Сейчас ваша корзина пуста!
Моделирование напряженного состояния при волочении заготовки н^ размер под профилирование
Цикл статей:
Глава 1 – Повышение качества и конкурентоспособности высокопрочной арматуры диаметром 10,0 мм для железобетонных шпал на основе разработки рациональных режимов холодной деформации и термической обработки
Глава 2 – Моделирование напряженного состояния при волочении заготовки н^ размер под профилирование
Определение диаметра заготовки под профилирование
При нанесении периодического профиля на поверхность круглой заготовки необходимо обеспечить получение арматуры требуемого номинального диаметра с заданным уровнем сцепления и минимальной массой погонного метра. Выполнение этих требований зависит от соотношений между параметрами периодического профиля и размера заготовки под профилирование. В табл. 2.1 приведены требования к геометрическим показателям качества периодического профиля (рис.2.1) для армирования железобетонных шпал по ТУ 14-125-704-96. Для определение диаметра заготовки под профилирование воспользовались универсальной методикой и инженерной формулой, полученной в работе [60].
0 V о г н н ,
k-Sr-sm.fi
где ¿г ^ ^ – критерий Рема, характеризующий сцепление арма-
туры с бетоном вне зависимости от вида периодического профиля;
– площадь проекции выступа конкретной конфигурации на плоскость, перпендикулярную продольной оси арматурного стержня (рис.2.2 ), мм2; /3 – угол наклона выступа к продольной оси стержня, град; X – шаг периодических выступов на поверхности стержня, мм; к- число выступов на периметре стержня; ТУ1 – масса арматурного профиля, г; I – длина арматурного профиля, мм;
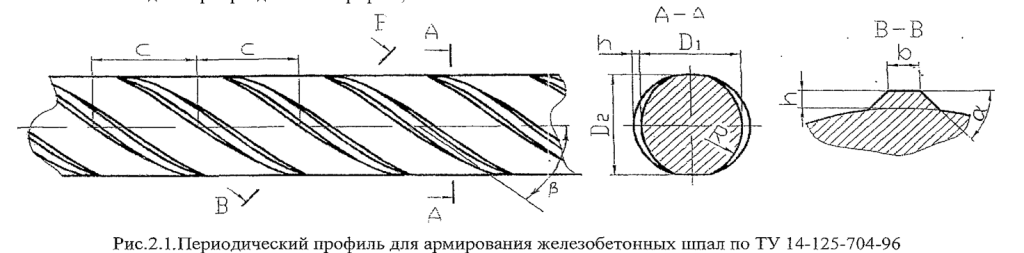
Номинальный диаметр, мм | Площадь сечения, мм2 | Линейная плотность г/м | Общие размеры профиля | Размеры, угол наклона анкерующих выступов | |||||
01, мм | Р2, мм | К, мм | Ь, мм | в, мм | с, мм | Р,град | |||
10 | 77,75+5% | 610±5% | +0,3 9,3 -0,2 | +0,3 10,2 -0,2 | 5,8 | 0,6+0,1 | 1,0 | ю., | 30 |
(73,8-81,6) | (580-640) | (9,0-9,5) | (9,9-10,4) | (0,5-0,7) | (9-10) |
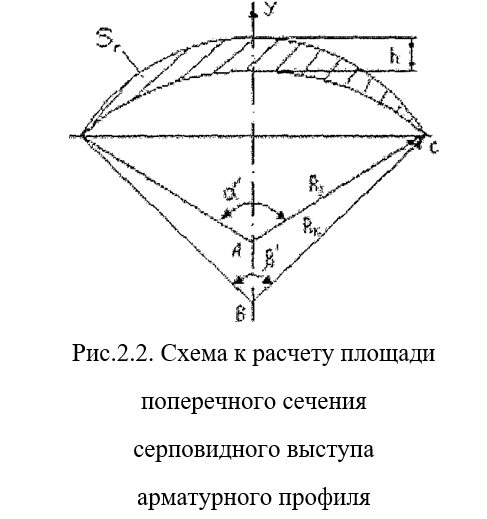
Площадь проекции серповидного выступа арматурного профиля на плоскость, перпендикулярную продольной оси арматурного стержня определится из выражения:
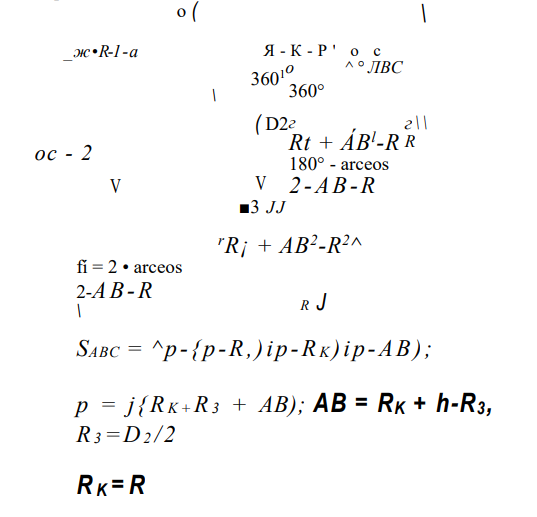
В полученной формуле номинальный диаметр является функцией металлоемкости элементов периодического профиля и основного сечения арматурного профиля. Масса прутка периодического профиля определяется из выражения:

Объём прутка периодического профиля складывается из объёма основной части прутка и объёмов выступов на произвольной длине:
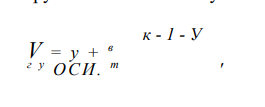
Полный объём одного выступа рассчитывается:
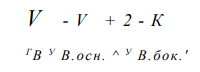
Рассчитаем объём одного серповидного выступа. В поперечном сечении выступ условно представим состоящим из двух блоков (рис. 2.3). Объем основного тела выступа определится из выражения:
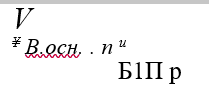
где Ь – ширина анкерующего выступа.
