Сейчас ваша корзина пуста!
Исследование процессов формирования качества клемм в технологическом блоке окончательной термообработки и контроля
Цикл статей:
Глава 1 – Повышение качества железнодорожных пружинных клемм на основе совершенствования режимов обработки
В настоящей главе приводятся результаты исследований динамики формирования прочностных и пластических свойств стали 40С2 при термическом упрочнении, необходимые для определения результативного технологического пространства окончательной термообработки, обеспечивающего стабильное достижение заданного уровня твердости и пружинящих свойств отформованных пружинных клемм.
Определение рационального диапазона температуры закалки стали 40С2
При выполнении основного условия- качественной закалки – получении структуры мартенсита во всем сечении изделия основную роль в достижении наилучших результатов такой обработки играет правильный выбор температуры нагрева. Общим правилом для назначения температуры нагрева под закалку доэвтектоидных сталей, к числу которых относится и сталь 40С2, является превышение на 30-50°С температуры верхней критической точки Асз, соответствующей полному превращению исходной структуры в аустенит.
Для оценки обоснованности выбора закалочной температуры при осуществлении окончательной термической обработки клемм были проведены опыты по выявлению уровня твердости стали 40С2 после печного нагрева до различных закалочных температур, а именно, 860 °С, 880 °С, 900 °С, 920 °С, 950 °С, 1000 °С. Результаты исследований приведены на рис. 4.1.
Видно, что максимальная твердость достигается при закалке с диапазона температур 910 -930°С, что удовлетворяет рекомендуемому в литературе условию качественной закалки, то есть Асз ± (30-50) °С. Такая температура способна придать обрабатываемой стали наибольшую твердость 59-60 HRC.
Следует иметь в виду, что кремнистые стали довольно чувствительны к перегреву. Повышение температуры до 960-980°С не только приведет к снижению твердости, но и в результате перегрева будет способствовать возникновению трещин при закалке, а также инициирует склонность к росту зерна.
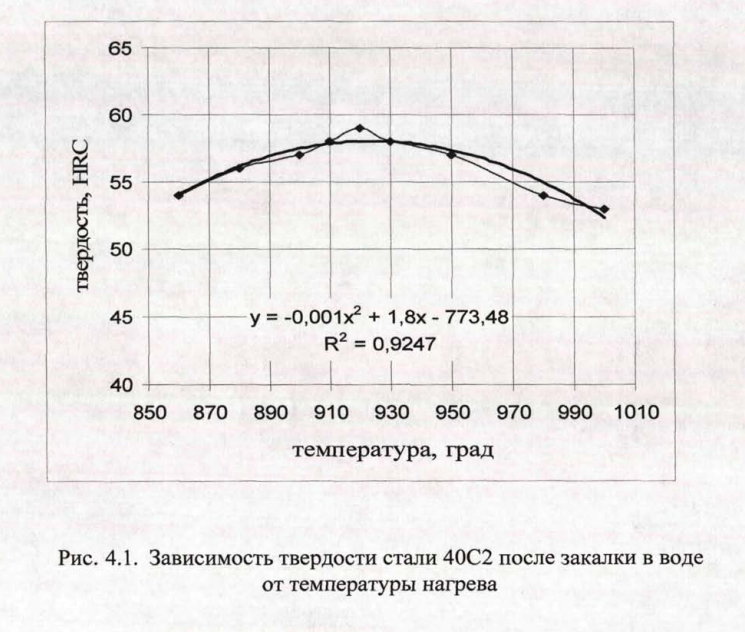
Окончательные свойства закаленная клемма приобретает в результате отпуска, при котором реализуются потенциальные возможности для повышения сопротивления малым пластическим деформациям и всего комплекса эксплуатационных свойств, создаваемых в процессе закалки с мартенситным превращением. Следующий раздел посвящен изучению поведения закаленной с оптимального интервала температур стали 40С2 в зависимости от тем- пературно-временных параметров отпуска.
Исследование влияния отпуска на механические свойства закаленной стали
Для выяснения закономерностей изменения механических свойств закаленной стали 40С2 в ходе отпуска выполнены исследования по изучению влияния его температуры и продолжительности на величину временного сопротивления разрыву, предела упругости, твердости и характеристик пластичности металла.
