Сейчас ваша корзина пуста!
Повышение ресурса буксовых подшипников грузовых вагонов
Цикл статей:
Глава 1 – Повышение ресурса буксовых подшипников грузовых вагонов
Глава 2 – Исследование влияния динамической нагруженности на ресурс буксового подшипника
Глава 3 – Модернизация буксы с целью повышения ресурса подшипников
Введение
Буксы грузовых вагонов являются одними из наиболее ответственных узлов подвижного состава, состояние которых влияет на безопасность движения. Согласно «Стратегическим направлениям научно-технического развития ОАО «Российские железные дороги на период до 2015 г.», утвержденным президентом ОАО «РЖД» 30.08.2007 г., предполагается увеличение нагрузки на ось до 25-27 тс и повышение скорости движения поездов до 120 км/ч [1]. Таким образом, требования к грузоподъемности и ресурсу опорных узлов подвижного состава непрерывно возрастают.
По данным Центральной дирекции по ремонту грузовых вагонов на сети железных дорог России за 9 месяцев 2007 г. количество случаев брака из-за неисправностей роликовых букс составило абсолютное большинство (95,2 %) в общем количестве выявленных случаев брака (рисунок 1) [2].
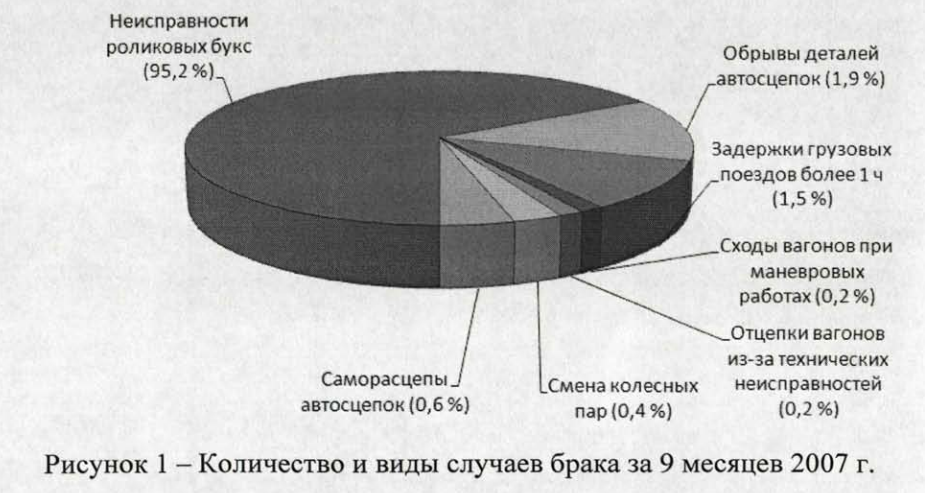
По сравнению с аналогичным периодом 2006 г. количество случаев брака из-за неисправностей роликовых букс увеличилось на 13 % (рисунок 2).
Основные неисправности роликовых букс, выявленные в 2006-2008 гг., приведены в таблице 1 [2].
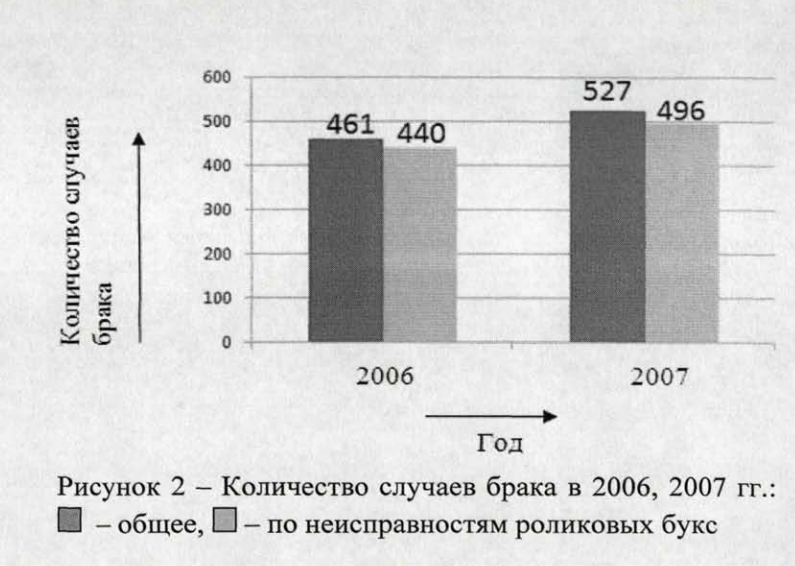
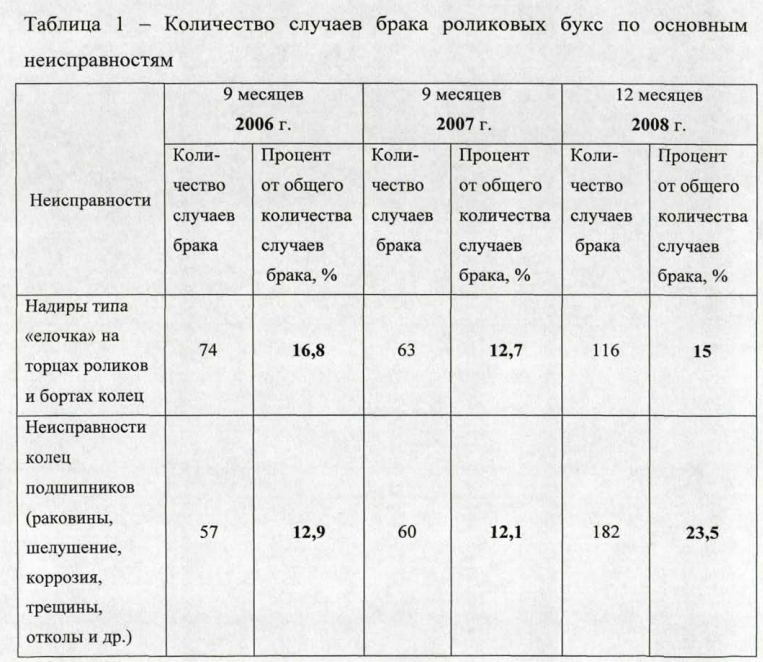
Характерным показателем неисправности буксы в пути следования является повышение температуры. В структуре показаний средств теплового контроля на сети российских железных дорог за 6 месяцев 2007 г. на нагрев букс грузовых вагонов пришлось 68 % от всех зарегистрированных случаев нагрева деталей подвижного состава (рисунок 3) [3].
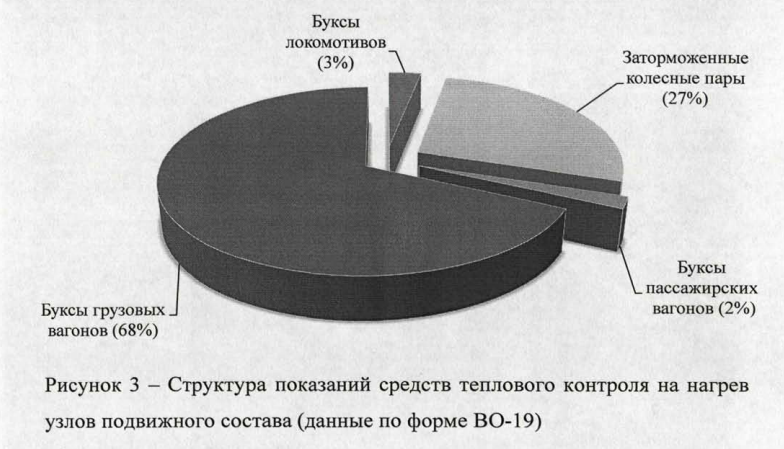
В 2007 г. по неисправностям букс отцеплено 13200 вагонов (в 2006 г. – 11700 вагонов), из них по нагреву букс 11500 вагонов или 87 %. За 6 месяцев 2008 г. из-за нагрева букс остановлено 22265 грузовых поездов, отцеплено 3818 грузовых вагонов, что на 8,1 % больше, чем за аналогичный период 2007 г, [4].
Большинство причин снижения ресурса роликовых букс и возникновения основных неисправностей связаны с конструктивными несовершенствами. Конструктивное устройство применяемой буксы обусловливает воздействие неблагоприятных сочетаний повышенных динамических нагрузок на подшипники качения, которые являются основными ресурсообразующими элементами буксы.
Актуальность работы обусловлена необходимостью выявления причин снижения ресурса буксовых подшипников и разработки предложений по их устранению.
Цель работы: повышение ресурса буксовых подшипников грузовых вагонов за счет снижения их динамической нагруженности путем модернизации конструкции буксы.
Для достижения указанной цели были поставлены и решены следующие задачи:
- провести анализ эксплуатации роликовых подшипников в буксах грузовых вагонов и существующей методики расчета ресурса подшипников;
- исследовать влияние динамической нагруженности элементов буксовых подшипников на их ресурс и уточнить методику расчета ресурса под воздействием рамной силы;
- предложить техническое решение, обеспечивающее повышение ресурса буксовых подшипников путем применения комбинированной опоры оси грузового вагона;
- разработать конструктивное устройство модернизированной буксы с раздельным восприятием радиальной нагрузки и рамной силы;
- разработать методику расчета ресурса комбинированной опоры оси грузового вагона, содержащей подшипниковый узел и шаровой подпятник;
- провести экспериментальное исследование модернизированной буксы грузового вагона с шаровым подпятником;
- выполнить технико-экономическое обоснование внедрения модернизированной буксы грузового вагона с шаровым подпятником.
Методы исследования. В работе использованы теоретические и экспериментальные методы исследования. Теоретическая часть работы представляет собой исследование наиболее неблагоприятных динамических воздействий на буксу грузового вагона, основанное на принципах аналитической механики. Прочностные расчеты предлагаемых конструктивных решений выполнены с применением основных положений теории упругости и сопротивления материалов, а также моделирования напряженно-деформированного состояния методом конечных элементов. Методика расчета ресурса комбинированной опоры разработана на основе теории трения и изнашивания. Экспериментальные исследования макетного образца модернизированной буксы в реальном масштабе проводились методом стендовых испытаний, обработка экспериментальных данных производилась с использованием основных положений математической статистики.
Научная новизна работы состоит в следующем.
Сформирована математическая модель динамической нагруженности буксового подшипника грузового вагона, учитывающая дополнительную радиальную нагрузку от перекоса тел качения.
Уточнена методика расчета ресурса цилиндрических роликовых подшипников буксы грузового вагона, позволяющая определить снижение ресурса под воздействием рамной силы.
На основе предложенного кинематического соединения разработана комбинированная опора оси грузового вагона, включающая шаровой подпятник и двухрядный цилиндрический’ роликовый подшипник с безбортовыми кольцами, обеспечивающая рациональное восприятие рамной силы и повышение ресурса подшипников.
Предложена методика расчета ресурса комбинированной опоры оси грузового вагона, состоящей из роликовых подшипников и шарового подпятника, позволяющая обеспечить работоспособность опоры при равном ресурсе составляющих элементов.
Достоверность научных положений и результатов диссертационной работы обоснована1 применением корректных математических моделей и подтверждена экспериментальными исследованиями, проведенными с применением сертифицированного оборудования и статистических методов проверки адекватности (Б-критерия Фишера).
Значение результатов диссертационной работы для теории и практики.
Уточненная методика расчета ресурса буксовых подшипников позволяет прогнозировать их ресурс в условиях роста скорости движения и нагрузок на ходовые части подвижного состава.
Применение комбинированной опоры, содержащей шаровой подпятник для восприятия рамной силы, способствует повышению безопасности движения и сокращению расходов на ремонт букс с заменой элементов.
Предложенная конструкция модернизированной буксы грузового вагона позволяет сохранить типовую конфигурацию корпуса буксы, шейки оси с центровым отверстием и торцевого крепления подшипников, что обеспечивает минимизацию затрат на модернизацию буксы и ее полную взаимозаменяемость с типовой конструкцией.
Расчет ресурса комбинированной опоры оси грузового вагона позволяет осуществить подбор оптимального начального зазора в нерабочем положении шарового подпятника с целью обеспечения работоспособности опоры при равном ресурсе составляющих элементов.
