Сейчас ваша корзина пуста!
Повышение качества железнодорожных пружинных клемм на основе совершенствования режимов обработки
Цикл статей:
Глава 1 – Повышение качества железнодорожных пружинных клемм на основе совершенствования режимов обработки
Введение
Российская Федерация – мощная железнодорожная держава. Протяженность железных дорог страны огромна, а их эксплуатация осуществляется в различных климатических поясах. Темпы роста отечественной экономики диктуют значительное увеличение объемов грузооборота и повышение производительности железных дорог. Основными путями интенсификации перевозок служат повышение скоростей движения поездов и их веса, что связано с резким ростом силового воздействия подвижного состава на путь. В подобных условиях устойчивое функционирование дорог во многом зависит от решения проблемы рельсовых скреплений. Данная проблема решается на основе перехода на прогрессивные виды упругих рельсовых скреплений для железобетонных шпал. Переход на упругие пружинные скрепления является в настоящее время кардинальным решением при разработке новых конструкций этих узлов, удовлетворяющих современным требованиям и обеспечивающих, повышение эксплуатационных возможностей железных дорог при снижении затрат на их текущее содержание [1].
На железных дорогах страны осваивается новый узел рельсового скрепления используемого на наиболее ответственных участках пути: стрелочных переводах, кривых малых радиусов, участках с высокими осевыми нагрузками. Принципиальным отличием нового узла скрепления является замена, в нем промежуточной жесткой клеммы с двухвитковой пружинной шайбой и стандартным клеммным болтом на пружинную прутковую клемму ОПЮ5 в комплекте с плоской жесткой шайбой и с клеммным болтом с квадратным подголовком. Данная конструкция узла обеспечивает более высокую пружинность скрепления особенно на пути с жестким подрельсовым основанием, возможность регулировки положения рельса по высоте в пределах 10-20 мм, снижение трудоемкости и затрат на текущее содержание пути, что особенно актуально для России с большой протяженностью железных дорог в сложных климатических условиях. Клемма ОП 105 обладает большой податливостью в упругой области и в то же время позволяет прижимать рельс к подкладке со значительным усилием, что исключает необходимость применения противоугонов. Прутковые пружинные клеммы ОП 105 в случае их применения в раздельных скреплениях рельсов со шпалами способны во много раз повысить эксплуатационные характеристики железнодорожного пути. С использованием таких клемм рельсовый путь приобретает пространственную упругость, обеспечивается усиление самого промежуточного скрепления, и оно становится способным выдержать длительные динамические нагрузки [1].
Передовым предприятием, на котором было организовано производство клемм ОП 105, стал ОАО «Магнитогорский метизно-калибровочный завод ММК-МЕТИЗ».
Технологическая схема производства железнодорожных пружинных клемм ОП105 включает три взаимосвязанных технологических блока: подготовительных операций, формообразующих операций и окончательной термической обработки и контроля. Структуру формирования качества составляют операции,, базирующиесяна использовании методов различной физической природы: термической обработки, холодной и горячей деформации, обработки резанием. Данная технологическая схема позволила заводу наладить бесперебойный выпуск продукции и в течение длительного времени удерживать значительную часть рынка,данной продукции. Однако требования к качеству клемм непрерывно ужесточаются, что нашло отражение в новых редакциях нормативно-технической документации ОСТ 32.156.-2000 и ОП 105 ТУ, в которых предусматривается 100% контроль качества; выпускаемой продукции, введены новые требования по геометрическим размерам и пружинящим свойствам.
Повышение требований к качеству пружинных клемм имеет целью исключить опасность их внезапного хрупкого разрушения при сборке скреплений, а также в процессе эксплуатации под действием прилагаемых: в пути нагрузок. Опыт производства пружинных клемм показал, что действующая технология не в полном объеме отвечает более жестким требованиям потребителя, что привело к увеличению выпуска несоответствующей продукции, особенно по геометрическим показателям качества и твердости готовых клемм.
Технологический процесс, разработанный в условиях дефицита времени, средств и сложности решаемых задач в период освоения уникального оборудования на основе обобщения собственного производственного опыта в процессе поиска и сравнения большого числа возможных вариантов изготовления, так как теоретические данные по технологии получения пружинных клемм в научной литературе не содержались, а опыт зарубежных фирм был не доступен, требует своего совершенствования, поскольку многие режимы обработки металла назначались не в результате целенаправленных научных и производственных исследований, а исходя из общих представлений о процессах, и без учета специфики взаимодействия различных по физической природе технологических операций обработки нестандартной кремнистой стали 40С2.
В связи с этим актуальным является комплекс исследований, направленный, на обеспечение заданных показателей качества клемм, уменьшение несоответствий и дефектности.
На наш взгляд повышение качества клемм может быть достигнуто на основе совершенствования технологических режимов подготовки металла к формообразованию, обеспечивающих устранение причин неблагоприятной технологической наследственности при формировании требуемых геометрических размеров клемм, и режимов их последующей окончательной термообработки. Такой подход позволит получать на этапе подготовительных операций металл с качеством; отвечающим специфике дальнейшей переработки в технологическом блоке формообразования и обеспечивающим формирование требуемых геометрических размеров »промежуточных заготовок и пространственного контура клемм, а на этапе окончательной термообработки достичь необходимого уровня качества готовой продукции в целом.
В развитие этого направления необходимо установить причины возникновения неблагоприятных наследственных связей на начальных этапах производства, инициирующих несоответствия по геометрическим размерам клемм, и разработать меры, направленные на их устранение. Провести исследования процессов формирования, качества стали 40С2 в блоке подготовительных операций с учетом специфики взаимодействия различных технологических методов между собой, и разработать, усовершенствованные режимы подготовки металла к формообразованию, обеспечивающие на последующих операциях достижение геометрических размеров промежуточных заготовок и пространственного контура клемм требуемого качества. Выполнить комплексные исследования динамики формирования прочностных и пластических свойств стали 40С2 при термическом упрочнении, включая оценку их взаимосвязи с уровнем пружинящих свойств изделия, и разработать усовершенствованные режимы окончательной термообработки отформованных клемм, обеспечивающие достижение заданного уровня качества готовой продукции.
Изучив процессы формирования качества в технологических блоках подготовительных операций и окончательной термообработки и контроля, на основе установленных закономерностей, необходимо разработать методику управления качеством пружинных клемм, позволяющую определять результативные технологические режимы, предупреждающие и корректирующие воздействия с целью обеспечения заданного уровня качества готовой продукции.
Представленная диссертационная работа является продолжением и дальнейшим развитием комплекса исследований, выполняемых на кафедре машиностроительных и металлургических технологий ГОУ ВПО «МГТУ», по освоению и совершенствованию производства пружинных клемм различных конструкций для рельсовых скреплений.
Состояние производства и проблематика формирования качества пружинных клемм
Современные требования к качеству пружинных клемм ОП 105 для железнодорожных рельсовых скреплений
Жесткие условия эксплуатации, динамические нагрузки, ощутимые температурные перепады, увлажнение и высушивание, замораживание и оттаивание, воздействие нефтепродуктов и других агрессивных веществ, предъявляют исключительно высокие требования к надежности и долговечности железнодорожных рельсовых скреплений (рис. 1.1).