В качестве исходного материала при проведении исследований использовались мерные образцы обточенного и отожженного подката длиной 250300 мм, подвергнутые закалке в воде с оптимальной температуры. Закаленные образцы отпускались в электрической камерной печи в заводской лаборатории на ОАО «ММК-МЕТИЗ» при температурах 350-450 °С в течение времени от 20 до 90 мин. Определение механических свойств термообработанных образцов производилось по ГОСТ 1497-84 на универсальной разрывной гидравлической машине ЕИ-100 с использованием шкалы 0…200 кН с ценой деления 1,0 кН и шкалы 0…400 кН с ценой деления 2,0 кН. Допускаемая погрешность машины + 1%, начиная от 1/10 установленного диапазона измерений. Фиксация усилия на машине ЕИ-100 осуществлялась с помощью индуктивного измерителя преобразователя давления. Механические испытания отпущенных образцов выполняли в сертифицированной лаборатории ОАО «ММК-МЕТИЗ». Определение условного предела упругости с допуском на остаточную деформацию 0,1 % производили по диаграммам, записанным испытательной машиной, в соответствие с п. 4.5.1 ГОСТ 1497-84. Для выполнения требований ГОСТ 1497-84 по масштабу записи усилия (не более 10 Н/мм2), запись диаграмм производилась преимущественно на шкале 200 кН