Сейчас ваша корзина пуста!
Совершенствование технологических режимов подготовки металла к формообразованию и окончательной термообработки клемм
Цикл статей:
Глава 1 – Повышение качества железнодорожных пружинных клемм на основе совершенствования режимов обработки
Технические и технологические мероприятия по совершенствованию режимов подготовки металла к формообразованию и окончательной термообработки
Выполненные исследования позволили определить комплекс мероприятий, направленных на обеспечение заданного уровня геометрических показателей качества и твердости готовых пружинных клемм ОПЮ5 в условиях ОАО «ММК-МЕТИЗ». Разработанные мероприятия основаны на технических и технологических методах управления качеством продукции, позволяющих повысить эффективность взаимодействия между технологическими блоками производства пружинных железнодорожных клемм (рис.5.1), направленно формировать необходимые технологические режимы, обеспечивающие стабильное достижение заданного уровня качества готовой продукции.
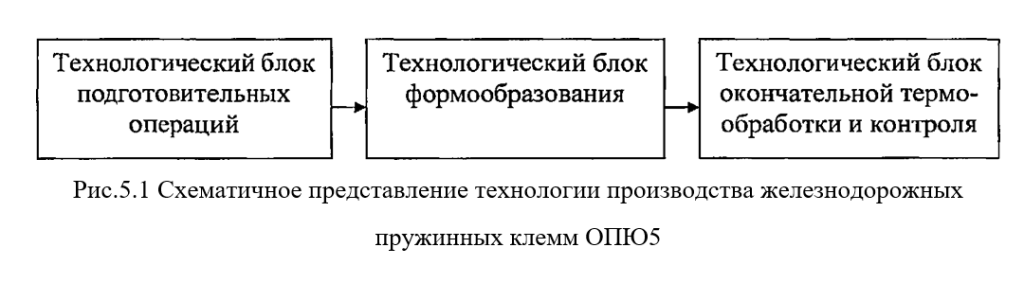
В технологическом блоке подготовительных операций процессы термообработки исходного подката и калиброванной (обточенной) стали предлагается выполнять по усовершенствованным режимам на печи непрерывного действия (роликовой проходной печи) в защитной атмосфере, взамен отжига в садочных печах СКБ 6001. Это позволит повысить показатели качества металла в части однородности микроструктуры, снизить разброс механических свойств стали по длине бунта и устранить связанные с этим неблагоприятные проявления: технологической наследственности в последующих технологических блоках при формообразовании геометрических размеров клемм. При этом сокращается длительность и повышается производительность процессов термической обработки, снижаются энергетические затраты на их выполнение [66].
В технологическом блоке: окончательной термической обработки; и контроля^ усовершенствования касаются температурно- временных параметров обработки на основе установленных закономерностей формирования прочностных и пластических показателей: качества; нестандартной, стали 40G2 и их взаимосвязи: с уровнем пружинящих свойств [67]. Реализация режимов осуществляется на действующем- оборудовании и не требует дополнительных материальных затрат.
Полученные в работе закономерности теплового и деформационного воздействия на нестандартную кремнистую сталь 40С2 могут быть использованы в указанном сочетании технологических блоков или в-отдельности : при производстве других видов железнодорожных пружинных клемм, таких как ЖБР-65, АРС и других.
Разработка методики управления качеством клемм
Выполненный комплекс исследований позволил разработать, методику управления качеством^ пружинных клемм ОПЮ5 с: учетом характера взаимодействия между технологическими блоками, реализующими принципы обработки различной физической природы, на основе которой определены рациональные режимы подготовки металла к формообразованию и окончательной термической! обработки; обеспечивающие повышение уровня ¡ качества готовой продукции [68]. Исходной информацией на входе в методику служат показатели качества горячекатаного подката стали марки 40С2 диаметром 14,0 мм . Оцениваются геометрические показатели качества подката, качество поверхности, механические свойства (с учетом реальной вариации), микроструктура (рис.5.2).
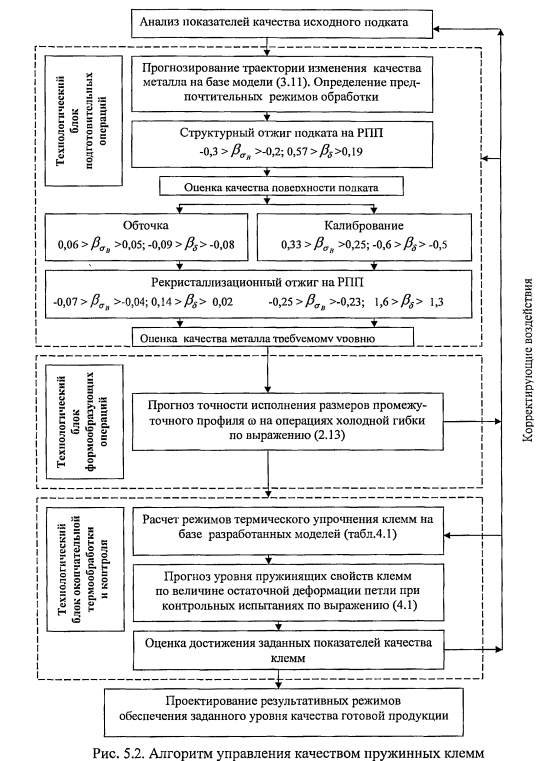
Прогноз трансформации показателей качества металла в блоке подготовительных операций и формирование необходимых технологических траекторий исполнения режимов подготовки металла к формообразованию осуществляют на базе разработанной математической модели (3:11). Выполненные исследования процессов формирования качества стали 40С2 в блоке подготовительных операций и полученные зависимости (3′. 1-3.5), описывающие пооперационную трансформацию контролируемых, показателей качества металла позволили сформировать систему технологических ограничений (табл.3.13) и определить на этой основе рациональные режимы обработки, устраняющие проявления неблагоприятной технологической наследственности и обеспечивающие требуемое качество металла.
