Сейчас ваша корзина пуста!
Оценка и прогнозирование надежности элементов верхнего строения железнодорожного пути
Цикл статей:
Глава 1 – Анализ методов управления техническим состоянием пути на основе оценки его надежности, рисков, наличия ресурсов
Глава 2 – Оценка и прогнозирование надежности элементов верхнего строения железнодорожного пути
Глава 3 – Ресурсное обеспечение ремонтов и текущего содержания пути в течение жизненного цикла
Глава 4 – Оценка стоимости жизненного цикла верхнего строения пути
Основные положения теории надежности
Основные понятия и термины
Верхнее строение пути, как конструкцию, обеспечивающую безопасность движения поездов, необходимо рассчитывать не только на прочность, но и на надежность.
Термины и определения основных понятии надежности для применения в науке и технике установлены действующими стандартами.
Объект – предмет определенного целевого назначения. В нашем случае это верхнее строение пути (ВСП) или его элементы.
Отказ – событие, заключающееся в нарушении работоспособности объекта.
В зависимости от назначения и характера функционирования объекты подразделяются на невосстанавливаемые и восстанавливаемые (ремонтируемые) в процессе применения.
Надежность есть свойство ВСП выполнять заданные функции (пропускать поезда), сохраняя эксплуатационные показатели в заданных пределах в течение требуемых промежутков времени или наработки в млн т брутто.
Наработкой называется продолжительность или объем работы ВСП.
Безотказность – это свойство ВСП непрерывно сохранять работоспособность в течение некоторого времени или некоторой наработки.
Долговечность – свойство ВСП сохранять работоспособность до наступления предельного состояния при установленной системе технического обслуживания.
Вероятность безотказной работы за время или наработку t:
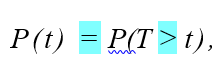
где t – текущее значение наработки; Т – наработка до первого отказа.
Функция распределения наработки до отказа F(t) есть вероятность отказа (ГОСТ 27.002-2015).
Исправная работа и отказ в течение времени t образуют полную группу событий, поэтому:
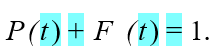
Плотность вероятности наработки до отказа:
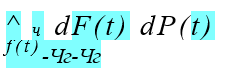
Из э т следует, что величина f(t)dt определяет вероятность dF(t) отказа объекта:
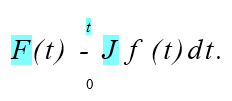
Если известен закон распределения t, то можно определить математическое ожидание наработки ВСП до первого отказа mt или среднюю наработку до отказа Тср:
Тр P(t)dt -\tf (t)dt.
По статистическим данным Тср вычисляется по формуле:
P(t) + F (t) = 1.
Плотность вероятности наработки до отказа:
^ ч dF(t) dP(t)
f(t)-Чг-Чг
Из формулы следует, что величина f(t)dt определяет вероятность dF(t) отказа объекта:
F(t) – J f (t)dt.
Если известен закон распределения t, то можно определить математическое ожидание наработки ВСП до первого отказа mt или среднюю наработку до отказа Тср:
Тр P(t)dt -\tf (t)dt.
По статистическим данным Тср вычисляется по формуле
T – 5L, ср – N0 ‘
где N0 – число испытуемых образцов.
Рассеивание случайной величины t определяется с помощью дисперсии:
D-J(t – ТсрJ f (t)dt.
Статистическая оценка дисперсии:
No (t – T )2
D-S V-T
i-1 N0 1
Расчеты удобно производить, используя центрированную и нормированную функцию. Для этого заменяют переменную ? другой величиной:
^ = (г _ Т;р)/ а,,
а величину среднего квадратичного отклонения принять аг = 1
Плотность распределения этой функции:
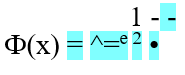
Интегральная функция
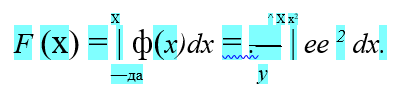
Значения функции F0(x) приводятся в таблицах обычно при х > 0. Если x оказывается отрицательным, то используют зависимость:

Оценка надежности по усеченной выборке отказов
Эксплуатировать объекты, связанные с безопасностью движения, до полного отказа всех элементов невозможно, поэтому используют усеченные выборки.
В этом случае параметры Тср и Gt определяют по методу квантилей UP. Значения функций F0(Up) = P и соответствующие ей значения Up и tt можно определить
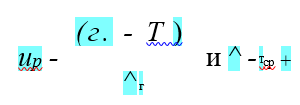
Индекс Р означает «вероятность», показатель ир находится по таблицам квантилей.
Вероятность отказа элементов ВСП после наработки V.
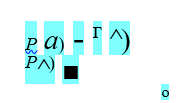
Далее по значениям Е^) определяют квантили иР по специальной таблице и составляют г уравнений:
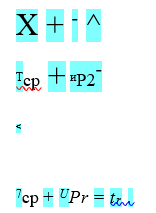
Полученную систему уравнений решают по методу наименьших квадратов, для чего из системы составляют два уравнения:
ТСр JüPl +vt JüPl 2 = ^иРг,г, (1)
V + at ZUPr = Z ti. (2)
Уравнения решают относительно неизвестных Тср и Gt. Проверка доверительных границ (95 %) определенных параметров Тср и Gt производится по формулам:
тср(тах/тт) = + 2ст(77ср X <5t (max/ min) = at + 2а(а?).
В зависимостях значения а(Тср) и a(öt) определяются по формулам
2 2 ст2(7сР) = ^f2(k); а2(а,) = ^¿(k),
,где к – коэффициент усечения выборки
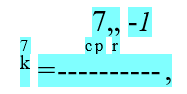
N0 – количество обследуемых рельсов на данном участке.
Показатели долговечности
Ресурсом называется наработка ВСП от начала эксплуатации после реконструкции до предельного состояния.
Характеристикой долговечности ВСП также является гамма-процентный ресурс Ят. Это наработка, в течение которой ВСП не достигает предельного состояния с заданной вероятностью у. Частота этой вероятности Я(ЯУ) определяется из отношения Р(Яу ) = у/100.
Риски неблагоприятных событий вследствие отказа технических средств
Понятие риска относится к числу философских категорий. Оно широко используется в обыденной жизни, в точных науках его стараются вычислить (определить значащим числом). В общем случае это значит, что ожидается некоторое неблагоприятное событие или какая-то «нехорошая» ситуация, и они, такого рода события или ситуации, могут произойти по любой причине: зависящей от нас (и тогда эта причина субъективна) либо не зависящей (и в таком случае она объективна).
Под приемлемым риском понимают такой, который можно считать допустимым.
Риск Я содержит некоторую меру случайности события Р и меру ущерба Н, т.е. * = (Р н X)
Одним из оперативных показателей оценки риска является * = н (1 _ п, где (1 – Р) – вероятность возникновения неблагоприятного события
Если при чрезвычайном происшествии известна вероятность Р{ для N летальных исходов, то риск представляется как * = рЛ
Форс-мажорные обстоятельства
Влияние форс-мажорных обстоятельств на величину риска учтем с помощью диалектической функции 5(?) , т.е. ВД,) = р5 (г) (2.28).
Диалектическая функция имеет вид:
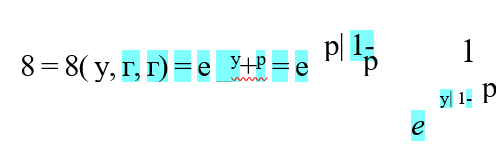
где параметры повреждающих явлений и факторов в и параметры упрочняющих явлений и факторов у:
Р = Р( , г), (2.30)
У = У(Уl, У2,…У, г). (2.31)
В крайних случаях диалектическая функция распадается на функцию (рисунок 1) 5у= е”‘ (2.32), и функцию разупрочнения (при у = 0) 5„ = ер (2.33):
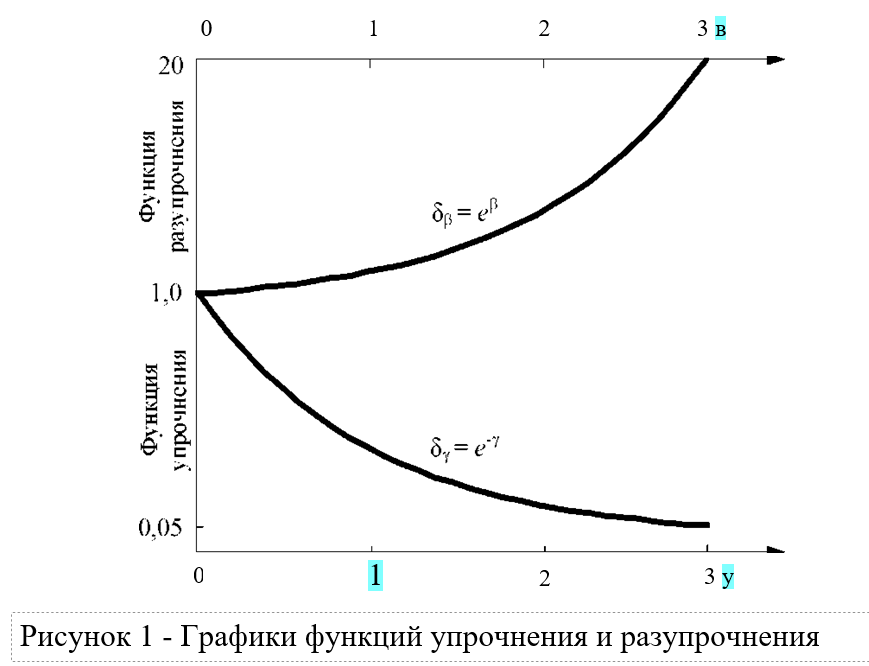
Общие закономерности развития процессов упрочнения-разупрочнения, прогнозируемые уравнениями (2.32) – (2.33), таковы. С одной стороны, рост параметра в ведет к нарастающему увеличению функции разупрочнения (2.33). С другой стороны, как бы не увеличивалось значение параметра у, функция упрочнения (2.32) оказывается затухающей – она асимптотически приближается к нулю, никогда его не достигая. И поэтому, когда оба параметра растут, система всегда идет к разупрочнению и далее к полной деградации, в том числе и взрывным способом (рисунок 2). Следовательно, упрочнение – явление ограниченное, его степень всегда конечна. А разупрочнение – явление неограниченное, его степень может расти до бесконечности, например, вплоть до разложения твердого тела.