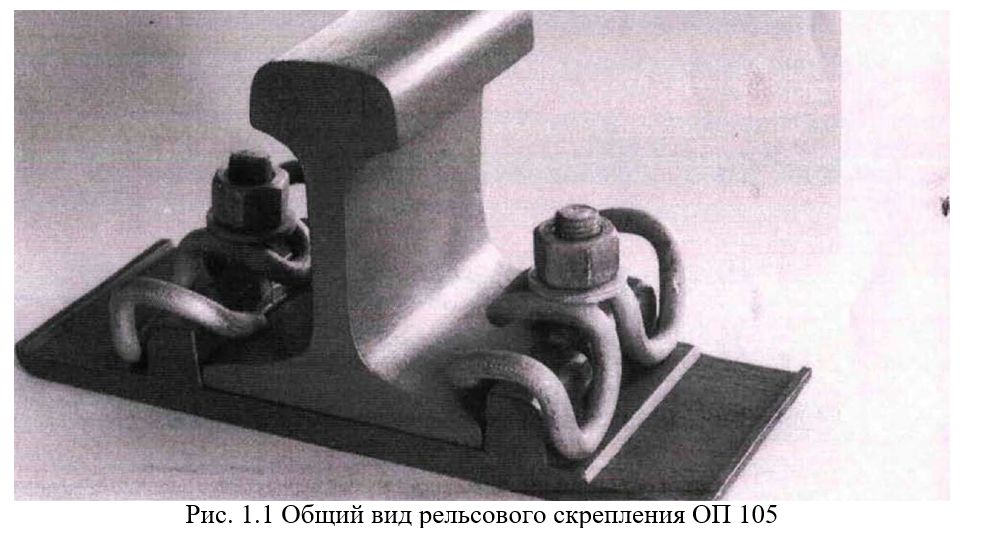
Пружинная клемма ОПЮ5 для железнодорожного рельсового скрепления является изделием сложной пространственной формы с жестко регламентированными геометрическими размерами, механическими свойствами, качеством поверхности и специальными свойствами (рис.1.2).
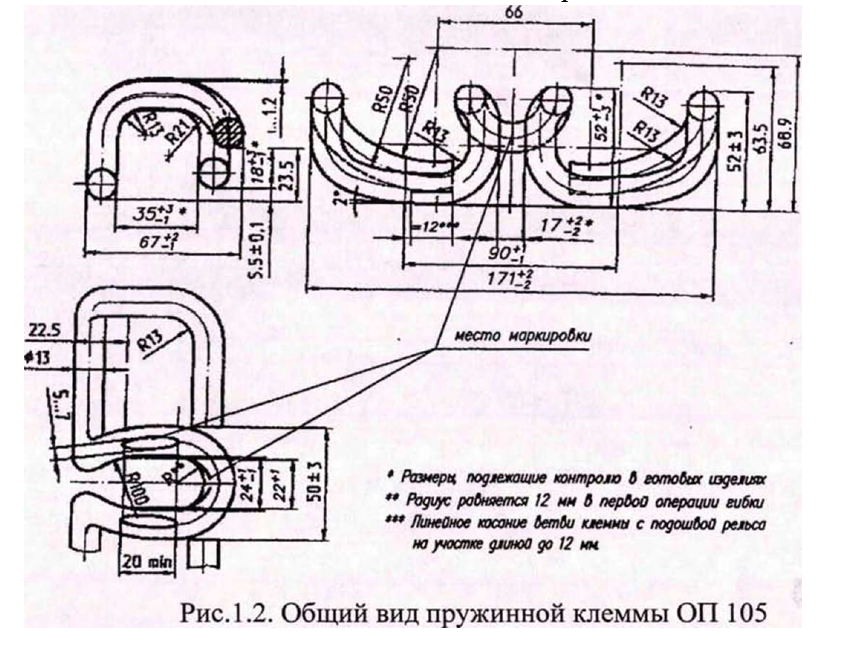
Принципиальным отличием клеммы ОПЮ5 от других видов клемм (АРС, ЖБР) является сложная пространственная форма. Конфигурация клеммы составлена многочисленными элементами в виде прямых и переходных участков переменной кривизны, работающих на изгиб и кручение. Пространственная форма клеммы обеспечивает большую длину изгибаемых и скручиваемых участков до мест соприкосновения с рельсом и подкладкой, и поэтому обладает особо низкими и постоянными значениями жесткости при больших прогибах [1]. Качество пружинных клемм оценивается по ряду параметров — точности исполнения геометрических размеров профиля, твердости, величине обезуглероженного слоя, наличию поверхностных дефектов и др. Структура обеспечения качества пружинных клемм ОПЮ5 для железнодорожных рельсовых скреплений показана на рис. 1.3. Конкретные показатели качества железнодорожных пружинных клемм ОПЮ5 установлены в отраслевых нормативно-технических документах: стандарте ОСТ 32.156-2000 и ТУ ОПЮ5 (таблица 1.1.).
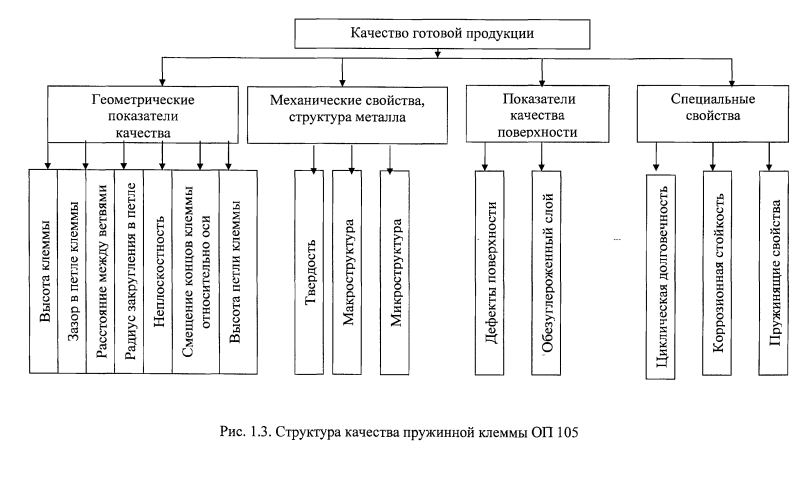
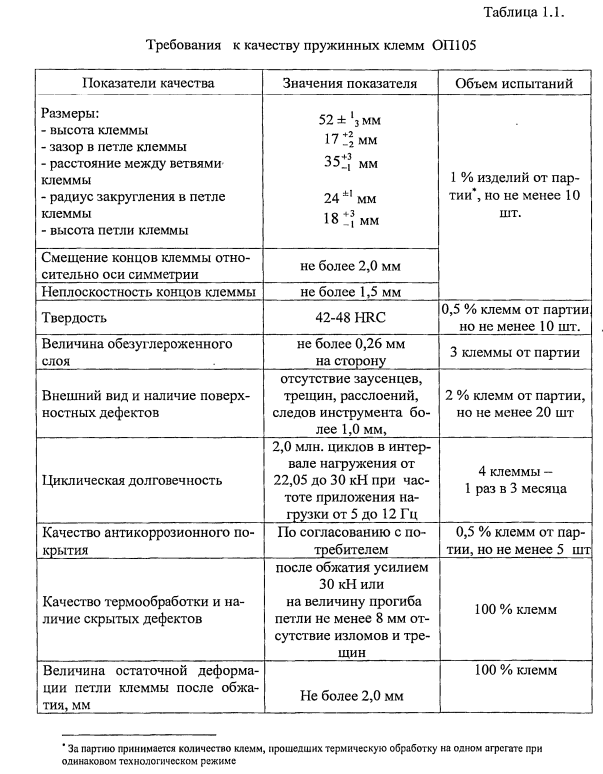
Для производства клемм нормативно-технической документацией предусмотрено использование нестандартной кремнистой стали 40С2. Кремний создает в твердом растворе направленные связи, а при повышенных концентрациях обеспечивает упорядоченность распределения атомов в решетке, что, в свою очередь, повышает сопротивление движению дислокаций на стадии микропластической деформации [2]. Кремний в малой степени увеличивает количество остаточного аустенита, но значительно повышает сопротивление малым пластическим деформациям, что оказывает положительное влияние на величину длительной прочности клемм [3]. Применение стали 40С2 позволяет использовать в качестве закалочной среды воду вместо масла, что значительно удешевляет технологический процесс производства клемм и делает его экологически безопасным. Сталь марки 40С2 менее склонна к обезуглероживанию поверхности и трещинообразованию, характеризуется-большей пластичностью и пониженным сопротивлением пластической деформации в холодном и горячем состоянии, по сравнению с другими, потенциально возможными для изготовления клемм, марками стали 55С2, 60С2, 60С2ХА и 60С2ХФА. Это дает возможность вести обработку давлением на универсальном оборудовании при удовлетворительной стойкости инструмента [4].