В качестве технологического фильтра; выравнивающего механические свойства подката и обеспечивающего необходимую структуру, служит, операция структурного отжига на зернистый перлит, осуществляемая на печи непрерывного действия РПП в защитной атмосфере; Управляющими воздействиями: на показатели качества: стали служат температурно-временные параметры обработки.
В зависимости от качества; поверхности исходного подката (металлургические дефекты- поверхности, обезуглероженный! слой) организация» дальнейшего исполнения: технологических; операций в первом технологическом блоке может быть скомпонована по нескольким вариантам (рис.5.2). В случае наличия’ поверхностных дефектов металлургического происхождения и обезуглероженного слоя прокат подвергается обточке на диаметр 12,9 мм. Применение ■ обточки необходимо при: наличии на поверхности исходного подката дефектов, металлургического происхождения значительной5 глубины (0,2 -0,5 мм); При этом для реализуемого режима обточки с: 14,0 мм на 12,9 мм коэффициент расхода металла в стружку может достигать 6-7% [60]. Из этого объема в пересчете на 1 тонну металла возможно дополнительно произвести 107-117 клемм. При этом параметры упроченного поверхностного слоя в зависимости от технологических факторов резцовой обработки можно оценить по зависимостям описанных в работах [69].
При незначительной глубине залегания поверхностных дефектов и обезуглероженного слоя осуществляется подготовка поверхности стали к волочению и калибрование. Подготовка поверхности исходного подката для поверхностной механической обработки осуществляется по рекомендациям, широко описанным в специальной литературе [70,71]. Режим калибрования отожженного подката диаметром 14,0 мм на размер 12,9 мм назначается исходя из условий обеспечения благоприятного напряженного состояния и максимально возможной равномерности деформации по сечению профиля [59]. Для анализа режимов калибрования возможно использование современного программного обеспечения, например описанного в работе [72].
После чего, с учетом деформационной специфики поверхностной обработки (калибрования или обточки), определяются режимы ускоренного рекристаллизационного отжига. При этом могут быть задействованы, различные источники теплового воздействия. При обычном печном нагреве рекри- сталлизационный отжиг рекомендуется проводить в защитной атмосфере по ускоренным режимам, определяемым по зависимостям (3.2-3.5)
В то же время, когда деформация неравномерно распределена по объему обрабатываемой стали и длительность инкубационного периода образования центров рекристаллизации в различных сечениях металла заметно отличается, особенно эффективно может быть использован скоростной индукционный нагрев[73]. При этом достигается однородная структура стали с мелким зерном, что повышает ее пластические свойства[74].
Отжиг по ускоренным режимам с использованием тепла печного или индукционного нагрева позволит устранить зональный характер структурной неоднородности, возникающей ввиду различных условий деформации поверхностных и центральных слоев металла на предыдущих операциях механической обработки, и получить качественную с минимальной величиной обезуглероженного слоя и однородными механическими свойствами заготовку для осуществления последующих операций формообразования.
На основании исследований и оценки взаимосвязи показателей качества металла и особенностей исполнения операций холодного формообразования промежуточного профиля со по выражению 2.13, а также обобщения-результатов производства клемм на ОАО «ММК-МЕТИЗ», рекомендуются следующие значения показателей качества калиброванной (обточенной) стали после блока подготовительных операций
- содержание зернистого перлита в структуре металла не менее 60 %;
- временное сопротивление разрыву 600- 660 Н/мм .
Такие показатели качества в совокупности с однородной микроструктурой и-минимальным разбросом механических свойств по длине бунта обеспечивают стабильные геометрические показатели качества промежуточного профиля со и отштампованных клемм.
Таким образом, после блока подготовительных операций получают термообработанную заготовку с однородной» структурой и механическими свойствами полностью отвечающим-условиям последующих операций формоизменения и обеспечивающим стабильное и бесперебойное осуществление процессов холодной гибки промежуточной заготовки со и горячей штамповки конфигурации клеммы.
