Сейчас ваша корзина пуста!
Разработка и опробование технологии плазменной наплавки на рельсовую сталь и сталь Гатфильда
Цикл статей:
Глава 1 – Формирование структуры и свойств при плазменной наплавке износостойких покрытий на медь и высокоуглеродистую, марганцовистую стали
Глава 2 – Материлы и методы исследования
Глава 3 – Разработка конструкции плазмотрона с расширяющимся каналом сопла для плазменной наплавки
Глава 4 – Плазменное нанесение жароизносостойкого покрытия на медную основу
Подбор материала наплавки и отработка технологии наплавки на рельсовую сталь и сталь Гатфильда
Неблагоприятное распределение температур при сварке или наплавке стали 110Г13Л, приводит к образованию значительных напряжений, связанных с неравномерным нагревом изделия, и плохо отражается как на качестве металла околошовной зоны, так и на качестве наплавленного металла, что связано с образованием горячих трещин, перекристаллизацией стали в зоне термического влияния и выпадением карбидов.
Для уменьшения отрицательного влияния указанных факторов и склонности к образованию трещин в практике используется ряд технологических приемов. В частности, в работе [54] рекомендуется применять проковку наплавленного металла, которая должна производиться в горячем состоянии сразу за наложением слоя и продолжаться до остывания металла. При этом длина наплавки должна быть в пределах 100 – 200 мм. Авторы связывают это с тем, что наплавленный металл при охлаждении дает усадку, в результате возникают дополнительные термические напряжения, способствующие образованию трещин.
При многослойной наплавке применяется деформация наплавленного слоя эксплуатационной нагрузкой [19].
Во избежание в процессе наплавки превращений, вызывающих выделение карбидов и охрупчивание стали, авторы [54] рекомендуют производить наплавку в условиях, обеспечивающих наименьшее тепловложение. Для этого длина каждой наплавки ограничивается 100 -150 мм. В процессе наплавки, прилегающий к зоне наплавки, высокомарганцовистый металл не должен разогреваться больше, чем на 200 °С. При разогреве больше > 200 °С наплавку необходимо прекратить.
Для предупреждения быстрого нагревания наплавляемую деталь можно охлаждать водой (помещать в сосуд с водой, поливать или смачивать мокрыми концами и т.п.), при этом закипание воды не допускается.
При разработке технологии наплавки на сталь Гатфильда и следует иметь в виду, что обычные стальные электроды для наплавки применять нельзя. При применении таких электродов, а также при наплавке высокомарганцовистой стали на углеродистую в переходной зоне может оказаться слишком мало марганца, вследствие чего в околошовной зоне происходит образование мартенситной структуры, которая, характеризуясь повышенной хрупкостью, может вызвать отслоение наплавки [80]. Поэтому при выборе электродов для наплавки высокомарганцовистой стали одним из основных требований является то, чтобы химический состав используемых наплавочных материалов обеспечивал получение аустенитной структуры в зоне наплавки и в наплавочном металле [81]. Выбор электродов для наплавки изделий из высокомарганцовистой стали зависит от их назначения и условий работы.
Если износ наплавленных рабочих поверхностей происходит интенсивнее развития дефектов, например, трещин, можно применять максимально износостойкие наплавочные материалы даже при их заметной чувствительности к образованию трещин. Если же нарастание износа при эксплуатации происходит относительно медленно, тогда развитие трещин, образовавшихся при наплавке, может привести к отколу наплавленного слоя задолго до достижения предельного износа. Поэтому в таких случаях следует применять электроды, наплавленный металл которых износостоек и не склонен к образованию трещин [80].
В номенклатуру отечественных наплавочных материалов, наиболее широко применяемых в промышленности для упрочнения и восстановления изделий из высокомарганцовистой стали входят:
- самозащитная никель – марганцевая порошковая проволока ПЛАН! 05 (90Г13Н4), разработанная в Институте электросварки им. Е.О. Патона для технологии полуавтоматической наплавки железнодорожных крестовин в стационарных условиях с вертикальным износом до 25 мм [19];
- электроды марки ЭНГ-13(Э-80Г14) с 0,7 – 0,9 % углерода и 12 – 16 % марганца [82];
- электроды марки ОМГ-Н (Э-65Х11НЗ) – хромо-никель-марганцевая проволока с содержанием марганца 0,7% и углерода 0,5 – 0,8 %. С целью уменьшения образования трещин в наплавленном металле в ВНИИЖТ была разработана электродная проволока марки ЦНИИН-4 (Э-65Х25ПЗНЗ) с высоким содержанием хрома (22-28 %) и марганца (11-14 %), предназначенная для наплавки железнодорожных крестовин взамен электродов марки ОМГ-Н и широко используемая в настоящее время [80].
Более поздние работы по изысканию и исследованию наиболее трещинностойких составов наплавочных материалов привели к созданию электродов марки Гр-5 и Гр-6 в ХАРИ (Харьковский автодорожный институт) [82]. Металл, наплавленный электродом Гр-5 относится к типу Э- 150Х2Г15М. Эти составы дополнительно легированы молибденом в пределах 1-2 %. По сравнению с металлом, наплавленным электродом ЦНИИН-4, он имеет более высокую износостойкость и твердость. Меньший износ наплавленного металла типа Э-150Х2Г15М относительно Э-65Х2Г13НЗ (ЦНИИН-4) авторы работы [82] объясняют более благоприятной мелкозернистой структурой благодаря влиянию молибдена. Производство электродов Гр-5 и Гр-6 освоено на Харьковском заводе транспортного машиностроения.
В целом ряде публикаций [81-85] приведены результаты исследований по легированию износостойкого наплавочного материала, проводимого с целью улучшения его физико-механических свойств, повышения износостойкости и уменьшения склонности к образованию трещин в наплавленном металле и в зоне наплавки. В вышеуказанных работах отмечается, что с точки зрения упрочнения высокомарганцовистой стали путем легирования перспективным следует считать дополнительное легирование аустенитной стали такими элементами как молибден, титан, ванадий и цирконий. Растворимость этих элементов в аустените увеличивается с увеличением в стали марганца. Добавки никеля к высокомарганцовистой стали стандартного состава практически не оказывают влияния на прочностные характеристики стали. Добавки никеля способствуют повышению устойчивости аустенитной структуры и повышают прочность соединения наплавленного металла со сталью Г13Л.
По поводу влияния хрома в больших количествах существуют разноречивые мнения. Как указывается в работе [80] преимущество высокого содержания хрома в металле, наплавленном электродом ЦНИИН-4 (Э-65Х25Г13НЗ), перед высокомарганцовистой сталью Г13Л состоит в снижении вероятности образования горячих трещин. Однако в работе [86] отмечается, что работоспособность изделий, имеющих горячие трещины в зоне термического влияния, не уменьшается. Авторы [80,82] утверждают, что легирование наплавленного металла Э-65Х25ПЗНЗ большим количеством хрома не привело к значительному улучшению механических свойств.
Замечено, что на образование трещин при наплавке оказывает влияние кремний и фосфор. По данным [87] полным отсутствием трещин в околошовной зоне обладают марганцовистые стали Г13Л с низким содержанием кремния и фосфора следующего состава: углерод не более 1,10%, марганец – не менее 12,5%, кремний – не более 0,45%, фосфор – не более 0,030%. И далее отмечается, что практически такое сочетание в стали получить нельзя (в основном по экономическим соображениям), так как обычные сорта ферромарганца, применяемые при литье, содержат слишком много фосфора. Там же [87] отмечается, что для снижения растягивающих напряжений в зоне термического влияния рекомендуется, как один из способов, предварительный подогрев.
Таким образом, проведенный анализ литературных источников и публикаций, посвященных вопросу наплавки, показал, что в технологическом процессе наплавки на высокомарганцовистую сталь до настоящего времени остается много проблем и, в том числе, проблема борьбы с трещинами, поиски более экономически и экологически выгодных способов наплавки, повышающих срок службы изделий.
Отработка технологии наплавки проводилась на полнопрофильных образцах вырезанных из железнодорожных крестовин и на образцах из рельсовой стали, подвергнутой следующим обработкам: 1 – закалка в масло 830 °С, 50 мин, отпуск 500 °С; 2- отжиг 850 °С, 2 часа, охлаждение с печью до 600 °С, далее на воздухе.
Экспериментальная наплавка образцов производилась на установке плазменной наплавки с помощью плазмотрона с расширяющимся каналом. В качестве плазмообразующего и транспортирующего газа использовался аргон. В качестве наплавочного материала – металлический порошковый сплав ПР – 65Х25Г13НЗ (с условным названием «Г13»), соответствующий химическому составу электродам ЦНИИН-4 и изготовленный по спецзаказу на заводе “Тулачермет” (химический состав по заводскому сертификату качества: основа – железо, 25,25% хрома, 13,26% марганца, 3,5% никеля, 0,8% кремния, 0,8% углерода и 0,024% фосфора).
Качество плазменной наплавки и свойства наплавленного соединения в первую очередь определяются качеством порошка и поверхности изделия под наплавку, правильным выбором режима наплавки и правильным выполнением техники наплавки.
Порошок, применяемый для наплавки, должен быть абсолютно чистым и иметь гранулы размером 160-315 мкм. На гранулах порошка не допускается следов масла, ржавчины, смазки, влаги и других загрязнений. Поэтому порошок перед наплавкой просеивается и подвергается сушке в печи при температуре 170 °С.
Перед наплавкой с поверхности изделия – литой части крестовины должны быть удалены дефекты контактной усталости, наплавляемые поверхности зачищены до «свежего» металла, тщательно очищена от слоя окислов, масла, ржавчины и других загрязнений. Лучше всего такая поверхность обеспечивается при дробеструйной или пескоструйной очистке. В данном случае применяли механическую очистку поверхности с помощью абразивного камня.
Такие требования к чистоте порошка и поверхности изделия диктуются не только соображениями получения качественного металла наплавки (отсутствия пор, окисных включений), но и необходимостью обеспечить смачивание поверхности изделия жидким наплавляемым металлом. Так как на условия смачивания оказывают влияние малые добавки, особенно наличие на поверхности изделия слоя окислов. Известно, что поверхностное натяжение окислов значительно меньше, чем соответствующих металлов. Поэтому металлы, покрытые слоем окислов, смачиваются, как правило очень плохо. Вот почему для обеспечения необходимых условий смачивания поверхности изделия жидким наплавляемым металлом изделие должно быть тщательно очищено от пленки окислов, всегда имеющейся на его поверхности. Такая очистка поверхности изделия уменьшит и переход элементов основного металла в металл наплавки, так как смачивание осуществляется в процессе растворения слоя окислов. И, наконец, удаление с поверхности слоя окислов увеличивает растекание жидкого металла по поверхности изделия, т. е. приводит к увеличению скорости наплавки.
Одним из основных параметров режима наплавки является величина сварочного тока. Увеличение сварочного тока приводит к увеличению перегрева наплавляемого металла и, как следствие, к увеличению нагрева поверхности основного металла. С учетом требований, предъявляемых к наплавке высокомарганцовистой стали по ограничению тепловложения пробные наплавки сначала проводились при силе тока 1=160 А. В этом случае сцепление наплавочного металла с основным материалом наблюдалось только по краям, на остальной поверхности, по результатам металлографического исследования – отсутствовало.
