Сейчас ваша корзина пуста!
Формирование структуры и свойств при плазменной наплавке износостойких покрытий на медь и высокоуглеродистую, марганцовистую стали
Цикл статей:
Глава 1 – Формирование структуры и свойств при плазменной наплавке износостойких покрытий на медь и высокоуглеродистую, марганцовистую стали
Глава 2 – Материлы и методы исследования
Глава 3 – Разработка конструкции плазмотрона с расширяющимся каналом сопла для плазменной наплавки
Глава 4 – Плазменное нанесение жароизносостойкого покрытия на медную основу
Введение
Актуальность проблемы. Эффективным и экономичным путем повышения долговечности деталей, работающих в условиях циклических нагрузок, контактной усталости и истирания, является создание на их поверхностях прочных, долговечных и износостойких слоев. Упрочнение тонкого поверхностного слоя массивных деталей из обычных конструкционных материалов позволяет экономить дорогостоящие и дефицитные материалы, повышать ресурс механизмов, успешно решать проблему восстановительного ремонта [1-4]. К таким деталям относятся элементы металлургического оборудования – стенки кристаллизатора машин непрерывного литья заготовок и изделия железнодорожного транспорта – в частности крестовины стрелочных переводов.
Процессы наплавки занимают одно из важных мест в современной сварочной технике. С их помощью на рабочих поверхностях разнообразных изделий получают сплавы с необходимыми свойствами: кислотоупорные, коррозионностойкие, жаропрочные, износостойкие, антифрикционные и т. п. Такие изделия находят применение практически во всех отраслях промышленности. Широкое использование биметаллических конструкций, получаемых путем наплавки, определяется не только техническими, но и экономическими преимуществами.
В большинстве случаев металл рабочих поверхностей изделий по своим свойствам должен отличаться от металла самой детали (например, зубья ковшей экскаваторов, вкладыши подпятников крупных турбогенераторов, коллекторные уплотнительные поверхности задвижек и клапанов для воды и др.). Такие изделия изготовляют преимущественно методами наплавки.
Многие изделия из дорогостоящих и дефицитных металлов и сплавов (например, из цветных металлов, нержавеющих, жаропрочных, кислотостойких сталей и т. п.) изготовляют комбинированными: основа состоит из наиболее дешевых материалов (например, обычной малоуглеродистой стали), а на рабочие поверхности наплавляют сплавы со специальными свойствами. Вес металла наплавки в этих изделиях составляет всего несколько процентов от веса всего изделиям. Поэтому такие биметаллические конструкции, полученные наплавкой, во много раз дешевле конструкций, изготавливаемых целиком из металла с требуемыми свойствами. Кроме того, эти конструкции по мере износа могут заново восстанавливаться наплавкой, что во много раз уменьшает расход металла для изготовления запасных частей оборудования [5].
Свойства металла наплавки и его соединения с основным металлом в большой мере зависят от глубины проплавления основного металла, перемешивания основного металла с наплавляемым и перехода элементов основного металла в металл наплавки. При этом, как правило, чем больше глубина проплавления, степень перемешивания и переход элементов основного металла в металл наплавки, тем хуже свойства как металла наплавки, так и соединения в целом. Поэтому для изготовления ответственных биметаллических изделий следует применять такие способы наплавки, которые обеспечивают минимальное проплавление или растворение основного металла. Наиболее широко применяющиеся в промышленности способы наплавки, основанные на плавлении основного и присадочного металлов, практически исчерпали свои возможности в части уменьшения глубины проплавления основного металла и его перехода в металл наплавки [6].
Из новых уже применяемых в промышленности способов наплавки наиболее полно удовлетворяют требованию получения биметаллических изделий с минимальной глубиной проплавления основного металла способы плазменной наплавки [7-9].
Струя низкотемпературной плазмы как источник тепла находит все более широкое использование в металлургии и обработке материалов, в том числе и для целей наплавки [10]. Энергетические, тепловые и газодинамические параметры струи низкотемпературной плазмы сравнительно легко регулируются в широких пределах. Это позволяет получать наплавленные слои с заданными физико-химическими и механическими свойствами. Наряду с этим плазменные способы наплавки обеспечивают и высокую производительность процесса, не требуют сложного оборудования и специализированных источников питания, могут быть с успехом внедрены в любом цехе, на любом участке, в любой мастерской, где производится наплавка разнородных металлов.
В производстве непрерывного литья заготовок одной из проблем является непродолжительность срока службы медного кристаллизатора из-за интенсивного износа материала стенок. В связи с этим перед исследователями встает задача повышения износостойкости медных стенок кристаллизатора [11,12].
Наиболее перспективным направлением на пути к повышению долговечности стенок медных кристаллизаторов является нанесение покрытий. Нашли применение покрытия из хрома, никеля и сплавов на их основе, основным недостатком которых является их незначительная толщина (до 1 мм). Получение покрытий большей толщины сопряжено с опасностью снижения прочности сцепления покрытия с медной основой. Поэтому разработка новых технологий плазменных покрытий большей толщины являются важной практической задачей.
Железнодорожные крестовины изготовленные из стали ПОГ 13 (сталь Гатфильда) являются главным элементом верхнего строения пути. Они подвержены вертикальным и боковым циклическим нагрузкам, которые могут быть достаточно большими в зависимости от интенсивности движения.
Срок службы крестовин определяется величиной износа, который зависит от работы под подвижной нагрузкой, качества материала и технологии изготовления и условий эксплуатации крестовин [13-16].
В последнее время усилилось внимание исследователей к вопросам восстановления изношенных крестовин и создания биметаллических крестовин на основе более простых марок сталей.
Восстановление работоспособности изношенных крестовин стрелочных переводов является важным резервом экономии в условиях недостаточного финансирования железных дорог и удорожания новых крестовин. К вопросу восстановления добавляется вопрос качества производимой наплавки, которая проводится вручную [17-20].
Одним из наиболее перспективных способов наплавки является плазменные методы с подачей порошка вместе с плазмообразующим газом. Однако, при разработке технологий нанесения покрытий (наплавки) существуют 2 основные проблемы:
- обеспечение максимальной прочности сцепления покрытия и металла основы;
- предотвращение остаточных напряжений и растрескивания в наплавленном слое.
Цель работы.
На основе исследования физико-технических характеристик плазмотрона с расширяющимся каналом сопла с внешним электродом и подачей порошка в разрядный промежуток, и установления закономерностей формирования структуры, фазового состава и механических свойств наплавленного слоя разработать установку для плазменной наплавки металлов и технологию плазменной наплавки жароизносостойкого сплава на медь, рельсовую сталь и сталь 110Г13, из которой изготавливают железнодорожные крестовины, обеспечивающие надежное сцепление покрытия с металлом основы и предотвращающие ее растрескивание.
Основные задачи работы:
- провести исследования физико-технических характеристик и определить оптимальные конструктивные параметры плазмотрона с расширяющимся каналом сопла с внешним электродом и подачей порошка в разрядный промежуток вместе с плазмообразующим газом;
- выявить закономерности формирования фазового состава, структуры, механических свойств и сопротивления разрушения жароизносостойкого
покрытия на медную основу и разработать технологию наплавки, обеспечивающую высокие прочность сцепления и износостойкость;
- установить механизм образования поперечных трещин в наплавленном металле при производстве наплавки на сталь 110Г13Л;
- разработать способ релаксационной обработки, предотвращающий растрескивание при производстве наплавки;
- исследовать закономерности формирования фазового состава, структуры, уровня остаточных напряжений, механических свойств и сопротивления разрушению наплавки порошкового сплава 65Х25Г13НЗ на рельсовую сталь типа 76ГФ и высоколегированную сталь 110Г13;
- создать опытно-промышленную установку и технологию плазменной наплавки для восстановления железнодорожных крестовин из стали 1 ЮГ 13Л, обеспечивающие увеличение в 2 раза эксплуатационного ресурса.
Научная новизна работы включает в себя:
•закономерности формирования фазового состава, структуры, механических свойств и сопротивления разрушению жароизносостойкого покрытия на медную основу, обеспечивающие толщину покрытия 4-6 мм, надежное сцепление с основой и увеличение износостойкости в 4-5 раз, что позволяет ожидать увеличения эксплуатационной стойкости стенок медного кристаллизатора машин непрерывного литья заготовок с покрытием данного типа до 500-1000 плавок;
• оптимальные конструктивные параметры плазмотрона с расширяющимся каналом сопла с внешним электродом и подачей порошка в разрядный промежуток вместе с плазмообразующим газом, обеспечивающие повышение КПД, надежности работы и эффективности наплавки, а также технологические параметры процесса наплавки;
•механизм образования поперечных трещин в наплавленном металле – как результат долома под действием остаточных напряжений не залеченных внутренних интеркристаллитных трещин возникающих при оплавлении границ зерен металла основы;
•способ релаксационной обработки, заключающийся в синхронном с процессом наплавки теплом ударном наклепе, приводящем к релаксации остаточных напряжений за счет фазового у->а превращения и предотвращающем растрескивание при производстве наплавки;
•закономерности формирования фазового состава, структуры, уровня остаточных напряжений, механических свойств и сопротивления разрушению наплавки порошкового сплава 65Х25ПЗНЗ на рельс, подтвердившие принципиальную возможность создания биметаллической железнодорожной крестовины из низколегированной стали типа 76ГФ с наплавкой наиболее подверженных износу областей крестовины взамен высоколегированной стали 110Г13.
Практическая ценность и реализация результатов работы:
Использование полученных результатов позволяет снизить расходы на эксплуатацию и ремонт стенок медных кристаллизаторов МНЛЗ и железнодорожных крестовин стрелочных переводов. Создана опытнопромышленная установка, разработана и освоена технология плазменной наплавки для восстановления железнодорожных крестовин из стали ПОГ 13Л, обеспечивающая увеличение эксплуатационного ресурса в 2 раза. Разработаны и согласованы с МПС РФ технические условия (см. Приложение).
