Сейчас ваша корзина пуста!
Исследование формирования качества арматуры периодического профиля термическим упрочнением с отдельного нагрева
Цикл статей:
Глава 1 – Повышение качества и конкурентоспособности высокопрочной арматуры диаметром 10,0 мм для железобетонных шпал на основе разработки рациональных режимов холодной деформации и термической обработки
Глава 2 – Моделирование напряженного состояния при волочении заготовки н^ размер под профилирование
Исследование режимов термической обработки арматуры периодического профиля с использованием тепла печного нагрева
В главе 1 показана возможность применения указанного способа упрочнения для формирования требуемых свойств арматурной стали периодического профиля. В связи с этим вели исследования по определению температурно-временных режимов закалки и отпуска для условий нагрева металла внешними источниками тепла и оценки возможности их использования в управлении качеством готовой продукции.
Исследования процессов формирования качества холоднопрофилиро- ванной арматуры диаметром 10,0 мм из сталей 40С2 и 55С2 на этапе термической обработки проводились в лабораторных условиях на образцах длиной 300-350 мм. Объем экспериментальной выборки составлял по 50 образцов арматуры из каждой марки стали. Образцы нагревали под закалку в электрической камерной печи без защитной атмосферы. Температура нагрева под закалку, принималась из условия Ас3 + (30-50) °С и для стали 55С2 составила 880 °С [76], а для стали 40С2 – 900 °С [77]. Продолжительность нагрева 25-30 мин обеспечивала необходимую равномерность распределения температуры в садке и полноту протекания фазовых превращений в стали. После нагрева образцы поштучно охлаждали в воде в вертикальном положении. Твердость образцов из стали 40С2 после закалки в воде соответствовала 56-58 HRC. Закалка стали 55С2 в воде обеспечивала более высокий уровень твердости арматуры 58-60 HRC. Визуально трещин закалочного происхождения на поверхности образцов обнаружено не было. Арматурные прутки после закалки были подвергнуты печному отпуску в интервале температур 350-400° С с различной продолжительностью 25-35 мин. Согласно литературным данным [49], отпуск в указанном интервале температур должен обеспечивать структурное состояние металла, приемлемое для формирования конечного уровня свойств, сопоставимых с требованиями, предъявляемым к арматурной стали в состоянии поставки. Испытания механических свойств арматуры после термообработки выполнили в сертифицированной центральной заводской лаборатории ОАО «Магнитогорский калибровочный завод» (ОАО «ММК- МЕТИЗ»). Результаты испытаний механических свойств образцов арматурной стали приведены на рис. 4.1, 4.2.