Особенности технологического процесса и проблематика формирования качества пружинных клемм
Содержание любой технологии производства составляют технологические процессы, материализованные в виде конструкций и компоновок машин. Именно в них, наряду с качеством исходного материала и режимами обработки, закладываются потенциальные возможности по формированию качества готовой продукции.
В условиях ОАО «ММК-МЕТИЗ» процесс производства железнодорожных пружинных клемм ОП 105 был организован в короткое время, на основе обобщения собственного производственного опыта в процессе поиска и сравнения большого числа возможных вариантов изготовления, так как теоретические данные по технологии получения пружинных клемм в научной литературе не содержались, а опыт зарубежных фирм был не доступен [88]. В связи с оригинальной сложной формой клеммы оказалось невозможным заимствование опыта отечественных производителей пружинных клемм более простых конструкций ЖБР, АРС калужского завода «Ремпутьмаш», Пермского мотовозоремонтного завода, горновского завода «Спецжелезобетон».
Ограниченные возможности прямого использования зарубежного опыта объективно предопределили проведение широкомасштабной подготовительной экспериментальной, исследовательской и конструкторской работы по разработке производства и его освоению. Основное внимание было сосредоточено на поиске эффективных приемов формирования сложного пространственного контура пружинной клеммы и разработки технологической оснастки и оборудования для производства данного вида продукции [85,88]. Решение вопросов подготовки металла к формообразованию и окончательной термической обработки было сориентировано на существующую материально-техническую базу предприятия.
Намеченные технологические подходы и технические решения по формообразованию профиля клеммы [85], базирующиеся на использовании холодной гибки и горячей штамповки, были предоставлены машиностроительным фирмам стран Западной Европы, имеющим опыт проектирования и изготовления комплектов оборудования для производства1 пружинных клемм. Впоследствии фирмами “MRP” (Германия), “ВКЕТ”(Франция), NEWELCO (Англия) были сконструированы, изготовлены и поставлены автомат холодной гибки заготовки клеммы, пресс гибки-штамповки для придания изделиям окончательного профиля и индукционная установка для нагрева заготовок под горячую штамповку.
Решение многочисленных вопросов организации выпуска нового вида продукции было инициировано ходом последующей работы по налаживанию и освоению производства после монтажа и наладки оборудования, поставленного на завод от зарубежных фирм [5].
Сложившийся технологический процесс изготовления клемм в условиях ОАО «ММК-МЕТИЗ» имеет линейно-последовательную структуру: каж-. дая последующая операция выполняется после полного завершения предшествующей,, совмещение операций во времени осуществляется при синхронизации их выполнения. На рис. 1.4. показана карта технологического потока производства пружинных клемм.
Анализ технологии позволяет выделить в сложившейся схеме производства железнодорожных пружинных клемм три взаимосвязанных техноло- , гических блока: технологический блок подготовительных операций, блок формообразующих операций, блок окончательной термообработки и контроля. Структуру процесса формировании качества пружинных, клемм в выделенных технологических блоках составляют операции, базирующиеся на использовании методов различной-физической природы: термической обработки, холодной и горячей пластической деформации, обработки резанием (рис. 1.5).
Формирование оригинального нестандартного профиля* клеммы осуществляется в два этапа с использованием операций холодной гибки и горячей штамповки, выполняемых на специализированной поточной линии, и является: одним из наиболее важных звеньев в технологии производства. На* первом этапе: формообразования предусмотрена холодная гибка промежуточного профиля» клеммы «омега»’ из круглой заготовки. На втором – пространственный контур клемма приобретает в процессе горячей; штамповки с индукционного нагрева в штампе с выталкивателем-прижимом.
Холодная гибка осуществляется: последовательно по различным участкам заготовки в несколько стадий (рис. 1.6).
Гибка, с точки зрения ОМД, относится к формоизменяющим операциям штамповки [20], для которых характерна реализация пластической деформации в специальной технологической’ оснастке – гибочных штампах. При этом необходимо обеспечить получение заданной точности изделий и реализацию пластической деформации давлением без разрушения заготовки.
