оценки прочности разработанных деталей с исследованием возможностей оптимизации их формы.
Определение напряжений, возникающих в деталях модернизированной буксы, производилось на ПЭВМ методом конечных элементов с помощью программного комплекса твердотельного моделирования КОМПАС 3D VIO SP2 и расчетного комплекса АРМ Win Machine (модуля АРМ Studio), широко применяемых в настоящее время для решения инженерных задач при проектировании конструкций.
Были сформированы трехмерные модели деталей (пяты, шара, опоры и корпуса опоры) с последующим разбиением на конечные элементы в форме правильного тетраэдра [111, с. 308-312] со стороной 2 мм (рисунок 3.10, а – е). Моделям присвоены механические свойства: корпусу опоры — свойства стали 40Х ГОСТ 4543-81, пяте, шару и опоре — свойства стали ШХ15 ГОСТ 801-78.
Из моделей пяты шара и опоры составлена контактная сборка. Ограничения перемещений и поворотов по всем координатным осям наложены на поверхность опоры, сопряженную с корпусом опоры. К контактной сборке прилагалась максимально допустимая горизонтальная поперечная нагрузка 120 кН, передаваемая со стороны пяты через поверхность, сопряженную с регулировочной шайбой. Полученные значения напряжений не превышают предела текучести материала (рисунок 3.11). Максимальные напряжения в материале корпуса опоры при аналогичном экстремальном значении нагрузки 120 кН, крайне редко реализующемся в эксплуатации, не превышают предела текучести выбранного материала. Результаты моделирования напряженно деформированного состояния сплошного корпуса показали, что напряжения в конической части практически отсутствуют, что позволяет выполнить в ней отверстия (рисунок 3.10, б). Зависимость максимальных напряжений в центральной части корпуса опоры с отверстиями от величины приложенной горизонтальной поперечной нагрузки, приведена на рисунке 3.12. Отверстия