Сейчас ваша корзина пуста!
Создание установки. Наплавка и ресурсные испытания опытной партии железнодорожных крестовин из стали гатфильда
Цикл статей:
Глава 1 – Формирование структуры и свойств при плазменной наплавке износостойких покрытий на медь и высокоуглеродистую, марганцовистую стали
Глава 2 – Материлы и методы исследования
Глава 3 – Разработка конструкции плазмотрона с расширяющимся каналом сопла для плазменной наплавки
Глава 4 – Плазменное нанесение жароизносостойкого покрытия на медную основу
Установка плазменной наплавки железнодорожных крестовин разработана с целью совершенствования технологии восстановления изношенных участков литой части крестовины, образовавшихся в результате контактной усталости. Принципиальная схема и общий вид приведены на рис. 6.1 и рис. 6.2, соответственно. Установка может быть также использована для плазменной наплавки других промышленных деталей, имеющих как плоскую, так и цилиндрическую поверхности.
Установка плазменной наплавки железнодорожных крестовин обладает рядом существенных преимуществ, повышающих удобство её эксплуатации и обеспечивающих требуемое качество обрабатываемых поверхностей.
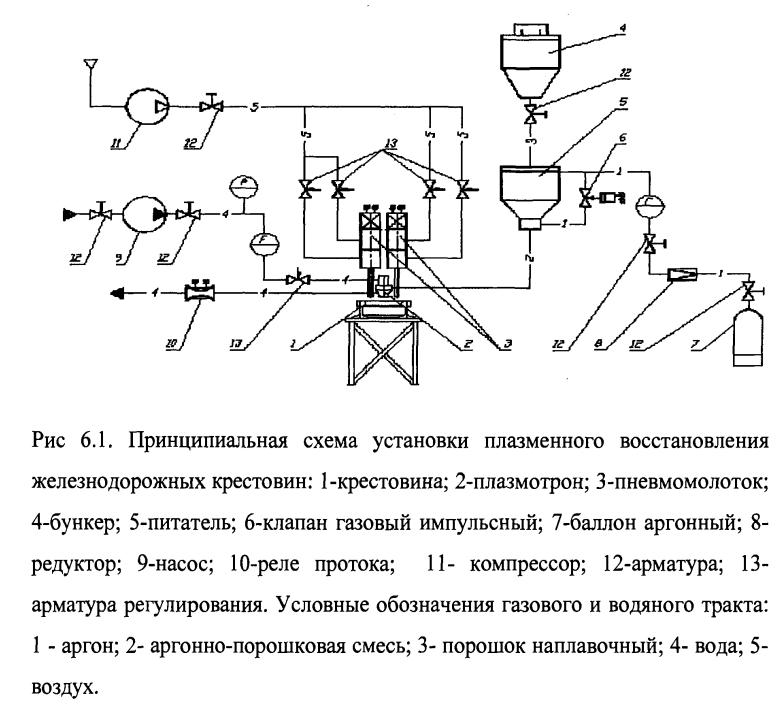
Важнейшими из них являются:
- наличие автоматического, с помощью ЭВМ, управления процессом наплавки при частичном сохранении возможности ручного ведения процесса;
- широкий диапазон и высокая точность регулирования расходов рабочих тел (аргона, порошка, воды), поперечной и продольной скорости наплавки, частоты и энергии удара, электрических параметров;
- наплавка широкой полосой за один проход (до 60 мм);
- сохранность данных о технологическом процессе.
Основные параметры установки Установленная мощность установки, кВА……………………………………………… 75
Производительность, шт/смену……………………… 1
Расход аргона, л/час не более…………………………. 2400
Расход воды, л/час не менее…………………………… 420
Скорость наплавки, м/час……………………………… 10
Ширина наплавляемой полосы, мм…………………. 80
Питание от сети трехфазного тока:
Напряжение, В…………………………………………….. 380
Частота, Гц………………………………………………….. 50
Сила наплавочного тока, А……………………………. 50-315
Давление воздуха атм, максимальное……………… 10
Основными узлами установки, обеспечивающими процесс наплавки, являются плазмотрон и механизм его перемещения, пневмомолоток, поворотный стол, ЭВМ.