При увеличении тока до 190 А сплавление наблюдалось по всей наплавляемой площади, и в дальнейших экспериментах сила тока не менялась и поддерживалась равной 190 А при выполнении наплавки первого слоя. При многослойной наплавке все последующие слои выполнялись на меньших токах (180 А) для уменьшения тепловложения.
Расход порошка оказывает большое влияние на характер переноса металла в сварочную ванну. Так как порошок вдувается в дугу и проходит через сопло с выходным диаметром 4 мм, то таким образом расход порошка определяется массой порошка, которую можно пропустить через это сечение. При этом нельзя допустить налипание порошка на водоохлаждаемые внутренние стенки сопла. Экспериментальные наплавки показали, что при поперечной скорости наплавки Упопер.= 20 мм/мин расход порошка должен быть равен ~0,3 г/сек.
Скорость наплавки при наплавке плазменной струей с вдуванием порошка в плазменную струю определяется режимом наплавки, расстоянием от торца сопла до поверхности основного металла, качеством подготовки поверхности основного металла, требованием попадания капель перегретого расплавленного металла присадочной проволоки в ванну жидкого металла. Оптимальной можно считать такую скорость наплавки, при которой капли перегретого жидкого наплавленного металла попадают в ванну перемещающегося по поверхности изделия жидкого металла наплавки на расстоянии 2 – 3 мм от головной части ванны. Критерием того, что установленная скорость наплавки максимальна, является то, что при увеличении установленной скорости наплавки капли присадочного металла начинают частично попадать на основной металл впереди перемещающейся ванны.
При уменьшении скорости наплавки (в определенных пределах) увеличиваются нагрев поверхности основного металла и длительность контактирования твердой и жидкой фаз, что может привести к увеличению содержания примесей основного металла в металле наплавки.
При чрезмерном уменьшении скорости наплавки, когда капли наплавляемого материала попадают в ванну на расстоянии свыше 8 – 10 мм от ее головной части, может произойти, уменьшение температуры разогрева поверхности основного металла. Это можно объяснить тем, что к моменту попадания капель наплавляемого металла в ванну, часть ванны, соприкасающаяся с твердым основным металлом, уже закристаллизовалась. Дополнительно введенное с каплями жидкого металла тепло недостаточно для расплавления уже закристаллизовавшегося металла. Кроме того, прослойка жидкого металла между плазменной струей и поверхностью основного металла значительно большая, чем при оптимальной скорости наплавки, что также приводит к уменьшению разогрева поверхности основного металла. Однако применение таких заниженных скоростей наплавки приводит к резкому уменьшению производительности труда, повышенному расходу наплавляемого металла. Поэтому скорость наплавки следует устанавливать оптимальной в соответствии с установленным режимом наплавки. В данном случае были подобраны следующие скорости: продольная скорость перемещения плазмотрона Упрод.=10 мм/мин, поперечная скорость перемещения плазмотрона Упопер.=20 мм/мин.
Как указывалось выше, расстояние от среза сопла до изделия очень сильно влияет на эффективную тепловую мощность источника теплоты: с уменьшением этого расстояния эффективная тепловая мощность, а следовательно нагрев поверхности основного металла и переход элементов основного металла в металл наплавки увеличиваются. Кроме того, при чрезмерном уменьшении расстояния от среза сопла до изделия ухудшается газовая защита из-за образования высокой турбулентности потока в результате подсоса воздуха. Чрезмерное увеличение расстояния (более 25 мм) приводит также к резкому ухудшению газовой защиты, вызывая дефекты в металле наплавки. Наиболее оптимальным, как показали исследования, является расстояние 10-14 мм.
В ходе экспериментальных наплавок на изношенной крестовине, проводилось исследование деформаций. Для экспериментов использовались центральные участки крестовины.
Измерение стрелы прогиба наплавленного образца проводилось с помощью специального приспособления, устанавливаемого на трех опорах и имеющего индикатор линейных перемещений с ценой деления 0,01 мм. Устройство содержит простейшую раму в виде скрепленных перпендикулярно между собой металлических стержней. На стержнях установлены три конические опоры, изготовленные из закаленной стали. Для того, чтобы приспособление занимало строго определенное положение, на усовиках накернивались два углубления, третья опора самоустанавливалась на образце. По изменению показаний индикатора до и после наплавки определялась величина продольной деформации образца.
Анализируя влияние наплавленного слоя на остаточную продольную деформацию можно сделать следующий вывод. При наплавке в наплавленном слое возникают остаточные напряжения растяжения, которые легко могут вызвать появления трещин.
С целью снижения деформации и остаточных напряжений при наплавке проводили исследование влияния отпуска и ударного наклепа на структурное состояние наплавки.
Исследование влияния отпуска и исходного состояния рельсовой стали на механические свойства основного металла, наплавки и переходной области
Известно, что релаксация остаточных микронапряжений может протекать в ходе нагрева металла после наплавки. В частности отпуск стали часто применяется для снятия остаточных макро- и микронапряжений. В связи с этим, представляло интерес исследование влияния отпуска на механические свойства границы наплавки и основного металла.
В качестве объекта исследования была выбрана рельсовая сталь в отожженном (850 °С, 2 часа до 600 °С и охлаждение на воздухе) и закаленном состоянии (закалка от 830 °С в масло и отпуск при 500 °С
89 50 мин). Отпуск после наплавки осуществляли при 450 °С в течении 1 часа.
Результаты испытаний поперечных образцов представлены в табл. 5.1. Видно, что отпуск несколько снижает значения прочности и предела текучести.
Однако, пластичность (относительное удлинение) практически не изменяется для исходного закаленного состояния и несколько возрастает для отожженного. Следует отметить, снижение величины поперечного сужения для наплавки на закаленную рельсовую сталь, что, по-видимому, связано с образованием дефектов типа микротрещин при наплавке на высокоуглеродистую закаленную рельсовую сталь.
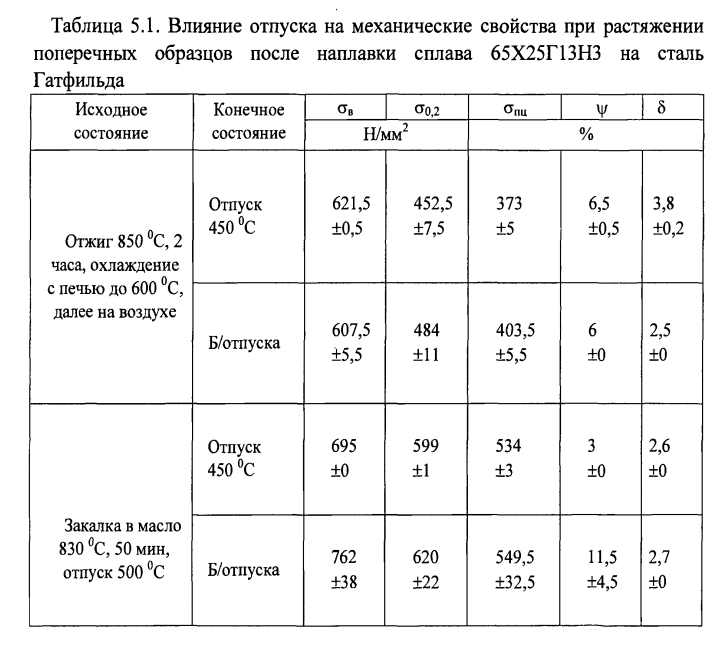
В пользу этого предположения свидетельствуют данные испытаний на ударную вязкость (табл. 5.2). Уровень ударной вязкости на границе наплавки для исходной закаленной рельсовой стали ниже, чем после наплавки на отожженную рельсовую сталь.
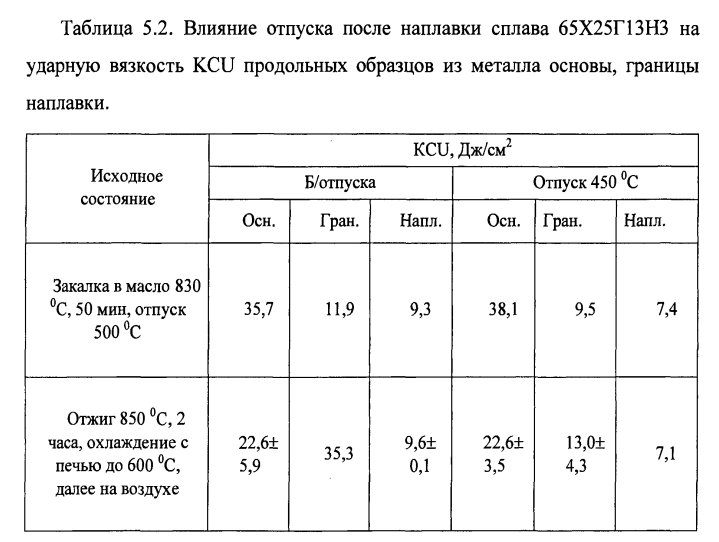
Таким образом, отпуск после наплавки на рельсовую сталь не является эффективной релаксационной обработкой. Особенно при наплавке на закаленную рельсовую сталь.
Результаты исследования влияния исходного состояния рельсовой стали на механические свойства и сопротивление разрушению при изгибе представлены на рис. 5.1. и рис. 5.2.
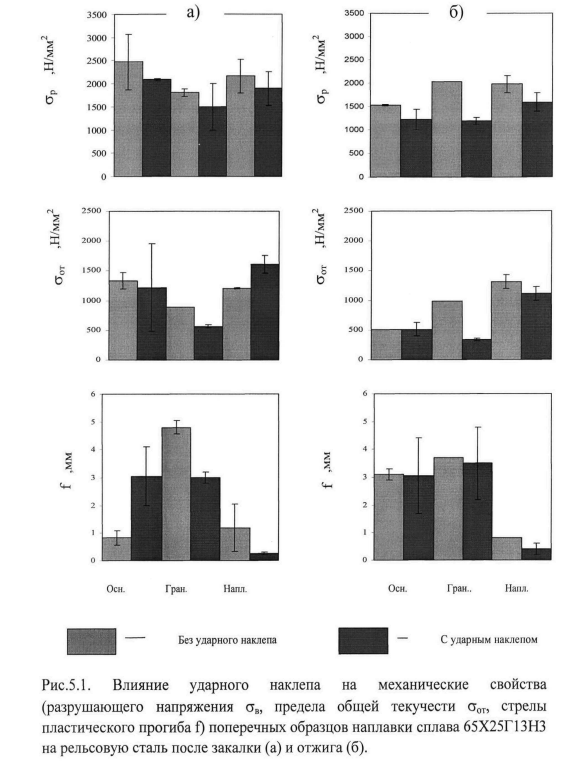
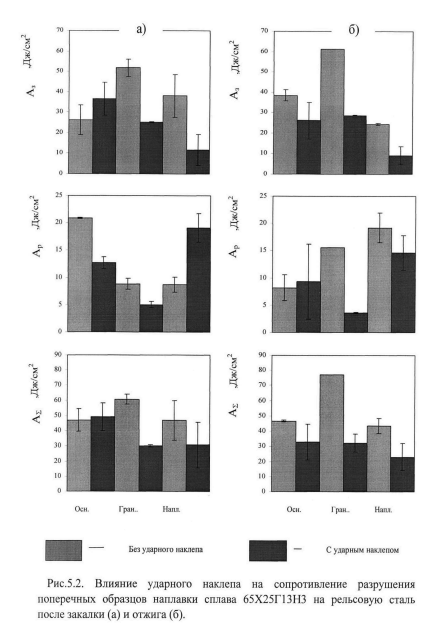
Видно, что при близких значениях разрушающего напряжения ор и напряжения общей текучести о0т суммарная работа разрушения и ее составляющие – работа зарождения А3 и распространения Ар трещины существенно выше при наплавке на отожженную рельсовую сталь, чем на сталь подвергнутую закалке. Кроме того, важно отметить, что при наплавке на закаленную рельсовую сталь провал твердости вблизи границы наплавленного слоя со стороны основного металл, что является следствием разупрочнения закаленной рельсовой стали в ходе нагрева поверхности металла при наплавке (рис.5.3).