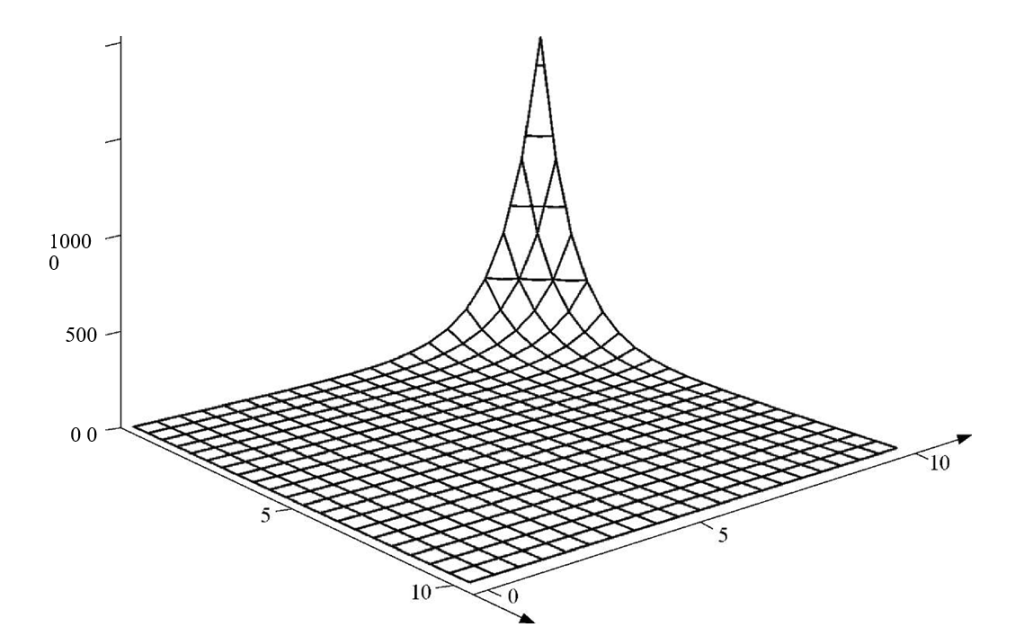
Рисунок 2 – Диалектическая функция, описывающая влияние форс-мажроных обстоятельств на состояние системы
Функции (2.30) и (2.31) конкретизируют применительно к анализируемым условиям развития событий (ситуаций), по характерным признакам которых оценивается риск.
В более общем понимании параметр в в (2.29) есть, подобно (2.30) , функция неблагоприятных явлений и факторов (в одной из работ ее называют, при анализе развития общества, функцией параметров смуты), а параметр у есть, подобно (2.31), функция благоприятных явлений и факторов (в одной из работ ее называют, при анализе развития общества, функцией параметров благополучия). И тогда формулы (2.29)-(2.33) оказываются применимыми и к различным явлениям, событиям, ситуациям в природе и обществе.
Исходя из этого тождества, заключаем, что любое «упрочнение» объекта есть, по существу, обеспечение его «безопасности».
Состояние и перспективы инновационного развития рельсового хозяйства
Рельс является самым уязвимым элементом ВСП, так как при его отказе резервирование не предусмотрено. Надежность рельсов определяется не только качеством их изготовления, но и эксплуатационными условиями. Одновременно с изменением грузонапряженности железных дорог происходит измерение нагрузок подвижного состава на рельсы.
Так падение грузонапряженности в период с 1992 по 1998 год вызывало снижение числа изымаемых с пути остро дефектных рельсов (ОДР) (рисунок 3).
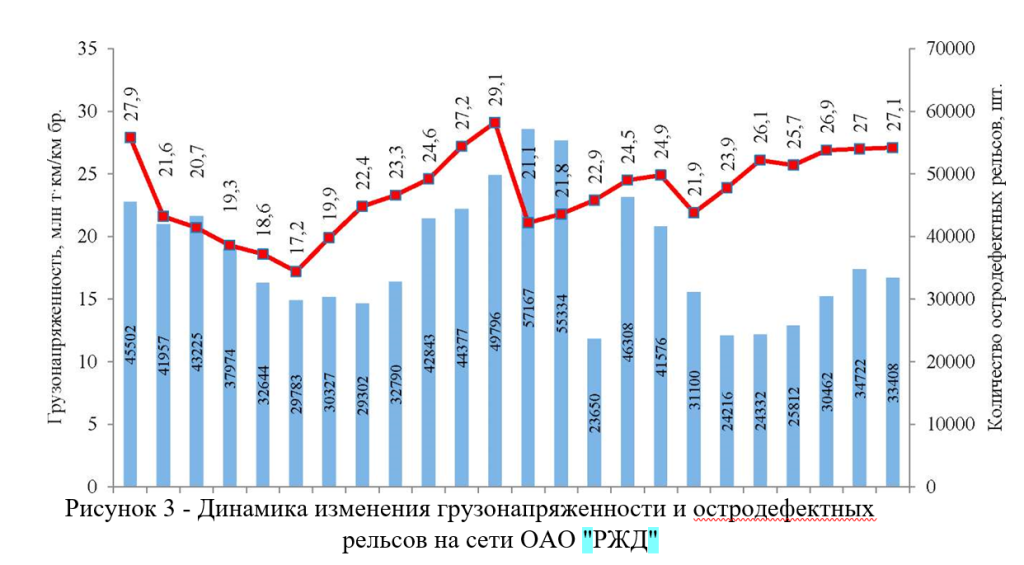
После оживления экономики и роста грузонапряженности начиная с 1998 по 2005 год происходит увеличение числа ОДР. С 2005 года число ОДР снижается из-за повышения качества рельсовой продукции и улучшения дефектоскопии рельсов. В целях повышения эффективности работы ОАО «РЖД» и в связи с переходом на участковую систему ведения путевого хозяйства с 15.11.2016 г. введено в действие «Положение о системе ведения путевого хозяйства ОАО «РЖД».
В соответствии с Положением для путей 1 и 2 классов предполагается укладка новых рельсов типа Р65, для специализированных линий О и Т рельсы категорий ОТ370ИК и ДТ370ИК, для линий специализации П и Г – ОТ350 и ДТ350.
По мере улучшения системы ведения рельсового хозяйства, перехода на бесстыковой путь, количеств изломов рельсов под поездами снижается (Рисунок 4).
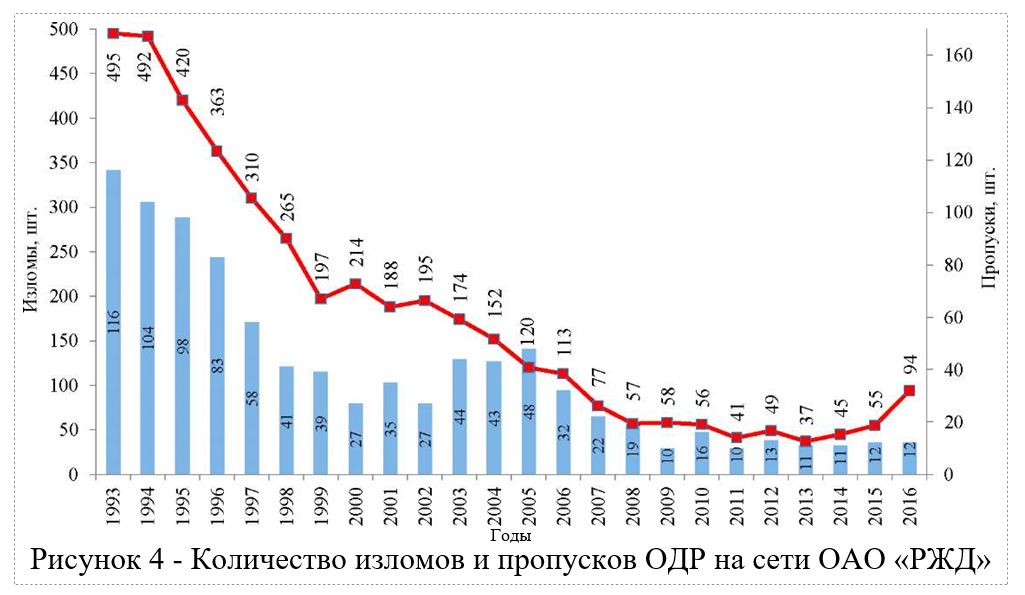
Так в период с 1993 по 2008 год количество изломов рельсов уменьшилось на 438 штук, т.е. в 8,7 раз. Количество пропусков дефектов диагностическими средствами также снизилось в 6,1 раз.
Всего за 7 лет начиная с 2010 года заменено 688 тыс. дефектных рельсов, из которых 177,9 тыс. (26 %) оказались остродефектными. При этом произошло 314 случаев излома дефектных рельсов под поездами (0,18 % от числа ОДР), что вызвало 9 сходов подвижного состава (0,005 % от числа ОДР).
В 2014 г. вступил в действие национальный стандарт Российской Федерации ГОСТ Р 51685-2013 «Рельсы железнодорожные. Общие технические требования», последняя редакция 24.02.2016 № 65-ст [63]. Разработка нового стандарта осуществлена в целях повышения эксплуатационной надежности и конкурентоспособности отечественных рельсов.
Классификация по категориям рельсов, изготавливаемых по стандарту ГОСТ Р 51685-2013 приведена в таблице:
Обозначение категории | Характеристика категории рельсов |
ДТ370ИК | Дифференцированно термоупрочненные с прокатного/отдельного нагрева повышенной износостойкости и контактной выносливости |
ОТ370ИК | Объемно термоупрочненные повышенной износостойкости и контактной выносливости |
ДТ350ВС | Дифференцированно термоупрочненные с прокатного/отдельного нагрева для высокоскоростного пассажирского движения |
ДТ350СС | Дифференцированно термоупрочненные с прокатного/отдельного нагрева для скоростного совмещенного движения |
ОТЗЗОСС | Объемно термоупрочненные для скоростного совмещенного движения |
ДТ350НН | Дифференцированно термоупрочненные с прокатного/отдельного нагрева низкотемпературной надежности |
ОТ350НН | Объемно термоупрочненные низкотемпературной надежности |
ДТ350 | Дифференцированно термоупрочненные с прокатного/отдельного нагрева общего назначения |
ОТЗбО | Объемно термоупрочненные общего назначения |
НТ320ВС | Нетермоупрочненные для высокоскоростного пассажирского движения |
НТ320 | Нетермоупрочненные высокой прочности общего назначения |
НТЗОО | Нетермоупрочненные повышенной прочности общего назначения |
НТ260 | Нетермоупрочненные обычной прочности общего назначения |
Периодичность проведения реконструкции или капитального ремонта установлена Положением после пропуска 750 млн т бр. или 1500 млн т бр. с заменой рельсов в середине межремонтного цикла. Периодичность реконструкции после укладки новых рельсов Р65 категории ДТ370ИК составляет 1100 млн т бр.
