Сейчас ваша корзина пуста!
Исследование процессов формирования качества металла в технологическом блоке подготовительных операций к формообразованию
Цикл статей:
Глава 1 – Повышение качества железнодорожных пружинных клемм на основе совершенствования режимов обработки
В настоящей главе содержатся результаты лабораторных и промышленных исследований, а также-моделирования процессов формирования качества стали 40С2 при термическом и деформационном воздействии, необходимые для^ получения исходных данных для проектирования »усовершенствован ных режимов подготовки металла к формообразованию, устраняющих неблагоприятные проявления1 технологической наследственности на последующих операциях холодной гибки и обеспечивающие достижение требуемых геометрических размеров промежуточных, заготовок и пространственного контура клемм.
Определение критических точек стали 40С2
Для изучения фазовых превращений был использован дилатометрический метод, который основан на измерении изменений объема, линейных размеров и коэффициента расширения исследуемого образца и эталона из сплава, не претерпевающего фазовых превращений при тепловом воздействии [63]. Критические точки при дилатометрическом анализе определялись по кривым, показывающим изменение длины изучаемого образца при нагреве и охлаждении. В исследованиях по определению критических точек стали 40С2 производства ОАО «Мечел» были использованы дифференциальный оптический дилатометр Шевенара. Дилатометрические кривые двух серий опытов по определению температур фазового равновесия при нагреве и охлаждении стали 40С2 приведены на рис. 3.1.Две серии кривых на этом рисунке соответствуют результатам двух проведенных опытов.
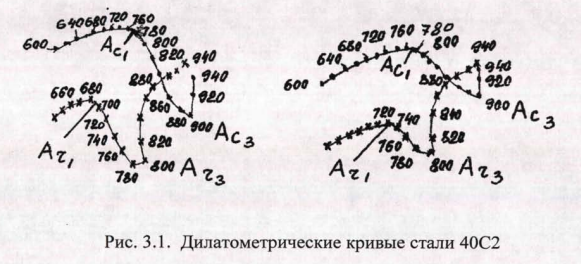
В табл. 3.1 представлены скорости нагрева и охлаждения образцов, зафиксированные в ходе дилатометрического исследования. Температуры критических точек, установленные в результате исследования и соответствующие прямому и обратному фазовым превращениям в стали 40С2 в сравнении с данными работы [55], указаны в табл. 3.2.
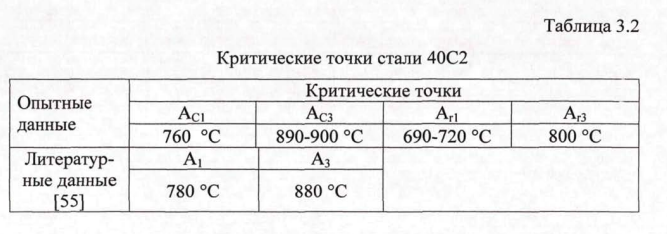
Выполненные исследования позволили получить данные необходимые для качественного осуществления процессов термической обработки стали 40С2 как на этапе подготовки металла к формообразованию, так и на этапе окончательной термической обработки отформованных клемм.
Исследование режимов отжига горячекатаного подката на структуру зернистого перлита в роликовой проходной печи
В 2006 году на ОАО «ММК-МЕТИЗ» была введена в эксплуатацию современная роликовая проходная печь, позволяющая осуществлять термо-обработку стали в бунтах массой до 2500 кг в защитной атмосфере.
Для получения исходной информации и проектирования режимов структурного отжига стали 40С2, производства ОАО «Мечел», на печи не-прерывного действия выполнили лабораторные исследования. Оценка характера изменения микроструктуры стали в ходе исследований производилась на микроскопе «Эпиквант» и системы компьютерного анализа изображений 81АМ8.
Исходный горячекатаный подкат имел феррито-перлитную структуру с карбидами пластинчатой формы в составе эвтектоида (рис.3.2).

Структурный отжиг осуществляли по типовому режиму с нагревом до температуры несколько ниже установленного значения точки Ai и последующей выдержкой при этой температуре. Температуру отжига принимали равной 720 ±10 °С, что соответствует типовым условиям обработки подката на печах непрерывного действия в режиме рекристаллизации. Использование указанного режима обеспечивает выполнение процессов как структурного, так и рекристаллизационного отжигов по унифицированной технологии.
В повседневной, практике термической обработки подката и калиброванного металла исследуемый режим многократно тиражируется на печи РПП, он> достаточно хорошо отработан, что, в свою очередь, предполагает также устойчивость формируемой на его основе режимов отжига на структуру зернистого перлита.
Динамика нарастания количества сфероидизированной фазы и изменения прочностных показателей качества металла при отжиге изучалась при варьировании продолжительности процесса от 5 до 12 часов. Результаты исследований приведены на рис.3.3.
Из рисунка 3.3 (а) видно, что деление цементитных пластин и образование карбидов зернистой формы отмечалось уже при выдержке металла в печи в течение 5 часов. Количество сфероидизированной фазы при этом составляло около 30%. Дальнейшее увеличение длительности отжига обеспечивает непрерывный прирост доли зернистого перлита в структуре стали (рис.З.З.б.). При выдержке 9-12 часов (рис.З.З.в.) количество сфероидизированной фазы составляло более 60 %, что полностью отвечает требованиям дальнейшей переработки подката.
