Сейчас ваша корзина пуста!
Плазменное нанесение жароизносостойкого покрытия на медную основу
Цикл статей:
Глава 1 – Формирование структуры и свойств при плазменной наплавке износостойких покрытий на медь и высокоуглеродистую, марганцовистую стали
Глава 2 – Материлы и методы исследования
Глава 3 – Разработка конструкции плазмотрона с расширяющимся каналом сопла для плазменной наплавки
Глава 4 – Плазменное нанесение жароизносостойкого покрытия на медную основу
Исследование распределения твердости по сечению покрытия и медной основы
Экспериментальная наплавка медных образцов 350x350x40 проводилась с помощью плазмотрона с расширяющимся каналом. Медный образец укладывался в специальную изготовленную печь, где на дне располагались тэны. Процесс наплавки вели металлическим порошковым сплавом ПР-Н77Х15СЗР2 на предварительно разогретую медь до температуры 600 °С, расход порошка 0,3 г/сек, расход аргона 1 м3/час, при силе тока 200 А и напряжении на дуге 40 В.
Проведенные исследования твердости на поверхности наплавленного слоя показали следующие значения – 75-82 НКВ. По мере удаления от поверхности покрытия твердость плавно снижается, достигая на расстоянии 1 мм от границы наплавленного слоя и металла основы значения 70 НКВ (рис. 4.1). На расстоянии 5 мм от поверхности наплавки наблюдается падение твердости, которое происходит на толщине образца примерно равной 1-1,5 мм, свидетельствующее о некоторой размытости переходного слоя между наплавленным металлом и медной основой. Уменьшение твердости происходит до уровня твердости меди, т.е. в 5-8 раз. Таким образом, твердость наплавленного слоя имеет достаточно высокую
однородность по сечению, превышает твердость меди в 5-8 раз и имеет размытую переходную область.
На рис. 4.2. приведено распределение микротвердости по сечению в области границы раздела основа-наплавка. Для исследования выбран участок на котором не было расплавления медной основы. В центральной области по толщине наплавки микротвердость составляет -2665 Н/мм2. Далее, при приближении к границе раздела наплавки и медной основы, происходит некоторое повышение микротвердости до -3375 Н/мм2, что, по-видимому, связано с повышением дисперсности структуры в результате высокой скорости охлаждения при кристалллизации первых тонких слоев наплавленного металла. На границе раздела на толщине примерно 0,5-0,3 мм происходит падение микротвердости до -840 Н/мм2, которая практически не меняется при продвижении в глубь меди.
Разброс значений твердости НКВ, микротвердости Но,981 и их среднее значение в наплавленном слое, переходной зоне и медной основе представлены в таблице 4.1. Видно, что наибольший разброс значений этих свойств наблюдается в переходной зоне, что является следствием взаимодействия металла основы и наплавки в процессе плазменного нанесения покрытия.
Средняя микротвердость покрытия примерно в 4 раза выше, чем медной основы, что несколько меньше, чем при измерении твердости и отражает локальные свойства структуры наплавки и меди.
Можно полагать, что износостойкость наплавленного слоя, которая пропорциональна уровню твердости, должна быть примерно в 4-8 раз выше износостойкости медной основы.
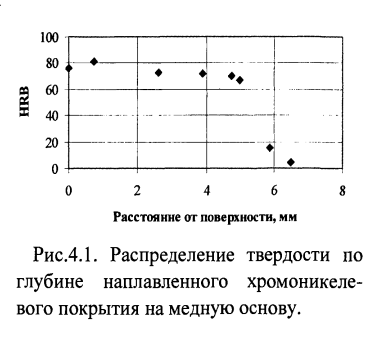
Кроме твердости, важным свойством, от которого зависит эксплуатационная стойкость покрытия, является его прочность и особенно прочность его сцепления с металлом основы.
Для определения прочности покрытия проводили испытания на растяжение образцов, вырезанных из поверхности наплавленного металла. Оценка уровня прочности показала, что сгв металла наплавки составляет 575 Н/мм2, а медной основы – 230 Н/мм2 (табл.4.1). Следует отметить, что разрушение наплавленного металла происходило по хрупкому механизму без заметной пластической деформации.