Реализация результатов работы. Изготовлен макетный образец буксы грузового вагона с шаровым подпятником, проведены его стендовые испытания. Результаты исследований легли в основу отчетов по научно- исследовательской работе кафедры (тема госбюджетной НИР ОмГУПСа ГБ 154 «Повышение несущей способности и ресурса конструкций механических устройств железнодорожного транспорта», номер государственной регистрации 01.95.0000749). Апробация результатов работы. Основные результаты исследований обсуждались на III международной конференции «Проблемы механики современных машин» (Улан-Удэ, 2006), всероссийской научной конференции студентов, аспирантов и молодых ученых «Наука. Технологии. Инновации.» (Новосибирск, 2006), IV международной научно- практической конференции «Транспорт Евразии XXI века» (Алма-Аты, 2006), международной научно-технической конференции «Актуальные проблемы трибологии» (Самара, 2007), V международной научно- практической конференции «Тгапэ-МесЬ-Ап-СЬет» (Москва, 2008), научно- практической конференции «Инновационные проекты и новые технологии на железнодорожном транспорте» (Омск, 2008).
Публикации. По теме диссертации опубликовано 17 научных работ, из них 3 статьи в изданиях перечня, рекомендованного ВАК Минобрнауки России, 5 патентов на полезную модель, 6 статей в материалах международных и всероссийских конференций, 3 статьи в сборниках научных трудов. Структура и объем диссертационной работы. Диссертация состоит из введения, пяти разделов, заключения, списка использованных источников из 110 наименований и 3 приложений. Общий объем диссертации составляет 141 е., объем основного текста 127 с. Текст работы содержит 43 рисунка, 14 таблиц и 3 приложения на 3 с.
Анализ эксплуатации подшипников качения в буксах грузовых вагонов
Конструкция букс грузовых вагонов
Буксы с подшипниками качения в отечественном вагоностроении
С каждым годом повышаются требования к грузоподъемности, надежности и ресурсу ответственных деталей и узлов подвижного состава, возрастают скорости движения и нагрузки на ходовые части. Для создания эффективных опор качения колёсных пар современных вагонов необходимо решение комплекса сложных технических вопросов.
В работах Н. А. Аверина, А. А. Амелиной, В. В. Лукина, Б. А. Генича,
- Ф. Девяткова, Е. П. Коннова, В. И. Кучугова, А. В. Лосева, И. Г. Морчиладзе, О. А. Русанова, И. М. Семенова, А. М. Соколова, К. Ф. Экгольма рассмотрены вопросы конструкции, эксплуатации и ремонта вагонных букс.
Исследованию динамики вагона и в частности ходовых частей посвятили свои труды П. С. Анисимов, Ю. П. Бороненко, М. Ф. Вериго,
- В. Вершинский, М. В. Винокуров, И. И. Галиев, В. Н. Данилов, О. П. Ершков, Н. А. Ковалев, К. П. Королев, М. Л. Коротенко, В. Н. Котуранов, Н. Н. Кудрявцев,В. А. Лазарян, В. А. Нехаев В. А. Николаев, Л. Н. Никольский, М. П. Пахомов, Г. И. Петров, П. Г. Проскурнев, В. Н. Филиппов, В. Д. Хусидов, И. И. Челноков и другие ведущие специалисты научно-исследовательских учреждений и железнодорожных вузов.
Вопросам исследования, расчета и конструирования опор качения машин и механизмов посвящены труды Р. Аллана, Р. Д. Бейзельмана, О. М. Беломытцева, А. В. Бородина, И. М. Карпухина, Р. В. Коросташевского, М. 3. Народецкого, В. Н. Нарышкина, В. Б. Носова,
A. А. Попова, С. В. Пинегина, Н. А. Спицына, И. А. Спришевского,
B. Н. Трейера, Н. Н. Федотова, А. А. Филатова, Т. Харриса, Б. В. Цыпкина, Л. В. Черневского.
Работу подшипников качения в буксах вагонов исследовали В. В. Абашкин, Н. Н. Волков, С. Г. Иванов, С. Н. Лозинский, В. Е. Пини,
A. М. Поляков, В. Л. Образцов, М. В. Орлов, В. А. Петров, Н. В. Родзевич,
B. Н. Цюренко, В. Г. Чурсин, В. С. Шаронин, А. Л. Ямпольский.
Наиболее распространенные дефекты буксовых подшипников являются следствием неблагоприятного воздействия рамной силы, которая передается от колесной пары через подшипники и приливы корпуса буксы ограничителям буксового проема боковой рамы. Поэтому конструктивное построение букс целесообразно рассматривать с точки зрения способов ее восприятия (рисунок. 1.1); аналогичный подход был применен группой специалистов под руководством Г. И. Давыдова (ОмИИТ) при исследовании ослабления торцевого крепления букс в 1975 г.
Массовое и систематическое испытание роликовых подшипников на магистральных железных дорогах началось в 1952 г. В 1955 г. отечественная промышленность приступила к выпуску всех цельнометаллических пассажирских вагонов, а с 1956 г. — части грузовых вагонов с роликовыми подшипниками [7].
С этого периода и по настоящее время на отечественных железных дорогах наиболее широкое распространение получил способ передачи рамной силы телами качения без демпфирующих устройств (за исключением отдельных опытных конструкций). Так, вагоны транссибирского направления оборудовались подшипниками со сферическими и цилиндрическими роликами. Характеристика подшипников вагонных букс приведена в Таблице 1.
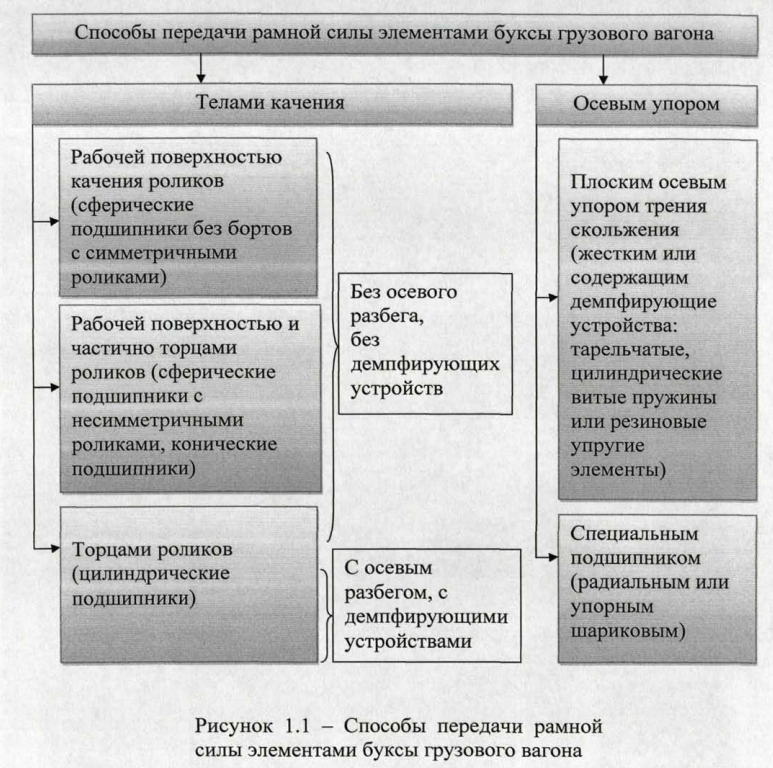
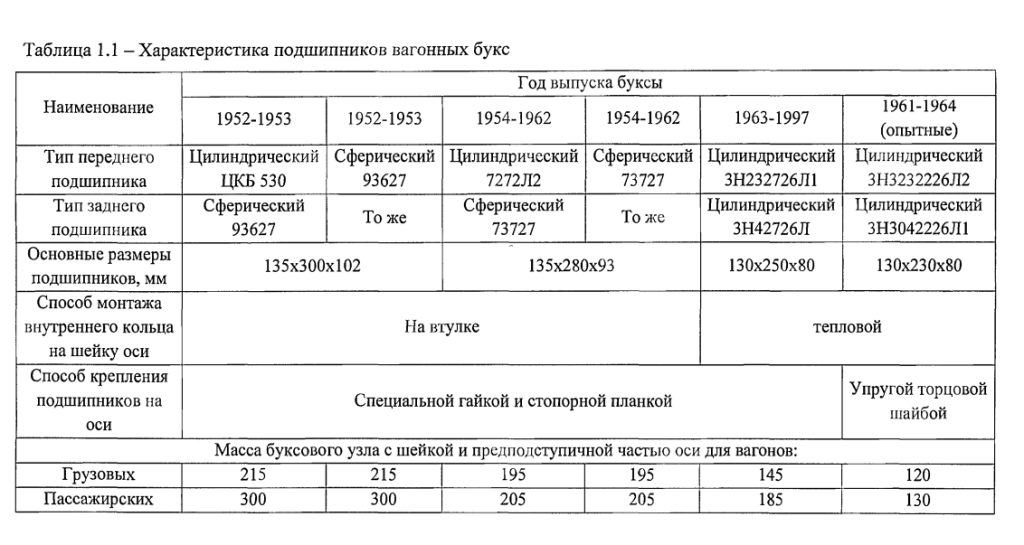
Вагоны широкой колеи были оборудованы буксами, выпущенными в 1952, 1954 и 1963 гг. В буксе, выпущенной в 1952 г., было установлено два подшипника: цилиндрический ЦКБ530 и сферический 93627 или два сферических 93627 (подшипники смонтированы на втулке, наружный диаметр подшипников 300 мм). В буксах, выпущенных в 1954 г., по сравнению с предыдущей конструкцией подшипники имели меньшие размеры, уменьшены также размеры корпуса. В таких буксах применены цилиндрические подшипники 72727 и сферические подшипники 73727; наружный диаметр подшипников 280 мм. Некоторое количество грузовых вагонов было оборудовано в 1954-1955 гг. следующими опытными, буксами:
- с одним цилиндрическим и одним сферическим подшипником диаметром 300 мм , посадка подшипников на втулке (рисунок 1,2, а);
- с одним сферическим подшипником ЦКБ553 диаметром 320 мм, посадка подшипников на втулке (рисунок 1.2, б);
- с двумя цилиндрическими подшипниками ЦКБ561 и ЦКБ562 диаметром 280 мм, подшипники смонтированы на шейке оси тепловым способом;
- с двумя сферическими подшипниками ЦКБ554 диаметром 300 мм, насаженными при помощи втулки на шейку оси диаметром 145 мм;
- с одним сферическим подшипником 73727 на втулке и одним цилиндрическим подшипником ЦКБ559 (передний) без втулки, наружный диаметр подшипников составляет 280 мм;
- с двумя сферическими подшипниками ЦКБ 1520 отечественного производства на втулочной посадке;
- с двумя подшипниками диаметром 250 мм и шириной 88 мм для грузовых вагонов (рисунок 1.3, а): передний подшипник цилиндрический с массивным беззаклепочным сепаратором, задний — сферический, подшипники смонтированы на втулках [8].
В 1958—1959 гг. были созданы новые опытные буксы: с двумя цилиндрическими подшипниками 42726Л (ЦКБ 1521) и 232726ЛЦЦКБ 1522) отечественного производства (рисунок 1.3, б).
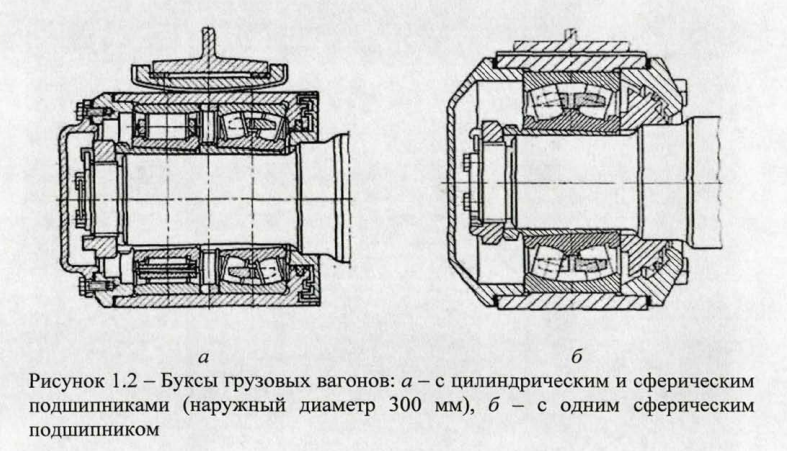
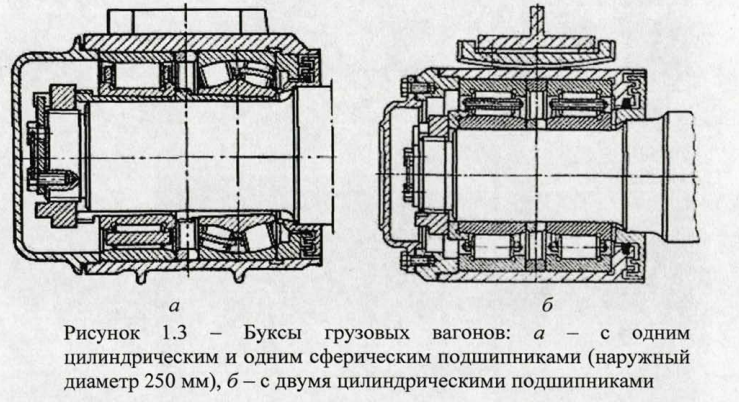
К 1970 г. буксами с роликовыми подшипниками были оснащены 25 % грузовых вагонов. В этот период производилась замена клёпаных сепараторов беззаклёпочными. Беззаклёпочные сепараторы обеспечивали более надежную работу роликовых подшипников в сложных силовых условиях, особенно при низкой температуре, напряжения в их перемычках в пять раз меньше, чем в перемычках клепаных сепараторов.