Динамика изменения временного сопротивления разрыву стали 40С2 в зависимости от времени выдержки t (час) при сфероидизации (рис.3.4) описывается выражением:
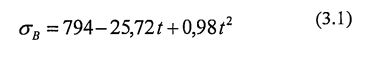
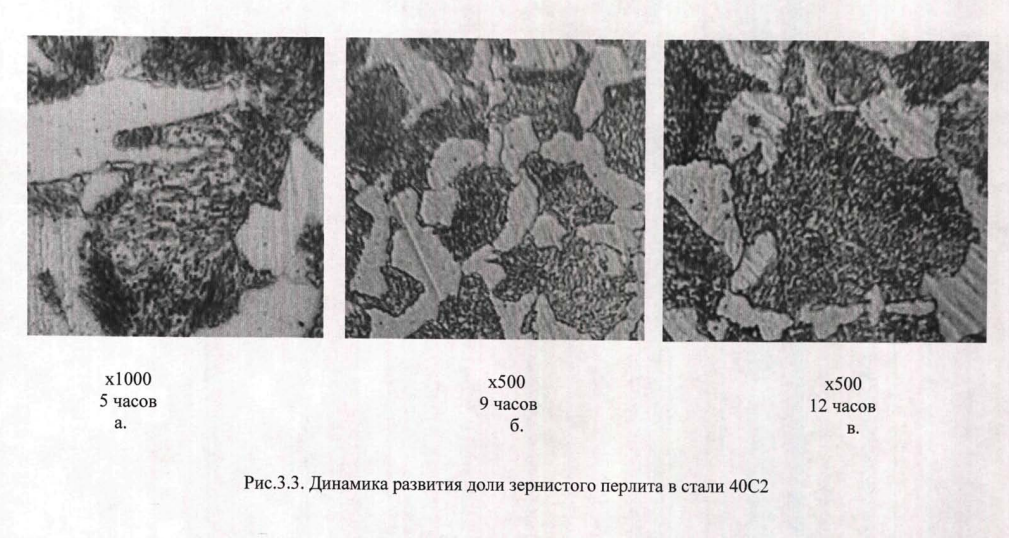
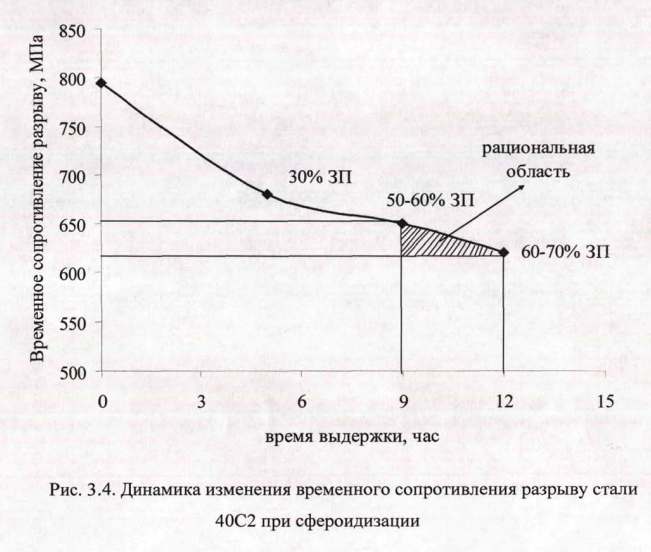
Полученные данные послужили основой для выполнения экспериментов в промышленных условиях на печи РПП-2 калибровочного цеха ОАО «ММК- МЕТИЗ». В таблице 3.3. приведена краткая техническая характеристика печи непрерывного действия.
Для исследования влияния режимов термической обработки на качество стали 40С2 были подготовлены образцы свидетели исходного подката диаметром 14,0 мм. Варьируемыми параметрами в экспериментах служили температура по зонам печи и скорость движения металла. Варианты исполнения режима отжига, реализованные в промышленных условиях, в таблице 3.4.
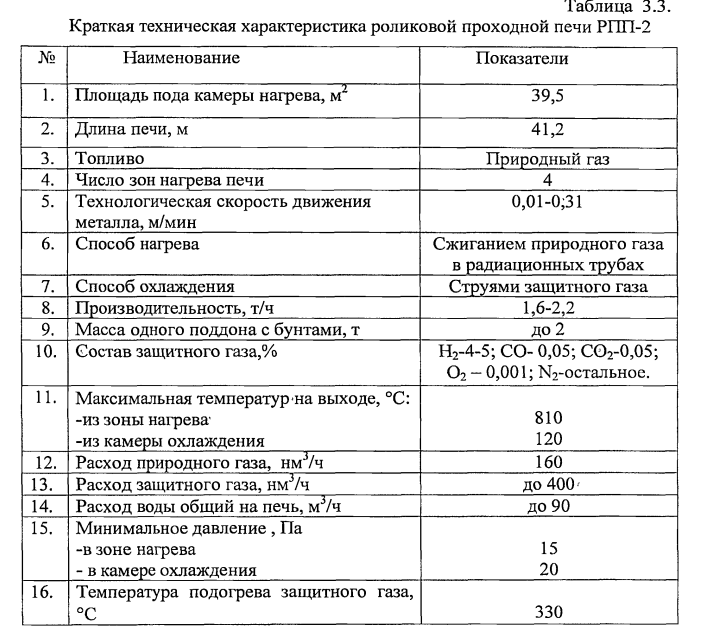
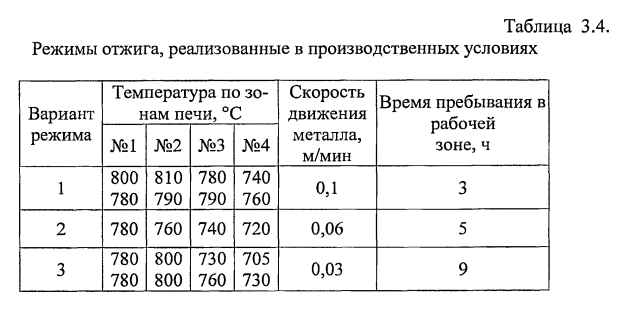
В таблице 3.5. приведены результаты сравнении показателей качества металл а до и после термообработки:
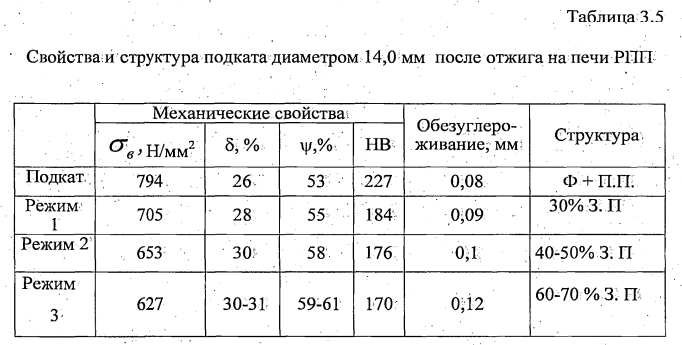
Из таблицы 3-.5 видно, что наибольшее смягчение стали достигается отжигом по режиму 3, который обеспечивает формирование показателей качества подката, необходимые для последующего стабильного осуществления процессов холодной гибки.
Вторая серия опытов проводилась на калиброванных прутках диаметром 12,9 мм из горячекатаного подката 14,0 мм без предварительной термообработки. Результаты представлены в табл. 3.6.