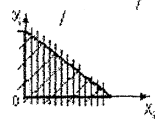

Рис. 2.3. К определению объема выступа периодического профиля 1-боковые участки, 2-основное тело выступа
Для расчета объёма боковых участков выступа рассмотрим его поперечное сечение и его боковой участок, который имеет вид прямоугольного треугольника рис. 2.3. В поперечном сечении с определенным шагом, проведем секущие плоскости в фронтальной части выступа, которые при пересечении боковой грани выступа, будут иметь серповидный вид. Эти площади рассчитываются следующим образом:
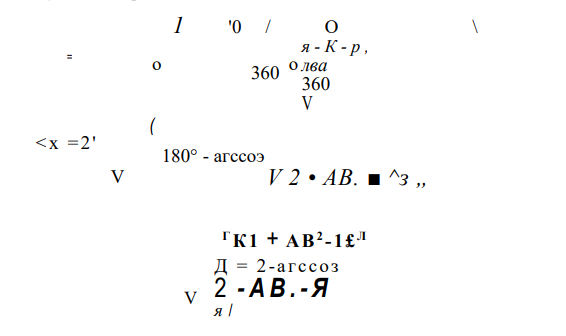
где У\ высота текущего сечения
Так как поперечное сечение бокового участка выступа имеет форму прямоугольного треугольника, то текущую ординату можно определить по формуле:
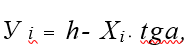
Интегрируя (2.12) вдоль линий скольжения & и £ получим
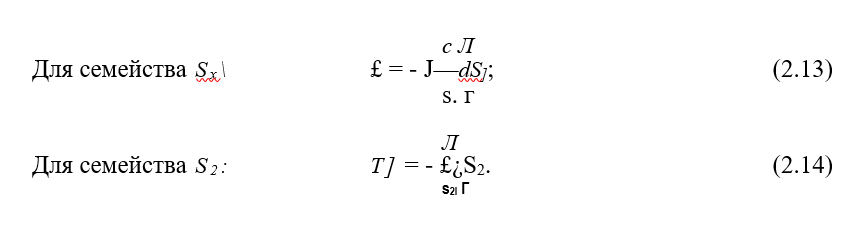
Сетка линий скольжения в меридиональном сечении (рис. 2.4) построена с использованием свойств линий скольжения и численного метода решения краевой задачи Римана. Сетка линий скольжения состоит из треугольной области ABC, примыкающей к контактной поверхности, двух центрированных вееров ACD, ВСЕ и криволинейной области CDOE. Сетка линий скольжения ограничивает очаг пластической деформации.
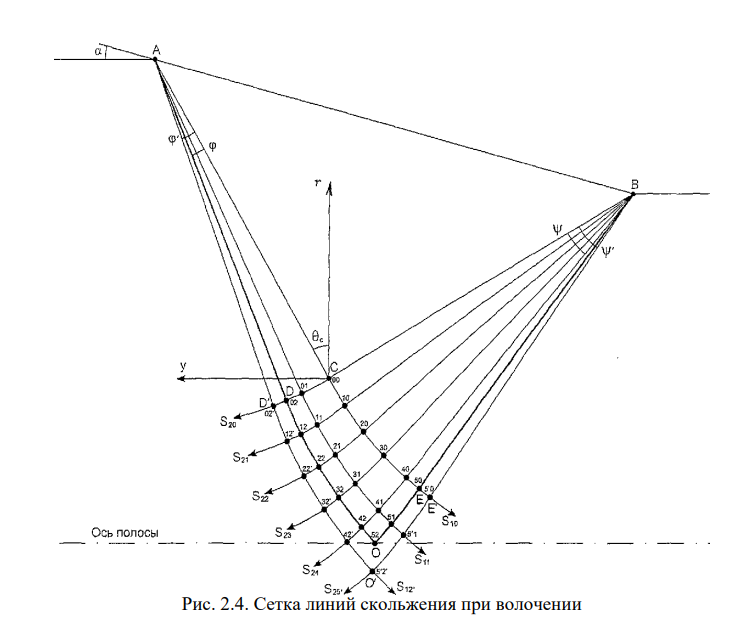
В области ABC, примыкающей к контактной поверхности, линии скольжения представляют собой два семейства взаимно перпендикулярных прямых. Согласно второму уравнению системы (2.5) всюду вдоль линии скольжения <т – к COS 26, в том числе и на поверхности тела. Поэтому, если в предельном случае трение на контакте отсутствует, то FR – равнодействующая сил, действующих на контактной поверхности, совпадает с <ти и перпендикулярна образующей волоки, а линии скольжения обоих семейств выходят на контактную поверхность под углом 45°.