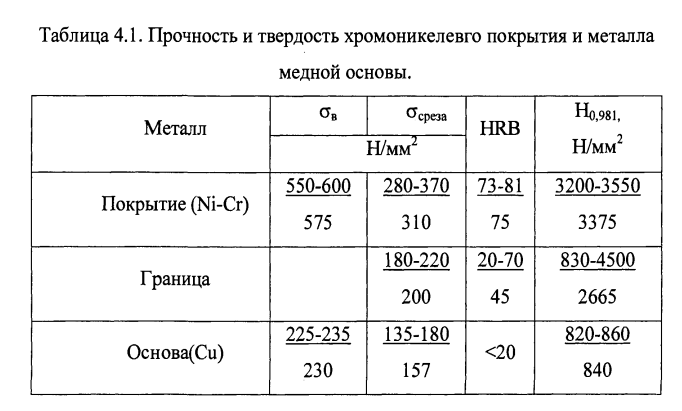
Основной особенностью работы медного кристаллизатора машины непрерывного литья заготовок (МНЛЗ) является скольжение кристаллизующегося металла стальной заготовки вдоль стенки кристаллизатора. При этом очевидно, что в поверхностных слоях стенки медного кристаллизатора возможно возникновение напряжений сдвига или среза. Можно предположить, что в случае недостаточной прочности сцепления покрытия с медной стенкой, первое может сползать с нее как внутренняя “рубашка”.
В связи с этим, для оценки служебных свойств медного кристаллизатора с наплавленным покрытием представляло интерес оценить прочность сцепления покрытия с медной основой в условиях, имитирующих напряженное состояние, которое может возникать в поверхностных слоях стенки кристаллизатора во время его работы.
Специально для этого был разработан метод и приспособления для испытания на срез.
Испытания на срез показали, что напряжение среза осреза наплавки вдвое выше, чем у меди (ЗЮН/мм2, против 157 Н/мм2). Металл переходной зоны (береза = 200 Н/мм2) также прочнее меди (табл.4.1). Типичные диаграммы испытания на срез представлены на рис. 4.3. Разрушение медной основы и переходного слоя происходит после значительной пластической деформации изгиба и смятия металла пуансоном (рис. 4.3 а и б). Срыв нагрузки на диаграмме испытания наплавленного слоя является следствием образования в наплавке хрупкой трещины (рис. 4.3 в).
Однако, при этом отрыва покрытия от медной основы не произошло – на диаграмме это отражается тем, что нагрузка не упала в результате этого до нуля. Можно отметить, что в процессе испытания разрушение переходной зоны происходило практически по меди, а не по линии стыка наплавка- подложка, что свидетельствует о высокой прочности сцепления.
Таким образом, полученные результаты свидетельствуют о том, что прочность сцепления покрытия с медной основой ниже прочности покрытия на срез и выше, чем прочность на срез медной основы. Это изменение прочности на срез по сечению (рис. 4.4) позволяет предположить, что разрушение покрытия или его сползание с медной стенки кристаллизатора в процессе его работы практически исключено.
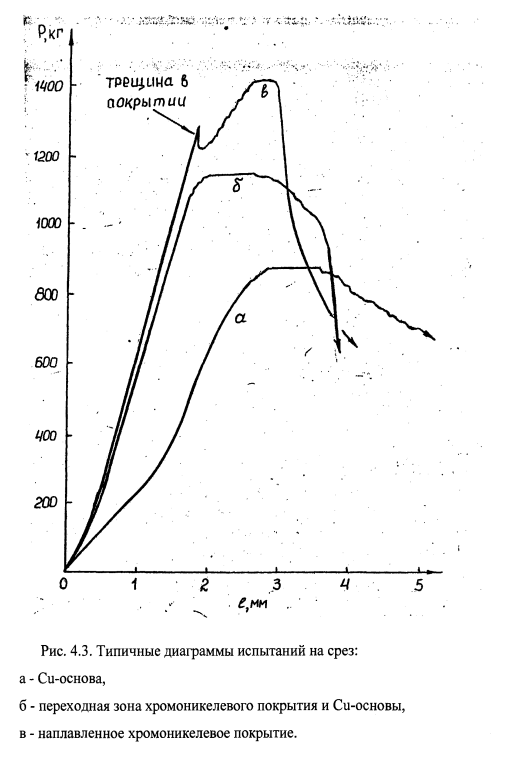
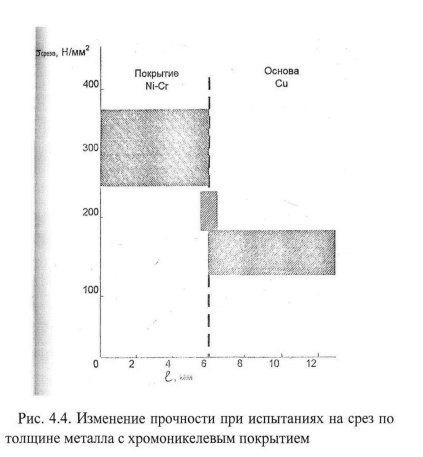
Исследования износостойкости металла покрытия проводили методом нанесения непрерывной царапины на поперечном шлифе образца с покрытием. Результаты испытаний представлены на рис. 4.5. Для покрытия характерен очень малый разброс значений ширины лунки – 23-26 мкм. Переходная зона узкая, всего 0,10-0,15 мм. Ширина лунки в ее пределах возрастает до 28-38,5 мкм. Медная основа имеет ширину лунки в 2-2,5 раза больше, чем плазменное покрытие 46-58 мкм.