Надежность и достоверность результатов обеспечена использованием современных научно-исследовательских приборов и методов исследования, автоматизированных технологических средств нанесения покрытий, всестороннего и тщательного проведения экспериментов, комплексным анализом результатов исследований, а также подтверждается отсутствием аварийных разрушений восстановленных железнодорожных крестовин при эксплуатации.
Технологические возможности основных методов поверхностного упрочнения и восстановления деталей
Виды поверхностного упрочнения и восстановления деталей
Процессы поверхностного упрочнения и восстановления деталей путем создания покрытий можно разделить по физическим явлениям, лежащим в основе упрочнения, на следующие основные группы: 1) поверхностное пластическое деформирование; 2) термическая обработка; 3) химикотермическая обработка; 4) наплавка; 5) химическое осаждение покрытий; 6) электролитическое нанесение покрытий; 7) газотермическое напыление; 8) ионно-вакуумное нанесение покрытий [20].
Первые две группы охватывают только методы упрочняющей технологии. Процессы групп 4, 6, 7 могут использоваться как для восстановления, так и для упрочнения рабочих поверхностей деталей. Группы процессов 3, 5 и 8 охватывают методы нанесения покрытий незначительной толщины и в основном применяются для упрочнения деталей, хотя при небольших эксплуатационных изменениях размеров рабочих поверхностей последних вследствие изнашивания, коррозии, эрозии возможно и их восстановление.
Область применения тех или иных методов определяется прежде всего технологическими возможностями и во вторую очередь техникоэкономическими показателями процессов упрочнения и условиями последующей эксплуатации изделий.
Современные способы наплавки и их возможности
Классификация способов наплавки
В настоящее время разработаны и широко применяются в промышленности различные способы наплавки металлов [21-27]. При наплавке однородных металлов путем применения проволок и флюсов
10 соответствующего состава удается получить металл наплавки такого же состава, что и основной металл и соответственно свойства соединения, аналогичные свойствам основного металла. Способ наплавки в этом случае практически не оказывает влияния на свойства соединения. Поэтому при наплавке стремятся применять такие способы, которые, обеспечивая качество соединения, в то же время обеспечивают максимальную производительность и эффективность процесса. Такими способами являются автоматическая наплавка под слоем флюса электродной проволокой и ленточным электродом, наплавка в среде защитных газов и т. д. (рис. 1.1).
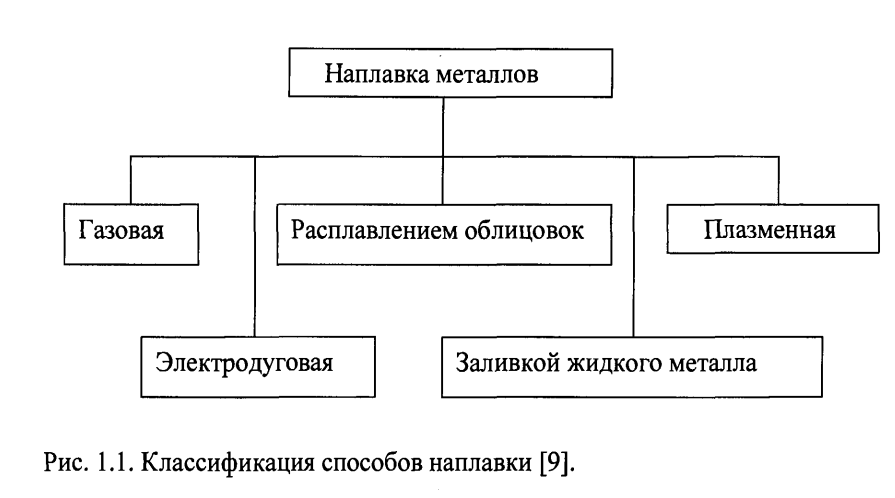
При необходимости наплавки на изделие металлов, отличных по химическому составу и теплофизическим свойствам от основного металла, задача получения качественного соединения усложняется. Это вызвано тем, что при соединении разнородных металлов в результате перемешивания основного и наплавляемого металлов, растворения твердого основного металла в жидком металле сварочной ванны и диффузионных процессов на межфазной границе в металл наплавки переходит значительная доля основного металла.
Газовая наплавка
При газовой наплавке для нагрева основного и наплавляемого металлов используют теплоту, выделяемую при горении смеси ацетилена или его 11
заменителей и кислорода. Газовое пламя – наименее интенсивный источник нагрева, поэтому его применение обуславливает большую, чем в других случаях, зону термического влияния. Испарения металла при использовании этого источника нагрева нет. Особенностью процесса является возможность получения малой доли основного металла в наплавленном (5-10%), что связано с отсутствием значительного давления струи газа на поверхность ванны. Давление потока газа оценивается прямо пропорционально квадрату количества газа, истекающего из сопла в секунду, и его плотности и обратно пропорционально расстоянию от среза сопла до поверхности ванны. Эта объективная зависимость позволяет оператору легко управлять процессом.
По виду применяемых присадочных материалов различают два метода газовой наплавки. По первому методу присадочный металл в виде проволоки, прутков или ленты подается в сварочную ванну вручную или специальными механизмами [6].
При газопорошковой наплавке в качестве присадочных материалов используют гранулированные порошки легкоплавких сплавов определенных фракций и горелки специальной конструкции, позволяющие осуществлять две разновидности процесса: предварительное напыление слоя порошка на поверхность изделия с последующим оплавлением покрытия; собственно наплавку – одновременное нанесение и оплавление малых порций порошка на поверхности детали.
Кроме малого проплавления, газовая наплавка имеет и другие преимущества: универсальность и гибкость технологии; возможность наплавки тонких слоев; пониженную опасность возникновения трещин, поскольку процесс наплавки легко совмещается с предварительным подогревом; низкую стоимость наплавочного оборудования. Недостатки газовой наплавки – низкая производительность процесса; нестабильность качества наплавленного слоя, зависящая от квалификации наплавщика.
Электродуговая наплавка
При ручной электродуговой наплавке и автоматической наплавке электродной проволокой разнородных материалов в первый слой металла наплавки переходит до 50—60% основного металла [28]. Конечно, такое высокое содержание доли основного металла в металле наплавки, как правило, недопустимо, и наплавку приходится осуществлять в 4 – 6 и более слоев для обеспечения необходимой чистоты наплавленного слоя. Это вызывает весьма значительное удорожание наплавленных изделий и, как правило, не обеспечивает их необходимых свойств (особенно в тех случаях, когда к изделию предъявляются высокие требования не только по чистоте наружного наплавленного слоя, но и по механическим свойствам как металла наплавки, так и соединения металла наплавки с основным металлом) [6].
Наплавка расплавлением облицовок
Способ наплавки расплавлением облицовок [29] нашел применение при наплавке бронз на чугун и сталь. Суть этого метода заключается в следующем: на основной металл накладывается заготовка из бронзы. Между заготовкой и угольным электродом возбуждается открытая электрическая дуга, тепло которой и плавит заготовку. В результате между дугой и изделием создается слой расплавленного металла заготовки, предохраняющий поверхность детали от прямого действия на нее дуги.
При определенных режимах наплавки расплавление поверхности детали из черного металла отсутствует, но поверхность нагревается до температуры, равной или несколько превышающей температуру плавления металла заготовки. В этих условиях процесс смачивания стали расплавленным цветным металлом протекает успешно, и получается качественное сварное соединение [27]. Однако указанный метод трудоемок, требует каждый раз специальной подготовки заготовки, наплавка производится вручную, не всегда обеспечивается сплавление по всему сечению наплавки.
Наплавка заливкой жидкого металла
Метод сварки металлов с разделенными процессами плавления основного и присадочного металлов был предложен В.П. Никитиным [25]. Идея этого метода заключалась в том, чтобы разделить тепловые процессы подготовки основного и присадочного металла, сделать подготовку и подачу последнего сколь угодно большой и независимой от источника тепла, ведущего подготовку основного металла. При применении способа наплавки по этому методу участок основного металла, оплавляется открытой угольной дугой, а присадочный металл в жидком состоянии с небольшой температурой перегрева вводится в ванну из специального металлосборника через разливочное устройство. Однако из-за больших неудобств, связанных с применением специального металлосборника с разливочным устройством, этот способ практически не нашел применения в промышленности.
Плазменная наплавка
С выделением плазменной струи аргона из столба дугового разряда были разработаны новые плазменные способы наплавки (рис. 1.2).
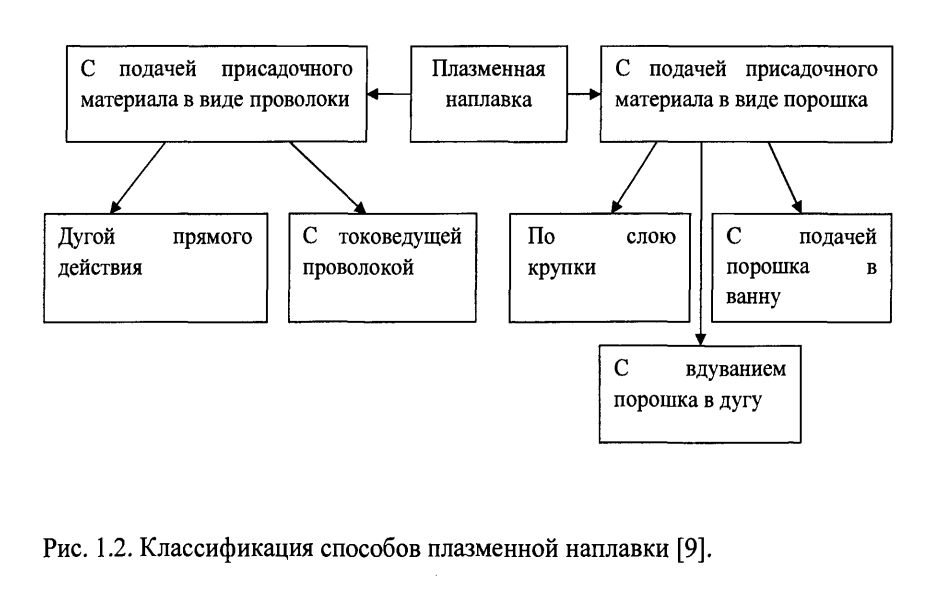
Наплавка с присадочной проволокой или лентой может быть осуществлена дугой прямого или косвенного действия (рис. 1.3). В первом случае (рис. 1.3 а) дуга горит между вольфрамовым электродом и изделием, а присадочная проволока электрически нейтральна или же подключается через балластное сопротивление к источнику питания [30,31]. Однако ввиду значительного проплавления основного металла ее можно рекомендовать только для наплавки металлов, не отличающихся по составу от металла изделия.