или с переключением после появления остаточной деформации на шкалу 400 кН. Измерение твердости отпущенных образцов выполнили на твердомере МТ-2. В каждой точке эксперимента реализовали по 10 наблюдений. Данные, характеризующие динамику изменения механических свойств стали 40С2 (средние значения в сериях) в зависимости от температуры и продолжительности отпуска, приведены на рис. 4.2-4.5.
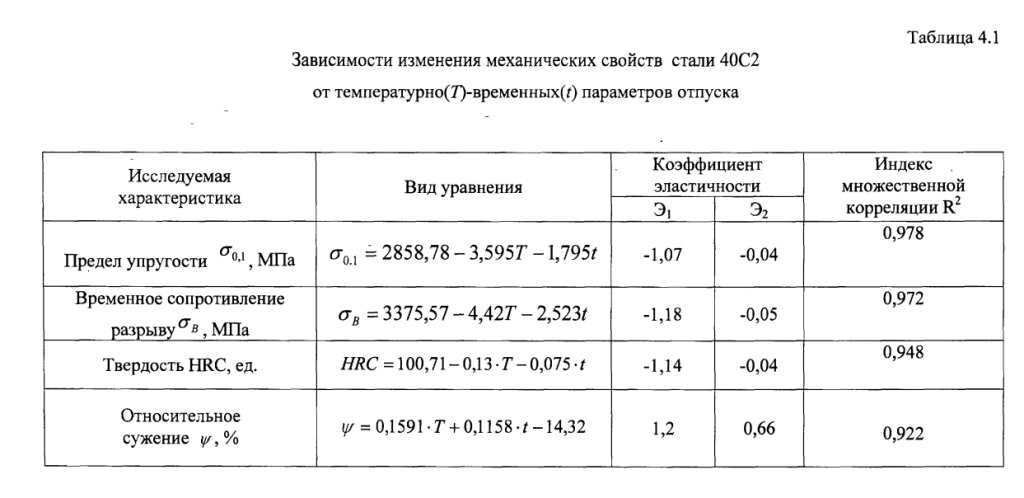
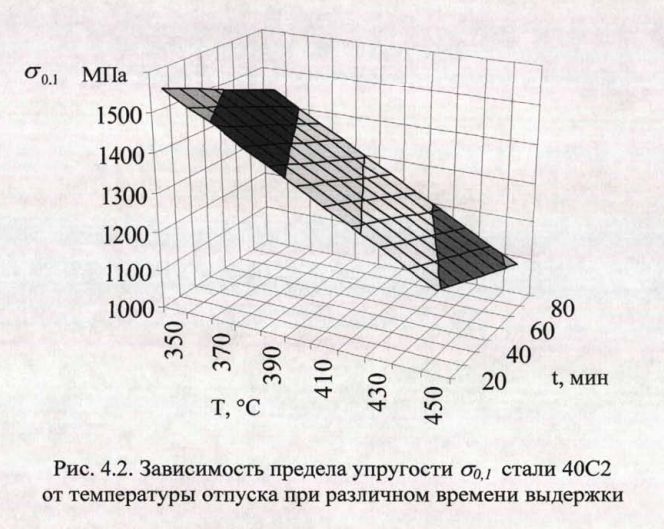
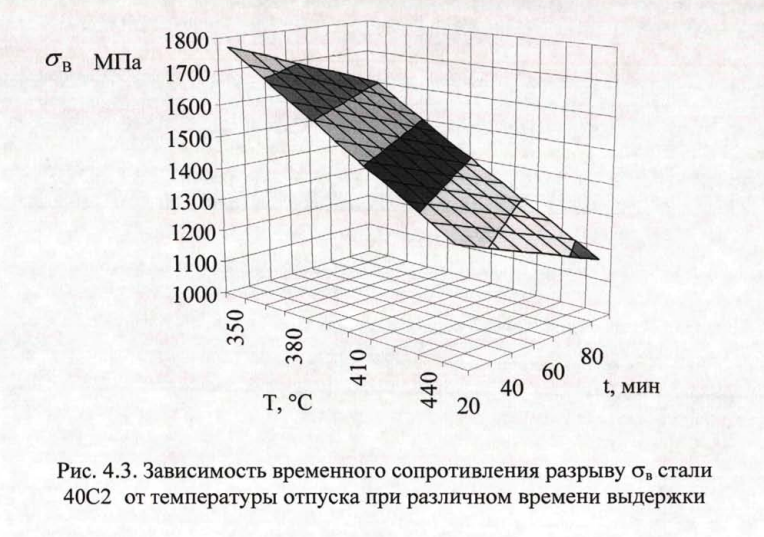
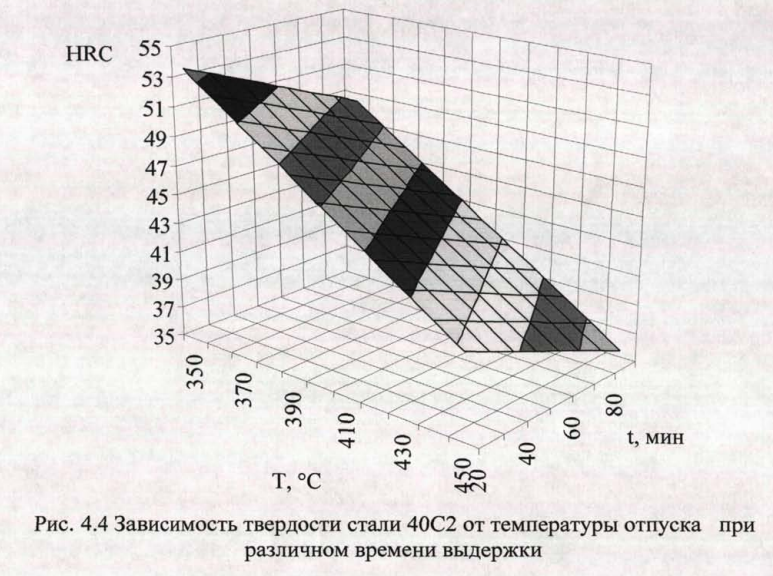
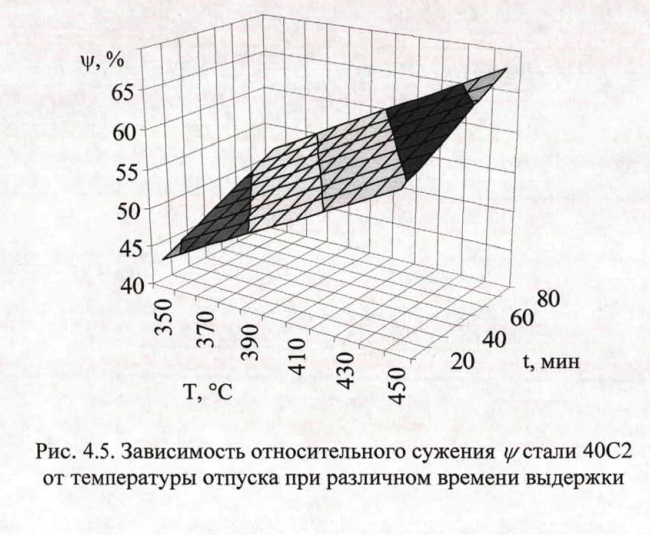
По результатам исследований, с использованием методов математической статистики и пакета программ «Statistica 6.0», получены уравнения (таблица 4.1), позволяющие прогнозировать механические свойства стали 40С2 в зависимости от температуры и времени проведения операций печного отпуска [64]. В качестве оценки адекватности моделей был рассчитан индекс множественной корреляции R2, используемый для статистической оценки тесноты связи между результативными и объясняющими показателями. Данный коэффициент выражает долю объясненной изучаемыми факторами дисперсии результативного признака и служит важной характеристикой построенной модели.
