Сейчас ваша корзина пуста!
История совершенствования химического состава и способов термической обработки рельсов
Цикл статей:
Глава 1 – Развитие конструкции железнодорожных рельсов, их стыковых соединений и технологий обработки
Глава 2 – Поставка рельсов для строительства железных дорог
Глава 3 – История совершенствования химического состава и способов термической обработки рельсов
Использование передовых технологий для изготовлений металлических рельсов в XVIII – первой половине XIX вв
Во второй половине XVIII в. для продления срока службы, повышения стойкости лежневых дорог и снижения усилий для перемещения повозок стали использовать металлические накладки, которые изготавливали из остатков выплавленного металла, независимо от его качества. Таким металлом оказался железоуглеродистый сплав (чугун), который подходил как по эксплуатационным свойствам, так и по цене (см. главу 1).
В 1767 г. из чугуна получали отливки в виде пластин, которые закрепляли на продольных брусьях лежневой дороги [80]. К этому времени технология получения отливок из чугуна была известна и, в какой-то степени, отработана для получения простейших изделий.
В 1708 г. технология получения отливок из чугуна в песчаные формы была запатентована английским промышленником А.Дерби. В 1709г. он арендовал старую домну в Коулброукделе и усовершенствовал способ изготовления кокса. В 1713 г. А. Дерби заменил в доменной плавке часть древесного угля каменным (коксом). Благодаря его экспериментам уголь стал завоёвывать позиции одного из основных источников энергии. Наследники А. Дерби продолжили дело своего предка, освоив технологию выплавки из железной руды. В 1735 г. его сын, А. Дерби второй, внедрил доменную плавку на коксе. Производство железа стало массовым, а чугун стал применяться в разных областях [80].
Эксплуатация лежневых дорог с металлическими накладками показала, что целесообразно использовать не накладки на деревянные брёвна, а изготавливать цельнометаллические рельсы. Такие рельсы оказались более выгодными и удобными при эксплуатации.
В ходе изменения условий эксплуатации и повышения стойкости лежневых дорог потребовалось усовершенствовать профиль цельнометаллических лежней.
Изменение профиля требовало разработки соответствующей технологии для получения отливки нужной формы и качества. Наиболее перспективными и удобными в эксплуатации являлись грибовидные рельсы (см. рисунок 7).
Совершенствование лежневых дорог, путём замены деревянных брусьев на металлические, позволило использовать на них конную тягу.
В процессе применения паровозной тяги на вновь построенных железных дорогах были повсеместно внедрены рельсы грибовидной формы.
Рельсы из чугуна можно было получать только отливкой, поэтому их длина составляла 1,5 – 2 м. Чугун – высоко-хрупкий материал, поэтому часто бывали отколы и разрушения у рельсов.
Развитие металлургической промышленности дало возможность заменить хрупкий чугун более пластичным сплавом – сталью. В свою очередь, изобретение Дж. Биркиншоу способа профильной прокатки железа позволило в 1820 г. увеличить длину рельсов примерно в 4 раза [89]. В этот период стали проводиться работы, связанные с подбором оптимального поперечного сечения рельсов. Каждый из предлагаемых профилей требовал разработки новой технологии. Это было связано с тем, что высокие нагрузки, действовавшие на рельсы, приводили к их разрушению. Эксплуатация показывала, что чугунные рельсы не могли конкурировать с более пластичными стальными рельсами.
К середине XIX в. остро вставал вопрос о повышении качества рельсов, что потребовало дальнейшего совершенствования металлургического производства и технологии изготовления рельсов. В 1864 г. на Нижне-Салдинском заводе впервые была осуществлена объёмная закалка рельсов из пудлингового железа в воду [35, с. 107-155]. Однако результаты эксперимента по повышению механических характеристик не известны.
Пудлинговое железо обладает низким качеством и не склонно к образованию закалочных структур, но имеет хорошие литейные свойства.
Таким образом, работы по выявлению оптимального химического состава металла для изготовления рельсов и повышения его эксплуатационных характеристик начались с появлением рельсовых дорог.
Разработка технологии производства и термообработки рельсов в период с 1866 г. до начала XX в
Данный период характеризуется большим разнообразием типов рельсов (Приложение А), изготавливавшихся заводами по различным технологиям из чугуна, пудлингованного железа и стали неодинакового химического состава. Целесообразность применения стальных рельсов, как таковых, широко обсуждалась специалистами того времени [17, 175].
Такое разнообразие типов рельсов затрудняло техническое обслуживание и эксплуатацию железнодорожного пути. Поэтому было принято решение о сокращении их количества, а также об отработке единой технологии изготовления и подборе оптимального химического состава. Для этой цели МПС был разработан план мероприятий.
Технические условия приёма и испытаний рельсов были впервые разработаны и утверждены министром путей сообщения в 1874 г. [10]. В 1878 и в 1887 гг. технические условия подверглись корректировке. Исследования рельсов, принятых по этим техническим условиям показали преимущества твёрдых рельсов перед мягкими [170, с. 8-9]. В 1894 г. в целях повышения качества поставляемых рельсов были разработаны и утверждены «Нормальные технические условия испытания и приёмки рельсов», которыми вводилось испытание стали на разрыв, вместо «испытания статической усиленной нагрузкой»[1]. В 1897 г., в соответствии с внесёнными в них изменениями были отменены химические анализы на углерод в заводских и правительственных лабораториях, так как несоответствие химического состава не являлось основанием для выбраковки рельсов [182, с. 5-7].
В 1899 г. были приняты новые технические условия, регламентировавшие размеры рельсов, вес, клейма, «наружный вид», испытания, химический состав, ограниченный только содержанием фосфора [170, с. 8-9; 182, с. 73-81].
В конце XIX – начале XX вв. при Инженерном совете МПС была образована Специальная рельсовая комиссия, во главе с Действительным статским советником Л.О. Николаи, которая занималась изучением влияния химического состава рельсовой стали и условий проката болванок на повышение качества рельсов [183, с. 100].
С 1899 по 1906 гг. Рельсовой комиссией проведено более 30 заседаний. На основании данных, полученных от металлургических заводов и с железных дорог, Рельсовая комиссия пришла к выводу о влиянии химического состава рельсовой стали на механические свойства рельсов [183, с. 101].
