Сейчас ваша корзина пуста!
Разработка рациональных режимов формирования заданного уровня качества высокопрочной арматуры для железобетонных шпал и реализация результатов работы в промышленности
Цикл статей:
Глава 1 – Повышение качества и конкурентоспособности высокопрочной арматуры диаметром 10,0 мм для железобетонных шпал на основе разработки рациональных режимов холодной деформации и термической обработки
Глава 2 – Моделирование напряженного состояния при волочении заготовки н^ размер под профилирование
Выполненные исследования позволили разработать технологическую схему формирования качества высокопрочной арматуры периодического профиля диаметром 10,0 мм из кремнистых марок стали для армирования железобетонных шпал, состоящую из двух технологических блоков [84] (рис. 5.1).
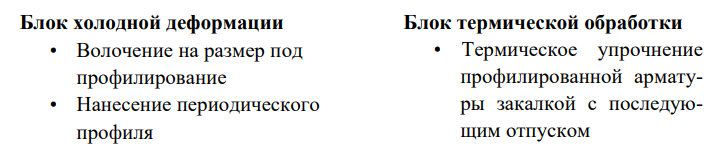
Рис. 5.1. Технологическая схема производства
На промышленных площадках метизных заводов целесообразно использование предлагаемых технологических блоков в единой технологической цепочке. Реализация режимов получения заготовки под профилирование и операция нанесения периодического профиля исполняются на стандартном волочильном оборудовании и не требуют дополнительных материальных затрат. Финишное термическое упрочнение профилированной арматуры осуществляется закалкой с последующим отпуском с использованием тепла печного или скоростных методов нагрева. Выбор методов термообработки определяется материально-технической базой конкретного предприятия. Такая организация технологического процесса обеспечит гибкость и
мобильность при смене сортамента, многовариантность схем получения готовой продукции при выпуске малотоннажных партий.
На металлургических заводах при выполнении многотоннажных заказов возможно отдельное использование блока термического упрочнения при окончательном формировании механических свойств арматуры. В данном случае необходимо организовать производство на прокатном переделе периодического профиля арматуры с соответствующими геометрическими показателями качества.
На базе выполненных исследований с учетом характера взаимодействия между технологическими блоками разработана методика управления качеством высокопрочной арматуры железобетонных шпал диаметром 10,0 мм и определены рациональные режимы обработки, обеспечивающие формирование заданного уровня качества и повышение конкурентоспособности готовой продукции.
Методика управления качеством высокопрочной арматуры периодического профиля для железобетонных шпал
Исходной информацией на входе в методику служат показатели качества горячекатаного подката (рис. 5.2). Показатели качества исходного подката из стали 40С2 должны соответствовать ТУ 14-101-481-2002, стали 55С2 -ГОСТ 14959. К исходной заготовке необходимо предъявлять жесткие требования по металлографической чистоте стали по непластичным и неметаллическим включениям по содержанию газов и вредных примесей. Известно, что в результате повышения загрязненности стали по содержанию газов, а также Б, Р, Аэ, 8В увеличивается склонность к образованию внутренних дефектов при волочении. Наиболее вредные примеси – азот, водород, кислород [30].
На втором шаге методики по инженерной формуле определяется размер круглой заготовки под профилирование из учета получения необходимых параметров сцепления с бетоном и минимальной массы погонного метра арматуры. Затем на базе разработанного в главе 2 программного обеспечения производится анализ напряженного состояния при волочении на размер под профилирование, определяются степень деформации, отвечающая условиям финишной обработки, параметры волочильного инструмента и диаметр исходного подката. В случае высокой исходной твердости горячекатаного подката в качестве дополнительного управляющего воздействия на металл может служить предварительная «смягчающая» термообработка-отжиг. Подготовка поверхности исходного подката для волочения на размер под профилирование осуществляется по рекомендациям, широко описанным в специальной литературе [80,81]. Для устранения травильной хрупкости рекомендуется применять ингибиторы, в качестве которых служат многие органические вещества с содержанием азота уменьшающие разъедающее действие кислоты.
