Сейчас ваша корзина пуста!
Автоматизированная система контроля напряженного состояния плетей бесстыкового пути
Цикл статей:
Глава 1 – Напряженное состояние рельсовой плети и методы его определения
Глава 2 – Исследование факторов, влияющих на формирование продольных сил в плети
Глава 3 – Метод определения напряженного состояния плети
Глава 4 – Автоматизированная система контроля напряженного состояния плетей бесстыкового пути
Автоматизированная система определения напряженного состояния
плетей бесстыкового пути
Принцип действия, устройство, конструкция
В главе 1 описано множество способов и устройств контроля напряженного состояния рельсов и рельсовых плетей. Эти способы основаны на фиксации изменения различных физических параметров рельса при воздействии продольной силы: изменение линейных размеров, электрического сопротивления, скорости распространения ультразвука, магнитной проницаемости, шума Баркгаузена и др. Эти способы применяются в основном для исследовательских целей, широкого использования на сети дорог они не нашли из за ряда существенных недостатков. Например, известно устройство для определения угона рельсов, защищенное авторским свидетельством SU 1786220, (автор Е.И. Соколов), заключающееся в том, что смещение рельса определяется по интервалу времени между импульсами от датчика стыкового зазора и датчика клемно-болтового соединения, при этом скорость движения устройства учитывается датчиком пути представляющим собой колесо катящееся по рельсу, соединенное со счетчиком. Недостатком этого устройства является низкая точность из-за возможного проскальзывания колеса счетчика пути по рельсу и возможность перемещения шпалы при угоне рельсошпальной решетки. К недостаткам относится и то, что удлинение рельса определяется только на его концах, в то время как при эксплуатации напряженного бесстыкового пути могут происходить подвижки отдельных ее частей (перераспределение напряжений как по величине, так и по знаку) при этом концы плети могут быть неподвижны.
Разработанная с участием автора, система позволяет исключить указанные недостатки за счет измерения подвижек по длине плети, т.е. смещение отдельных ее участков. Кроме того, повышается точность измерения подвижек плети. Этот результат достигается тем, что подвижки определяются относительно неподвижных точек расположенных по всей длине плети на определенном расстоянии друг от друга и результаты измерения не зависят от скорости движения считывающего устройства. В расчетах напряженного состояния плети принимается не средняя температура плети, а температура по каждому ее участку, измеренная в процессе движения. Эта мера вызвана тем, что при длине плети в несколько километров температура ее различных участков неодинакова.
В настоящее время на сети железных дорог России используется система контроля угона плетей по маячным шпалам [106], предполагающая визуальный контроль подвижек плети. Разработанная автором система контроля напряженного состояния плетей бесстыкового пути позволит автоматизировать процесс сбора и обработки данных о подвижках плети. Данные о распределении температуры по длине плети, деформации отдельных ее участков и величине стыковых зазоров позволят получать достоверную информацию о распределении напряжения по длине плети, а не среднее значение напряжения в ней. Затем информация о распределении напряжения по длине плети анализируется с учетом плана и профиля пути, расположения и параметров мостов, наличия участков разгона/торможения и др. Если полученное значение напряжения близко к критическому значению, то выдаются соответствующие рекомендации о производстве разрядки напряжений или ограничении скорости.
Разработанное с участием автора устройство позволяет определять смещения рельсовой плети и отдельных ее участков в автоматизированном режиме без учета скорости движения считывающего устройства посредством отслеживания изменения положения меток на рельсовой плети относительно неподвижных меток (реперов), например, опор контактной сети, маячных шпал.
Способ измерения продольных подвижек рельсовых плетей бесстыкового пути предложенный автором, осуществляется следующим образом. При укладке плети, когда плеть находится в ненапряженном состоянии, в створе реперов или возле грани подкладки маячной шпалы на плеть наносится метка.
Метки на маячных шпалах или реперах являются неподвижными, метки на плети – подвижными вследствие температурной работы плети и воздействия дополнительных сил.
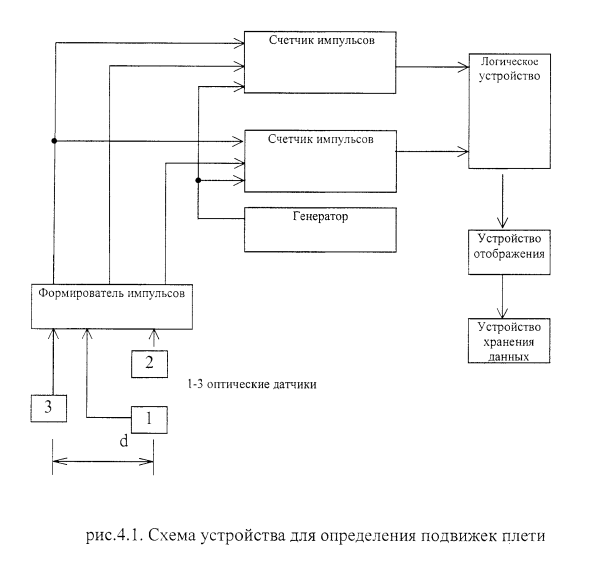
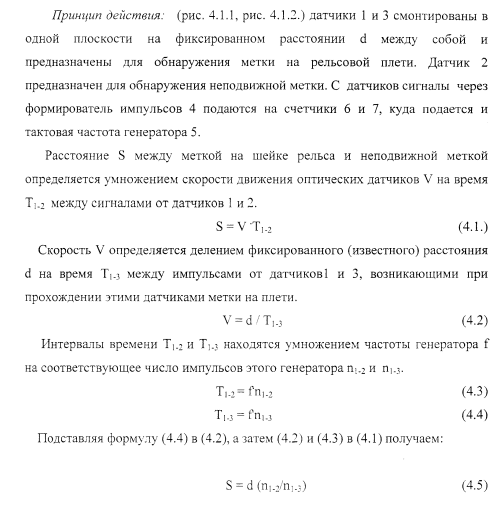
Таким образом, на определение расстояния меду неподвижной меткой и меткой на шейке рельса не влияет скорость движения датчиков.