Способ наплавки металлов плазменной струёй с токоведущей присадочной проволокой (рис. 1.3 б), аналогичный наплавке двойной косвенной дугой, но более усовершенствованный [32].

Плазменная струя, выделенная из дугового разряда, является независимым источником ионизации дугового промежутка между неплавящимся электродом и токоведущей присадочной проволокой, что способствует устойчивому возбуждению и горению дуги между неплавящимся электродом и проволокой, исключает обрывы дуги и позволяет резко упростить кинематическую и электрическую схему автомата для наплавки.
На представленной на рис. 1.3. б принципиальной схеме устройства для наплавки металлов плазменной струей источником теплоты для проволоки является независимый от изделия двухдуговой разряд. Одна дуга (маломощная) горит между вольфрамовым электродом 1 и водоохлаждаемым соплом-анодом 2, вторая дуга – между вольфрамовым электродом и токоведущей присадочной проволокой 7. Для питания обеих дуг достаточно одного сварочного генератора 5. Электрическая схема позволяет перераспределять энергию генератора между первой и второй дугой с помощью ограничительного сопротивления (балластных реостатов) 4. Основным источником теплоты для основного металла в случае наплавки плазменной струей с токоведущей присадочной проволокой является сам перегретый жидкий наплавляемый металл, дополнительным источником теплоты является плазменная струя. При применении способа наплавки плазменной струей с токоведущей присадочной проволокой возможно такое регулирование, при котором количество теплоты, вводимое в основной металл, будет всецело определяться величиной тока в проволоке 1п и расстоянием между торцом проволоки и изделием йг.
Плазменная наплавка с применением присадочного материала в виде порошка [32] может осуществляться несколькими способами (рис. 1.4). Самым простым из них является способ наплавки по слою крупнозернистого порошка (крупки) (рис. 1.4. а). В этом случае порошок заранее насыпается на наплавляемую поверхность, а плазменная дуга, горящая между электродом и изделием, расплавляет его.
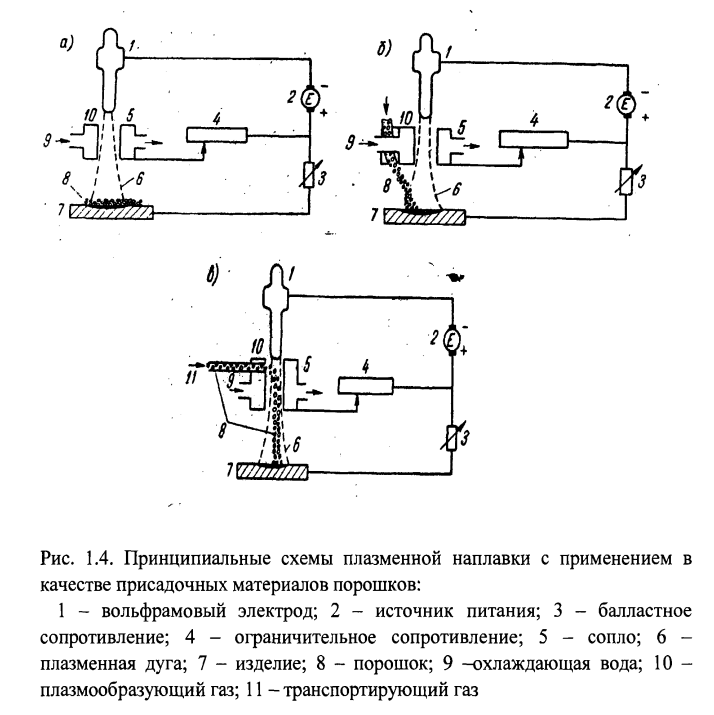
При наплавке с подачей порошка в сварочную ванну (рис. 1.4 б) дуга горит между электродом и изделием. На изделии образуется ванна основного металла, куда подается порошок тугоплавкого металла. Способ этот применяется тогда, когда необходимо, чтобы в матрицу металла изделия были вкраплены частицы тугоплавких материалов.
Наплавка с вдуванием порошка в дугу (рис. 1.4. в) предусматривает подачу порошка в плазменную струю, плавление его в этой струе и перенос на поверхность изделия, подогретую и оплавленную дугой прямого действия.
Плазменная наплавка с применением в качестве присадочного материала порошковых сплавов благодаря минимальному проплавлению 17
основного металла обеспечивает получение деталей с высокими физикомеханическими свойствами.
В качестве критерия, определяющего возможности различных способов наплавки, можно рассматривать степень проплавления, определяемую [6] как долю проплавленного основного металла в составе металла наплавки. Сравнительные данные о степени проплавления при способах наплавки медных сплавов и сталей аустенитного класса на стали перлитного класса, показали, что степень проплавления минимальна при наплавке двойной косвенной дугой и плазменной струей с токоведущей присадочной проволокой.
Таким образом, для соединения разнородных металлов из существующих способов лучшие результаты получены при плазменной наплавке. Технологичность процесса, простота устройства, возможность регулирования параметров процесса наплавки и обеспечение высоких физико-механических свойств металла наплавки и наплавленного изделия при высокой эффективности процесса позволяют рекомендовать плазменную наплавку металлов для широкого применения в различных отраслях промышленности.
Схемы получения плазменной дуги
Плазма представляет собой вещество в сильно ионизированном состоянии.
Практически в любом дуговом разряде образуется плазма. В результате короткого замыкания находящихся под напряжением двух электродов в точках контакта выделяется большое количество тепла, под действием которого катод начинает эмитировать электроны, а находящийся в межэлектродном пространстве газ ионизируется. Межэлектродное пространство оказывается заполненным ионами, электронами и парами электродных материалов. Поскольку электроды находятся под напряжением, то под действием электрического поля возникает направленное движение
18 частиц, скорость которых достигает 300 – 1000 м/сек [8]. В результате соударения движущихся с такой большой скоростью заряженных частиц с нейтральными атомами, а также столкновений нейтральных атомов между собой, степень ионизации газов в межэлектродном пространстве значительно повышается и, по существу, поток заряженных частиц между электродами представляет собой поток плазмы.
Плазма характеризуется повышенной электропроводностью, поддается действию магнитных полей. Существование плазмы поддерживается непрерывно протекающим процессом ионизации. Высокая степень ионизации обусловливает высокую температуру плазмы вещества. Интенсифицировать процесс плазмообразования можно путем обдува дуги соосным потоком газа. Если же часть столба дуги поместить в узкий канал с охлаждаемыми стенками, то будет достигнута дальнейшая интенсификация процесса. Это объясняется тем, что в узком канале столб дуги сжимается, особенно при обдуве ее соосным столбу дуги потоком газа. Так как с увеличением тока столб дуги из-за ограничивающего действия, стенок канала расширяться не может, температура газа и степень его ионизации резко повышаются. Практически весь газ, проходящий сквозь столб сжатой дуги, ионизируется и превращается в плазму. На этом принципе и основано устройство применяемых при наплавке плазмотронов [34].
В качестве плазмообразующих газов могут быть использованы аргон, азот, гелий, аммиак. Водород и кислород можно применять в смеси с аргоном, азотом. Применение одного водорода невозможно из-за его высокой теплопроводности, что приводит к быстрому нагреву и разрушению сопла.
Различные газы и газовые смеси обладают разными физикохимическими свойствами, целесообразность использования которых определяется видом плазменной обработки металлов (наплавка, напыление, закалка и др.) и степенью воздействия на вольфрамовый электрод. Наилучшим газом, защищающим вольфрамовый электрод от окисления,
19 является химически инертный аргон. Но аргон – одноатомный газ, и энергия, приобретенная им в столбе электрической дуги, определяется лишь теплоемкостью и процессами ионизации.
Водород диссоциирует на 90% при 4700 К, а азот – при 9000 К, причем их теплосодержание (энтальпия) при данных температурах равна теплосодержанию аргона при температуре 14000 К.
Плазма приобретает новые свойства по сравнению с обычными газами. Высокая концентрация электронов делает ее электропроводной, причем электропроводность плазмы достигает величины электропроводности металлов. Из-за большой насыщенности заряженными частицами плазма поддается действию магнитных полей [5].
В настоящее время основным методом получения плазмы для технологических целей является метод пропускания газовой струи через сжатую электрическую дугу, расположенной в узком медном канале.
В современной сварочной технике применяют следующие схемы получения плазмы. Первая соответствует схеме сжатой дуги прямого действия, когда анодом служит обрабатываемый материал. Вторая – сжатая дуга косвенного действия возникает между вольфрамовым электродом и соплом-анодом плазмотрона. Дуга косвенного действия (плазменная струя) электрически не связана с обрабатываемым металлом. Вторая схема нашла применение при обработке неэлектропроводных материалов, а также при напылении и закалке.
КПД при нагреве сжатой дугой прямого действия составляет 30 – 75%, косвенного -10 – 50% [3].
В обычных условиях при прямой полярности столб дуги между неплавящимся вольфрамовым электродом и деталью в атмосфере защитного газа имеет вид конуса, размеры которого зависят от силы тока и напряжения. Так как с увеличением силы тока и напряжения столб такой дуги имеет возможность расширяться, то значительного изменения температуры и степени ионизации газа не наблюдается. Если каким-либо образом
20 воспрепятствовать электрической дуге занять естественный объем и принудительно сжать ее, оставив в то же время сварочный ток постоянным, то и количество электронов, проходящих по сечению столба дуги, не изменится, а количество упругих и неупругих соударений увеличится, т. е. повысится степень ионизации, возрастут плотность тока и напряжение дуги, что вызовет значительное повышение температуры. Таким образом, наличие у плазмотронов стабилизирующего водоохлаждаемого канала сопла является основным отличием от обычных горелок, применяемых для сварки в среде защитных газов.