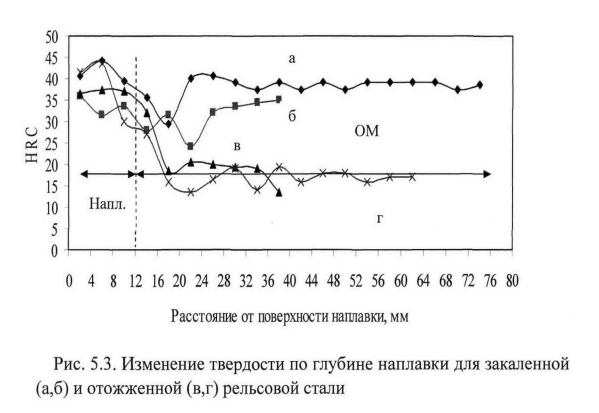
Таким образом, из полученных результатов следует, что для получения качественной наплавки на рельсовую сталь предпочтительно ее осуществлять на предварительно отожженный металл во избежание получения высоких уровня напряжений и неоднородности свойств в поперечном направлении.
Исследование влияния ударного наклепа на механические свойства, фазовый состав и уровень остаточных микронапряжений при наплавке хромомарганцевого сплава на рельсовую сталь
Известно, что релаксация остаточных напряжений, возникающих при термическом воздействии в металле, может быть инициировано фазовым превращением в результате пластической деформации. В связи с этим, исследовали влияние теплого ударного наклепа на механические свойства и структурное состояние наплавки на рельсовую сталь.
Влияние ударного наклепа на механические свойства и сопротивление разрушению металла основы, границы наплавки и наплавленного металла представлено на рис. 5.1 и рис. 5.2. Видно, что прочностные свойства после ударного наклепа на границе наплавки и в наплавленном металле близки. При этом сопротивление разрушению (А3; Ар и А^) в результате наклепа снижаются.
С целью выяснения причин такого изменения механических свойств и сопротивления разрушению проводили анализ влияния ударного наклепа на фазовый состав и уровень внутренних микронапряжений наплавки на рельсовую сталь.
Известно, что склонность к хрупкому разрушению стали и сплавов зависит в основном от их структурного состояния – количества фаз и их соотношения, уровня внутренних напряжений и степени однородности их распределения.
Проведено рентгеноструктурное исследование структурного состояния наплавки из сплава 65Х25Г13НЗ на поверхность термообработанных рельсов Исследованию подлежали три типа обработок.
- основа- рельсовая сталь (закалка в масло 830 °С, 50 мин, отпуск 500 °С)
+ наплавка порошком 65Х25Г13НЗ + наклеп (ударная обработка);
- основа – рельсовая сталь + отжиг 850 °С, 2 часа, охлаждение с печью до 600 °С, далее на воздухе + наплавка порошком 65Х25ПЗНЗ + наклеп (ударная обработка);
- основа- рельсовая сталь (закалка в масло 830 °С, 50 мин, отпуск 500 °С) + наплавка порошком 65Х25ПЗНЗ.
Объектами исследования являлись образцы (20х20х20),вырезанные из наплавленных рельсов, сошлифованных по сечению.
Рентгенографирование проводили с поверхности и по глубине наплавки (на расстоянии 3,5; 6.5; 8.5; 10; 11; 12; 14.5 мм от поверхности) на рентгеновском дифрактометре ДРОН-3 в Ее излучении, в режиме записи дифрактограмм интерференционных линий (111)у, (311)у и (110)а, (211)а
Определяли количество фаз – а и у – из соотношения интенсивностей интерференционных линий (111) у-фазы и (110) а- фазы.
Об уровне внутренних остаточных микронапряжений судили по ширине интерференционных линий (311)у у-фазы и (211)а а- фазы, прямо пропорциональной их величине. Для выяснения характера процессов, протекающих в твердом растворе при наплавке сплава на рельсовую сталь определяли период кристаллической решетки ау у- фазы. Локальную концентрацию микронапряжений оценивали из доли площади «хвостов» дифрактограмм к общей интенсивности (площади) дифрактограмм.
Характер изменения структурного состояния по сечению наплавленного рельса одинаков для трех исследуемых состояний.
Наплавка представляет собой металл с гранецентрированной кристаллической ешеткой (ГЦК) – у- фазой и небольшим количеством (15-25%) а- фазы- с ОЦК решеткой.
На рис.5.4 представлена дифрактограмма интерференционных линий (111) у-фазы и (110) а- фазы по сечению наплавленного рельса (для обработки 1). Она иллюстрирует изменение соотношения интенсивностей у и а фаз по глубине наплавленного слоя: интенсивность линии (111)у 1у уменьшается, а 1а – (111) а-растет, и на границе количество у – фазы уменьшается и она исчезает. Толщина слоя с ГЦК – решеткой составляет
12 мм.
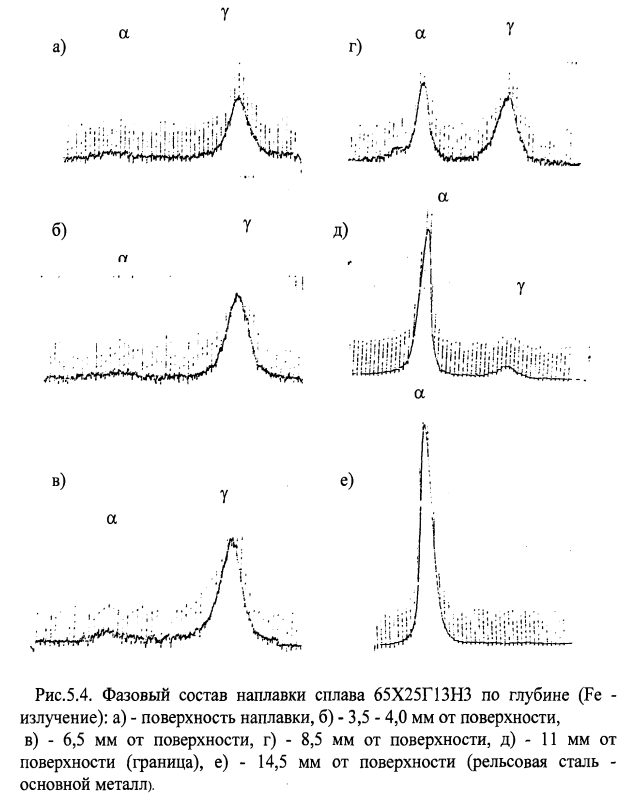
Изменение количества у-фазы и а-фазы по глубине наплавки для трех обработок представлена на рис.5.5.
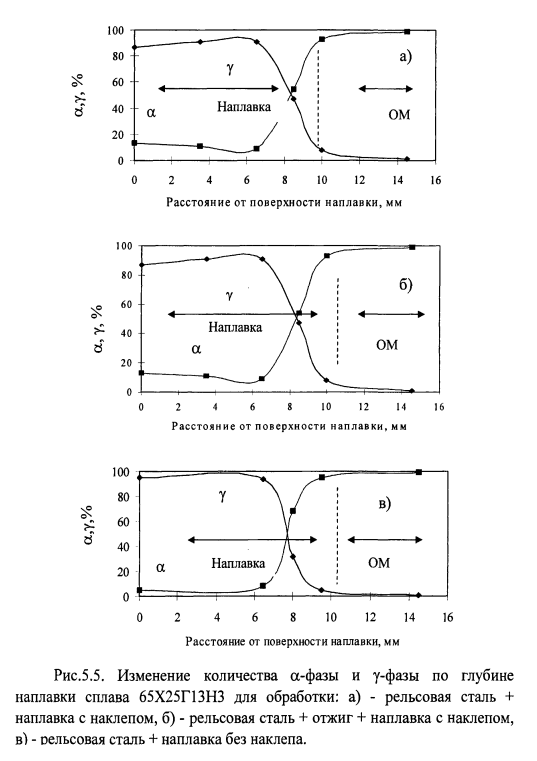
В наплавленном слое количество а- фазы больше в образце после обработки 1 и 2 , где исходной обработкой рельса перед наплавкой была закалка и отжиг с последующим наклепом, чем после обработки 3. а-фаза на поверхности наплавки, по-видимому, возникает как результат у-а превращения при наклепе – конечной обработке наплавленного слоя.
На рис. 5.6. представлены зависимости периода кристаллической решетки у-фазы по глубине наплавки. Для обработок 1 и 2 они аналогичны.
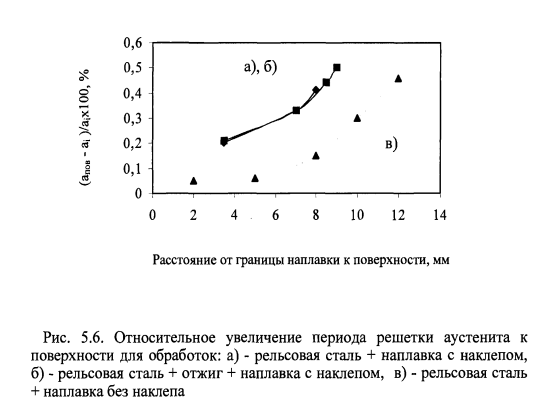
Период решетки легированной у-фазы на поверхности наплавки выше и монотонно уменьшается с увеличением глубины наплавленного слоя. Напротив, как следует из измерения периода решетки а-фазы его значение возрастает от ”тела ” рельсовой стали к границе наплавки. Так, на глубине й=14.5мм, где наплавки нет, аа=2.8606 А, а при 11=10 мм – вблизи границы наплавки аа=2.862 А.
Как известно, при растворении легирующих элементов Сг, №, Мп в мартенсите, феррите и аустените происходит увеличение периода кристаллической решетки. Соответственно – снижение их содержания свидетельствует об обеднении твердого раствора этими элементами.
Исследуемые образцы вырезаны из рельсовой стали имеют достаточно малые размеры, что исключает влияние макронапряжений, определяемых по смещению максимума интерференционных линий. Поэтому изменение значений периода кристаллической решетки по глубине наплавленного слоя, определенные по максимуму интерференционных линий (311) у-фазы и (211) а-фазы, свидетельствует об уменьшении содержания легирующих элементов в у-фазе и об обогащении а-фазы этими элементами.
Полученные данные позволяют считать, что при наплавке происходит диффузия легирующих элементов внутрь слоя, следовательно и в а-фазу у границы наплавленного слоя.
На рис. 5.7 представлена зависимость ширины интерференционных линий у-фазы (311)у по глубине наплавки на рельсовую сталь после обработок 1,2 и 3.