По результатам исследований с использованием методов математической статистики и пакета программ (^айвйса 6.0» построены уравнения, позволяющие прогнозировать механические свойства термически упрочненной арматуры в зависимости от температуры и времени проведения операций печного отпуска [78]. В качестве оценки адекватности моделей был рассчитан коэффициент детерминации Я2, используемый для статистической оценки тесноты связи между результативными и объясняющими показателями. Данный коэффициент выражает долю объясненной изучаемыми факторами дисперсии результативного признака и служит важной характеристикой построенной модели. Математические модели зависимости механических свойств арматуры периодического профиля от температурно-временных параметров отпуска имеют вид:
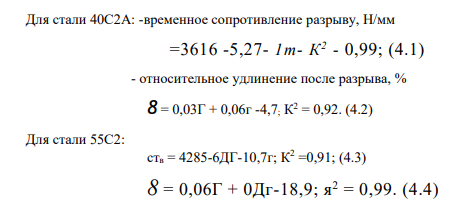
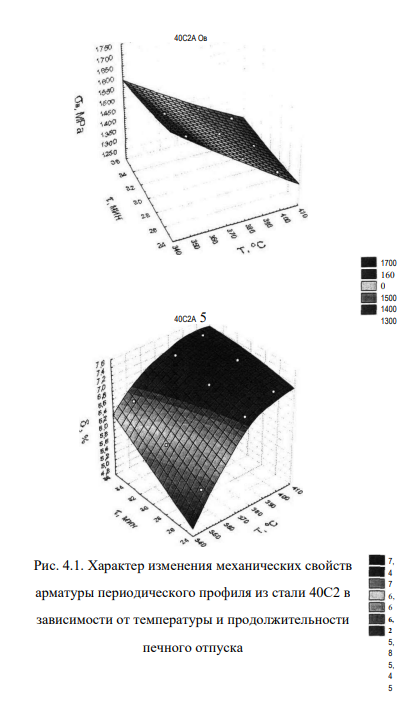
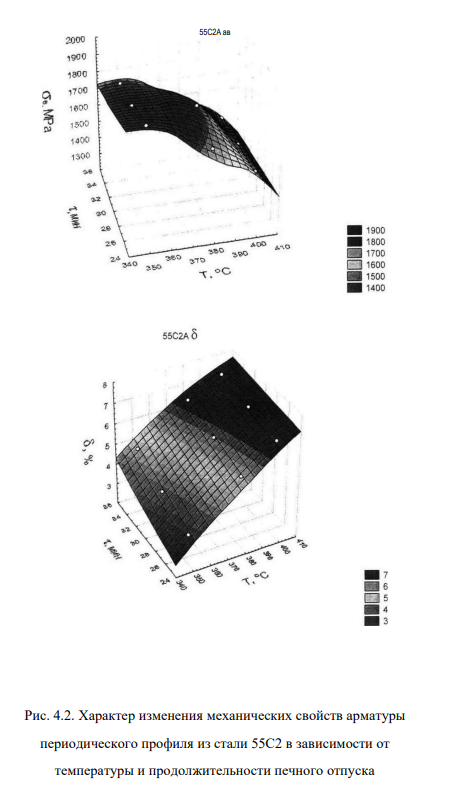
Расчеты по полученным моделям (4.1 – 4.4) позволяют определить тем- пературно-временные интервалы печного отпуска, при которых показатели качества профилированной арматуры полностью выходят на уровень, соответствующий требуемым значениям.
Так, показатели механических свойств металла при отпуске опытных образцов арматурной стали 40С2 при температуре 360° С продолжительностью 30 минут полностью соответствуют нормативным значениям ТУ 14125-704-96. Для стали 55С2 требуемый комплекс механических свойств металла обеспечивается отпуском при температуре 390° С в течение 30 минут. Полученные результаты были использованы при апробации опытно- промышленной технологии производства высокопрочной арматурной стали периодического профиля для железобетонных шпал.
Исследование влияния скоростного отпуска на механические свойства арматуры периодического профиля
Более прогрессивный вариант организации поточной технологии термического упрочнения арматуры предполагает использование тепла индукционного нагрева. В этом направлении наибольший интерес представляет изучение поведения закаленной стали при индукционном отпуске.
Исследование режимов закалки профилированной арматуры с использованием тепла индукционного нагрева выполнили в условиях калибровочного цеха ОАО «МКЗ» на установке УТВЧ оснащенной двумя индукционными нагревателями и используемой для рекристаллизационного отжига калиброванного металла диаметрами 20-40 мм. Конструкция индукционных нагревателей в установках рекристаллизационного отжига рассчитана на обеспечение конечной температуры нагрева металла 720-750° С, что явно недостаточно для перевода изучаемых кремнистых сталей в аустенитное состояние. Интервал закалочных температур для указанных сталей в условиях скоростного нагрева ТВЧ смещен в область более высоких значений и соответствует 900-950° С.