Несмотря на высокую температуру плазменной струи, плазмотроны работают довольно устойчиво. Это объясняется тем, что сопло, изготовлено из меди. Вода, охлаждающая стенки сопла, препятствует нагреву и ионизации наружного слоя газа, проходящего через дугу.
Сжатая дуга косвенного действия может иметь различную длину. Внутри сопла она сжата, однако при выходе за его пределы начинает постепенно расширяться. На расстоянии 25 – 30 мм от нижнего среза сопла сжатая плазменная струя расширяется до свободных размеров.
Наплавочные материалы
Характеристика наплавочных материалов
Наплавка – сложный металлургический процесс, требующий комплексного решения ряда сложных вопросов: выбор наплавочного материала, обеспечивающего необходимые свойства, соответствующие условиям эксплуатации; выбор способа и режимов наплавки.
Выбор наплавочных материалов определяется видом износа. В свою очередь, вид износа деталей зависит от условий работы машины, агрегата, узла: одни детали работают при значительном абразивном изнашивании, другие – при высоких температурах, третьи – при знакопеременных нагрузках в условиях высоких давлений, ударов. Выбор наплавочных материалов оптимального состава вызывает определенные трудности,
21 поскольку наплавка слоев с заданными физико-механическими свойствами зависит от многих факторов: состава и формы наплавочного сплава, состава металлической основы детали, характера взаимодействия легирующих и других элементов, способа и режима наплавки и др. [5].
Например, изменение грануляции порошковых сплавов сопровождается изменением интенсивности реакций окисления. Применяемые при наплавке различные газовые среды также по-разному влияют на протекание реакции в сварочной ванне. Поскольку теоретически определить соотношение элементов в исходном наплавочном и наплавленном металле и характер их взаимодействия можно только ориентировочно, то выбор рациональных составов порошковых сплавов применительно к восстановлению конкретных деталей возможен путем проведения экспериментальных исследовании (металлографических, химических, физико-механических) и эксплуатационных испытаний.
Опыт последних лет показывает, что при восстановлении деталей машин нанесение покрытий твердыми порошковыми сплавами во много раз повышает срок службы этих деталей [3].
Твердые сплавы особого класса – износостойкие металлические материалы, обладающие высокой твердостью и сохраняющие ее при высоких температурах в процессе работы. Для твердых сплавов характерно содержание большого количества карбидов и боридов, сцементированных соответствующей эвтектикой. Название «твердые сплавы» условное, поскольку большинство из них имеют твердость ниже твердости закаленных высокоуглеродистых сталей. Многие закаленные стали имеют твердость порядка НК.С 56 – 60, но их износостойкость ниже, чем, например, у наплавленного слоя ПГС1, имеющего твердость НКС 45—50. Твердые порошковые сплавы – это, в первую очередь, износостойкие сплавы, предназначенные для нанесения покрытий на детали, работающие в условиях абразивного изнашивания, коррозии, эрозии при повышенных температурах. Однако ценность твердых порошковых сплавов не только в их
22 использовании для увеличения срока службы деталей, подверженных различным видам абразивного изнашивания. Твердые сплавы, как высоколегированные наплавочные материалы, открывают широкие возможности для разработки новых наплавочных сплавов путем создания композиций с другими наплавочными материалами. Применение таких сплавов оказалось весьма эффективным при других видах изнашивания и характера нагрузок, например, при знакопеременных нагрузках, где требуется не только высокая износостойкость, но и пластичность. Несмотря на разнообразный ассортимент наплавочных сплавов, выпускаемых отечественной промышленностью, обеспечить требуемый состав наплавленного металла часто не представляется возможным. Чтобы получать слои требуемого состава при плазменной наплавке с использованием порошковых твердых сплавов, а также выбирать рациональный состав путем их смешения в различных соотношениях с другими наплавочными материалами, следует знать свойства наплавочных порошковых сплавов, их склонность к образованию трещин, а также свойства легирующих и раскисляющих элементов, оказывающих влияние на состав и структуру наплавленных слоев.
Износостойкость наплавленных слоев определяется не только наличием в сплаве тех или иных карбидов, но и строением матрицы – основы сплава [36], которая может быть ферритной, аустенитной, мартенситной. Феррит имеет низкую твердость, и в силу этого в нем плохо удерживаются твердые карбидные частицы характеризующие износостойкость сплава. Мартенситная основа обладает наибольшей износостойкостью при абразивном изнашивании без ударных нагрузок. При ударных нагрузках из-за высокой хрупкости происходит выкрашивание карбидов, что ускоряет изнашивание. При ударных нагрузках более высокую износостойкость обеспечивают аустенитная и аустенитно-мартенситная основы. Аустенит по сравнению с мартенситом менее износостойкий, но зато более вязкий и создает условия для прочного удержания внедренных карбидных частиц в
23 своей основе. Но и в аустенитной матрице для получения сплавов с высокой износостойкостью количество карбидов должно быть в определенных пределах. Значительное увеличение их может уменьшить износостойкость сплава, так как карбиды начинают выкрашиваться, а не изнашиваться. При ударно-абразивном изнашивании рекомендуется, чтобы количество карбидной фазы не превышало 25 – 30%. В процессе работы соединения в покрытиях из высоколегированных и хромоникелевых сплавов в результате их пластической деформации и упрочнения происходит превращение аустенита в мартенсит, что повышает износостойкость поверхностных слоев и сопротивляемость к схватыванию.
Хромоникелевые сплавы содержат в своем составе присадки бора и кремния, которые снижают температуру плавления и придают сплавам способность самофлюсования. Эти сплавы имеют низкую температуру плавления (980—1080°С), хорошо смачивают поверхность наплавляемого изделия, обладают высокой износо- и жаростойкостью.
Сплавы на основе железа – это высокоуглеродистые, высокохромистые заэвтектические сплавы, обладающие высокой износостойкостью при истирании в абразивной среде. Температура плавления этих сплавов 1275 – 1350°С. Характерный недостаток сплавов – высокая хрупкость, приводящая к образованию трещин[3].
Причины образования трещин при наплавке
Трещины подразделяются на два вида: горячие и холодные. Горячие трещины образуются при температурах, близких к линии солидус. Их возникновение связано с процессами нагрева и кристаллизации, в результате которых в наплавленном соединении возникают пластические деформации сжатия, а при последующем охлаждении появляются напряжения растяжения. В результате воздействия на металл двух противоположных процессов, нагрева и охлаждения создаются условия для его сжатия. Если деформации сжатия превышают деформационную способность кристаллизующегося металла, то в наплавленном соединении могут возникнуть горячие трещины.
Вероятность возникновения горячих трещин повышается при содержании в наплавляемом металле элементов, склонных к образованию легкоплавких эвтектик и химических соединений, кристаллизующихся на границах зерен при низких температурах и значительно понижающих его пластичность. К таким элементам, образующим по границам зерен легкоплавкие прослойки, относятся, в первую очередь, сера и углерод.
Возникновение холодных трещин наиболее характерно для закаливающихся сталей перлитного и мартенситного классов. Холодные трещины образуются при переохлаждении наплавленного металла и зоны термического влияния, причем происходит быстрое превращение у-железа в а-железо при температуре ниже 200°С. В результате без диффузионного превращения образуется твердая и хрупкая мартенситная структура с большим объемом по сравнению с объемом исходной у-структуры.
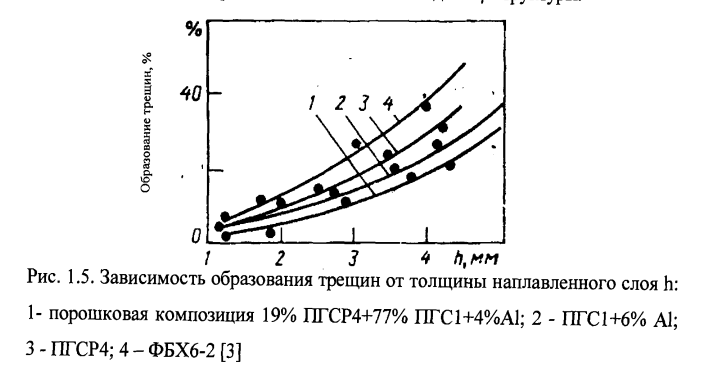
Опыты по определению склонности к образованию трещин различных порошковых твердых сплавов показали, что с увеличением толщины наплавляемого металла процесс трещинообразования возрастает (рис. 1.5). Наиболее предрасположены к образованию трещин сплавы ФБХ6- 2 и ПГСР4.
Основные методы повышения эксплуатационной стойкости медных кристаллизаторов машин непрерывного литья заготовок (МНЛЗ)
Условия работы медного кристаллизатора МНЛЗ
В технологическом процессе непрерывного литья стали кристаллизатору отведена одна из самых основных функций – формирование слитка требуемого сечения.
В ходе разливки жидкий металл непрерывно подается в кристаллизатор и, соприкасаясь с его водоохлаждаемыми рабочими стенками, кристаллизуется по периметру. При выходе из кристаллизатора оболочка слитка образует сосуд с жидким металлом, внутри которого в направлении от стенок к центру продолжается кристаллизация, но форма слитка и его поперечные размеры уже определены формой и размерами рабочей полости кристаллизатора. Основное требование к кристаллизатору – обеспечить необходимый теплоотвод от затвердевающей стали и получить на выходе из кристаллизатора прочную оболочку слитка с хорошей поверхностью, которая не разрушалась бы под действием тепла жидкой фазы и ферростатического давления, а также от взаимодействия с направляющим аппаратом зоны вторичного охлаждения [11,12].