Для цилиндрических роликовых подшипников, у которых внутреннее кольцо может устанавливаться на шейку оси и сниматься с неё отдельно от других деталей подшипника – наружного кольца, роликов и сепаратора, –
втулочная посадка не является технологически оправданной. Широкое распространение при монтаже таких подшипников получила горячая посадка.
Для обобщения опыта эксплуатации вагонов на роликовых подшипниках в 1967 г. была создана межведомственная комиссия из специалистов МПС и промышленности. Было проанализировано около 30 тысяч роликовых колёсных пар, прошедших деповской и заводской ремонты.
Фактический ресурс сферических подшипников оказался ниже расчётного практически в восемь раз. На основании результатов эксплуатационных и стендовых испытаний наиболее работоспособной была признана конструкция буксы для грузовых вагонов серийного производства (рисунок 1.4) [9].
В этой конструкции задний подшипник 2 (ЗН42726Л, ЦКБ1521) имеет однобортное внутреннее кольцо, у переднего подшипника 1 (ЗН2Э2726Л1, ЦКБ 1522) роль борта выполняет плоское приставное упорное кольцо [10, 11, 12, 13, 14].
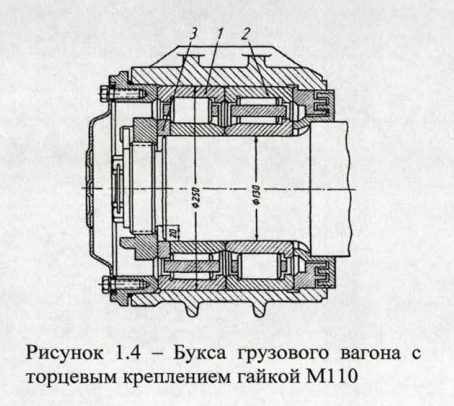
В 1997 году сепараторы из латуни марки ЛЦ40С были заменены на сепараторы из стекло наполненных полиамидов марок Армамид ПА СВ 3017 1ЭТМ, Технамид Б-СВЗО. Указанные марки полиамидов являются композициями, содержащими наряду с полимерной основой на базе Полиамида 6, армированного стекловолокном, различные наполнители и модифицирующие добавки функционального действия. По габаритным размерам такие сепараторы полностью взаимозаменяемы с латунными. Единственным отличием является размещение в подшипнике 15 роликов вместо 14 при латунном сепараторе. В буксах грузовых вагонов стали серийно применяться подшипники 30-4276Е2 и 30-232726Е2 [15].
Резьбовая часть шейки оси подвержена частым механическим повреждениям, а ее восстановление представляет собой трудоемкий длительный процесс. При этом качество восстановленной резьбы получается заведомо худшим, чем первоначальной. Исходя из этого, более рациональным было признано торцевое крепление букс тарельчатой шайбой 1 (рисунок 1.5) и началось массовое внедрение этого вида крепления букс на шейках осей РУ1Ш [16, 17].
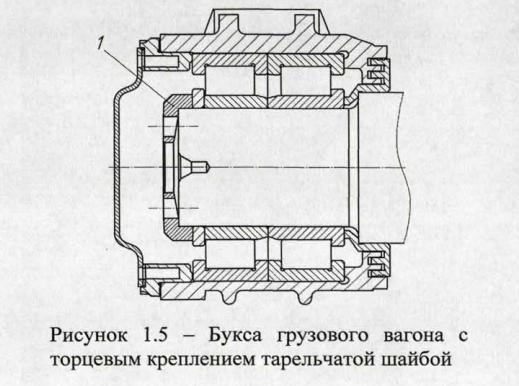
Наряду с эксплуатацией типовой буксы в разные годы проводилась разработка опытных конструкций букс, направленных на улучшение восприятия рамной силы [18].
Одной из первых опытных конструкций была букса для скоростного поезда «Аврора», в которой предпринята попытка разделения функций подшипников: шариковый 2 (рисунок 1.6) предназначался для восприятия рамной силы, а два цилиндрических роликовых 1 – для восприятия радиальной нагрузки. Недостатком этой буксы является восприятие радиальной нагрузки шариковым подшипником.
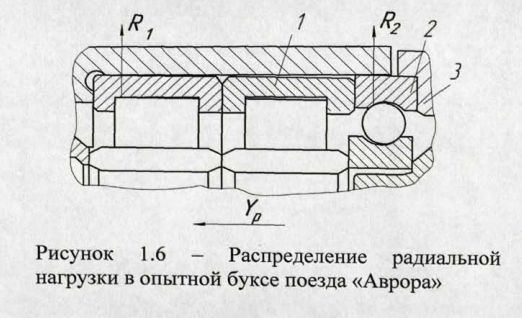
Наружное кольцо шарикового подшипника 2 зажимается крепительной крышкой 3 вместе с наружными кольцами цилиндрических подшипников. При изменении направления рамной силы Ур шарики перекатываются по
желобу внутреннего кольца, приподнимая край корпуса буксы. Возникает перегружение радиальными нагрузками и Я2 заднего цилиндрического и шарикового подшипников, а передний цилиндрический подшипник 1 оказывается полностью разгруженным. Другим недостатком этой буксы является раздельное фиксирование наружного и внутреннего колец шарикового подшипника, которое вызывает их относительный угловой перекос в вертикальной плоскости.
В еще одной опытной буксе между двумя укороченными цилиндрическими роликовыми подшипниками установлен шариковый радиальный подшипник с сепаратором, центрируемым по наружному кольцу. Для обеспечения возможности монтажа и демонтажа это кольцо выполнено
разъемным. Однако существенное укорочение длины роликов привело к снижению грузоподъемности подшипников и снижению их ресурса в 20 раз. Еще один выявленный недостаток заключается в отсутствии возможности постоянного соосного расположения двух наружных полуколец шарикового подшипника, зажимаемых наружными кольцами роликовых подшипников, а также в относительном угловом перекосе наружного и внутреннего колец шарикового подшипника в вертикальной плоскости. Фиксирование разъемного наружного кольца шарикового подшипника вместе с наружными кольцами роликовых подшипников монтажными усилиями зажатия в условиях действия рамной силы приводит к двустороннему восприятию шариковым подшипником радиальной нагрузки и к ее неблагоприятному перераспределению между задним и передним роликовыми подшипниками.
В связи с неудовлетворительными результатами поездных испытаний обе рассмотренные опытные буксы были сняты с эксплуатации.
В 1998 г. в нашей стране на подшипниковом заводе ВПЗ-15 (г. Волжский) были спроектированы и изготовлены кассетные конические подшипники для нагрузки на ось 250 кН в габаритах 150x250x175 мм [19].
В настоящее время в эксплуатацию запущена опытная партия грузовых вагонов, оснащенных буксами кассетного типа с двухрядными коническими подшипниками. Букса кассетного типа отечественного производства показана на рисунке 1.7.
При подкатке под грузовую тележку модели 18-100 колесной пары с напрессованными в холодном состоянии на ее шейки буксовыми узлами кассетного типа необходима специальная деталь — адаптер. Адаптер предназначен для передачи нагрузки на кассетный узел, а также ограничения перемещений колесной пары вдоль и поперек вагона. В качестве материала адаптера использован алюминиевый сплав АМгб.
Наружная поверхность адаптера (рисунок 1.8) в верхней части выполнена из прессованных труб ТФ-2, ТФ-5 и из штампованной заготовки.
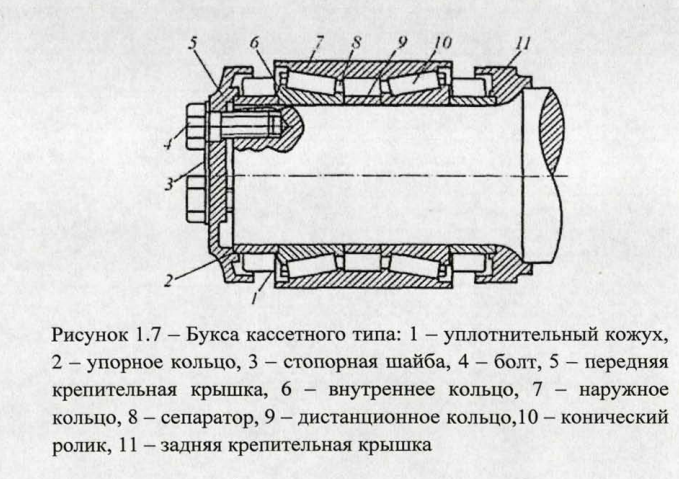
Потолок между опорными выступами в поперечном сечении имеет переменную толщину, уменьшающуюся от центральной вертикальной плоскости к опорным выступам. Масса адаптера составляет 12,7 кг. Одновременно был разработан адаптер из стальной литой заготовки, масса которого равна 32 кг.

Конические подшипники сложны и дороги в изготовлении, при их производстве необходимо соблюдение высокой точности. В противном случае разноразмерность конусности тел качения может привести к заклиниванию подшипника.
Резкому снижению работоспособности конических подшипников способствует также возникновение перекосов при изгибе оси под воздействием динамических нагрузок. Динамические качества тележки 18-100, в частности, наличие значительных осевых зазоров в буксовых проемах, также создают крайне тяжелые условия для работы конических подшипников и герметизирующих устройств.
В конструкцию зарубежных аналогов кассетных букс включена тройная герметизация подшипниковой полости, которая позволяет применять жидкий смазочный материал. Уплотнения отечественных кассетных букс не обладают достаточными барьерными свойствами, а применяемый по этой причине пластичный смазочный материал не является оптимальным для эффективной работы конических подшипников.
Первые пробеговые испытания конических кассетных подшипников были проведены на экспериментальном путевом кольце ВНИИЖТа на основании указания МПС № Н-569у от 09.06.2003 г. Затем испытания были перенесены на Северную железную дорогу. В процессе проведения испытаний в зимних условиях на участке ст. Череповец — ст. Воркута внутрь подшипников производства ВПЗ-15 проникла вода, что привело к нагреву букс и даже к разрушению подшипников и излому шейки оси (а это — возможное крушение). Помимо наличия, а иногда и скопления воды в буксах, был обнаружен выброс смазки на колесную пару через лабиринт. Приборы КТСМ-01Д зафиксировали, что средний уровень нагрева букс с коническими подшипниками в 1,6 — 2 раза выше, чем в серийных цилиндрических подшипниках.
Основные дефекты кассетных подшипников на основании комиссионных осмотров аналогичны распространенным дефектам цилиндрических подшипников [19, 20].
В настоящее время большая часть грузовых вагонов российских железных дорог по-прежнему оснащена буксами с двумя цилиндрическими роликовыми подшипниками (рисунок 1.6).
Буксы грузовых вагонов зарубежного производства
В мировых масштабах не существует строго обоснованного единого метода выбора подшипников качения для букс вагонов. В ходе эволюции конструкций вагонных букс выбор подшипников часто зависел от того, какие подшипники в преобладающем количестве производились в конкретной стране. Помимо размещения в буксе различных конфигураций и сочетаний роликовых подшипников, воспринимающих радиальную нагрузку, известны конструкции, дополненные шариковыми подшипниками или другими видами осевых упоров (рисунок 1), предназначенными для передачи рамной силы.
Так, в Японии буксы высокоскоростных экспрессов «Токайдо» содержат один двухрядный цилиндрический и один радиальный шариковый подшипники (рисунок 1.9, а). От опытной буксы скоростного поезда «Аврора» она отличается свободной установкой наружного кольца шарикового подшипника, что обеспечивает его одностороннюю нагруженность. Между наружным кольцом и крышкой буксы, в которой он находится, предусмотрен зазор 0,5 мм. Для смягчения ударов, направленных вдоль оси буксы, имеется упругое демпфирующее устройство, состоящее из двух тарельчатых пружин. Пружины устанавливают в буксу сжатыми на 5 мм; в эксплуатации пружины дополнительно деформируются еще на 3,5 — 5 мм.