Последующие операции формоизменения предусматривают холодную пластическую деформацию обточенной прутковой заготовки путем изгиба при малых значениях относительных радиусов гибки. При этом наружные слои прутка получают значительную пластическую деформацию растяжения. В этих условиях, образовавшиеся-в-процессе резания. микронеровности, могут являться концентраторами напряжений и инициировать развитие дефектов поверхности, которые усугубляясь на стадии выполнения закалочных операций выявляются только при контрольных испытаниях или в процессе эксплуатации клемм.
В качестве мер ликвидирующих эту неблагоприятную «наследственность» и повышающих качество поверхности обточенной стали рекомендуется обработка продольной обкаткой с малыми пластическими деформациями [75,76]. Выполненные исследования [77] показали, что обкатка обточенной стали позволяет существенно повысить качество ее поверхности. Применительно к действующей на ОАО «ММК-МЕТИЗ» технологии производства пружинных клемм наиболее рациональным’ вариантом реализации этого способа является: совмещение операций обкатки и правки обточенной стали на вспомогательном оборудовании холодногибочного автомата.
При последующей реализации методики осуществляется расчет режимов финишной; обработки клемм в технологическом блоке окончательной термообработки и контроля на основе математических моделей изменения механических свойств стали 40С2 при термическом: упрочнении (табл. 4.1) и оценки их взаимосвязи с величиной: остаточной деформации: петли клемм (4.1). При этом также учитываются условия обеспечения поточности обработки и синхронизации; исполнения; операций закалки и последующего’ отпуска.
Режимы,окончательной термообработки рекомендуется ориентировать на получение твердости клемм 46-48 НЯС, которая обеспечивает после;кон- трольного испытания путем, обжатия петли клеммы усилием З0 кН минимальное значение величины остаточной деформации петли клеммы и требуемый уровень пружинящих свойств изделий. В этом; случае при сборке рельсового скрепления; и приложении монтажной нагрузки 20-25 кН материал клеммы будет работать только в> условиях упругой деформации, обеспечивая высокие эксплуатационные свойства рельсового скрепления в целом:
Важным; дополнительным фактором повышения, качества; пружинных клемм после выполнения термоупрочняющих и контрольных операций может стать финишная дробеструйная обработка. Такая обработка приводит к уничтожению упругих деформаций растяжения термического происхождения в поверхностных слоях клемм и формированию, в последних благоприятных сжимающих остаточных напряжений [78]. Это позволит повысить циклическую и коррозионную стойкость клемм, продлить срок их эксплуатации.
Необходимыми элементами методики являются ограничения, которые обеспечивают выполнение условий по стабильности формирования требуемого качества, пружинных клемм. В технологическом блоке подготовительных операций режимы обработки определяются с учетом следующих ограничений: неудовлетворительные механические свойства стали, повышенный разброс механических характеристик, несоответствие по микроструктуре, повышенная; овальность калиброванной стали. В технологическом блоке окончательной термической обработки: и контроля в роли ограничений; выступает несоответствие полученных механических свойств готовой продукции заданному уровню качества.
Для обеспечения соответствия между заданным и достигнутым по результатам контроля уровнем показателей качества готовой продукции методика. предусматривает корректирующие воздействиям на свойства; исходной заготовки, режимы ее обработки в блоке подготовительных операций окончательной термообработки и контроля. Результатом служат усовершенствованные режимы подготовки металла к формообразованию и финишной термической обработки, обеспечивающие стабильное формирование заданных значений геометрических показателей качества; и твердости пружинных клемм.
Реализация разработанных мероприятий в промышленности и оценка уровня качества продукции
Разработанный комплекс мероприятий, направленный на совершенствование режимов подготовки металла к формообразованию и окончательной термообработки клемм, реализован в условиях ОАО «ММК-МЕТИЗ».
В соответствии с методикой управления, качеством пружинных клемм выполнили оценку показателей качества горячекатаной стали. Исходный горячекатаный прокат стали 40С2 диаметром 14,0 мм производства ОАО «Мечел» по предельным отклонениям соответствовал обычной точности прокатки В по ГОСТ 2590. Содержание основных легирующих элементов углерода и кремния в перерабатываемой стали по данным входного контроля составляло, соответственно, 0,41-0,42 % и 1,6-1,7 %. Микроструктура стали феррит + пластинчатый перлит 1-2 балла. Качество поверхности соответствовало группе 2ГП по ГОСТ 1050. Глубина обезуглероженного слоя составляла 0,09 мм. Для анализа вариаций прочностных и пластических показателей качества от 26 бунтов исходного подката отбирались образцы длиной 300 мм для проведения механических испытаний. Механические испытания проводились в сертифицированной ЦЗЛ ОАО «ММК-МЕТИЗ» по ГОСТ 1497-84 на универсальной разрывной гидравлической машине ЕИ-100. Обработку полученных данных проводили методами математической, статистики. В таблице 5.1 приведены результаты испытаний.
Для получения необходимой микроструктуры, механических свойств и качества поверхности стали исходный подкат в блоке подготовительных операций обрабатывали в следующей последовательности: подкат – структурный отжиг – поверхностная механическая обработка – рекристаллизационный отжиг. С учетом рекомендуемых коэффициентов оперативного наследования свойств (табл. 3.13) по модели (3.11) рассчитали характер трансформации показателей качества металла и определили рациональные режимы его-подготовки к операциям формообразования.