Вместе с тем, сравнение качества и способов испытаний отечественных и зарубежных рельсов проводилось без унификации параметров. Поскольку только к отечественным рельсам предъявлялись требования повышенной ударной вязкости при низких температурах, российские рельсы изготавливали более «мягкими», чем аналогичные рельсы иностранного производства. Ошибочно считалось, что меньшая твёрдость должна была снизить хрупкость рельсов при низких температурах.
Однако выявить оптимальный химический состав рельсовой стали не представлялось возможным. В данных, полученных с железных дорог, не была выявлена какая-либо определённая зависимость, т.к. сравнивались лучшие иностранные и худшие отечественные рельсы. Исследуемые рельсы разных типов эксплуатировались на участках пути с различным климатом, интенсивностью движения и весом поездов [92, 95, 186].
Таким образом, были сформулированы лишь общие требования, в соответствии с которыми ограничивалось только содержание фосфора не более 0,10 %. Остальные примеси являлись допустимыми при соответствии остальных условий приёма рельсов. Такой подход мог привести к использованию на железных дорогах низкокачественной продукции.
По решению Рельсовой комиссии для выработки единых норм производства рельсов были проведены опросы инженеров «отделов по испытанию и освидетельствованию» заказов МПС [183, с. 101].
Для этой цели была разработана анкета, включавшая 8 вопросов, на которые должны были ответить специалисты-практики:
- какой обработке подвергаются болванки перед прокаткой;
- продолжительность нагрева болванки перед прокаткой или продолжительность охлаждения болванки, если прокатка совершается, не дожидаясь полного её охлаждения, то при каких условиях происходит охлаждение отлитой болванки до температуры, при которой начинается прокатка;
- продолжительность прокатки;
- размеры прокатываемой болванки;
- как охлаждаются прокатанные рельсы;
- тип и сила прокатных станов;
- какой металл идёт для отливки болванок и, если мартеновский, то основной или кислый;
- принимаются ли какие-нибудь меры против пузыристости стали при отливке болванок и, если принимаются, то какие именно [ 186].
Наиболее подробные ответы, полученные с предприятий, приведены в Приложении В.
К сожалению, не все заводы дали исчерпывающие ответы на поставленные вопросы. Для примера рассмотрены ответы специалистов четырёх ведущих заводов: Нижне-Салдинского, Мариупольского, Новороссийского и «ответ Инженера1 Уральских заводов».
На вопрос о наличии предварительной прокатки для получения болванки определённых геометрических размеров перед поступлением её на рельсопрокатный стан положительный ответ был получен только с Нижне-Салдинского завода и от Инженера1 Уральских заводов.
‘ Пишется с большой буквы, как указано в [186].
На вопрос о продолжительности нагрева болванки перед прокаткой участники анкетирования ответили, что выполняется предварительный подогрев, без указания температур, до которых нагревают болванки. Вместо этого специалисты дали информацию о продолжительности нагрева без указания мощности печи. Это приводило к различным условиям нагрева и получению неодинаковой температуры перед началом прокатки, поэтому окончательная структура и механические свойства металла готового рельса могли получаться разными.
По поводу продолжительности прокатки были получены разноречивые ответы, которые привязывались к собственным технологиям заводов. Даже ответы специалистов Донецкого и Мариупольского заводов, у которых продолжительность прокатки оказалась близкой (4-5 и 4,5-5,5 минут, соответственно) указали различные условия: Донецкий – для болванки весом 110 пудов, а Мариупольский – в зависимости от количества пара в котлах.
Размеры прокатываемой болванки на каждом заводе зависели от размера изложницы, способа производства, а также от расчётной длины рельса (одинарная, двойная или тройная).
Охлаждение рельсов на заводах происходило на стелюгах в закрытых помещениях в течение 1 ч. 15 мин. – 2 ч. до температуры окружающего воздуха. В ответе специалиста Мариупольского завода было указано, что «при последних проходах в стане рельсы отчасти охлаждаются водой, обильно поливающей валки». Такое ускоренное охлаждение могло приводить к образованию закалочных структур в поверхностных слоях рельса, что повышало их твёрдость и прочность, но снижало пластичность.
Типы прокатных станов и силовые установки на заводах отличались друг от друга, что требовало особой технологии каждого изготовителя.
Для отливок использовался металл, полученный бессемеровским, мартеновским и томасовским способами. Футеровка конверторов использовалась кислая и основная, поэтому химический состав металла рельсов мог отличаться друг от друга, что, в свою очередь, меняло его свойства.
Нижне-Салдинский и Уральские заводы раскисляли металл болванки алюминием в количестве один золотник на один пуд стали; Новороссийский завод раскислял ферроманганом[2], Мариупольский – ферросилицием и ферроманганом, а Донецкий никаких мер для раскисления металла не принимал. Поэтому заводы получали сталь различной степени раскисленности и, следовательно, количество пор в болванках отличалось.
Таким образом, анализ анкет показал, что качество стали , рельсопрокатные станы и технология прокатного производства рельсоделательных заводов отличались друг от друга. На железных дорогах использовались также различные типы рельсов (см. параграф 1.4). Отсутствие специального полигона для проведения исследований не позволяло оперативно выбрать конфигурацию, геометрические параметры, материал, оборудование и технологии изготовления рельсов.
Таким образом, к концу XIX в. в России, впервые в мире, были разработаны нормативные документы на рельсовую продукцию, эквивалентные современным стандартам.
[1] Точных цифр нет.
[2] Для рельсов весом 30-35 кг/пог.м.