Расчеты по полученным моделям (таблица 4.1) позволяют определить температурно-временные интервалы отпуска, при которых показатели качества клемм после окончательной’термообработки полностью выходят на уровень, соответствующий требуемымзначениям..
На рис.4.6 определена область технологического пространства результативных температурно-временных режимов исполнения операции отпуска. Реализация режимов; отпуска, определяемых значениями технологических факторов температуры и время внутри подобласти ABC (рис.4.6) обеспечивает формирование требуемых показателей качества пружинной клеммы по механическим свойствам. Проекция линии АС на ось температур, определяет диапазон возможных температур отпуска от минимального 360 °С до максимального значения 440°С. Проекция линии АС на ось времени определяет диапазон времени отпуска от минимально возможного 20 мин до максимальной величины 90 мин.
В подобластях 2,3 не выполняются ограничения по температурно- временным технологическим факторам и не достигаются требуемые показатели качества изделия.
На примере показателя качества готовой клеммы «Твердость» реализация технологических режимов отпуска характерных точкам А (Т = 445°С; t = 20 мин) и С (Т = 360°С; t = 90 мин) обеспечивает получение самого низкого значения твердости, регламентированного нормативно-технической документацией – 42 HRC. В точке В (Т = 400°С; t = 20 мин) наблюдается самое высокое значение твердости – 48 HRC. В подобласти ABC показатель качества «Твердость» принимает значения от 42 до 48 HRC.
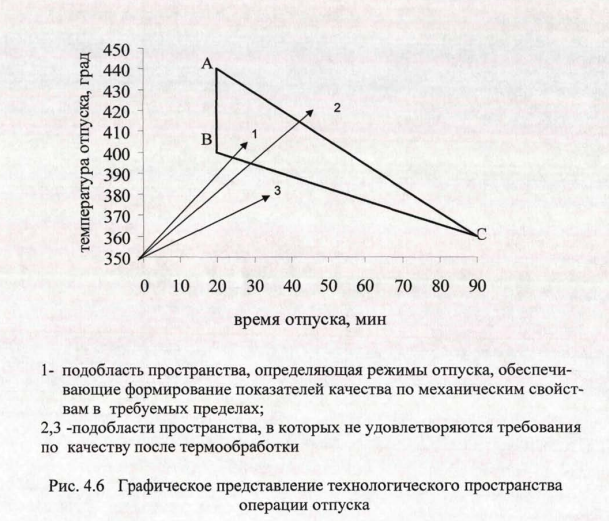
Видно, что диапазон возможных сочетаний температурно-временных технологических режимов отпуска, обеспечивающих достижение заданных значений показателей твердости достаточно широк.
По результатам статистической обработки были определены коэффициенты эластичности, показывающие степень влияния каждого из факторов на исследуемую величину [65]:
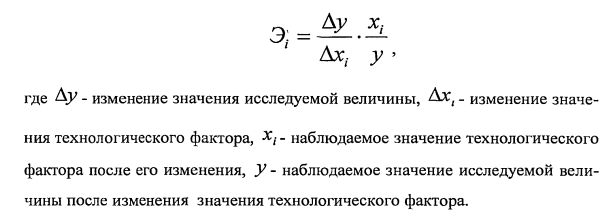
Из полученных значений коэффициентов эластичности (таблица 4.1) видно, что наиболее значительное влияние на свойства стали при отпуске оказывает температурный фактор. Так коэффициент эластичности Э1 = -1,18 показывает, что при увеличении температуры отпуска на 1% временное сопротивление стали снижается на 1,18%. Коэффициент эластичности Э2= -0,05 показывает, что при увеличении времени отпуска на 1% временное сопротивление уменьшается на 0,05%. Аналогично, на примере показателя относительного сужения, значение Э1 = 1,2 означает увеличение пластичности на 1,2 % при увеличении температуры отпуска на 1%, при этом реакция на изменение времени отпуска на 1% менее значительна, и составляет 0,66%.