Если на поверхности контакта металла с инструментом касательные напряжения максимальны тк = то линия скольжения семейства о, перпендикулярна к контактной поверхности, а линия семейства касательная к ней и угол между образующей волоки и составляет аг^ —. Поэтому, если на поверхности имеет место трение скольжения (0< тк <—) и принимается закон трения Амонтона тк – /(7п, то линии скольжения семейства выходят на поверхность углами ^ > в > О (рис. 2.5).
При варьировании Тк в тех же пределах мы можем наблюдать изменение угла наклона ^ к контактной поверхности в диапазоне п % 1
— > 0) >– агс^ —. Анализируя влияние контактного трения на угол выхода к контактной поверхности в и угол наклона к образующей волоки СО с учетом ортогональности семейств линий скольжения, было выдвинуто предположение, что угол наклона ^находиться в прямой зависимости от угла наклона линии семейства . Используя данное предположение, определим численное влияние контактного трения, которое характеризуется величиной угла
Из геометрических соображений (рис. 2.5) видно, что угол [3 определяется из выражения:
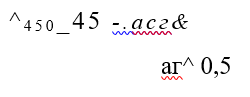
Применение закона трения Амонтона при волочении обосновано в работах [34,86] и хорошо подтверждается практикой. В работах [45,61] задача
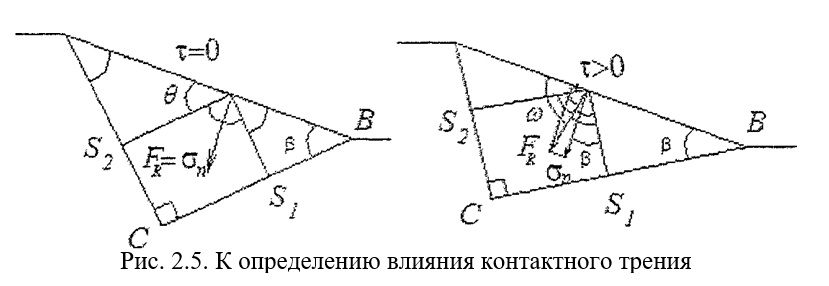
Из работы [61] следует, что при использовании закона Зибеля угол, характеризующий трение равен:

Закон трения Амонтона впервые применяется при использовании метода линий скольжения, поэтому был проведен сравнительный анализ влияния законов трения на угол (3, который представлен на рис. 2.6.
Видно, что трение по закону Амонтона оказывает большее влияние на угол ¡3 во всем диапазоне изменения коэффициента трения /.
К треугольной области ABC со стороны катетов АС и ВС примыкают центрированные поля АСЕ и BCD, образованные лучами прямых и концентрическими окружностями. Сетку линий скольжения в четырехугольной криволинейной области CDOE строим, решая по данным на дугах СЕ и CD начальную характеристическую задачу Римана. Точки пересечения линий скольжения назовем узловыми точками. Узловая точка «mn» образована пересечением n-ой линией скольжения семейства S] и га-ой линией скольжения семейства S2.
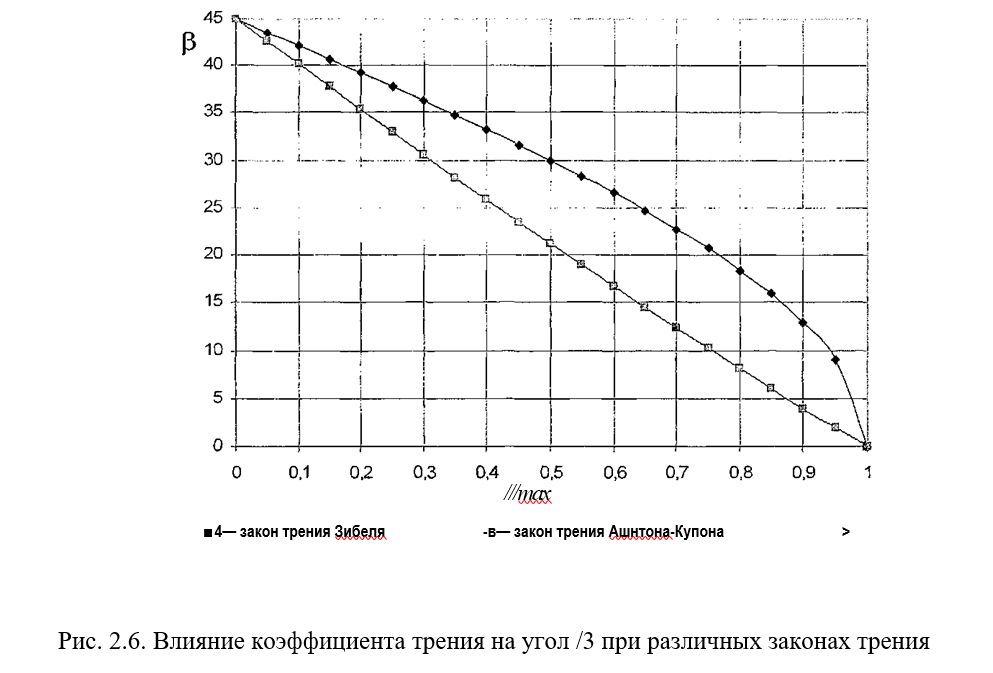
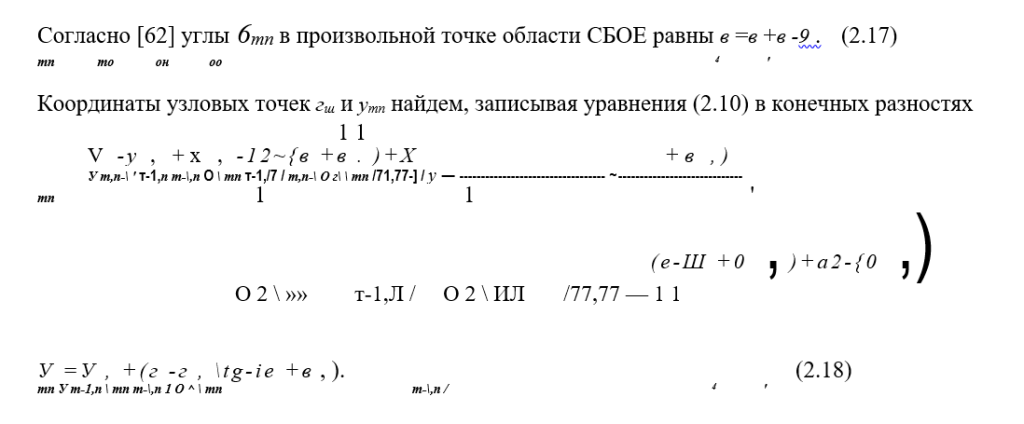
После построения сетки линий скольжения находим в каждой узловой точке функции напряженного состояния £ и Т]. При этом достаточно найти одну из них так как, вычитая первое уравнение (2.8) из второго, получим:
г] = % + (2.19)
ля нахождения величины % кривую OD разобьем на 100 участков. На каждом участке кривую заменим хордой. Это допущение значительно упрощает интегрирование в (2.13, 2.14), при этом погрешность расчетов не превышает 1%.