Применение стандартов и технологий на изготовление рельсовой стали в первой половине XX в
Разработка стандартов на химический состав рельсовой стали
К началу XX в. в ходе многолетней эксплуатации, конфигурация и материал, из которого следовало изготавливать железнодорожные рельсы, в основном были определены. Рельс – широкоподошвенный, с большой головкой и высокой шейкой. Материал – сталь, с необходимыми свойствами. Вместе с тем, на эксплуатационные характеристики рельсов оказывают большое влияние их химический состав и технология выплавки. В связи с этим, по мере повышения качества получаемых сталей, необходимо было пересматривать технические условия на их химический состав и прочностные характеристики. До введения в 1932 г. в действие
ОСТ 4118-1932 принимались технические условия в 1908, 1914 и 1924 гг., причём последним был присвоен регистрационный номер (343-ТУ-24) [170, с. 9; 188, с. 128]. В разработанном ОСТ 4118-1932 были установлены нормы содержания основных элементов химического состава рельсовой стали и заменена прочностная характеристика предела упругости на предел прочности. В данном стандарте предъявлялись более высокие требования к качеству используемой рельсовой стали, согласно которому могли изготавливаться рельсы первого сорта, с наименьшим пределом прочности 70 кгс/мм и рельсы второго сорта – 55 кгс/мм . Во введённом ОСТ 4118-1932 регламентировался химический состав в зависимости от способа выплавки стали (таблица 18) [188, с. 129], а также проведения испытаний на растяжение: для мартеновской стали – от каждой плавки, а бессемеровской и томасовской – от каждой двенадцатой плавки; копровые испытания осуществлялись поплавочно. Это было необходимо из-за нестабильности получавшегося химического состава [183, с. 103].
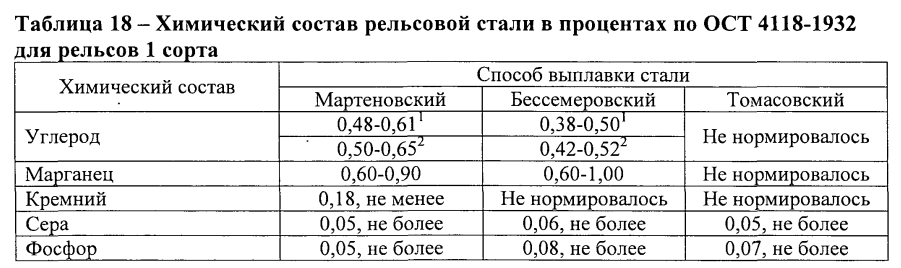
На начало введения ОСТ 4118-1932 химический состав мартеновских и особенно бессемеровских рельсовых сталей не соответствовал выдвигаемым требованиям. Томасовские рельсы, изготавливаемые Керченским металлургическим заводом, в ещё большей мере не соответствовали требованиям ОСТ 4118-1932.
Свыше 80 % плавок не удовлетворяло требованиям стандарта из-за чрезмерного содержания вредных примесей – серы и фосфора. Подавляющее болыпинст- во рельсов не удовлетворяло требованиям стандарта и по состоянию поверхности из-за большого количества плен, раковин и волосовин [183, с. 103].
Рельсы, изготовленные из томасовской стали, сминались, а при отрицательных температурах часто ломались. В связи с этим в 1933 г. производство рельсов на Керченском заводе было прекращено [188, с. 134].
В соответствии с нормами стандарта для рельсовых сталей мартеновского и бессемеровского производства требовалось повысить содержание углерода и уменьшить содержание вредных примесей – серы и фосфора. В мартеновских сталях повышение содержания углерода и снижение содержания фосфора было осуществлено достаточно просто. Труднее было выполнить условия по пределам, предусмотренным стандартом, для других элементов, и уменьшить разброс для разных плавок. Непросто оказалось понизить содержание фосфора в бессемеровской стали, а без его понижения невозможно было повысить содержание углерода [189, с. 170-174]. Возникали трудности и по снижению содержания серы. В связи с этим, на период освоения стандарта, часть рельсов принимали по старым техническим условиям НКПС-343 ТУ-24. Это позволило сначала освоить льготные, а затем постоянные, более жёсткие нормы стандарта ОСТ 4118-1932 [188, с. 134].
К концу 1935 г. практически вся рельсовая продукция заводов стала удовлетворять требованиям ОСТ 4118-1932, и льготные нормы были отменены [188, с. 134-135].
На Кузнецком металлургическом комбинате им. Сталина, выпускавшем рельсы из мартеновской стали, рельсы изготавливались в полном соответствии с требованиями ОСТ 4118-1932 после ввода в эксплуатацию рельсопрокатного цеха.
За период выпуска рельсов в соответствии с ОСТ 4118-1932 в него были внесены необходимые корректировки [183, с. 103].
Введение ОСТ 4118-1932 позволило значительно улучшить качество выпускаемых рельсов [188, с. 135-141]. Например, в первой половине 1941 г. рельсы из мартеновской и бессемеровской стали, изготавливаемые на всех заводах, удовлетворяли требованиям ОСТ 4118-1932. На Кузнецком металлургическом комбинате выход рельсов I сорта составлял около 88 %, на заводах Юга – около 85 %. Остальные 12-15 % рельсов распределялись между вторым сортом и браком приблизительно поровну [183, с. 103-104].
В соответствии с ОСТ 4118-1932 допускалось наличие некоторых дефектов: ликвации, волосовины, закат и трещины в подошве рельса глубиной до 1 мм, а для рельсов II сорта – до 3 мм; флокены и др. Поэтому в 1943 г. А.И. Скаковым была начата работа по проектированию новых технических условий на материалы для рельсов. В 1930-е гг. впервые в мире в СССР зародилась рельсовая дефектоскопия (сначала магнитная), использование которой позволило совершенствовать технологии и качество проката рельсов [183, с. 105; 184, 185].
Таким образом, в первой половине XX в. процесс регламентации распространялся на технические условия, в т.ч. химический состав рельсовой стали, который шёл в направлении повышения содержания углерода и уменьшении вредных примесей – серы и фосфора в зависимости от способов выплавки (мартеновского, бессемеровского, томасовского), а также повышения прочностных характеристик, а применение дефектоскопии позволило исключить попадание брака в путь.
Организация упрочняющей термической обработки рельсов
П.П. Аносов и Д.К. Чернов, занимавшиеся исследованием прочности материала, научно обосновали, что при быстром охлаждении стали с определённых температур металл приобретает повышенные значения прочности и твёрдости, что улучшает его эксплуатационные качества. В связи с этим в различных странах начали подбирать режимы термической обработки для рельсовой стали. В зависимости от технологического процесса проведения такой термической обработки на рельсовой стали можно получить только закалённый поверхностный слой или подвергать закалке весь объём рельса. В первой половине XX в. были разработаны различные варианты закалки, основные из которых приведены в таблице 19 [35, с 107-155].