Для формирования структуры зернистого перлита подкат отжигали на печи непрерывного действия Pill 1-2 в защитной атмосфере в условиях калибровочного цеха по разработанному в ходе исследований режиму: I зона – 760±10 ; II зона- 780 ±10 ; III зона 720±10 ; IV зона – 700±ш °С время пребывания металла в камере нагрева: 380 мин [79]. Общее время термообработки с учетом прохождения камеры охлаждения составляло 540 мин.
С целью удаления с поверхности отожженного подката дефектов металлургического происхождения осуществляли механическую обработку – резцовую обточку. Подготовка поверхности стали перед обточкой производилась в соответствии с действующими на предприятии технологическими инструкциями:
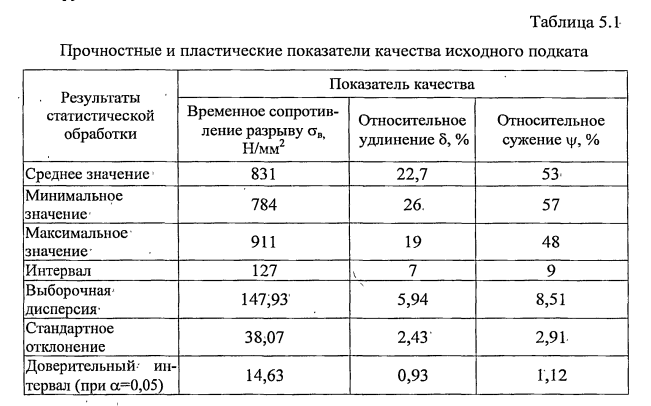
Обточку осуществляли на стане «Кизерлинг» вращающимися резцами- с режущими кромками, находящимися на головке. Перед прохождением через режущую головку подкат подвергали правке в роликоправильной секции стана. Режущая головка состояла, из четырех резцедержателей, в которые вставлялись твердосплавные режущие пластины трехгранной формы. Режим обточки указан в табл.5.2. При обточке стали использовали охлаждающую жидкость, приготовленную на основеэмульсола «Ровел-Уверол».
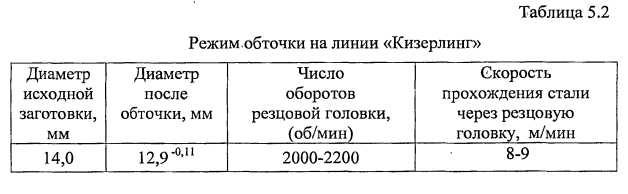
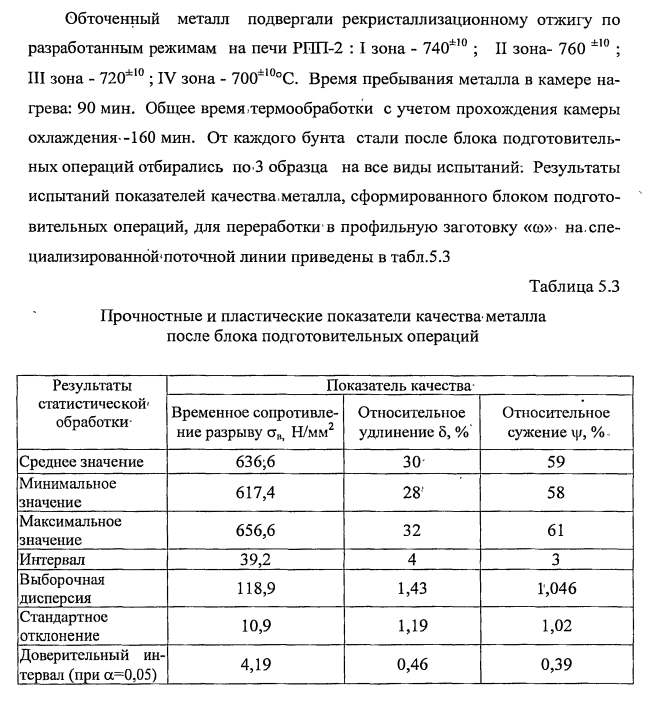
Анализ микроструктуры металла после блока подготовительных операций показал, что доля зернистого перлита в структуре стали-составляла не менее 60 %, размер зерна цементита соответствовал, 6-7 баллам, глубина обезуглероженного слоя была в пределах от 0,01-0,02 мм Прирост глубины обезуглероженного слоя на поверхности обточенной стали вызван спецификой состава применяемых на заводе защитных атмосфер.
Из табл.5.3 видно, что диапазон разброса механических свойств исходного подката после переработки в блоке подготовительных операций заметно сузился (рис.5.3). По сравнению с ранее действующими режимами термообработки в колпаковых печах интервалы разброса показателей качества металла снизились по временному сопротивлению разрыву в 3,07 раза, по относительному удлинению в 2,76 раза, по относительному сужению в 2,33 раза.