В Австрии были разработаны буксы с амортизатором рамной силы (рисунок 1.9, б), которая передается от переднего подшипника через упорное кольцо 1, кольцо 2 и резинометаллическую коническую подушку 3 на кольцо 4, укрепленное на оси со стороны торца тремя болтами [8].
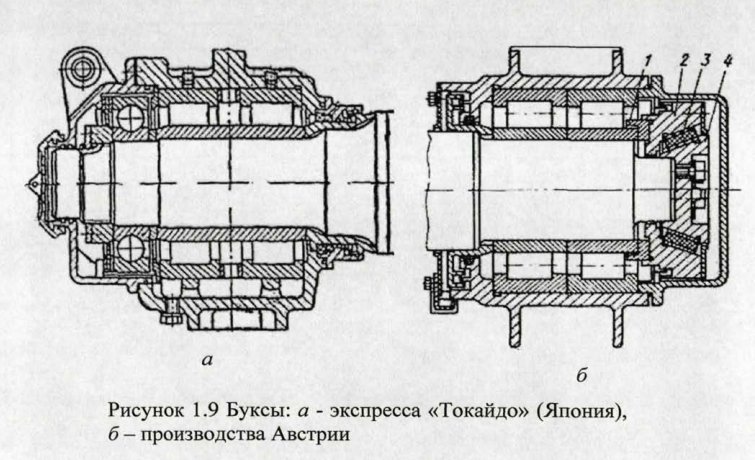
Одним из мировых лидеров подшипниковой промышленности, выпускающим подшипники для железнодорожного транспорта, является международный концерн 8К1\ Первоначально 8КР производил для вагонных букс двухрядные сферические подшипники с удлиненными роликами, имеющими форму симметричной бочки, с плавающим средним бортом и штампованными полусепараторами (рисунок 1.10), торцевое крепление осуществлялось шайбой и тремя болтами. Однако такие подшипники имели подшипников повышенный коэффициент трения, и концерн ЗКИ приступил к производству для букс вагонов не только сферических, но и цилиндрических, а впоследствии – конических двухрядных кассетных подшипников (рисунок 1.11).
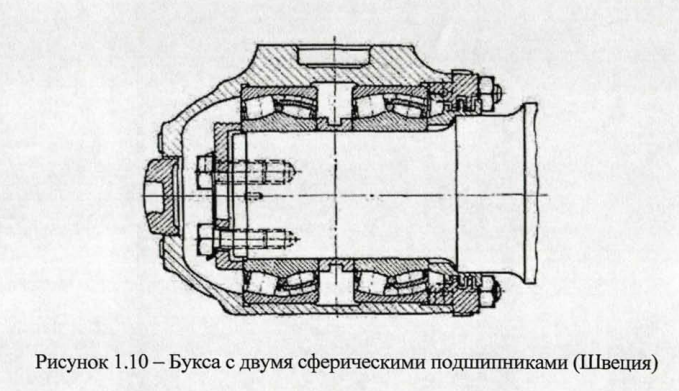
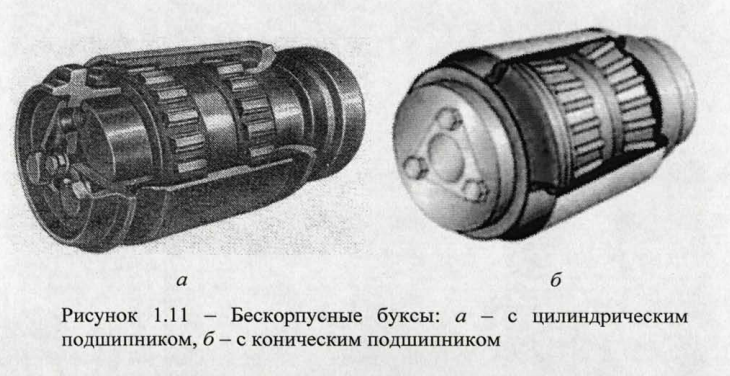
Такие подшипники получили с конца 1950-х гг. широкое распространение в странах с развитой железнодорожной сетью, таких как США, Канада, ЮАР, Австралия [19].
В США на колесных парах грузовых вагонов эксплуатируются бескорпусные узлы с коническими (фирмы Timken) или цилиндрическими (фирмы SKF и Bower) подшипниками.
В настоящее время на крупнейшие железнодорожные сети мира поставляются готовые к монтажу буксы от SKJF под маркой TBU, в частности, компактные Compact TBU (или сокращенно – CTBU). Между внутренним и наружным кольцами на заплечике внутреннего кольца в буксу встраивается уплотнение с малым трением. Оно представляет собой сочетание лабиринтного уплотнения, контактирующей губки и маслоразбрызгивающей шайбы. Во избежание фрикционной коррозии в зоне
перехода от лабиринтного кольца к внутреннему контактная пара «сталь — сталь» заменена парой «сталь — полимер». Сепаратор из армированного полиамида дополнительно оптимизирован вследствие малого монтажного объема. В пакете с буксовым коническим роликовым подшипником Compact TBU отделение SKF Railway группы компаний SKF предлагает интегральную мехатронную систему. В буксовом узле смонтированы встроенные датчики для регистрации следующих параметров: температуры подшипника, частоты и направления вращения, вертикальных и боковых ускорений, а также пройденного расстояния, определяющего местонахождение подвижного состава. Эти датчики используются для управления торможением и тягой, регистрации скорости и контроля температуры подшипников. Буксы Compact TBU с коническими роликовыми подшипниками были разработаны для тележек типа Y25 с нагрузкой на ось 250 кН. [21].
Конструктивные причины неисправностей букс с цилиндрическими и коническими подшипниками
Типовая конструкция буксы с цилиндрическими подшипниками была принята на основании обобщения опыта эксплуатации различных вариантов букс с подшипниками качения, пришедшими на смену подшипникам скольжения [9]. В современных условиях роста скоростей движения поездов и нагрузок на ходовые части в сочетании с необходимостью обеспечения безопасности движения актуальной становится задача усовершенствования конструкции буксы с целью устранения или снижения воздействия неблагоприятных факторов, сокращающих ресурс подшипников и узла в целом. Эффективность работы буксы и ресурс ее основных элементов зависит как от характера действующих нагрузок, так и от конструктивного устройства узла. Описание взаимного расположения и возможных относительных перемещений основных элементов типовой буксы схематично представлено на рисунке 1.12.
Рассмотрим конструктивные особенности типовой буксы, которые ухудшают условия работы подшипников и являются причинами возникновения наиболее распространенных дефектов.
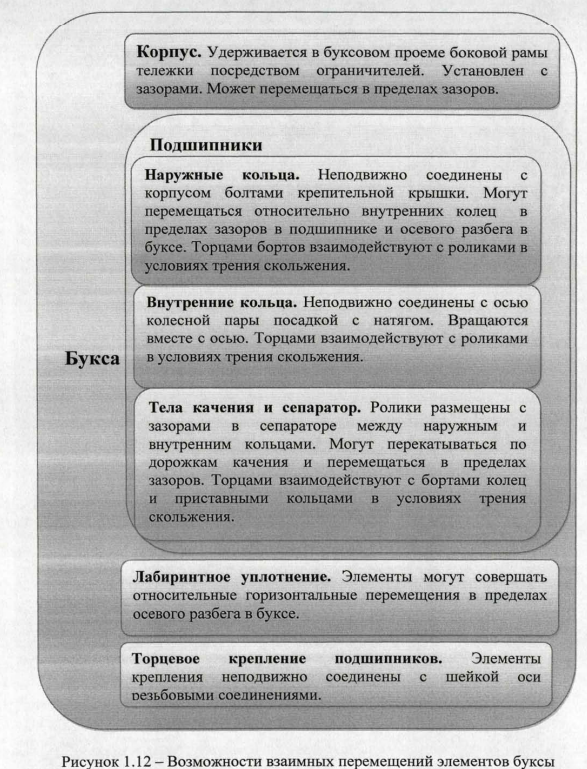
Роликовые подшипники
Неэффективное восприятие рамной силы. Основной причиной возникновения надиров на торцах роликов и бортах колец, трещин и отколов бортов буксовых подшипников является их неэффективная работа под воздействием комбинированной нагрузки (радиальной нагрузки и рамной силы). Передача рамной силы происходит при контакте небольшой площади торцов роликов с бортами колец в условиях трения скольжения.
На рисунке 1.13 представлены схемы передачи рамной силы Ур передним (а) и задним (б) цилиндрическими буксовыми подшипниками.
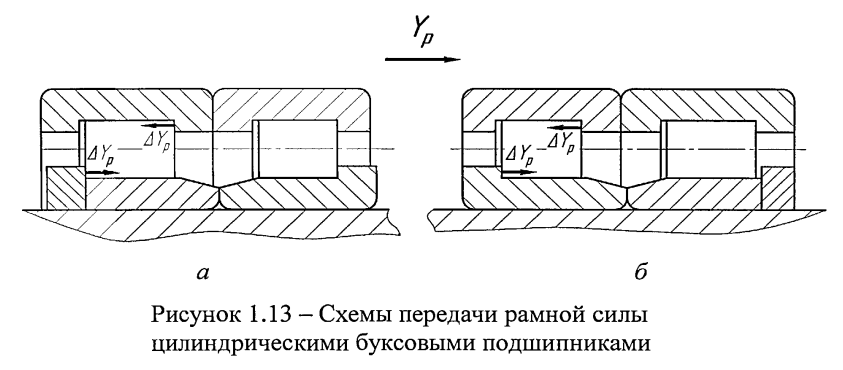
При скольжении торцов роликов относительно бортов колец происходит торможение роликов и нарушение параллельности осей роликов и колец. Частицы металла, образующиеся при трении скольжения, попадают в смазочный материал и на дорожки качения колец, что приводит к увеличению их абразивного износа [22].
В зоне трущихся поверхностей в условиях недостаточной смазки возникает значительный нагрев, который фиксируется диагностическими приборами и приводит к необходимости отцепки колесной пары [18].
Согласно существующей электронной теории трения [23] при нарушении диэлектрического слоя масляной пленки на трущихся поверхностях как диэлектриков, так и проводников образуются потенциалы противоположной полярности и последующие периодические электроискровые пробои, вызывающие микроэлектросварку, а далее разрушение кристаллической решетки материала. Происходящие физико-химические процессы сопровождаются интенсивным выделением тепла.
При изготовлении подшипниковых колец в зоне галтелей между бортами и дорожками качения образуются остаточные напряжения. Под воздействием значительной горизонтальной поперечной нагрузки в этих местах происходит ускоренное развитие трещины, которая может впоследствии привести к отколу борта.
По данным комиссионных осмотров, аналогичные неисправности, связанные с неэффективным восприятием рамной силы, зафиксированы и в конических кассетных подшипниках при выборе осевого зазора и нарушении условий смазывания [19]. Тепловые потоки, образуемые работой сил трения на поверхностях подшипника, условно делятся на две категории: от сил трения качения и сил трения скольжения. Зоны образования тепловых потоков в цилиндрических и конических буксовых подшипниках представлены на рисунке (1.14) [24].
Тепловые потоки на поверхностях скольжения роликов по кольцам цилиндрических подшипников возникают только от воздействия рамной силы (рисунок 1.14, а). В конических подшипниках тепловые потоки скольжения возникают как от рамной силы, так и от радиальной нагрузки (рисунок 1.14, б). Этим объясняется их повышенный нагрев и опасность заклинивания при работе под комбинированной нагрузкой в буксах грузовых вагонов.
Опрокидывающий момент. Цилиндрические подшипники чувствительны к перекосам. В применяемой буксе часть горизонтальной поперечной силы, передаваемой через ролик, создает на определенном плече момент, который изменяет давление по длине образующей, перегружая одну половину дорожки качения кольца и разгружая другую. Порождаемое перекосом резкое возрастание давления приводит к разрушению; масляной пленки и соприкосновению металлических поверхностей: При этом действие торца ролика на’ кольцо подшипника” аналогично действию резца, что значительно повышает вероятность возникновения различных дефектов кольца [25]. Более: подробно образование опрокидывающего момента в цилиндрическом подшипнике рассмотрено в п. 2.2.
Конические подшипники обладают еще большей чувствительностью к перекосам и технологическим допускам, установленная допустимая величина перекоса составляет 7 мкм. Следовательно, требования к их изготовлению и условиям эксплуатации являются более жесткими.