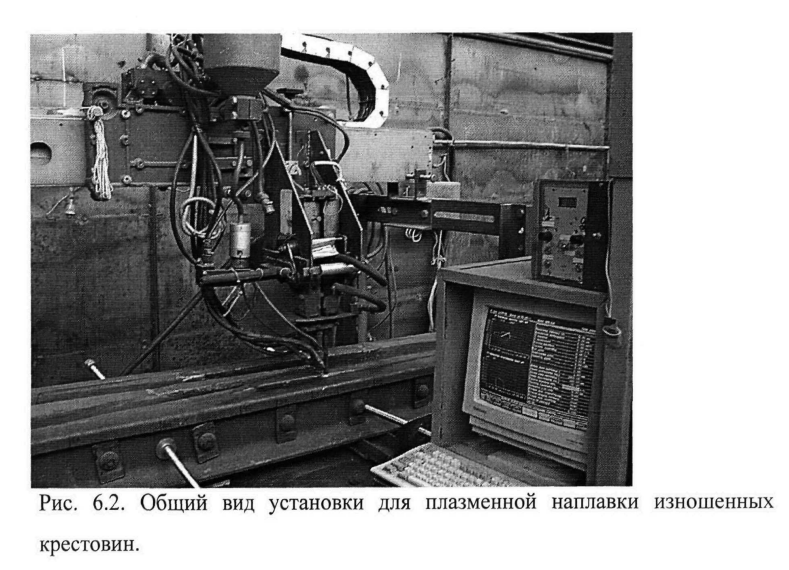
Система управления предназначена для управления процессом наплавки и проковки, а также для контроля за технологическим процессом, регистрации его параметров, сигнализации и обеспечения защит и блокировок.
Управляющая ЭВМ предназначена для расчета технологических режимов наплавки, управления контроллером ведения технологического режима и установкой в целом, задания технологических параметров процесса наплавки, измерения и отображения их в табличном и графическом виде на экране монитора, а также регистрации всей технологической информации по процессу наплавки в архиве. Для осуществления проковки разработан специальный пневматический молоток с энергией удара около 10 Дж, имеющий минимальные весогабаритные характеристики, с управлением частотой ударов от специального электронного устройства и с возможностью варьирования параметров (рабочее давление, ход поршня, масса движущихся частей).
Порядок работы на установке сводится к следующему. Оператор установки принимает зачищенную крестовину (рис. 6.3) внешним осмотром и устанавливает ее на специальный поворотный стол. Т.е. стол сделан таким образом, чтобы была возможность установить крестовину параллельно плоскости движения плазмотрона, для предотвращения стекания расплавленного порошка с зоны наплавки. Плазмотрон расположен на каретке, которая в свою очередь крепится за раму с винтом, тем самым обеспечивает продольное перемещение всей конструкции относительно неподвижной крестовины. Плазмотрон с внешним электродом (в качестве внешнего электрода служит крестовина) состоит из корпуса, в котором крепится сменный электрод с наконечником из торированного или лантанированного вольфрама, и водоохлаждаемого сопла с уплотняющими и электроизоляционными прокладками.
Подача порошка вместе с рабочим газом значительно упростила конструкцию плазмотрона и позволила уменьшить его внешний габаритный диаметр до 30 мм. Тем самым это позволило кроме плазмотрона на каретке разместить питатель, механизм поперечного перемещения плазмотрона и пневмомолоток, что обеспечило возможность проковки наплавленного слоя при температуре около 500°С, когда материал находится в пластичном состоянии.
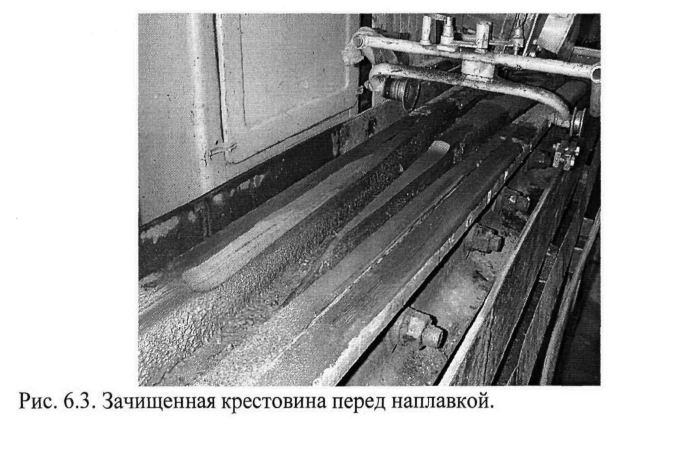
После установки крестовины на рабочем столе оператор по точкам задает траекторию будущей наплавки. Поскольку крестовина имеет сложную поверхность зоны наплавки – в разных сечениях ширина наплавки различна. В процессе наплавки необходимо менять амплитуду колебаний плазмотрона, так например поверхность сердечника крестовины имеет форму клина. С этой целью при наплавке плазмотрон (и вместе с ним и пневмомолоток) движется по следующей схеме (рис. 6.4).