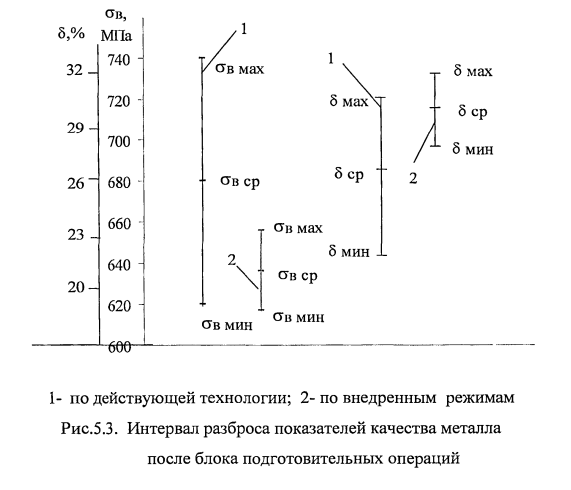
Это предопределило однородность условий последующей холодной пластической деформации промежуточного профиля заготовки клеммы со и точность исполнения ее размеров на холодногибочном автомате «ЦВН-600». После операции гибки в разное время было отобрано 100 промежуточных заготовок омега (рис. 2.6) и выполнены измерения геометрических показателей качества (табл. 5.4).
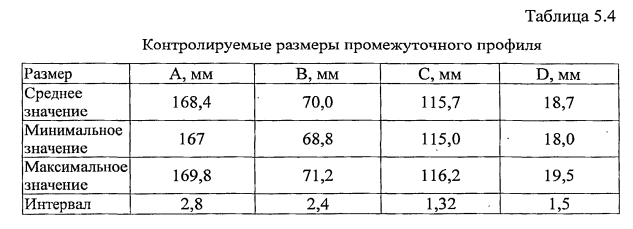
В результате установлено, что при переработке стали, полученной по разработанным режимам, вариации изменения контролируемых размеров профиля по сравнению с ранее действующей технологией были снижены в среднем более чем 2,5 раза (рис.5.4).
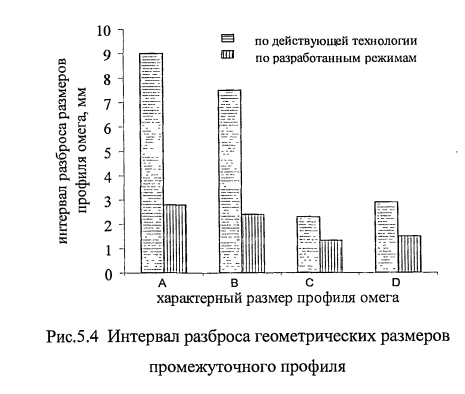
При этом указанные в табл.5.4 интервалы достаточно узкие, что предопределяет точное и одинаковое базирование заготовки перед горячей штамповкой и получение требуемых геометрических показателей качества готовых клемм.
После получения- промежуточного профиля омега пространственный контур готового изделия формировали на операции горячей гибки- штамповки. Температура нагрева под горячую обработку на протяжении всего контрольного периода времени составляла 920-940 °С. Данная температура удовлетворяет условиям пластической деформации профильных заготовок при формировании окончательной геометрии готовых изделий. Кратковременный нагрев заготовок ТВЧ под горячую штамповку до температуры 920940 °С, как показали опытные данные не приводит к увеличению обезуглероживания поверхности стали.
Для обеспечения’ заданного уровня качества клемм, окончательно отформованные методом горячей штамповки изделия подвергали термической обработке – закалке с последующим отпуском. Согласно методике управления качеством пружинных клемм по статистическим моделям (табл.4.1) на основе прогноза достижения требуемых показателей качества термоупрочненной стали 40С2 и пружинных свойств готового изделия- были определены- режимы окончательной термообработки. Термическая обработка проводилась на конвейерном закалочно-отпускном агрегате и соответствовала условиям поточного производства: На протяжении всего цикла контрольных мероприятий в процессе термической обработки температура нагрева под закалку составляла 910-920°С, а температура отпуска- 400-410°С. Настройку агрегата выполнили с целью обеспечения продолжительности пребывания клемм в закалочной печи в процессе нагрева 30-35 мин- и продолжительность выдержки в отпускной печи 30-35 мин. В” качестве охлаждающей среды при закалке использовалась вода, температура которой не превышала 40°С. После проведения-операций термоупрочнения 100% клемм подвергались испытаниям на пружинящие свойства путем обжатия петли клеммы усилием ЗОкН на стенде специальной конструкции. После проведения контрольного обжатия измерялись все необходимые показатели качества готовых изделий. Проверку геометрических показателей качества клемм после обжатия проводили с использованием предельных контрольных шаблонов в
соответствии с ЦПТ 82/23 «Методика проведения контроля размеров прутковой пружинной клеммы ОПЮ5», согласованных с ОАО «РЖД».