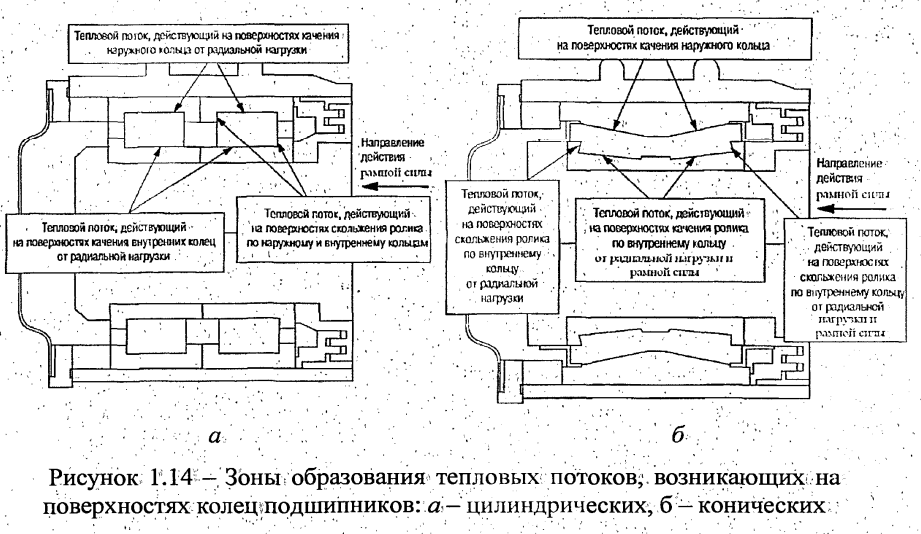
Неравномерное распределение нагрузки между подшипниками. 6 случае применения; двух однорядных роликовых подшипников разноразмерность, погрешность формы и износ посадочных поверхностей наружных и внутренних колец и опорных поверхностей буксовых проемов боковой рамы и корпуса буксы вызывают неравномерную нагрузку на подшипники и возможную перегрузку одного из них.
Лабиринтное уплотнение
При движении поезда в буксе в пределах осевого разбега происходит знакопеременное горизонтальное перемещение одной группы конструктивных элементов буксы относительно другой. При этом возникает поршневой эффект, который приводит к всасыванию из окружающей среды влаги и абразивных частиц в рабочую полость буксовых роликоподшипников. Эта проблема особенно ощутима в весеннее-осенний период. Распределение случаев брака по неисправностям букс по месяцам (рисунок 1.15) показывает, что наибольшее число отцепок было произведено в марте и апреле.
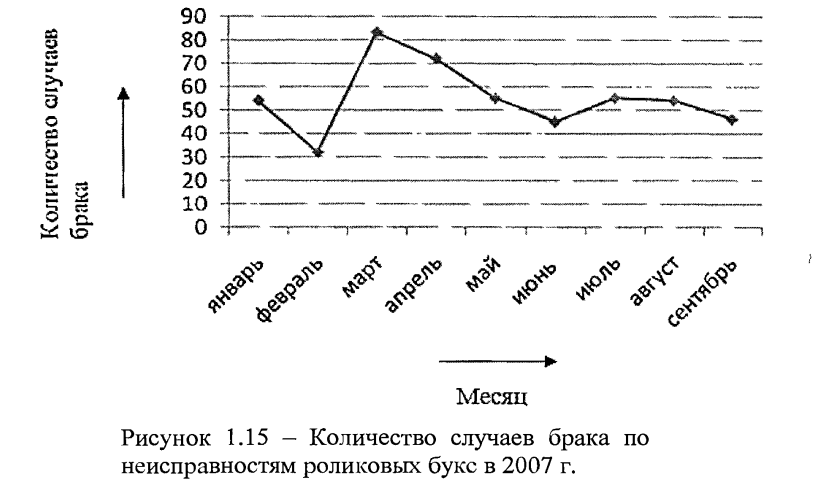
В этот период в условиях высвобождения значительных объемов талых вод вследствие недостаточных барьерных свойств лабиринтного уплотнения происходит интенсивное обводнение и загрязнение смазочного материала. Кроме того, при неравномерном оттаивании верхнего строения пути возникают неровности, приводящие к повышению динамических нагрузок на необрессоренные части подвижного состава. Последствия неэффективной герметизации были выявлены и при испытаниях букс с коническими подшипниками. При повышенной температуре, характерной для конической буксы (см. п. 1.1.1), свойства смазки меняются, она приобретает повышенную текучесть. В результате под действием центробежных сил и разности давлений внутри буксы и в окружающей среде происходит выброс смазки на колесную пару. После этого давление внутри буксы становится ниже атмосферного, и в нее попадают влага и мелкие частицы с рельсовой колеи [19].
Торцевое крепление
Сжатие бортов наружных колец под действием монтажных усилий.
Под действием монтажной силы сжатия кольца- цилиндрических и конических подшипников испытывают волнообразную деформацию, имеющую наибольшие значения в, зоне болтовых соединений. Вследствие этого происходит уменьшение величины осевого зазора между торцом ролика и плоскостью направляющего борта кольца. Температурный перепад между нагревом ролика и наружного кольца может выбрать оставшуюся часть этого зазора и заклинить подшипник.
Непараллельность рабочих поверхностей направляющих бортов* наружных колец, обусловленная, их неравномерным сжатием, сказывается на характере их контакта с роликами. Эффективность передачи рамной силы снижается вследствие включения в работу только части роликов.
Изгиб дорожек качения под действием монтажных усилий. При контактировании крепительной крышки и опорной поверхности корпуса буксы с торцовыми поверхностями переднего и заднего цилиндрических подшипников прикладываемая сила Р3 действует на определенном плече к по отношению к центру изгиба ЦИ (рисунок 1.16). Под воздействием силы зажатия Р3 наружные кольца подшипников подвергаются воздействию изгибающих моментов, которые стремятся исказить форму образующей дорожки качения в сторону вогнутости.
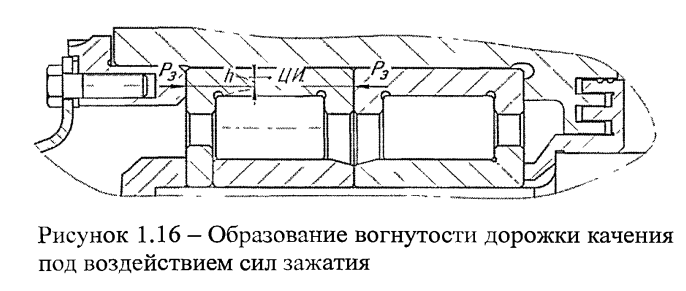
Подобная ситуация возникает и при различных вариантах контакта торцовых поверхностей колец переднего и заднего цилиндрических подшипников (рисунок 1.17).
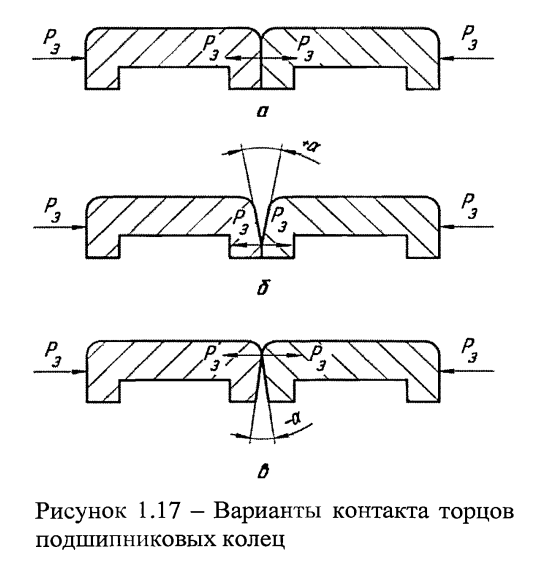
Случай а является наиболее благоприятным, однако даже при идеальной геометрии соприкасающихся бортов на величину изгибающего момента могут повлиять отклонения от перпендикулярности торцовых
поверхностей противоположных бортов и деталей, сопряженных с ними. Из случаев бив наиболее неблагоприятным является случай б вследствие меньшей жесткости торцовых поверхностей бортов под воздействием приложенных сил. Известно, насколько важно соблюдение правильной формы образующей роликов и дорожек качения наружного и внутреннего колец. Уменьшение концентрации контактных напряжений на краях роликов и дорожек качения колец может быть достигнуто скосами на роликах и выпуклостью большого радиуса на дорожках качения колец или на образующей роликов. При сжатии колец вогнутость дорожки качения негативно сказывается на ресурсе наружного кольца.
Температурные деформации
Установлено, что в эксплуатации при движении вагона возникает перепад температур между наружным кольцом подшипника и корпусом буксы. В буксе зажатые наружные кольца, нагретые сильнее корпуса, не имеют возможности для расширения. Искажение образующей наружных колец в сторону вогнутости при температурных деформациях является одной из причин выхода из строя наружных колец подшипников по усталостным раковинам [26]. При температурном удлинении конических роликов возможна полная ликвидация осевого зазора, что приводит к их заклиниванию.
Следует заметить, что явления, перечисленные в п.п. 1.1.3.3 и 1.1.3.4 практически неизбежны ввиду особенностей конструкции, технологии изготовления и монтажа элементов буксы, а также тяжелых условий ее работы. Однако к наиболее негативным последствиям указанные явления приводят в сочетании с воздействием рамной силы на буксовые подшипники.
Нагрузки, действующие на элементы типовой буксы грузового вагона
Буксы грузовых вагонов в эксплуатации воспринимают статические и
динамические нагрузки, передающиеся от кузова и рамы тележки, а также со стороны колесной пары при взаимодействии пути и подвижного состава. Воздействие различных сочетаний этих нагрузок способствует появлению необратимых процессов, приводящих к прогрессивному износу деталей подшипников качения в буксе и снижению их ресурса.
В тележке модели 18-100 боковые рамы жестко, через опорное соединение устанавливаются на буксовые узлы. Это соединение не только передает вертикальные, горизонтальные и продольные нагрузки, но и в пределах зазоров обеспечивает ограниченную возможность самоустановки колесных пар с жестким ограничением их перемещений, участвует в гашении горизонтальных колебаний необрессоренных масс тележки за счет сил трения в опоре. На рисунке 1.18, а показано взаимодействие боковой рамы с буксой в вертикальной плоскости.

Боковая рама 1 через прямоугольную опорную поверхность 2 опирается на опорные приливы буксы 3, которая снабжена жесткими ограничителями 4. Через такое опорное соединение передаются вертикальная радиальная нагрузка F,. и горизонтальные нагрузки FT или Fтг
Силовое воздействие от тормозной системы FT тележки (при одностороннем нажатии колодок на колеса в грузовых вагонах) старается сдвинуть буксу (рисунок 1.18, а, влево), прижимая её к упору боковой рамы.
Другое воздействие Frr реализуется при торможении вагонов на горке, при входе в кривые участки пути и стрелочные переводы. Под воздействием силы Frr букса также прижимается боковой раме (рис. 1.18, а, вправо).
Разные диаметры колес в тележке, непараллельность опорных поверхностей боковой рамы (угол а на рисунке 1.18, ¿г) и другие причины часто приводят к тому, что буксовый узел занимает одно из крайних положений. При этом резко усложняются условия самоустановки колесных пар, неравномерно изнашиваются отдельные поверхности букс и боковых рам.
На рисунке 1.18, б показано взаимодействие частей опорного соединения в поперечной вертикальной плоскости. Из-за непараллельности опорных поверхностей боковой рамы 1 или ее маятниковых колебаний (угол Ф на рисунке 1.18, б) возможно краевое опирание на приливы буксы 3. При этом один из подшипников буксы перегружается, и начинается интенсивный неравномерный износ опорных поверхностей. Неравномерный износ ухудшает самоустановку колесных пар, что приводит к росту силовых взаимодействий.
На рисунке 1.18, в представлена схема взаимодействия элементов опорного соединения в горизонтальной плоскости. Боковая рама 1 устанавливается на буксу 3 с зазорами в поперечном направлении dp, в продольном направлении dn. Наличие значительных зазоров обусловливает воздействие ударных нагрузок на элементы буксы.