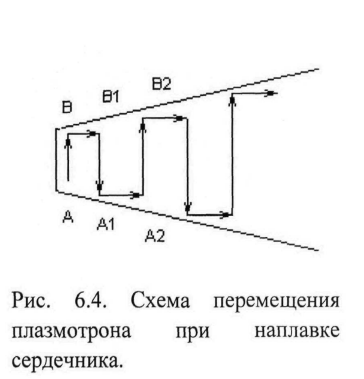
При перемещении из точки А в точку В на ширину изделия работает колебатель плазмотрона в поперечном направлении, затем – из точки В в точку В1 на величину шага наплавки работает каретка, перемещая плазмотрон вдоль изделия и т.д.
Затем оператор ставит плазмотрон в нулевую точку зоны наплавки и запускает процесс в автоматическом режиме от ЭВМ.
Включение плазмотрона в работу производится при повышенном расходе плазмообразующего газа. Первоначально осуществляется высоковольтный пробой между электродом и соплом и зажигается между ними вспомогательная дуга, которая потоком газа выдувается из сопла, обеспечивая условия зажигания основной дуги между катодом и анодом, после чего вспомогательная дуга автоматически отключается. По двум трубкам и каналам в изоляционной проставке между электродом и соплом наплавочный порошок транспортируется рабочим газом в зону горения дуги. Пневмомолоток включается с определенным запозданием и осуществляет проковку наплавленного слоя.
Управление технологическим процессом осуществляет ЭВМ по разработанной программе «Полярная Звезда» (рис. 6.5). Программа производит опрос датчиков с частотой 10-20 Гц, обрабатывает сигналы, отображает информацию на экране монитора в виде графиков и таблиц и выдает управляющие воздействия через плату управления. С помощью программы с точностью до 0,5% поддерживаются продольная и поперечная скорости перемещения плазмотрона, расход газа и порошка, сила тока, частота и энергия удара.
Программа осуществляет плавный выход на режим в начале работы и останов плазмотронов по завершении процесса, а также аварийное отключение при невозможности поддержания номинального значения какого-либо технологического параметра.
По окончании процесса наплавки – наложения первого слоя идет его абразивная зачистка с целью удаления окислов. Далее следует наложение второго слоя и т.д. до конечной толщины наплавки. Таким образом наплавленная крестовина подвергается окончательной абразивной обработке для придания поверхности необходимого профиля (рис. 6.6). Далее заполняется ее паспорт с указанием размеров износа (входной контроль), размеров после зачистки под наплавку, конечных размеров и заключение о годности крестовины (рис. 6.7).