По условиям генерирования тока высокой частоты в проводниковых материалах тонких сечений индукторы большого диаметра, применяемые для рекристаллизационного отжига, не обеспечивают нужной концентрации энергии магнитного потока и не позволяют нагреть металл до требуемых закалочных температур. В связи с этим была проведена реконструкция одной экспериментальной установки, в результате которой действующие нагреватели были оснащены индуктирующим проводом с меньшим диаметром проходного сечения рис. 4.3. что дало возможность нагреть прутки диаметром
10,0 мм до требуемых закалочных температур.
Питание установки током высокой частоты 4000 Гц осуществляли от
тиристорных преобразователей напряжением 600 В. Скорость движения прутков профилированной арматуры длиной 2650 мм через индукционные нагреватели составляла 1,5 м/мин. Измерение температуры образцов производили оптическим пирометром. Путем однофакторных экспериментов были установлены температуры нагрева под закалку с индукционного нагрева, обеспечивающие формирование структуры мартенсита 3-5 балла, равномерно распределенной по всему сечению арматуры. Температура нагрева под закалку для стали 40С2 составляла 930-950 для стали 55С2 – 900-920 0 С.
Важной составляющей экспериментального исследования по отработке режимов термического упрочнения арматурной стали с использованием тепла индукционного нагрева явилось проектирование и изготовление охлаждающего устройства для закалки профилированных прутков на установке УТВЧ. Для осуществления закалки была разработана конструкция и изготовлено закалочное устройство (рис. 4.4) с тангенциальной подачей воды в охлаждающие полости, обеспечивающей устойчивую работу при любых режимах охлаждения. Закалочное устройство размещали на расстоянии 20 мм от второго индуктора. Давление воды в сети в опытах составляло 3 -4 атм. Закаленные при указанных технологических параметрах образцы арматуры из стали 40С2 имели твердость 55-59 HRC, из стали 55С2 – 57-60 HRC.
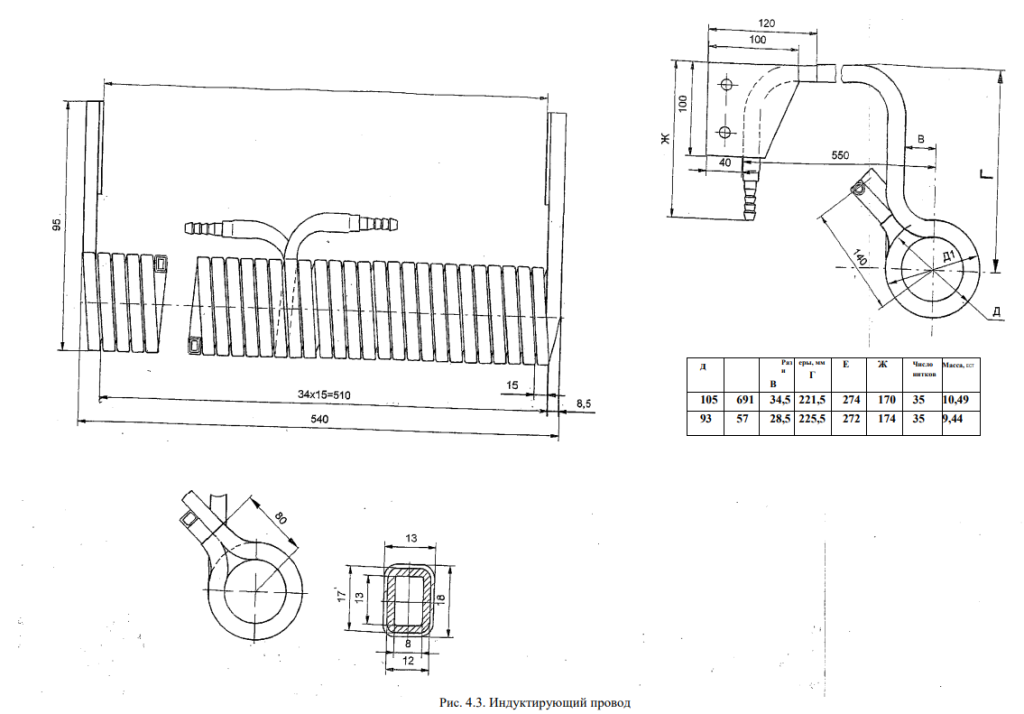
Исследование поверхности металла методом магнитной порошковой дефектоскопии с помощью дефектоскопа ЭМИД-3 не показало образование закалочных трещин.