Износ оценивали, как величину пропорциональную квадрату ширины лунки, поскольку именно эта величина отражает потери материала при нанесении царапины конусом пирамиды. Оценка показала, что износостойкость плазменного покрытия в 4-5 раз больше, чем медной основы.
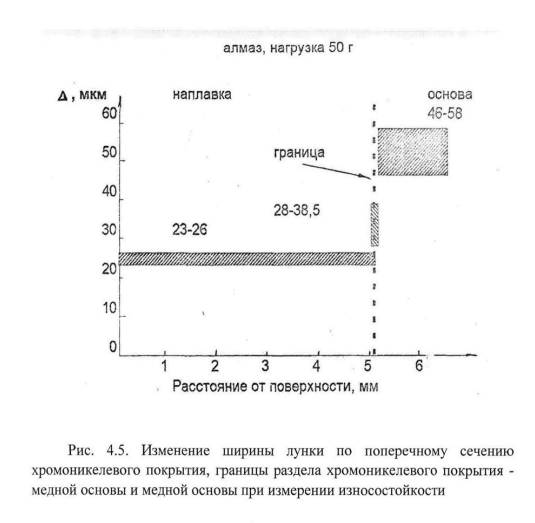
Таким образом, с учетом уровня твердости, износостойкости покрытия и сопротивления на срез, можно ожидать увеличения эксплуатационной стойкости кристаллизатора МНЛЗ до 500-1000 плавок.
Исследование микроструктуры по сечению покрытия и металла основы
На рис.4.6, представлена панорама микроструктуры на границе раздела основной металл – наплавка. Медная основа имеет достаточно крупное ~120 мкм равноосное зерно с множеством двойников, что характерно для отожженной структуры. Есть двойники и непосредственно на самой границе. Существенных различий в характере микроструктуры у границы основа- наплавка нет. Но можно отметить чуть больший размер зерна меди у границы (порядка 140 мкм).
Никаких дефектов (пор, микротрещин и т.п.) на границе раздела не обнаружено. Наплавка чрезвычайно плотно прилегает к основе – толщина стыка соизмерима с толщиной межзеренных границ меди.
Можно предположить, что на основном протяжении границы расплавления подложки в процессе наплавления №-Сг не происходит. Однако имеются незначительные участки, на которых «языки» расплавленной меди внедряются в металл наплавки на глубину до 0,2 мм. В этих местах четкая граница раздела Си – №-Сг отсутствует, зерно меди не вытравливается. Доля таких участков не превышает 5 % от общей протяженности границы (рис. 4.7)
Наплавка в области, примыкающей к меди, имеет мелкодисперсную структуру. Протяженность этой зоны 0,2-0,3 мм. Далее располагается зона дендритов (рис. 4.8), вид которых практически не изменяется до самой поверхности наплавки.
Таким образом размытость по поперечному сечению и высокая твердость переходного слоя, а также высокая прочность сцепления покрытия с медной основой связаны с образованием слоя с мелкодисперсной структурой со стороны покрытия, а также взаимного внедрения участков медной основы и хромоникелевого сплава.