Для повышения эффективности рельсового хозяйства ОАО «РЖД» с 31.12.2015 г. введена в действие для опытного применения с 01.03.2016 г. «Инструкция па определению назначенного ресурса рельсов в зависимости от условий эксплуатации и фактического состояния рельсов». Инструкция разработана на основе и с использованием требований действующей в ОАО «РЖД» нормативно-технической документации.
Назначенный ресурс рельсов первой укладки в соответствии с Техническими условиями, утвержденными ОАО «РЖД» 18.01.2013 г. с изменениями от 19.01.2018 г. № 101р, составляет для бесстыкового пути 700 или 1400 млн т бр. в зависимости от состава промежуточных ремонтов пути. С учётом этого ресурса в настоящее время имеет место значительное протяжение главных путей со сверхнормативным пропущенным тоннажем при различных условиях эксплуатации. Применение данной инструкции позволит продлить ресурс рельсов с применением показателей оценки их фактического состояния.
На каждой дистанции пути ведется учет в электронном виде:
- выхода рельсов по дефектам с указанием кодов дефектов (в соответствии с Инструкцией «Дефекты рельсов» [67]) и их количества, и при каком пропущенном тоннаже были изъяты дефектные рельсы;
- выхода остродефектных рельсов с указанием кодов дефектов и их количества, и при каком пропущенном тоннаже были изъяты остродефектные рельсы;
- количества лежащих в пути дефектных рельсов с указанием кодов дефектов и их количества.
Данные заносятся в формы ПУ-2а и в электронную форму учёта ЕКСУИ. По результатам оценки фактического состояния рельсов принимается решение о продлении ресурса рельсов. Если за последний год эксплуатации средневзвешенный выход рельсов на участке составил 2 шт./км и более, такой участок включается в план первоочередного ремонта пути. После ремонта все рельсы следует направлять в рельсосва- рочные предприятия для проведения комплексного их ремонта с последующей повторной укладкой в путь.
Оценка и прогнозирование надежности рельсов в различных эксплуатационных условиях
Рельсы отечественного производства по наработке тоннажа уступают рельсам из стран Европы, США и Японии.
В связи с этим ставится задача довести продолжительность жизненного цикла ВСП до наработки 1100-1400 млн т брутто.
Нормативная периодичность выполнения ремонтов железнодорожного пути, по которой определяется их ежегодная потребность при текущем и перспективном планировании определяются с учетом нормативного ресурса конструкции верхнего строения пути, соответствующей определенному классу.
Эти нормативные ресурсы являются базовыми и используются с учетом повышающих и понижающих коэффициентов, зависящих от условий эксплуатации. Значение нормативных ресурсов Тн для верхнего строения пути 1 и 2 классов с рельсами типа Р65 категории качества Т1 установлены ТУ.
Нормативные ресурсы ВСП после его реконструкции с укладкой рельсов Р65 категорий ДТ350 и ДТ370 установлены как минимальные значения Тн = 1100 млн т брутто с обязательным учетом дополнительных критериев и корректирующих коэффициентов, которые не имеют строгого научного обоснования.
В связи с этим автором выполнена оценка в различных условиях эксплуатации долговечности рельсов категории качества Т1, которые до сих пор имеют большую протяженность на сети ОАО «РЖД».
Оценка надежности рельсов по усеченной выборке отказов
Элементы ВСП относятся к невосстанавливаемым объектам. Их отказы вызваны большим количеством равновлияющих факторов, многочисленными исследованиями подтверждено, что отказы элементов ВСП соответствуют нормальному закону распределения случайной величины. При оценке отказов элементов ВСП расчет средней наработки до отказа производится по формуле:
Тср = Х -П,
Дисперсия величины t по статистическим данным об отказах определяется по формуле
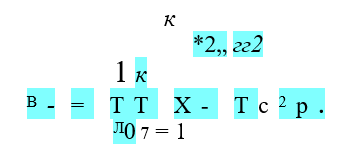
Расчет ведется с использованием интегральной функции нормального распределения
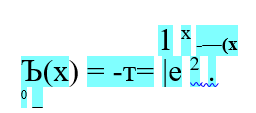
Переменная величина этой функции
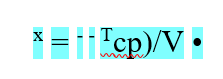
Так как эксплуатировать верхнее строение пути до полного отказа всех элементов невозможно (капитальный ремонт пути выполняется при достижении 4-8 отказов рельсов за срок службы на 1 км), то для расчета параметров распределения отказов применяются усеченные выборки.
Определение гамма-процентного ресурса рельсов
В соответствии с ГОСТ Р 51685-2013 «Рельсы железнодорожные. Общие технические условия» гамма-процентный ресурс рельсов должен составлять не менее 92,5 % при наработке тоннажа 1100 млн т брутто.
Гамма процентному ресурсу рельсов у = 92,5 % соответствует вероятность безотказной работы
Р(Тт) = у/100 = 0,925.
Значения функции вероятности отказа Е0(иР) и соответствующие ей значения квантиля иР находятся по специальным таблицам.
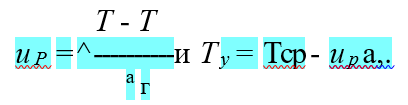
В данном случае иР = 1,44.
Прогнозирование отказов рельсов
Для расчета долговечности элементов ВСП необходимо прогнозировать их отказы.
Прогноз отказов рельсов производится использованием формулы
п(1г) = 160 ^ (?,),
где 160 – число рельсов длиной 12,5 м, условно лежащих в пределах одного километре бесстыкового пути.
Достоверность прогноза определяется отношением периода упреждения и ретроспективного периода
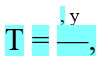
где – период упреждения;
Ц – величина ретроспективного периода.
Ошибка прогноза определяется по формуле:
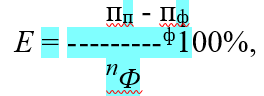
где пп и Пф – прогнозируемые и фактические значения отказов рельсов.
Исследование отказов и долговечности рельсов
Оценка надежности ВСП производилась по отказам рельсов типа Р65 категории качества Т1.
Технические параметры опытных участков приведены в таблице 2.2. Данные об отказах взяты из системы ЕК АСУИ ОАО «РЖД» с 2009 по 2015 гг. Величина пропущенного тоннажа по этим рельсам составила 100¬1300 млн т бр.
Эксплуатационное направление | Технические параметры участков | ||||
Средняя грузонапряженность, млн т км брутто/км в год | Средняя осевая нагрузка, кН | Средневзвешенный радиус кривых, M | Доля кривых на участке, % | Гамма- процентный ресурс рельсов (у = 92,5 %), млн т брутто | |
О.-Н., 1 | 111 | 186 | 721 | 0,3 | 1100 |
О. – Н., 2 | 74 | 123 | 648 | 0,3 | 1520 |
Н.-К., 1 | 65 | 157 | 629 | 24,0 | 1157 |
Н. – К., 2 | 80 | 183 | 629 | 23,5 | 923 |
В.-С., 1 | 112 | 215 | 802 | 2,6 | 923 |
В.-С., 2 | 42 | 76 | 828 | 2,4 | 1913 |
С.-К., 1 | 105 | 216 | 541 | 38,4 | 769 |
С.-К., 2 | 34 | 76 | 556 | 23,7 | 1674 |
Данные об отказах рельсов на конкретных опытных участках приведены в таблицах 3-5.