Первые попытки термической обработки рельсов были проведены в Англии. В дальнейшем такие работы велись в Швеции, Франции, Германии и СССР [183, с. 105-106].
До середины 1930-х гг. все виды термического упрочнения проводились с прокатного нагрева. В 1937 г. В.П. Вологдиным была осуществлена поверхностная закалка концов рельсов с использованием токов высокой частоты (ТВЧ), позволившая получить твёрдый закалённый поверхностный слой и вязкую, пластичную середину. В дальнейшем нагрев рельсов под термическую обработку осуществлялся путём дополнительного специального подогрева разными методами.
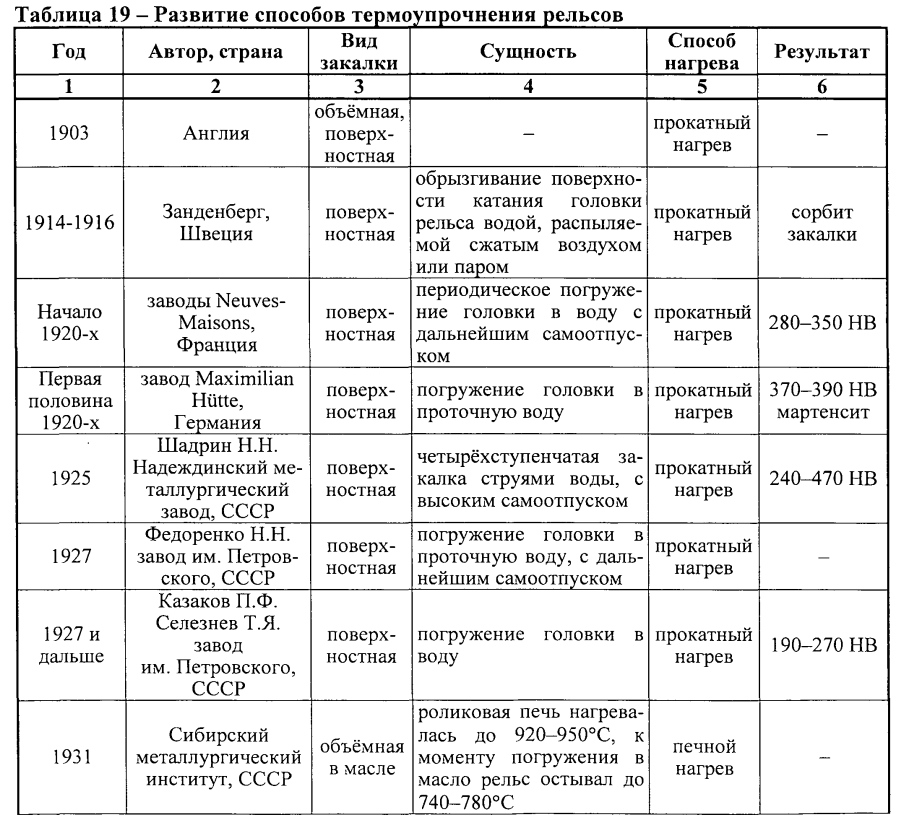
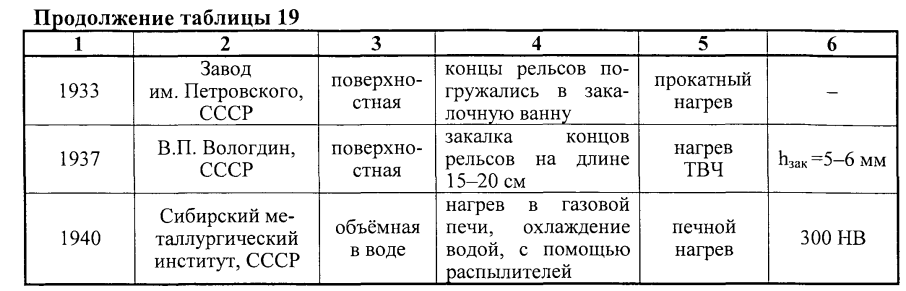
Таким образом, в первой половине XX в. все виды термической обработки сводились, в основном, к поверхностной закалке головки рельса и лишь в середине века было уделено внимание дополнительной закалке концов рельсов. Такая термическая обработка позволяла повысить вместе с механическими свойствами металла и эксплуатационные характеристики, в первую очередь, износостойкость, что сокращало расход рельсовой стали, и, соответственно, объёмы замены рельсов в пути по износу.
Совершенствование государственных стандартов на изготовление рельсов в период с 1947 г. до начала XXI в
Во второй половине XX в. восстановленные после Великой Отечественной войны железные дороги перешли на более высокий уровень развития. Вместо паровозов на железнодорожном транспорте стали применять более мощные тепловозы и электровозы, с помощью которых формировались и перевозились более тяжеловесные поезда массой до 12 тыс. т. Одновременно увеличивались скорости движения пассажирских и грузовых поездов. Всё это определяло изменение динамики воздействия на путь и повышение на него нагрузки.
В связи с этим в данный период шло обновление железнодорожного пути и, в том числе, рельсов. У них менялся химический состав, механические свойства, технология выплавки металла, его прокатка и последующая термическая обработка, что в целом позволяло удовлетворить эксплуатационные требования, предъявляемые к рельсам.
3.4.1. Внедрение новой технологии производства рельсов Начиная с 1947 г., все рельсы изготавливались только в соответствии с государственными стандартами [183, с. 106].
В 1948 г. было завершено проектирование и создан стандарт – ГОСТ 422448, на материалы для изготовления железнодорожных рельсов широкой колеи весом до 45 кг/пог. м. В соответствии с новым стандартом на рельсы, вводимым в действие с 1949 г., в отличие от ОСТ 4118-1932 требовалось полное раскисление стали, удаление усадочной раковины и ликвационной зоны, уменьшение допускаемой глубины волосовин и закатов в подошве с 1 до 0,5 мм и ряд других, более жёстких требований. Всё это способствовало снижению вероятности попадания в путь рельсов с металлургическими дефектами, опасными для эксплуатации. При этом химический состав рельсовой стали лишь немногим отличался от требований ОСТ 4118-1932 (таблица 20) [188, с. 145].