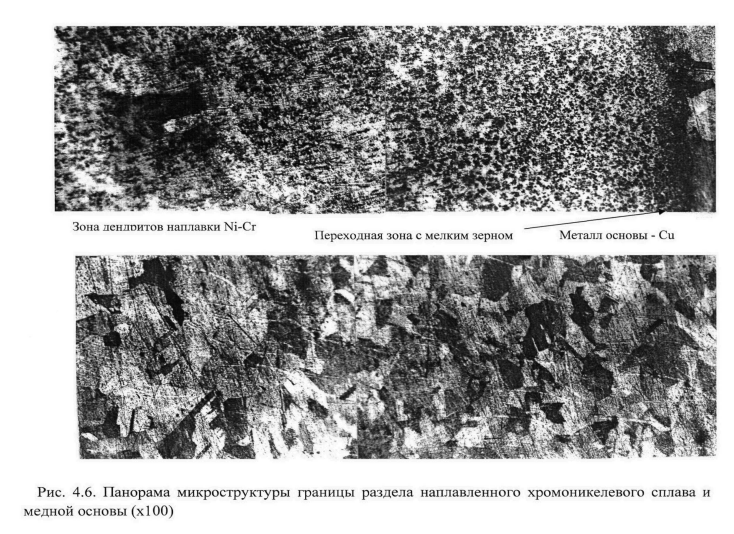
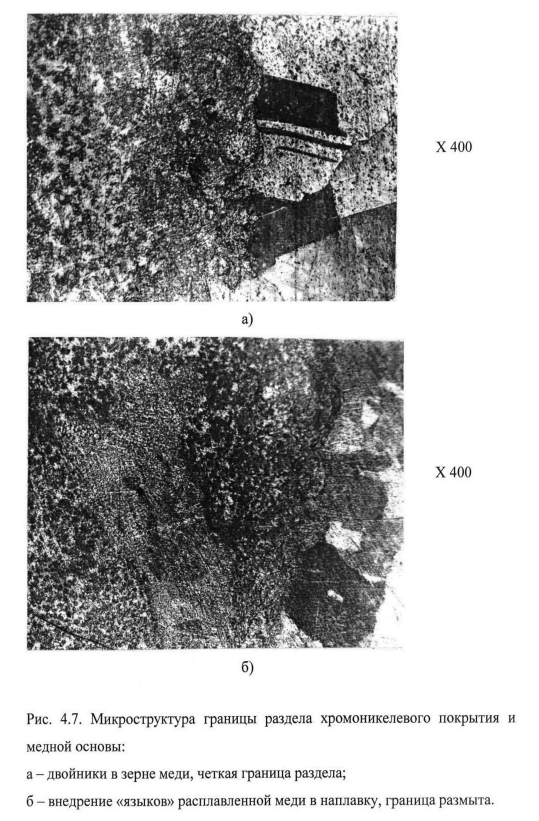
Исследование напряженного состояния наплавленного слоя и металла основы, фазового состава, периода кристаллической решетки и концентрационных зависимостей покрытия, переходного слоя и металла основы
Рентгеноструктурным методом оценивали уровень остаточных микронапряжений (по ширине рентгеновских интерференций (311) металла).
В результате плазменной наплавки в наплавленном слое возникают высокие внутренние микронапряжения, о чем свидетельствует большая размытость рентгеновской интерференционной линии (311). Причем в тонком поверхностном 15 мкм слое они наиболее высоки – ширина рентгеновской линии достигает 62 мрад (рис. 4.9). Далее внутренние микронапряжения резко уменьшаются и по глубине наплавленного слоя практически не меняются. Однако их уровень весьма высок и может быть соотнесен с уровнем микронапряжений, возникающих в углеродистой закаленной стали, содержащей 0,4-0,9 % С.
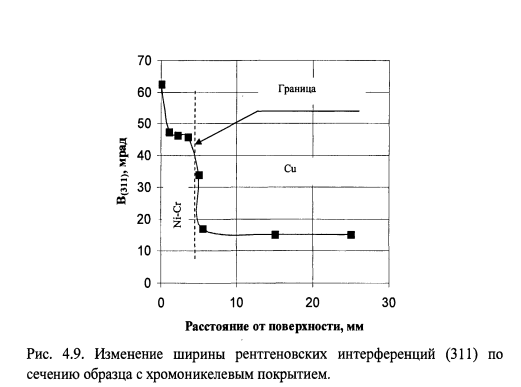
У границы наплавки остаточные микронапряжения резко снижаются, и далее по сечению медной подложки практически не меняются. Ширина рентгеновской линии в меди составляет 15 мрад (рис. 4.9), что почти в 4 раза меньше, чем в наплавленном металле.
Высокий уровень остаточных микронапряжений в наплавленном металле, по-видимому, связан, с особенностями фазового состава образующегося в процессе охлаждения расплавленного металла на поверхности медной основы в результате протекания процессов конвекции и взаимной диффузии химических элементов, входящих в состав наплавленного сплава и подложки. Нельзя исключить также роли термического фактора, связанного с различием в коэффициентах линейного расширения меди и никелевых сплавов, которые могут различаться почти в 1,5 раза [75].