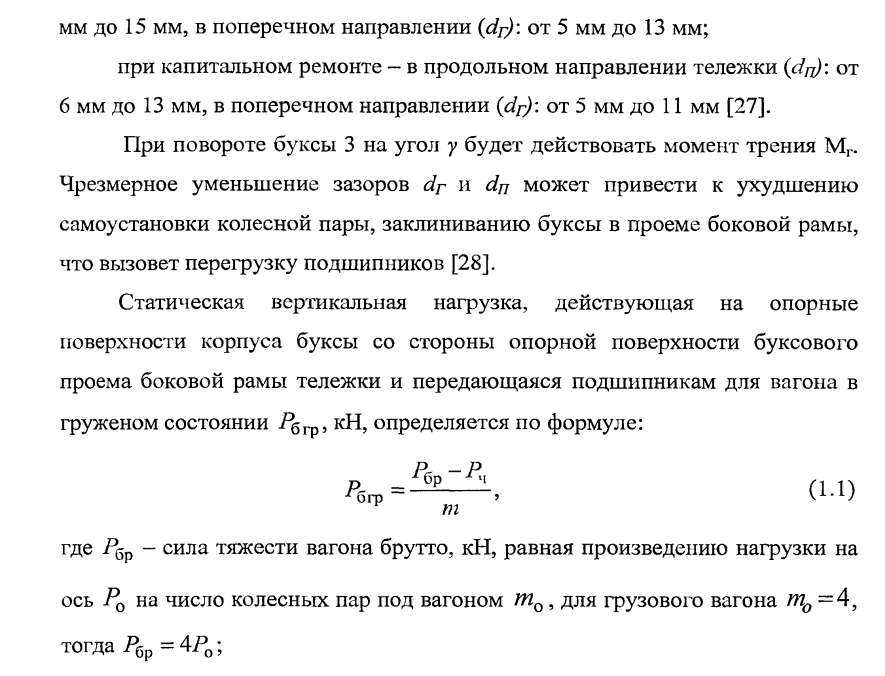
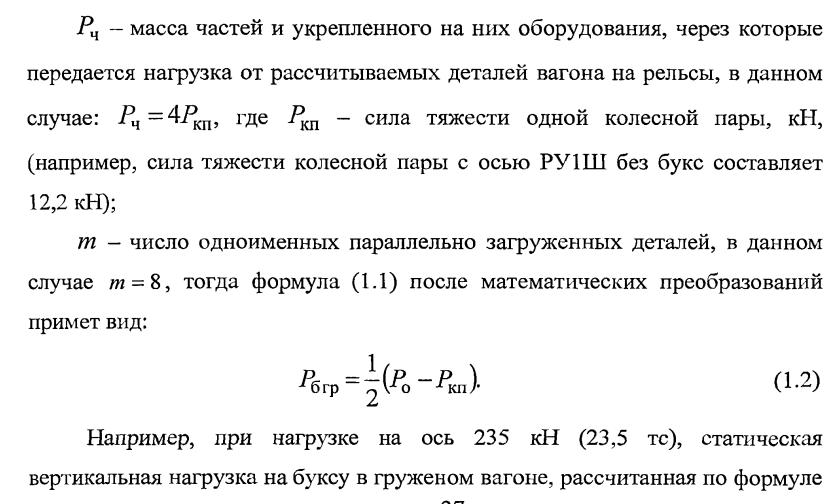
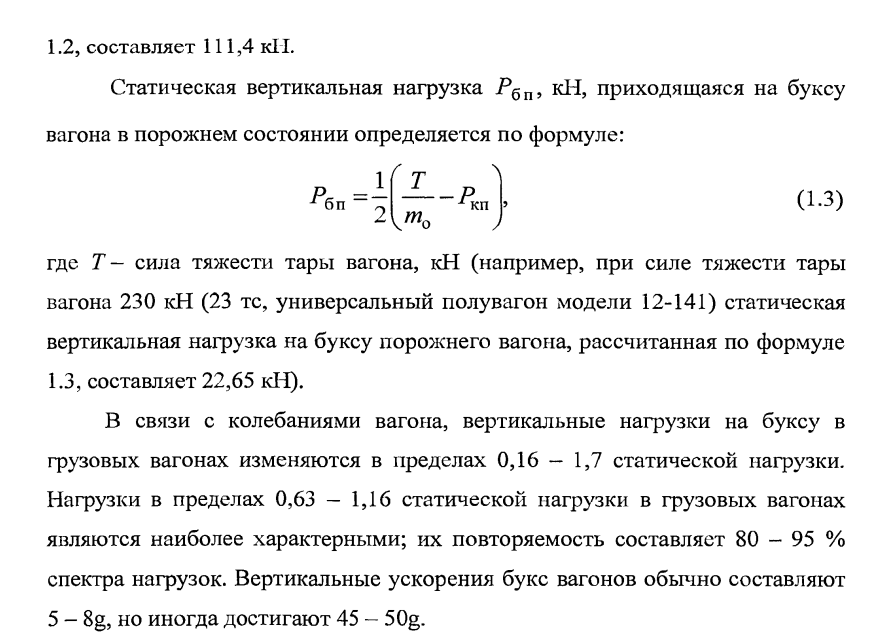
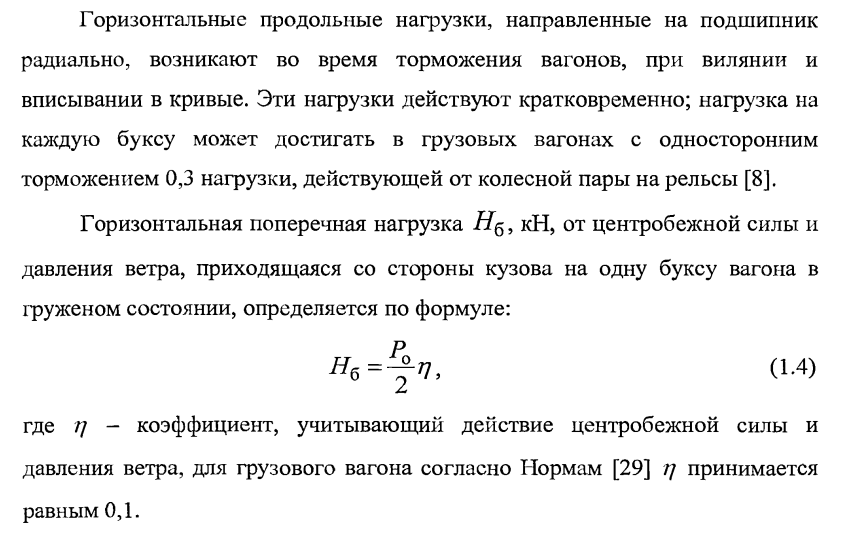
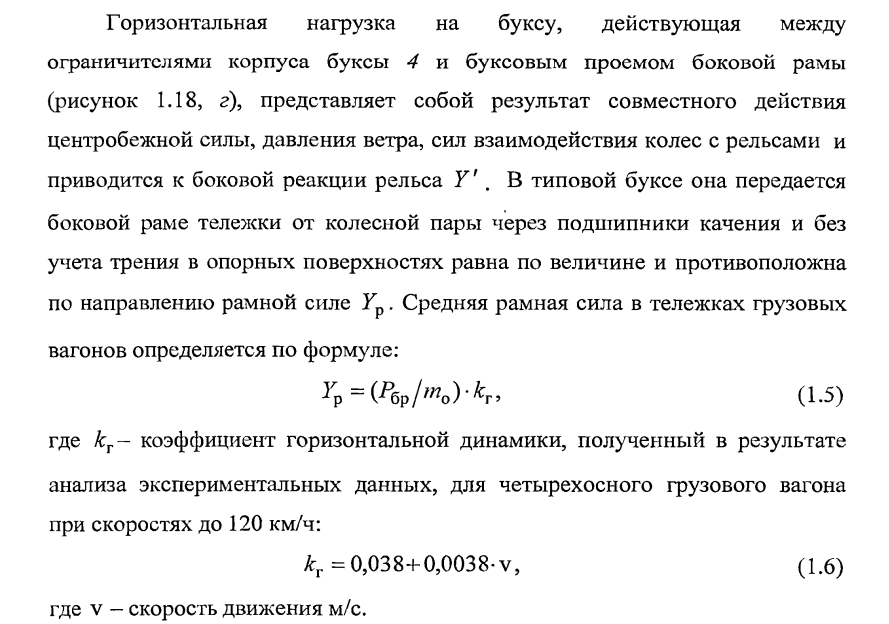
По условиям безопасности движения и устойчивости пути от сдвига максимальная горизонтальная сила взаимодействия подвижного состава и пути не должна превышать 40 % от вертикальной статической нагрузки на ось [30,31].
Расчет допустимой горизонтальной нагрузки на радиальный роликовый подшипник
В работах [32, 33] отмечается, что радиальные подшипники с цилиндрическими роликами обычно применяются только для восприятия радиальной нагрузки. Допустимая величина горизонтальной нагрузки на такие подшипники определяется не усталостными характеристиками материала, а зависит от условий скольжения торцовых поверхностей бортов
или приставных колец относительно роликов. При этом важную роль играют характер нагрузки, скорость вращения и смазка подшипника. Допустимая для цилиндрического роликового подшипника горизонтальная нагрузка Fа, кгс, при консистентной смазке определяется по формуле:
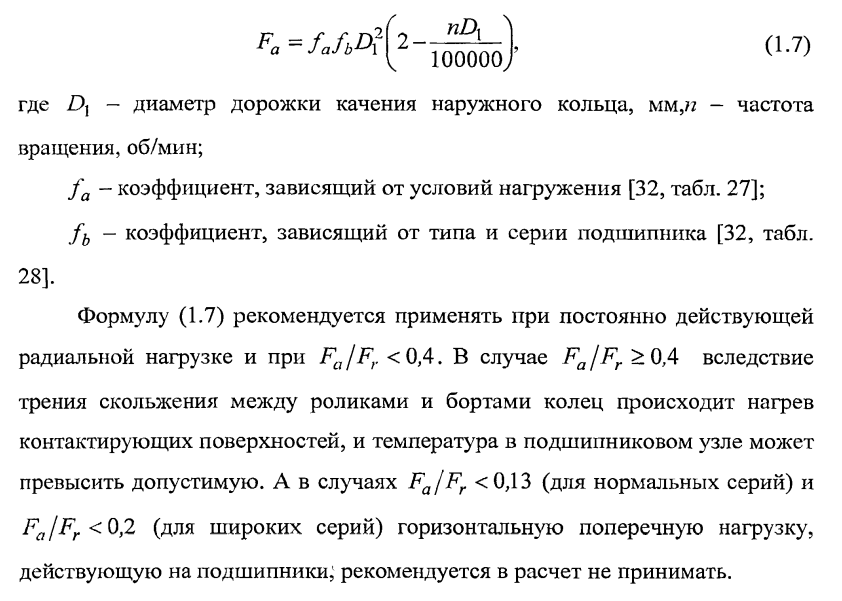
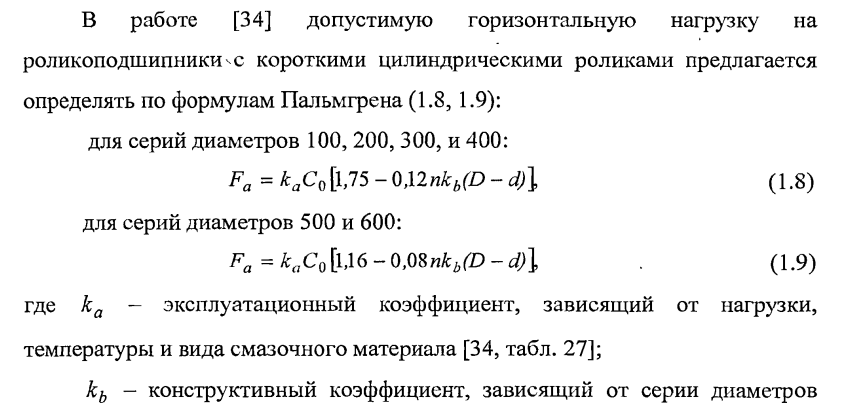
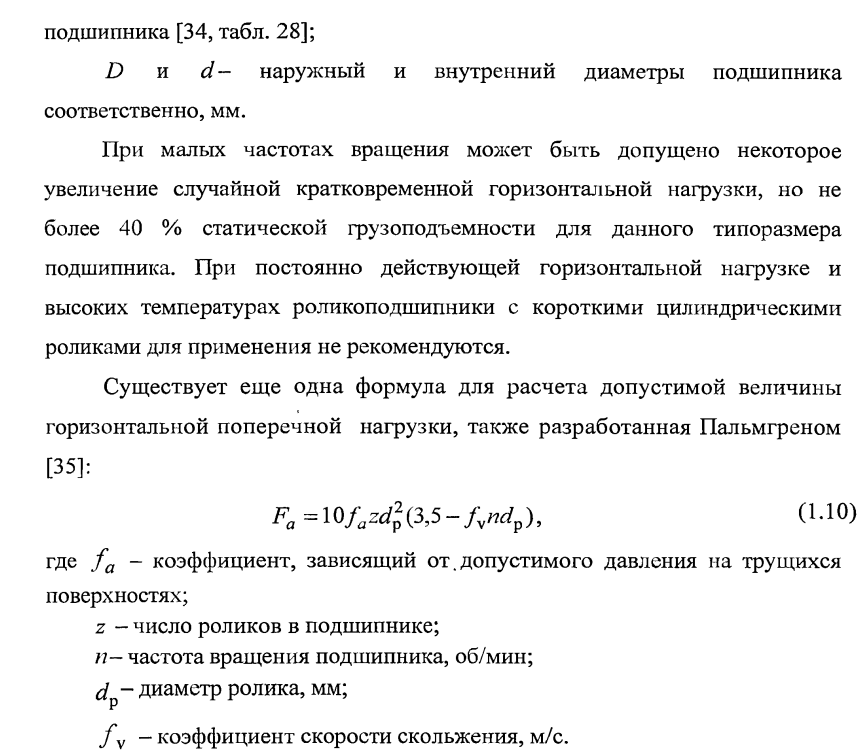
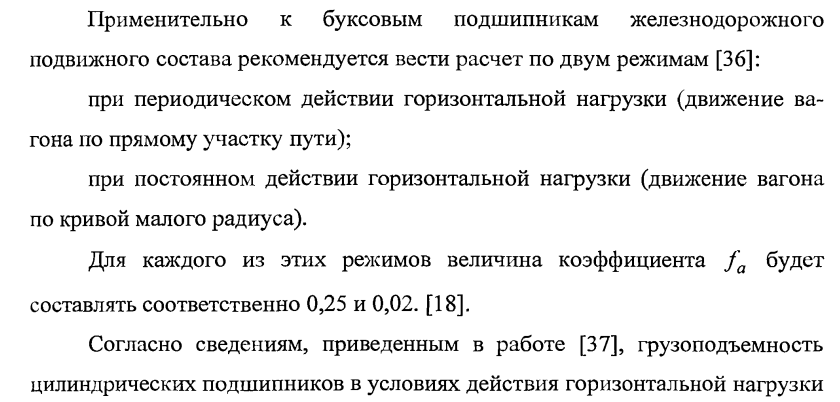
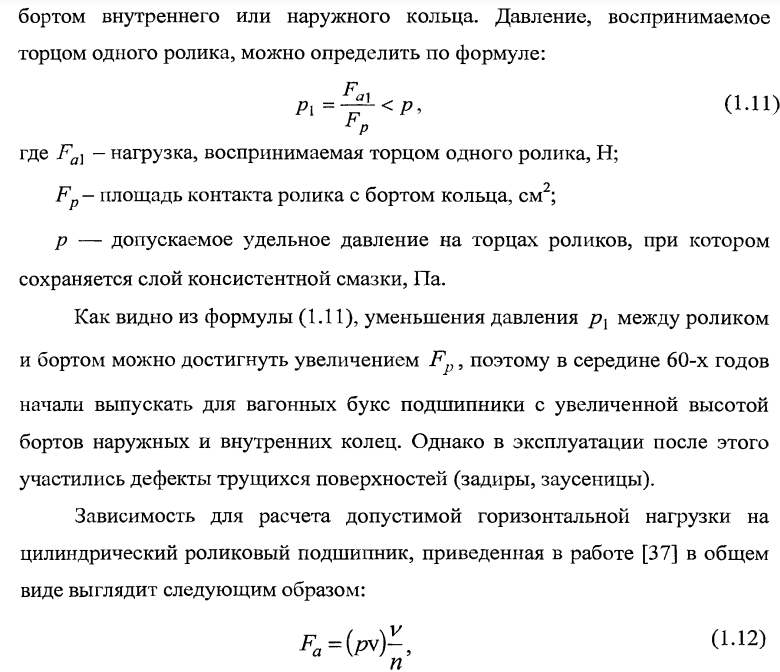
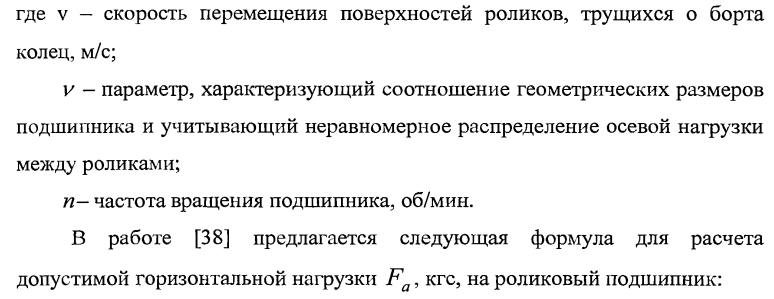
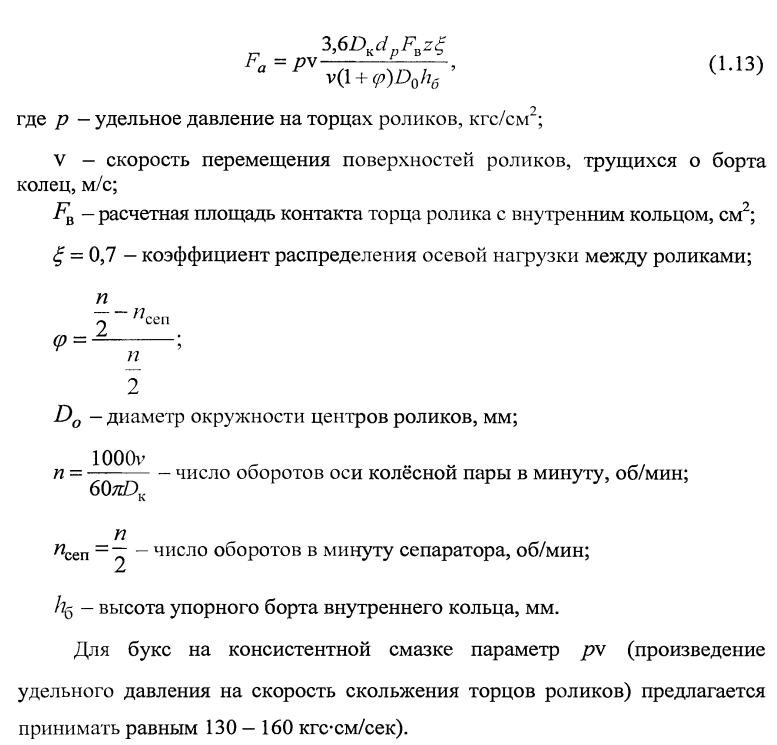
Необходимо иметь в виду, что перечисленные расчетные зависимости (1.7 — 1.13) справедливы, только при соблюдении условия соосности роликов и колец подшипников. Однако в буксовых подшипниках могут возникать перекосы, что снижает достоверность и ограничивает применение предложенных методов оценки допустимой горизонтальной нагрузки.