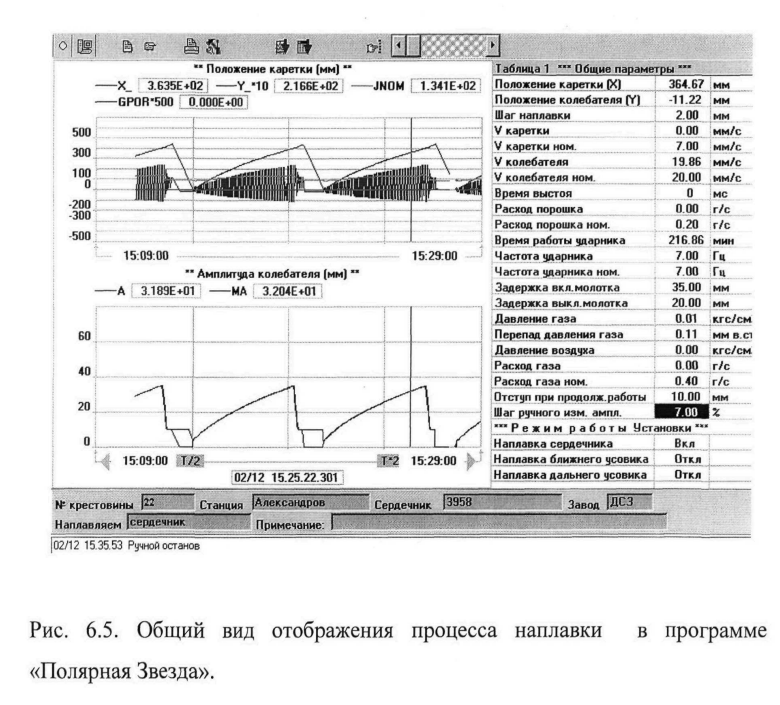
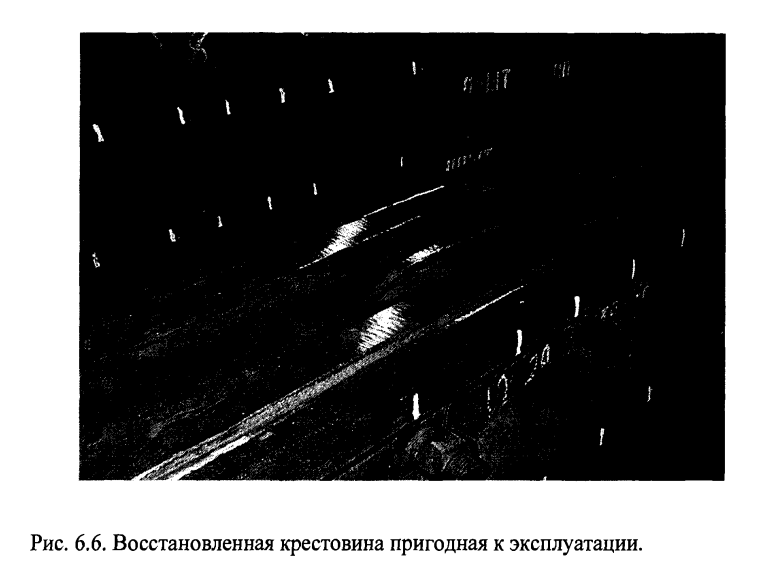
Две крестовины, изъятые из эксплуатации в главных путях Московской железной дороги по предельному износу, были восстановлены плазменной наплавкой и направлены на полигонные испытания на экспериментальном кольце ВНИИЖТ.
Испытания проводились при осевой нагрузке подвижного состава 27 т на ось, скорости движения – 70 км/ч и грузоподъемности – 1.3 млн. т. брутто груза. Обе крестовины были изъяты по причинам, не связанным с зоной наплавки. Максимальный износ одной составил 4 мм, другой – 3 мм, в то время как даже на главных путях допускается износ до 6 мм. Кривая износа одной из крестовин, приведенная на рис. 6.8, показывает, что наплавленный слой имеет еще достаточный ресурс.
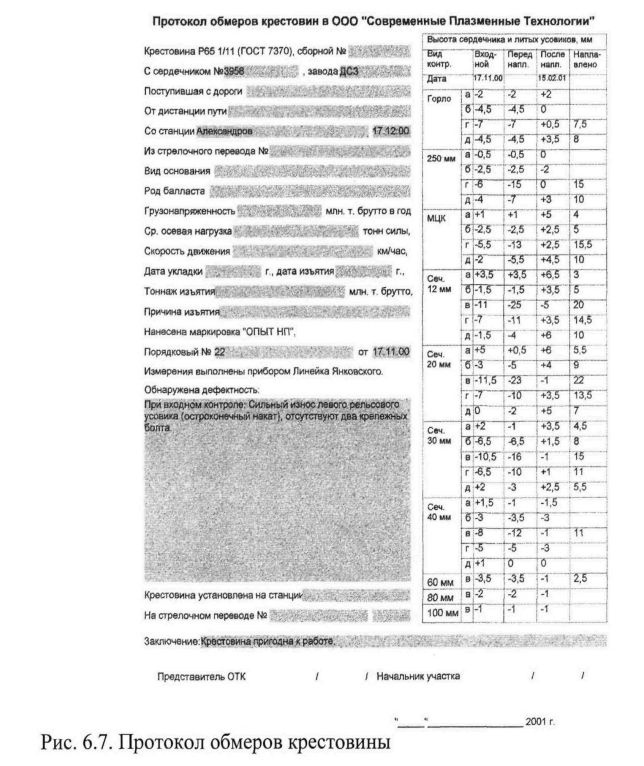
После этого было принято решение провести испытания на путях Московской железной дороги. Две крестовины типа Р65, восстановленные плазменной наплавкой по разработанной нами технологии, были направлены на Московскую железную дорогу.