По данным рентгеноструктурного анализа фазовый состав по сечению образца с наплавкой представлен в табл.4.2. Вблизи поверхности наплавки (~15мкм) выявлены два типа твердых растворов ЫьСг и №-Си.
Присутствуют также нитриды хрома, которые, по-видимому, образуются в процесс кристаллизации наплавленного слоя.
Далее (~3,5 мм) вблизи границы наплавленного слоя и металла основы появляются окислы хрома и участки меди. Окислы хрома очевидно образуются при контакте расплавленного металла с воздухом.
Под наплавленным слоем (~6-8 мм) кроме медной основы выявлены окислы и немногочисленные нитриды хрома. Проникновение их в медную основу, очевидно, связано с перемешиванием жидкого расплава и расплавленных поверхностных слоев меди.
На глубине 8-10 мм выявляется только медь.
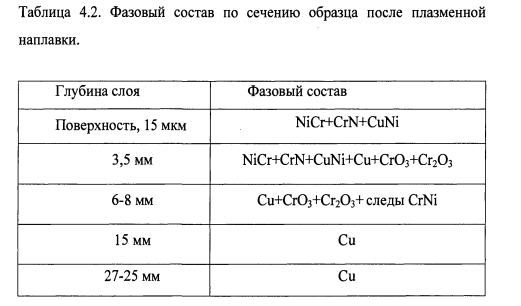
При плазменном нанесении покрытия происходит разогрев металла основы, что создает условия для протекания диффузионных процессов, интенсивность протекания которых может в значительной степени определять структурное состояние переходного слоя между покрытием и подложкой. Для оценки интенсивности протекания диффузионных процессов проводили измерение периода кристаллической решетки в наплавке и медной основе и микрорентгеноструктурный анализ по поперечному сечению образца для построения концентрационных зависимостей химических компонентов сплава.
Данные об изменении периода кристаллической решетки представлены на рис. 4.10,4.11.
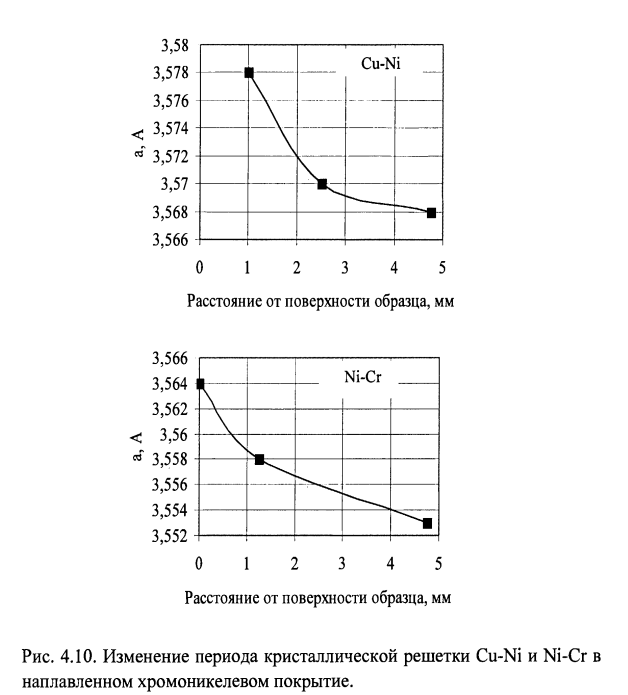
Период кристаллической решетки основных фазовых составляющих наплавленного слоя Си-КП и КП-Сг монотонно уменьшается от его поверхности к границе медной основы. Причем основные изменения периода решетки наблюдаются в пределах половины толщины наплавленного покрытия (до 2-2,5 мм).
Период кристаллической решетки меди плавно уменьшается от границы наплавленного слоя. Это уменьшение происходит на глубину, сравнимую с толщиной образца. В связи с этим изменение периода решетки, как в наплавленном слое, так и в меди, не видимому, не связано с диффузионными процессами в ходе операции нагрева при наплавлении и последующего охлаждения. Это подтверждает оценка
толщины диффузионных слоев. Так, если принять коэффициент диффузии № в Си при температуре 700°С равным 1,4×10’11 см2/сек [76], а время нагрева и охлаждения от 1 до 100 сек, то среднее расстояние диффузии никеля в медь составит Х=7ш’=0,01 – 1,0 мкм, что на несколько порядков меньше, чем изменение периода кристаллической решетки.
То же самое можно сказать об изменении параметров решетки в наплавленном слое.