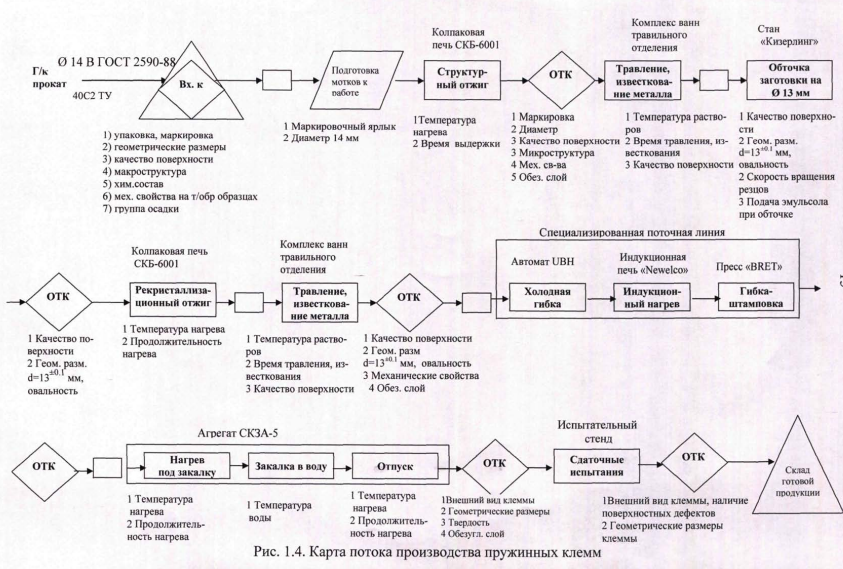
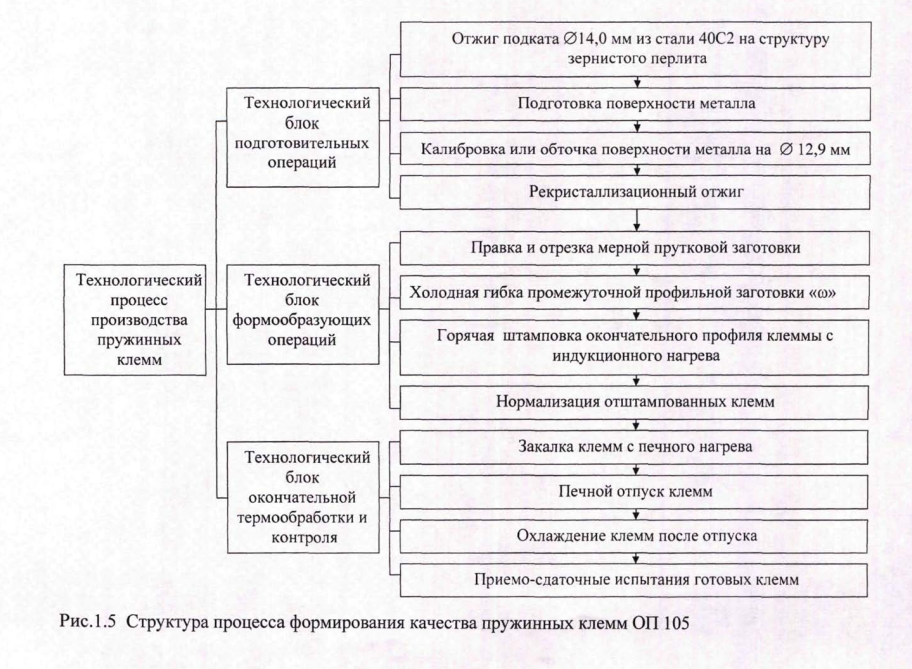
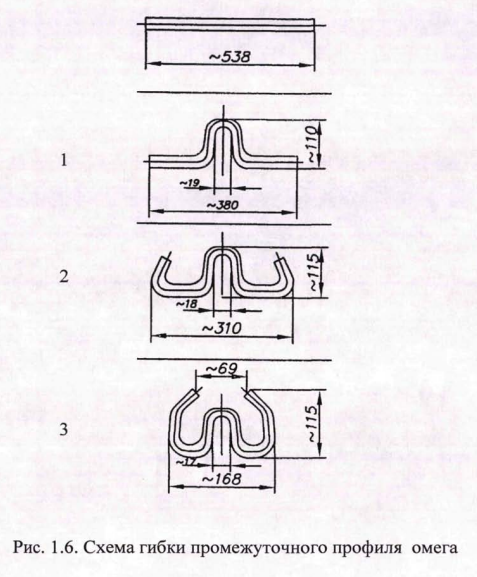
Проблемным аспектом, в случае применения в качестве формообразующей операции при изготовлении пружинных клемм метода холодной гибки, является возможность выполнения малого радиуса кривизны в готовых изделиях, отличающихся большими размерами сечения обрабатываемого металла [94]. Критерием приемлемости данного процесса и одним из основных требований к его технологичности является значение относительного радиуса гибки гот = гтщ/с1, которое определяет возможность деформирования металла без нарушения его сплошности (с! – диаметр заготовки). На технологических переходах гибки среднее значение величины гот составляет 1,24, что согласно данным работ [83,84], соответствует для доэвтектоидных угле
родистых и некоторых конструкционных легированных сталей с содержанием углерода от 0,3 до 0,7 % наименьшему допустимому значению.
Для осуществления гибки в таких условиях и достижения требуемых геометрических размеров промежуточного профиля клемм резко возрастает роль качества исходного металла, и подготовки его к формообразованию с обеспечением однородной структуры и механических свойств.
Производственный опыт показывает, что структура и механические свойства исходного металла играют большую роль в формировании качества передельной заготовки, предназначенной для производства пружинных клемм. В связи с этим особое внимание на подготовительных операциях должно уделяться подготовке структуры металла, как основного фактора, определяющего стабильность процессов последующего деформирования [6,7]. Вопросы, влияния- структуры металла на пластичность при холодной; деформации рассмотрены в работах [8-10].
Установлено, что наибольшими пластическими свойствами и: минимальным сопротивлением деформации обладает сталь, подвергнутая отжигу на структуру зернистого перлита. Структура зернистого перлита обеспечивает высокий1 запас пластичности, а следовательно; и более высокую технологичность операций холодного формообразования профиля клеммы. Зернистый перлит является оптимальной исходной структурой перед закалкой, так как обеспечивает меньшую склонность к росту аустенитного зерна, расширяет интервал допустимых закалочных температур, уменьшает склонность к растрескиванию [11]. В технологии производства пружинных клемм структура зернистого перлита достигается использованием, сфероидизирующего (структурного) отжига.
Особенности эксплуатации пружинных изделий, к которым относятся и упругие клеммы, заключаются в том, что наиболее нагруженными-являются поверхностные слои прутка клеммы. Напряжения кручения и изгиба, действующие в поверхностных слоях и принимающие наибольшие значения в местах технологических перегибов клемм, могут при наличии дефектов на поверхности клемм в виде трещин, волосовин, рисок, вмятин от технологической оснастки приводить к излому клемм в эксплуатации. Важнейшим фактором, отвечающим за эксплуатационную стойкость упругих клемм рельсовых скреплений, является качество их поверхности, которое определяется техническими мероприятиями как на стадии производства прутка стали 40С2, так и на стадии производства самой клеммы. Из литературы известно, что кремнистые стали при горячей прокатке более склонны к возникновению на поверхности проката дефектов в виде волосовин, рисок и др. [12,13]. Эксплуатация готовых изделий с наличием в них обезуглероженного слоя и поверхностных дефектов прокатного происхождения при работе в условиях многоцикловой усталости, как известно, приводит к резкому снижению предела выносливости и релаксационной стойкости упругих элементов [14]. Во ВНИИЖТ для сравнительной оценки горячекатаного и калиброванного прутка стали 40С2 были проведены,их усталостные (в воздушной среде) и корро- зионно-усталостные (в 0,5*н растворе хлорида натрия) испытания [15].
Испытания образцов стали 40С2 с различной чистотой поверхности прутка проводили после стандартной термической обработки — закалки и отпуска. Результаты испытаний показывают, что в воздушной среде предел выносливости стали 40С2 с калиброванной поверхностью значительно выше (на 17 %), чем у горячекатаной (рис. 1.7). Опыт эксплуатации рельсовых скреплений показывает, что срок службы клемм из калиброванного или обточенного прутка на 30…40 % выше срока службы клемм из горячекатаного прутка.
Этот результат подтверждает необходимость применения калиброванного (обточенного) проката для изготовления клемм. Данное направление реализовано всеми основными производителями упругих элементов верхнего строения пути в мировой практике производства упругих деталей, в том числе и такими известными у нас фирмами, как Уобб^Ь и Репс1го1 [16,17].
Также мировым опытом производства и эксплуатации упругих клемм показано, что повышение их стоимости в результате применения качественного прутка экономически оправданно за счет снижения затрат на текущее содержание пути с такими клеммами [18].