Общая блок схема сбора и обработки данных
В автоматизированной системе контроля напряженного состояния плетей бесстыкового пути сбор и обработка данных осуществляется по схеме представленной на рис. 4.3. Сначала формируется база исходных данных путем ввода с клавиатуры ПЭВМ в табличной форме следующей информации: дорога, дистанция пути, перегон, путь, границы плети, тип шпал, рельсов, балласта, радиусы и длины кривых, расположение и параметры мостов, тип локомотива, скоростной режим, номер плети, длина плети, дата укладки, температура крепления и др., по каждому перегону формируется отдельный файл. Производится расчет теоретической эпюры продольных напряжений.
При движении вагона путеизмерителя производится запись положения (по пикетажу) и величины стыковых зазоров. В это же время производится запись значений температуры плети с определенной дискретностью и запись значений подвижек участков плети относительно неподвижных меток. По каждому перегону формируется отдельный файл результатов измерений. По результатам измерений строится эпюра дополнительных напряжений, вызванных дополнительными воздействиями. Исходя из теоретической (температурной) эпюры и эпюры дополнительных напряжений, строится результирующая эпюра, по которой можно судить о фактическом напряженном состоянии рельсовых плетей. Сопоставляя результирующую эпюру напряжений с планом и скоростным режимом поезда, особое внимание обращается на значение напряжений в критических местах, таких как: кривые, мосты, переезды, участки разгона и торможения. В случае если эти значения близки к критическим для данного типа пути, выдаются рекомендации по разрядке напряжений или ограничению скорости.
Составные части автоматизированной системы контроля напряженного состояния плетей бесстыкового пути
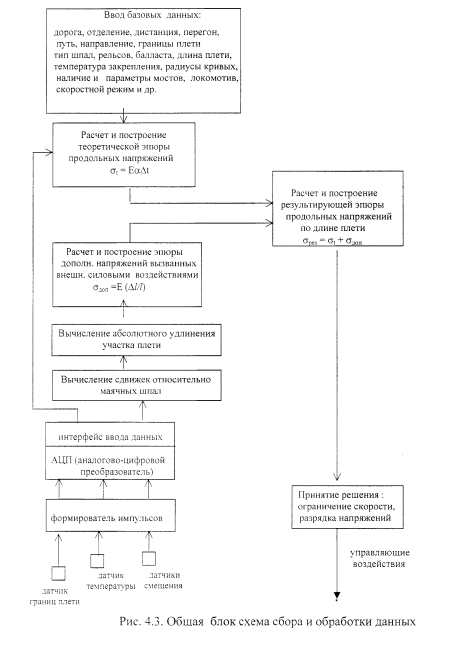
Алгоритм ввода исходной информации, структура базы данных исходной информации
Исходная информация на начальном этапе вводится с клавиатуры в ПЭВМ техническим отделом дистанции пути по каждому перегону в виде отдельного файла, представляющего собой таблицу (см. прил. 2, 3). Введя один раз данные по каждому перегону, в последствии нужно будет только вносить появляющиеся изменения и для расчетов выбрать требуемый перегон из базы данных. Исходная информация включает в себя: наименование дороги, дистанции пути, перегона, тип рельсов, шпал, балласта, пропущенный тоннаж, тип локомотива, вес поезда, уклоны продольного профиля, местоположение, тип и длина мостов, наличие переездов, положение, радиус и длины кривых, расположение станций, участков разгона и торможения. По уложенным плетям вводится следующая информация: номер плети, длина плети, дата укладки, температура закрепления, пикетажное положение начала и конца плети, дата последней разрядки напряжений (или восстановления плети) и температура закрепления. Структура отдельного файла базы данных представлена в приложениях 2 и 3.
Алгоритм ввода результатов измерения, структура базы данных результатов измерений
Алгоритм, приведенный на рисунке 4.4 позволяет обойтись без загрузки исходной информации о пикетаже концов и длине плети перед началом измерения. В этом случае производится запись величины стыковых зазоров, температуры, и смещения меток по всему пути (включая уравнительные пролеты и участки звеньевого пути). При этом сравнение получаемой информации с исходной будет производиться не в процессе измерения, а после его окончания.
Структура базы данных результатов измерения представлена в приложении.
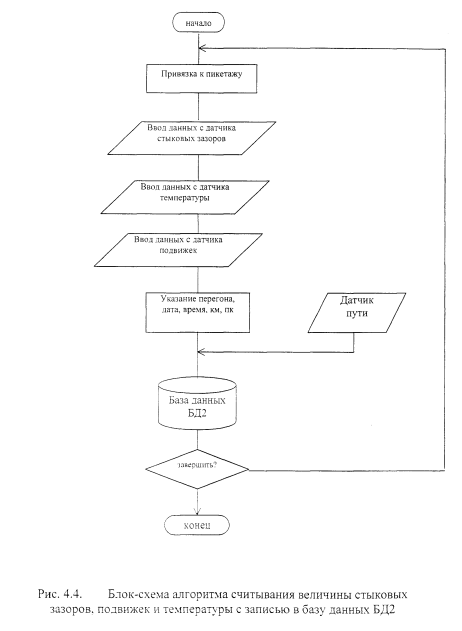
Алгоритм программы обработки информации о подвижках, температуре и границах плети
Программа при запуске предлагает выбрать файл (по интересующему перегону) из базы данных исходной информации и соответствующий ему файл из базы данных результатов измерения. Затем производится расчет критического значения напряжения (при котором может произойти выброс пути). После чего в зависимости от разности фактической температуры и температуры закрепления определяется форма теоретической эпюры. По исходным данным взятым из БД1, с учетом корректировки строится эпюра теоретических напряжений. По результатам измерения взятым из БД2 вычисляются сдвижки контрольных точек плети, по которым можно определить, что произошел угон участка плети или его деформация, после чего строится эпюра дополнительных напряжений, вызванных воздействием внешних сил. Исходя из этих двух эпюр, строится результирующая эпюра напряжений, по которой можно судить о фактическом напряженном состоянии плети, то есть распределение напряжений по длине плети. Особое внимание обращается на критические места: кривые, мосты, переезды и подходы к ним, участки разгона и торможения. Если значение напряжения по результирующей эпюре близко к критическому значению, то принимается решение о разрядке напряжений или ограничении скорости. Особое внимание следует уделить участкам торможения, так как в ряде случаев именно на них возникали выбросы пути. Ерафическое представление совмещения исходной информации с результатами измерений и расчетами напряженного состояния плетей приведено в приложении 8.