Расчет базового ресурса буксового подшипника
Базовый расчетный ресурс подшипников L10 представляет собой
наработку, отсчитываемую от ввода в эксплуатацию числом оборотов или километрами пробега, в течение которой не должны появляться признаки усталости металла на любом из колец или тел качения не менее чем у 90 % подшипников данной группы при одинаковых условиях эксплуатации [39].
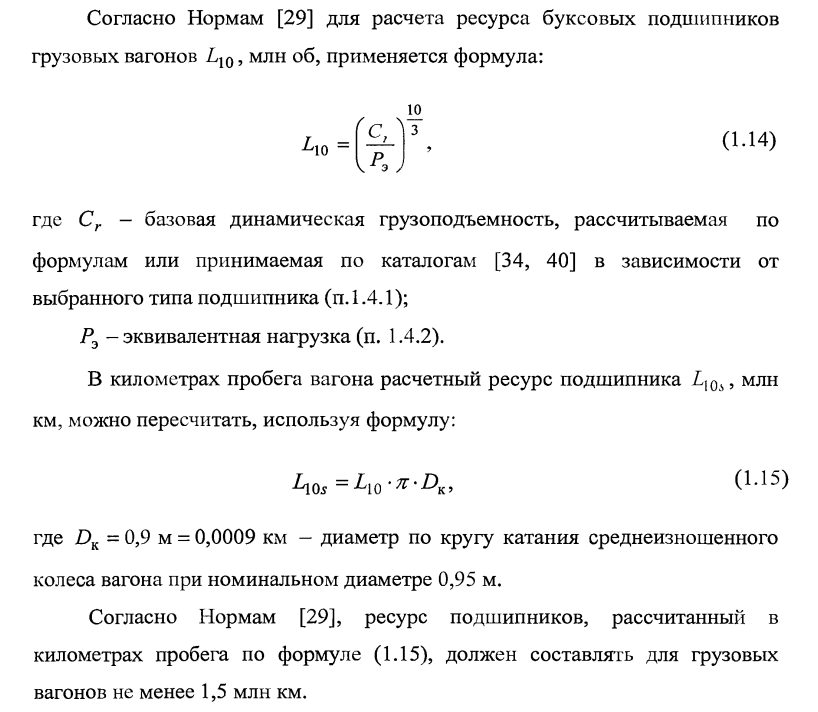
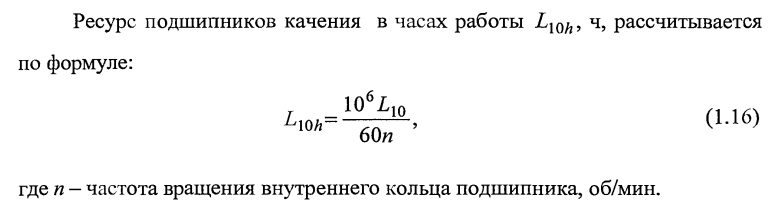
Для определения частоты вращения внутреннего кольца буксового подшипника грузового вагона необходимо задаться значением средней скорости движения.
Расчет динамической грузоподъемности буксового подшипника
Расчет ресурса подшипников производится исходя из динамической грузоподъемности. Под динамической грузоподъемностью радиальных подшипников понимается постоянная радиальная нагрузка, которую группа идентичных подшипников с неподвижным наружным кольцом сможет выдержать в течение расчетного срока службы, исчисляемого в 1 млн оборотов внутреннего кольца. Динамическая грузоподъемность Cr, Н, для буксового радиального роликового подшипника с полиамидным сепаратором определяется по формуле [32, табл. 1, 5, 8-11 с.105-111]:
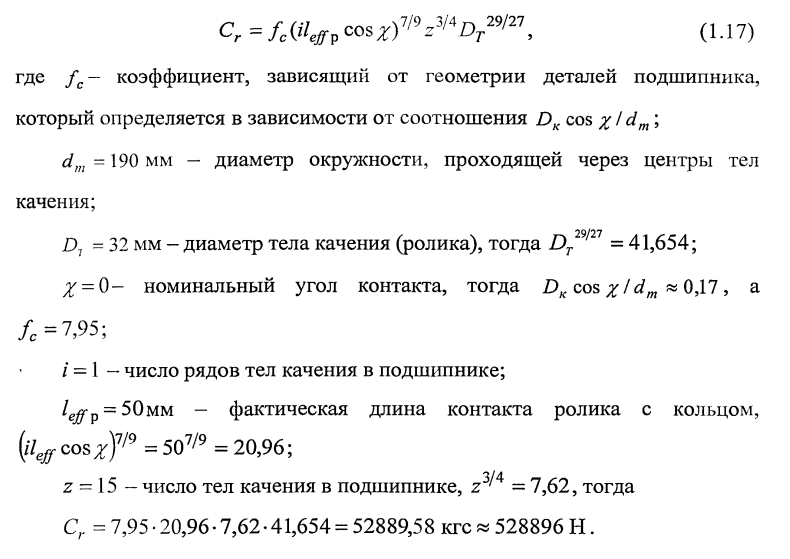
Расчет эквивалентной нагрузки на буксовый подшипник
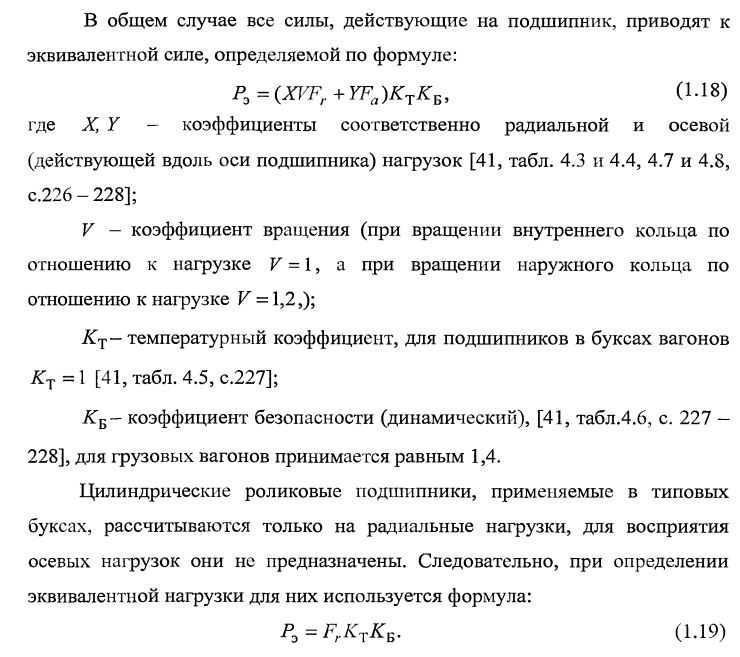

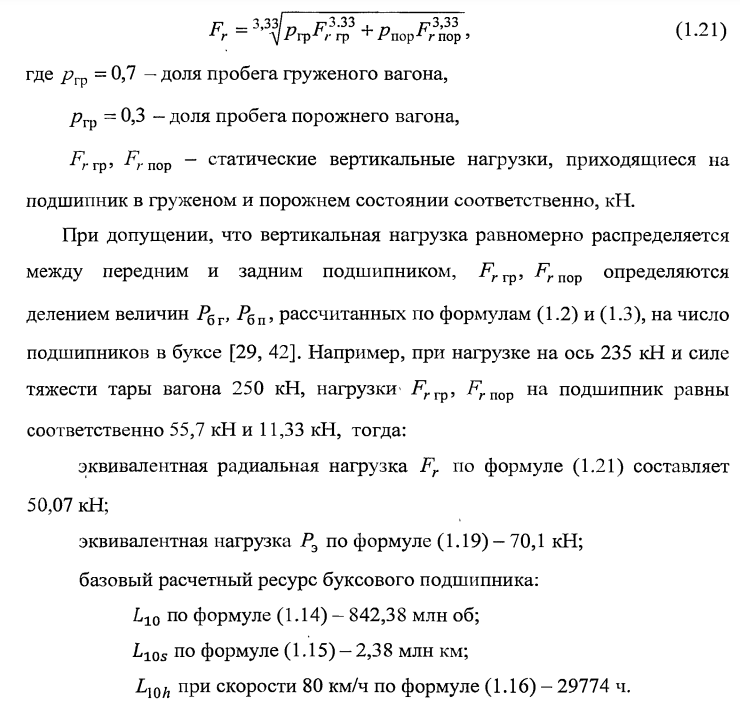
Выводы
На основании анализа применения подшипников качения в буксах
грузовых вагонов можно сделать следующие выводы.