С использованием полученных моделей формоизменения рассчитывается режим профилирования арматуры. Далее осуществляется расчет режимов финишной обработки арматуры на основе математических моделей изменения механических свойств арматуры периодического профиля при термическом упрочнении. Для стали 40С2 в качестве закалочной среды целесообразно использовать воду, для стали 55С2, как более склонной к трещино- образованию можно рекомендовать закалочную среду на основе водорастворимых полимеров [82].
Необходимыми элементами методики являются ограничения, которые обеспечивают выполнение требований по стабильности формирования требуемого качества арматуры. В технологическом блоке «холодная пластическая деформация» режимы обработки определяются с учетом следующих ограничений: возникновение при волочении на размер под профилирование неблагоприятной зоны напряженного состояния с преобладанием в очаге деформации напряжений растяжения, повышенная овальность профиля, невыполнение высоты анкерующего выступа. В технологическом блоке «термическая обработка» в роли ограничений выступает несоответствие полученных механических свойств готовой продукции заданному уровню качества.
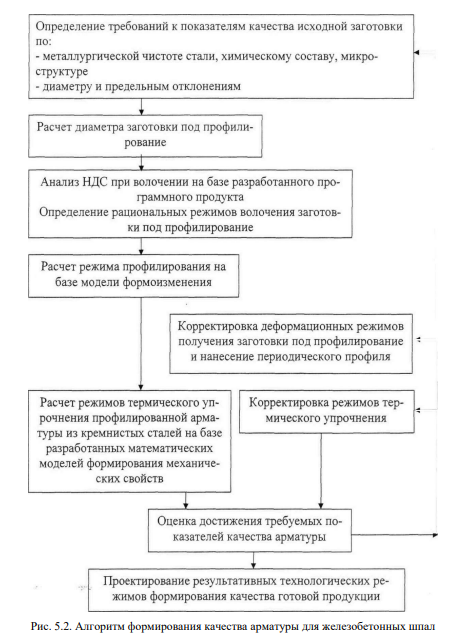
Для обеспечения соответствия между заданным и достигнутым по результатам контроля уровнем показателей качества готовой продукции методика предусматривает корректирующие воздействия на свойства исходной заготовки, режимы волочения, профилирования и термообработки. Результатом служат стабильные режимы холодной деформации на этапе получения периодического профиля и финишной термической обработки, обеспечивающие формирование заданных значений показателей качества и повышение конкурентоспособности высокопрочной арматуры диаметром 10,0 мм для железобетонных шпал.
Результаты опытно-промышленной апробации и оценка уровня качества готовой продукции
Разработанные режимы реализованы на ОАО “МКЗ”, в условиях которого были выпущены опытно-промышленные партии высокопрочной арматуры по ТУ-14-125-704-96 диаметром 10,0 мм из сталей 40С2 и 55 С2 (Приложение 1). Исходный горячекатаный подкат диаметром 13,0 мм подвергали рекристаллизационному отжигу по технологической инструкции ТИ-102-86- 192-05. Подготовку поверхности металла к волочению осуществляли в соответствии с технологическими инструкциями, действующими на предприятии. Волочение подката на размер под профилирование вели в монолитных волоках на однократном стане 1/750 с использованием сухой смазки. Параметры волочильного инструмента по ГОСТ 9453, полуугол канала волоки 6°. Профилирование вели по маршруту 11,2-10,0 мм на промышленных скоростях в клети-волоке со смещенными парами валков, установленной в линию волочильного стана ИЗТМ 10-28. Диаметр валков клети -170 мм. Калибровки валков на рис. 5.3. Геометрические параметры периодического профиля контролировали микрометром типа МК 0 – 25 по ГОСТ 6507, а высоту выступа микрометром по ГОСТ 6727 СТП 2-41 – 88 со специальной пяткой. Линейную плотность
определяли взвешиванием одного метра профиля на весах марки ВНЦ – 2 по ГОСТ 29329.