В соответствии с принятой методикой по найденным для каждого участка Тср и Gt при иР = 1,44 получены значения гамма-процентного ресурса Тт, которые приведены в таблице 2 и на рисунке 3
Средняя осевая нагрузка, кН | Протяженность кривых, % | Средняя грузонапряженность, млн т брутто/км в год | Наработка ti, млн т брутто | Протяженность участка, км | Фактическая частота отказов r(t,j, шт/км | Прогнозируемая частота отказов гШ шт/км | Относительная ошибка Е в зависимости от глубины прогноза, % |
182 | 0,3 | 111,0 | 100 | 582,9 | 0,08 | 0,09 | 1 1,8 |
112,1 | 300 | 553,0 | 0,28 | 0,30 | 8,3 | ||
114,8 | 500 | 144,9 | 1,05 | 0,91 | -13,6 | ||
112,6 | 700 | 141,1 | 2,61 | 2,41 | -7,6 | ||
111,0 | 900 | 130,0 | 5,85 | 5,69 | -2,8 | ||
110,7 | 1100 | 255,6 | 11,90 | 11,97 | 0,6 | ||
107,1 | 1300 | 102,5 | 21,10 | 22,49 | 6,6 | ||
_ | 1500 | _ | _ | 38,03 | _ | ||
Гср= 1893 млн т бр.; аг = 550 млн т бр.; 71(92,5 %) = 1100 млнтбр. | ■Ёср | 7,3 |
Средняя осевая нагрузка, кН | Протяженность кривых, % | Средняя грузонапряженность, млн т брутто/км в год | Наработка /„ млн т брутто | Протяженность участка, км | Фактическая частота отказов /-(г1/), шт/км | Прогнозируемая частота отказов Ли), шт/км | Относительная ошибка Е в зависимости от глубины прогноза, % |
76 | 0,3 | 41,5 | 100 | 780,0 | 0,15 | 0,16 | 6,7 |
42,2 | 300 | 201,4 | 0,31 | 0,30 | -4,0 | ||
41,9 | 500 | 136,3 | 0,55 | 0,52 | -5,0 | ||
27,3 | 700 | 102,4 | 0,96 | 0,89 | -7,4 | ||
41,2 | 900 | 110,5 | 1,42 | 1,47 | 3,5 | ||
41,5 | 1100 | 140,7 | 2,25 | 2,36 | 5,1 | ||
– | 1300 | – | – | 3,68 | – | ||
– | 1500 | – | – | 5,57 | – | ||
Гср = 3503 млн т бр.; а, = 1104 млн т бр.; Т(92,5 %) = 1913 млн т бр. | ^ср | 5,3 |
Средняя осевая нагрузка, кН | Протяженность кривых, % | Средняя грузонапряженность, млн т брутто/км в год | Наработка /„ млн т брутто | Протяженность участка, км | Фактическая частота отказов /-(г1/), шт/км | Прогнозируемая частота отказов Ли), шт/км | Относительная ошибка Е в зависимости от глубины прогноза, % |
76 | 0,3 | 41,5 | 100 | 780,0 | 0,15 | 0,16 | 6,7 |
42,2 | 300 | 201,4 | 0,31 | 0,30 | -4,0 | ||
41,9 | 500 | 136,3 | 0,55 | 0,52 | -5,0 | ||
27,3 | 700 | 102,4 | 0,96 | 0,89 | -7,4 | ||
41,2 | 900 | 110,5 | 1,42 | 1,47 | 3,5 | ||
41,5 | 1100 | 140,7 | 2,25 | 2,36 | 5,1 | ||
– | 1300 | – | – | 3,68 | – | ||
– | 1500 | – | – | 5,57 | – | ||
Гср = 3503 млн т бр.; а, = 1104 млн т бр.; Т(92,5 %) = 1913 млн т бр. | ^ср | 5,3 |
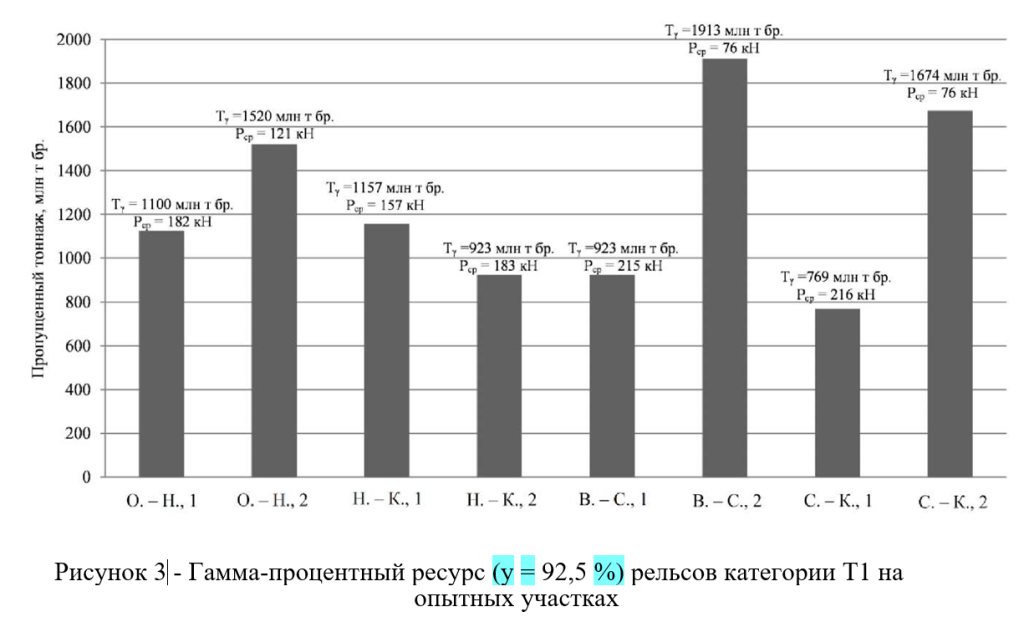
Из таблицы 3 и рисунка 3 видно, что рост гамма-процентного ресурса Тт происходит при уменьшении средней осевой нагрузки относительно стандартной Рст = 180 кН, а спад ресурса при росте осевой нагрузки. Также уменьшение гамма-процентного ресурса рельсов вызывается снижением средневзвешенного радиуса кривых участков.
Статистическая обработка данных Тт с использованием регрессионного анализа позволила получить следующую зависимость Тт
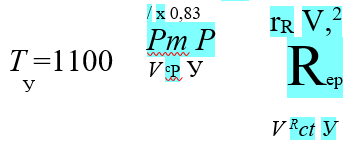
где Рср – средняя осевая нагрузка;
Рст – стандартная нагрузка (Рст = 180 кН);
Яст – стандартный радиус, при котором определены параметры функции (2.43) (Яет =700 м);
Яср – средневзвешенный по протяженности пути радиус кривых на рассматриваемом участке.
В этом случае формула будет иметь вид
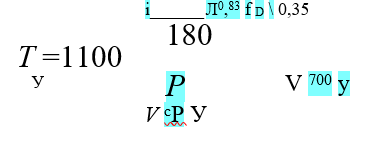
В соответствии с формулой суммарные отказы рельсов при F(Ty) = 0,075 составляют 12 штук при наработке 1100 млн т бр., что достаточно много. При невыполнении реконструкции и дальнейшем росте тоннажа выход рельсов в дефектные резко нарастает (см. таблицы 3-5), что ведет к риску излома их под поездом. Отсюда следует, что наработка тоннажа до 1400 млн т брутто возможна только на участках, где средние осевые нагрузки не превосходят 180 кН, а протяженность кривых не будет превышать 30 % от общей длины участка.
Переход на поставки плетей вместо отдельных рельсов длиной 25 или 100 м коренным образом изменит всю технологию путеремонтных работ, что даст дополнительный экономический эффект. На основании выполненных расчетов по приведенной в данном разделе методике предложена корректировка среднесетевого нормативного тоннажа на участках со сложными условиями эксплуатации. Этот тоннаж снижается на участках 1 и 2 классов, где установленная скорость движения грузовых поездов превышает 60 км/ч, на которых:
средняя осевая нагрузка находится в интервалах:
- 180-200 кН – на 5 %;
- 201-220 кН – на 15 %;
- 221-240 кН – на 20 %;
- 241 и более – на 30 %
средневзвешенные по протяженности пути радиусы кривых находятся в интервалах:
- 700-500 м – на 5 %;
- 501-301 м – на 10 %;
- 300 м и менее – на 20 %.
На перевальных участках с уклонами протяженностью более длины тяжеловесного состава нормативный тоннаж снижается при уклонах:
- 8-15 %о – на 5 %;
- более 15 %0 – на 10 %.
Суммарное снижение нормативного тоннажа с учетом всех перечисленных факторов не должно превышать 25 %, а на перевальных участках – 40 %.
Оценка надежности рельсовых скреплений по результатам эксплуатационных испытаний
Сравнительный анализ современных рельсовых скреплений
Являясь одним из важных элемент ВСП, рельсовое скрепление в существенной степени определяет эксплуатационную надежность рельсовой колеи и условия взаимодействия ее с подвижным составом. От надежности скреплений зависит стоимость жизненного цикла верхнего строения пути. На бесстыковом пути наиболее распространенными в настоящее время типами промежуточных рельсовых скреплений являются ЖБР различной модификации (подкладочные и бесподкладочные) и АРС.
Наиболее распространенными являются бесподкладочные скрепления шу- рупно-дюбельного типа – ЖБР-65Ш (рисунок 4) и подкладочные – ЖБР- 65ПШМ (рисунок 5)
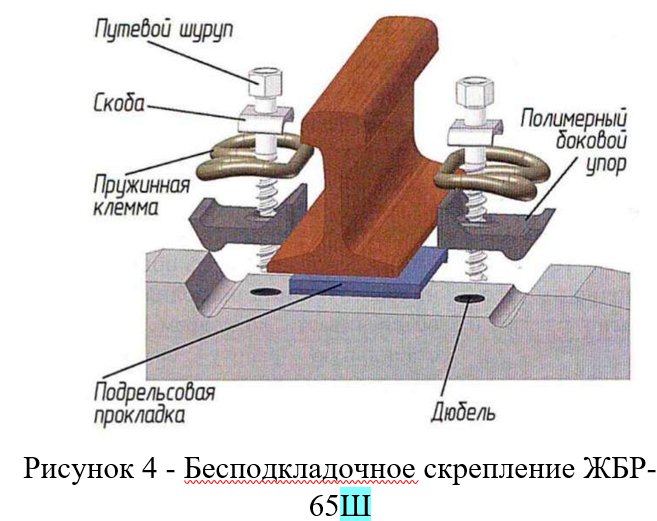
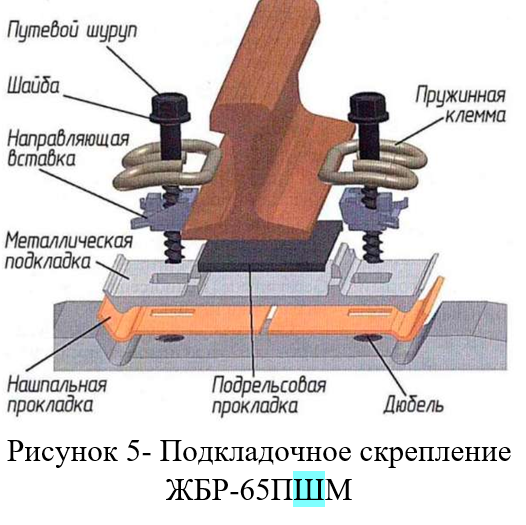
Металлическая подкладка значительно усиливает узел скрепления ЖБР- 65ПШМ и стабилизирует упорную рельсовую нить, поэтому такие скрепления желательно применять в кривых малых радиусов.
Анкерное рельсовое скрепление (АРС), приведенное на рисунках 6 и 7, не имеет болтов и шурупов, а следовательно не требует сезонной протяжки прикрепителей. Узел скрепления АРС легко монтируются с использованием пружинных клемм, изоляторов и двух эксцентриковых монорегуляторов.