Результаты испытаний автоматизированной системы контроля напряженного состояния плетей бесстыкового пути на вагоне ЦНИИ-4М
Конструктивное исполнение опытного образца
Датчики стыковых зазоров, подвижек плети и температуры закреплены на поперечной неподрессоренной балке колесной тележки вагона путеизмерителя ЦНИИ-4МД №70001 (рис. 4.8, 4.9). Электронный блок первичной обработки сигналов с датчиков и вторичные блоки питания смонтированы в отдельном корпусе, который расположен в приборной стойке в салоне вагона и подключен к компьютеру. Электропитание опытного образца и компьютера осуществляется от генератора -220 В, 50 Гц, установленного в вагоне.
Проведение испытаний
Испытания проводились на станции Кубинка Московской железной дороги с участием автора. Перед проведением испытаний проверено: комплектность устройства и вспомогательных приспособлений; правильность сборки и монтажа узлов устройства; выполнение условий испытаний.
Для испытаний были выбраны две плети на станционном пути, на которых имитировались подвижки путем нанесения меток из катафотной пленки со смещением относительно маячных шпал (рис. 4.11). На подходе к станции Кубинка был выбран участок (с таким расчетом, чтобы скорость движения вагона по нему составляла 80…90 км/ч) и на нем наносятся две метки из катафотной пленки для проверки работоспособности системы на этой скорости.
В техническом отделе дистанции пути была собрана информация об участке испытаний: пикетажное положение концов плетей, длины плетей, температура закрепления плетей, длины и количество уравнительных пролетов, заполнены соответствующие графы таблицы 4.1 с указанием характеристик плетей и значений смещений плетей относительно маячных шпал (измеренные вручную). Сформирован файл исходной информации путем ввода в ПЭВМ данных об участке испытаний: пикетажное положение концов плетей, длины плетей, температура закрепления плетей, длины и количество уравнительных пролетов.
Непосредственно перед испытаниями измерена температура плетей, стыковые зазоры и подвижки плетей вручную. Запускалась технологическая программа проверки работоспособности опытного образца. После окончания ее работы в ПЭВМ было введено пикетажное значение (координата) положения вагона.