Условия индукционного отпуска моделировались нагревом закаленных образцов, отобранных от арматурных прутков, в ванне с расплавом солей KN03 и NaNC>3, обогреваемой электрическим током. Данные по продолжительности нагрева образцов до температур отпуска 500, 550 и 600° С приведены на рис. 4.5, 4.6. в виде термограмм нагрева. Термограммы получены путем записи сигнала от хромель-алюмелевой термопары, зачеканенной в одном из образцов, на электронном автоматическом потенциометре КСП-4. На рис. 4.5 приведены термограммы нагрева образцов в печи. Как видно из представленных данных, продолжительность печного нагрева до рабочих температур 500 и 600° С составляет 6 и 9 мин, соответственно.
Нагрев в расплаве солей до указанных температур протекает за более короткое время, соответственно, 23 и 37 сек, что эквивалентно скоростям нагрева 13,5 и 26 град/сек (рис. 4.6).
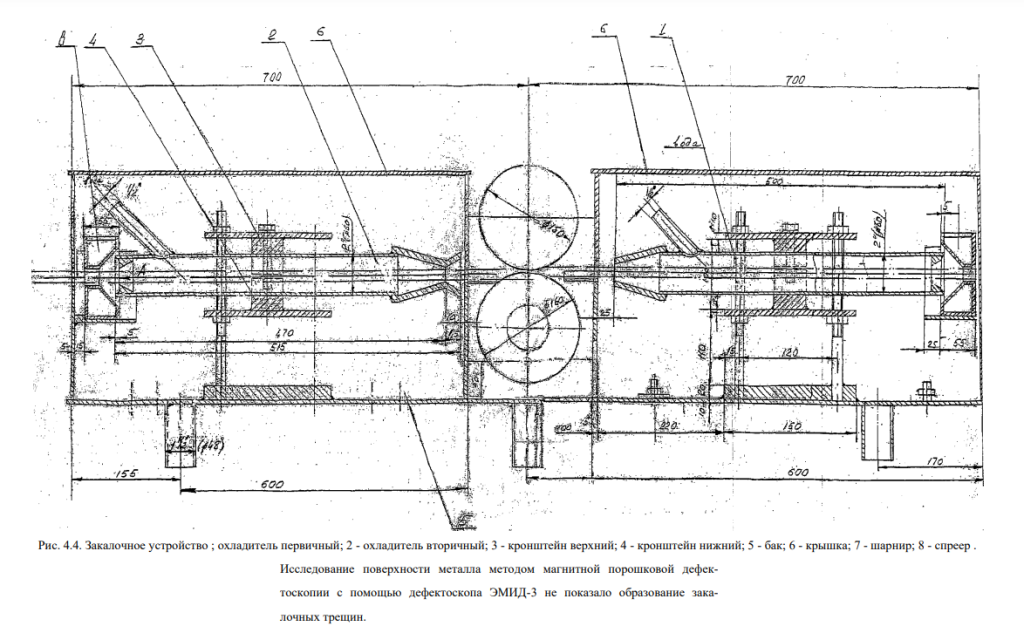
В первой серии опытов закаленные образцы отпускали в расплаве соли при температурах 450, 500, 550 и 600° С с относительно длительными выдержками в 1, 2, 3, 4, 5 и 10 мин.
Было установлено, что выдержка 60-180 с при температурах отпуска 550 и 600° С приводит к полному распаду мартенсита в исследуемых сталях с получением структуры сорбита отпуска. В результате образцы, отпущенные при указанных температурах, приобретают пониженную прочность, уровень которой не соответствует установленным требованиям.