в конической части корпуса опоры предназначены в первую очередь для осмотра буксы в пути следования поезда без демонтажа шарового подпятника. Кроме того, уменьшение массы корпуса опоры способствует экономии металла, снижению необрессоренной массы тележки с модернизированными буксами, а также облегчает физический труд слесаря РГТС при монтаже буксы.
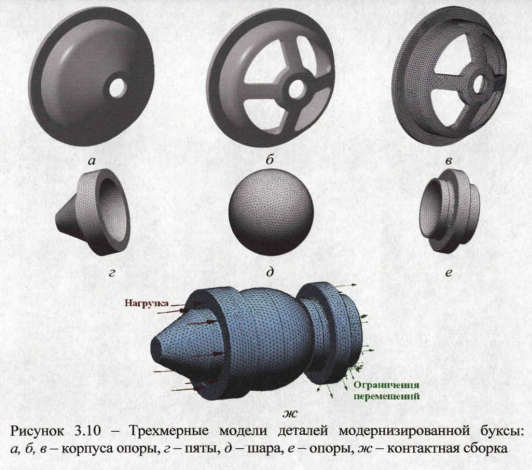
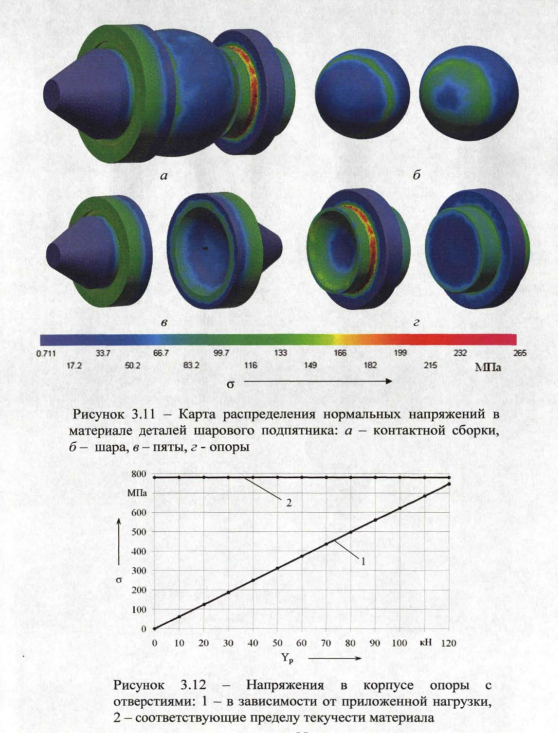
Методика расчета ресурса комбинированной опоры
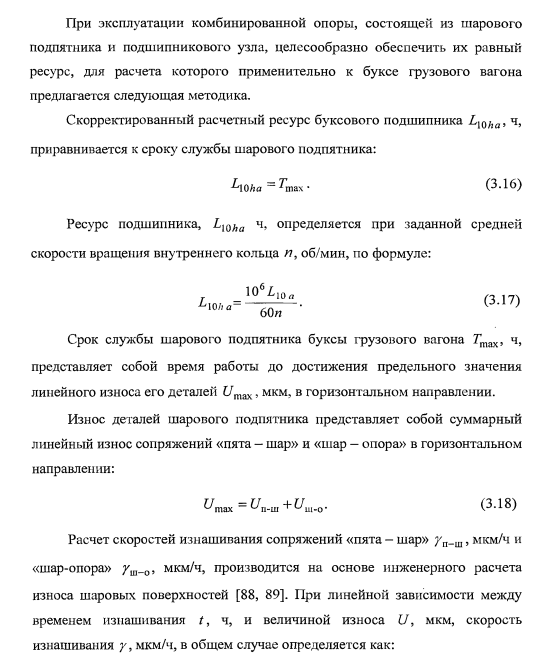
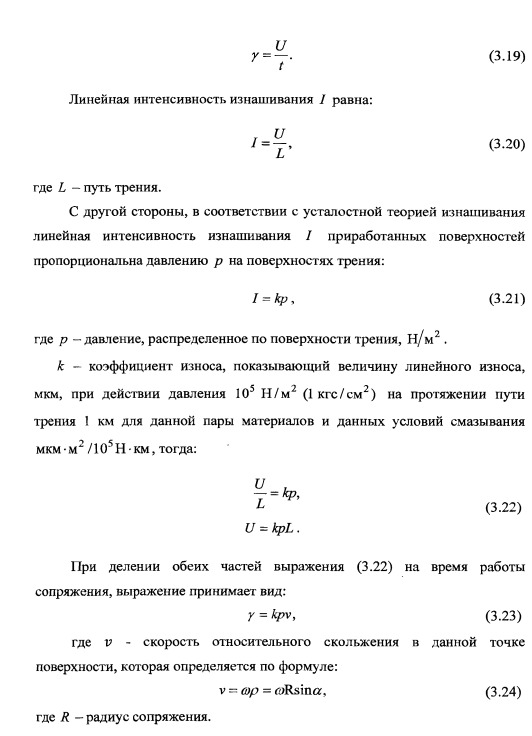
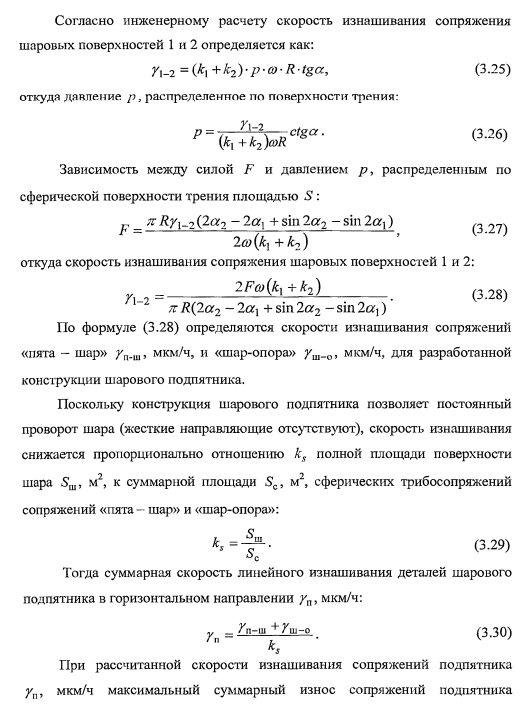
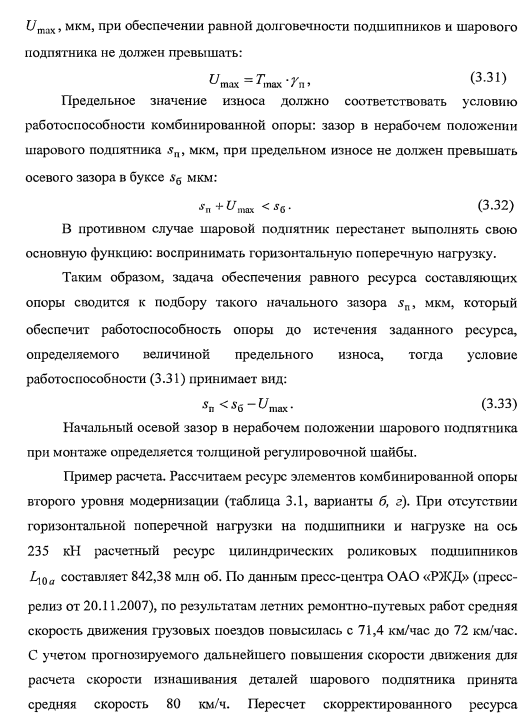
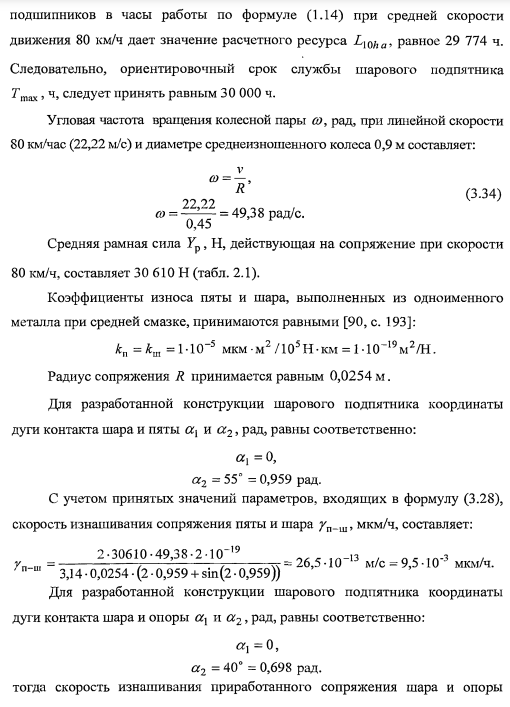
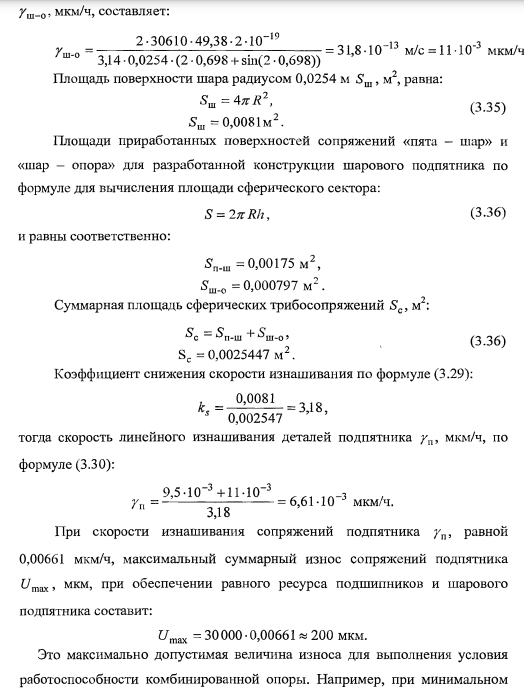
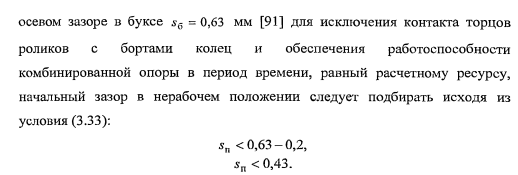
Выводы
При исследовании возможностей модернизации буксы грузового вагона с целью повышения ресурса роликовых подшипников были получены следующие результаты.