Твердость и структуру материала отпущенных клемм определяли на темплетах вырезанных из центральной части изделия после проведения контрольных испытаний на пружинящие свойства. Анализ микроструктуры стали показал, что разработанные режимы термической обработки в контролируемый период производства обеспечили формирование в закаленных изделиях структуры мартенсита 3-6 баллов, а в изделиях подвергнутых отпуску – структуры троостита отпуска. В процессе окончательной термической обработки был зафиксирован прирост глубины обезуглероженного слоя до 0,1 мм, что удовлетворяет требованиям нормативно-технической документации.
Численные значения показателя качества «Твердость» находятся ближе к верхней границе допускаемого интервала и большей частью изменяются в пределах 46-48 HRC, что обеспечивает минимальную остаточную деформацию-при контрольном, испытании и выполнение требований по «пружинящим свойствам клемм (таблица 5.5).
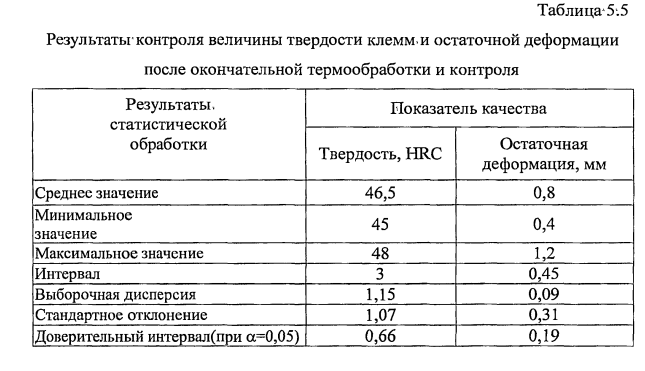
Из анализа результатов промышленной апробации режимов окончательной термической обработки установлено, что расхождение между предсказываемыми математическими моделями (табл.4.1) и фактическим уровнем показателя качества «Твердость» не превышает 7 %.
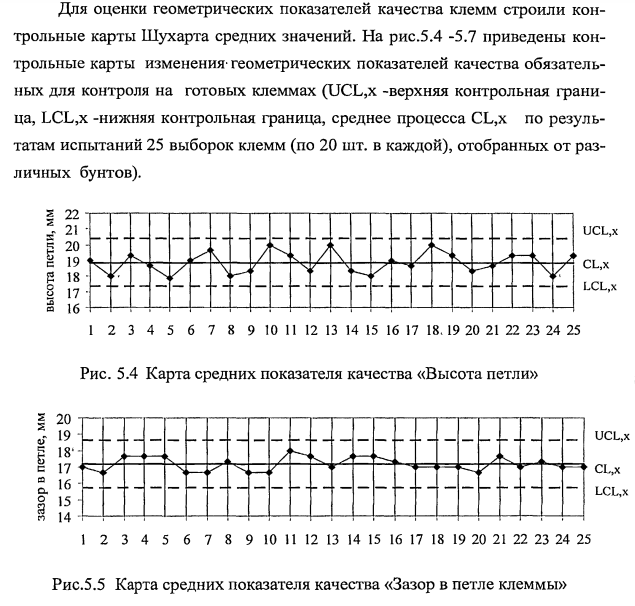
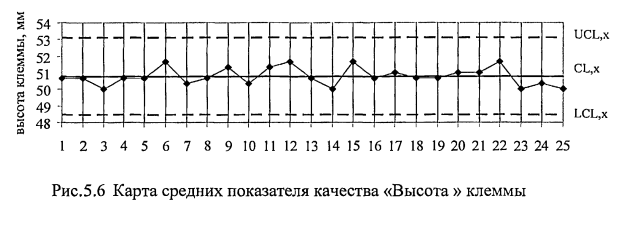
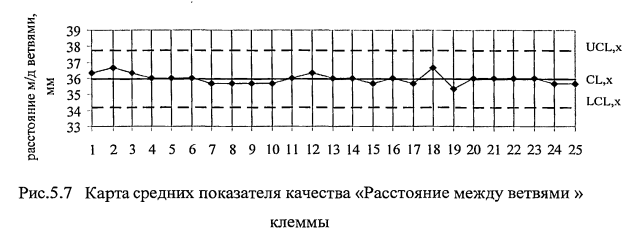
Анализ контрольных карт Шухарта для геометрических показателей качества клемм показывает, что подавляющее количество их значений укладывается в заданный нормативно-технической документацией интервал.
Анализ диаграмм Парето, построенных после совершенствования технологических режимов подготовки металла к формообразованию и окончательной термической обработки, показал, что в сравнении с исходной технологией в общей структуре несоответствующей продукции дефектность по геометрическим показателям качества была снижена на 93 %, а несоответствия по твердости готовым клемм были полностью устранены (рис.5.8).