Было сделано восемь проездов путеизмерительного вагона по испытательному участку (по станции) с установленной скоростью. Во время проездов осуществлялась автоматизированная запись в ПЭВМ значений стыковых зазоров, подвижек плети и температуры плети с указанием пикетажа (координаты). Каждый проезд записывался в соответствующий файл.
Проезды осуществлялись в обоих направлениях для выявления повторяемости результатов измерения. Был произведен один проезд путеизмерительного вагона по испытательному участку (по перегону) со скоростью 80 км/ч для проверки работоспособности опытного образца на этой скорости. Сразу после испытаний повторялось измерение температуры плетей, стыковых зазоров и подвижек плетей вручную и заполнялись соответствующие графы таблицы 4.1.
Испытания показали, что оптические датчики автоматизированной системы способны распознавать метки из белой катафотной пленки даже на фоне свежего снега рис. 4.11, а не только на фоне темной (контрастной) поверхности рис. 4.7.
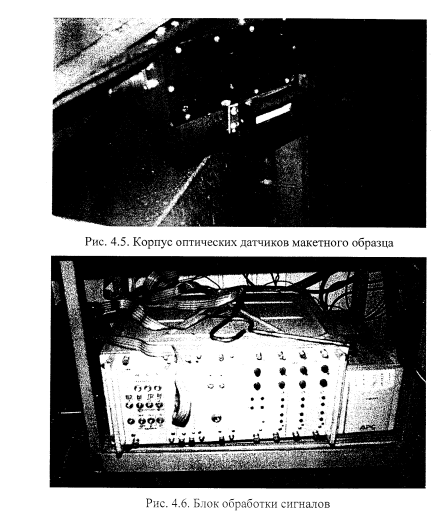
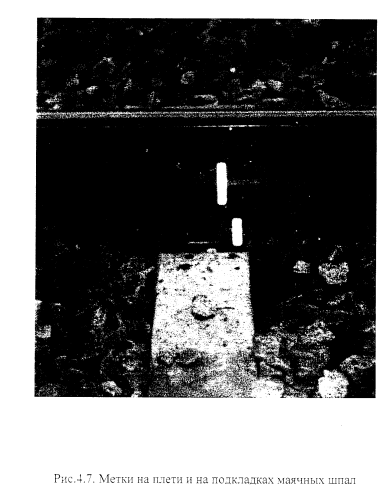
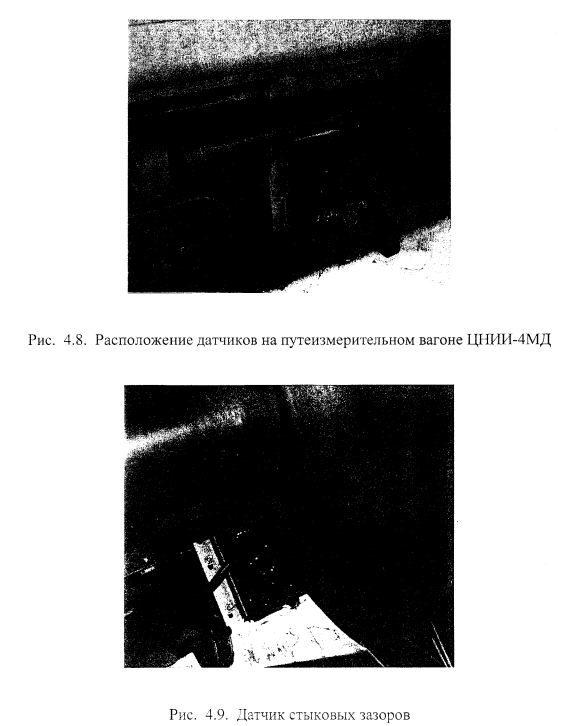
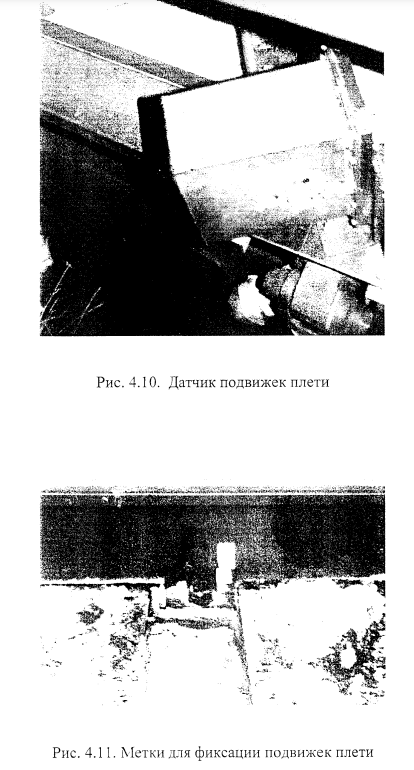
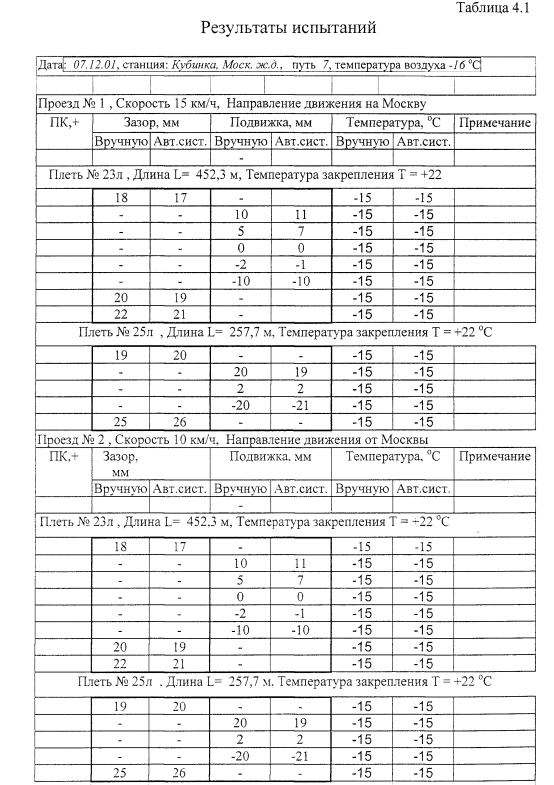
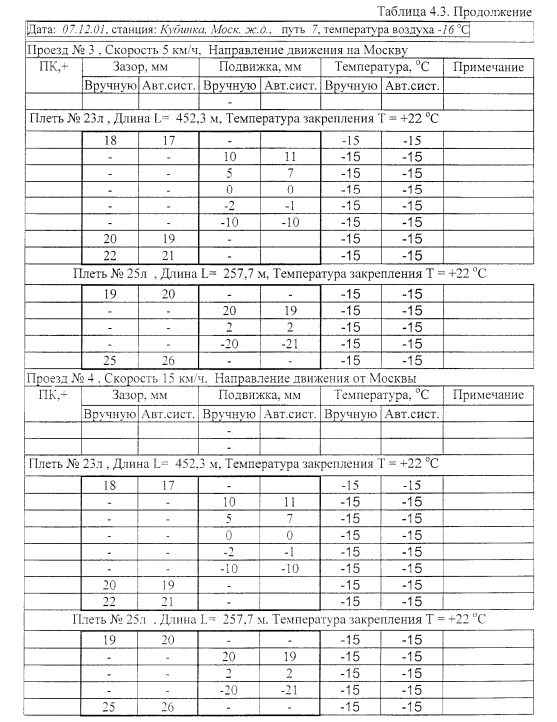
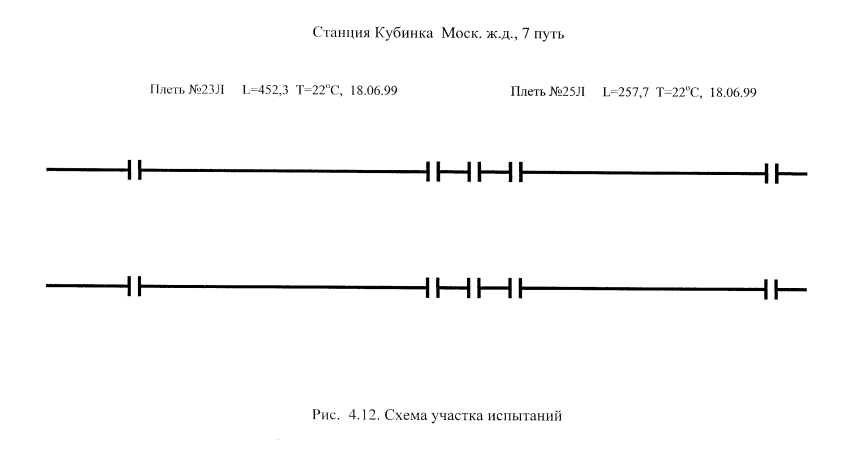
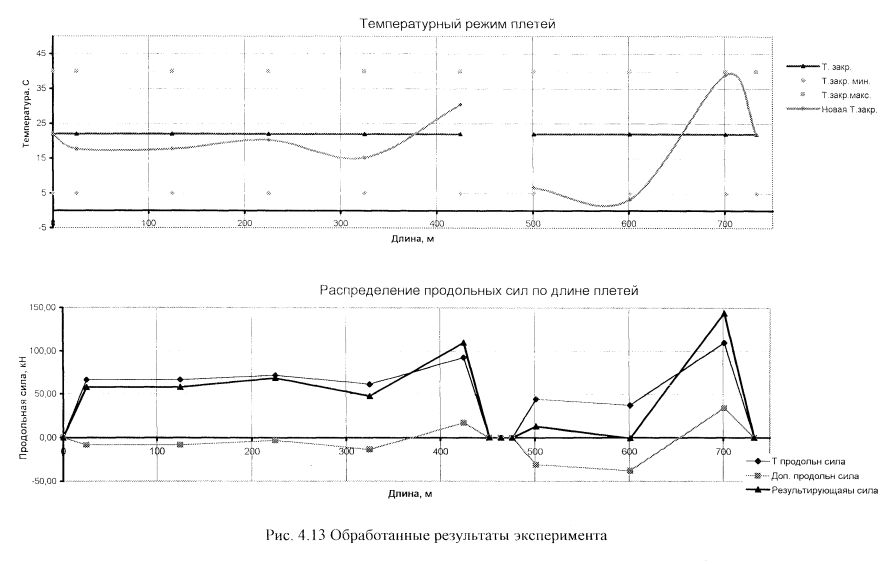
Технико-экономическое обоснование автоматизированной системы контроля напряженного состояния плетей
В качестве базового варианта (вариант 1) выбрана методика контроля подвижек плети по маячным шпалам. Эта методика предполагает измерение подвижек плети вручную миллиметровой линейкой с последующим расчетом нейтральной температуры плети. В базовом варианте контроль подвижек и расчет нейтральной температуры выполняет помощник дорожного мастера (пом. ПД) по квалификации техник с часовой тарифной ставкой 15,4 руб. в час., и сигналист с часовой тарифной ставкой 12,8 руб. в час. В расчетах примем, что в день контролируется 5 км пути (с учетом затрат времени на расчет).