Отсюда следует, что наиболее рационально управлять параметрами отпуска через температуру нагрева при минимально возможном времени выдержке (с учетом синхронизации выполнения операций закалки и отпуска в потоке), что не противоречит экономическим принципам организации производства. Полученные в данном разделе результаты позволяют обоснованно управлять режимами окончательной термической обработки клемм с достижением заданного уровня значений показателей качества готовой продукции. Конкретные значения температурно-временных параметров- отпуска на заданный уровень твердости необходимо назначать с учетом обеспечения регламентированных пружинящих свойств готовых изделий на основе изучения поведения материала клемм при контрольных испытаниях на осадку. Для этого необходимы исследования влияния твердости стали 40С2 на величину остаточной деформации петли клемм после осадки.
Исследование величины остаточной деформации петли клемм при контрольных испытаниях
Для проведения необходимых исследований были отобраны клеммы от нескольких партий после технологического блока формообразующих операций. В лабораторных условиях клеммы подвергали закалке и отпуску на различный уровень твердости по режимам, определенным по математическим моделям, приведенным в таблице 4.1. Твердость термообработанных клемм измерялась в поперечных сечениях образцов, вырезанных из испытуемых изделий по завершении работы с ними.
Исследования проводились на испытательной машине Е02-20(Германия) путем нагружения петли клемм нарастающим усилием до 40 кН с непрерывной записью кривых деформации при изменении условий нагружения по методике, описанной в работе [89]. Положение клеммы в процессе испытаний показано на рис. 4.7.
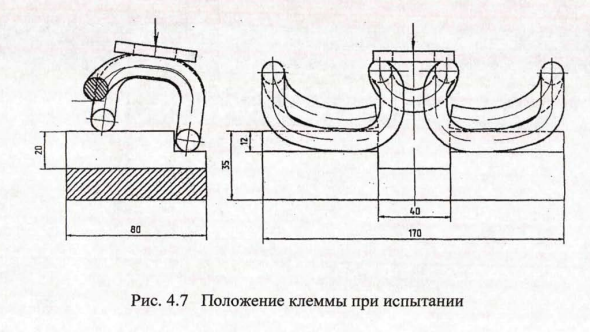
Для создания запаса свободного пространства при линейном смещении нагружаемой петли клеммы под незамкнутые концы изделия устанавливались прокладки. Высота их подбиралась таким образом, чтобы размещение клеммы на опорной поверхности соответствовало положению ее в контрольном приспособлении, применяемом для измерения размеров изделия в ходе сдаточных испытаний. После нагружения всех клемм регламентируемым нормативно- технической документацией усилием 30 кН изделия подвергались контролю остаточной деформации. Характер изменения остаточной деформации петли клеммы в зависимости от уровня твердости приведен на рис.4.8. На графике представлены средние значения, полученные по данным 10 замеров твердости испытуемых изделий. Из рис.4.8 следует, что все клеммы вне зависимости от уровня твердости после их нагружения усилием 30 кН имели остаточную деформацию в пределах от 0,4 до 1,6 мм. При этом прослеживается тенденция к росту остаточной деформации у клемм с нижним пределом твердости, требуемым нормативно-технической документацией.
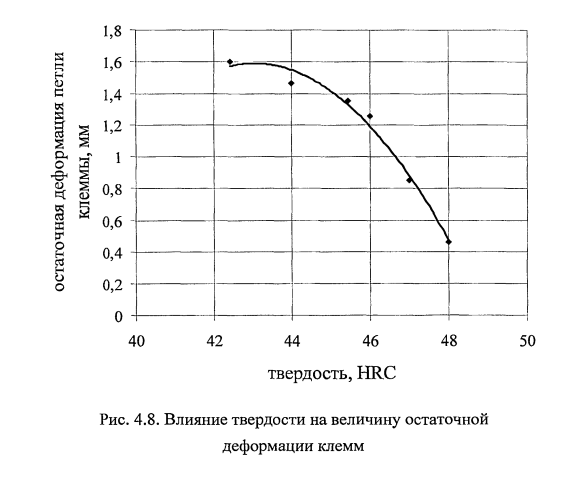
В результате обработки» экспериментальных данных было получено выражение зависимости остаточной деформации петли клеммы после снятия нагрузки ЗОкН от уровня твердости изделий после проведения операций окончательной термообработки:

Важным выводом является тот факт, что величина остаточной деформации в диапазоне изменения твердости 42-48 НЯС не превысила предельно допустимого по техническим условиям значения 2,0 мм, что подтверждает результативность выполненных исследований по совершенствованию режимов окончательной термической обработки клемм на заданный уровень твердости.