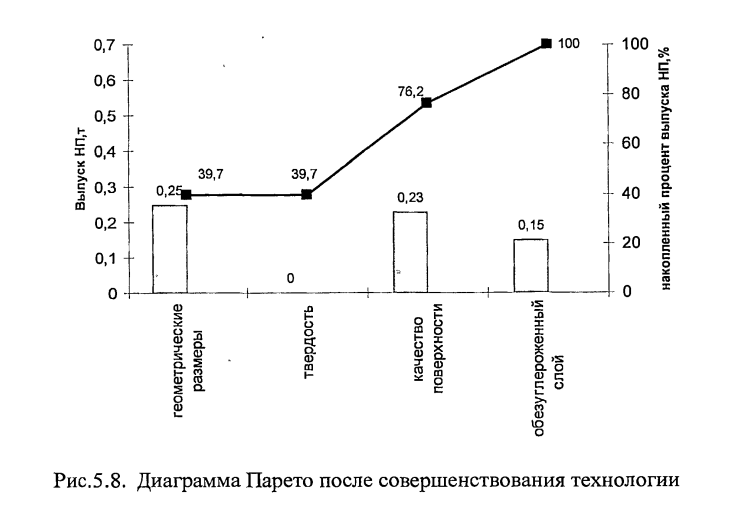
Таким образом, на основании анализа промышленной апробации производства железнодорожных клемм на ОАО «ММК-МЕТИЗ» можно заключить, что полученные в ходе исследований разработки, позволили усовершенствовать технологию и значительно повысить уровень качества готовой продукции.
По результатам исследований разработаны и внесены изменения в технологическую инструкцию ТИ 176-Т-241-2002 «Производство проката для изготовления, пружинных клемм». Подтвержденный экономический эффект от совершенствования процессов обработки стали в блоке подготовительных операций составил 992,7 руб на 1 тонну товарной продукции.
Были разработаны и внесены в технологическую карту ТК 176-МТ.КР- 390-2006 «Клемма пружинная прутковая для крепления рельсов по ОП 105 ТУ» результативные режимы окончательной термической обработки клемм на агрегате СКЗА, без снижения производительности, поточной линии.
Согласно требованиям нормативно-технической документации, при изменении технологии производства необходимо проводить испытания клемм на соответствие показателей качества требуемому уровню значений по методике, утвержденной Департаментом пути и сооружений. Для проведения испытаний от промышленной партии пружинных клемм ОПЮ5 были отобраны 10 образцов готовой продукции и переданы в исследовательскую лабораторию Всероссийского научно-исследовательского института железнодорожного транспорта (ВНИИЖТ г. Москва). По заключению института пружинные клеммы ОПЮ5 производства ОАО «ММК-МЕТИЗ» по всем показателям качества полностью соответствовали требованиям отраслевых стандартов и были рекомендованы для эксплуатации на отечественных железных дорогах.
Выводы по главе
- Предложен комплекс технических и технологических мероприятий направленный на усовершенствование технологических режимов подготовки металла к формообразованию профиля клемм ОПЮ5 и окончательной термической обработки, позволяющий повысить качество готовой продукции по геометрическим размерам и механическим свойствам.
- Разработана методика управления качеством железнодорожных пружинных клемм, отличающаяся учетом наследственных связей при взаимодействии технологических методов различной физической природы между процессами подготовительных операций, формообразования, окончательной термообработки и контроля при формировании потребительских свойств готовой продукции. Использование методики позволяет направленно формировать технологические режимы подготовки металла к формообразованию и окончательной термической обработки, обеспечивающие достижение заданного уровня качества клемм ОПЮ5.
- Разработанные усовершенствованные режимы подготовки металла к формообразованию профиля клемм и окончательной термообработки внедрены в промышленное производство в условиях ОАО «ММК-МЕТИЗ». В результате в общей структуре несоответствующей продукции на 93 % была снижена дефектность по геометрическим размерам и полностью устранены несоответствия по твердости клемм, что свидетельствует о значительном повышении качества готовой продукции. Экономический эффект от внедрения разработок в производство составил 992,7 руб на 1 тонну товарной продукции. Полученные по разработанным режимам клеммы успешно прошли сертификационные испытания во ВНИИЖТ (г. Москва).
Заключение
- Выполнен анализ процесса производства пружинных клемм ОПЮ5 с позиций теории технологической наследственности во взаимосвязи технологических блоков подготовительных операций, формообразования и окончательной термообработки и контроля, на основе которого определены основные направления исследований по совершенствованию процессов формирования качества готовой продукции, а именно режимов подготовки металла к формообразованию профиля клемм и их окончательной термической обработки.
- Разработана инженерная формула для прогноза упругого пружинения и оценки точности исполнения промежуточного профиля клеммы «омега» при холодной гибке из круглой прутковой заготовки в зависимости от прочностных показателей качества металла. Анализ расчетных данных подтвердил, что в формировании геометрических размеров профиля клемм основную роль играет стабильность механических свойства металла, получаемого в блоке подготовительных операций. Расчеты по полученному выражению также позволили определить рациональный диапазон прочностных свойств металла, обеспечивающий требуемую точность исполнения промежуточного профиля омега.