Ни один из опытных режимов отпуска образцов стали 40С2 не обеспечил положительного результата. Единственный режим, который позволил получить нормируемые значения прочности и пластичности металла – это отпуск, выполненный при температуре 450° С с выдержками 5 и 10 мин на образцах из стали 55С2. Однако, такой режим не может быть реализован в поточной технологии термического упрочнения арматурной стали по причине существенного дисбаланса временных параметров нагрева под закалку и отпуск.
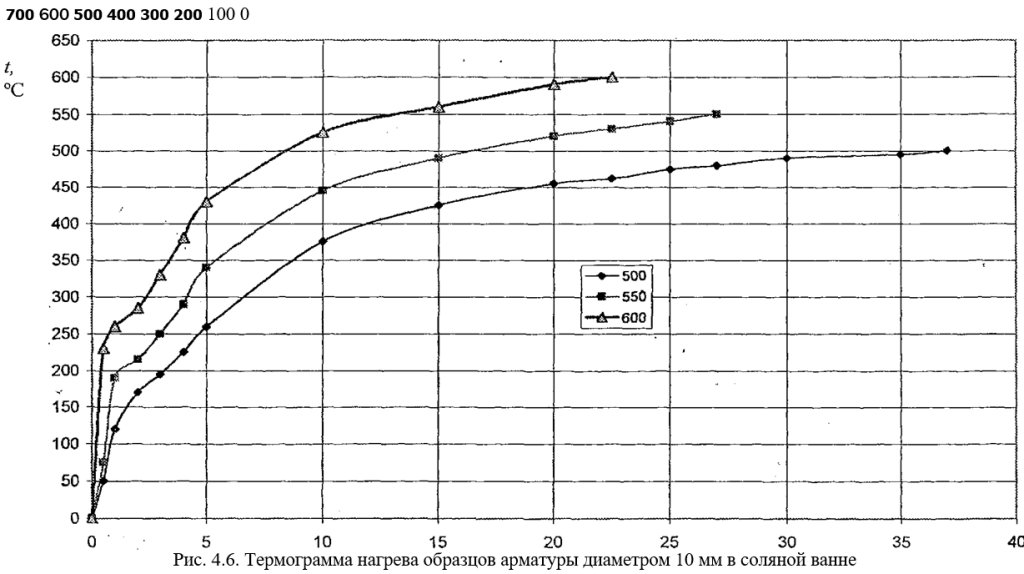
С учетом данных полученных на первом этапе исследований режимы скоростного отпуска были скорректированы в направлении сокращения длительности пребывания образцов в расплаве соли. Последующие опыты выполнялись при температурах отпуска 500 и 550° С продолжительностью 10, 20, 30, 40 и 60 сек. Характер изменения свойств сталей 40С2 и 55С2 при обработке по указанным режимам представлен на рис 4.7, 4.8.