- Конструкция буксы с двумя цилиндрическими роликовыми
подшипниками, применяемая в настоящее время на российских железных дорогах, была принята около пятидесяти лет назад на основании обобщения эксплуатационного опыта и не соответствует возрастающим требованиям к высоконагруженным узлам подвижного состава. Она обладает рядом существенных недостатков, приводящих в условиях роста скоростей и нагрузок на ходовые части к возникновению дефектов и снижению ресурса подшипников. Следовательно, остается актуальной необходимость поиска технического решения, повышающего ресурс буксовых подшипников. - Применение букс отечественного и зарубежного производства с двухрядными коническими подшипниками кассетного типа на отечественных железных дорогах встречает ряд серьезных затруднений, связанных с конструкцией конических подшипников и требованиями к ним, а также с динамическими качествами тележек грузовых вагонов без поводковых устройств. Дефекты, выявленные в конических подшипниках под действием рамной силы, аналогичны дефектам в цилиндрических подшипниках.
- Расчет базового ресурса производится с учетом исключительно радиальной составляющей динамической нагрузки. Воздействие рамной силы не учитывается, хотя именно оно приводит к возникновению наиболее распространенных дефектов цилиндрических и конических буксовых подшипников. Таким образом, расчет ресурса буксовых подшипников не является объективным, то есть не отражает реальной динамической нагруженности буксовых подшипников в условиях эксплуатации и нуждается в уточнении.
Список литературы
- Гапанович, В. А. Белая книга ОАО “РЖД”: Стратегические направления научно-технического развития компании [Текст] /
B. А. Гапанович // Железнодорожный транспорт. – 2007. – №8. – С. 2-6. - Богинский, О. И. Укреплять безопасность движения / О. И. Богинский // Вагоны и вагонное хозяйство. – 2007. – №4. – С. 10-13.
- Миронов, А. А. Тепловой контроль буксовых узлов инфракрасной оптикой [Текст ] / А. А. Миронов, В. JI. Образцов, В. С. Митюшев, Д. Н. Салтыков // Локомотив. – 2008. – №4. – С. 29-32.
- Воротилкин, А. В. Усилить контроль за подвижным составом [Текст] / А. В. Воротилкин // Вагоны и вагонное хозяйство. – 2008. – №3(15). –
C. 40-41. . - Allan, R. К. Roller Bearings [Text] / R. К. Allan. – London: Sir Isaak Pitman and Sons, 1956. – 2nd ed. – 401 p.: il. .
- Harris, T. A. Rolling bearing analysis [Text+ 2 CD-ROMs included] / T. A. Harris, M. N. Kotzalas. – Pennsylvania: CRC Press, 2007. – 5th ed. – 2v. – 723 p.
- Амелина, А. А. Устройство и ремонт вагонных букс с роликовыми подшипниками / А. А. Амелина – 4-е изд., перераб и доп. – М. : Транспорт, 1975.-288 с.
- Волков, Н. Н. Подшипники качения колесных пар вагонов и локомотивов / Н. Н. Волков, Н. В. Родзевич. — М. : Машиностроение, 1872. — 168 с.
- Абашкин, В. В. Опыт эксплуатации вагонов с буксовым узлом на роликовых подшипниках / В. В. Абашкин, В. Ф. Девятков, А. А. Амелина, В. Н. Цюренко, В. Г. Чурсин, А. Л. Ямпольский //. Работа вагонных букс с роликовыми подшипниками при высокоскоростном движении: Труды ЦНИИ, вып. 405. – М.: Транспорт. – 1970. – с. 4-9.
- ГОСТ 3189-89. Подшипники шариковые и роликовые. Система
128
условных обозначений [Текст]. – Введ. 1989-12-21. – М.: Издательство стандартов, 1989. – 11 с. - ГОСТ 3395-89. Подшипники качения. Типы и конструктивные исполнения [Текст]. – Введ. 1989-12-21. – М.: Изд-во стандартов, 1989. – 53 с.
- ГОСТ Р 52598-2006.По дшипники качения. Радиальные и радиально-упорные подшипники. Основные размеры. Размерные ряды. – Введ 2006-11-28. – М. Госстандарт России: Изд-во стандартов, 2006. – 30 с.
- ГОСТ 520-2002. Подшипники качения. Общие технические условия [Текст]. – Введ. 2003-07-01. – 104 с. – М.: Изд-во стандартов, 2003. -.
- ГОСТ 24810-81. Подшипники качения. Зазоры [Текст]. – Введ. 1981¬07-01. – М. Изд-во стандартов, 1981. – 20 с.
- Аверин, Н. А. Работоспособность букс можно повысить [Текст] / Н. А. Аверин, О. А. Русанов, С. Г. Иванов, В. И. Кучугов, Р. X. Халиков // Локомотивы. – 2006. – №12. – с.36.
- ГОСТ 4835-2006. Колесные пары вагонов магистральных железных дорог колеи 1520 мм. Технические условия [Текст]. – Введ. 2008-01-01. – М.: Госстандарт России: Изд-во стандартов, 2008. – 15 с.
- ГОСТ 22780-93. Оси для вагонов железных дорог колеи 1520 (1524) мм. Типы, параметры и размеры [Текст]. – Введ. 1995-01-01. – М.: Госстандарт России: Издательство стандартов, 1995. – 16 с.
- Цюренко, В. Н. Надежность роликовых подшипников в буксах вагонов / В. Н. Цюренко, В. А. Петров. – М. : Транспорт, 1982. – 96 с.
- Сергеев К. А. Повышение работоспособности буксового узла с кассетным подшипником / К. А. Сергеев, А. Н. Францев // Железнодорожный транспорт. – 2008. – №7. – С.58-62..
- Цюренко, В. Н. А ларчик…трудно открывался / В. Н. Цюренко // РЖД Партнер. – 2004. – №12. – С.20-26.
- Буксовые узлы с датчиками компании ЭКГ для современного подвижного состава / По материалам компании БКР // Железные дороги
мира. – 2008. – №4. – С. 47-51. - Гулюткии, А. И. Использование ЭЦВМ для исследования, движения деталей вагонных роликовых подшипников [Текст] / А.И. Гулюткин, М.М. Курганов, В.А. Петров//К вопросу применения ЭЦВМ для прочностных и тормозных расчетов в вагонном хозяйстве: Труды ВЗИИТ,вып.26.-М.:ВЗИИТ,1967.~С. 15-50.
- Рыбников С. Ю. Основы электронной теории износа при трении [Текст] / Ю. С. Рыбников, Л. В. Круглова // Вестник машиностроения. – 1989. – №6. – С. 6-10.
- Миронов, А. А. Моделирование температурных полей буксового узла с цилиндрическими и коническими роликовыми подшипниками / А. А. Миронов, А. Э. Павлюков, В. Л. Образцов, А. В. Занкович // Вестник ВНИИЖТ. – 2007. – №2. – с. 37-42.
- Шаронин, В. С. Буксовый узел с подшипниками качения для пассажирских вагонов высокоскоросных поездов/ В. С. Шаронин // Работа вагонных букс с роликовыми подшипниками при высокоскоростном движении: Труды ЦНИИ, вып.405. – М.: Транспорт, 1970. – с. 10-45.
- Цюренко, В. Н. О деформации наружных колец цилиндрических роликовых подшипников в осевом направлении / В. Н. Цюренко //Работа вагонных букс с роликовыми подшипниками при высокоскоростном движении: Труды ЦНИИ, вып.405. – М.: Транспорт, 1970. – с.68-79.
- РД 32 ЦВ 052-99. Инструкция по ремонту тележек грузовых вагонов [Текст]:[утверждена зам. руководителя Департамента вагонного хозяйства 31.05.1999]. – М.: ГПСБ ЦВ, 1999. – 87 с.
- Морчиладзе, И. Г. Совершенствование и модернизация буксовых узлов грузовых вагонов / И. Г. Морчиладзе, А. М. Соколов // Железные дороги мира. – 2006. – №10. – С. 59-64.
- Нормы расчета и проектирования грузовых вагонов железных дорог колеи 1520 мм Российской Федерации [Текст]. – М.: ФГУП ВНИИЖТ –
ФГУП ГосНИИВ, 2004. – 212 с. - Динамические нагрузки ходовых частей грузовых вагонов: Труды Всесоюз. науч.-исслед. ин-та ж.-д. трансп., вып. 572 / Под ред. Н. Н. Кудрявцева. – М: Транспорт, 1977 г. – 143 с.
- Бороненко, Ю. П. Тележки с повышенной осевой нагрузкой / Ю. П. Бороненко, А. М. Орлова // Железнодорожный транспорт. – 2008. – №8. – С. 50-53.
- Бейзельман, Р. Д. Подшипники качения. Справочник [Текст] / Р. Д. Бейзельман, Б. В. Цыпкин, JI. Я. Перель.
- SKF General Catalogue N 2800 E/GB 600. – 1970. – 502 p.
- Подшипники качения: Справочник-каталог [Текст] / Под ред. В. Н. Нарышкина, Р. В. Коросташевского. – М.: Машиностроение, 1984. – 280 с.
- Palmgren, А. Crundlagen der wälylagertechnick. – Stuttgart: Frankh’sche Verlogshandlung, 1950. – 350 p.
- Illmann, О. Walzlager in Eisenbahnwagen und Dampflokomotiven / Obst Illmann. – Berlin: Verlag von Wilhelm Ernst und Sohn, 1957. – p.53.
- Спицын H. А. Осевая грузоподъемность и трение в торцах роликов цилиндрических роликовых подшипников [Текст] / Н. А. Спицын // Подшипниковая промышленность: реф. сб. — Вып. 4. – М.: Специнформцентр ВНИПП, 1966.-с. 26-30.
- Поляков, А. И. Воспринятие цилиндрическим подшипником осевых нагрузок [Текст] / А. И. Поляков // Подшипниковая промышленность. – М.: ЦИНТИАМ, 1964. – Вып. 1. – 154 с.
- ГОСТ 27.002-89. Надежность в технике. Основные понятия, термины и определения. Межгосударственный стандарт.
- АО ВНИИ ТЕМП. Подшипники качения и свободные детали: Каталог-справочник. М. : ИФК Каталог, ч1,2 -1997, 4.3-1998. стр.: ч.1- 122,4.2-104, 4.3-104.