Вариант 2 – это контроль напряженного состояния плетей автоматизированной системой, смонтированной на путеизмерительном вагоне ЦНИИ-4.
Вариант 3 – это контроль напряженного состояния плетей прибором КаПБсап Венгерской фирмы МЕТАЬЕЬЕКТЯО, который основан на измерении магнитного шума Баркгаузена (см. гл.1). Методика измерений предполагает нанесение меток на рельс через 5 м, в этих точках производятся измерения, скорость измерения 1… 1,5 км/ч. Повторные измерения производятся в тех же точках, когда температура рельса изменится не менее чем на 7°С по сравнению с первоначальными измерениями. Конструктивно прибор выполнен в виде двухколесной тележки, передвигающейся вручную по одной рельсовой нити, прибор имеет жидкокристаллический монитор, на котором в числовом и графическом виде отображаются значения нейтральной температуры для каждой тачки. Прибор обслуживает один человек и два сигналиста. Потребность в данных приборах – два на дистанцию пути. Стоимость прибора в 2000 г. ориентировочно составляла 40 ООО $ (по данным МАУ) или 1160 тыс. руб . В качестве базы сравнения принимается такой участок пути (протяженность или административное деление), для контроля которого используется один путеизмерительный вагон ЦНИИ-4. Как правило, на каждой дороге используется один путеизмерительный вагон.
В качестве базы сравнения выберем Московскую дорогу, так как на ней по сравнению с другими дорогами больший процент бесстыкового пути относительно общей протяженности пути – 66,4%, что составляет 8,9 тыс. км.
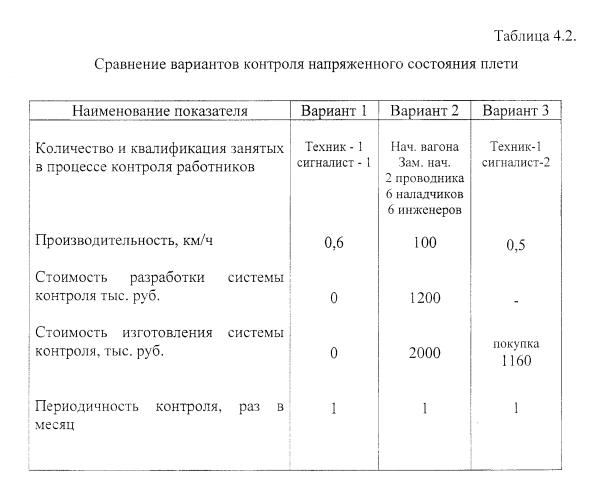
Стоимость контроля напряженного состояния 1 км пути при базовом варианте (вариант 1)
Протяженность бесстыкового пути на дороге – 8900 км. Производительность контроля – 0,6 км/ч. Часовая тарифная ставка техника 15,4 руб. в час, с учетом начислений составляет 21,6 руб. в час. (по данным ГТЧ-2). Часовая тарифная ставка монтер пути 3 разряда (сигналиста) 12,8 руб. в час, с учетом начислений составляет 17,9 руб. в час. (по данным ПЧ-2). Километр контролируется за 1,67 часа. Стоимость контроля напряженного состояния (контроль подвижек и расчет нейтральной температуры) 1 км пути составляет (21,6+17,9)*1,67 = 66 руб. Для того чтобы за месяц (176 рабочих часов) проконтролировать 8900 км необходимо (8900 / Г76)/0,6 = 85 техников и соответственно 85 сигналистов. Стоимость контроля в месяц 8900 км бесстыкового пути составит (21,6+17,9)Т76-85 = 590 920 руб.