Одна из крестовин пропустила 115 млн. т./брутто и вторая крестовина пропустила 174 млн.т./брутто (см. Приложение) по причине предельного износа были изъяты из эксплуатации (следует отметить, что средний ресурс новой крестовины составляет примерно 60 млн.т. брутто груза).
После чего было принято решение о плазменной наплавке 30 железнодорожных крестовин, которые были переданы для эксплуатации на Московской железной дороге.
Полученные результаты позволяют разработать новую биметаллическую крестовину с основой из обычной углеродистой стали и рабочей зоной из наплавленного износостойкого покрытия. Преимуществами такой крестовины являются: уменьшение затрат дефицитного и дорогостоящего марганца, лучшая ремонтопригодность (металл литых крестовин из стали Гатфильда имеет много дефектов). Также является целесообразным создание передвижных установок для плазменного восстановления крестовин без их изъятия из железнодорожных путей.
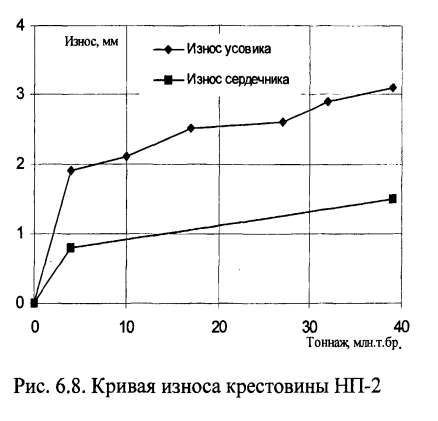
Выводы
- На основе исследованных физико-технических характеристик плазмотрона и закономерностей образования структуры, фазового состава, механических свойств наплавленного металла, переходной зоны и основного металла разработаны технологии плазменной наплавки износостойкого материала на медь, железнодорожный рельс и железнодорожную крестовину из стали Гатфильда.
- Разработана конструкция плазмотрона с внешним электродом, с расширяющимся каналом сопла и расплавлением порошка в канале выходного электрода для плазменной наплавки порошковых материалов, обладающего повышенными надежностью и ресурсом работы.
- Проведено комплексное исследование химического и фазового составов, микроструктуры и механических свойств жаростойкого хромоникелевого покрытия на медную основу. Установлено, что твердость покрытия в 4 раза, а износостойкость в 4-5 раз выше, чем твердость и износостойкость медной основы, что позволяет ожидать увеличения эксплуатационной стойкости стенок медного кристаллизатора машин непрерывного литья заготовок с покрытием данного типа до 500-1000 плавок.
- Прочность сцепления покрытия с медной основой при испытании на срез на 20% выше, чем прочность на срез меди, и на 35% ниже таковой для металла покрытия. Показано, что высокая прочность сцепления хромоникелевого покрытия с медной основой является следствием формирования при наплавке плавной переходной зоны с мелкодисперсной структурой, образовавшейся в результате конвективных и диффузионных процессов массопереноса в жидком наплавленном слое.
- Предложен механизм образования трещин на поверхности в области окончания процесса наплавки и перехода к металлу основы, заключающийся в образовании внутренней оплавленной интеркристаллитной
141 трещины в металле основы, не залеченной жидким расплавом наплавки в результате “закупорки” её русла на поверхности остатками окалины, и хрупком доломе тонкого наплавленного слоя под воздействием остаточных термических напряжений. - Разработан и внедрен эффективный способ релаксационной обработки наплавки из стали 65Х25Г13НЗ на рельсы из стали 76ГФ и литую железнодорожную крестовину из стали ПОГ 13Л, включающий теплый ударный наклеп наплавленного слоя синхронно следующий за наплавкой, обеспечивающий снижение уровня остаточных напряжений и склонности к трещинообразованию.