Естественно, что производительность машины, и качество слитка во многом определяются тем, что насколько кристаллизатор удовлетворяет всем технологическим требованиям. Установлено, что подавляющее число поверхностных дефектов слитка (продольные и поперечные горячие трещины, ужимины, плены, паукообразные трещины) зарождаются в кристаллизаторе. Следовательно, при проектировании технологического оборудования машин непрерывного литья стали конструкции кристаллизаторов должно быть уделено особое внимание.
Важное значение для обеспечения хорошей работы кристаллизатора имеет выбор материала его рабочих стенок. Этот материал должен обладать достаточно высокой теплопроводностью, износоустойчивостью, сохранять
26 стабильность механических свойств при повышенных температурах. Кроме того, материал стенок не должен смачиваться жидкой сталью и оказывать вредное воздействие на поверхность заготовки в результате взаимодействия с ней при высоких температурах. При выборе материала должна учитываться и экономическая целесообразность его применения. Очевидно, что подбор материала с такими разнородными свойствами сопряжен с определенными трудностями.
В настоящее время для изготовления рабочих стенок кристаллизаторов, в основном, применяется электролитическая медь, несмотря на то, что она далеко не полностью удовлетворяет всем выше указанным требованиям. Так, например, несмотря на то, что в процессе разливки применяют шлакообразующие смеси, подаваемые на мениск металла, которые в расплавленном состоянии не только предохраняют металл от окисления, но и служат смазочным материалом между рабочими стенками и слитком, иногда наблюдается прилипание жидкой стали к медной поверхности [11].
Для перемещения оболочки заготовки относительно рабочей стенки кристаллизатора требуется определенное усилие, величина которого находится в прямой зависимости от характера явлений адгезии и суммарной площади участков прилипания поверхности заготовки к малым стенкам. Безусловно, прилипание жидкой стали к медным стенкам кристаллизатора отрицательно сказывается на качестве отливаемой заготовки и может служить причиной зависания ее корочки, и как следствие, возникновения продольных и поперечных трещин ее поверхности [11].
Стойкость кристаллизаторов с медными рабочими стенками в условиях высокопроизводительной работы МНЛЗ явно недостаточна. При высоких скоростях разливки температура рабочей поверхности кристаллизатора достигает величин, приближающихся к температуре разупрочнения меди. Низкая износостойкость меди приводит к повышенному износу ее рабочей поверхности в нижней части кристаллизатора и особенно поверхности узких стенок. На практике во избежании прорывов корочки слитка при достижении определенного износа малых стенок кристаллизатор снимают и направляют на переточку. Кристаллизаторы выходят из строя также вследствие пластических деформаций поверхностного слоя узких медных стенок от термических напряжений, что часто выражается в раскрытии стыка широких и узких стенок.
Наконец, кристаллизаторы с медными рабочими стенками имеют еще один существенный недостаток. У непрерывнолитых слитков иногда наблюдаются поверхностные дефекты в виде мелких паукобразных трещин, которые могут служить причиной серьезного брака при прокатке. Хотя существуют различные мнения о причинах образования паукообразных поверхностных трещин, результаты целого ряда исследований связывают появление этих дефектов с диффузионным внедрением меди на отдельных участках поверхности слитка, в результате чего механические свойства стали резко снижаются [11].
Методы повышения стойкости кристаллизаторов
Таким образом, для рабочих стенок кристаллизаторов медь не может считаться лучшим и единственно возможным материалом. Поэтому активно проводятся работы по выбору новых материалов для рабочих стенок кристаллизаторов [37-39]. Многими исследователями опробованы кристаллизаторы с рабочими стенками сплавов меди и других материалов. В табл. 1.1. приведены свойства различных медных сплавов, рекомендуемых институтом «Гипроцветметобработка» для изготовления рабочих стенок кристаллизаторов. Широкое распространение в нашей стране и за рубежом получил сплав меди с серебром типа МСр (0,1 % А§), который в большинстве случаев используется для изготовления узких стенок слябовых кристаллизаторов. Сплав МСр при незначительном снижении теплопроводности обладает по сравнению с медью более высокой прочностью и температурой разупрочнение, благодаря чему удалось
28 повысить износостойкость узких стенок и, что особенно важно, снизить вероятность раскрытия стыков между стенками.
На ряде отечественных заводов для узких стенок также используется дисперсионно-твердеющий сплав МН2,5КоКрХ (2,5 % №; 2,5 % Со; 0,75 % 81; 0,7 % Сг), который по имеющимся данным [11] позволяет заменить сплав МСр с одновременным повышением износостойкости стенок. Опубликованы данные об использовании для рабочих стенок кристаллизаторов хромовых и хромоциркониевых бронз [11].
Легирование меди любыми элементами приводит, с одной стороны, к повышению температуры ее разупрочнения, а с другой – к снижению теплопроводности. Например, медь, легированная долями процентами серебра, олова или циркония, имеет Л=3 70-380 Вт/(м*К), а из-за уменьшения теплопроводности по сравнению чистой медью примерно на 50 °С возрастает температура стенок кристаллизатора, достигая 265 °С [12].
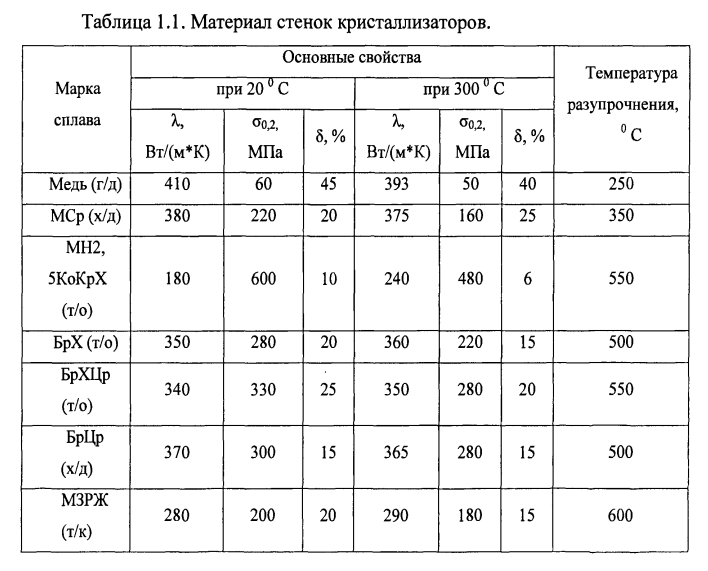
Долгое время у нас в стране и за рубежом применяли сплав меди с серебром. Однако из-за его дороговизны применение этого сплава сократилось, но и в настоящее время он применяется на УНРС ОАО «Северсталь». Используют сплавы Сп-Сг и Си-Хг. За рубежом широкое распространение получили дисперсно-твердеющие бронзы, такие как хромистая, бериллиевая, кобальтобериллиевая, хромоциркониевая.
Дисперсно-твердеющие бронзы отличает сложность как литья, так и последующей термообработки. Это приводит к удорожанию кристаллизаторов при снижение теплопроводности на 60-80 % по сравнению с медными, при этом срок эксплуатации возрастает незначительно.
Поэтому в мировой практике для повышения технологических характеристик материала кристаллизаторов в последнее время нашли распространение процессы поверхностного упрочнения, т.е. нанесение защитных покрытий.
В настоящее время наиболее полно удовлетворяют всем предъявляемым требованиям кристаллизаторы со стенками, выполненными из металлов с высокой теплопроводностью, т.е. из меди и ее сплавов, но с покрытием рабочих поверхностей другими материалами, более износоустойчивыми и термостойкими и не оказывающими вредных воздействий на поверхность стального слитка. Нанесение этих материалов на рабочие поверхности стенок может осуществляться самыми различными способами: гальваническим, напылением, наплавкой, термодиффузионным насыщением поверхностного слоя, плакированием меди листовым материалом. Наибольшее распространение получил гальванический метод покрытия.
Гальванические, в основном хромоникелевые, покрытия увеличивают стойкость на 25-43% за счет предотвращения химического взаимодействия расплава с материалом кристаллизатора, а также увеличения твердости. Однако эти покрытия склонны к отслаиванию в процессе эксплуатации.
На рис. 1.6. показаны различные типы гальванических покрытий, применяемые для повышения износоустойчивости медных рабочих стенок кристаллизаторов.
Хромирование позволяет значительно поднять твердость рабочих поверхностей стенок кристаллизаторов, что способствует повышению их износоустойчивости. Так хромирование рабочих стенок сортовых кристаллизаторов МНЛЗ Молдавского металлургического завода, выполненное НПО “ВНИИМЕТМАШ”, позволило увеличить их стойкость в несколько раз. Однако хромовое покрытие недостаточно эффективно для кристаллизаторов слябовых МНЛЗ. При малой толщине покрытия оно легко разрушается, особенно при прохождении захоложенных концов слитка. При большой толщине покрытия из-за большой разницы коэффициентов теплового расширения меди и хрома, слой хрома может отслаиваться.
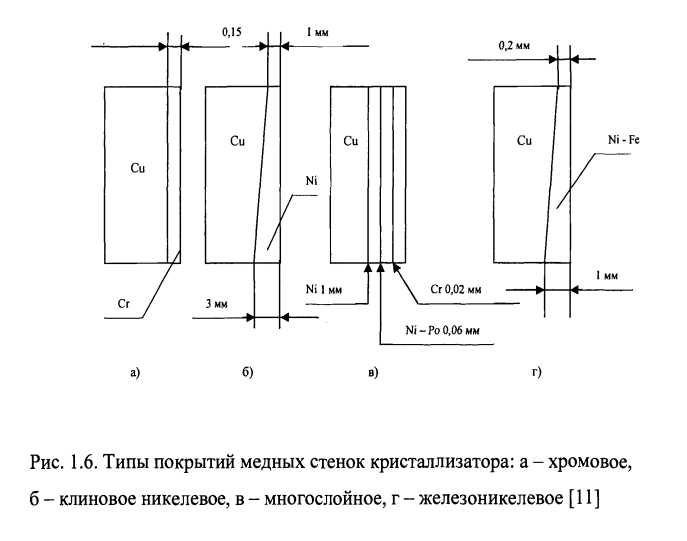
Никелевое покрытие дает хорошее сцепление с медью, но имеет значительно более низкую износостойкость. Обычно никель наносится более толстым слоем. В некоторых случаях покрытие выполняют переменным по высоте кристаллизатора – более тонким в районе мениска и толще в нижней части стенки.