По результатам статистической обработки получены зависимости, позволяющие прогнозировать механические свойства термически упрочненной арматуры периодического профиля в зависимости от температуры и времени проведения операций скоростного отпуска [78]:
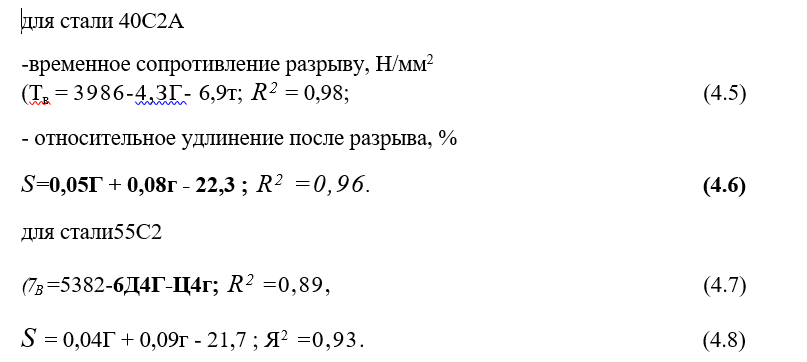
Анализ математических моделей свидетельствует о том, что наиболее существенное влияние на механические свойства металла оказывает температура отпуска. В стали 40С2 распад мартенсита происходил непосредственно на стадии прогрева образцов до конечной температуры отпуска 550° С, обеспечивая формирование структуры троостита отпуска и свойственного этой структуре комплекса механических свойств металла, удовлетворяющего требованиям к показателям качества готовой арматуры. Расчеты по получен,- ным моделям показали, что для арматуры из стали 40С2 необходимые показатели качества арматуры по временному сопротивлению разрыву и относительному удлинению могут быть достигнуты отпуском при температуре 550° С за время 20 сек, а в стали 55С2 за время 30 и 40 сек.
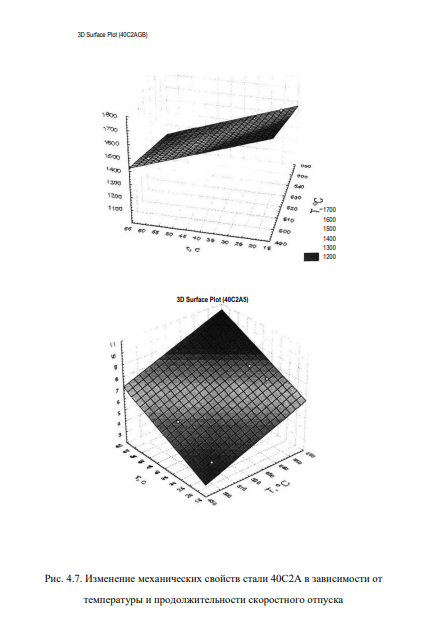
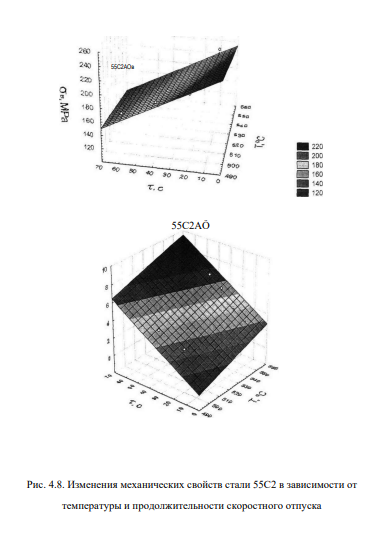
С учетом времени прогрева металла 27 с до заданной температуры в расплаве соли, установленным по термограммам рис. 4.6, чистое время пребывания образцов при температуре отпуска в последнем случае соответствует 3 и 17 сек.
По данным работы [54] такие скорости нагрева применяются в технологиях индукционного отжига калиброванного металла, что говорит о возможности использования индукционных установок для проведения операции отпуска закаленных прутков арматуры.
В ходе исследований установлено, что отпуск, выполненный в условиях быстрого нагрева, является сокращенным по продолжительности. Однако в режиме ускоренного отпуска сталь в состоянии приобретать такую же прочность, что и сталь, отпущенная в печи, но при более высокой (на 100-150° С) температуре.
Полученные данные свидетельствуют о том, что структурные превращения при скоростном отпуске стали успевают происходить как с выдержкой, так и без выдержки при температуре отпуска.
Следует полагать, что формирование механических свойств, исследуемых сталей, при ускоренном отпуске формируются не за счет специфического влияния скорости нагрева, а за счет интенсификации диффузионных процессов, которые в условиях повышенных температур протекают за более короткое время, обеспечивая полный распад мартенсита и образование структуры троостита отпуска.