- Установлено, что эффект релаксации остаточных микронапряжений в результате ударной обработки наплавленного слоя из сплава 65Х25Г13НЗ является следствием более полного протекания фазового превращения (у->а) в наплавленном металле и развития процессов микропластической деформации в результате воздействия ударной нагрузки.
- Исследование влияния исходного состояния (термическое упрочнение и отжиг) рельсовой стали на структурное состояние, уровень остаточных микронапряжений и механических свойств наплавленного металла и переходной области показало, что наиболее предпочтительной является наплавка на отожженную рельсовую сталь с последующей релаксационной обработкой, приводящей к однородному распределению свойств и остаточных микронапряжений.
- На основе установленных закономерностей формирования фазового состава, структуры, уровня остаточных напряжений, механических свойств и сопротивления разрушению наплавки порошкового сплава 65Х25Г13НЗ на рельс, показана принципиальная возможность создания биметаллической железнодорожной крестовины из низколегированной стали типа 76ГФ с наплавкой наиболее подверженных износу областей крестовины взамен высоколегированной стали 110Г13.
- Наплавка с релаксационной обработкой порошкового сплава 65Х25ПЗНЗ на сталь Гатфильда увеличивает твердость и износостойкость, однако снижает пластичность; снижение пластичности тем больше, чем ближе к границе между наплавкой и основным металлом, что является следствием неоднородности фазового состава (увеличения а-фазы в результате образования мартенсита деформации) и влияния дефектов на границе раздела.
- Разработана и опробована автоматизированная опытно-промышленная установка и технология восстановления плазменной наплавкой изношенных крестовин. Ресурсные испытания железнодорожных крестовин, проведенные на Московской железной дороге показали, что эксплуатационная стойкость восстановленных по разработанной технологии крестовин в два раза выше, чем исходных, новых крестовин из стали Гатфильда.
Список литературы
78. Захаров М.В., Захаров А.М. Жаропрочные сплавы. М., “Металлургия”, 1972 г., 383 с.
79. Бэджер и Фритурин “Сплавы на основе никеля и кобальта” в ст. “Жаропрочные сплавы для сверхзвуковых полетов”, М., Металлургиздат, 1962 г., с. 147-175.
80. А.И.Быков. Высоколегированный хромомарганцовистый наплавочный металл для наплавки крестовин. В сб. Теоретические и технологические основы наплавки. Науковадумка,Киев, 1977,с.45-51.
81. Н.А.Гринберг. Упрочнение наплавкой деталей из высокомарганцовистой стали, работающих в условиях ударно-абразивного изнашивания. В жур. Автоматическая сварка. №2,1976,с.51-55.
82. Г.В.Рюмин., Б.В. Савченков. Новые износостойкие наплавочные материалы обеспечивающие повышение долговечности изделий из высокомарганцевой стали. В сб. Наплавка в машиностроении и ремонте. Киев. ИЭС им. Е.О.Патона, 1981.,с. 122-129.
83. Е.Н.Морозовская. Структура и свойства высокомарганцевого металла наплавленного порошковой проволокой. В жур. Автоматическая сварка. №4,1966,с.22-26.
84. Н.А.Гринберг, Л.С.Лифшиц. Наплавка деталей, работающих в условиях абразивного износа и ударных нагрузок. В жур. Автоматическая сварка. №7,1962,0.18-24.
85. Н.Г. Корнаушенков, Ю.Н. Корнаушенкова, А.А.Астафьев. Влияние легирующих элементов на механические свойства и износостойкость стал» 110Г13Л. В жур. Литейное производство. №6,1973,с.27-29.
86. Н.А.Гринберг, И.Я. Дзыкович. Химическая и структурная неоднородность и механические свойства износостойких легированных наплавок. В жур. Сварочное производство №3,1974.с.7-10.
87. Е.Н. Морозовская. Автоматическая наплавка высокомарганцовой аустенитной стали Г13. В журнале Автоматическая сварка. № 3, 1961 с.32-41.