Метод гальванических покрытий имеет и ряд недостатков. Процесс гальванизации происходит крайне медленно, требует организации специального участка для восстановления изношенного покрытия с очистными сооружениями, что не всегда целесообразно для металлургического завода при ограниченном парке кристаллизаторов. Поэтому продолжаются поиски других альтернативных методов покрытия.
Газоплазменное напыление позволяет расширить спектр применяемых материалов. Однако для увеличения адгезии покрытия к основе требуется последующая термообработка, что удорожает и усложняет процесс. Кроме того покрытие имеет значительную шероховатость, удаляемую только механической обработкой.
Наиболее прост метод термодиффузии, позволяющий увеличить твердость поверхности, получить упрочненный слой глубиной до 2,0 мм, достичь минимального снижения теплопроводности материала и благодаря образованию переходного слоя на границе раздела покрытие – основа обеспечить высокую прочность сцепления.
Имеются сведения, что стойкость такого кристаллизатора в четыре – шесть раз выше, чем с другими покрытиями.
Украинским ГНИИ металлов применен способ термодиффузионного нанесения в промышленных условиях защитных покрытий на базе алюминия на рабочую поверхность гильз кристаллизаторов, позволяющих повысить их эксплуатационную стойкость.
Алитирование увеличивает микротвердость поверхности до Нм= 300400 при Нц основы 90-100. Глубину слоя следует четко регламентировать, так как при значительных слоях (>0,8 мм) возникают структурные 32
напряжения, которые могут привести к образованию трещин на поверхности [40].
Широкое распространение получили многослойные покрытия, пример одного из которых приведен на рис. 1.6. По данным зарубежных фирм применение такого многослойного покрытия позволило повысить износостойкость рабочих стенок в несколько раз. Однако при этом значительно усложняется технология нанесения покрытия [12].
Большие перспективы имеет однослойное покрытие на железоникелевой основе при 4-10 % Ге.
Основные методы повышения эксплуатационной стойкости железнодорожных крестовин
Условия работы железнодорожных крестовин
Крестовина с неподвижными элементами – один из наиболее уязвимых узлов стрелочных переводов. Срок службы ее в 2,5-3 раза меньше строка службы стрелочного перевода в целом. Это обусловлено сложными условиями перекатывания колес подвижного состава через желоба крестовины, резкими перепадами вертикальной и горизонтальной жесткости конструкции, наличие углов удара колес в усовики и другими особенностями взаимодействия крестовин с подвижным составом. Интенсивный износ и потребность в частой смене крестовин из-за недостаточной их надежности – одна из причин их дефицита и ограничения скоростей движения на железных дорогах [13,14]. По износостойкости срок службы определяется пропущенным тоннажем Тв до появления вертикального износа величиной 6 мм (для главных путей) сердечника в сечении 40 мм или усовика в наиболее изнашиваемом месте. По прочности срок службы определяется тоннажем Тд, пропускаемым крестовиной до появления дефекта, из-за которого она подлежит изъятию из пути [15].
Основными процессами, формирующими регламентируемый износ крестовины, осадка литой части за счет выбора люфтов соединения с
33 рельсовыми усовиками [16], а также потеря металла с первоначального контура поперечного сечения в результате его истирания колесами и сплывов металла за счет пластических деформаций, определяющихся недостаточно высокими значениями предела текучести стали 1 ЮГ 13Л.
Работу крестовины в пути можно разбить на четыре основные стадии. На первой стадии свойства конструкции и качество изготовления крестовин определяют возможность взаимных перемещений рельсовых усовиков и литой части. Как показали результаты измерений на дорогах и Экспериментальной кольце ВНИИЖТа, в современных конструкциях типовых крестовин осадка литой части составляет в среднем 0,5 мм по сердечнику и 0,8 мм по наиболее интенсивно работающему усовику. Основная часть осадки реализуется под первыми поездками. После пропуска по крестовине 3-5 млн. т брутто груза осадка реализуется практически полностью.
После осадки начинается процесс смятия (вторая и третья стадии). Смятие в зоне перекатывания начинается в местах сопряжений рабочих поверхностей с боковыми, поэтому, вначале положение точек регламентируемого износа остается неизменным (вторая стадия). После того как процесс смятия достигает точек, в которых регламентируется износ, их положение также начинает меняться (третья стадия). Во время второй и третьей стадий износа идет интенсивный наклеп металла, сопровождающийся большими пластическими деформациями.
По мере того, как крестовина наклепывается, пластические деформации уменьшаются. В износе начинает преобладать доля истирания, т.е. крестовина переходит в четвертую стадию износа, характеризующуюся линейной зависимостью между регламентируемой потерей высоты рабочих поверхностей крестовины и ее наработкой.
Для отливки сердечников крестовин на железнодорожном транспорте применяется высокомарганцовистая сталь. Процесс упрочнения этой стали сопровождается существенным снижением пластичности и вязкости, что
34 ограничивает ее сопротивляемость износу и способствует контактноусталостным разрушениям, а в конечном итоге приводит к снижению эксплуатационной стойкости железнодорожных крестовин. Поэтому сохранение на достаточном уровне пластичности высокомарганцовистой стали при деформированном упрочнении является одним из возможных методов повышения эксплуатационной стойкости крестовин [41].
По улучшению высокомарганцовистой стали ведутся работы в следующих трех направлениях: 1) поиск оптимального химического состава, включая легирование и модифицирование; 2) поиск оптимальной технологии изготовления (режим плавки, термической обработки, способ разливки и т.п.); 3) улучшение прочностных характеристик стали за счет предварительной обработки отливок давлением (холодная накатка, взрыв).
Металлургический метод улучшения механических свойств высокомарганцовистой стали
Вопросами улучшения химического состава высокомарганцовистой стали занимались многие специалисты [42-47]. Стоит отметить, что классический состав стали Г13Л [48], по механическим свойствам практически не уступает (или мало уступает) всем последующим модификациям. Это говорит о том, что резервы повышения прочностных, пластических и износостойких свойств данной стали практически исчерпаны. Предложены конкретные составы улучшенной высокомарганцовистой стали (табл. 1.2). Как показывает сравнительный анализ свойств этих сталей, среди указанных составов наилучшее сочетание прочностных, пластических свойств и ударной вязкости обеспечивает сталь 130Г14ХМФАЛ [49,50].
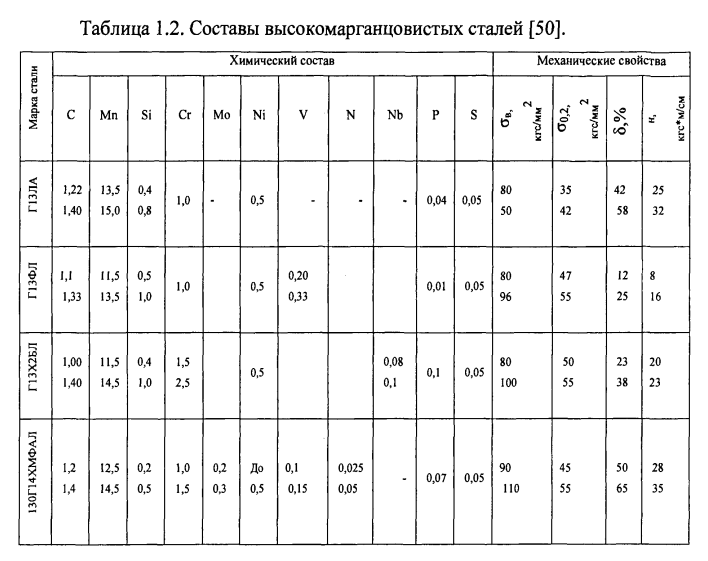
Углерод.
С повышением в литой стали содержания углерода (при прочих равных условиях) ее прочность и твердость возрастает, а пластические свойства (ударная вязкость, удлинение, сужение) резко падают практически до нуля при концентрации углерода 1,18 % [51]. В закаленном состоянии влияние углерода на механические характеристики заметно сказывается при концентрации больше 0,81 %. С увеличением содержания углерода от 1,06 до 1,48 % ударная вязкость после закалки уменьшается при 20 °С от 2,29 до 0,83 мДж/м2, т.е. примерно в 2,6 раза, а при – 40 °С и – 60 °С в 5,3 и 13 раз соответственно. Из этого следует, что повышение содержания углерода (больше 1,18%) опасно для высокомарганцовистых отливок.
Ухудшение ударной вязкости стали с ростом концентрации углерода можно объяснить увеличением в ее литой структуре количества крупных
36 карбидов, расположенных по границам аустенитных зерен и внутри них, а также дисперсных пластинчатых карбидов вдоль кристаллографических плоскостей, повышенной склонностью такой стали к образованию холодных и горячих трещин.
В работе [52] указывается, что поверхностная твердость железнодорожных крестовин с чисто аустенитной структурой повышается с 170…210 НВ до 450…480 при глубине наклепанного слоя до 18 мм, а при наличие в структуре металла даже одиночных мелких карбидов – только до 350…400 НВ при глубине наклепанного слоя 7…8, причем в последнем случае наклепанный слой является хрупким.
Марганец.
Марганец как и углерод расширяет у-область, а при их совместном присутствии это влияние усиливается. Марганец также повышает растворимость углерода в аустените при достаточно высокой температуре. Содержание марганца в аустените высокоуглеродистой стали должно превышать определенные минимальные значения.
По данным работ [53], с повышением содержания марганца в стали 110Г13Л увеличивается ее загрязненность карбидами после литья и термической обработки, снижается износостойкость, растет склонность к транскристаллитному строению и образованию горячих трещин. С повышением содержания марганца от 10 до 15 % содержание водорода в стали возрастает, поэтому усадка увеличивается с 2,2 до 3,0%, что может служить причиной образования горячих трещин.