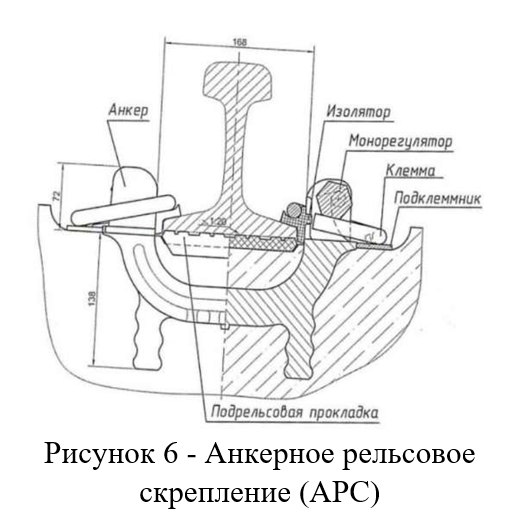
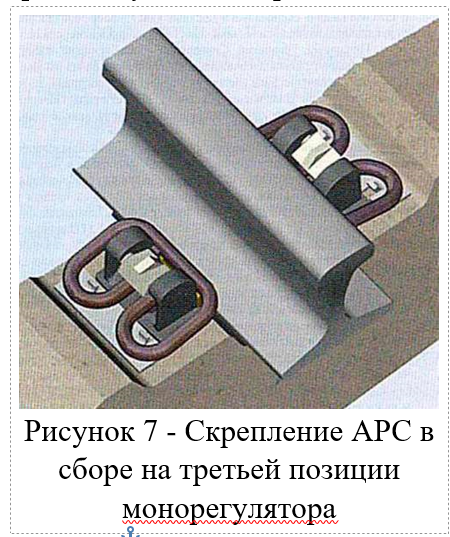
Скрепление АРС-4 укладывается при реконструкции пути преимущественно в европейской части страны. На грузонапряженных участках Сибири в кривых малого радиуса происходит интенсивный износ изоляторов, приводящий к интенсивному уширению колеи, что требует больших затрат труда на ее регулировку.
Частота отказов элементов рельсовых скреплений типов ЖБР-ПШМ, ЖБР- 65Ш, АРС, определенная на основании статистических данных об отказах элементов в процессе их эксплуатации, приведена в таблице 6.
Элементы скреплений | |||||||||||
Тип скрепления | Наработанный тоннаж, млн т бр. | шуруп с шайбой (скобой) | клемма | боковой упор (вставка) | подрельсовая прокладка | металлическая подкладка | нашпальная прокладка | анкер АРС | монорегулятор | уголковый изолятор | подклеммник |
200 | 0,5 | 0,3 | 0,2 | 0,4 | |||||||
ЖБР-65Ш | 400 | 2,0 | 0,5 | 0,8 | 3,0 | ||||||
600 | 5,0 | 1,0 | 2,6 | 7,0 | |||||||
800 | 7,0 | 1,8 | 4,0 | 10,0 | |||||||
200 | 0,2 | 0,2 | 0,1 | 0,2 | 0,5 | 0,0 | |||||
ЖБР-ПШМ | 400 | 0,8 | 0,5 | 0,5 | 1,5 | 1,5 | 0,5 | ||||
600 | 1,3 | 1,0 | 1,0 | 3,0 | 5,0 | 1,5 | |||||
800 | 1,8 | 1,5 | 2,0 | 5,0 | 7,0 | 2,0 | |||||
200 | 0,5 | 0,3 | 0,1 | 0,1 | 0,3 | 0,2 | |||||
АРС | 400 | 0,8 | 1,6 | 0,3 | 0,2 | 3,0 | 0,6 | ||||
600 | 1,5 | 2,7 | 0,5 | 0,3 | 7,5 | 1,0 | |||||
800 | 2,0 | 5,0 | 1,0 | 0,5 | 15,0 | 2,0 |
После определения параметров нормального распределения Тср и аг и вероятности безотказной работы Р() отдельных элементов скреплений переходят к определению вероятности безотказной работы узлов скреплений. Для этой цели составляются логические структурные схемы оценки надежности скреплений ЖБР-65Ш, ЖБР-ПШМ, АРС.
Отказ узла скреплений у подкладочного скрепления ЖБР-65ПШМ и анкерного АРС произойдет тогда, когда откажут обе параллельные ветви цепи элементов прикрепителей. У бесподкладочных креплений ЖБР-65Ш отказ узла скреплений наступит при отказе любого из его элементов.
Вероятности безотказной работы узлов рельсовых скреплений в зависимости от наработки тоннажа, определенные по формулам, в соответствии со структурными схемами (рисунок 8), приведены на рисунке 9
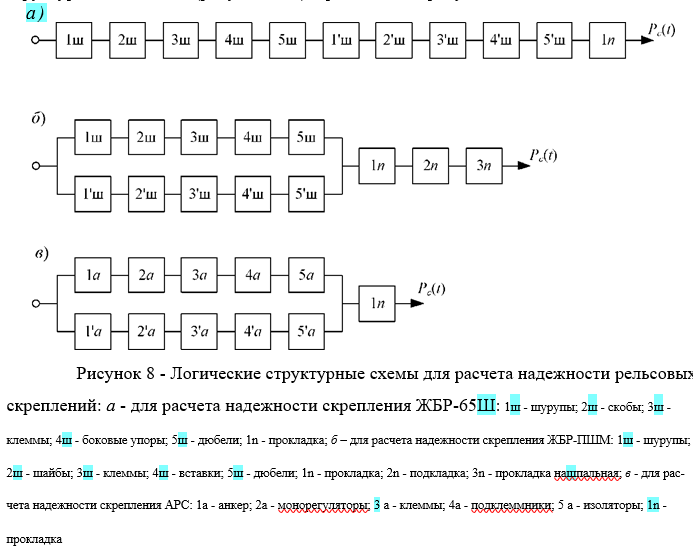
Проанализировав полученные данные установлено, что вероятность безотказной работы выше у скрепления типа ЖБР-ПШМ, а наименьшая у скрепления тина АРС(рис. 9).
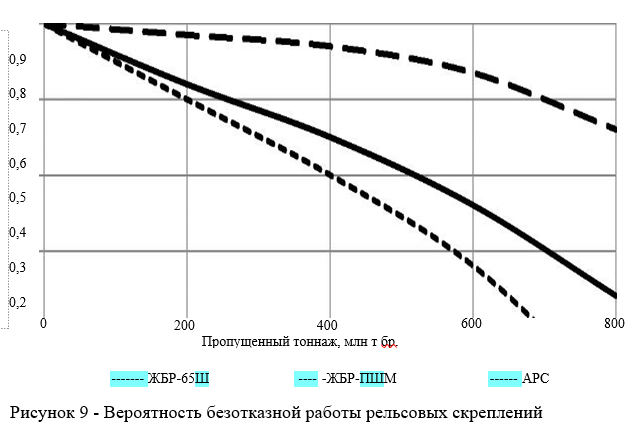
Объясняется это тем, что подкладки скрепления ЖБР-ПШМ дублируют работу двух шурупов и цепи этих элементов являются резервированными. Важное значение имеет качество изготовления элементов скреплений, особенно упругих клемм и прокладок.
Низкая надежность узлов скрепления АРС объясняется высокой горизонтальной жесткостью скреплений и недостатками конструкции изолирующих уголков.
План линии оказывает сильное влияние на долговечность элементов скреплений. Износ и отказ элементов скреплений часто наблюдается в кривых малого и среднего радиуса в связи с появлением больших поперечных сил, передаваемых на наружную рельсовую нить и соответствующие узлы скреплений. Исходя из этого гарантийный ресурс элементов скреплений установлен для кривых радиусом менее 350м – 350 млн т бр.; для кривых радиусом от 350 до 650 м – 500 млн т бр; для кривых радиусом более 650 м и для прямых участков – 700 млн т бр.
Тип скрепления | Стоимость 1 шпалы с 2 собранными узлами, руб. | Стоимость 1 км пути с эпюрой шпал 2000 шт./км, руб. |
ЖБР-65Ш | 2 327 | 4 654 000 |
ЖБР-65ПШМ | 3 052 | 6 104 000 |
АРС-4 | 2 999 | 5 998 000 |
Наименьшую стоимость изготовления одной железобетонной шпалы с комплектом двух узлов скреплений имеют ЖБР-65Ш (таблица 2.7). Однако стоимость текущего содержания бесстыкового пути в кривых среднего и малого радиуса наименьшая у скреплений ЖБР-65ПШМ из-за более высокой их надежности.
Учитывая надежность узлов скреплений ЖБР-65Ш, ЖБР-65ПШМ и АРС-4, долговечность их элементов и стоимость ткущего содержания пути, рекомендованы национальные сферы их применения в зависимости от грузонапряженности участков и радиусов кривых (таблица 8). Наиболее широкий диапазон рационального применения имеют скрепления ЖБР-65ПШМ.
Условия эксплуатации | Тип скрепления | |||
Грузонапряженность, млн т бр. км / км в год | Радиус кривых, м | ЖБР-65Ш | ЖБР- 65ПТТТМ | АРС-4 |
более 80 | более 650 | |||
от 350 до 650 | ||||
менее 350 | ||||
от 50 до 80 | более 650 | |||
от 350 до 650 | ||||
менее 350 | ||||
до 50 | более 650 | |||
от 350 до 650 | ||||
менее 350 |
Оценка долговечности железобетонных шпал в различных эксплуатационных условиях
Началом массового применения железобетонных шпал на сети железных дорог СССР следует считать 1959 г., когда на вновь построенных специализированных заводах был начат выпуск типовых шпал С-56. С этого времени продолжался неуклонный рост применения железобетонных шпал.
До 1959 г. на железных дорогах проводились широкие эксплуатационные испытания железобетонных шпал различных типов и конструкций, которые показали, что лучшими из них являются струнобетонные шпалы, по основным параметрам в большей степени удовлетворяющие эксплуатационным требованиям. По результатам испытаний была утверждена типовая железобетонная шпала С-56, принципиальные основы конструкции которой сохранились и в современных стандартных шпалах [105]. Дальнейшее совершенствование конструкции железобетонных шпал продолжалось на основе научно-исследовательских работ, проводимых на базе большого полигона укладки и многолетней эксплуатации железобетонных шпал. По получаемым результатам в проекты типовых железобетонных шпал вносились некоторые конструктивные улучшения.