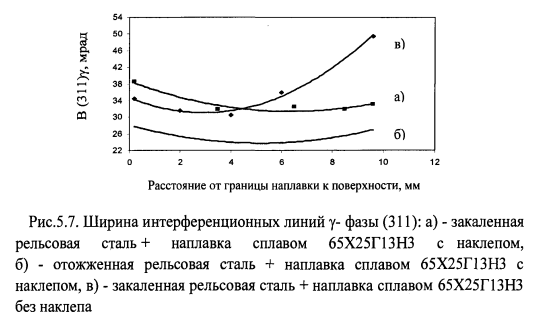
Отсюда следует, что уровень внутренних микронапряжений вблизи границы (ширина линий) намного ниже в наплавке после обработок 1 и 2, чем обработки 3. Однако, для обработок 1 и 2 характер изменения ширины линий, а следовательно, уровня внутренних микронапряжений одинаков.
На поверхности возникают высокие внутренние микронапряжения. По глубине слоя наплавки их средний уровень снижается, о чем свидетельствует уменьшение ширины линий (311)т. Причем оно не монотонно: следовательно с глубины 3,5-4 мм до границы слоя микронапряжения несколько повышаются, оставаясь значительно ниже их значений на поверхности.
Однако, при этом локальная концентрация остаточных микронапряжений (микронапряжений, уравновешивающихся в областях, на несколько порядков меньших размера зерна) в у-фазе возрастает по мере приближения к границе наплавки для обработки 1 (рис. 5.8). Тогда как локальные микронапряжения без наклепа снижаются к границе наплавленного слоя, что вероятно является их релаксации образованием микротрещин.
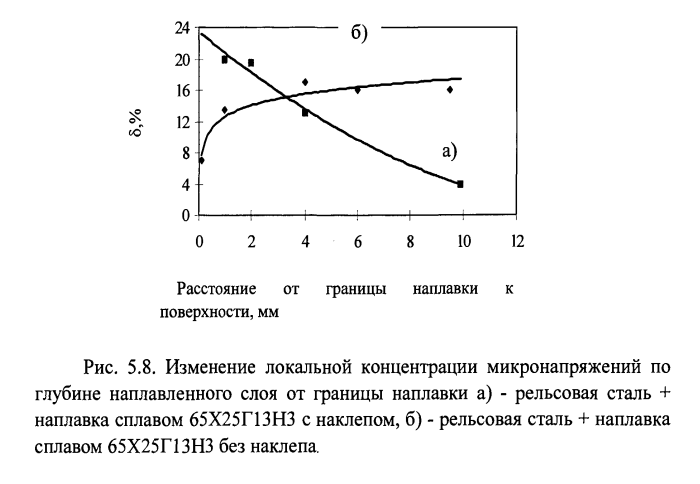
Это подтверждается металлографическими исследованиями поперечных шлифов, где видны микротрещины на границе наплавленного слоя без ударного наклепа (рис. 5.9).
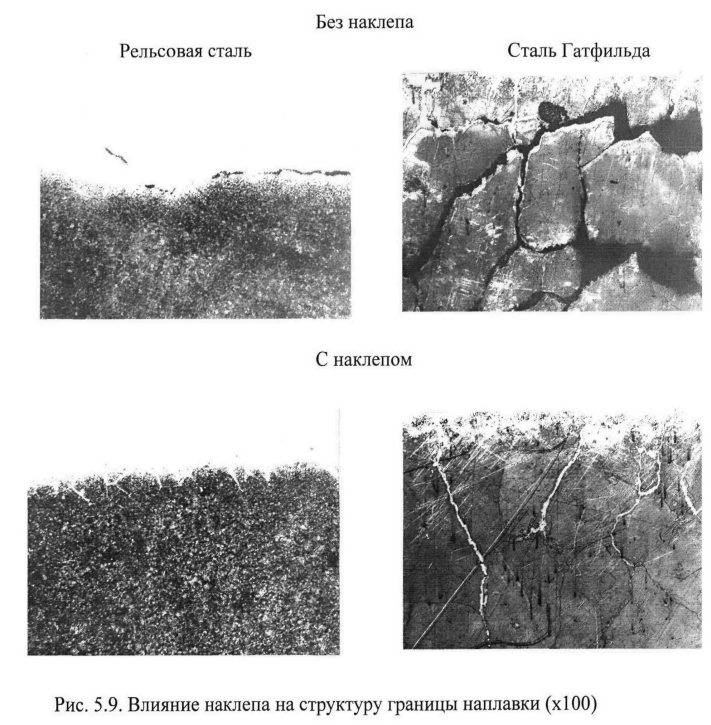
Таким образом, наиболее высокая локальная концентрация микронапряжений после наклепа имеет место на границе наплавки, а средний уровень микронапряжений здесь ниже, чем в середине и на поверхности наплавки. Это значит, что микронапряжения, хотя и не велики, но распределены неоднородно. Однако, а- твердый раствор (феррит) на границе должен быть более прочным, чем в ”теле” основного металла, так как обогащен легирующими элементами. Это должно снижать вероятность хрупкого разрушения.
Исходя из ширины рентгеновских интерференционных линий внутренние микронапряжения в а-фазе ниже чем в у-фазе (рис. 5.7 и рис. 5.10, 5.11). На поверхности после обработки 1 и 2 микронапряжения в а- фазе меньше, чем в более глубоком слое, что по-видимому, связано с их релаксацией при наклепе последнего наплавленного слоя и отсутствия новых наплавленных слоев. По глубине слоя микронапряжения в а- фазе монотонно снижаются к границе слоя, и в теле основного металла практически отсутствуют (рис. 5.10 и 5.11).
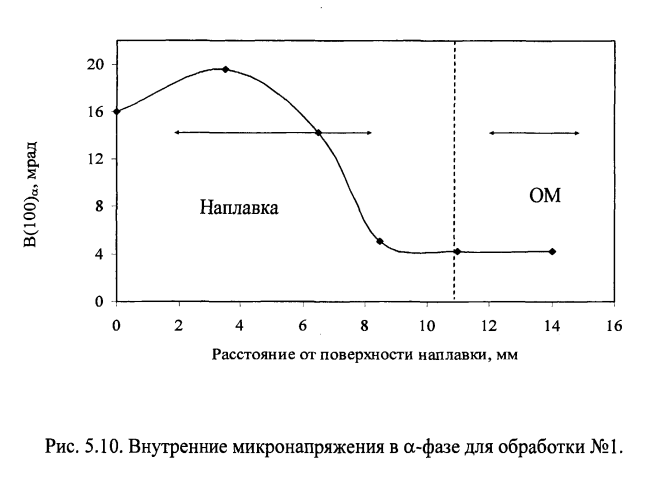
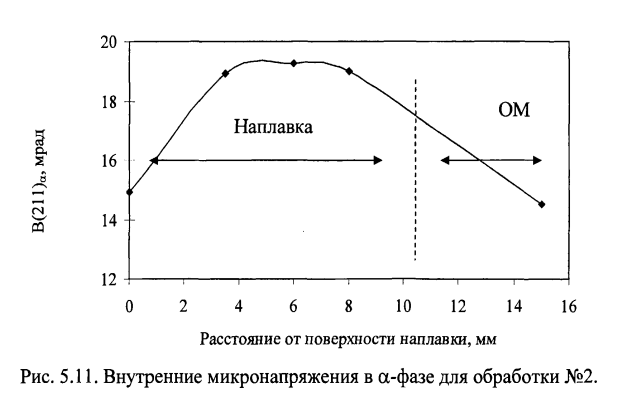
Таким образом, в результате наплавки на рельс возникает слой, структурное состояние которого неоднородно по его глубине. Характер изменения по сечению одинаков для исследованных обработок:
- Наплавленный слой имеет двухфазную структуру – в основном у-фазу + небольшое количество а- фазы;
- При наплавке возникают высокие внутренние микронапряжения в у-фазе. Они снижаются по глубине слоя, в случае обработки с наклепом, тогда как возрастают без наклепа. Средний уровень микронапряжений в а- фазе снижается к границе слоя, и в теле основного металла отсутствуют;
- Происходит диффузия легирующих элементов вглубь слоя и дополнительное легирование а-фазы (феррита) на границе слоя, что должно уменьшать вероятность зарождение трещин;
- При соблюдении одинаковых прочих условий обработки рельсовой стали, включающие проведение наплавки и завершающей ударной обработки, исходная термообработка по полученным данным, оказывает влияние на уровень внутренних микронапряжений в наплавленном слое и имеет значение для выбора наиболее технологичных режимов наплавки. При исходном состоянии отожженной рельсовой стали – уровень микронапряжений в слое получается ниже, чем при наплавке на закаленную рельсовую сталь. Поэтому этот режим предпочтителен для обеспечения более оптимальных эксплуатационных характеристик рельсовой стали с наплавкой.
Таким образом, отличие варианта наплавки без наклепа от режимов с наклепом, главным образом состоит в напряженном состоянии полученного слоя: создается высокий уровень микронапряжений на границе наплавки, что представляет опасность преждевременного разрушения.
Введение теплого наклепа наплавленного слоя приводит к релаксации микронапряжений у его границы за счет у->а превращения.
Исследование состава и механических свойств при плазменной наплавке на сталь Гатфильда хромомарганцевого порошкового сплава
Эксперименты проводились с целью определения влияния проковки на уменьшение остаточных напряжений и продольной деформации наплавленного образца. Наплавка всех образцов проводилась на усовиках крестовины, наплавляли по два слоя по следующему режиму: ток наплавки 1=190 А ( для 1-го слоя ), 180 А ( для 2-го слоя ), 11=40 В, расход аргона О =1 м3/ч, поперечная скорость движения плазмотрона Упопер.=20мм/сек, продольная скорость движения плазмотрона Упрод.=10мм/сек, расход порошка 0,3 г/сек. Толщина каждого наплавленного слоя составила 2,5 мм и длина 600 мм. Были выполнены следующие эксперименты: а) наплавка без ударного наклепа, б) наплавка с ударным наклепом и энергией удара 5 Дж и в) наплавка с ударным наклепом и энергией удара 10 Дж. В каждом случае проводили измерение стрелы прогиба, которая оказалась равной 1,41 мм, 1,28 мм 1,20 мм соответственно. Таким образом проковка снизила величину прогиба наплавки, проведенной с проковкой 5 Дж на 0,13 мм, а проведенной с проковкой 10 Дж на 0,21.
Проковка по своему действию противоположна наплавке. Она вызывает деформацию растяжения и напряжения сжатия, которые могут в 105
некоторой степени уравновесить напряжения растяжения. Кроме того, проковка повышает плотность наплавленного металла, залечивает мелкие трещины и закрывает поры. Для повышения эффекта проковки ее необходимо вести с применением энергии удара не менее 10 Дж. Другим путем повышения эффективности проковки является использование высокой температуры наплавленного слоя, что значительно облегчает работу деформации. Поэтому необходимо стремиться приблизить по времени процесс проковки наплавленного слоя к моменту его наплавки.
Наплавка проводилась порошком 65Х25Г13НЗ на реальный образец, вырезанного из новой крестовины, в несколько слоев, с промежуточной абразивной зачисткой между слоями и ударным наклепом каждого наплавленного слоя для снятия остаточных напряжений. При этом общая толщина наплавки составила 22 мм. С целью определения механических свойств металла основы, наплавки и переходной области (границы) были проведены комплексные механические испытания образцов, вырезанных в продольных и в поперечных направлениях.