Вопрос об оптимальном соотношении содержания марганца и углерода в высокомарганцовистой стали типа 110Г13Л в настоящее время еще нельзя считать окончательно решенным. Многие исследователи придерживаются мнения, что необходимо соблюдать соотношение Мп:С >10 для обеспечения высоких показателей ударной вязкости, прочности и пластичности [54,55]. Кремний.
Кремний обычно вводится в высокомарганцовистую сталь в
37 количестве, необходимом для ее хорошего раскисления и улучшения литейных свойств.
О степени влияния кремния на свойства стали типа 110Г13Л в литературе нет пока единого мнения. Например, по данным работ [54,56], концентрация кремния до 1% практически не влияет на уровень механических и других характеристик стали. В структуре метала, содержащего < 1% кремния, редко встречаются крупные карбиды.
По данным работ [57,58], чем больше в стали содержится кремния, тем хуже ее износостойкость, ниже прочность и ударная вязкость и выше брак по горячим трещинам (особенно при высоком содержании углерода и фосфора). Было установлено, что при повышении в высокомарганцевой стали содержания кремния с 0,17 до 1,11 % ее ударная вязкость уменьшается в 4 раза, а относительное удлинение и сужение – в 1,5 раза.
Фосфор.
По данным многих исследований, фосфор является одним из важнейших элементов, определяющих весь комплекс механических, литейных и эксплуатационных свойств высокомарганцевой стали типа 110Г13Л. Установлено, что с повышением его содержания резко падает ударная вязкость (особенно при отрицательных температурах), понижается хладноломкость, ухудшаются пластические свойства и износостойкость, заметно увеличивается склонность к образованию горячих и холодных трещин, укрупнение аустенитного зерна и транскристаллическому строению[58-60].
Вредное влияние фосфора на свойства высокомарганцовистой стали объясняется образованием хрупких соединений фосфидов железа и марганца и сложной карбидофосфидной эвтектики, которые при затвердевании металла вследствие их значительно ликвации, относительно низкой температуры плавления и способности смачивать металл располагаются в межосных пространствах дентридов и по границам зерен. За время же обычного нагрева и выдержки под закалку фосфиды из-за пониженной
38 растворимости фосфора в аустените [60] не успевают полностью перейти в металл и тем самым ослабляют пограничные связи между зернами, существенно ухудшая основные характеристики стали. Включения фосфидной эвтектики по границам зерен и внутри них наблюдаются уже при содержании в металле 0,085 % Р, а по данным работы [61], даже начиная с 0,05 % Р.
Полученные данные [60] свидетельствуют о повышение износостойкости крестовин на 10 % с пониженным содержанием фосфора в стали 110Г13Л от 0,076 до 0,030 %. Снижение фосфора в стали в указанных пределах повысило также дефектостойкость крестовин 2 раза.
Широкому распространению низкофосфористой стали типа 110Г13Л мешает недостаточное количество и относительно высокая стоимость получаемых в нашей стране низкофосфористого ферромарганца Мр-1 и Мр- 2, применяемых для легирования этой стали.
Методы повышения стойкости крестовин
При эксплуатации железнодорожных крестовин с сердечниками из стали Г13Л изменение размеров происходит от колес подвижного состава. Поэтому необходимо доэксплуатационное упрочнение сердечников крестовин, для того чтобы износ их определялся истиранием металла. Известны различные методы упрочнения: упрочнение энергией взрыва, электрогидравлический удар, науглероживание, вакуумная обработка, применение холодильников и т.д.
Упрочнение взрывом.
Весьма перспективным способом повышения износостойкости железнодорожных крестовин является упрочнение их рабочей поверхности энергией взрыва. В нашей стране обширные исследования взрывного упрочнения высокомарганцевой стали были начаты в 1960 г. в Институте гидродинамики Сибирского отделения АН СССР совместно с Новосибирским стрелочным заводом [62]. Известны в этой области работы Волгоградского политехнического института, Московского института стали и сплавов, Восточного научно-исследовательского горнорудного института, Всероссийского научно-исследовательского института железнодорожного транспорта и др.
Большое число лабораторных экспериментов и промышленных испытаний отливок, упрочненных взрывом, показало, что их износостойкость повышается на 50-300%, а долговечность возрастает в 1,31,8 раза [63]. Стоимость обработки взрывной волной относительно невысока и составляет примерно 1-7% стоимости отливки.
Сущность упрочнения деталей взрывом заключается в том, что рабочая поверхность отливок подвергается кратковременному воздействию (10‘9 с) высоких давлений (30-40 ГПа), возникающих при детонации различных видов взрывчатых веществ (ВВ). При этом поверхностная твердость составляет 300-500 НВ и более. В качестве ВВ применяют порошкообразный гексоген, аммониты, детонит, тетрил и пластические ВВ различных типов.
Упрочнение взрывной волной изменяет структуру металла, его физикомеханические свойства, а также размеры изделия. Анализ физикомеханических свойств стали Г13Л показывает, что ее прочностные характеристики после упрочнения взрывной волной существенно улучшаются; при этом пластичность металла оказывается достаточной [63].
Временное сопротивление разрыву и относительное удлинение, получаемые в результате упрочнения взрывом и влияющие на износо- и дефектостойкость, зависят не только от уровня достигнутой твердости на упрочненной поверхности, но в значительной степени от исходной прочности и пластичности стали. Так у стали с низкой прочности уже после упрочнения до 345 НВ (нагружение зарядом ВВ 9 мм) характеристики пластичности резко снижаются. Заряд 15 мм (375 НВ) нежелательно применять к материалу с низким исходными свойствами, так как снижается эффект увеличения прочности из-за исчерпания пластических свойств металла. Изменение ударной вязкости зависит в основном от режима упрочнения, а с исходными свойствами связано слабо.
Ударно-волновая обработка стали не приводит к каким либо фазовым преобразованиям в исследованном металле, т.е. аустенит стали Г13Л является достаточно устойчивым, а упрочнение идет за счет скольжения и двойникования. Повышенная хрупкость отдельных участков может вызываться усиленным наклепом границ зерен у мест газовых пор, плен, неметаллических и шлаковых включений из-за разницы их плотности с плотностью металла [64].
В общем случае степень упрочнения металла при взрыве определяется величиной давления продуктов взрыва и длительностью его воздействия. В системе ВВ – металл для каждого конкретного случая имеют место свои специфические особенности взаимодействия, точные критерии определения величины давления и его длительности на металл отсутствуют.
Взрывное упрочнение железнодорожных крестовин осуществляется детонацией слоя ВВ в контакте с поверхностью упрочняемого металла. Опытным путем наиболее оптимальной была признана схема упрочнения с двухкратным взрывом с боковым нависанием ВВ, при которой происходило одновременное упрочнение поверхности катания и рабочих галтелей. Эксплутационные испытания большого числа упрочненных взрывом крестовин показали, что их износостойкость была в 1,5-2,0 раза выше, чем неупрочненных, отлитых из металла тех же плавок [63,65]. Таким образом степень упрочнения высокомарганцевой стали зависит от ее химического состава, механических свойств, чистоты аустенитной структуры, давления, характера приложения нагрузки. На результаты упрочнения стали взрывом влияют количество и свойства взрывчатых веществ, величина заряда, способ нанесения ВВ на упрочняемую поверхность, направление распространения ударной волны, число взрывов.
Электрогидравлический удар.
На Днепропетровском стрелочном заводе был разработан, опробован и предложен способ упрочнения железнодорожных крестовин методом
41 электрогидравлического удара [66]. Плавное и точное регулирование ударной нагрузки обеспечивается использованием электроимпульсных разрядов в среде электролита на установках электрогидравлического удара (ЭГУ), принцип действия которых основан на создании избыточного давления при скоростном изменении агрегатного состояния электролита под воздействием высоковольтных разрядов. Была предложена формула для расчета напряжения на электроде, обеспечивающего получение заданной твердости отливок из высокомарганцовистой стали с учетом ее химического состава. При воздействии на высокомарганцовистую сталь электроимпульсными разрядами в среде электролита при напряжении ниже рассчитанного по формуле упрочнение крестовин не обеспечивается; если же это напряжение выше рассчитанного, то на обрабатываемой поверхности образуются микротрещины. При существенном увеличении напряжения на электроде по сравнению с рассчитанным происходит разрушение отливки. Наибольшая твердость (360 НВ) рабочей поверхности достигалась при обработке ЭГУ (пятикратное нанесение ударов) на подкладках из стального листа. Спад твердости до значения необработанного металла наблюдается на глубине 7 мм; протяженность зоны разупрочнения при этом составляла примерно 4 мм.
Проведенные металлофизические, электронно-графические исследования деформированного металла показали, что в поле упругих волн, возникающих при ударном нагружении (кратковременное многократное действие высокого давления), состояние металла значительно отличается от состояния, появляющегося при действии других видов нагружения. С начальных стадий деформаций наблюдается скольжение множества дислокаций, происходящее практически одновременно по многим непараллельным плоскостям: наблюдается переход к интенсивному двойникованию, плотность которого весьма высока.
Дальнейшее исследование и совершенствование технологий упрочнения взрывом и ЭГУ рабочих поверхностей деталей и широкое применение этих технологий в промышленности позволит существенно повысить надежность и увеличить срок службы отливок из высокомарганцовистой стали.
Метод науглероживания.
Ученые ВЗИИТа предложили новый метод продления срока службы крестовин, который они успешно внедрили на Московско-Ряменском и Раменском дистанциях пути Московской дороги [67].
Метод науглероживания состоит в насыщении поверхности изнашиваемой части крестовины из стали Г13Л потоком атомарного углерода за счет обработки сварочной дугой угольного электрода диаметром 6 мм марки СК-6 на постоянном токе обратной полярности (плюс на электроде) силой 150-160 А. Образующиеся карбиды железа и марганца аустенитного металла и предохраняют металл крестовины от износа на глубину науглероживания (1-1,5 мм).