Стоимость контроля напряженного состояния 1 км пути при помощи автоматизированной системы на ЦНИИ-4 (вариант 2)
Средняя зарплата обслуживающего персонала в месяц тыс.руб. – 3 Состав обслуживающего персонала – 16 чел Срок службы оборудования, лет – 5
Стоимость эксплуатации вагона в месяц составляет 350 тыс.руб. (по данным ПЖ Прогресс и ЦНИИ-4 №5)
Стоимость контроля 1 км пути вагоном ЦНИИ-4 составляет 39,3 руб. при этом доля затрат на контроль напряженного состояния пути составляет примерно пятую часть от затрат на контроль вагоном всех параметров пути
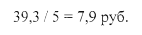
Стоимость контроля напряженного состояния 1 км пути прибором ЯаП8сап (вариант 3)
Состав обслуживающего персонала – 1 техник и 2 сигналиста. Часовая тарифная ставка техника 15,4 руб. в час, с учетом начислений составляет 21,6 руб. в час. (по данным ПЧ-2).Часовая тарифная ставка монтер пути 3 разряда (сигналиста) 12,8 руб. в час, с учетом начислений составляет 17,9 руб. в час. (по данным ПЧ-2). Срок службы оборудования 5 лет. Стоимость прибора – 1160 тыс. руб. (по данным МАУ). Производительность по двум рельсовым нитям – 0,7 км/ч. Километр контролируется за 1,4 часа. Для контроля
бесстыкового пути по всей дороге при двух приборах на дистанции пути потребуется
8900/0,7/37-2 = 172 часа = 22 рабочих дня Стоимость контроля 1 км составляет:
(21,6+17,9+17,9)*1,43 = 82 руб. Стоимость эксплуатации прибора в месяц:
Выбросы бесстыкового пути и изломы плети за 1995-1999г.
(21,6+17,9+17,9)*176*37*2 = 747 577,6 руб.
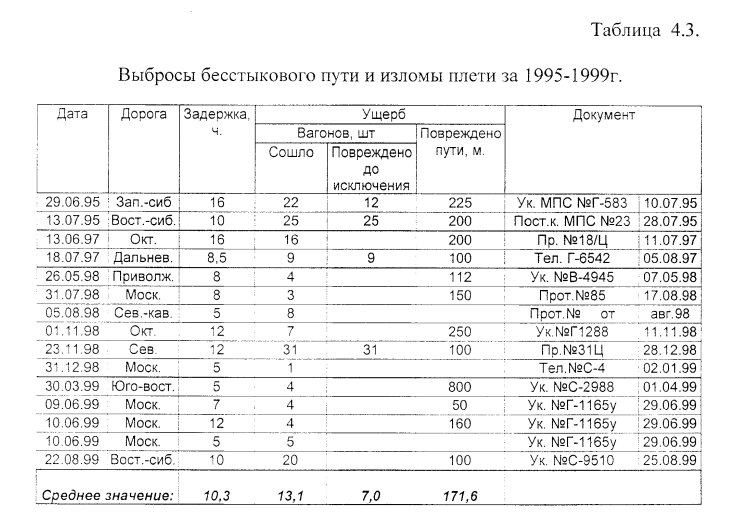
Расчет убытков (в среднем) от одного выброса пути
977,38 руб. – стоимость часа задержки в движении поездов;
1226 руб. – усредненная стоимость восстановления 10 м пути (резка автогеном, рихтовка, выпиловка части плети, замена выпиленной части инвентарными рельсами, планировка балласта );
40000 тыс. руб. стоимость одного вагона (полувагона, цистерны, платформы…) в среднем;
408,52 – стоимость остановки + простоя грузового поезда ( среднее значение ПЧ – 2 Московской ж.д.), руб ;
435,64 – стоимость остановки + простоя пассажирского поезда ( по данным ПЧ – 2 Московской ж.д.), руб ;
66,61 – стоимость остановки + простоя пригородного поезда (по данным ПЧ – 2 Московской ж.д. ), руб ;
12,80 – средняя заработная плата монтера пути в час ( калькуляция отделения экономики ВНИИЖТ), руб.
19,3 – средняя заработная плата бригадира пути в час ( калькуляция отделения экономики ВНИИЖТ ), руб.
25,6 – средняя заработная плата дорожного мастера в час ( калькуляция отделения экономики ВНИИЖТ), руб.
15,4-средняя заработная плата помощника дорожного мастера в час ( по данным ПЧ – 2 Московской ж.д.), руб ;
Стоимость остановки и простоя одного поезда на промежуточной станции равна С1 = Сост. + Сет.
Для расчетов примем, что в течении одного часа простаивают : один пассажирский ( ЧС 7 ) и один грузовой поезд ( ВЛ – 80 ), а также два пригородных поезда ЭР22.
Расходы по задержкам поездов зависят от следующих основных факторов: продолжительность задержки; среднесуточных размеров движения грузовых 1Чгр и пассажирских Мп поездов на участке; массы поездов брутто; ходовой скорости, скорости и времени предупреждения; доли поездов, направляемых по неправильному пути; удаленности ремонтируемого участка от станции; возможности отцепки локомотивов при простое поездов на станциях; возможности остановки поездов на перегонах.
Время простоя поездов и их количество при разной продолжительности перерыва движения отражены в таблице: при условии, что работы ведутся на двухпутных линиях, оборудованных автоблокировкой.
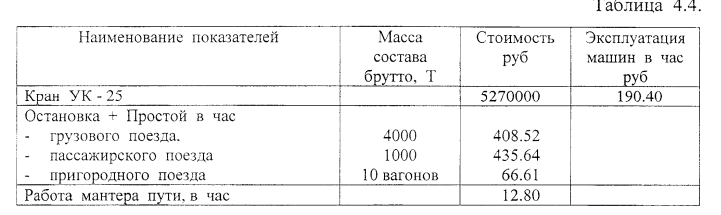
Средняя стоимость ликвидации последствий одного выброса пути
Задержка в движении поездов: 977,38*10 = 9,8 тыс. руб. Восстановление пути после выброса: 1226*171,6 = 210,4 тыс. руб. Исключение подвижного состава: 40000*7 = 280000 тыс. руб.
9,8 + 210,4 + 280000 = 280220,2 тыс. руб. Годовой экономический эффект определяется как разность затрат на контроль напряженного состояния при различных вариантах контроля. При этом учитываются затраты на разработку (проектирование) и изготовление средств контроля для нового варианта.
Затраты на контроль 8,9 тыс. км. бесстыкового пути ежемесячно в течении года
- для базового варианта: 53,4-12 = 640,8 тыс. руб.
- для автоматизированной системы контроля: 1200+2000+350-12 = 7400 тыс. руб.
- для прибора ЯаИЗсап:
1160*30*2 = 69600 тыс. руб. – стоимость всех приборов 30*8*24*12*30*2 = 4147,2 тыс. руб. – зарплата всех техников в год 69600 + 4147,2 = 73747,2 тыс. руб.