Рассматривая кривую ODA как совокупность участков прямых линий, найдем параметр проинтегрировав в качестве примера уравнение (2.13) на отрезке AD. В произвольной точке G на линии AD по формуле (2.13) имеем: rÄdS. Р

С учетом уравнения (4.10) выражение (4.20) легко интегрируется

В уравнении (2.22) в итоге неизвестно <f0 в точке О. Так как функция £ по уравнению (2.22) может быть найдена в любой узловой точке на линии ODA, то может быть найдено в каждой точке и <7 через соотношение

На линии скольжения ODA на входе в очаг деформации помимо нормальных напряжений действует максимальное касательное напряжение Ттт = к. Для нахождения проецируем все силы, действующие на линии ODA на ось у и приравниваем к противонатяжению, которое принимаем равным нулю. Уравнение равновесия сил при отсутствии противонатяжения принимает вид:

После вычисления по (2.24), используя формулу (2.22) находим £
во всех узловых точках линии ODA. Затем, интегрируя (2.13, 2.14), находим ^ и во всех остальных точках сетки линий скольжения. Зная функции и ¡7 во всех узловых точках сетки по (2.23) и (2.5) находим компоненты тензора напряжений оп, <Jyy, (Jry.
Описанный выше алгоритм позволяет рассчитать напряжения и определить границы зон с разными схемами напряженного состояния в очаге деформации при волочении в зависимости от технологических факторов процесса.
Влияние технологических факторов на напряженное состояние
Методика расчета напряженного состояния с использованием метода линий скольжения требует большого объёма графических построений и математических вычислений, поэтому с целью автоматизации расчетов и построения полей напряжений очаге деформации был разработан программный продукт «Автоматизированный расчет напряженного состояния при волочении» на языке «Delphi» (подана заявка на регистрацию программы в Федеральный орган исполнительной власти по интеллектуальной собственности). Программа имеет понятный интерфейс (рис.2.7.) и доступна пользователям, не имеющим специальной подготовки, легко вписывается в систему управления качеством продукции. Разработанный программный продукт позволяет оперативно моделировать и оценивать уровень напряженного состояния при волочении в зависимости от технологических факторов обработки и показывать визуальную картину распределения напряжений в очаге деформации (рис. 2.8-2.9).
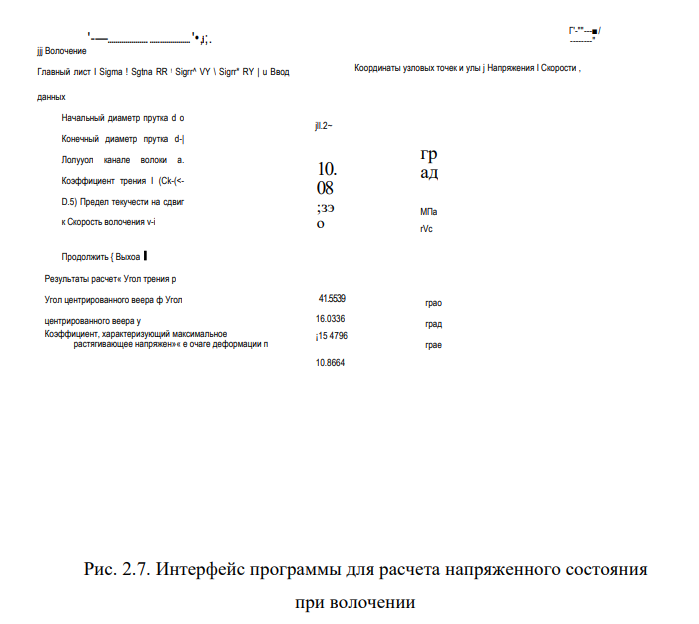
На базе программы выполнили анализ влияния технологических факторов волочения на распределение напряжений по сечению проволоки. На рис. 2.10-2.12 показано распределение напряжений <7п и <7уу вдоль границы поля линий скольжения на входе в очаг деформации, в связи с наибольшей неравномерностью распределения напряжений, и влияние на него различных факторов – степени деформации, угла волоки и контактного трения. Анализируя полученные данные видно, что продольные напряжения сг , растягивающие в центральной части очага деформации и сжимающие в контактной области. С учетом знака они уменьшаются от оси к контактной поверхности и увеличиваются от входного сечения к выходному.