В 1987 г. на железных дорогах СССР железобетонные шпалы эксплуатировались более чем на 55 тыс. км пути (112,7 млн шт.). Согласно статистическим данным суммарный выход из стоя типовых струнобетонных шпал за 16 лет составил 3,2 %. Около 60 % этого количества по новой классификации дефектов железобетонных шпал связано с дефектами эксплуатационного происхождения, а 40 % – с технологическими дефектами.
Железобетонные шпалы применяют широко в большинстве зарубежных стран. Их конструкции достаточно многочисленны и разнообразны, поэтому приходится ограничиться лишь их общей оценкой. Наибольшее применение, как и в России, получили предварительно напряженные железобетонные шпалы брускового типа. Кроме брусковых предварительно напряженных шпал, за рубежом в значительно меньшем количестве, но все же достаточно широко применяют ненапряженные железобетонные шпалы двух- блочного типа. Такие шпалы применяют во Франции, Испании, Швеции, ряде стран Африки, Южной Америки и др.
Для большинства шпал характерна наиболее простая форма без всяких выступов за пределы основного напряженного бруса с плавными переходами от одного участка к другому. Высота шпалы в подрельсовой части обычно больше, чем в средней. Во многих конструкциях ширина шпалы увеличивается к концам.
Исключением из этого правила являются шпалы с так называемыми «ушами», «галстуками», цель которых – повысить сопротивляемость боковому сдвигу и увеличить опорную площадь.
В настоящее время при текущем содержании шпал механизмы повреждения и законы роста трещин исследуются как экспериментально, так и в рамках полевых наблюдений. Параллельно автоматизируются процессы выявления и определения трещин.
Все изготавливаемые в России шпалы брускового типа предварительно напряженные с прямолинейной проволочной арматурой без анкеров (струнобе- тонные). В соответствии с ГОСТ Р 54747-2011 и ГОСТ Р 33320-2015 железобетонные шпалы в зависимости от типа рельсового скрепления подразделяют на 3 типа и несколько подтипов с отдельными конструктивными особенностями. По качеству изготовления шпалы относят к первому или второму сорту. Шпалы второго сорта могут применяться только на малодеятельных путях 5 класса.
Жесткость пути, как показывают произведенные измерения, при железобетонных шпалах в 2-3 раза выше, чем при деревянных. Это свойство железобетонных шпал отрицательно влияет на стабильность пути и работу взаимодействующих с ним элементов. Данные ряда дорог показывают, что при железобетонных шпалах одиночный выход рельсов по повреждениям в зоне стыков в 2-3 раза выше, чем при деревянных.
Для предотвращения этого железобетонные шпалы на дорогах России укладываются, как правило, только на бесстыковом пути.
Общий принцип всех систем, уменьшающих динамическое воздействие подвижного состава на элементы пути – применение упругих прокладок различного рода. Эти системы действуют как преграда для частот, превышающих собственную частоту колебаний в 42 раза.
Основным потребителем продукции и единственным крупным заказчиком железобетонных шпал и брусьев является ОАО «РЖД», которое практически и формирует российский рынок на уровне 10 млн шт./год. Доля сторонних заказчиков составляет 3-4 %, к ним относятся промышленные и горнодобывающие предприятия.
ОАО «БетЭлТранс» обеспечивает более 90 % российского рынка железобетонных шпал. Остальные 10 % рынка занимают ОАО «РЖДстрой» и ОАО «ТрансЮжстрой», а также заводы Беларуси, Казахстана и Украины.
С 2013 г. на всех заводах ОАО «БелЭлТранс» началась поставка железобетонных шпал укомплектованных промежуточными рельсовыми скреплениями, что также положительно влияет на сохранение и укрепление позиции общества на рынке. Гарантийный срок эксплуатации железобетонных шпал определен межгосударственным стандартом ГОСТ 33320-2015 и составляет всего пять лет или наработку в 300 млн т бр. груза. Для увеличения гарантийного срока до 10 лет и назначенного ресурса 1,5 млрд т бр. ОАО “БЭТ” необходимо решить следующие задачи:
- повысить морозостойкость бетона шпал F200 (200 циклов замораживания и оттаивания) до F300 и более;
- повышение прочности бетона на сжатие с класса В40 до В50 и В60.
- Наряду с существующими на заводах ОАО «БетЭлТранс» введена в 2010 г.
- новая полуавтоматическая технологическая линия конвейерного типа для производства железобетонных шпал, впервые разработанная итальянской фирмой <Ю1Ш1».
Приемку готовых шпал производят партиями в соответствии с требованиями ГОСТ 13015-2012. Шпалы принимают по результатам:
- приемо-сдаточных испытаний;
- периодических испытаний;
- испытаний для обязательного подтверждения соответствия
Оценка надежности железобетонных шпал на этапе эксплуатации
Расчет надежности железобетонных шпал ведется по данным об отказах их в процессе эксплуатации. При этом использован нормальный закон распределения их отказов. Параметрами распределения для нормального закона являются средняя наработка до отказа Тср и среднее квадратическое отклонение оР
В данном случае удобно пользоваться интегральной функцией нормального распределения
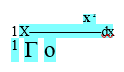
Для определения параметров распределения отказов Тср и ог. используются усеченные выборки.
Гамма процентному ресурсу шпал у = 97,0 % соответствует вероятность безотказной работы Р(Тт) = у/100 = 0,970.
Каждому значению у/100 соответствует определенное значение квантили ЦР, равное корню функции вероятности отказов ^(ЦР).
Значения функции ^0(ЦР) и соответствующие ей значения иР и Тт определяются из зависимостей
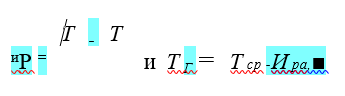
В нашем случае ЦР = 1,881.
Прогнозирование отказов шпал
Оценку суммарного выхода шпал из расчета на один километр бесстыкового пути определим по формуле п(11) = 1880^ (г. )■
Исследование отказов и долговечности железобетонных шпал
Технические параметры опытных участков Западно-Сибирской дирекции инфраструктуры: О. – Н., Н. – К., приведены в таблице 9.
Эксплуатационное направление | Технические параметры участков | |||
Средняя осевая нагрузка, кН | Средневзвешенный радиус кривых, м | Доля кривых на участке | Гамма- процентный ресурс шпал (у = 97%), млн т брутто | |
О. — Н., 1 путь | 180 | 721 | 0.06 | 1821 |
О. – Н., 2 путь | 123 | 748 | 0.17 | 2333 |
Н. – К., 1 путь | 205 | 509 | 0.09 | 1629 |
Анализ отказов шпал производился с использованием учета шпал в ЕК АСУИ, лежащих в пути с 2009 по 2016 год.
Данные об отказах шпал на конкретных опытных участках представлены в функции наработки II тоннажа (таблицы 10-12).
Средняя осевая нагрузка, кН | Доля кривых | Наработка t„ млн т брутто | Количество отказов шпал «(?;), шт. | Фактическая частота отказов ?'(/;), шт/км | Прогнозируемая частота отказов г'(/,), шт/км | Относительная ошибка Е, % |
200 | 0 | 0 | 0,0 | 0 | ||
400 | 2 | 2 | 1,8 | 8,4 | ||
600 | 3 | 3 | 3,2 | 7,6 | ||
180 | 0,06 | 800 | 5 | 5 | 5,5 | 10,4 |
1000 | 10 | 10 | 9,2 | 8,2 | ||
1200 | 15 | 15 | 15,0 | 0,03 | ||
1400 | 23 | 23 | 23,6 | 2,6 | ||
1600 | 0 | 0 | 0,0 | 0 | ||
Гср = 4017 млн т бр.; at = 1167 млн т бр.; Г(97,0 %) =1821 млн т бр. | о. | 6,2 |
Средняя осевая нагрузка, кН | Доля кривых | Наработка 1„ млн т брутто | Количество отказов шпал «(/;), шт. | Фактическая частота отказов r(t,:), шт/км | Прогнозируемая частота отказов /•'(?;), шт/км | Относительная ошибка Е, % |
121 | 0,17 | 200 | 1 | 1 | 1,1 | 11,6 |
400 | 2 | 2 | 1,7 | 13,8 | ||
600 | 3 | 3 | 2,6 | 12,0 | ||
800 | 4 | 4 | 4,0 | 0,5 | ||
1000 | 5 | 5 | 5,9 | 18,4 | ||
1200 | 8 | 8 | 8,6 | 8,0 | ||
1400 | 13 | 13 | 12,5 | 3,9 | ||
1600 | 18 | 18 | 17,7 | 1,7 | ||
Тср = 5277 млн т бр.; ot = 1565 млн т бр.; 7197,0 %) = 2333 млн т бр. | р ^ср | 8,7 |
Средняя осевая нагрузка, кН | Доля кривых | Наработка t„ млн т брутто | Количество отказов шпал «(?,), шт. | Фактическая частота отказов /-(/,), шт/км | Прогнозируемая частота отказов r\t,), шт/км | Относительная ошибка Е, % |
215 | 0,09 | 200 | 0 | 0 | 0,0 | 0 |
400 | 2 | 2 | 2,2 | 10,1 | ||
600 | 4 | 4 | 4,1 | 1,5 | ||
800 | 8 | 8 | 7,2 | 9,5 | ||
1000 | 14 | 14 | 12,5 | 10,8 | ||
1200 | 21 | 21 | 20,9 | 0,7 | ||
1400 | 30 | 30 | 33,7 | 12,5 | ||
1600 | – | 0 | 0,0 | 0 | ||
Тср = 3619 млн т бр.; о> = 1058 млн т бр.; Г(97,0 %) = 1629 млн т бр. | г | 7,5 |
Используя зависимость по найденным для каждого участка Тср и аг при Up = 1,881 получены значения TY, которые приведены в таблице 9
Анализ данных этого рисунка показывает, что при снижении средней осевой нагрузки относительно стандартной для Транссибирской магистрали Рст = 180 кН гамма-процентный ресурс TY = 1821 млн т бр. увеличивается, а при росте – падает. При снижении величины средневзвешенного радиуса и увеличении доли кривых на участке значение гамма-процентного ресурса шпал также падает.