Анализ данных табл. 3.6 показал; что развитие процессов сфероидизации в стали, подвергнутой предварительной .холодной пластической деформации путем: калибрования осуществляется за более короткое время, по сравнению с термической обработкой горячекатаного проката. Так достижение структурного состояния стали (60-70% зернистого перлита), отвечающего требованиям последующих формообразующих операций холодной гибки, происходит за время пребывания металла в рабочей зоне печи в течение 5 часов. При термообработке горячекатаного подката для этого необходимо время около 9 часов, что в 1,8 раза больше.
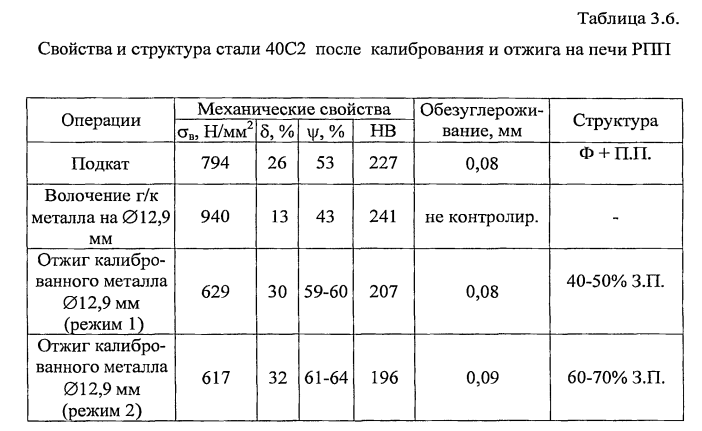
В результате экспериментов были получены исходные данные для проектирования результативных режимов отжига подката на печи непрерывного действия с достижением необходимого структурного состояния и механических свойств металла, отвечающих условиям его дальнейшей переработки в технологическом блоке формообразования.
Анализ влияния поверхностной механической обработки на механические свойства стали
Последующая операция в технологическом блоке подготовки металла к формообразованию направлена на формирование требуемых геометрических размеров и устранение дефектов поверхности подката. В зависимости от качества поверхности подката после структурного отжига для этой цели могут применяться операции калибрования или резцовой обточки. Для оценки влияния поверхностной механической обработки на механические свойства стали и характер распределения деформации по сечению металла в заводских условиях были выполнены эксперименты по волочению образцов из стали 40С2 в горячекатаном и термически обработанном состоянии с диаметра 14,0 на диаметр 12,9 мм (степень деформации 14 %). Калибрование подката вели в монолитных волоках на однократном стане 1/750 с использованием сухой смазки. Параметры волочильного инструмента по ГОСТ 9453, полуугол канала волоки 6°. После калибрования от образцов были отобраны темплеты и проведены замеры микротвердости по сечению металла. Распределение микротвердости по сечению темплетов оценивали методом вдавливания алмазной пирамиды на твердомере ПМТ-3 в соответствии с методикой ГОСТ 9475. Результаты приведены на рис. 3.5 и 3.6.
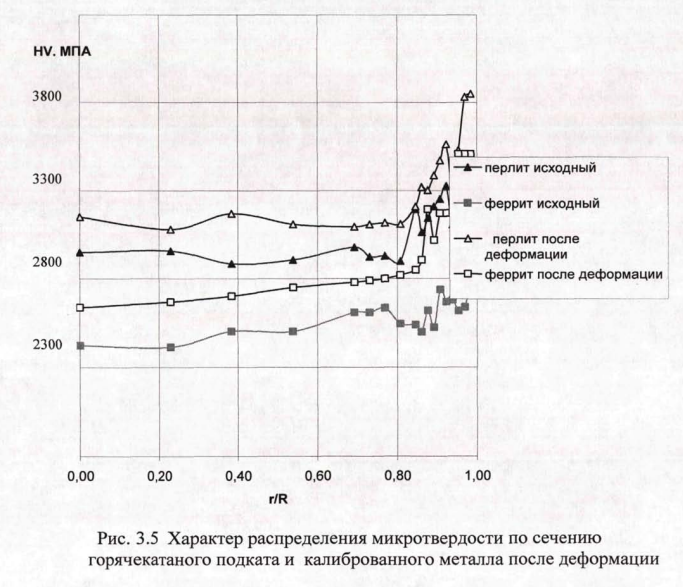
Из анализа полученных графических зависимостей видно, что горячекатаный подкат в состоянии поставки имеет неравномерность распределения твердости по сечению, обусловленную спецификой металлургического передела, связанную с условиями охлаждения металла после горячей прокатки (рис.3.5). При этом более высокая твердость свойственна поверхностным слоям металла. Наибольшим значением твердости обладают поверхностные слои со структурой перлита. Однако в процессе пластической деформации наиболее интенсивно упрочняется ферритная фаза, особенно в поверхностных слоях металла. При этом характер распределения микротвердости по сечению деформированного металла определенным образом наследуется от исходного состояния.
В таблице 3.7 приведены результаты изменения механических свойств стали.

В результате термообработки горячекатаной стали (структурный отжиг) твердость по сечению подката выравнивается, но характер ее распределения по сечению после калибрования также носит ярко выраженную локализацию в поверхностных слоях рис. 3.6.
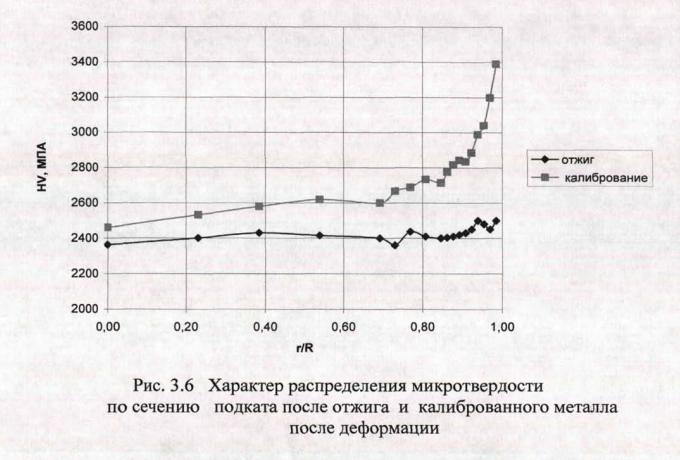
В таблице 3.8 приведены результаты изменения механических свойств стали после отжига и калибрования.