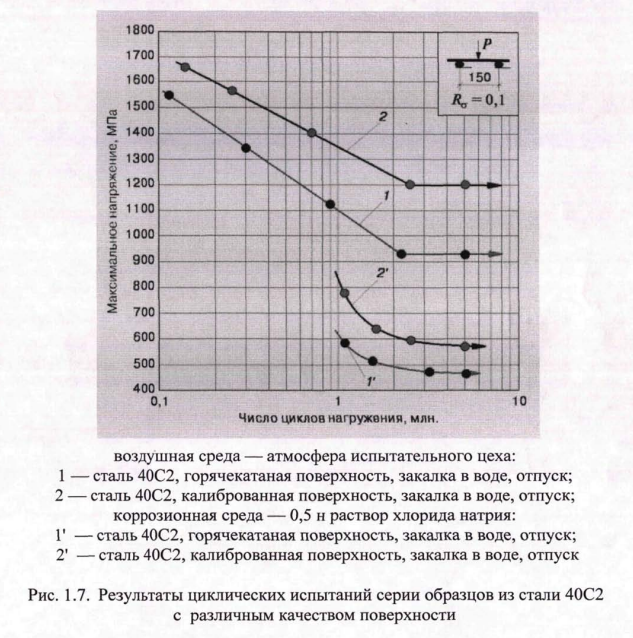
Это обстоятельство инициировало включение в технологический процесс подготовки металла к формообразованию операции калибрования или обточки поверхности отожженного горячекатаного подката вращающимися резцами на установке «Кизерлинг».
Однако в процессе калибрования или обточки сталь наклёпывалась и становилась непригодной для стабильного осуществления последующих операций холодного формообразования профиля омега, осуществляемых с малыми радиусами гибки [19]. Это вызвало необходимость включения в технологический процесс еще одной термической обработки рекристаллизационного отжига.
В условиях завода процессы отжига на зернистый перлит и рекристаллизационного отжига выполняются в колпаковых печах без защитной атмосферы. В силу специфики садочных печей режим термообработки, обеспечивающий требуемый уровень структурного состояния металла и механических свойств, характеризуется низкой производительностью и значительной продолжительностью, а следовательно, и большими материальными затратами. Отожженный металл приобретает на поверхности значительный обезуг- лероженный слой, а вследствие перепада температур по высоте садки неравномерность структурного состояния и механических свойств. Качество металла, получаемое по действующим режимам, не обеспечивает стабильного процесса формообразования на этапе холодной гибки.
Окончательная термообработка, то есть закалка и отпуск отформованных клемм, осуществляется на агрегатах непрерывного действия типа СКЗА, в условиях поточного производства. В настоящее время на заводе при окончательной термической обработке отформованных пружинных клемм температура нагрева металла в закалочной печи составляет 880 °С. Как показывает обзор литературы [3,8] такая температура более свойственна сталям 55С2, 60С2 и может быть недостаточной для гомогенизации аустенита в кремнистой стали 40С2 с пониженным содержанием углерода. Это инициирует разброс показателей твердости клемм и снижает эксплуатационные показатели качества готовых изделий.
В процессе освоения нового типа рельсовых скреплений и накопления сведений о его эксплуатации, требования к качеству клемм ОПЮ5 постоянно ужесточались.
В целях обеспечения гарантированного качества выпускаемой продукции по инициативе ОАО «Российские железные дороги», в новые редакции отраслевых стандартов на пружинные клеммы, включено требование 100 % контроля всех изделий по окончании производственного цикла их изготовления и введены новые требования по пружинящим свойствам изделий. Способом такого контроля является испытание клемм принудительным обжатием регламентированным нормативно-технической документацией усилием 30 кН. Испытание клемм на осадку является последней операцией производственного процесса их изготовления, предназначенной исполнять исключительно контрольные функции, такие как выявления брака после термообработки и скрытых дефектов изделия.
Опыт производства пружинных клемм по новой нормативно- технической документации показал, что действующая технология оказалась не готова к удовлетворению ужесточившихся требований потребителя к качеству продукции. Как следствие увеличился выпуск несоответствующей продукции.
Из анализа диаграмм Парето установлено, что наибольшие несоответствия наблюдаются по геометрическим размерам и значениям твердости готовых клемм, определяющим уровень их служебных характеристик (рис. 1.8).
Технологический процесс, который был разработан в условиях дефицита времени, средств и сложности решаемых задач в период освоения уникального оборудования требует своего совершенствования, поскольку многие технологические режимы подготовки используемой нестандартной стали 40С2 к холодной пластической деформации и придания конечных свойств отштампованным изделиям назначались исходя из общих представлений о процессах, а не в результате целенаправленных научных и производственных исследований, без учета взаимодействия технологических методов разной физической природы на этапах подготовительных операций, формообразования и финишной обработки.
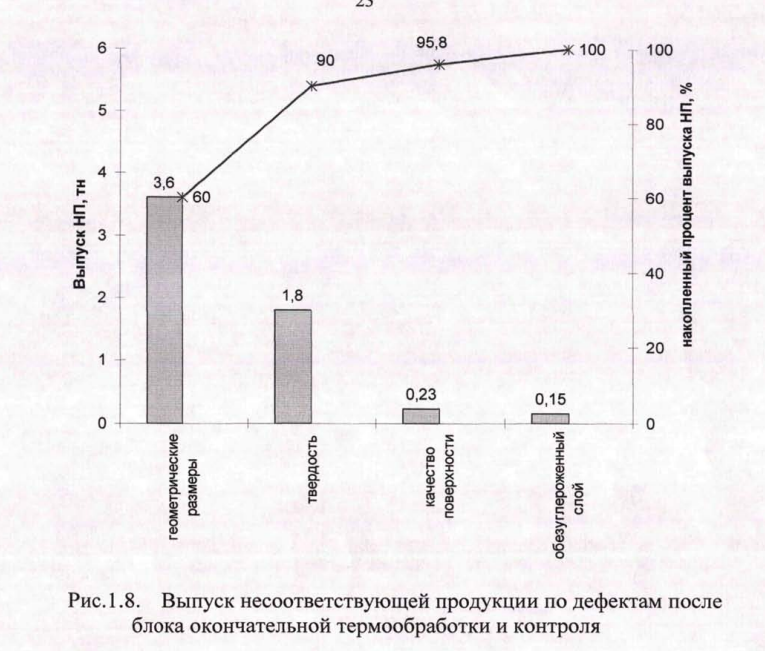
Без проработки вопросов повышения качества продукции, изготовленные на ОАО «ММК-МЕТИЗ» клеммы могут оказаться невостребованными на рынке. Принимая во внимание значительные средства, вложенные заводом в организацию производства нового вида продукции, приобретенный при этом практический опыт и накопленный научный потенциал, по которому предприятие занимает лидирующее положение в отрасли, вопросы повышения качества клеммы ОП 105 являются приоритетными.
Современные подходы к управлению качеством продукции, выбор и обоснование направлений исследований
В любом технологическом процессе объектом управления являются показатели качества продукции, установленные нормативно-технической документацией [21]. Для современного этапа развития характерен процесс рас
ширения набора показателей качества, определяющих способность удовлетворять те или иные потребности. Это свидетельствует о том, что происходит углубление знаний, расширяются возможности использования различных свойств материалов и изделий с целью более полного удовлетворение потребностей [22]. В достижении нормируемого уровня показателей качества используются различные методы: экономические, организационные, инновационные, технологические, статистические и др. (рис. 1.9) [23]. От грамотного сочетания этих методов зависит эффективность и результативность технологических процессов, и конкурентоспособность продукции [24]. Негласным правилом при этом является разработка путей повышения результативности (экономичности, прибыльности, производительности, действенности) на основе принципа сквозного интегрированного управления качеством и положений всеобщего управления качеством (TQM) [93].