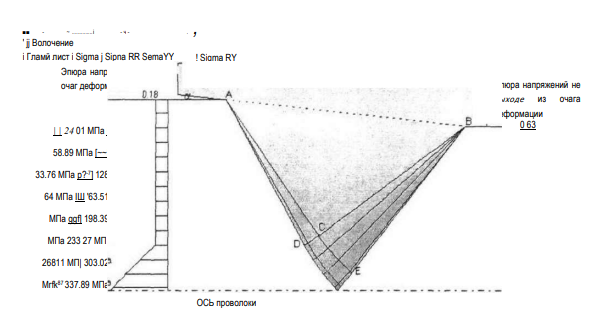
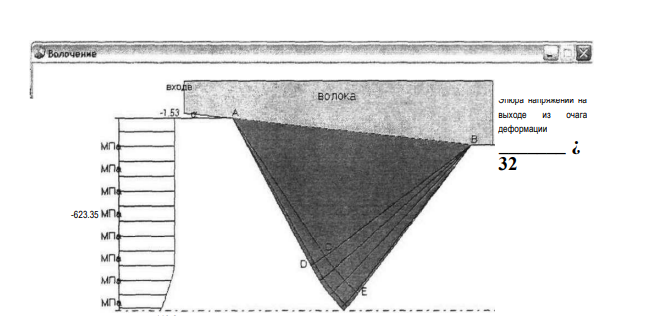
Рис.2.8. Результаты расчета волочения заготовки под профилирование а- поле продольных напряжений ак> ; б – поле радиальных напряжений <7 (при 8=25%, полуугол волоки-60)
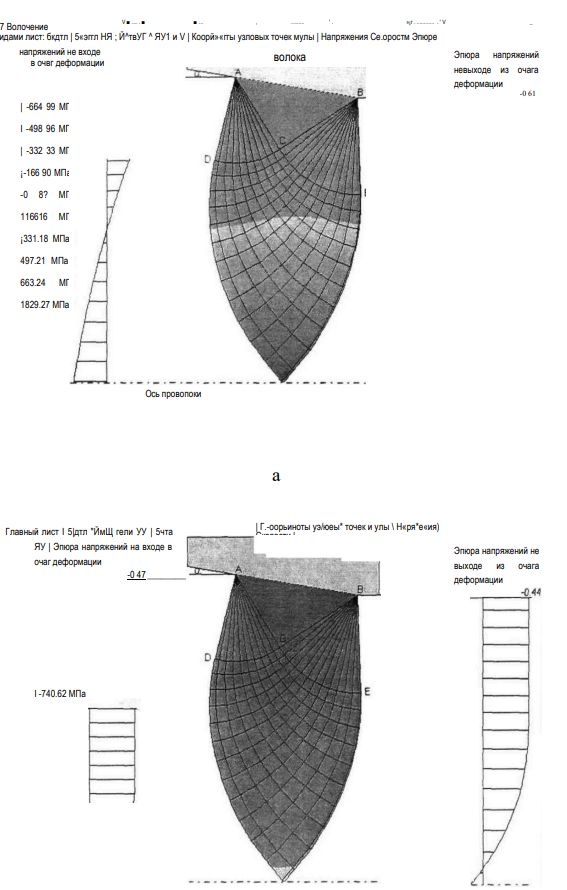
Рис. 2.9. Результаты расчета волочения заготовки под профилирование а- поле продольных напряжений сг^ ; б – поле радиальных напряжений <т (при £=12%, полуугол волоки-60)
Радиальные напряжения <7гг, преимущественно сжимающие по всему очагу деформации. По абсолютной величине они уменьшаются от контактной поверхности к оси и от входного сечения к выходному.
Таким образом, наиболее неблагоприятное напряженное состояние имеет место на оси проволоки, где максимальны с учетом знака и продольные, и радиальные напряжения.
Неравномерность распределения напряжений по сечению проволоки с уменьшением степени деформации возрастает (рис. 2.10). Продольные напряжения ст являются растягивающими на оси проволоки при любых степенях деформации. Причём, с уменьшением степени деформации они увеличиваются. При малых степенях деформации поверхностные слои проволоки у входа в волоку оказываются сжатыми в продольном направлении <7 < 0).Радиальные напряжения <7гг с учетом знака уменьшаются от оси
проволоки к поверхности, где имеют максимум по абсолютной величине. Причем, при больших степенях деформации радиальные напряжения на оси проволоки сжимающие, а при малых степенях деформации – растягивающие. Таким образом, при определенных параметрах процесса волочения в центральных слоях проволоки может возникнуть неблагоприятная зона напряженного состояния всестороннего растяжения.
Из рис. 2.10 видно, что чем меньше степень деформации, тем больше растягивающие напряжения, и больше протяженность зоны всестороннего растяжения.