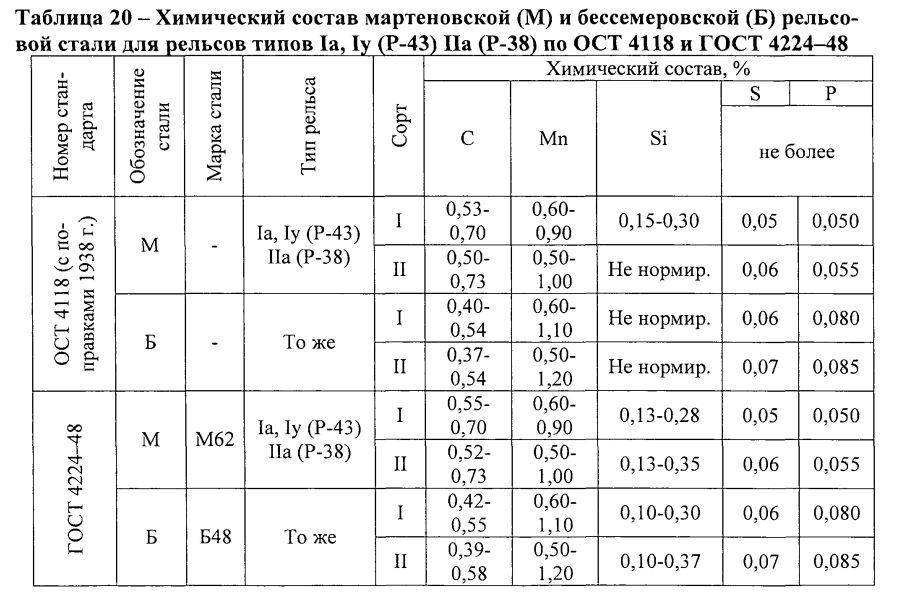
Из таблицы 20 видно, что содержание марганца, серы и фосфора осталось без изменения. Содержание углерода незначительно увеличено, за счёт повышения в мартеновской стали нижнего предела содержания углерода на 0,02 %, и в бессемеровских – нижнего предела на 0,02 % и верхнего предела на 0,01 %. Более значительное повышение содержания углерода было не целесообразно, так как при существовавшей тогда технологии возникала опасность образования флокенов в мартеновской стали и опасность повышения хрупкости и хладноломкости бессемеровской стали.
Для полного раскисления стали и удаления ликвационной зоны в соответствии с требованиями нового стандарта было необходимо установить нормы содержания кремния в бессемеровской стали. Минимальный предел прочности в мартеновских сталях был повышен с 70 до 72 кгс/мм [188, с. 144].
Выполнение требований ГОСТ 4224-48 для мартеновской стали не представляло трудностей для заводов. Для раскисления бессемеровской стали, в процессе её изготовления было предложено использовать ферросилиций, что несколько повысило её качество. Однако это не устранило основного недостатка – хрупкости и хладноломкости рельсовой стали, а, следовательно, не повысило её износостойкость и не уменьшило смятие. В тот период невозможно было повысить содержание углерода в бессемеровской рельсовой стали из-за её высокой хрупкости.
Во второй половине XX в. в СССР для улучшения качества бессемеровской рельсовой стали уменьшалось содержание фосфора, улучшалось раскисление, и азот связывался титаном. В зарубежных странах, например, в США и Англии, такие попытки по улучшению бессемеровской стали были прекращены ещё в начале XX в., и производство рельсов из бессемеровской стали прекратилось.
По свидетельству A.A. Байкова и В.Е. Грум-Гржимайло, рельсы, изготовленные из бессемеровской стали, выплавленной по «старому русскому» способу бессемерования, были отличного качества. Данный способ отличался от зарубежных тем, что продувка кислородом останавливалась на заданном уровне высокого содержания углерода [188, с. 149].
До 1977 г. были разработаны и внедрены ГОСТы на разные типы рельсов, использовавшихся в то время (см. таблицу 10). С 1 июля 1981 г. вступил в действие ГОСТ 24182-80, который объединил ранее действовавшие ГОСТ 8160-63, ГОСТ 6944-63, ГОСТ 7174-75 и ГОСТ 8161-75, так как за основные типы рельсов были приняты железнодорожные рельсы из мартеновской стали типов Р75, Р65 и Р50 для широкой колеи.
К 1985 г. был разработан международный стандарт на рельсы для стран социалистического лагеря СТ СЭВ 4983-85 на основании созданного ГОСТ 2418280 [190],
Производили рельсы двух групп. Рельсы первой группы изготавливали из спокойной мартеновской стали, раскисленной в ковше комплексными раскислителями без применения алюминия или других раскислителей, образующих в стали вредные строчечные неметаллические включения. Рельсы второй группы изготавливали из спокойной мартеновской стали, раскисленной алюминием или марганец-алюминиевым сплавом. Химический состав сталей для рельсов первой и второй групп должен был соответствовать нормам, указанным в таблице 21 [190].
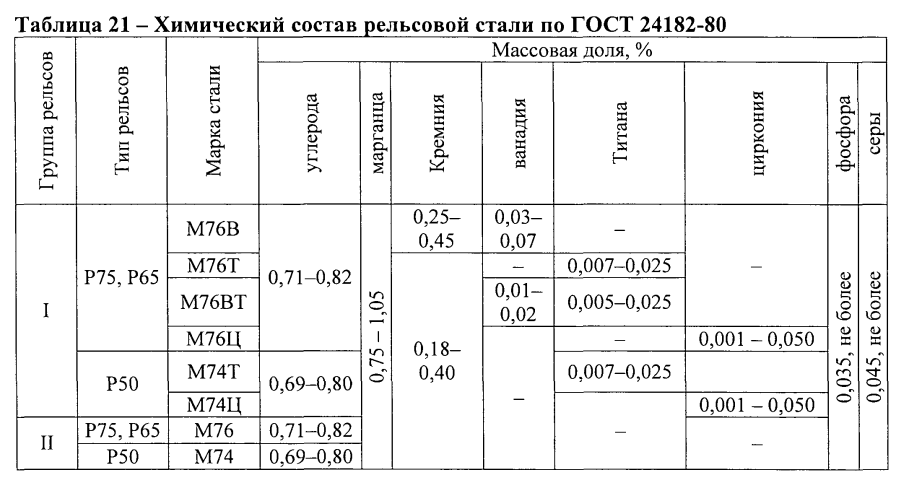
Рельсы, изготовленные из стали марки М76В, относят к рельсам с ванадием; из сталей марок М76Т, М76МТ – к рельсам с титаном; из сталей марки М76Ц – к рельсам с цирконием. По ГОСТ 24182-80 допускалось производство рельсов типа Р50 из кислородно-конверторной стали, при этом в обозначении марки стали ставилась буква К, вместо буквы М. Механические свойства сталей М74 и М76 для рельсов типов Р75, Р65 и Р50 должны были соответствовать нормам, указанным в таблице 22.