280220,2 тыс. руб. – Средняя стоимость ликвидации последствий одного выброса пути
Экономический эффект между первым и вторым вариантом:
Э = 640,8 – 7400 + 280220,2 = 273461 тыс. руб. Экономический эффект между вторым и третьим вариантом: Э – 73747,2 – 7400 = 66347,2 тыс. руб.
Выводы
Эксплуатационные испытания опытного образца автоматизированной системы контроля напряженного состояния плетей показали возможность ее использования для оценки устойчивости пути.
Отказов и ложных срабатываний устройства измерения подвижек плети и устройства определения стыковых зазоров не зафиксировано.
Точность измерения температуры ± 2°С.
Точность измерения стыковых зазоров ±1 мм.
Точность измерения подвижек плети ±2 мм.
Конструктивное исполнение блока датчиков подвижек плети и электронного блока обработки сигналов с него, позволяют использовать это устройство даже при наличии снежного покрова. На снег датчик не реагирует.
По сравнению с макетным образцом существенно повышена чувствительность и помехозащищенность устройства измерения подвижек плети.
Заключение
Применение бесстыкового пути является одним из эффективных способов улучшения технического состояния пути и уменьшения расходов на его содержание. Укладка и эксплуатация бесстыкового пути в точном соответствии с техническими указаниями обеспечивает его надежную работу в расчетном интервале температур. Контроль температурного режима плетей, предусмотренный этими указаниями, является трудоемким и потому неэффективным. В целях снижения эксплуатационных расходов на содержание пути и повышения безопасности движения автором разработан ряд предложений по диагностике напряженного состояния бесстыкового пути.
- Анализ возможности использования различных приборов для контроля напряженного состояния плетей бесстыкового пути показал, что в настоящее время нет достаточно надежных аппаратных средств, позволяющих диагностировать напряженное состояние плетей с высокой производительностью. Существует множество математических моделей и методов расчета напряженного состояния бесстыкового пути, но эти методы приемлемы только для исследовательских целей. Pix нельзя использовать для диагностики устойчивости действующего бесстыкового пути в больших объемах.
- Исследование факторов, влияющих на устойчивость бесстыкового пути, позволяет сделать вывод о том, что наиболее информативными параметрами его состояния являются: температура закрепления плети; фактическая температура по длине плети; продольные подвижки участков плети. Разработанные в диссертации средства диагностики напряженного состояния бесстыкового пути учитывают именно эти параметры. При дальнейшем совершенствовании методов и средств диагностики бесстыкового пути необходимо учесть: неровности пути в плане; очертание балластной призмы; пропущенный тоннаж.
- В настоящей работе автором показана возможность определения напряженного состояния рельсовых плетей с учетом ее продольных и поперечных подвижек. По ней определяется:
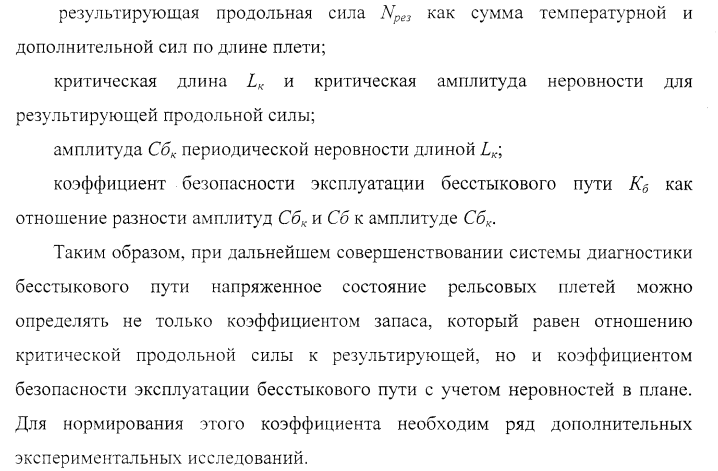
- Предложенная автором автоматизированная система контроля напряженного состояния рельсовых плетей бесстыкового пути устанавливается на путеизмерительном вагоне ЦНИИ-4МД. Все датчики, входящие в систему, являются бесконтактными. Информация с датчиков обрабатывается и хранится в ПЭВМ. Это позволяет повысить точность измерения и обработки данных. Испытания показали, что автоматизированная система позволяет производить измерения на скорости до 100 км/ч. Таким образом, производительность контроля многократно возрастает.
- Периодическая диагностика напряженного состояния плетей способствует предотвращению выбросов бесстыкового пути. Это позволяет сократить эксплуатационные расходы на содержание пути, повысить безопасность движения и расширить полигон укладки бесстыкового пути.
Список литературы
- Оптико-механический тензометр для определения продольных сил в бесстыковом пути – Duetche Eisenbachntechnick, 1971, N19, s.390-393, пер.с нем.
- Оценка ультразвуковых способов проверки собственных напряжений в железнодорожных рельсах на заводе “Гута Котовице” // Информационные материалы. Варшава, 1985. 12 с.
- Оценка устойчивости бесстыкового пути / Э. П. Исаенко. А. Б. Васильев, А. К. Кимбасов, М. В. Безруков // Конечноэлементные модели расчета железнодорожного пути на прочность и устойчивость: Сб. статей. М.: Гудок, 1997. С. 86 – 95.
- Першин С. П. Метод расчета устойчивости бесстыкового пути //’ Тр. МИИТ. Вып. 147: Путь и путевое хозяйство. М., 1962. С. 28 – 97.
- Першин С. П. Температурные воздействия на рельсовый путь и их влияние на его устройство и условия эксплуатации /7 Вопросы бесстыкового пути: Тр. МИИТ. Вып. 318. М.: Транспорт, 1969. С. 3 – 135.
- Покацкий В. А. Угон бесстыкового пути в условиях обращения длинносоставных поездов и разработка предложений по его предотвращению. Диссертация на соискание ученой степени кандидата технических наук. М.: ВНИИЖТ, 1990
- Першин С. П. Определение смещений концевого участка бесстыкового пути /У Вестник ВНИИЖТ. 1960. № 6. С. 52 – 54.