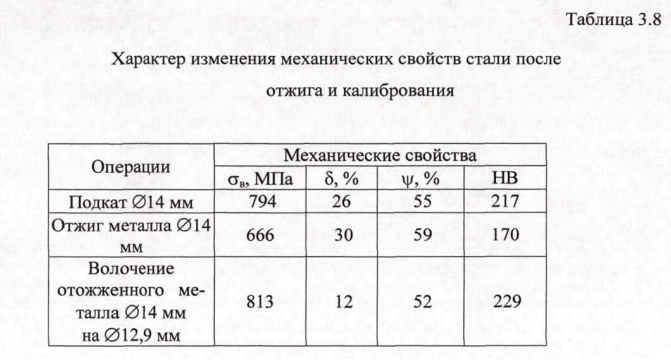
Еще более существенная локализация деформации в поверхностных слоях сечения металла характерна для стали подвергнутой поверхностной механической обработке – обточке на линии «Кизерлинг» (рис. 3.7).
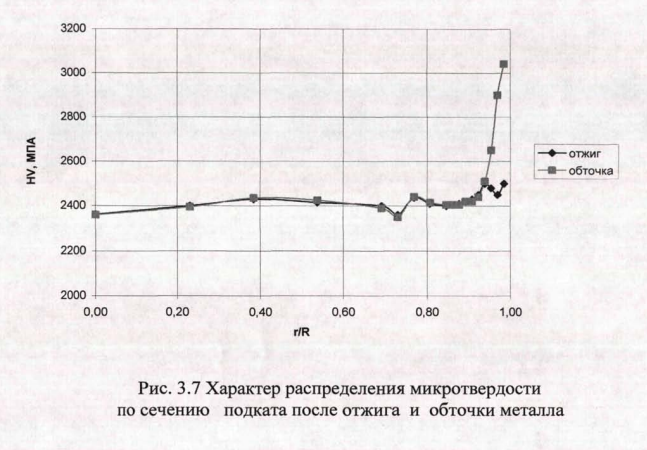
Опыты, выполненные на отожженных образцах из стали 40С2 при обточке подката 14,0 мм на диаметр 12,9 мм показали, что поверхностная механическая обработка существенно влияет на механические свойства обрабатываемой стали (таблица 3.9).
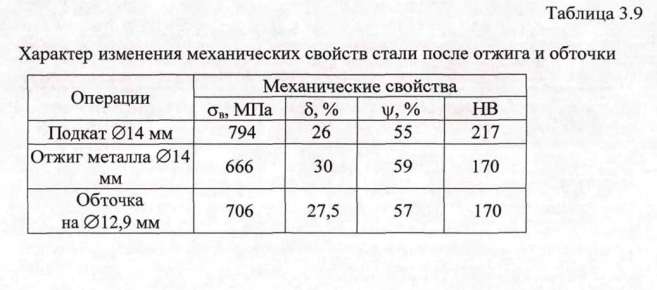
Под воздействием режущего инструмента наиболее заметно изменяется структура поверхностных слоев металла (рис.3.8). Зерна приобретают вытянутую дугообразную форму со следами полос скольжения.
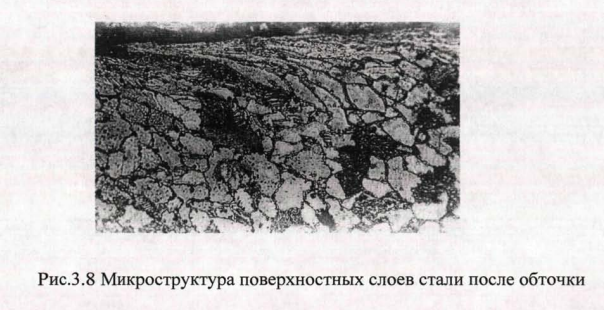
Наблюдаемый рост прочностных и падение пластических свойств стали, фиксируемые в макрообъеме металла при механических испытаниях, обусловлены изменением состояния поверхностных слоев, получивших наклеп в результате деформационного воздействия режущего инструмента.
Различная динамика накопления деформации в процессах калибрования или обточки поверхностных и центральных слоев стали, будет предопределять различия в термодинамическом состоянии отдельных сечений металла, а следовательно, и неодинаковую степень развития в них процессов рекристаллизации при выполнении операций термообработки. Наблюдаемое незначительное развитие процессов деформации в центральных слоях металла способствует получению в них неоднородных степеней деформации и может привести при последующей термообработке к неодинаковой степени развития процессов рекристаллизации и формированию неоднородной структуры и свойств по сечению металла, получаемого в блоке подготовительных операций.
В свою очередь, это предопределило специфику формирования подходов к проектированию режимов рекристаллизационного отжига на основе характера предшествующей холодной пластической деформации или поверхностной механической обработки и устранения-наследования этих негативных явлений. Реализация указанного подхода предполагает сокращение длительности процессов термообработки. Исследованию этого вопроса посвящен следующий раздел диссертационной работы.
Исследование режимов рекристаллизационного отжига сталипосле механической обработки
Следующим этапом исследований явилось изучение формирования качества калиброванной или обточенной’стали при рекристаллизационном отжиге в печи непрерывного действия. Из образцов подката диаметром 14,0 мм стали 40С2, подвергнутой отжигу по режиму 3 (табл. 3.4); были подготовлены холоднотянутые и отдельно обточенные образцы диаметром 12,9 мм. С учетом выдвинутого в результате исследований, предположения о взаимосвязи характера распределения деформации по сечению стали и продолжительностью термической обработки, были определены сокращенные по времени режимы отжига при времени пребывания’металла в рабочей зоне печи в интервале 30-120 мин. Температура по зонам, печи соответствовала режиму 3 (табл.3.4). Скорость движения металла составляла от 0,15-0,2 м/мин. Характер изменения механических свойств металла в таблице 3.10. Результаты промышленных экспериментов в виде графических зависимостей изменения показателей качества стали 40С2, подвергнутой предварительной механической, обработке, от длительности (1, мин) рекристаллизационного отжига приведены на рис. 3.9. С использованием методов математической статистики получены зависимости (3.2-3.5), позволяющие прогнозировать изменение механических свойств стали в процессе отжига, и определять рациональные режимы обработки.