Проявление остаточной деформации в клеммах можно объяснить двумя- причинами. С одной стороны, она может быть обусловлена релаксационными процессами, протекающими в материале изделий при нагружении. Другой причиной появления остаточных деформаций может являться переход стали в пластическое состояние при нагружении клемм.
Оценка возможности упрочнения пружинных клемм при контрольных испытаниях
Пружинная клемма спроектирована с малым запасом прочности и поэтому проблема выбора способа повышения ее ресурса работоспособности без изменения конструкции клеммы и перехода на другие, более дорогостоящие стали стоит особенно актуально.
Из практики производства пружинных изделий известен «упрочняющий» эффект при пластической осадке пружин малого индекса с < 4 [40,42]. Можно предположить, что эффект от пластического упрочнения может быть получен при осадке пространственной пружины с малыми радиусами гибки, например, пружинной клеммы рельсового скрепления.
С целью анализа условий перехода в пластическое состояние и возможности упрочнения пружинных клемм малыми пластическими деформациями в процессе выполнения контрольных испытаний выполнены отдельные исследования.
На рис. 4.9 представлена экспериментальная диаграмма пластической осадки пружинной клеммы с уровнем твердости 48 НRС.

Линия 0S аппроксимирована прямой ш-п, показывающей, что в точке 8 появляется отклонение от прямолинейности и начинается пластический участок деформирования SВ. Прямолинейный участок ОЭ соответствуют условиям работы клеммы в упругой области. Изменение высоты клеммы в пределах данных участков происходит пропорционально увеличивающейся нагрузке. Регламентированный прогиб петли клеммы на величину 8,0 мм соответствует усилию прижатия 20кН, что меньше монтажного усилия. При таком усилии нагружения остаточная деформация в изделиях, как показывают опыты, не проявляется. Монтажная нагрузка в 25 кН находится еще в границах области упругой деформации. При этом петля клеммы упруго прогибается на величину порядка 11 мм. Появлению остаточной деформации соответствуют нагрузки, превышающие значение: монтажной нагрузки 25 кН. Усилие прижатия, соответствующее точке перехода из упругой области в пластическую, составляет значение 27,5 кН. С ростом нагрузки до 30кН:остаточная деформация петли клеммы существенно возрастает, что свидетельствует о переходе материала изделия в пластическое, состояние. Точка ВТ на диаграмме соответствует усилию нагружения порядка 37,5 кН, вызывающего разрушение клемм. Таким образом интервал усилий нагружения в котором возможно ожидать проявления «упрочняющего» эффекта составляет 27,5 кН-35кН.
Для реализации: этого направления пружинная клемма была повторно подвергнута осадке усилием 35кН. При этом линия упругой разгрузки В-Е на диаграмме (рис. 4.9) проходит параллельно линии упругого нагружения ш-п: и отсекает на. оси абсцисс величину остаточной деформации около 3,0 мм. После упрочнения; упругий участок повторного или рабочего нагружения ЕВ: становится значительно больше, а нагрузка до начала пластических деформаций,увеличивается с 27,5 кН до 35 кН или в 1,27 раза. Видно, что эффект упрочнения значителен.
Выполненные исследования позволяют сделать, ряд практических выводов, которые могут быть направлены на повышение качества пружинных клемм на этапе приемо-сдаточных испытаний при осадке:
-регламентированное усилие ЗОкН обеспечивает перевод материала: клемм, в пластическое состояние и инициирует «упрочняющий» эффект. Остаточная деформация клемм находится в пределах: требуемых техническими; условиями. При сборке рельсового крепления и приложения монтажной нагрузки 25 кН, которую в данном: случае можно рассматривать как повторное нагружение, материал клеммы, будет работать в условиях только упругой деформации;
– более высокие усилия нагружения до 35 Кн вызывают повышенную остаточную деформацию и могут быть использованы для упрочнения клемм которые несоответствуют требованиям технических условий по показателю качества «Высота петли» и имеют завышенные его значения;
– режимы термообработки предпочтительнее ориентировать на получение твердости клемм соответствующей верхнему пределу значений 46-48 Н11С, который обеспечивает минимальное значение остаточной деформации.