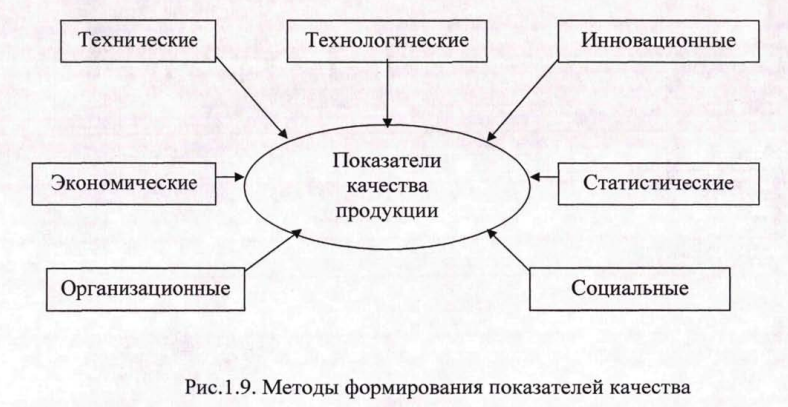
Развиваются комплексные методы, объединяющие различные подходы к управлению качеством [25,26]. Одним из эффективных методов повышения качества на современном этапе принято считать концепцию «Шесть Сигм». Коротко суть этой системы можно сформулировать так: статистический анализ-качество-клиент-прибыль [27]. Внедрение этого метода предусматривает сравнение уровня производства определенной продукции с конкурирующими организациями и определение степени конкурентоспособности производимой продукции [28]. Однако в условиях сложившихся российских производственных отношений получить достоверные данные о конкуренте практически невозможно. В России руководством по разработке и внедрению современной методологии управления качеством являются нормативные документы, созданные на основе стандартов ISO серии 9000; одним из положений которого рекомендуется применение, широко используемых зарубежными производителями, статистических методов для понимания изменчивости- в процессах и их результатах [29] (рис. 1.10)
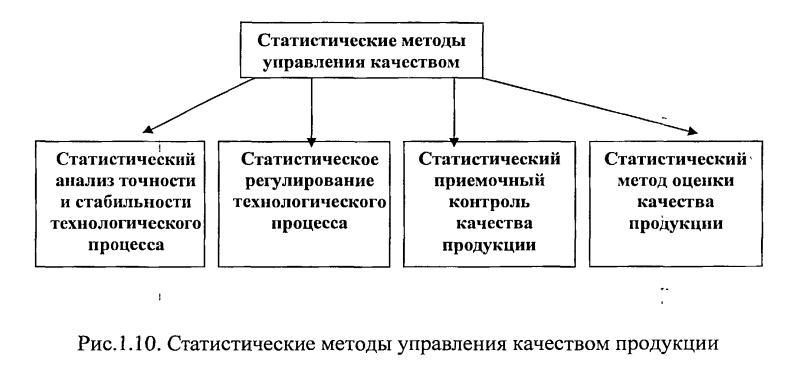
Для оценки стабильности и воспроизводимости технологических процессов используется метод анализа процессов, который включает обширный набор технологий, таких как анализ пригодности процесса, анализ повторяемости и воспроизводимости измерений, анализ Вейбулла, выборочных планов и компонентов дисперсии для случайных эффектов, для расчетов индексов пригодности процесса (например, Ср, Сг, Срк, Ср1, Сри, К, Срт, Рр, Рг, Ррк, Рр1, Рри) [30,31]. В отечественной практике для оценки и управления качеством в технологических процессах применяют коэффициент относительного рассеяния К, коэффициент относительной асимметрии а, коэффициент настроенности процесса Е, коэффициент точности Кт. Совместное ис-
пользование всех вышеперечисленных параметров и коэффициентов можно считать взаимодополняющим.
Основу этих оценок составляют данные статистического приемочного контроля. Определенный недостаток этих методов заключается в отсутствии возможности оперативного вмешательства в технологический процесс в случае неудовлетворительных результатов контроля, так как процедура приемки готовой продукции требует значительных затрат времени. Методы оценки воспроизводимости и стабильности технологических процессов применимы только в том случае, если объект находится в статистически управляемом состоянии. Известные статистические методы (контрольные карты, метод Парето, причинно-следственные диаграммы, гистограммы, контрольные листы, стратификация, диаграмма разброса) позволяют оценить несоответствия, однако не дают конкретных рекомендаций по выявлению причин, вызывающих изменчивость и вариативность технологических процессов и качества продукции. В то же время, когда коренные причины рассматриваемой проблемы устранены, использование методов статистического контроля качества в сочетании с другими подходами, например методом экономного производства, ориентированного на устранение излишних затрат, может дать значительный эффект [32].
При решении задач комплексной оценки эффективности и результативных технологических процессов перспективность использования показал теоретический и математический аппарат квалиметрии [33,87]. В работах [34,35] данный аппарат был использован при оценке эффективности разных вариантов технологии производства через оценку изменения качества продукции при изменении технологии. Однако получаемые при этом единичные и комплексные оценки, учитывающие стабильность и воспроизводимость процессов получения требуемых параметров качества изделия, основываются на значениях коэффициентов конечных операций и не учитывают влияния предыдущих операций технологического процесса, на которых так же формировался этот параметр качества. Большую роль в получении этих оценок- играет достоверность информации, получаемой от экспертов, которая зачастую носит субъективный характер. Применение методов квалиметрии можно считать особенно эффективными в начальной фазе реализации инновационных проектов, связанных со значительными капитальными затратами, для анализа которых оправданным является привлечение значительного круга экспертов-специалистов из различных областей знаний.
Для действующей технологии производства пружинных клемм приоритетом становится обеспечение заданных показателей качества по геометрическим размерам и механическим свойствам, уменьшение несоответствий и дефектности при снижении затрат на производство. Для многостадийного технологического процесса производства пружинных клемм управление качеством продукции может быть эффективно обеспечено через технологию производства, совершенствование технологических переделов, применением современного оборудования^без изменения предназначения операций [37].
Отечественные исследования производства близких по конфигурации к клемме ОП 105 изделий не учитывают многопараметричность технологии, начиная от химического состава стали, прокатки, термической обработки, холодной пластической деформации, повторных термообработок и окончательной термообработки[3,36,38-44]. Результаты исследований не содержат описания и рекомендаций по достижению требуемого уровня качества сложных по форме пружинных изделий из нестандартной кремнистой стали 40С2 в таком сочетании технологических воздействий.
На наш взгляд повышение качества клемм может быть достигнуто на основе совершенствования технологических режимов подготовки металла к формообразованию, обеспечивающих устранение причин неблагоприятной технологической наследственности при формировании требуемых геометрических размеров клемм, и режимов окончательной термообработки отштампованных клемм.
Руководствуясь одним из главных принципов теории технологической наследственности о том, что качество готовой продукции формируется на всем протяжении технологии производства, становится очевидно, что в первую очередь неблагоприятные проявления технологической наследственности должны быть учтены в первоначальных этапах обработки, то есть в блоке подготовительных операций. Этому не противоречит и экономическая целесообразность организации производства, из которой следует, что бороться с несоответствиями и дефектами продукции значительно дешевле на начальных этапах процесса, чем на финишных операциях.