В настоящее время железнодорожные рельсы изготавливаются в соответствии с ГОСТ Р 51685-2000 [158]. В данный стандарт, по сравнению с ГОСТ 2418280, в обозначение марки стали введена буква Э, обозначающая способ выплавки стали в электропечах. В маркировке стали буквы Ф, С, X, Т обозначают легирующие элементы ванадий, кремний, хром и титан, соответственно. Химический состав рельсовых сталей должен соответствовать данным, приведённым в таблице 23.
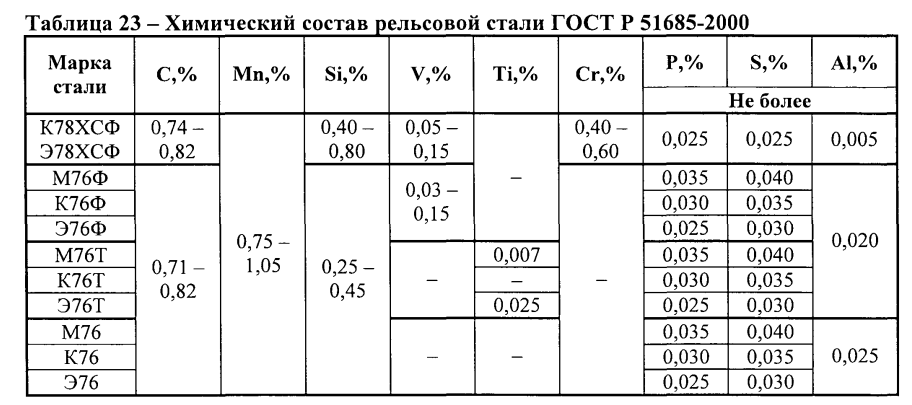
Технология изготовления рельсов должна гарантировать отсутствие в них флокенов, а также местных неметаллических включений (глинозёма, карбидов и нитридов титана или глинозёма, сцементованного силикатами), вытянутых вдоль направления прокатки в виде дорожек – строчек длиной не более 2 мм для рельсов первой группы, и длиной более 8 мм – для рельсов второй группы [158, 191]. Поверхность рельса на его концах должна быть подвергнута закалке с прокатного нагрева или индукционного нагрева токами высокой частоты.
Таким образом, начиная с послевоенного периода и до начала XXI в. отечественными и зарубежными учёными проводились всесторонние исследования, как рельсовой стали, так и самих рельсов. На основании этих работ совершенствовались стандарты на химический состав, механические свойства и геометрические параметры рельсов в направлении устранения хрупкости и хладноломкости и повышения предела прочности рельсовой стали.
Основные требования, предъявляемые к рельсам по условиям современной и перспективной эксплуатации
Железнодорожный путь работает в сложнейших условиях, определяющихся динамическими воздействиями на него подвижного состава и влиянием природно-климатических явлений и факторов.
Основными параметрами, обусловливающими, в первую очередь, динамику взаимодействия пути и подвижного состава, то есть уровень силовых воздействий и интенсивность его деформаций, являются скорости движения поездов, грузонапряжённость брутто и нагрузки на ось. Указанные параметры, действующие на путь от подвижного состава, существенно дополняются в его эксплуатации воздействиями суточных и годовых изменений температур и влажности, атмосферных осадков в виде дождя и снега, промораживанием балласта и земляного полотна, а также влиянием инженерно-геологических, гидрологических условий, сейсмичности и др.
Воздействие колёс подвижного состава, в зависимости от статической и динамической нагрузок на ось в общем виде может быть представлено следующим выражением [53]:
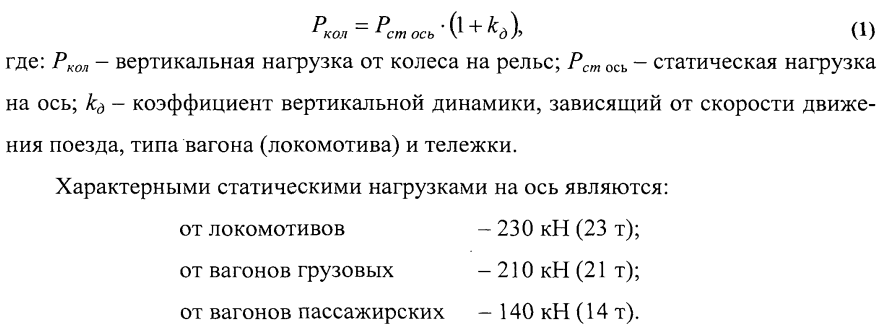
Среднестатистические нагрузки на ось современных грузовых вагонов с учётом их реальной загрузки составляют 195-198 кН/ось (расчётная нагрузка может доходить до 250-270 кН/ось). Действующими «Правилами технической эксплуатации железных дорог Российской Федерации» (ПТЭ) [192, 193] установлены следующие наибольшие скорости движения поездов:
пассажирских -140 км/ч;
рефрижераторных – 120 км/ч;
грузовых – 90 км/ч.