Химический состав основного металла (ОМ) крестовины и наплавленного металла (НМ) представлен в таблице 5.3.
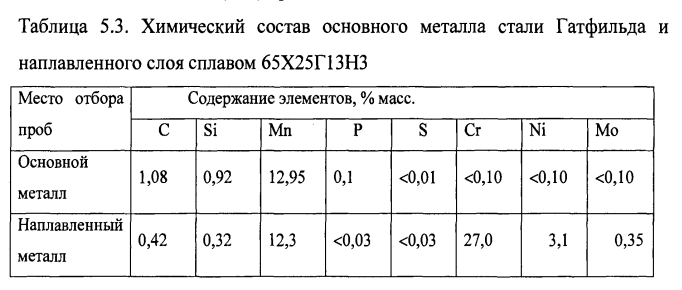
Твердость.
Измерения значений твердости НКС проводили на глубину наплавленного слоя до 20 мм и основного металла до 30 мм. Как видно из рис. 5.12. на глубине 30 мм ОМ твердость составляет 9-12 НК.С. По мере приближения к границе твердость возрастает до 17-20 НКС на глубине ~ 2 мм. На границе уровень твердости резко возрастает и составляет 32-34 НКС. Далее в наплавленном металле от границы и до глубины 20 мм уровень твердости стабилен и составляет 32-35 НКС.
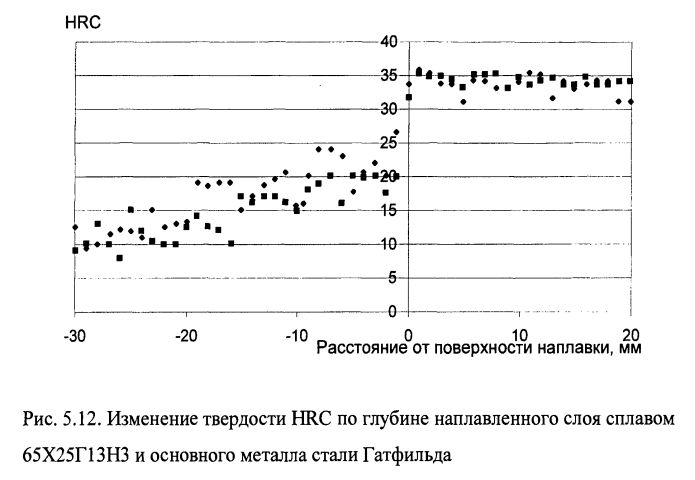
Механические свойства при растяжении
Как видно из представленной на рис. 5.13. диаграммы растяжения продольных образцов из наплавленного металла (НМ), переходной зоны (ГР) и основного металла (ОМ) образец из НМ разрушился при наибольшей нагрузке равной приблизительно 2900 кг, в то время как, для разрушения образцов из ГР и ОМ потребовалось приложить нагрузку в 1,7-2,0 раза меньшую.
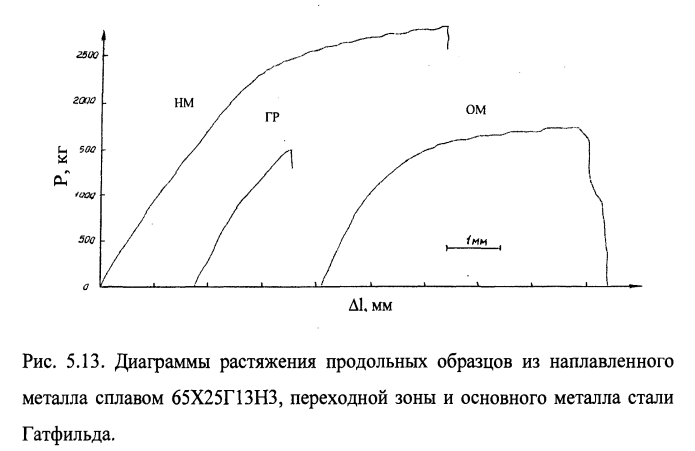
Следует отметить, что характер разрушения у всех образцов был хрупким. На рис. 5.14 приведены диаграммы растяжения поперечных образцов из наплавленного и основного металла сердечника.
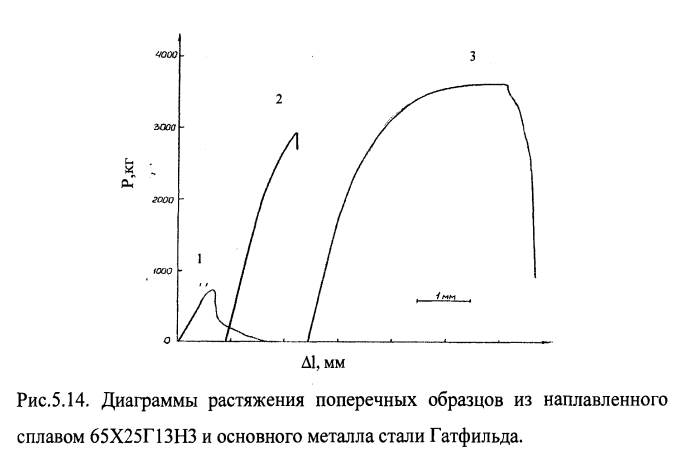
Образец 1 разрушился уже при нагрузке ~ 750 кг. Разрушение произошло по зоне сплавления и носило вязкий характер. Разрушение образца 2 имело место при значительно более высокой нагрузке ~ 3000 кг, прошло по наплавленному металлу и было хрупким. Наибольшую нагрузку выдержал образец 3. Разрушающая нагрузка составила ~3700 кг, образец разрушился по основному металлу хрупко.
На рис. 5.15 представлены механические свойства металла основы, наплавки и переходной зоны. На продольных образцах наилучшие свойства показал НМ. Временное сопротивление составило 951 Н/мм2, при уровне пластичности 5= 9,1%, механические свойства ГР значительно ниже: при пределе прочности 501 Н/мм2 и а0,2 = 348 Н/мм2 удлинение составило всего 1,6%. Наблюдался большой разброс значений ав от образца к образцу: от 433 до 553 Н/мм2
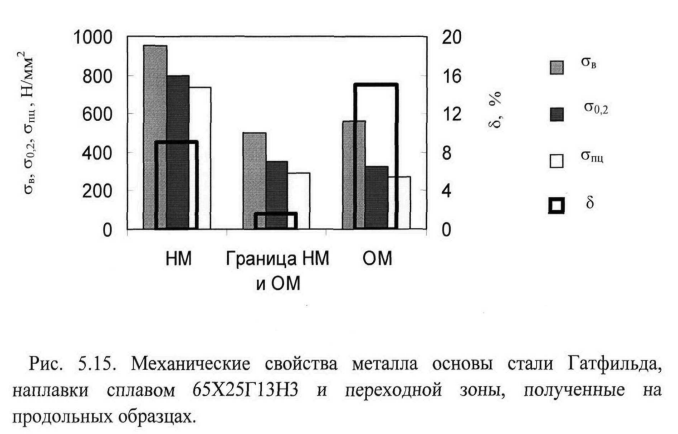
Прочностные свойства ОМ находятся практически на уровне ГР. Если ов = 558 Н/мм2 несколько выше, чем у ГР, то <т0,2= 324 Н/мм2 – ниже. Однако, пластичность ОМ весьма высока и составляет 6= 15,0%.
Однако, по уровню прочности ов и пластичности 5 основной металл несколько уступает обычно наблюдаемым свойствам литой стали 110Г13Л – ов = 800-1000 Н/мм2, § = 25-35%.
Испытания поперечных образцов, показали, что они обладают самыми низкими прочностными свойствами: временное сопротивление составляет всего 376 Н/мм2 при относительном удлинении 5 = 3,6%.
Ударная вязкость
Результаты испытаний на ударную вязкость представлены в табл. 5.4. Ударная вязкость образцов НМ, как взятого непосредственно у границы, так и на расстоянии 10 мм, близка по значению : 8,7 Дж/см2 и 7,5 Дж/см2. Излом хрупкий, зона вязкой составляющей в изломе В=0%. Следует отметить, что в изломе вскрылись мелкие округлые поры с неокисленной поверхностью. Испытания ОМ дали прямо противоположные результаты. КСИ образца, находящегося непосредственно у границы, составила 143 Дж/см2, а у образца, удаленного от границы на 10 мм, КСИ=212 Дж/см2, что в 18-25 раз превышает значение КСИ наплавленного металла. Характер излома – вязкий. Доля вязкой составляющей в изломе В составляет 100%.
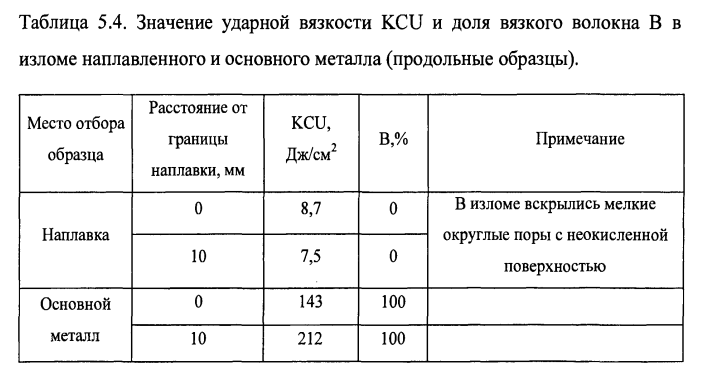
Механические свойства при испытании на статический изгиб
На рис. 5.16. представлена диаграмма испытаний на статический изгиб продольных образцов с надрезом из НМ и ОМ, взятых непосредственно у границы и с расстояния 10 мм от нее. Из рис. 5.16. видно, что разрушение обоих образцов из НМ носило хрупкий характер, тогда как ОМ показал высокие пластические свойства.
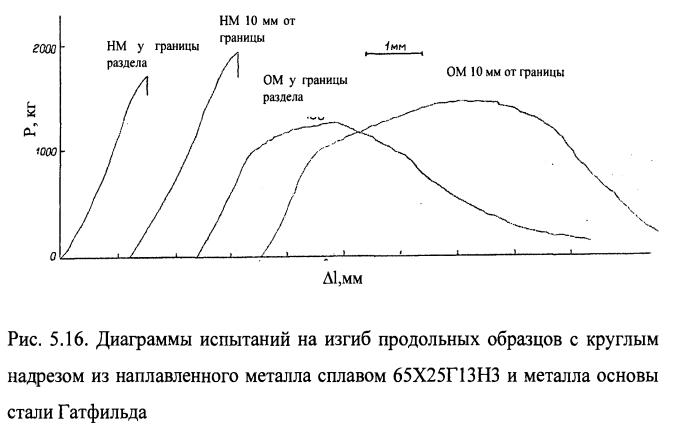
В таблице 5.5. приведены механические свойства при испытании образцов с надрезом.
Так, если разрушающее напряжение для образцов из НМ составляет 1612 и 1731 Н/мм2 соответственно, то для образцов из ОМ оно в 1,4 раза ниже. Пластические же свойства образцов из ОМ в 11-14 раз выше, чем у НМ. Причем Гпл образца, удаленного от границы на 10 мм, в 2 раза выше, чем у образца, находящегося непосредственно у границы. Такая же тенденция наблюдается и у образцов от НМ. Работа зарождения трещины Аз образцов НМ низкая, особенно у образца вблизи от границы -1,7 Дж/см2 . При удалении от границы наплавки А3 НМ возрастает до 6,5 Дж/см2 . Суммарная работа разрушения у обоих образцов ОМ близка по значениям (48,8 и 52,7 Дж/см2) и в 2-3 раза превышает А^ образцов от НМ.