Упрочнять поверхности сердечника и изнашиваемых частей у совиков из высокомарганцовистой стали марки Г13Л типов Р50 и Р65 марок 1/9 и 1/11 методом науглероживания можно как в пути, так и в станционарных условиях. Обрабатывать крестовины в пути рекомендуется после пропуска по ним не менее 5-10 млн. т груза. Максимальный износ упрочняемых поверхностей крестовин (в сечении сердечника 40 мм) не должно превышать 2 мм. Науглероживать крестовины вне пути следует непосредственно перед их укладкой.
Опыт показал, что износ упрочненной науглероживанием крестовины начинается только после пропуска по ней 80-90 млн. т. при соблюдении технологии срок ее службы увеличивается не менее, чем вдвое, а при периодическом двух- трехкратном науглероживании или в сочетании с последующей электродуговой наплавкой изношенного места может быть обеспечен наибольший срок службы крестовин по нормативам общего износа.
Вакуумная обработка.
При вакуумной термической обработке железнодорожных крестовин [46,68] содержание водорода на расстоянии 8 мм от поверхности снижается с 7-12 см3 на 100 г металла до 0,8.. 1 см3, в результате чего ударная вязкость деформированной стали (30 % деформации) возрастает в 1,4 раза. Водород хорошо растворяясь в высокомарганцевом аустените, оказывает отрицательное влияние на пластичность стали при ее деформировании. При значительных ударных нагрузках это приводит к выкрашиванию металла крестовин. Объясняется это явление тем, что при деформировании водород из ионного и атомарного состояния переходит в молекулярное на границах зерен, в зоне залегания неметаллических включений и др. При накоплении водорода его давление возрастает, что способствует образованию сначала микро-, а затем и макротрещин. Удалить водород в процессе его плавки не представляется возможным, так как легирование металла производится доменным ферромарганцем с высокой водородонасыщенностью ( до 30 см3 на 100 г металла).
Вакуумная термообработка железнодорожных крестовин производится в печи глубокого вакуума (1,33…0,13 Па) по следующему режиму: нагрев до 1100 °С в течении 24 ч с последующим охлаждением в проточной воде.
Применение холодильников.
Крестовины в соответствии с ГОСТ-7376 изготавливают из высокомарганцовистой стали 110Г13Л представляют собой массивные отливки сложной конфигурации, заливаемые в песчано-глинистые формы. Структура стали при этом способе производства характеризуется крупнозернистым строением, наличием массивных карбидов, развитой дендритной ликвацией и пористостью, то есть имеет ряд недостатков, которые полностью не могут быть устранены последующей термической обработкой [47].
В литейном производстве известен способ местного повышения качества металла посредством использования наружных холодильников.
Технология отливки крестовин с использованием холодильников изменяется незначительно. Холодильники, представляющие собой стальные полосы со скошенными краями, запрессовывают в стандартную песчаноглинистую форму в районе зоны перекатывания. Их присутствие приводит к увеличению теплоотвода и скорости охлаждения металла на данном участке, создает определенную направленность кристаллизации и уменьшает пористость стали.
Применение наружных холодильников при изготовлении из высокомарганцовистой стали крупных заготовок со стенками толщиной 40-100 мм способствует получению мелкозернистой структуры в зоне их действия и повышению сопротивляемости образованию горячих трещин, если температура заливки формы не превышает 1420 °С, а соотношение толщин стенок холодильника и отливки составляет 0,8…0,9 [66].
Внедрение отливки крестовин с холодильниками на стрелочных заводах требует решения ряда проблем, таких как организация производства, повторное использование холодильников и их удаление с вибрационных выбивных решеток.
Применение внутренних холодильников для сталей различных марок с этой же целью не дало положительных результатов из-за плохой свариваемости металла холодильников с металлом отливки, ухудшения структуры металла отливок и т.д. [66].
Наплавка крестовин
До недавнего времени изношенные крестовины восстанавливались только в пути электродами ОМГ-Н и ЦНИИН-4 [69,17-19]. Однако ручная наплавка мало производительна, условия сварщиков тяжелые. Кроме того при многослойной наплавке практически не удается избежать трещин в наплавленном металле. Поэтому к наплавке допускаются крестовины с вертикальным износом усовиков и сердечников не более 4,5 мм. В Институте электросварки им. Е.О. Патона разработана технология полуавтоматической наплавки крестовин в стационарных условиях,
45 позволяющая восстанавливать крестовины с вертикальным износом усовиков и сердечника до 25 мм при высоком качестве наплавленного слоя. Для наплавки применяются самозащитная порошковая проволока ПП-АН105 диаметром 2,8 мм и специализированные полуавтоматы типов А-765, А-1197С и др. Режим наплавки: ток 200-220 А, напряжение дуги 22-24 В, полярность обратная. Производительность наплавки составляет 3,5..4 кг/ч. Оптимальный состав наплавленного металла, %: С 0,85; Мп 14; Ы1 3,5 и 81 0,2. Твердость металла после наплавки НВ 180.. .200, после наклепа – до 400.
Полуавтоматическая наплавка крестовин порошковой проволокой ПЛАН 105 применяется на Юго-Западной и Красноярской железных дорогах. На каждой из дорог ежегодно наплавляется более 300 крестовин.
Основным недостатком механизированной наплавки порошковой проволокой является развитие горизонтальных усталостных трещин в основном металле по границе сплавления их с вертикальными трещинами, возникающими в горячем наплавленном металле и развивающимися в процессе эксплуатации. Кроме того наблюдаются возникновения трещин в хвостовой части, выколов усовиков в начале врезки. Это объясняется недостаточно тщательным контролем подготовленных к наплавке крестовин. Поскольку контроль производится только путем визуального осмотра крестовин, при этом все зависит от добросовестности сварщика и шлифовщика [19].
Список литературы
- Современные методы упрочнения поверхностей деталей машин : Аналит. обзор. (Науч.-техн прогресс в машиностроении; Вып.9.) М. : МЦНТИ, 1989.286 с.
- Хасуй А., Моригаки О. Наплавка и напыление. М. Машиностроение. 1985. 239 с.
- Сидоров А.И. Восстановление деталей машин напылением и наплавкой. -М. М.: Машиностроение, 1987.- 192 с.
- Лещинский Л.К., Самотугин С.С., Пирч И.И. и др. Плазменное поверхностное упрочнение. Киев.:Техника.199О. 109с.
- Меликов В.В. Многоэлектродная наплавка. – М.: Машиностроение, 1988.- 144 с.
- Земзин В.Н. Сварные соединения разнородных металлов. М.-Л., изд -во «Машиностроение», 1966.
- А.Н.Краснов, С.Ю.Шаривкер, В.Г.Зильберберг, Низкотемпературная плазма в металлургии, М., Металлргия, 1970.
- Калугин И.Д., Николаева А.В. Дуговая плазменная струя как источник теплоты при обработке материалов. – «Сварочное производство», 1959, №9.
- Плазменная наплавка металлов. Вайнерман А.Е., Шоршоров М.Х., Веселков В.Д., Новосадов В.С., изд -во «Машиностроение», 1969 г., 192 с.
- Ю.Л.Н.Усов, А.И.Борисенко Применение плазмы для получения высокотемпературных покрытий. М., Наука, 1965.
- Нисковских Н.Н., Карлинский С.Е., Беренов А.Д. Машины непрерывного литья слябовых заготовок. М: Металлургия. 1991. 272 с.
- Развитие технологии непрерывной разливки стали. Лякишев Н.П., Шалимов А.Г. М.: ЭЛИЗ,2002. 208 с.
- Изменение геометрических и динамико-прочностных характеристик крестовин в процессе эксплуатации. / Н.Н. Путря, Б.Э. Глюзберг, А.М. Тейтель, М.И. Титаренко. // Вестник ВНИИЖТ. 1997. -№ 5. – с.47-51.
- Особенности наклепа в пути сердечников крестовин из высокомарганцовистой стали 110Г13Л. / Б.Э. Глюзберг, К.И. Красиков // Вестник ВНИИЖТ. 1984. -№ 7. – с.50-52.
- Крысанов Л.Г., Титаренко М.И. Влияние средних статистических осевых нагрузок вагонов на срок службы крестовин // Вестник ВНИИЖТ. – 1981.-№ 7. -с. 52-55.
- Путря Н.Н. Улучшение условий эксплуатации крестовин // Вестник ВНИИЖТ. – 1965. № 6. – с. 29-33.
- Шепель В.Н., Обухов А.В. Сварка и наплавка рельсов и крестовин И Транспорт-М.: 1959. С. 25-38.
- Андреев В.В., Ушаков М.В. Термитная и дуговая сварка высокомарганцовистых сталей типа 110Г13Л // Сварочное производство. 1987. №5. С. 13-15.
- И. А. Кондратьев, Н.М. Пономаренко. Полуавтоматическая наплавка крестовин стрелочных переводов. В сб. Наплавка в машиностроении и ремонте. Теоретические и технологические основы наплавки. Киев. ИЭС им. Е.О. Патона, 1981, с. 129-132.
- Плазменные и лазерные методы упрочнения деталей машин/ Н.В. Спиридонов, О.С., Кобяков, И.Л. Куприянов; Под. Ред. В.Н. Чачина. – Мн.: Выш. Шк„ 1988.- 155 с.
- Хренов К.К. Электрическая сварочная дуга. Машгиз, М., Киев, 1949.
- Технология электрической сварки плавлением. Под ред. Б. Е. Патона. Москва-Киев, Машгиз, 1962.
- Лукашек Я., Лебль К. Способ автоматической наплавки высоколегированных сталей и сплавов под флюсом. – «Автоматическая сварка», 1959, №12.
- Пацкевич И.Р., Баутина В.А. Вибродуговая наплавка бронзы на сталь. – «Сварочное производство», 1962, №11.
- Никитин В.П. Метод сварки металлов с раздельным процессами плавления. ДАН СССР, т.56, №5, 1947.