- Проведение комплекса исследований по созданию системы высокоскоростного железнодорожного транспорта и технических средств для этой магистрали: Отчет о НИР ВНИИЖТ МПС. H.H. Путря. Инв. № I- 93а.-М.: 1991. 67 с.
- Путря H.H. Диагностика напряженного состояния и обеспечение устойчивости и прочности бесстыкового пути. // Вестник ВНИИЖТ, №6, 1994, С. 3-8.
- Поляков В.Е., Сборовский А.К. Ультразвуковой контроль качества конструкций – Д., Судостроение, 1978, 238 с.
- Прибор для измерения напряжений в рельсах бесстыкового пути RailScan / Приборы для контроля пути и колес. Информационный листок – Graw, Варшава, 1999, 7 с.
- Причины и характер расстройств рельсовой колеи железнодорожного пути и особенности его проверки / О. П. Ершков, Г. П. Евдаев. Г. П. Власенко, М. Г. Зак // Тр. ВНИИЖТ. Вып. 628. М.: Транспорт, 1980. С. 5-41.
- Приборы и методы неразрушающего контроля. Информационный листок. – М.: РКК. 2000. 1с.
- Разработка алгоритма программного обеспечения устройства сопряжения датчика температуры плети для совместной работы с системой контроля подвижек плети и системой обнаружения границ плети. Савин A.B. Отчет о НИР ВНИИЖТ МПС. Инв. № 1-171. М.: 2000. 22 с.
- Разработка дополнительных требований к устройству и содержанию бесстыкового пути с плетями длиной до перегона и совершенствование системы контроля их напряженного состояния (линия С.Петербург-Москва).
Анализ новых технических средств контроля напряженного состояния бесстыкового пути. Рекомендации по совершенствованию системы контроля. Виногоров Н.П. Отчет по НИР, ВНИИЖТ МПС, Архив ВНИИЖТ № 1-136, М.: 1997. 35 с. - Ройтман В.И., Коновалов О.С., Головко A.C. и др. Магнитный контроль механических свойств материала труб феррозондовыми коэрцитиметрами. // Дефектоскопия, 1982, №11, С.39-45.
- Разработка и внедрение новой технологии разрядки температурных напряжений в плетях бесстыкового пути и усовершенствованной системы контроля за продольными силами в них. Новакович В.И. Отчет о НИР РИИЖТ МПС (заключительный). Архив РИИЖТ № 3930. Ростов, 1986. 44 с.
- Савин A.B. Определение продольно-напряженного состояния бесстыкового пути //Вопросы работы железнодорожного транспорта в условиях реформирования: Сб. науч. тр./ Под ред. канд. техн. наук В.М. Богданова и д-ра техн. наук Г.В. Гогричиани. – М.: Интекст, 2001. с. 125-129
- Сакмауэр JI. Расчет бесстыкового пути на действие продольных сил // Eisenbahntechnische Rundschau. 1960. Т VIII. № 8. S. 389 – 397.
- Система диагностики рельсов RAILCHECK // Железные дороги мира — 1999, № 9 с.65-67, D, Maiwald et al Eisenbahningenieur, 1998, № 7, S. 33 – 37.
- Технические указания по устройству, укладке, содержанию и ремонту бесстыкового пути / МПС России. М.: Транспорт, 2000. 96 с.
- Технические указания по расшифровке записей путеизмерительных вагонов, оценки отступлений от норм содержания рельсовой колеи железнодорожного пути, мерам по обеспечению безопасности движения поездов при их обнаружении. Департамент пути и сооружений МПС РФ. ЦП- 515. М.: Транспорт, 1999. 55 с.
- Токарева А. Е., Перегудова М. В. Фактические температурные режимы эксплуатации бесстыкового пути на дорогах сети // Совершенствование конструкций бесстыкового пути: Тр.ВНИИЖТ. М.: Транспорт, 1988. С. 126¬129.
- Устройство для измерения продольных перемещений рельсовой плети железнодорожного пути. A.C. № RU 2174082 С1 /Виногоров Н.П., Савин
A. B. №2000127662/28; Заявл. 08.11.00; Опубл. 27.09.01. – Бюл.№ 27,- Зс. - Ультразвуковой измеритель напряжений UMN-10. – Информационный листок исследовательского институту техники транспортных проблем ПНР, “Techpan”, 1 л., 1 илл., г.Варшава, 1985. 5 с.
- Управление надежностью бесстыкового пути / B.C. Лысюк, В.Т. Семенов,
B. М. Ермаков, Н.Б. Зверев, J1.B. Башкатова; под ред. B.C. Лысюка, М.: Транспорт, 1999. 373 с. - Шиладжян А. А. Устойчивость щебеночной балластной призмы, обработанной вяжущими материалами: Кандидатская диссертация. М.: ВНИИЖТ, 1986. 176с.
- Шур Е. А. О выборе допускаемых напряжений при прочностных расчетах рельсов// Вестник ВНИИЖТ. 1977. № 8. С. 38 -41.
- Эгл Д.М., Брей Д.И. Использование эффекта акустической упругости для измерения напряжений, действующих в железнодорожных рельсах – “Materials Evaluation”, 1979, N4, р.41-46,55.
- Энгель Э. Устойчивость бесстыкового пути в условиях изменения температуры / Перевод ЦНТБ МПС П-8314. 41 с.
- Экспериментальное изучение устойчивости бесстыкового пути. Бромберг Е.М. // Тр. ВНИИЖТ. Вып. 244. М.: Трансжелдориздат. 1962. С. 129 – 163.
- Эксплуатационная проверка и корректировка (на основе исследования) временных технологических процессов на укладку и содержание бесстыкового пути с плетями более 950 м. Виногоров Н.П. Отчет о НИР ВНИИЖТ МПС тема 600-П-84. р.2. Архив ВНИИЖТ № 1-79, 1984. 104 с.
- Hengstrum van , L, A. Finite Element Analysis of Track Stability//’ Rail Engineering International. 1987. № 4. P. 19 – 20.