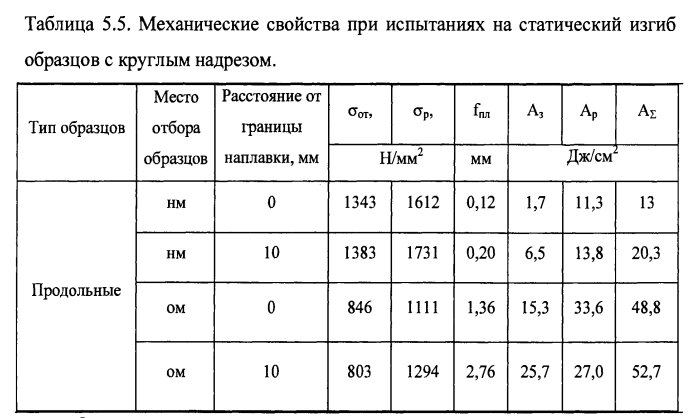
Однако, и в этом случае удаление от границы наплавки повышает работу зарождения трещины от 15,3 до 25,7 Дж/см2.
Более низкие значения сопротивления зарождению трещины вблизи границы наплавки, по-видимому, являются следствием изменения состава и структуры металла в результате оплавления поверхности, а также образованием дефектов, связанных с процессом наплавки.
На рис. 5.17. представлены диаграммы испытаний на изгиб поперечных образцов без надреза. Видно, что пластичность образца №1 значительно выше, чем №2.
В таблице 5.6 представлены механические свойства образцов: Гпл образца № 1 в 7,3 раза превышает значение этого показателя у № 2. Следует отметить, что при испытаниях в изломе образца № 2 вскрылся окисленный участок на границе ОМ-НМ.
Наибольшее разрушающее напряжение у образца № 1 -1170 Н/мм2 при самом высоком значении суммарной работы разрушения Ау = 32,7 Дж/см2.
Наименьшей А^ обладает образец № 2, т.к. работа зарождения трещины в данном случае равна всего А3= 2,5 Дж/см2.
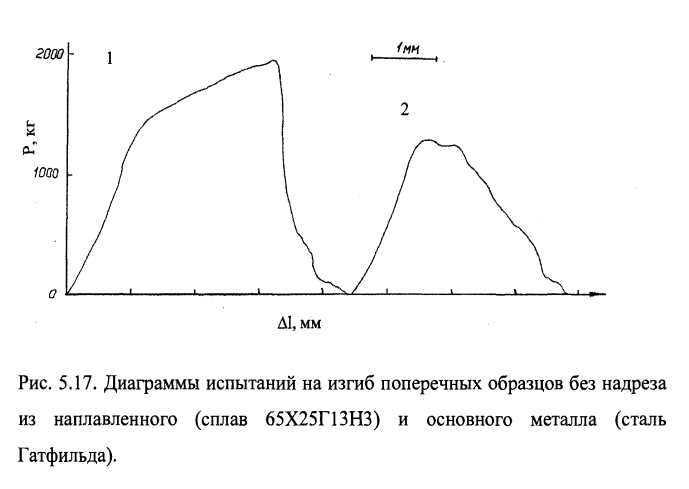
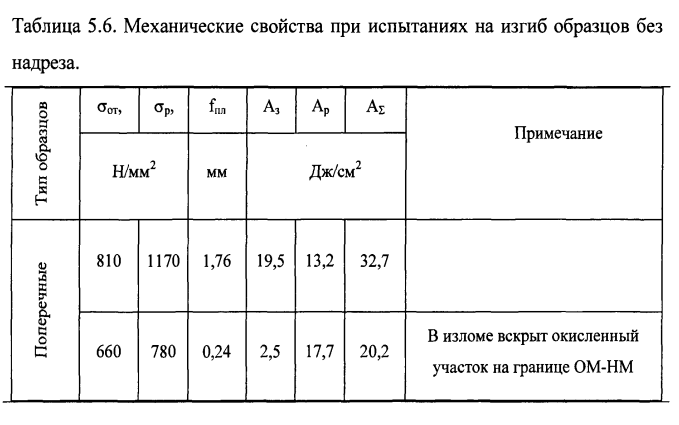
Таким образом, разброс значений характеристик пластичности и сопротивления зарождению трещины наплавленного и основного металла зависит от расстояния от границы наплавки и металла основы и обусловлен наличием дефектов в области переходного слоя.
Фрактографические исследования поверхности разрушения. Оценка микроструктуры основного металла, наплавки и переходной области при плазменной наплавке хромомарганцовистого сплава на сталь Гатфильда. Механизм образования трещин на поверхности области стыка наплавленного слоя металла основы.
Фрактографические исследования поверхности разрушения.
Разрушение металла основы литой стали 100Г13Л происходит по хрупкому межзеренному механизму с участками вязкого разрушения (рис. 5.18). В изломе наблюдаются крупные фасетки до 500-700 мкм межзеренного скола. Рельеф поверхности излома сильно выражен и изменяется в пределах до 1-1,5 мм.
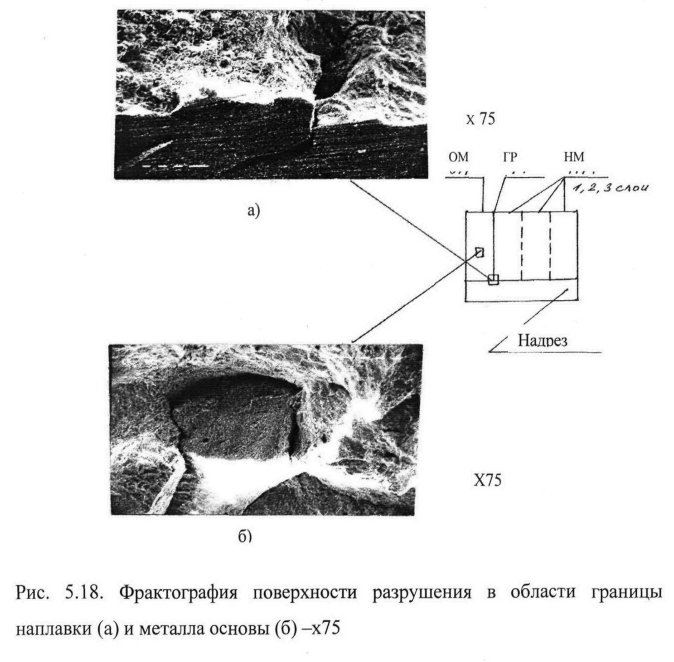
Поверхность разрушения в области 1-го наплавленного слоя также носит смешанный характер – межзеренные фасетки хрупкого скола чередуются с вязкими участками (рис. 5.19). Строение излома более дисперсное, чем основного металла, что отражает кристаллизацию наплавки в условиях больших скоростей охлаждения. Видны вторичные трещины, характерные для межзереного разрушения (рис. 5.19 б)).
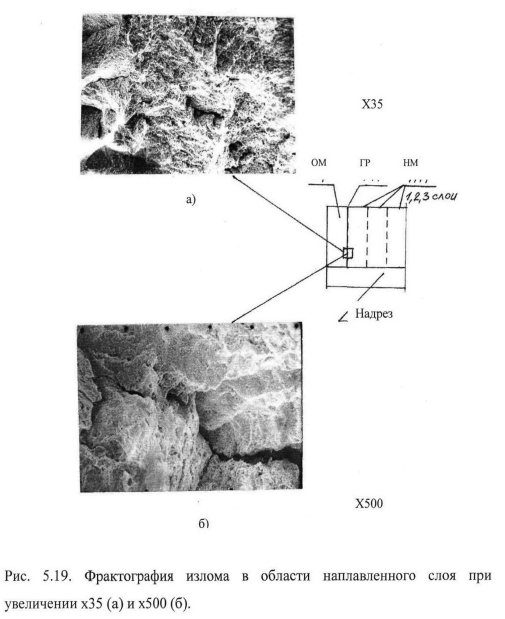
Излом в условиях 2-го и 3-го слоев наплавки такой же как и 1-го слоя. Однако, в области 2-го слоя доля вязкого разрушения существенно меньше (рис. 5.20 а)). Встречаются крупные до 100-150 мкм хрупкоразрушенные неметаллические включения, которые располагаются вблизи границ между наплавленными слоями (рис. 5.18 б))
По данным микрорентгеноспектрального анализа в состав их входит хром, что свидетельствует об образовании в процессе наплавки окислов сложного состава.
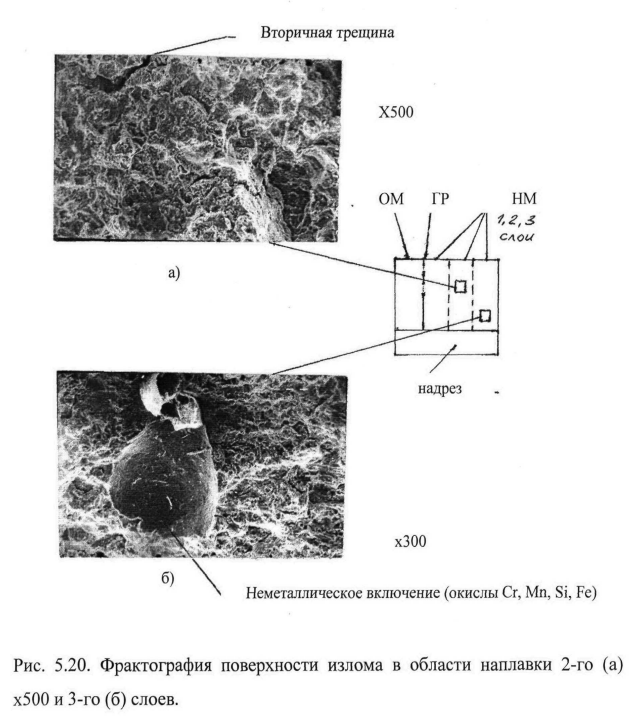
На границе между наплавленными слоями встречаются дефекты типа пор, иногда заполненные неметаллическими включениями сложного состава (рис.5.21). Как показал микрорентгеноспектральный анализ в состав таких включений входят также марганец, кремний и хром.
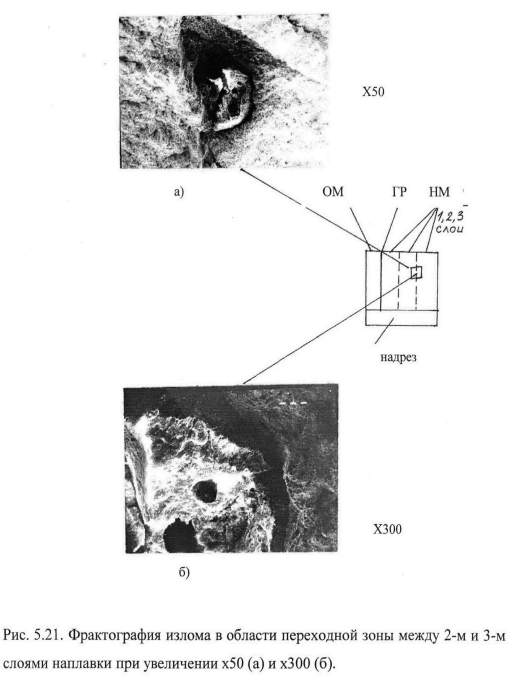
Таким образом, более высокий комплекс свойств наплавленного металла связан с дисперсной литой структурой, образующейся при охлаждении наплавки. Наблюдаемые различия в строении излома наплавленных слоев, вероятно, обусловлены различными условиями охлаждения и наклепа при послойном наплавлении.