Таким образом, изменение периода кристаллической решетки в наплавленном слое и медной основе обусловлены не взаимной диффузией химических элементов №, Сг, и Си в твердом состоянии, а другими причинами. Можно предположить, что одной из причин наблюдаемого изменения периода решетки, является возникновение при охлаждении внутренних остаточных термических макронапряжений и микронапряжений в результате особенностей фазового состава, образующегося при наплавке, сплава.
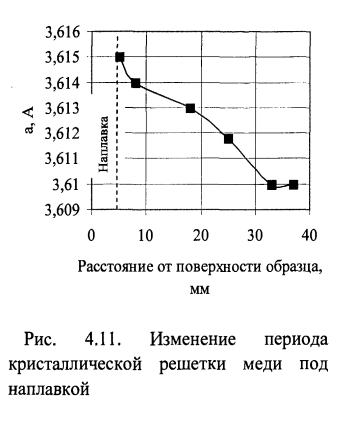
Для оценки интенсивности протекания диффузионных процессов в процессе нанесения покрытия проводили микрорентгеноспектральный анализ на поперечных шлифах образцов с покрытием. Как показали исследования, содержание легирующих элементов – 81, М и Ре в наплавленном слое ниже, чем в исходном. Так средняя концентрация кремния и железа в 3 раза меньше, а никеля – на 17% по массе (рис. 4.12-4.15). Кроме того, в наплавленном слое обнаружено около 0,7% ниобия (рис. 4.12). Содержание хрома практически не изменяется и составляет около 16% (рис. 4.13).
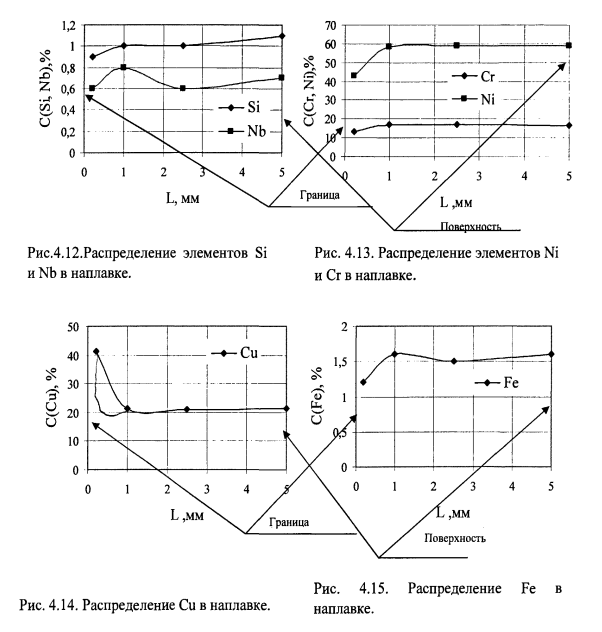
Наиболее интересным оказалось обнаруженное высокое содержание в наплавленном слое меди от 20% до 40% (рис. 4.14). При этом высокая концентрация меди наблюдается вблизи границы наплавленного слоя (примерно до 0,5 мм). Далее по сечению наплавки она практически не изменяется.
Важно отметить, что вблизи границы наплавленного слоя происходит уменьшение концентрации 81, №, Ре и Сг. Это уменьшение отмечается на расстоянии до 1 мм от границы раздела между наплавкой и основным металлом.
Для более точного определения концентрационного профиля распределения элементов проводили спектральный анализ по основным элементам в окрестности переходного слоя (рис. 4.16). При этом осуществляли послойный рентгеноспектральный анализ с шагом равным 46 мкм по обе стороны от границы раздела (рис. 4.17). Концентрационные кривые по основным элементам вблизи границы раздела представлены на рис.4.18-4.21.
Концентрация кремния в исследованном слое ниже, чем в исходном сплаве (рис. 4.17). Наблюдается всплеск концентрации этого металла непосредственно вблизи границы раздела между наплавкой и медной основой, вероятно связанный с образованием при наплавлении кислородных включений. Этим вероятно объясняется пониженная концентрация кремния в наплавленном слое (см. рис. 4,12).
Концентрация никеля скачкообразно снижается на расстоянии 200-250 мкм при переходе от наплавленного слоя к медной основе. Для хрома это снижение наблюдается на расстоянии около 100 мкм (рис.4.19).
Неоднородная концентрация хрома в наплавленном слое, вблизи границы, вероятно связана с образованием нитрида хрома, выявленного рентгеноструктурным методом.