Статистическая обработка данных TY c использованием регрессионного анализа позволила получить следующую зависимость TY:
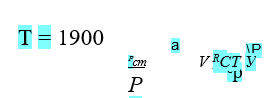
где Рср – средняя осевая нагрузка подвижного состава на рассматриваемом участке; Рст – стандартная нагрузка, при которой определены параметры функции (Рст = 180 кН); Яст – стандартный радиус, при котором определены параметры функции (2.51), Яст = 700 м; Яср – средневзвешенный по протяженности пути радиус кривых на рассматриваемом участке; а = 0,8, в = 0,4 – параметры регрессии.
В этом случае формула будет иметь вид
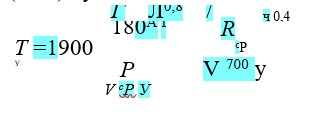
В соответствии с этой формулой суммарные отказы шпал при ^(Тт) = 0.03 составляют 56 штук, что не противоречит ТУ. При дальнейшем росте тоннажа выход шпал быстро нарастает (см. таблицы 10-12), что ведет к дополнительным затратам при текущем содержании пути. Расчеты по формуле показывают, что гамма-процентный ресурс (Ту = 97 %) может колебаться в пределах наработки Ту = 1500…2500 млн т бр. в зависи¬мости от эксплуатационных условий. При этом нормативную наработку тоннажа 1400 млн т бр. можно достигнуть только на участках, где средние осевые нагрузки не превышают 230 кН, а доля кривых не превышает 30 % от протяженности участка. В противном случае прогнозируемая частота отказов шпал превысит 35 шт./км.
Оценка работоспособности балластного слоя
Повышение скоростей движения и осевых нагрузок вагонов на железных дорогах РФ предъявляет все более высокие требования к обеспечению надёжности балластной призмы.
Балластный слой должен обладать следующими качествами:
- передавать давление от шпал на возможно большую поверхность основной площадки земляного полотна;
- обеспечивать наименьшую неравномерность остаточных осадок;
- оказывать максимально возможное сопротивление поперечному и продольному сдвигу шпал;
- производится из прочного материала, хорошо сопротивляющегося механическому износу и выветриванию.
Лучшим материалом, который может удовлетворить перечисленным требованиям, является щебень из прочных каменных пород. Балласт выполняет свои функции до наступления загрязненности 30-35 % от объема, после чего начинается интенсивное развитие деформаций. Это может приводить к осадке пути с разуплонением балласта и повышением его пластичности. Величина весового содержания частиц засорителя при этом должны быть не выше 26 %. В противном случае появляются грязевые выплески из-под шпал, количество которых на путях 1 и 2 класса превышает 3-5 %. В этих условиях назначается очистка щебня при реконструкции или среднем ремонте пути.
Оценка состояния пути по записям путеизмерительных вагонов и тележек применяется как у нас, так и за рубежом. Неравномерность осадки одной рельсовой нити по отношению к другой фиксируется на ленте, и все неисправности, выходящие за пределы допусков, штрафуются баллом по специально разработанной шкале. Следовательно, балльная оценка объективно показывает наличие неисправностей, превышающих установленные нормы.
Критерии назначения работ по среднему ремонту приведены в таблице 13.
Класс | Основные критерии | Дополнительные критерии | ||
пути | Загрязненность щебня по массе, % | Количество шпал с выплесками более, % | Потребность в замене балласта или очистке | Количество негодных скреплений более, % |
1 | 30 и более | 3 | 12 | |
2 | 30 и более | 5 | есть | 15 |
3 | 30 | 7 | 20 | |
4 | 30 | 10 | 30 | |
5 | Не лимитируется. Средний ремонт назначается по усмотрению начальника дистанции пути по согласованию с начальником службы пути |
Состояние балластного слоя оценивают засоренностью щебня и грязевыми выплесками балласта из-под шпал или количеством отступлений по показателям вагона-путеизмерителя. Оценивать состояние балласта по доле шпал с выплесками следует по формуле
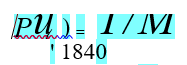
где т(Ъ) – доля шпал с выплесками при наработке %
По результатам наблюдений строится вариационный ряд т(?г) в функции наработки тоннажа определяются частости и квантили нормального рас¬пределения Црг, а по ним указанным ранее способом – Тср и <5г этого ряда наблю¬дений. По этим параметрам можно определить гамма-процентную наработку для участка пути с выплесками. В Инструкции по текущему содержанию пути доля протяженности пути с грязевыми выплесками варьируется от 5 до 30 %, при этом скорости движения поездов ограничиваются от 140 до 25 км/ч.
Выводы
. Надежность элементов верхнего строения пути в эксплуатации характе-ризуется случайным процессом накопления их отказов в функции наработанного тоннажа. Параметры случайных процессов определяются на основе обработки статистических данных с конкретных участков с учетом кривизны пути, средних осевых нагрузок подвижного состава, качества рельсов. Расчеты выполнены с ис-пользованием интегральной функции нормального распределения. Нормы меж-ремонтного тоннажа между реконструкциями пути определяются расчетом гамма- процентного ресурса рельсов на основе ограничений накопленного одиночного их выхода.
В результате обработки полученных данных определены зависимости гам¬ма-процентного ресурса (наработки тоннажа) рельсов при у = 92,5 % и величине суммарных отказов рельсов за межремонтный период n = 12 шт./км. Анализ пока¬зал, что интенсивность выхода рельсов увеличивается при увеличении осевой нагрузки и уменьшается при снижении доли кривых на участке. В связи с этим наработка тоннажа для рельсов Р65 до 1400 млн т бр. возможна только на участ¬ках, где средняя осевая нагрузка не превышает 180 кН, а доля кривых не превы¬шает 30 % от протяженности участка.
На основании выполненных исследований предложена корректировка нор-мативного тоннажа на участках со сложными условиями эксплуатации.
Нормативный тоннаж снижается на участках со скоростями движения гру-зовых поездов 60 км/ч и более, на которых средняя осевая нагрузка превышает 180 кН, на величину от 5 до 30 % (в зависимости от величины осевой нагрузки). Если средневзвешенные по протяженности пути радиусы кривых менее 700 м, нормативный тоннаж предложено снижать на величину от 5 до 20 % (в зависимо¬сти от величины средневзвешенного радиуса). Суммарное снижение нормативно¬го тоннажа с учетом всех перечисленных факторов не должно превышать 25 %, а на перевальных участках – 40 %.
- Оценка надежности скреплений показала, что наибольшей вероятностью безотказной работы обладают скрепления типа ЖБР-ПШМ, а наименьшей – скрепление типа АРС. Невысокая надежность скрепления АРС объясняется низ¬кой надежностью изолирующих уголков с обеих сторон подошвы рельса.
Надежность элементов скреплений сильно зависит от плана линии. Поэтому для кривых радиусом менее 350 м гарантийный ресурс элементов устанавливают Тг = 350 млн т бр., для кривых радиусом от 350 до 650 м – Тг = 500 млн т бр., для прямых и кривых радиусом более 650 м гарантийный ресурс составляет Тг = 700 млн т бр.
Учитывая надежность узлов скреплений, долговечность их элементов и сто-имость текущего содержания пути рекомендованы сферы применений указанных скреплений в зависимости от грузонапряженности участков и радиусов кривых. Наиболее широкий диапазон целесообразного и рационального применения име¬ют скрепления ЖБР-65ПШМ. - В качестве характеристики долговечности железобетонных шпал на этапе эксплуатации принят гамма-процентный ресурс наработки Тт от реконструкции (усиленного капитального ремонта) до предельного состояния с заданной вероят-ностью у = 97 %. Оценка надежности шпал ведется по усеченным выборкам отка¬зов.
Статистическая обработка данных с использованием регрессионного анали¬за позволила получить формулу для оценки гамма-процентного ресурса железобе-тонных шпал от осевых нагрузок, радиусов и доли кривых на рассматриваемом участке. В соответствии с этой формулой гамма-процентный ресурс (у = 97 %) может колебаться в зависимости от условий эксплуатации в пределах Тт = 1500.2500 млн т бр. При этом наработка тоннажа свыше 1400 млн т бр. возможна только на участках, где средние осевые нагрузки не превышают 180 кН, а доля кривых не превышает 30 % от протяженности участка. - Наработка тоннажа до наступления критической интенсивности развития деформаций, когда осадка пути сопровождается разуплотнением балласта и его повышенной пластичностью, определяется максимально допустимым засорением балласта, равным 35 % от его объема. При этом предельно допустимое весовое содержание сухого засорителя не должно превышать 26 %. В этих условиях назначается очистка щебня при выполнении работ по реконструкции или среднему ремонту пути.
Список Литературы
- Стратегия развития железнодорожного транспорта в Российской Федера¬ции до 2030 года [Электронный ресурс]: Распоряжение Правительства РФ от 17.06.08 № 877-р. Доступ из СПС «КонсультантПлюс». То же // Российские же¬лезные дороги [офиц. сайт]. URL: http://doc.rzd.ru/doc/public/ru?STRUCTURE_ID= 704&layer_id =5104&id=3997.
- Транспортная стратегия Российской Федерации на период до 2030 года [Электронный ресурс]: Распоряжение Правительства РФ от 22.11.08 № 1734-р (в ред. от 11.04.14 № 1032-р). Доступ из СПС «КонсультантПлюс».
- Правила технической эксплуатации железных дорог Российской Федера-ции: утв. приказом Минтранса России от 21.12.2010 № 286; зарегистрировано в Минюсте России 28.01.2011 № 19627; с изм. и доп., вступ. в силу с 01.07.2017.
- Положение о проведении планово-предупредительного ремонта верхнего строения пути, земляного полотна и искусственных сооружений железных дорог Союза ССР. – М.: Стройиздат, 1964. – 45 с.
- О переходе на новую систему ведения путевого хозяйства на основе по-вышения технического уровня и внедрения ресурсосберегающих технологий: приказ МПС РФ № 12Ц от 16.08.1994. – М.: 1994 г.
- Технические условия на работы по ремонту и планово- предупредительной выправке пути: утв. МПС РФ от 28.06.1997 г. – М.: Транс¬порт, 1998 г.
- Концепция реформирования организационной структуры путевого ком-плекса // Путь и путевое хозяйство. – 2001. – № 7. – С. 3-9.
- Положение об организации участковой системы текущего содержания пути: утв. распоряжением ОАО «РЖД» от 13.12.2013 г. № 2758р.