- Предложена принципиальная схема комбинированной опоры оси грузового вагона с раздельным восприятием радиальной нагрузки и рамной силы, содержащая роликовые подшипники и шаровой подпятник.
- Разработана конструкция шарового подпятника, обоснован выбор конфигурации опорных поверхностей, выполнен расчет контактных напряжений в основных элементах.
- Разработана конструкция двухрядного роликового подшипника с безбортовыми кольцами, предназначенного для применения в буксе с шаровым подпятником.
- Предложена двухуровневая модернизация буксы, приводящая к повышению ресурса роликовых подшипников до 67 %. Модернизация предусматривает сохранение типового корпуса буксы, торцевого крепления подшипников и центрового отверстия в шейке оси. Выполнены подбор упругого элемента и оценка прочности разработанного корпуса опоры шарового подпятника.
- Предложенная методика расчета ресурса комбинированной опоры оси грузового вагона позволяет обеспечить равный ресурс элементов путем подбора начального зазора в нерабочем положении шарового подпятника.
Список литературы
- Горячева, И. Г. Механика контактного взаимодействия / И. Г. Горячева. – М.: Наука, 2001. – 478 с.
- Тимошенко, С. П. Теория упругости / С. П. Тимошенко, Д. Гудьер. – М.: Наука, 1975. – 575 с.
- Демкин, Н. Б. Контактирование шероховатых поверхностей / Н. Б. Демкин. – М.: Машиностроение, 1970. – 227 с.
- Демкин, Н. Б. Качество поверхности и контакт деталей машин / Н. Б. Демкин, Э. В. Рыжов. – М.: Машиностроение, 1981. – 244 с.
- Джонсон, К. Механика контактного взаимодействия / К. Джонсон. – М.: Мир, 1989. – 509 с.
- Динник, А. Н. Удар и сжатие упругих тел / А. Н. Динник // Известия Киевского политехнического института, кн. 4. – Киев, 1909..
- Ковальский, Б. С. Напряжение на участке местного сжатия при учете сил трения / Б. С. Ковальский // Известия АН СССР. – 1942г.
- Ковальский, Б. С. Расчет деталей на местное сжатие / Б. С. Ковальский. – Харьков: ХВКИУ, 1967. – 222 с.
- Сакало, В. И. Контактные задачи железнодорожного транспорта / В. И. Сакало, В. С. Коссов. – М.: Машиностроение, 2004. – 496с.
- Новиков, С. П. Контакт массивного тела с цилиндрической оболочкой / С. П. Новиков // Динамика и прочность транспортных машин. – Брянск, 2000. – с.72-78.
- Новожилов, В. В. Основы нелинейной теории упругости / В. В. Новожилов. – JL: Гостехиздат, 1948. – 211 с.
- Ольшевский, А. А. Решение контактных задач с учетом микронеровностей поверхности контакта с использованием трехмерных базовых конченоэлементных схем / А. А. Ольшевский и др. // Динамика и прочность транспортных машин. – Брянск, 2000. С. 109 -118.
- Саусвелл, Р. В. Введение в теорию упругости / Р. В. Саусвелл. – М.: Гос. изд-ва иностранной литературы, 1941. – 675 с.
- Рыжов, Э. В. Решение контактных задач релаксационным методом конечных элементов / Э. В. Рыжов, В. И. Сакало, Ю. П. Подлеснов // Машиноведение. – 1980.-№6.- С. 64-69.
- Рыжов, Э. В. Контактная жескость деталей машин / Э. В. Рыжов. – М.: Машиностроение, 1966. – 93 с..