Такой подход позволит получать на этапе подготовительных операций металл с качеством, отвечающим специфике дальнейшей переработки в технологическом блоке формообразования и обеспечивающим формирование требуемых геометрических размеров промежуточных заготовок и пространственного контура клемм, а на этапе окончательной термообработки достичь необходимого уровня качества готовой продукции по механическим свойствам.
В развитие этого направления необходимо раскрыть причины возникновения неблагоприятных наследственных связей на начальных этапах производства, инициирующих несоответствия по геометрическим размерам клемм и разработать меры, направленные на их устранение, при подготовке металла к формообразованию.
Основной задачей такой работы является отыскание в технологических процессах тех операций и переходов, на которых возникают несоответствия снижающие качество продукции, и научное предвидение их дальнейшего развития. По своей сути эта работа представляет задачу «анализа» и выгодно отличается от задачи «черного ящика», распространенной в теории технических систем [49]. Такой анализ позволит наметить соответствующие технологические методы управления качеством продукции, направленно сформировать режимы обработки, обеспечивающие устранение неблагоприятных проявлений технологической наследственности на начальных этапах производства.
Наибольшее развитие учение о технологической наследственности получило в машиностроении, наиболее значимые закономерности которой изложены в работах П.И. Ящерицына. A.M. Дальского Г.Д. Деля, В.И., Авер- ченкова, Э.В. Рыжова, JI.A. Хворостухина и других авторов [45-47, 95,96]. Носителями наследственной информации являются показатели качества изделий. Они активно участвуют в технологическом процессе проходя, по выражению академика П.И.Ящерицына, через различные “барьеры”, либо задерживаясь на них частично или полностью [45]. Операции технологического процесса могут ликвидировать некоторые свойства объектов и создавать новые. Наследование свойств в ходе технологического процесса свойственно как для детерминированных, так и для вероятностных систем. Первый случай характерен для уже разработанных и требующих совершенствования процессов, где не возникает никакой неопределенности в. передаче свойств. Если известны предыдущее состояние системы-и способ переработки информации, то можно предсказать ее последующее состояние. Для разработанных детерминированных технологических процессов закономерности технологического наследования могут быть установлены на основе экспериментальных исследований и обработки статистической информации, направленных на установление причинно-следственной-связи между значениями технологических факторов и показателями качества изделия. Для описания трансформации свойств предмета труда с учетом явлений технологической наследственности разработан эффективный математический аппарат, позволяющий прогнозировать качество изделий. Множество значений показателей качества изделия после выполнения j-ой операции его производства имеет вид [45]:
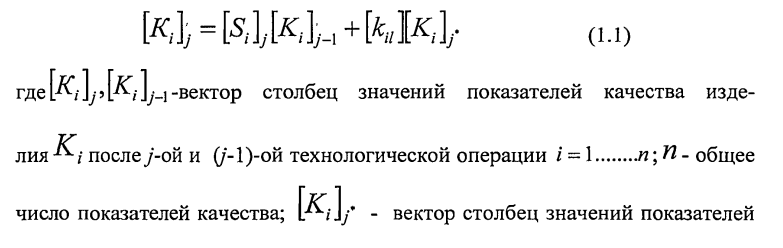
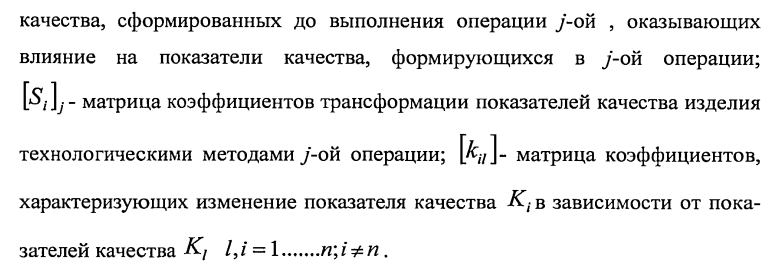
На основе результатов этих исследований в настоящее время, накоплен значительный массив коэффициентов трансформации показателей качества изделий машиностроения, позволяющий реализовывать технологии управления эксплуатационными свойствами высокоточных деталей, в первую очередь, на начальной стадии их изготовления в процессах резания. Результаты исследований дают возможность проанализировать влияние технологической наследственности на параметры поверхностного слоя (шероховатость поверхности, точность размеров деталей, полей допусков) [48,90,91].
Применительно к технологии получения пружинных клемм, наряду с решением этих задач, в большей степени имеют место задачи связанные с прогнозированием формирования показателей качества металла в технологических процессах, реализующих методы различной физической природы. Для эффективного использования указанного математического аппарата необходимо установить закономерности и диапазоны изменения значений коэффициентов трансформации механических свойств стали 40С2 в блоке подготовительных операций, сформировать на этой основе систему технологических ограничений, получить исходные данные для проектирования результативных режимов подготовки, металла формообразованию, устраняющих неблагоприятные наследственные связи на операциях холодной гибки.
Осуществление качественных процессов термообработки на этапах подготовки металла к формообразованию и окончательной термообработки возможно только при условии надежного представления об особенностях и основных характеристиках обрабатываемой стали. Особенно большое значение имеют сведения о температурных границах фазовых превращений, характеризуемых положением критических точек А] и А3. Сталь 40С2 не входит в перечень стандартных материалов, используемых в производстве упругих элементов деталей машин. Сведений об этой стали в литературе представлено недостаточно. Одним из немногочисленных источников, содержащим информацию о температурах фазовых равновесий и особенностях поведения переохлажденного аустенита в стали 40С2, явилась работа [55]. Однако эти данные были получены в 50-60 годах прошлого века и сегодня нуждаются в проверке и уточнении в связи со значительным изменением технологии получения стали 40С2 на современных металлургических предприятиях.
Также необходимо выполнить оценку точности исполнения геометрических размеров промежуточного профиля «омега» в процессе- холодной гибки круглой заготовки в зависимости от уровня механических свойств стали, подготовленной для формообразования. Пластический изгиб полосы с учетом этих вопросов исследовали Н.И. Безухов [50], А.А.Ильюшин [51], H.H. Малинин [52], А. Надаи [53], Р. Хилл [54], М.В.Сторожев, Е.А. Попов [92]. Однако данные работы относятся к пластическому изгибу заготовки в форме полосы прямоугольного сечения или листовой заготовки и требуют дополнительной адаптации применительно к процессу гибки заготовки круглого сечения.
С целью удовлетворения этих требований необходимо провести исследования процессов формирования качества стали 40С2 в блоке подготовительных операций и разработать усовершенствованные режимы подготовки металла к формообразованию, устраняющие проявления- неблагоприятной технологической наследственности и обеспечивающие на последующих операциях достижение геометрических размеров, промежуточных заготовок и пространственного контура клемм требуемого качества. Окончательные свойства отформованная клемма приобретает в процессе выполнения операций закалки и отпуска. Учитывая ограниченность сведений о данной стали, обеспечить заданный уровень качества клемм на этой стадии возможно только получив достоверные знания о характере формирования ее механических свойств в зависимости от температурно-временных режимов термического упрочнения. В этом направлении необходимо определить рациональные диапазоны закалочных температур и температурно- временные параметры отпуска. Рациональный режим закалки обеспечит достижение максимального уровня твердости стали и необходимую микроструктуру и механические свойства стали при последующем отпуске.