Увеличение угла волоки действует аналогично уменьшению степени деформации (рис. 2.11). Чем больше угол волоки, тем больше неравномерность напряженного состояния. С увеличением угла волоки радиальное напряжение <7п растет по всему сечению. Продольное напряжение (Туу при этом увеличивается на оси проволоки, а у поверхности убывает и достигает даже отрицательного значения.

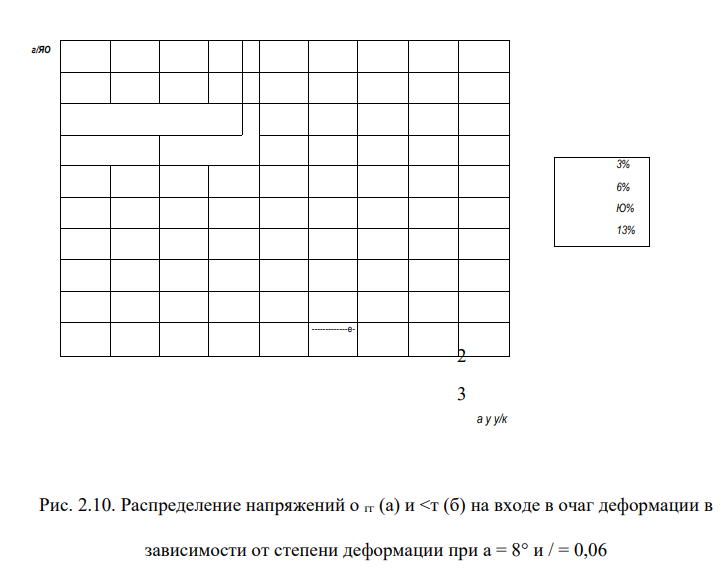
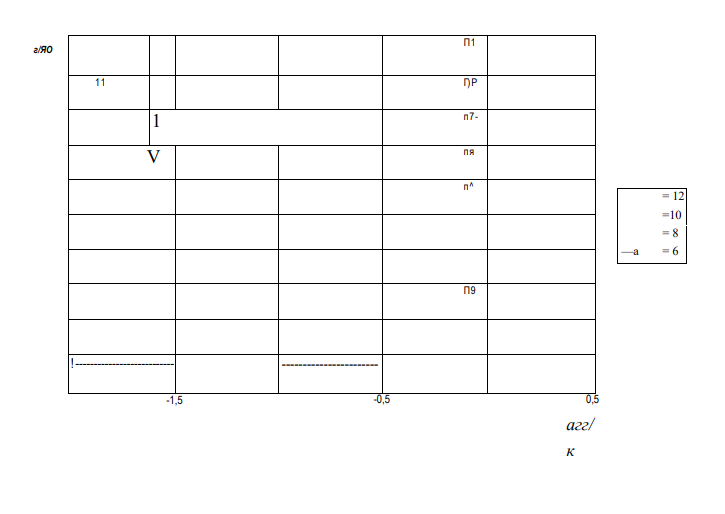

Рис. 2.11. Распределение напряжений С7п (а) и СТуу (б) на входе в очаг деформации в зависимости от полуугла волоки при £ = 13% и / = 0,06
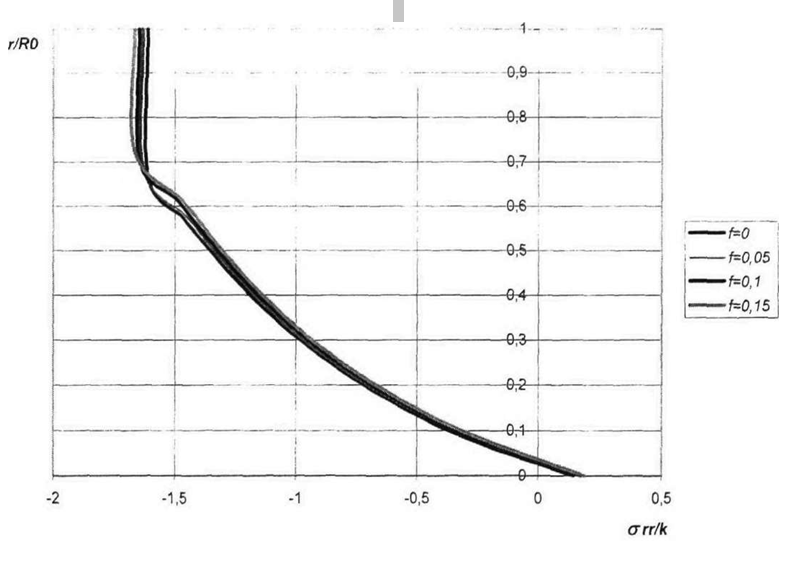
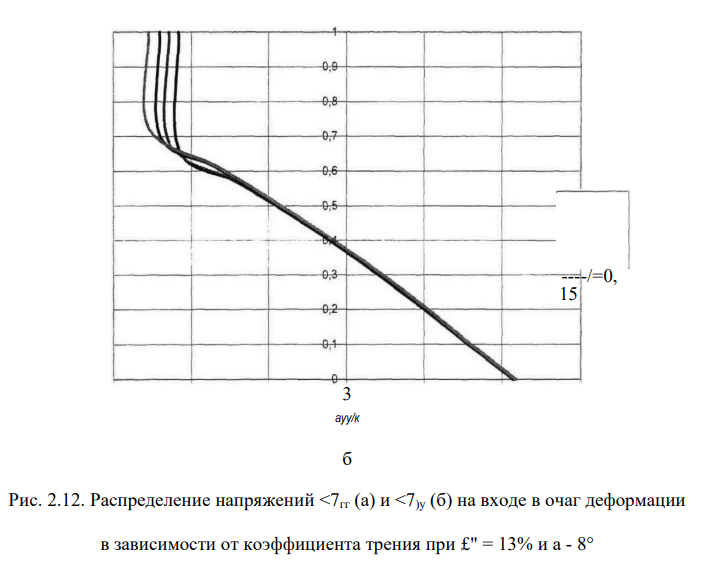
Контактное трение оказывает сравнительно слабое влияние на напряженное состояние (рис. 2.12). С увеличением трения на контакте неравномерность напряженного состояния возрастает.