- Инструкция по содержанию земляного полотна железнодорожного пути: ЦП-544: утв. МПС РФ от 30.03.1998 г. – М.: Транспорт, 2000. – 189 с.
- Положение о системе ведения путевого хозяйства ОАО «РЖД»: утв. распоряжением ОАО «РЖД» от 31.12.2015 г. № 3212 р.
- Инструкция по устройству, укладке, содержанию и ремонту бесстыково¬го пути: утв. распоряжением ОАО «РЖД» от 14.12.2016 г. № 2544/р.
- Инструкция по текущему содержанию железнодорожного пути: утв. распоряжением ОАО «РЖД» 14.11.2016 г. № 2288/р.
- Карпущенко, Н.И. Обеспечение надежности рельсов, имеющих коррози- онно-усталостные повреждения / Н.И. Карпущенко, А.В. Быстров, П.С. Труханов // Известия Транссиба. – 2015. – № 3 (23). С. 104-108.
- Каменский, В. Б. Направления совершенствования системы ведения пу-тевого хозяйства / В. Б. Каменский. – М.: Академкнига, 2006. – 392 с.
- Гапанович, В. А. На основе комплексных показателей рисков / В. А. Гапанович // Железнодорожный транспорт. – 2010. – № 4. – С. 35-37.
- Гапанович, В. А. Белая книга ОАО «РЖД». Стратегические направления научно-технического развития компании / В. А. Гапанович // Железнодорожный транспорт. – 2007. – № 9. – С. 165-172.
- Козлов, Ю. П. Принципы и методология реализации основных положе¬ний Закона о транспортной безопасности / Ю. П. Козлов, В. Н. Цигичко, Д. С. Черкашин // Транспорт Российской Федерации. – 2007. – № 9. – С. 50-56.
- Гапанович, В. А. Программа научно-технического развития ОАО «РЖД» / Г. А. Гапанович // Железнодорожный транспорт. – 2007. – № 2. – С. 2-7.
- ГОСТ 27.002-2015. Межгосударственный стандарт. Надежность в тех¬нике. Термины и определения. – Взамен ГОСТ 27.002-89; введ. 01.03.2017. – Москва: Стандартинформ, 2016. – 28 с.
- РД 50-690-89. Руководящий документ по стандартизации. Методические указания. Надежность в технике. Методы оценки показателей надежности по экс-периментальным данным. – Взамен ГОСТ 27.504-84; введ. 01.01.1991. – Москва: Изд-во стандартов, 1990. – 136 с.
- РД 50-204-87. Руководящий документ по стандартизации. Методические указания. Надежность в технике. Сбор и обработка информации о надежности из-делий в эксплуатации. Основные положения. – Москва: Изд-во стандартов, 1987. – 14 с.
- Дружинин, Г. В. Надежность автоматизированных производственных систем / Г. В. Дружинин. – 4-е изд., перераб. и доп . – М. : Энергоатомиздат, 1986 . – 480 с.
- Кубарев, А. И. Надежность в машиностроении / А. И. Кубарев. – М.: Из- во стандартов, 1989. – 224 с.
- Баранов, Н. А. Основы теории безопасности динамических систем / Н. А. Баранов, Н. А. Северцев. – М.: Вычислительный центр им. А. А. Дородни¬цына Российской акад. наук (ВЦ РАН), 2008. – 236 с.
- Дивеев, А. И. Универсальные оценки безопасности: монография /
A. И. Дивеев, Н. А. Северцев. – М.: Изд-во Рос. ун-та дружбы народов, 2005. – 87 с. - Covello, V. T. Risk Assesment Methods // V. T. Convello, M. V. Merkhofer. Plenum Press, London, 1993. – 306 p.
- Белов, П. Г. Системный анализ и моделирование опасных процессов в техносфере: учебное пособие / П. Г. Белов. – М.: Изд. центр «Академия», 2003. – 512 с.
- Управление риском: Риск. Устойчивое развитие. Синергетика /
B. А. Владимиров, Ю. Л. Воробьев, С. С. Салов и др. – М.: Наука, 2000. – 431 с. - Хованский, Н. В. Математические основы представления рисков в сложных системах / Н. В. Хованский. – СПб.: Изд-во СПбГУ, 1998. – 305 с.
- Хохлов, Н. В. Управление риском / Н. В. Хохлов. – М.: ГОНИТИ, 1999. 215 с.
- Пригожин, И. Современная термодинамика (от тепловых двигателей до диссипативных структур) / И. Пригожин, Д. Кондепуди. – М.: Мир, 2002. – 461 с.
- Куклев, Е. А. Модели рисков и катастроф как маловероятных событий в системах с дискретными состояниями / Е. А. Куклев // Сборник траспортной меж-дународной конференции «Системный анализ и системное моделирование». – СПб.: ЛЭТИ, 2003. – С. 15-18.
- Хенли, Э. Дж. Надежность технических систем и оценка риска: пер. с англ. / Э. Дж. Хенли, Х. Кумамото. – М.: Машиностроение, 1984. – 528 с.
- Karwowski, W. Fuzzy concept in Human Factors / W. Karwowski, A. Mital // Ergonomics Research Application of Theory in Human Factors. – 1986. – № 6 – p. 41¬54.
- Сосновский, Л. А. Состояние объектов и ситуации безопасности / Л. А. Сосновский // Чрезвычайные ситуации: предупреждения и ликвидация: тез. докл. II Международ. науч.-практ. конф., 23-25 июня 2003 г. – Минск, 2003. – Ч. 1. – С. 136-137.
- Сосновский, Л. А. Показатель безопасности и оперативная характери¬стика риска: метод. указания / Л. А. Сосновский – Гомель: БелГУТ, 1991. – 16 с.
- Махутов, Н. А. Риск применения и безопасность силовых систем / Н. А. Махутов, Л. А. Сосновский // Труды 4-го Международного симпозиума по трибофатике (ISTF4), 23-27 сентября 2002 г., Тернополь (Украина). – Тернополь, 2002. – Т. 1. – С. 44-49.
- Сосновский, Л. А. Прогнозирование рисков / Л. А. Сосновский // Чрез-вычайные ситуации: предупржедение и ликвидация: тез. докл. II Международ. науч.-практ. конф., 23-25 июня 2003 г. – Минск, 2003. – Ч. 1. – С. 134-135.
- Попов, В. А. Проблемы повышения скоростей, массы и безопасности движения поездов на подходах к портам Дальнего Востока / В. А. Попов, Н. И. Карпущенко, И. А. Котова. – Новосибирск: Наука, 2004. – 250 с.
- Крысанов, Л. Г. Эксплуатационная стойкость и надежность рельсов / Л. Г. Крысанов // Путь и путевое хозяйство. – 2008. – № 5. – С. 2-5.
- Абдурашитов, А. Ю. Совершенствовать систему ведения рельсового хо-зяйства / А. Ю. Абдурашитов, Е. А. Шур // Путь и путевое хозяйство. – 2005. – № 6. – С. 2-6.
- Рейхарт, В. А. Рельсы для высокоскоростных магистралей / В. А. Рей- харт // Путь и путевое хозяйство. – 2006. – № 12. – С. 6-8.
- ГОСТ Р 51685-2013. Рельсы железнодорожные. Общие технические условия. В редакции (изменение 1), утв. Приказом Росстандарта от 24.02.2016 № 65-ст. – М.: Стандартинформ, 2014. – 31 с.
- Инструкция по определению назначенного ресурса рельсов в зависимо¬сти от условий эксплуатации и фактического состояния рельсов. Утверждена рас-поряжением ОАО «РЖД» от 31.12.2015 № 3193 [электронный ресурс] // СПС «Аспижт» – (Дата обращения: 01.03.17).
- Методика классификации и специализации железнодорожных линий ОАО «РЖД». Утв. распоряжением ОАО «РЖД» от 23.12.2015 г. № 3048р. – М.: ОАО «РЖД», 2015. – 7 с.
- Положение об участковой системе текущего содержания. Утв. распоря-жением ОАО «РЖД» от 13.12.2013 г. № 2758р. – М.: ОАО «РЖД», 2013. – 28 с.
- Инструкция «Дефекты рельсов. Классификация, каталог и параметры дефектных и остродефектных рельсов». Утв. распоряжением ОАО «РЖД» от 23.10.2014 г. № 2499р.
- Инструкция по обеспечению безопасности движения поездов при произ-водстве путевых работ. Утв. распоряжением ОАО «РЖД» от 29.12.2012 г. № 2790р.
- Ромен, Ю. С. Проблема формы профиля в системе «колесо – рельс» / Ю. С. Ромен // Путь и путевое хозяйство. – 2016. – № 12. – С. 22-26.
- Шаньгин, Р. В. Анализ эксплуатации рельсов категории ДТ на Западно-Сибирской ДИ / Р. В. Шаньгин, О. М. Соколов // Путь и путевое хозяйство. – 2017. – № 2. – С. 2-5.
- Шур, Е. А. Износостойкость рельсовых и колесных сталей / Е.А. Шур, Н. Я. Бычкова, Д. П. Марков и др. // Трение и износ. – 1995. – Т. 16, № 1. – С. 80-91.
- Шур, Е А. Увеличить ресурс рельсов, лимитируемый их боковым изно¬сом / Е. А. Шур, А. И. Борц, А. Ю. Абдурашитов // Путь и путевое хозяйство. – № 5. – 2015 – С. 2-9.
- Прилепко, А. И. Влияние параметров кривых на срок службы рельсов / А. И. Прилепко // Путь и путевое хозяйство. – 2014. – № 7. – С. 7-9.
- Лужнов, Ю. М. О влиянии поверхностной прочности материалов на фрикционные свойства колес и рельсов / Ю. М. Лужнов // Вестник ВНИИЖТ. – 2012. – № 2. – С. 38-41.
- Куксенова, Л. И. Износостойкость конструкционных материалов / Л. И. Куксенова, С. А. Герасимов, В. Г. Лапетва. – М.: МВТУ, 2011. – 327 с.
- Шур, Е. А. К вопросу об оптимальном соотношении твердости рельсов и колес / Е. А. Шур // Колесо-рельс: сб. докладов научн.-практ. конф. – Щербинка, 2003. – С. 87-93.