Рациональный режим отпуска обеспечивает условия для достаточно полного распада остаточного аустенита и образования большого количества дисперсных частиц карбидов. Эти частицы не только закрепляют дислокации, но и сами непосредственно увеличивают сопротивление малым пластическим деформациям. При этом сталь обладает наибольшей усталостной прочностью и релаксационной стойкостью. Во избежание нежелательных изменений в структуре (коагуляция* карбидов) режим отпуска должен быть регламентирован по температуре и времени на достижение заданного уровня твердости клемм. Для большинства стандартных кремнистых сталей, выпускаемых по ГОСТ 14959-79, в литературе [3,8] приводятся зависимости изменения механических свойств от температуры и продолжительности отпуска. Для нестандартной стали 40С2 такие данные в литературе не встречаются. В работе [80] приведены результаты исследований поведения закаленной стали 40С2 в процессе индукционного отпуска. Однако эти данные получены на образцах профилированной в холодном состоянии арматуры периодического профиля и не могут быть напрямую использованы в технологии производства пружинных клемм.
Для обеспечения новых требований нормативно-технической документации по уровню пружинящих свойств необходимы исследования по оценке взаимосвязи механических свойств термически упрочненной стали 40С2 с величиной остаточной деформации петли клеммы после контрольных испытаний, так как этот вопрос ранее не исследовался и в литературе не описан.
Таким образом, в- блоке окончательной термообработки и контроля требуются комплексные исследования динамики формирования прочностных и пластических свойств стали 40С2 при термическом упрочнении с оценкой их взаимосвязи с уровнем пружинящих свойств изделия. Результатом исследований должны стать математические модели, описывающие причинно-следственные связи между технологическими факторами и показателями механических свойств отформованных клемм при окончательной- термообработке. Это позволит прогнозировать механические свойства клемм по состоянию технологических режимов, а изменением значений технологических факторов влиять на показатели качества, и в конечном счете разработать усовершенствованные режимы окончательной термообработки отформованных клемм, обеспечивающие достижение заданного уровня качества готовой продукции.
Изучив процессы формирования качества в технологических блоках подготовки металла к формообразованию и окончательной термообработки и контроля, на основе установленных закономерностей, необходимо разработать методику управления качеством пружинных клемм, позволяющую определять результативные технологические режимы, предупреждающие и корректирующие воздействия по обеспечению заданного уровня качества готовой продукции.
Цель и задачи исследования
Целью работы является обеспечение заданного уровня качества железнодорожных пружинных клемм ОП105 совершенствованием технологических режимов обработки.
Для достижения поставленной цели в работе необходимо решить следующие задачи:
– Выполнить анализ причин возникновения неблагоприятных наследственных связей, инициирующих несоответствия по геометрическим размерам и механическим свойствам клемм и разработать меры, направленные на их устранение;
- Выполнить исследования процессов формирования качества металла в блоке подготовительных операций и разработать усовершенствованные режимы подготовки металла к формообразованию, устраняющие проявления неблагоприятной технологической наследственности на последующих операциях гибки и обеспечивающие достижение требуемых геометрических размеров промежуточных заготовок и пространственного контура клемм; -Провести комплексные исследования динамики формирования прочностных и пластических свойств стали 40С2 при термическом упрочнении и разработать усовершенствованные режимы окончательной термообработки, обеспечивающие достижение заданного уровня твердости и пружинящих свойств отформованных пружинных клемм;
- Разработать методику управления качеством железнодорожных пружинных клемм, позволяющую определять результативные технологические режимы, предупреждающие и корректирующие воздействия по обеспечению заданного уровня качества готовой продукции при взаимодействии технологических методов различной физической природы между процессами подготовительных операций, формообразования и окончательной термообработки;
- Внедрить результаты исследований в промышленное производство и выполнить оценку уровня качества железнодорожных пружинных клемм.
- Шарапов С.Н. Разработка и внедрение рельсовых скреплений// Железнодорожный транспорт.- 1997.- № 7.- С.47-51
- Термическая обработка в машиностроении: Справочник (под ред. Ю.М. Лахтина, А.Г. Рахштадта).- М.: Машиностроение,- 1980.- 467С.
З.Рахштадт А.Г. Пружинные стали и сплавы,- М.: Металлургия.- 1982,- 400С. - Федоров Н.Я. Универсально-гибочные автоматы.- М.:Машгиз.- 1961,- 237С.
- Кривощапов В.В., Вершигора С.М., Мезин И.Ю., Чукин В.В. Разработка и совершенствование технологии производства пружинных клемм // Производство проката.- 2000.- №7.- С. 21-24.
- Е.В. Карпов, В.В. Чукин, И.Ю. Мезин Обеспечение качества подготовки металла в сквозной технологии производства упругих элементов рельсовых скреплений//Фазовые и структурные превращения в сталях: Сб.науч.тр.,вып.З / под ред.В.Н. Урцева-Магнитогорск, 2003.-С.510-515.
- Рудаков В.П., Пестряков А.П. Связь качества штампованных изделий с состоянием исходного металлопроката // Производство проката.- 2003.- №7.-С23-25.
- Зубов В.Я. Структура и свойства стальной пружинной ленты. – М.: Металлургия.- 1964.-224С.
- Гриднев В.Н. Современные представления о влиянии пластической деформации на структуру и свойства стали.- Киев: Техника.- 1964.- 120С.
- Ю.Гаврилюк В.Г., Мешков Ю.Я. Прочность и пластичность холоднодеформированной стали.- Киев: Наукова думка.- 1974.- 232С.
- П.Раузин Я.Р. Термическая обработка хромистой стали.- М.: Машиностроение.-1978.- 325С.
- Высокопрочная арматурная сталь / Кугушин А.А., Узлов И.Г., Калмыков В.В., Мадатян С.А., Ивченко А.В. М.: Металлургия.- 1986.- 272G.
- Лахтин Ю.М. Металловедение и термическая обработка металлов.- М.: Металлургия.- 1979.-320С.
- Бараз Р.В., Зубов В.Я. Стабильность структуры и релаксация напряжений в цилиндрических пружинах// Известия вузов- №2.- 1970.-С. 34-38.
- 15.Федин В. М., Борц А. И., Кузнецов В. В. Технология производства упругих клемм рельсовых скреплений ЖБР-65: пути совершенствования//Вестник ВНИИЖТ.- 2005.- №5.- С.5-8.
- Патент СССР №1482536, МКИ Е01В9/48 Устройство для крепления рельса. Фирма Vossloh. Опубл. 23.05.89.Бюл.№19.
- А.С. 1210666 СССР, МКИ Е01В9/48 Клемма рельсового скрепления. Фирма Pendrol Limited(GB). Опубл. 07.02.86 .Бюл. №5.
- Айсенманн И. Совершенствование верхнего строения железнодорожного пути //Железные дороги мира.- 1997,- №2.-С. 61-65.
- Корчунов А.Г Чукин В.В., Слабожанкин Е.А. и др. Влияние поверхностной механической обработки на структуру и свойства калиброванного металла // Труды пятого конгресса прокатчиков. М.: Черметинформация, 2004.-С. 410-412.
- Сторожев М.В. Попов Е.А. Теория обработки металлов давлением. М. Машиностроение, 1971, С.324.
- Тавер Е. Объект управления при управлении качеством // Стандарты и качество.-2001.-№ 2.-С. 15-19.