Как видно из вышеуказанного источника, сочетания осевых нагрузок и скоростей движения, в первую очередь, определяют динамику воздействий на путь. Интенсивность эксплуатации пути, его работы определяется количеством динамических воздействий за единицу времени. Параметром, характеризующим загруженность, интенсивность работы пути является грузонапряжённость. В физическом смысле грузонапряжённость — это грузооборот, отнесённый к одному километру пути за год:

В настоящее время средний вес грузового поезда составляет порядка 4000 т брутто. Нужно иметь в виду также, что с середины 1980-х гг. на отдельных на-правлениях обращаются поезда повышенного веса (до 9,0 тыс. т), поезда грузовые повышенной длины (350 осей и более), соединённые (из двух и более сцепленных между собой с действующими локомотивами в голове каждого поезда), грузовые тяжеловесные (весом, превышающим на 100 т и более установленную графиком движения весовую норму на участке следования). Веса пассажирских поездов со-ставляют 0,8-1,2 тыс. т. При этом поезда, имеющие в составе 20 и более вагонов, в соответствии с ПТЭ, называются поездами пассажирскими длинно-составными. Веса пригородных поездов составляют порядка 500-600 т.
С 2004 г. техническая оснащённость инфраструктуры ОАО «РЖД» не пре¬терпела существенных изменений. Между тем, нагрузка на инфраструктуру в этот период существенно росла в связи с увеличением объёмов и дальности перевозок.
Так, за период с 2004 г. густота движения грузов по сети выросла более чем на 17% [195, с. 111-112].
Основные эксплуатационные параметры, определяемые движением поездов, будут постоянно возрастать. Перспективы их роста определены долгосрочной программой «Стратегия развития железнодорожного транспорта в Российской Федерации до 2030 года» [194]. Предусмотрены два этапа развития:
• первый этап 2008-2015 гг. – коренная модернизация производственной базы отрасли, которая позволит снять все ограничения в пропускных и провоз¬ных способностях и обеспечить растущий спрос на грузовые и пассажир¬ские перевозки;
• второй этап 2016-2030 гг. – динамичное расширение железнодорожной сети страны, направленное на создание инфраструктурных условий для сущест-венного роста показателей экономики.
В результате реализации Стратегии по максимальному (оптимистичному) ва-рианту к 2030 г. должно быть:
• построено более 20,0 тыс. км новых железнодорожных путей;
• сооружена высокоскоростная (с V до 350 км/ч) линия Санкт-Петербург- Москва, обеспечено скоростное движение (с умах =160 км/ч и выше) на по¬лигоне 10880 км;
• повышены среднесетевые маршрутные скорости с 56,3 км/ч (2006 г.) до 61¬66 км/ч в 2030 г.;
• организовано тяжеловесное движение поездов (6,0-12,0 тыс. т) на полигоне протяжением 13,8 тыс. км;
• обеспечен рост к 2030 г. (по сравнению с 2006 г.): грузооборота в 1,7 раза – до 3300,0 млрд. ткм; пассажирооборота в 1,3 раза – до 231,0 млрд. пасс.км [194].
В Стратегии инновационного развития ОАО «Российские железные дороги» на период до 2015 года (Белой книге ОАО «РЖД») прогнозируемый рост указан¬ных показателей одновременно должен сопровождаться повышением осевых (до 25 тс) и погонных (до 10,5 т/м) нагрузок от подвижного состава, что существен¬ным образом повлияет на эксплуатационные условия и усложнение работы же¬лезнодорожного пути, в 2012-2015 гг. [1, с. 17].
В соответствии с Программой инновационного развития ОАО «РЖД» преду-смотрено применение рельсов с ресурсом до 1,5 млрд. ткм брутто и оптимальным профилем, а также рельсовых скреплений для высокоскоростного и тяжеловесно¬го движения на ряде полигонов сети в 2011-2015 гг.; освоение отечественной промышленностью производства рельсов длиною 100 м и укладка рельсовых пле¬тей длиной 800 м; производство рельсовых скреплений для высокоскоростного и тяжеловесного движения; применение при ремонтах пути малообслуживаемых рельсовых скреплений, рельсовых плетей, бесстыкового пути, сваренных из рель¬сов длиной 100 м, кубовидного щебня повышенной прочности – в 2014-2015 гг. [195].
В Государственной программе Российской Федерации «Развитие транспорт¬ной системы (2010-2020) на 2013 – 2020 годы» скорректированы данные по же-лезнодорожному транспорту, в том числе планируется ввести в эксплуатацию 2,6 тыс. км железнодорожных линий и 1,9 тыс. км дополнительных главных пу¬тей, электрифицировать 2,4 тыс. км линий; долю протяжённости проблемных в отношении пропускной способности железнодорожных линий, составивших на начало 2012 г. более 7,6 тыс. км, сократить на 35 %. Тем самым скорость доставки грузовых отправок достигнет 309,1 км в сутки. Инвестиционной программой на развитие и модернизацию железнодорожного транспорта предусмотрено выде¬лить 3,8 млрд. руб. [5, с. 13, 23, 37-38, 184].
В связи с этим путевому комплексу предстоит решать сложные проблемы дальнейшего совершенствования конструкций пути и системы его технического обслуживания. Важнейшей составляющей системы, обеспечивающей соответст¬вие технического состояния пути параметрам перевозочного процесса, является классификация путей в зависимости от эксплуатационных условий, в частности, от сочетаний скоростей движения поездов и грузонапряжённости.
Типизация верхнего строения пути на дорогах СССР, с основным критерием – грузонапряжённость, впервые была введена в 1958 г. и доработана к 1964 г. Для главных путей она включала в себя три типа – нормальный, тяжёлый и особо тя-
жёлый. Г.М. Шахунянцем была также разработана методика для определения ти¬па пути приближенным способом [196, с. 10-11].