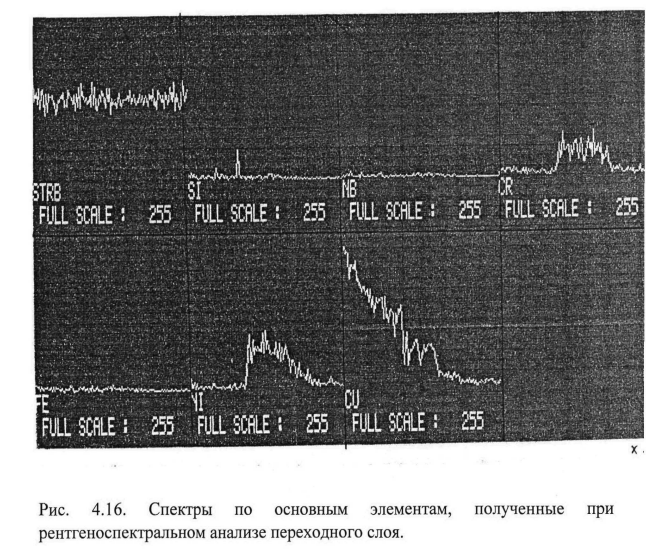
Скачок концентрации на границе между наплавкой и основой отмечен для меди (рис. 4.20). Вблизи границы, со стороны наплавки, концентрация меди достигает 40-50%, а затем она снижается до 20%, что соответствует данным рентгеноструктурного анализа (рис.4.14).
Концентрация железа также резко изменяется при переходе от наплавленного металла к медной основе и его количество существенно ниже, чем в исходном сплаве (рис. 4.21).
Полученные концентрационные кривые подобны тем, которые наблюдаются для диффузионных процессов.
Таким образом, в процессе формирования наплавленного слоя кроме перемешивания расплава происходит окисление его компонентов, сродство.
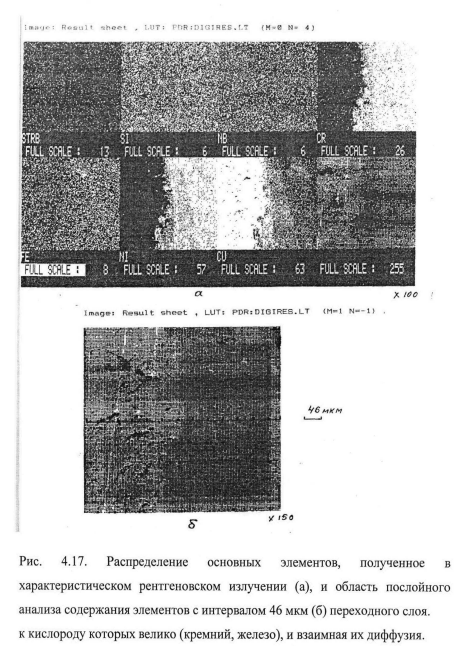
Как показала оценка коэффициента диффузии исходя из наблюдаемых концентрационных профилей, для длительности процесса в пределах 1-100 сек, его величина изменяется от 10′4 до 10’6 см2/сек. Коэффициент диффузии, например, никеля в меди и меди в никеле составляют при 600- 700°С 1,4×10′” и 4,1х10′12 см2/сек соответственно [76]. В тоже время, известно, что величины коэффициентов диффузии в жидком состоянии примерно одинаковы и составляют 10′4-10’5 см2/сек [77]. Поэтому можно полагать, что наблюдаемый концентрационный профиль является следствием диффузии компонентов в жидком расплаве.
Известно, что жаропрочные сплавы на никелевой основе по своему химическому и фазовому составу разнообразны. К числу элементов, повышающих их жаропрочность, относятся Со, Сг, Мо, Т1, ЫЬ, А1, В и другие [78]. Медь образует с никелем непрерывный ряд твердых растворов и не 79
увеличивает его жаропрочность [78]. Однако медь придает никелевым сплавам пассивность по отношению к ряду агрессивных сред, что является положительным фактором [79].
В результате плазменной наплавки хромоникелевого сплава на поверхности меди формируется по существу новый сплав, содержащий в виде компонента до 20% меди с меньшим содержанием кремния, бора и железа.
Таким образом:
- Проведено комплексное исследование химического и фазового составов, микроструктуры и механических свойств жаростойкого хромоникелевого покрытия на медную основу.
- Установлено, что твердость покрытия в 5-8 раз, а износостойкость в 4-5 раз выше, чем твердость и износостойкость медной основы.
- Прочность сцепления покрытия с медной основой при испытании на срез на 20% выше, чем прочность на срез меди, и на 35% ниже таковой для металла покрытия.