С увеличением коэффициента трения радиальное напряжение растет по всему сечению, а продольное напряжение на оси увеличивается и убывает к поверхности проволоки. Однако при реально существующих коэффициентах трения / = 0,02 ОД все эти изменения невелики. Таким образом, увеличение контактного трения действует аналогично уменьшению степени деформации и увеличению угла волоки.
Анализируя полученные результаты, можно сделать вывод, что при некоторых параметрах процесса волочения в центре очага деформации имеется зона напряженного состояния всестороннего растяжения. Протяженность её по радиусу проволоки и действующие в ней растягивающие напряжения (7п. и <7 тем больше, чем меньше степень деформации, больше угол волоки и
контактное трение. Напряженное состояние всестороннего растяжения является весьма неблагоприятным для материала протягиваемой проволоки. В зависимости от материала, его структуры, параметров обработки наличие зоны всестороннего растяжения может проявлять себя по разному во внутренней области изделия. В одних случаях могут образовываться внутренние дефекты в проволоке, в других только понижаться твердость и наблюдаться явление «разрыхления» [63].
Для характеристики напряженного состояния и оценки рациональности назначаемых режимов обработки введем коэффициенты тип. Коэффициент т характеризует протяженность зоны напряженного состояния всестороннего растяжения в радиальном направлении:
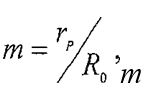
где гр – радиус, до которого действуют радиальные растягивающие напряжения, Я0 – начальный радиус.
С уменьшением степени деформации и увеличением угла волоки коэффициент т увеличивается, а напряженное состояние продукта волочения становится неблагоприятным для последующего профилирования и термической обработки. (рис. 2.13).
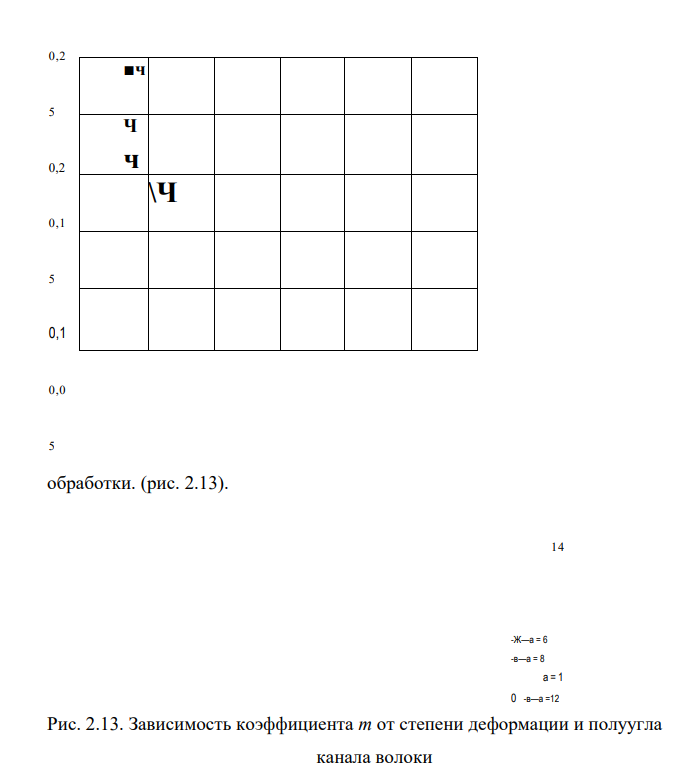
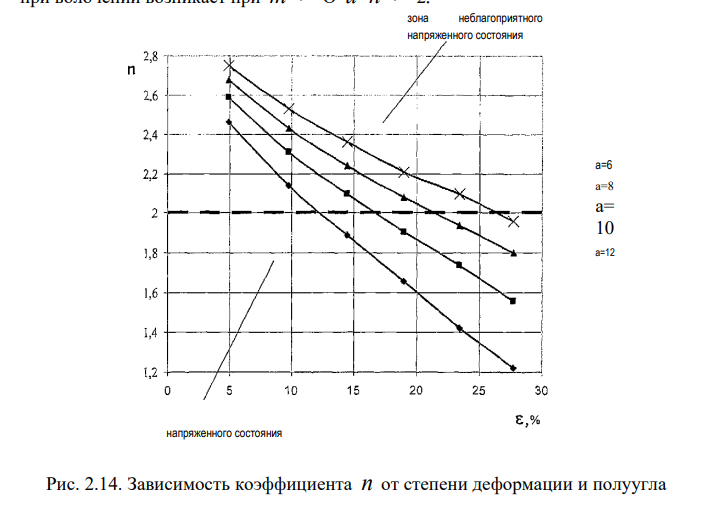
Максимальное растягивающее напряжение действует на оси проволоки, в точке О, и является продольным напряжением. Коэффициент п (рис.2.14) позволяет судить о вероятности возникновения дефектов в проволоке. На оси проволоки, в точке О, сг, = <т , а <т3 = (7п.. Тогда из условия пластичности (2.1) получим а =2к + <7гг. Следовательно, при растягивающем радиальном напряжении сп > 0 продольное напряжения ст превышает предел текучести, а коэффициент п>2. Итак, неблагоприятное напряженное состояние при волочении возникает при т > О и п > 2.