Выводы
Установлены закономерности формирования механических свойств, предварительно профилированной в холодном состоянии, арматуры периодического профиля диаметром 10,0 мм из кремнистых марок стали 40С2 и 55С2 на этапе термического упрочнения с отдельного нагрева.
Получены математические модели формирования механических свойств арматуры периодического профиля диаметром 10,0 мм в зависимости от температурно-временных параметров термической обработки по схеме «закалка-отпуск» с использованием тепла печного и скоростного нагрева. Модели позволяют определить режимы термического упрочнения полученной на этапе холодного профилирования арматуры, обеспечивающие получение требуемых показателей качества высокопрочной арматуры для железобетонных шпал.
Показана возможность синхронного выполнения процессов закалки и отпуска по ускоренным режимам в поточных технологиях, которые наиболее успешно могут быть реализованы путем индукционного нагрева и отпуска.
Список литературы
- Блейлоб Ф., Борн X. Длительная прочность пружин из улучшенной закаленной и патентированной холоднотянутой проволоки//Черные металлы – №25 – 1963.-С. 13-19.
- Изготовление высококачественных метизов. Кулеша
B. А., Клековкина H.A., Белалов Х.Н. и др. Коллективная монография, г. Бело- рецк, 1999, 328С. - Головин Г.Ф. Высокоточная термическая обработка. Машгиз, 1959,
212С. - Сергеев Г.Н. Термическая обработка и волочение стали с применением ТВЧ. М.: Металлургия, 1978, 223С.
- Шепеляковский К.З. Упрочнение деталей машин поверхностной за¬калкой при индукционном нагреве. М.: Машиностроение. 1972, 288 С.
- Кидин И.Н. Термическая обработка стали при индукционном нагреве, Металлургиздат, М, 1950, 289С.
- Башнин Ю.А., Ушаков Б.К., Секей А.Г. Технология термической об¬работки. Учебн. для вузов, М. Металлургия, 1986, 424 С.
- Электротермическое оборудование. Справочник. Издание 2. Под об¬щей редакцией А.П. Альтгаузена, М.: Энергия. 1980, 376С.
- Соколовский П.И. Арматурные стали.- М.: Металлургия, 1964, 208С.
- Харитонов A.B. Исследование и разработка технологии изготовления бунтовой арматурной стали класса А500 с использованием холодного профи¬лирования : Дис. канд. техн. наук.- Магнитогорск: МГТУ, 2003,124С.
- Аркулис Г.Э. О распределении напряжений в очаге деформации при волочении круглых прутков// Известия вузов. Черная металлургия- №3.- 1969.- C. 90-92.
- Аркулис Г.Э., Антонова Р.Г. Расчет волочения однородной полосы методом линий скольжения: Методическое пособие для вузов. – Магнитогорск: МГМИ, 1979.65С.
- Аркулис Г.Э., Х.И. Копыловский Влияние условий волочения на образование трещин в проволоке// Сталь.- 1970.-№3.-С.756-759.
- Никифоров Б.А., Харитонов Вик.А., Королева Н.Ф., Копылова Е.С., Харитонов В.А. Диаграммы естественных вытяжек систем многовалковых калибров. МГМИ. Магнитогорск, 1987. Деп. в Черметинформации 10.08.87, № 4121 – 4M 87.
- Мулин Н.М. Стержневая арматура железобетонных конструкций.- М..’Металлургия, 1974, 232С.
- Дзугутов М.Я Пластичность, ее прогнозирование и использование при ОМД.- М.: Металлугия, 1984.212С.
- Есипов В.Д., Соколов И.В. Калибровка валков для прокатки профилей трехсторонней арматурной стали // Сталь,- 2000.-№10.-С.23-28.
- Корчунов А.Г. Разработка технологии производства холоднодефор- мированной низкоуглеродистой арматурной проволоки диаметрами 6,0-10,0 мм: Дис. канд. техн. наук.- Магнитогорск: МГТУ, 2001, 172С.