- Показано, что высокая прочность сцепления хромоникелевого покрытия с медной основой является следствием формирования при наплавке плавной переходной зоны с мелкодисперсной структурой, образовавшейся в результате конвективных и диффузионных процессов массопереноса в жидком наплавленном слое.
- Высокий уровень твердости и прочности металла покрытия обусловлен химическим составом, структурой и внутренними микронапряжениями, формирующимися в ходе наплавления, кристаллизации и охлаждения наплавленного металла и медной основы.
- Полученные экспериментальные результаты позволяют ожидать увеличения эксплуатационной стойкости стенок медного кристаллизатора машин непрерывного литья заготовок с покрытием данного типа до 500-1000 плавок.
Список литературы
41. Б.Э. Глюзберг. Особенности износа крестовин стрелочных переводов с. 39-42.
42. Н.Я. Самарин, Р.З. Кац, В.А. Старцев О повышении эксплуатационной стойкости высокомарганцовистой стали для железнодорожных крестовин.
43. Красиков К.И., Строк Л.П., Шаурова М.К. О распределении углерода в аустените при пластической деформации. – Известия АН СССР, Металлы, 1976, № 2 с. 171-174.
44. О влиянии содержания углерода, марганца, никеля и азота на фазовый состав и свойства деформированной высокомарганцовистой стали / Н.Я. Самарин, Р.З. Кац, В.А. Старцев, И.А. Петрова. – Металловедение и термическая обработка металлов, 1981, № 1. с. 39-42.
45. А.Г. Коган, В.В. Наркевич Влияние качества металла крестовин на их износостойкость в эксплуатации // Вестник ВНИИЖТ. – 1994. № 2. – с. 25-27.
46. М.С. Михелев, В.П. Балдина Влияние исходных свойств стали 110Г13Л на ее упрочнение наклепом. // Литейное производство №6, 1974. – с.33¬34.
47. С.В. Амелин, Э.И. Даниленко, Е.И. Пряхин Сталь повышенной прочности для железнодорожных крестовин // Вестник ВНИИЖТ. – 1979. №3.-с. 45-49.
48. Марганцовистая сталь. Перевод с англ. Б.А. Белоусова под ред. Д.т.н., проф. М.Е. Блантера М., Металлургиздат, 1959, 94 с.
49. Пряхин Е.И., Петрова Э.В., Макельский М.Ф. и др. Сталь для тяжелонагруженных литых изделий. Авт. Свид. №404892, 1973.
50. «Открытия, изобретения, промышленные образцы», 1973, № 44, С. 94.
51. Е.И. Пряхин, Б.Б. Гуляев, Э.И. Даниленко Сталь для литых железнодорожных крестовин // Литейное производство. – 1979. № 8. – с. 9-10.
51. Шульте Ю.А., Гладкий С.И. Литые образцы для контроля механических свойств стального литья И Литейное производство. – 1964. №4.-с. 5-8.
52. Кац Р.З., Михалев М.С. О содержании углерода в стали Г13Л И Литейное производство. – 1967. № 6. – с. 46.
53. Костинский Д.С. О соотношение содержания Мп и С в стали Г13Л // Литейное производство. – 1965. № 1.-е. 8-9.
54. Власов В.И., Комолова Е.Ф. Литая высокомарганцовистая сталь. М. Машгиз, 1963. 196с.
55. Корнаушенков Н.Г. Влияние легирующих элементов и термической обработки на механические свойства и износостойкость стали типа Г13Л/М.: 1970.277 с.
56. Новомейский Ю.Д., Глазков В.М. Высокомарганцовистая аустенитная сталь Г13Л. М.: Металлургия, 1969.100 с.
57. Михайлов С.П., Туманский Б.Ф., Шерстюк А.А. Влияние кремния и фосфора на свойства высокомарганцовистой стали // Технология и организация производства. 1988. №1. С. 39-40.
58. Михайлов С.П., Туманский Б.Ф., Шерстюк А.А. Совместное влияние кремния и фосфора на физико-механические свойства стали ПОГ 13Л// Литейное производство. 1988 №11. С.8-9.
59. Шерстюк А.А., Лунев В.В., Туманский Б.Ф. Эксплуатационная надежность высокомарганцовистой стали// Металловедение и термическая обработка металлов. 1972. № 10 С. 68-69.
60. Низкофосфористая высокомарганцевая сталь для железнодорожных крестовин/ Н.Я. Самарин, Р.З. Кац, В.А. Старцев и др.// Вестник ВНИИЖТ. 1981. № 1. С. 56-58.