Полученные результаты использованы при проектировании режимов волочения заготовки под профилирование.
Выводы
- Получена инженерная формула, позволяющая определять диаметр круглой заготовки под профилирование арматурного периодического профиля по ТУ 14-125-704-96 из учета получения требуемого уровня сцепления с бетоном и минимальной массы погонного метра профиля.
- На основе метода линий скольжения выполнен анализ напряженного состояния в очаге деформации при волочении заготовки под профилирование. Показано влияние основных технологических факторов процесса волочения на распределение напряжений в очаге деформации. Для анализа влияния технологических параметров волочения на вероятность возникновения неблагоприятного напряженного состояния предложены коэффициенты тип, характеризующие соответственно размеры зоны всестороннего растяжения и отношение максимального растягивающего напряжения в очаге деформации к пределу текучести обрабатываемой стали.
- Разработано программное обеспечение расчета напряженного состояния в очаге деформации при волочении методом линий скольжения, с помощью которого возможно оперативно моделировать и анализировать условия деформирования в зависимости от технологических факторов процесса и исходной заготовки с учетом особенностей последующего профилирования и термической обработки.
Список литературы
- В.В Битков Технология и машины производства проволоки.- УРО РАН, Екатеринбург, 2004., 368С.
- Зубов В.Я. , Мальцева Л.А. О масштабном факторе при разрушении стальной проволоки //. Термическая обработка и физика металлов. Вып.2. -Свердловск: УПИ, 1976. С. 15-19.
- Семавина А.Н., Гаврилюк В.Г., Терских С.А. О природе масштабного эффекта в холоднотянутой стальной проволоке // Физико-химическая механика материалов.- 1979.- №2.-С. 24-28.
- Р.Б. Красильщиков. Деформационный нагрев и производительность волочильного оборудования.- М: Металлургия, 1970, 218 С.
- Э. Штольте., В. Геллер. Самозакаливающаяся арматурная сталь с улучшенными эксплуатационными свойствами//Черные металлы- №1.- 1974.- С.11-14.
- Закалка с высоким отпуском пружинной проволоки// Новости черной металлургии за рубежом – №3.- 2005.-С. 48-49.
- И.А. Юхвец. Производство высокопрочной проволочной арматуры- М.: Металлургия, 1973, 324С.
- Фогель Л. М. Повышение свойств арматурной проволоки с четырех-сторонним профилем на основе совершенствования режимов волочения и про-филирования. Дис. канд. техн. наук.- Магнитогорск: МГМИ, 1991, 138С.
- Киреев Е.М. Совершенствование производства высокопрочной арма-турной проволоки с целью повышения ее релаксационной стойкости. Дис. канд. техн. наук.- Магнитогорск: МГМИ, 1984, 146С.
- Харитонов В.А. Исследование и разработка способа производства вы-сокопрочной арматурной проволоки прокаткой в трехвалковых калибрах: Дис. канд. техн. наук.- Магнитогорск: МГМИ, 1975Д35С.
- Харитонов В. А Повышение эффективности производства пружинной и арматурной проволоки диаметром 6,0 -8,0 мм холодной прокаткой в трехвал¬ковых калибрах: Дис. канд. техн. наук.- Магнитогорск: МГМИ, 1988, 138С.
- Белан А.К. Исследование и разработка технологии изготовления низ-коуглеродистой арматурной проволоки прокаткой в многовалковых калибрах. Дис. канд. техн. наук.- Магнитогорск: МГМИ, 1981,172С.
- Г. JI. Горелик, A.M. Тельтейбаум. Новые виды высокопрочной проволоки для производства железобетонных шпал// Бетон и железобетон .- № 4.- 1991.-С.14-16.
- Высокопрочная арматурная сталь / Кугушин A.A., Узлов И.Г., Калмы¬ков В.В., Мадатян С.А., Ивченко A.B. – М.: Металлургия, 1986, 272С.
- Сычков А.Б., Жигарев М.А., Перчаткин A.B. Высокопрочный арма¬турный прокат из высокоуглеродистой стали// Вестник МГТУ им.Г.И. Носова.- 2005.-№ 1.-С.42-45.
- С.А. Мадатян. Арматура железобетонных конструкций.-М.: Воентех- лит, 2000, 256 С.
- Мадатян С.А. Новое поколение арматуры железобетонных конструк¬ций // Бетон и железобетон. – 1998. – №2.-С. 3-6.
- Баскин С. Л. Арматурные профили малых сечений для сборного желе-зобетона//Сталь. – 1987.- № 10.-С. 12-16.
- В.А. Шеремет. Проблемы производства бунтового проката с заданными физико-механическими свойствами// Труды шестого конгресса прокатчиков., М.: Черметинформация, 2006.- Т.1.-С. 135-136.
- Рахштадт А.Г. . Пружинные стали и сплавы. М.: Металлургия, 1982,
400 С.