- Разработана математическая модель трансформации показателей качества стали 40С2 на этапе подготовительных операций к формообразованию с учетом технологического наследования свойств. На основе модели с учетом специфики исполнения последующих операций формоизменения разработаны режимы подготовки металла к формообразованию, устраняющие проявления неблагоприятной технологической наследственности и обеспечивающие формирование геометрических размеров промежуточных заготовок и пространственного контура клемм требуемого качества.
- Получены новые сведения о термическом воздействии на кремнистую пружинную сталь 40С2 в процессах термического упрочнения с использованием тепла печного нагрева. Разработаны математические модели оценки изменения прочностных и пластических показателей качества стали в зависимости от температурно-временных факторов термического упрочнения. Установлена взаимосвязь уровня твердости термически упрочненных пружинных клемм
- ОПЮ5 с величиной остаточной деформации петли изделия при нагружении регламентированным нормативно-технической документацией усилием. Выявленные закономерности динамики трансформации показателей качества стали при термическом упрочнении и характер поведения клемм при контрольном нагружении послужили основой для определения результативных управляющих воздействий на процессы формирования качества готовой продукции в блоке окончательной термообработки и контроля.
- Разработана методика управления качеством пружинных клемм с учетом характера взаимодействия между технологическими блоками подготовительных операций, формообразования, окончательной термообработки и контроля, на основе которой определены усовершенствованные режимы обработки, обеспечивающие формирование заданного уровня качества геометрических показателей клемм и их механических свойств
- Результаты исследований внедрены в действующее производство в виде изменений в технологическую инструкцию ТИ 176-Т-241-2002 «Производство проката для изготовления пружинных клемм» и технологическую карту ТК 176-МТ.КР-З90-2006 «Клемма пружинная прутковая для крепления рельсов по ОПЮ5 ТУ». В итоге в общей структуре несоответствующей продукции на 93 % была снижена дефектность по геометрическим размерам и полностью устранены несоответствия по твердости клемм, что свидетельствует о значительном повышении качества готовой продукции по сравнению с исходной технологией. Подтвержденный экономический эффект от внедрения результатов работы в условиях ОАО «ММК-МЕТИЗ» составил 992,7 руб на 1 тонну товарной продукции.
- Результаты работы использованы при успешном прохождении сертификации клемм ОПЮ5 производства ОАО «ММК-МЕТИЗ» во ВНИИЖТ (г. Москва)
- Полученные в работе теоретические и практические результаты используются в учебном процессе ГОУ ВПО «МГТУ» при подготовке инженеров по специальности 200503 – «Стандартизация и сертификация» (металлургия), 150106 – «Обработка металлов давлением»
Список литературы
- Горелик С.С. Рекристаллизация металлов и сплавов.- М:: Металлургия.- 1978.- 567С.
- Малов А.Н. Технология холодной штамповки.- М.: Машиностроение.- 1969. – 568 С.
- Головин В.А. Технология и оборудование холодной штамповки.- М.: Машиностроение. 1987.- 352 С.
- Кривощапов М.В. Разработка, исследование и совершенствование оборудо¬вания и технологии изготовления рельсовых скреплений нового поколения /Дис. на соискание учен. степ, к.т.н. – Магнитогорск,-1999, 211С.
- Сивак Б.А., Протасов А.В..Применений модульных технологий в металлургии //Черные металлы.- 2000.- № 10.- С.13-16
- Ратников В.Ф., Салганик В.М., Шемшурова Н.Г. Квалиметрия и управление качеством продукции.- Учебное пособие. -Магнитогорск: МГТУ.- 2000.-184С.
- Кривощапов В.В. Технология производства, пружинных клемм.-: Магнито¬горском ДП.-1999.-176С.
- Е.В., Гун Г.С., Чукин В.В; Разработка методики и оборудования приемо-сдаточных испытаний железнодорожных пружинных клемм //Обработка сплошных и слоистых материалов: Межвуз. междунар. сб. науч.тр.- Магнитогорск: МГТУ, 2003.-С. 198-202.
- Касьянов С.В. Прослеживание процесса создания продукции как основа улучшения качества//Методы менеджмента качества;- 2007.- № 8.-.С.38-43.
- Розенберг A.M. Качество поверхности, обработанной деформирующим протягиванием.- Киев : Наукова думка.- 1977.- 187 С.
- Сторожев М:В;, Попов Е;А. Теория обработки металлов давлением. – М.: Машиностроение.- 1971.- 424С.
- Лапидус В.А. Всеобщее управление качеством (TQM) в российских компаниях — М.: Новости в российских компаниях . — 2000. – 432С.
- Корчунов А.Г., Чукин В.В. Одинаева В.М. Сравнительная характеристика формирования: качества пружинных клемм в технологиях холодной; и горячей пластической деформации// Известия ТулГу. Серия. Механика деформируемого твердого телами обработка металлов давлением.-Тула:; ТулГУ, Вып.2, 2006.- С. 48-55.
- Суслов А.Г. Научные основы технологии машиностроения.- М.: Машиностроение,- 2002.- 684С.
- Зайдес С.А., Исаев А.Н. Технологическая механика осесимметричного дет формирования.-Иркутск: Изд-во ИрГТУ,- 2007.-432С.