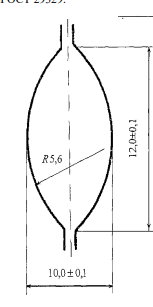
а
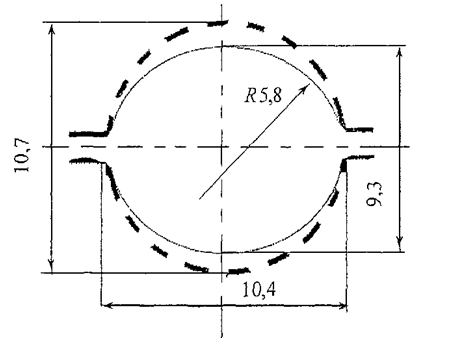
б
Рис. 5.3. Схема калибровки валков профилирующей клети а- первая пара валков; б- вторая пара валков
Высота анкерующего выступа составляла 0,56±0,03. Масса погонного метра арматуры -0,616±0,004 кг. Овальность профилированной арматуры не превышала величины 0,2 мм.
Полученные арматурные прутки по геометрическим показателям и массе погонного метра полностью отвечали требованиям технических условий. На процесс получения холодной пластической деформацией периодического профиля арматуры по ТУ-14-125-704-^96 разработана технологическая карта ТК 176-МТ.ПР-112-2006 (Приложение 2).
Далее задача достижения требуемого уровня качества арматуры решалась с применением методов термического упрочнения профилированных прутков путем закалки с последующим отпуском. Закалку образцов осущест
вили на установке УТВЧ, оснащенной двумя индукционными нагревателями и охлаждающим устройством с тангенциальной подачей воды. Скорость прохождения металла через индукционную установку составляла 1,5 м/мин. Частота тока -4000Гц. Напряжение 600 В. Давление воды составляло 3 атм. Тем- пературно-временные параметры отпуска определили с использованием моделей, описывающих формирование механических свойств арматуры периодического профиля из сталей 40С2 и 50С2А. Измерение температуры металла при термообработке производили оптическим пирометром. В процессе обработки температура металла после первого индуктора составляла 740±20° С, перед охлаждающим устройством для стали 40С2 температура имела значение 940-950 0 С, для стали 55С2 – 920-930 0 С. Структура закаленных образцов-мартенсит 3-5 балла. Твердость НЯС 56-60.
Печной отпуск профилированных прутков вели на роликовой проходной печи в течение 30 минут при температуре 360±15° С для стали 40С2 и 390±15° С для стали 50С2А. Индукционный отпуск выполнили на установке УТВЧ, отключив один индуктор, при скорости движения металла 1,5 м/мин и пониженным давлением воды по следующим режимам: для стали 40С2- температура прутков на выходе из индуктора 500±10° продолжительность отпуска- 40 сек.; для стали 50С2А – 540 ±10° С и 40 сек. В процессе производства отбирались образцы для испытаний эксплуатационных свойств арматуры. Механические испытания проводились согласно ГОСТ 12004 – 81 в сертифицированной ЦЗЛ ОАО “МКЗ” (ОАО ММК-МЕТИЗ») на разрывных машинах типа ТО – 20. Обработку полученных данных проводили методами математической статистики. Механические свойства полученной арматуры приведены в табл. 5.1.
Из анализа результатов опытно-промышленной апробации было установлено, что расхождение между предсказываемыми математическими моделями и фактически полученными механическими свойствами арматуры не превышает 12%. Опытно-промышленная проверка показала, что разработанные режимы холодной пластической деформации и термообработки обеспечивают получение конкурентоспособной продукции с заданным комплексом показателей качества по ТУ-14-125-704-96.