Выводы по главе
- Определен рациональный интервал закалочных температур, обеспечивающий максимальный уровень твердости стали 40С2 после закалки, что предопределяет формирование заданного уровня качества клемм при последующем отпуске.
- Получены математические модели оценки изменения прочностных и пластических показателей качества стали 40С2 в зависимости от температурно- временных факторов термического упрочнения с использованием тепла печного нагрева. Модели позволяют определить. результативное технологическое пространство выполнения операций окончательной термообработки, что позволяет обоснованно управлять процессом формирования заданного уровня качества готовых клемм;
- Установлена взаимосвязь уровня твердости термически упрочненных пружинных клемм ОПЮ5 с величиной остаточной деформации петли изделия’при контрольном нагружении регламентированным нормативно-технической документацией усилием. Это позволяет определять значения температурно- временных параметров отпуска на заданный уровень твердости стали с учетом обеспечения требуемых пружинящих свойств готовых изделий.
- Установленные закономерности динамики трансформации показателей качества стали 40С2 при термическом упрочнении и характер поведения клемм при нагружении фегламентированным усилием послужили основой для определения результативных управляющих воздействий на процессы формирования качества отформованных клемм в блоке окончательной термообработки и контроля.
Список литературы
- Корчунов А.Г., Слабожанкин Е.А. Совершенствование процесса управления качеством железнодорожных пружинных клемм // Сталь .- 2008.-№ 1 .- С.52- 54.
- Дальский А.М. Технология конструкционных материалов.- М.г. Машиностроение.-1990.- 352С.
- Белалов Х.Н., Клековкина H.A. и др. Производство стальной проволоки.- Магнитогорск.- 2005.- 543С.
- Шахпазов Х.С., Недовизий И.Н., Ориничев В.И. и др. Производство метизов.-М.: Металлургия.- 1972.- 472С.
- Корчунов А.Г., Андреев В.В., Дорогобид В.Г. Автоматизированный расчет напряженно-деформированного состояния методом линий скольжения при во¬лочении// Свидетельство об официальной регистрации программы для ЭВМ № 2006614009.
- Кидин И.Н. Термическая обработка стали при индукционном нагреве.- М.: Металлургиздат.- 1950.-289С.
- Полухин П.И. Физические основы, пластической деформации.- М.: Металлургия.-1980.- 546 С.
- Корчунов А.Г., Пивоварова К.Г., Слабожанкин Е.А.Использование малых пластических деформаций в технологических процессах формирования качест¬ва метизных изделий// Вестник МГТУ им.Г.И. Носова.- 2007.-№ 3 .- С. 52-55
- В.Г. Капорович Обкатка металлоизделий в производстве.- М.: Машиностроение.-1973.- 168С.
- Корчунов А.Г., Чукин В.В:, Пивоварова К.Г. и др. Влияние способа обработки на состояние поверхности калиброванного металла // Вестник МГТУ им.Г.И. Носова.- 2003.-№3.-С.52-55.
- Одинцов Л.Г. Упрочнение и отделка деталей* поверхностным пластическим деформированием.- М.: Машиностроение.- 1987.- 328С.
- Корчунов,А.Г., Слабожанкин-Е.А. Исследование и совершенствование про¬цессов формирования качества пружинных клемм для железнодорожных рель¬совых скреплений’ // Ползуновский альманах.-ГОУ ВПО АлГТУ(г. Барнаул)- 2007.-№ 1-2- С.89-93.
- Челищев В.Н. Повышение качества и конкурентоспособности высокопрочной арматуры диаметром-10,0 мм для железобетонных шпал на основе разработки рациональных режимов холодной деформации и термической обработки: /Дис. на соискание учен. степ, к.т.н. — Магнитогорск: МГТУ . — 2006, 113С.
- Егоров С.А. Повышение качества и производительности на операциях обточки и калибрования пруткового материала на автоматических линиях. /Дис. на соискание учен. степ, к.т.н. – Иваново:- 1995, 148С.