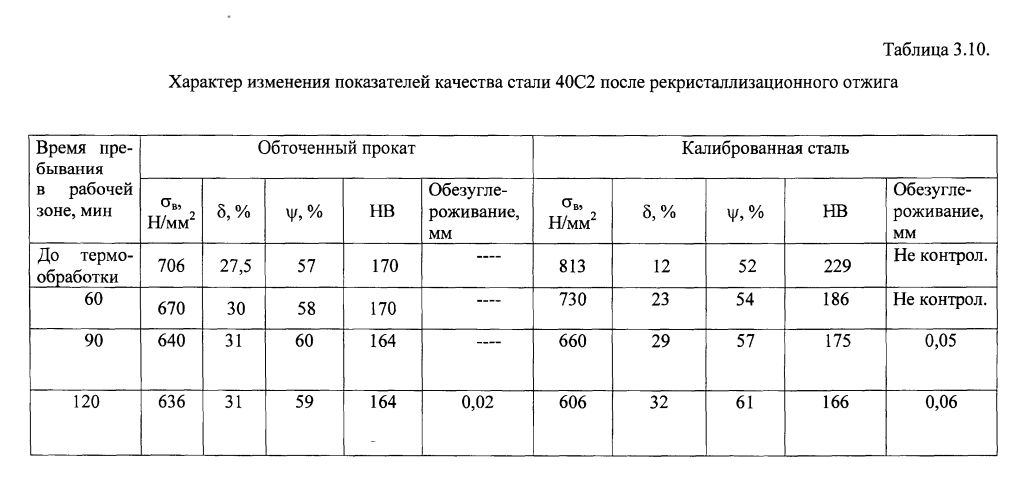
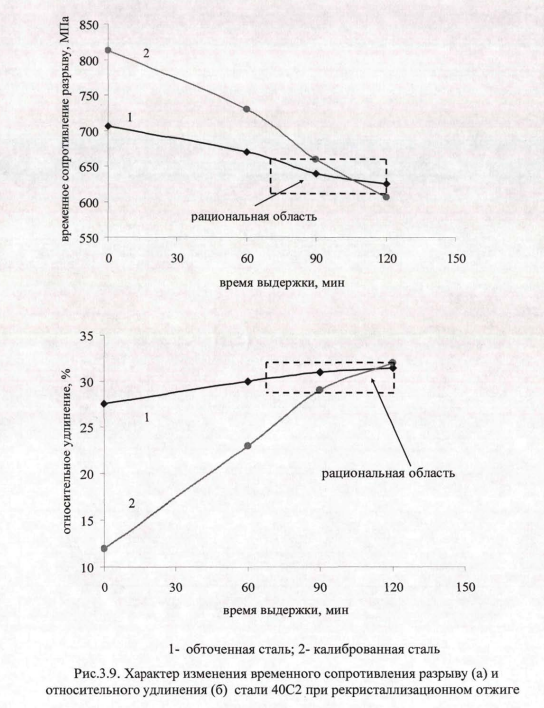
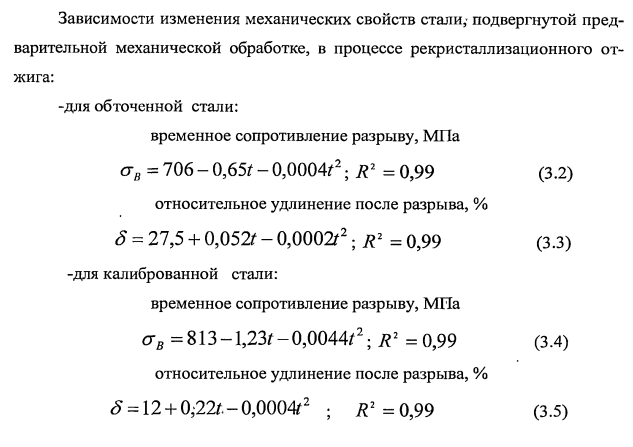
Из анализа экспериментальных данных видно, что показатели качества стали после обточки полностью выходят на уровень механических свойств стали до поверхностной механической обработки за время пребывания в камере нагрева 60-90 мин. Дальнейшее увеличение времени выдержки не привело к более значительному смягчению стали. Для калиброванной стали восстановление требуемых показателей механических свойств стали было достигнуто за более длительное время выдержки 90-120 мин.
Для оценки качества термообработки из образцов обточенной и отожженной стали изготовили темплеты и провели измерения микротвердости по сечению (рис.3.10). Результаты, измерения показали, что различия величины микротвердости поверхностных и центральных слоев составляет не более 6%, что свидетельствует об однородности структуры по сечению стали.
Таким образом, выполненные исследования подтвердили, что отжиг по ускоренным режимам, позволяет устранить зональный характер структурной неоднородности, возникающий ввиду различных условий деформации поверхностных и центральных слоев металла при механической обработке и получить металл с однородными механическими свойствами для осуществления последующих операций формообразования.
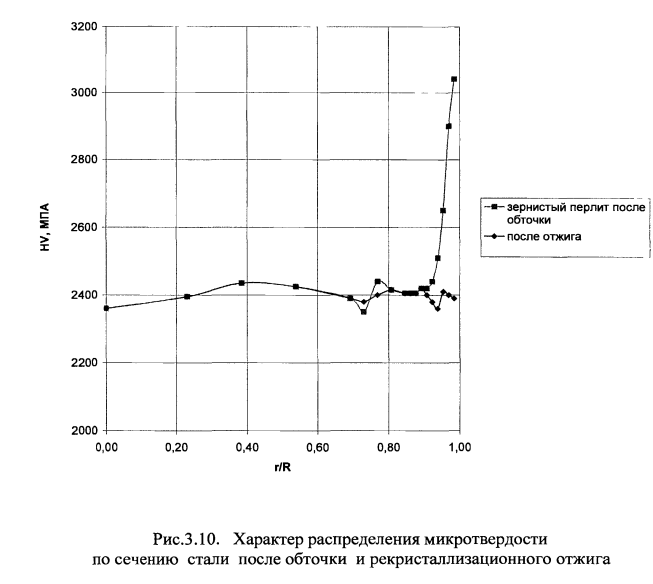
Результаты представленных экспериментов легли в основу разработки ресурсосберегающих промышленных режимов рекристаллизационного отжига калиброванной (обточенной) стали в бунтах на печи непрерывного действия взамен осуществления процесса термообработки в печах СКБ.