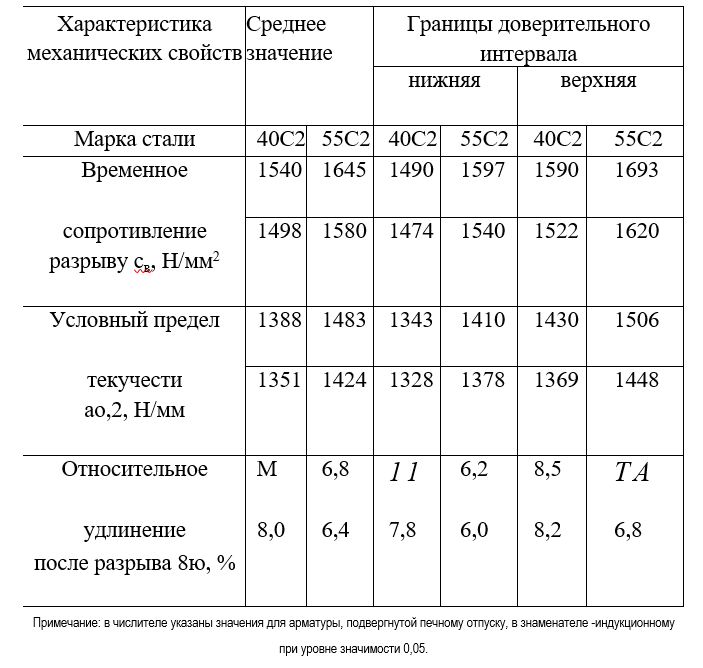
Таблица 5.1 Механические свойства термоупрочненной арматуры
Важным аспектом апробации технических разработок явилось обоснование принципиальной возможности синхронного выполнения процессов закалки и отпуска по ускоренным режимам в поточных технологиях термического упрочнения арматурной стали.
Результаты работы были использованы при составлении программы технического развития ОАО “ММКЗ” до 2010 г. по организации выпуска новых высоколиквидных видов продукции, разработке технического задания и проведении тендера по закупке оборудования для производства высокопрочной арматуры для железобетонных шпал.
Компоновка технологической линии финишной термообработки арматуры периодического профиля
Для организации промышленного производства высокопрочной арматуры диаметром 10,0 мм для железобетонных шпал с использованием технологического блока термического упрочнения предлагается следующий состав оборудования специализированной поточной линии (рис. 5.4) :1 -устройство размотки профилированной арматуры; 2- правильно-отрезной станок; 3- приемный стеллаж; 4-проводящие ролики; 5-группа индукционных нагревателей под закалку; 6-устройство охлаждения водой; 7-индукционный нагреватель для отпуска; 8-ролико-правильное устройство; 9-контрольно- упаковочный стеллаж.
Исходной заготовкой для работы линии служит профилированная в холодном состоянии арматура с периодическим профилем из кремнистых сталей марок 40С2 и 55С2.
Разматывающее устройство должно обеспечивать возможность работы линии с бунтов или катушки. Правильно отрезной станок служит для нарезки прутков арматуры мерной длины 2650±5 мм.
Далее прутки поступают на приемный стеллаж и с помощью проводящих роликов поступают в индукционные нагреватели. Параметры индукционных нагревателей должны обеспечивать возможность достижения необходимых для проведения закалочных операций температур нагрева металла 920 – 960°С. Рекомендуемые параметры: частота 4 – 8 кГц, напряжение 600 – 800В, сила тока 300-330 А. После нагрева арматурные прутки подвергаются закалке под давлением воды 3-4 атм. Параметры закалочного устройства должны обеспечивать формирование структуры мартенсита в сталях. Рекомендуется закалочное устройство с тангенциальной подачей закалочной среды.