Крупные дефекты типа пор и неметаллических включений на границах между наплавкой и основным металлом и между наплавленными слоями является причиной неоднородностей механических свойств и сопротивления разрушению на поперечных образцах.
Оценка микроструктуры основного металла стали Гатфильда, наплавки сплавом 65Х25Г13НЗ и переходной области.
Исследование микроструктуры проводили на поперечных и продольных шлифах, вырезанных из сердечника крестовины в разных участках. Выявление микроструктуры основного металла проводили путем травления в 10% НС1, а металла наплавки в 3% НМО3.
Микроструктура металла основы – стали 110Г13Л представляет собой аустенит с крупными зернами литой структуры (рис. 5.22, 5.23.). Размер зерен литой структуры стали Гатфильда составляет 400-1500 мкм.
Микроструктура наплавленного металла существенно более мелкозернистая (рис. 5.24). Отмечается большая неоднородность этой структуры по слоям наплавленного металла. Так, вблизи поверхности раздела ОМ-НМ структура с ярковыраженными признаками литого металла. Видны дендритные кристаллы и крупные зерна (рис.5.24). Далее следует микроструктура с рекристаллизованной структурой. Размер зерен аустенита в этой области наплавки соответствует 30-100 мкм. На границе раздела между наплавленными слоями видны дефекты в виде пор и неметаллических включений. Крупная пора на границе между наплавленными слоями представлена на рис. 5.25. Ее размер достигает 100-300 мкм. Встречаются поры и большего размера до 400-600 мкм.
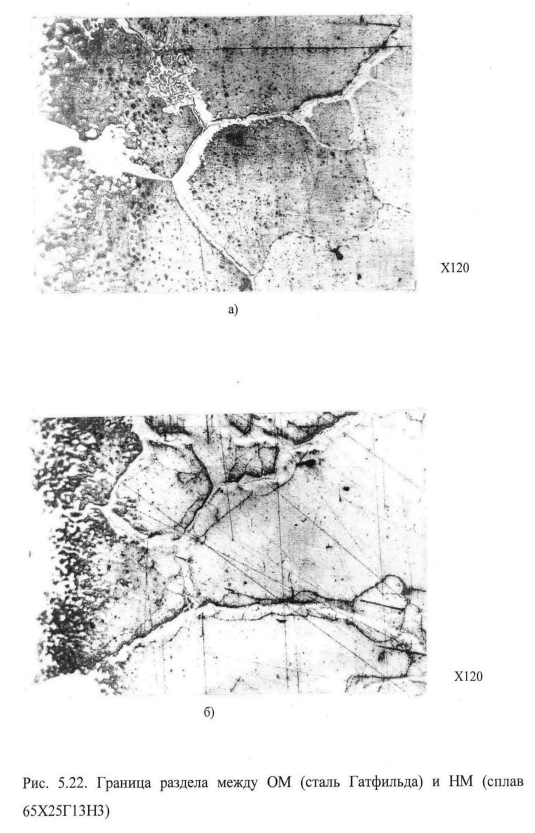
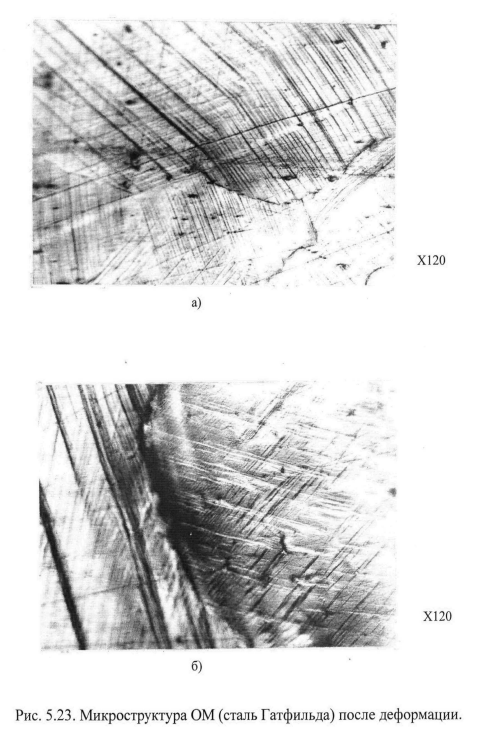

После пластической деформации в микроструктуре основного металла видны двойники и 8-фаза, закономерно располагающаяся в пределах одного зерна литой структуры (рис. 5.23).
Наибольший интерес представляет граница раздела НМ-ОМ (рис. 5.22). На самой границе обнаружен слой смешанной структуры ОМ и НМ, образовавшийся в результате перемешивания расплавленного металла основы и наплавки. Толщина этого слоя составляет 150-500 мкм. Хорошо виден дефект оплавления границ аустенитных зерен в поверхностных слоях основного металла и затекания в них жидкого расплава наплавки. Такие “ручьи” расплавленного металла наплавки иногда достигают размера нескольких зерен литой структуры металла основы.
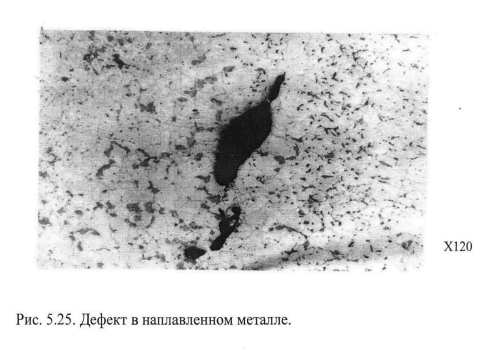
Это, с одной стороны, повышает эффективность сцепления наплавленного слоя с подложкой, поскольку “ручеистое” межзереное внедрение металла наплавки в основной металл не дает возможности отслоения его от матрицы. Это, кстати говоря, объясняет тот факт, что при растяжении поперечных образцов разрушение не всегда происходит строго по границе раздела ОМ-НМ, а в силу случайных причин может быть локализовано в наплавке или металле основы.
С другой стороны, такое внедрение в металл основы расплава наплавки должно упрочнять приповерхностные слои металла основы и охрупчивать их, что также находит подтверждение при испытаниях образцов, вырезанных на разных расстояниях от границы раздела ОМ-НМ. Чем ближе образцы к поверхности раздела, тем меньше пластичность при изгибе и работа зарождения трещины.
О механизме образования трещин на поверхности области стыка наплавленного слоя и металла основы.
На рис. 5.26. представлена панорама трещины, обнаруженной в конце наплавки. Эта трещина разрушает небольшой по толщине слой (непротравленный на рис. 5.26) металла наплавки и распространяется в металл основы по межзеренному механизму. Причем распространение ее происходит по границам зерен основного металла, практически не содержащим следов затекшего расплава наплавки. Не исключено, что такие границы являются наиболее слабыми с точки зрения развития трещины, где под воздействием высоких остаточных растягивающих термических напряжений в месте окончания наплавки происходит растрескивание.
Следует отметить также, что на поверхности наплавленного металла в месте образования трещины наблюдается повышенная загрязненность наплавленного металла неметаллическими включениями.
Таким образом, наблюдаемая в области окончания процесса наплавки хрупкая трещина обладает рядом характеристик, в том числе необычных особенностей:
- трещина интеркристаллитная;
- трещина пересекает наплавку, зону конвективного перемешивания жидкого расплава наплавки и металла основы, область внутреннего окисления металла основы и распространяется по границам литых кристаллитов металла основы;
- ширина русла трещины возрастает не от вершины к поверхности, как это должно было бы быть при зарождении трещины на поверхности и распространении ее внутрь металла, а наоборот, по мере углубления ее в металл основы;
- вблизи поверхности наплавки у русла трещины видны скопления неметаллических включений.
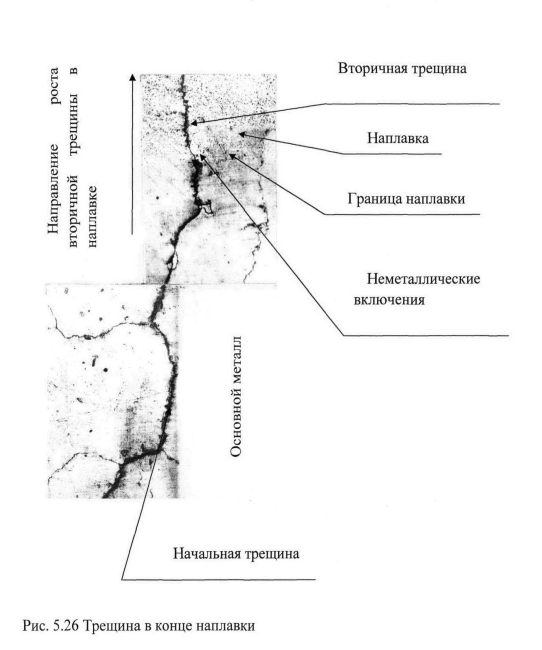
Исходя из перечисленных особенностей этой трещины можно предположить, что зарождение ее происходило не на поверхности наплавки, а внутри металла. Тогда один из наиболее вероятных механизмов возникновения трещины в конце наплавки можно представить следующим образом.
При не очень тщательной зачистке поверхности крестовины перед наплавкой, особенно в области, где процесс наплавки должен быть завершен, окалина может быть частично не снята, в частности, в локальных местах дефектов поверхности и выхода границ зерен.
Поскольку окислы Ре, Мп, 8т, входящие в состав окалины металла основы, являются более тугоплавкими, то при оплавлении границ зерен литой структуры они могут препятствовать проникновению жидкого расплава наплавки вдоль границ, выходящих на поверхность металла основы (рис. 5.26). Кстати, ширина русла внутренней трещины в металле основы близка к ширине оплавленных и заполненных жидким расплавом наплавки границ на соседних участках. Это приводит к эффекту закупоривания границ зерен снаружи. Оплавленные же границы в результате усадочных процессов не залечиваются при быстром остывании (малая толщина жидкого расплава) и служат готовыми внутренними трещинами.
В пользу этого механизма свидетельствует то, что наблюдаемая трещина раскрыта в большей степени не у поверхности, а в конце, в толще металла основы. Создается впечатление, что границы зерен в результате оплавления раскрылись под поверхностью основного металла и вызвали долом более прочного наплавленного слоя под воздействием остаточных напряжений.
Иначе говоря, развитие трещины происходило не снаружи, с поверхности наплавки, как можно было ожидать, а изнутри из оплавленной и не заросшей жидким расплавом интеркристаллитной трещины в металле основы.
В пользу этого предположения говорит и наблюдаемое у поверхности наплавки в месте нахождения трещины скопление неметаллических включений, которые, по-видимому, частично всплыли в жидкой фазе, оторвавшись от поверхности металла основы.
Рентгенографический анализ фазового состава наплавки и основного металла.