Математическое моделирование трансформации показателей качества металла в блоке подготовительных операций
Комплекс исследований процессов формирования качества металла в блоке подготовительных операций позволил оценить динамику пооперационной трансформации свойств и их чувствительность к технологическим воздействиям различной физической природы (таблица 3.11). Особенностью’технологического процесса в блоке подготовительных операций является то, что все группы показателей качества претерпевают изменения (трансформацию) своих значений. Интенсивность изменения показателей качества различна. Существует группа показателей качества (механические свойства) изменяющих свои значения после каждой технологической операции. В то время как геометрические показатели качества, изменив свое значение на операциях обточки или калибрования, в последующем сохраняют свои значения. Интересен и тот факт, что практически отсутствует монотонность (постоянное уменьшение или увеличение) изменения показателей качества по всем рассматриваемым группам.
При установлении качественных характеристик изменения, показателей качества последующий этап должен базироваться на определении количественной трансформации, их моделированию и построению на этой основе результативных режимов обработки, обеспечивающих заданное качество металла с учетом специфики дальнейшей обработки в последующих технологических блоках. Это во многом зависит от эффективности аппарата описания! пооперационной трансформации показателей качества металла.
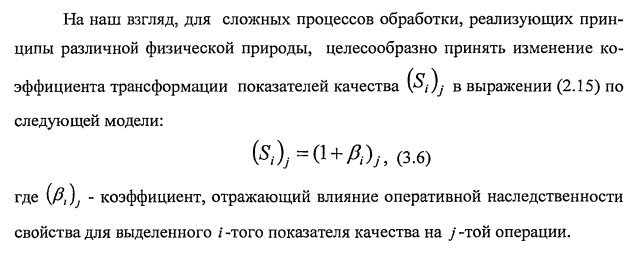
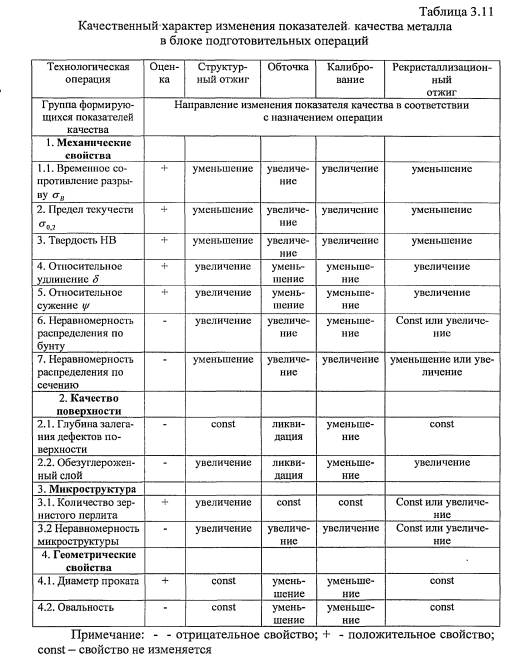
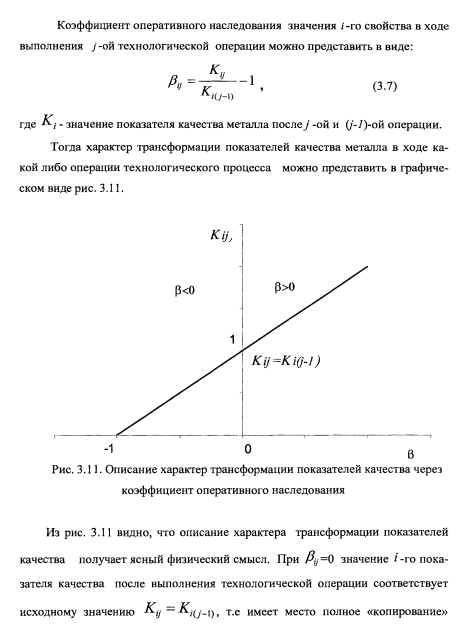
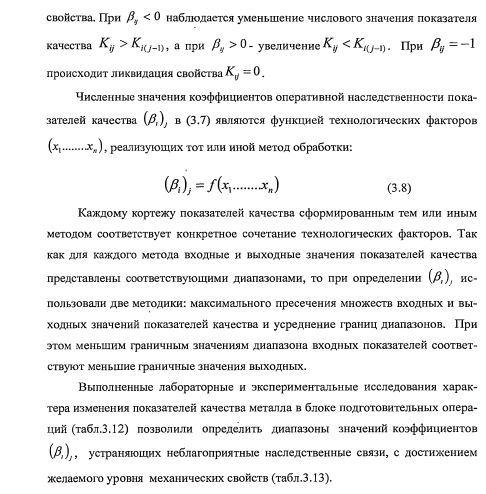
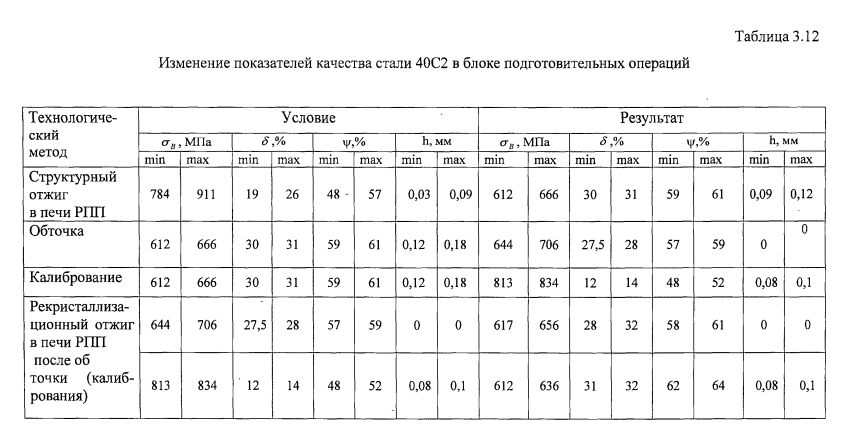
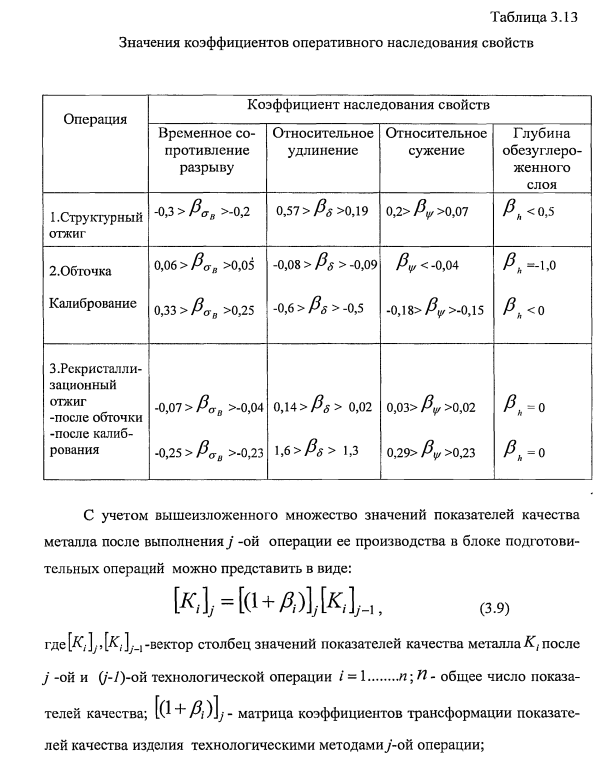
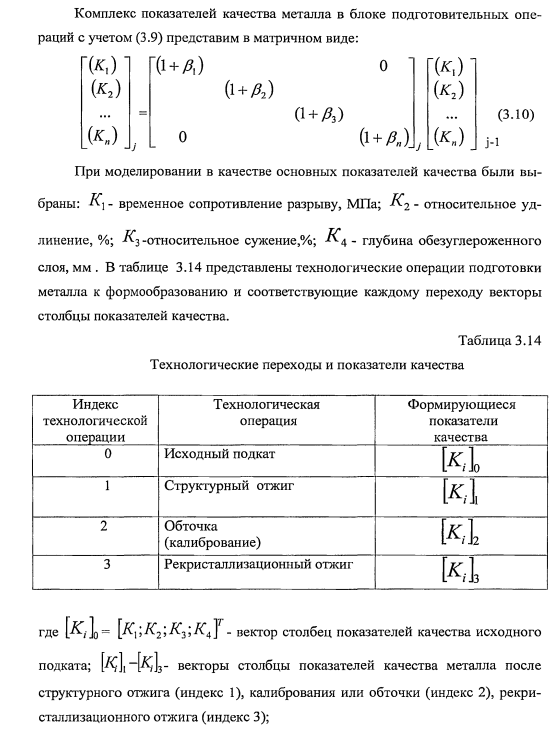
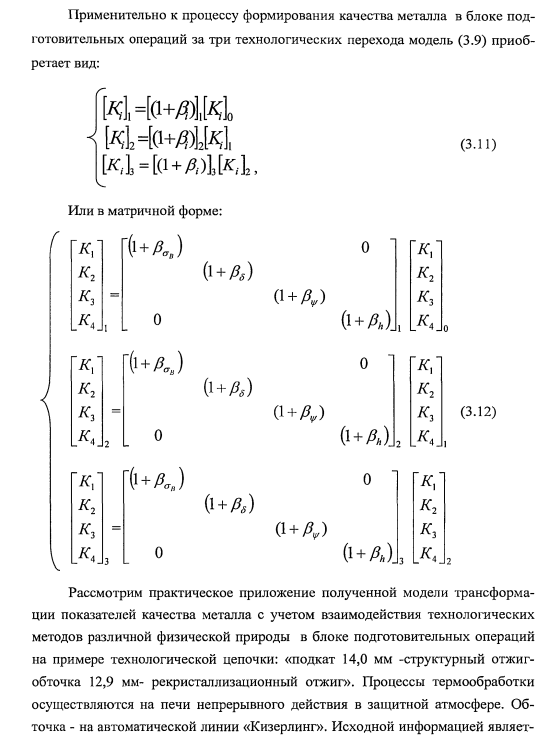
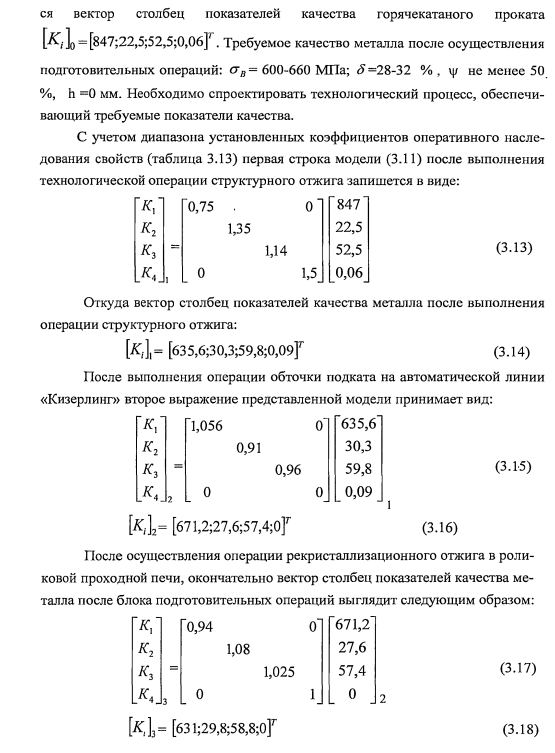
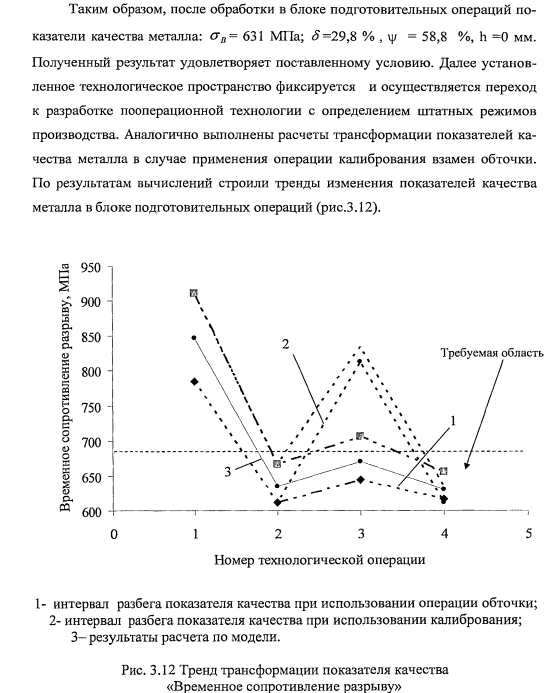
Из рисунка 3.12 видно, что диапазон разбега временного сопротивления разрыву планомерно уменьшается от операции к операции, что удовлетворяет условию управления качеством продукции с позиций теории технологической наследственности.