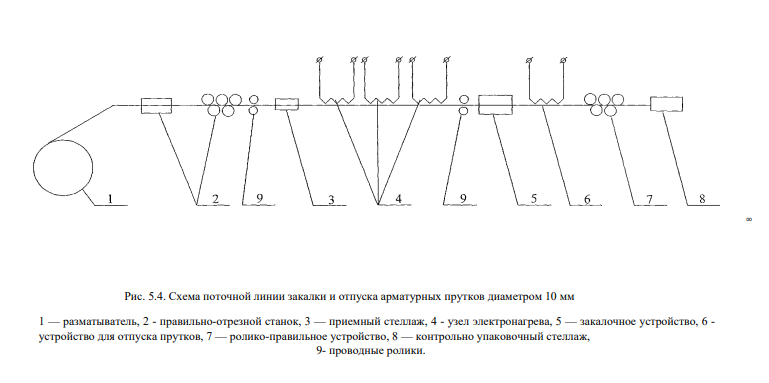
Выводы
- Предложена результативная технологическая схема производства высокопрочной арматуры диаметром 10,0 мм для армирования железобетонных шпал, состоящая из блоков «холодная пластическая деформация» и «термическое упрочнение».
- Разработана методика управления качеством высокопрочной арматуры диаметром 10,0 мм для железобетонных шпал в предлагаемом сочетании технологических блоков.
- Проведена опытно-промышленная апробация разработанных технологических режимов получения арматуры периодического профиля на этапе холодной пластической деформации и финишного термического упрочнения по схеме «закалка-отпуск». Выпущены опытно- промышленные партии термоупрочненной арматуры 10,0 мм по ТУ 14125-704-96 из кремнистых марок стали 40С2 и 55С2. Полученная арматура, с учетом реального разброса показателей качества, отвечает требованиям технических условий.
- Результаты работы использованы при составлении программы технического развития ОАО «ММК-МЕТИЗ» до 2010 г. по организации выпуска новых высоколиквидных видов продукции требуемого уровня качества.
Заключение
- Предложена результативная схема производства высокопрочной арматуры диаметром 10,0 мм для армирования железобетонных шпал, состоящая из технологических блоков холодной пластической деформации и финишного термического упрочнения закалкой с отпуском.
- На основе метода линий скольжения разработано программное обеспе-чение, позволяющее проектировать режимы получения заготовки под про-филирование путем оценки и анализа уровня ее напряженного состояния в зависимости от технологических параметров процесса волочения с учетом специфики финишной термообработки.
- Разработана модель управления геометрическими показателями качества арматуры в процессе холодного профилирования в клети- волоке со смещенными парами валков. На основе модели разработаны калибровки валков и режимы профилирования, обеспечивающие формирование требуемых геометрических показателей качества арматуры.
- Получены математические модели оценки изменения механических свойств арматуры периодического профиля из кремнистых марок стали 40С2 и 55С2 при термическом упрочнении по схеме «закалка-отпуск». На базе моделей определены режимы финишной обработки, обеспечивающие получение требуемого качества готовой арматуры.
- Разработаны технологические режимы изготовления арматуры диаметром 10,0 мм для железобетонных шпал, обеспечивающие формирование заданного уровня качества и повышение конкурентоспособности готовой продукции. На процесс получения холодной пластической деформацией периодического профиля арматуры по ТУ-14-125-704-96 разработана технологическая карта ТК 176-МТ.ПР-112-2006.
- Выпущены опытно-промышленные партии высокопрочной арматуры диаметром 10,0 мм из сталей 40С2 и 55С2. Даны рекомендации по составу оборудования специализированной поточной линии для промышленной peaлизации технологии термического упрочнения высокопрочной арматуры периодического профиля.
- Разработана методика управления качеством высокопрочной арматуры железобетонных шпал диаметром 10,0 мм в гибком сочетании технологических блоков «холодная пластическая деформация»- «термическое упрочнение».
- Результаты работы использованы в программе технического развития ОАО «ММК-МЕТИЗ» до 2010 г. по организации выпуска новых конкурен-тоспособных видов продукции с заданным уровнем качества.