Объектами исследования были шлифы, изготовленные по сечению наплавленного металла из стали ПР-65Х25Г13НЗ на сталь 110Г13. Задачами исследования были оценка фазового состава и напряженного состояния стали.
Из анализа расчитанных межплоскостных расстояний (б=А/28т0тах), где б- межплоскостное расстояние; X – длина волны рентгеновского излучения; 0тах – угол Вульфа-Бреггов следует:
- дифрактограммы с 20mах ~ 54,7° и 49,3° – соответственно принадлежат интерференционным линиям у-фазы (111)« и (Ш)р. Интенсивность последней в 6 раз меньше (111)а;
- дифрактограмма с 20mах ~ 57,4° относится к е-мартенситу;
- дифрактограммы с 20mах ~ 50,9° и 56,3° соответствуют линиям (200)а цементиту Ре3С и карбиду Сг23С (511)а.
Таким образом, фазовый состав наплавки аустенит + е-мартенсит (табл. 5.7). Причем доля е-мартенсита незначительна в поверхностном слое до 15 мм и содержит от 7 до 9%.
Кроме того, в поверхностном наплавленном слое 3 и 7 мм наблюдается небольшое количество карбидов – карбиды Сг23С и Ре3С. Их дисперсность возрастает по глубине наплавки (табл. 5.7). Судя по ширине линий (511) хромистого карбида и (200) цементита из уравнения Селякова-Шелера :
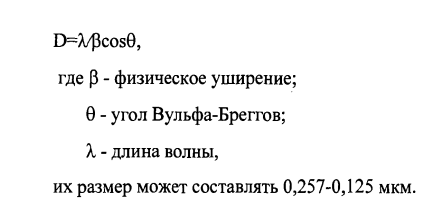
В области близкой к границе наплавки на расстоянии 19-22 мм от поверхности наблюдается от 20 до 25 % 8-мартенсита. А на границе наплавки и основного металла до 28-30% этой фазы.

Однако, под наплавленным слоем ниже его на 3-5 мм количество е- мартенсита опять незначительно, менее 5%.
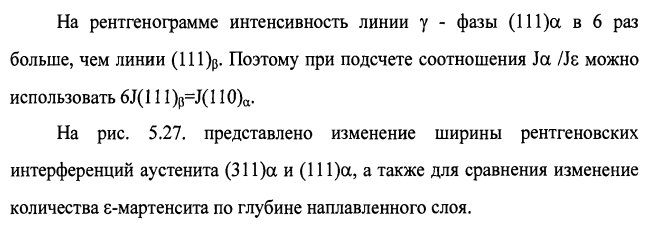
Из рис.5.27, следует, что по глубине слоя возникают внутренние микронапряжения. Необходимо подчеркнуть, что при этом наблюдается увеличение количества Е-мартенсита и резкое его возрастание у границы наплавленного слоя. Однако, на границе наплавленного слоя остаточные микронапряжения резко падают. При этом имеет место наибольшее количество е-мартенсита. Как известно, е-мартенсит – мартенсит с гексогональной решеткой – является хрупкой фазой и ее наличие в значительных количествах может вызвать охрупчивание стали, что подтверждается при испытаниях механических свойств.
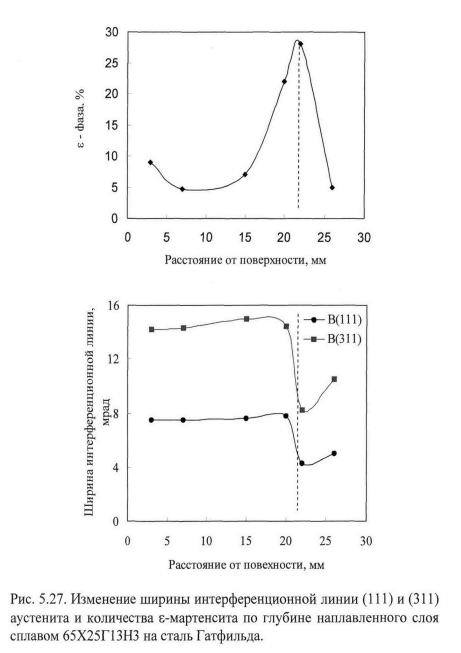
Резкое падение ширины линий, по-видимому, связано релаксацией микронапряжений за счет фазового превращения. Образование е-мартенсита, возрастание его количества, особенно в области границы наплавки, является следствием наклепа металла первого наплавленного слоя.
Таким образом, фазовый состав наплавленного слоя неоднородный по глубине, что, по-видимому, является следствием особенностей деформации слоев при ударной обработке и температурно-скоростных процессов нагрева и охлаждения при послойной наплавке.
Для оценки влияния наклепа на количество е-фазы исследовали влияние степени деформации на фазовый состав металла основы и наплавки. Деформация растяжением на 5 % приводит к некоторому возрастанию количества е-фазы в металле основы от 9,7 до 12% (табл. 5.8.). При этом немного увеличивается ширина рентгеновской линии (111) аустенита.
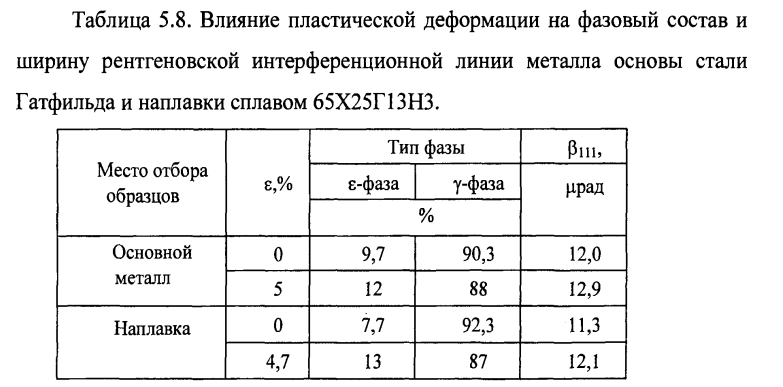
Деформация наплавленного металла на 4,7 % приводит к большому увеличению количества е-фазы от 7,7 до 13%, при также некотором 129 возрастании ширины рентгеновской линии (110) аустенита.
Таким образом, увеличение е-фазы в ближайших к границе наплавленных слоях связано с остаточными микронапряжениями и ударным наклепом после нанесения наплавленного слоя.
Полученные результаты позволяют заключить:
- проведенное комплексное исследование состава, структуры, механических свойств и сопротивления разрушению металла наплавки из стали 65Х25ПЗНЗ на рельсовую сталь и литую железнодорожную крестовину из стали 110Г13Л, показало, что прочность и твердость металла наплавки почти в 2 раза выше, чем металла основы, а пластичность ниже; прочность сцепления наплавки с основным металлом несколько ниже прочности металла основы, что является следствием влияния дефектов на границе раздела;
- разработан способ релаксационной обработки, заключающийся в ударном наклепе, синхронном с процессом наплавки, приводящем к фазовому у->а превращению и снижению в результате этого остаточных напряжений, возникающих при наплавке;
- показана принципиальная возможность изготовления биметаллической крестовины на основе рельсовой стали с наплавкой хромомарганцевого сплава в участках, подверженных наибольшему износу;
- показано, что наиболее предпочтительным технологическим вариантом наплавки на рельсовую сталь является наплавка на предварительно отожженную или горячекатаную рельсовую сталь;
- установлена зависимость пластичности и сопротивления зарождению трещины от расстояния от границы раздела между основным металлом и наплавкой; удаление от границы повышает пластичность и работу зарождения трещины, что является следствием влияния дефектов в переходной области;
- показано, что фазовый состав наплавки на сталь Гатфильда неоднородный по слоям: вблизи границы раздела у-фаза и 8-фаза (мартенсит), у поверхности наплавки кроме того обнаружены карбиды Сг2зС6 и ГезС;
- остаточные внутренние микронапряжения возрастают от поверхности наплавки к границе наплавленного слоя; на самой границе наблюдается резкое уменьшение микронапряжений и возрастание до 30 % 8-фазы, что является следствием их релаксации путем образования новой фазы в результате ударного наклепа;
- предложен механизм образования трещин на поверхности в области окончания процесса наплавки и перехода к металлу основы, заключающийся в образовании внутренней оплавленной интеркристаллитной трещины в металле основы, не залеченной жидким расплавом наплавки в результате “закупорки” её русла на поверхности остатками окалины, и хрупком доломе тонкого наплавленного слоя под воздействием остаточных напряжений.
Список литературы
- Шульте Ю.А. Электрометаллургия стального литья. М.: Металлургия, 1970. 224 с.
- Упрочнение взрывом рабочих органов горного оборудования/ А.М. Кудрявцев, В.С.Бухтин, Б.В. Захваткин и др.Кемерово: Кемеровское кн. Издательство, 1973. 40 с.
- Упрочнение стали Г13Л взрывом/ Р.З. Кац, Ф.П. Заманская, М.В. Генце и др.// Вестник машиностроения. 1966. № 3. С. 67-69.
- Исследование влияния исходной прочности стали Г13Л на ее свойства после упрочнения взрывом/ Е.Е. Зубков, Т.С. Тесленко, Т.М. Соболенко// Вестник ВНИИЖТ. 1982. № 2. С. 44-47.
- Упрочнение взрывом высокомарганцовистой стали/ А.А. Дерибас, Ф.И. Матвеенков, Т.М. Соболенко// Физика горения и взрыва. 1966. № 3 С.87-94. 66. Давыдов Н.Г., Ситников В.В. Свойства, производство и применение высокомарганцовистой стали. М.: Машиностроение, 1996. – 232 с.
- Крестовины, упрочненные методом науглероживания. ТУ // Путь и путевое хозяйство. 1994. № 2. С. 6-9.
- Кац. Р.З. Перспективные методы повышения износостойких железнодорожных крестовин // Вестник ВНИИЖТ № 2 1967. с. 42-43.
- Новиков И.И. Теория термической обработки металлов. – М.: Металлургия, 1978.-391 с.
- Медовар Б.И. Сварка жаропрочных аустенитных сталей и сплавов. М., Изд-во «Машиностроение», 1966.
- 3емзин В.Н., Петров Г.Л. и Брук Б.И. Новые достижения научно-исследовательских организаций в области сварки легированных сталей. – Сварочное производство. Под ред. Н.О. Окерблома. Лениздат, 1957.
- В.М.Кудинов, Н.В.Березина, В-Г. Петушков, К.Р. Мадей. Упрочнение взрывом наплавленного высокомарганцовистого металла. В журнале Автоматическая сварка. № 12.1977.С.21-24.
- Е.Н.Морозовская. Автоматическая наплавка высокомарганцовой аустенитной стали Г13. В журнале Автоматическая сварка. № 3,1961 с.32-41.
- Обобщение передового опыта тяжеловесного движения: вопросы взаимодействия колеса и рельса: Пер. с англ. / У. Дж.Харрис, С. М.Захаров, Дж. Ландгрен, X. Турне, В. Эберсен. М.: Интекст, 2002. . 408 с.
- Рутес В.С., Аскольдов В.И., Евтеев Д.П. и др. “Теория непрерывной разливки” М., “Металлургия”, 1971 г., 293 с.
- 3айт В. Диффузия в металлах. М., “Иностранная литература”, 1958 г., 378 с.
- Металловеление. Сталь. Справочник под ред. М. Л, Бернштейна, М., “Металлургия”, 1995 г, т1.1, с.97.