Результаты вычислений позволяют сделать ряд выводов, направленных на выработку управляющих воздействий на качество металла в блоке подготовительных операций. Структурный отжиг подката на печи РПП обеспечивает снижение разброса показателей качества металла по сравнению с горячекатаным состоянием, особенно по прочностным характеристикам. Переработка по схеме «исходный подкат – структурный отжиг – калибрование- рекристаллизационный отжиг» обеспечивает получение металла с более узким интервалом вариации механических свойств, по сравнению с технологической схемой, где вместо операции калибрования используется операция-обточки.
На наш взгляд это – объясняется снижением вариации механических свойств исходного отожженного металла после деформации (по-временному сопротивлению разрыву более чем в 2 раза) и более равномерной проработкой« объема металла при калибровании, что обеспечивает формирование более однородной структуры рекристаллизации при последующем отжиге. Кроме того, в данном направлении имеется резерв повышения равномерности деформации при волочении за счет управления технологическими факторами процесса калибрования (геометрические параметры.волоки, степень деформации) [59]. Использование процессов-термообработки в защитной атмосфере позволяет при этом получать допускаемые нормативно-технической документацией значения величины обезуглероженного слоя
Таким образом, используя^ разработанную модель, возможно определять предпочтительные траектории исполнения» технологических режимов в блоке подготовительных операций, ликвидирующих или заметно уменьшающих негативные проявления технологической наследственности и обеспечивающих получение качественного металла для формообразования пружинных клемм.
Выводы по главе
- Дилатометрическим методом уточнены температуры критических точек, соответствующие прямому и обратному фазовым превращениям в стали 40С2, необходимые для обоснованного назначения режимов термообработки.
- В результате лабораторных и промышленных экспериментов получены исходные данные для проектирования результативных режимов отжига горячекатаного подката на структуру зернистого перлита в печи непрерывного действия.
- Проведены исследования по изучению характера распределения деформации по сечению стали 40С2, подвергнутой после структурного отжига, калиброванию или обточке. Показано, что процессы накопления деформации по сечению стали при этом, протекают неравномерно и локализуются в основном в поверхностных слоях металла, инициируя структурную неоднородность в деформированном состоянии. Исходя из этого, сформулирован подход к проектированию режимов рекристаллизационного отжига, учитывающий характер предварительной механической обработки.
- Получены исходные данные для проектирования ускоренных режимов рек-ристаллизационного отжига калиброванной (обточенной) стали, обеспечиваю¬щие получение однородной структуры и механических свойств металла на эта¬пе подготовки к формообразованию.
- На основе выполненных исследований разработана математическая модель трансформации показателей качества металла в блоке подготовительных операций. Предложена зависимость количественно отражающая «копирование», «ликвидацию», увеличение или уменьшение значения показателя качества в ходе выполнения технологических операций различной физической природы. Модель позволяет направленно формировать рациональные траектории обеспечения качества металла в блоке подготовительных операций, устраняющие проявления неблагоприятной технологической наследственности на последующих формообразующих операциях холодной гибки промежуточного профиля омега.
Список литературы
- Безухов Н И. Теория упругости; пластичности5 и ползучести.- М. Высшая школа.-1961. 324С.
- Ильюшин А.А. Пластичность.-М: Изд-во ГТИ.- 1948.-376С. 52.Малинин Н.Н. Прикладная теория. пластичности и ползучести.- М.: Маши¬ностроение.-1968.- 398С.
- Надаи А. И. Пластичность и разрушение твердых: тел.- М: Изд-во иностранной литературы.- 1954.-43 5С. .
- Хилл Р1 Математическая.теорияшластичности;- М.: Наука.-1956-435С.
- Попов А.А. Справочник термиста. Изотермические и термокинетические диаграммы распада переохлажденного аустенита.-М.: Машгиз.- 1961.- 43ОС.. .
- Геттель X., Нейхаус Я., Окерналь В. Высокопроизводительная? обдирка. — экономичный! способ» производства:круглого стального прутка // Черные метал¬лы..- 1987. – № 22. – С. 24-31.
- Бернштейн М.Л. • Структура деформированных материалов. М.:Металлургия.т1977.- 431С.
- В: Бэкофен Процессы деформации.- М.: Металлургия.- 1977.-288С.
- Носов А.Д;, Слабожанкин Е.А., Корчунов А.Г. Моделирование: режимов волочения калиброванной стали// Вестник МЕТУ им: Г.И; Носова.- 2007.-№ 2 .- С.49-51
- Корчунов А.Г. Производство калиброванного металла со специальной отделкой поверхности //Заготовительные производства’ в машиностроении: – 2005.- № 7.- С. 35-40
- Феодосьев В.И: Сопротивление материалов.- М.: Наука.- 1974.-560С.
- Чижиков Ю.М. Теория подобия и моделирование процессов обработки ме¬таллов давлением.- М. Металлургия.- 1970.-296С.
- Лившиц Б.Г., Крапошин B.C., Линецкий Я.Л. Физические свойства металлов и сплавов.- М.:Металлургия.-1980.- 320С.
- Носов А.Д., Слабожанкин Е.А., Корчунов А.Г. Статистические модели оценки изменения механических свойств метизных изделий из кремнистых сталей при термическом упрочнении // Производство конкурентоспособных мети¬зов. Сб. науч. тр. -ГОУ ВПО «МГТУ».-2007.- Вып.2 .- С.71-74.
- Львов Ю.А. Основы экономики и организации бизнеса.- С-Петербург.- 1992.-383С.
- Носов А.Д., Слабожанкин Е.А., Корчунов А.Г. Повышение эффективности производства пружинных клемм совершенствованием технологического блока подготовительных операций // Современные достижения в теории и техноло¬гии пластической обработки металлов. Труды междунар.- науч.- техн. конф. .- С-Петербург 2007.-С. 374-376.
- Структура и свойства перспективных металлических материалов / Громов В.Е., Гун Г.С., Корчунов А.Г., Слабожанкин» Е.А и др.- Томск. Изд-во НТЛ.- 2007.- 580С.