- Полученные в работе теоретические и практические результаты ис-пользуются в учебном процессе ГОУ ВПО «МГТУ им. Г.И. Носова» при подготовке инженеров по специальности 200503 – «Стандартизация и сертификация» и 150106 – «Обработка металлов давлением».
Список литературы
- Ресурсосбережение в метизном производстве: Коллективная моно-графия. Магнитогорск, МГТУ,2001,163С.
- A.A. Штер, Ю.Н. Попов. Волочение фасонных профилей в волоках со смещенными парами роликов // Труды четвертого конгресса прокатчиков., М.: Черметинформация, 2002.- Т.2.-С 186-187.
- И.Д. Костогрызов., B.C. Славин. Волочение фасонных профилей вы-сокой точности в клетях-волоках с многовалковым калибром // Производство проката.-№7.- 1999.-С.23-26.
- Гулько В.И. Войцеховский В.А. Производство профилей и проволоки в роликовых волоках.- Ижевск, 1989, 132С.
- Лавренчик В.Н. Постановка физического эксперимента и статистиче-ская обработка его результатов.- М.: Энергоатомиздат, 1986, 212С.
- Чукин В.В., Корчунов А.Г., Челищев В.Н. Отработка технологических режимов производства высокопрочной арматуры для железобетонных шпал// Обработка сплошных и слоистых материалов. Вып. 30: Межвуз. сб. на- уч.тр./Под ред. Г.С. Гуна.- Магнитогорск: МГТУ, 2004.-С. 115-118.
- Спиридонов A.A.. Планирование эксперимента при исследовании технологических процессов.- М.: Машиностроение, 1981, 184 С.
- Попов A.A., Попова А.Е. Справочник термиста. Машгиз. ГНТИ. Ма-шиностроительная литература. М.; Свердловск, 1961. 300 С.
- Кривощапов В.В. Технология производства пружинных клемм. Моно-графия. Магнитогорск:МДП, 1999, 176С.
- Носов А.Д., Носков Е.П., Вершигора С.М , Рудаков В.П, Корчунов А.Г., Челищев В.Н Исследование вариантов технологических про-цессов производства высокопрочной стержневой арматуры для железобетонных шпал// Вестник МГТУ им.Г.И. Носова,- 2005.-№ 3. – С.80-83.
- Лахтин Ю.М. Новые стали и сплавы в машиностроении. М.: Машино-строение, 1978, 346С.
- Белалов Х.Н., Клековкина H.A. и др. Производство стальной проволо-ки. Монография, Магнитогорск, 2005, 543С.
- Шахпазов Х.С., Недовизий И.Н., Ориничев В.И. и др. Производство метизов. М.: Металлургия, 1972,472С.
- Хина М.Л. Закалочные среды на основе водорастворимых полимеров. Металловедение и термическая обработка, № 8, 1978,.-С-26-31.
- Малинкина Е.И. Образование трещин при термической обработке стальных изделий. М.: Машиностроение, 1965, 345С.
- Корчунов А.Г., Чукин В.В. Челищев В.Н. и др. Оценка формирова¬ния качества высокопрочной стержневой арматуры для железобетонных шпал в технологиях термического и деформационного упрочнения// Производство проката.- №10.- 2006 .-С 19-21.
- Корчунов А.Г., Чукин В.В.,Челищев В.Н. Анализ возможности полу-чения высокопрочной арматуры диаметром 10,0 мм для железобетонных шпал деформационным упрочнением //Обработка сплошных и слоистых материалов: Межвуз. междунар. сб. науч.тр,- Магнитогорск:МГТУ, 2005.-С.94-98.
- Контактное трение в процессах обработки металлов давлением / Леванов А.Н., Колмогоров В.Л., Буркин С.П., и др.- М.: Металлургия, 1976, 342С.