В начале XXI в. применялась классификация, представленная в таблицах 24 и 25 [53, с. 103]:
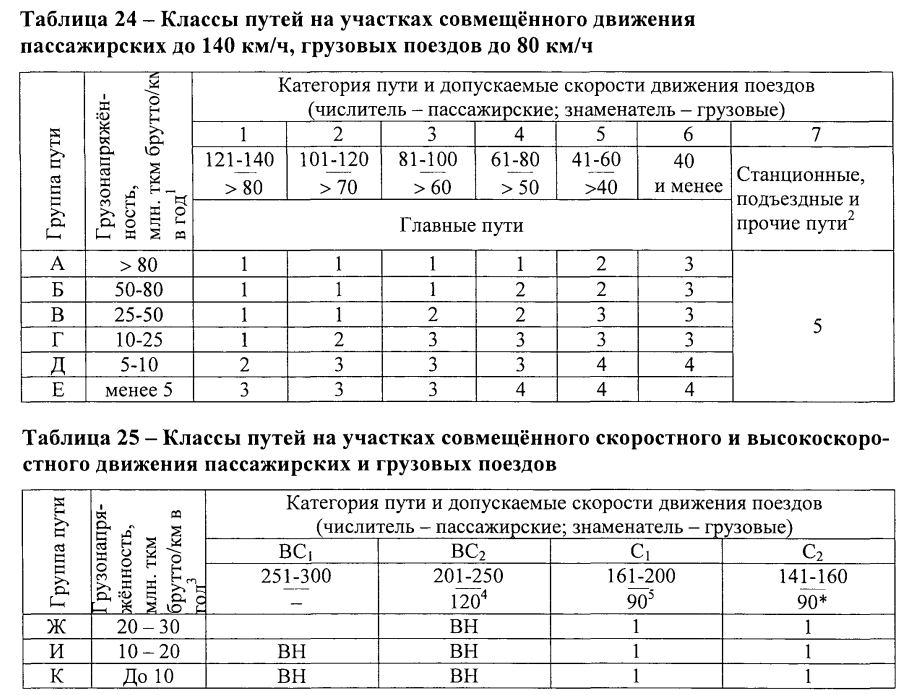
В настоящее время «Положением» о системе ведения путевого хозяйства (СВПХ), разработанном в соответствии с распоряжением ОАО «РЖД» от 02 мая 2012 г. № 1393р «Об утверждении методики классификации железнодорожных линий», установлена классификация путей (таблица 26), при обращении по ним пассажирских поездов с максимальной скоростью до 200 км/ч и грузовых – до 140 км/ч.
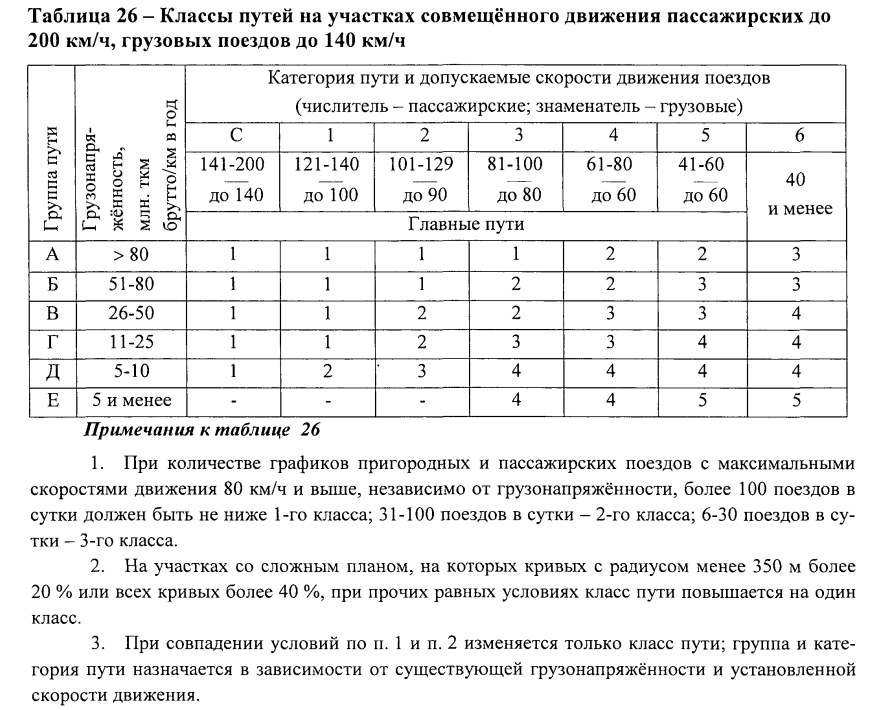
Классы путей на участках совмещённого скоростного и высокоскоростного движения пассажирских и грузовых поездов устанавливаются в соответствии с изменением условий эксплуатации, усилением железнодорожного пути, повышением его надёжности, увеличением скоростей движения пассажирских поездов после проведения комплексной реконструкции железнодорожного пути (далее – комплексная реконструкция). До конца 2011 г. классы путей утверждались Департаментом пути и сооружений ОАО «РЖД» по представлению железной дороги.
Классы путей указываются в техническом паспорте каждой дистанции пути. Информация о них используется для планирования ремонтно-путевых работ.
Для скоростного движения поездов современные условия эксплуатации требуют бесстыкового пути на железобетонных шпалах. Для такого пути стрелочные переводы должны применяться также на железобетонном основании, а стыки с рельсами основного пути необходимо выполнять сварными. Контактная сварка для этих целей пока по ряду причин не может быть широко использована (сложность и высокая цена оборудования; невозможность сварки в зоне стрелочных переводов). В настоящее время, на действующих стрелочных переводах только алюминотермитная сварка позволяет получить соединение с необходимой прочностью и пластичностью [197].
Начиная с 1995 г. на отечественных железных дорогах было уложено и эксплуатируется более 41 тыс. стрелочных переводов на железобетонных брусьях. Укладка их осуществлялась в пути первого и второго классов при выполнении усиленных (по действовавшей в те годы классификации путевых работ) капитальных и средних ремонтов пути.
В настоящее время на дорогах ежегодно при выполнении работ по капитальному ремонту верхнего строения или реконструкции железнодорожного пути укладывается порядка 5 тыс. стрелочных переводов на железобетонных брусьях [183, с. 113].
Сведения об эксплуатационных условиях пути, в котором уложен стрелочный перевод и где выполнялась сварка стыков термитом, в обязательном порядке отражаются в специальном журнале учёта производства сварочных работ. Например, если сварка стыков произведена в стрелочном переводе на пути с грузонапряжённостью 63 млн. ткм/км год и скоростями движения: пассажирских поездов – до 120 км/ч, грузовых – более 70 км/ч, то этот путь, в соответствии с классификацией (по таблице 26) относится к первому классу, группе А, второй категории и обозначается следующим образом: 1А2. Если же в «Техническом паспорте дистанции пути» конкретный путь обозначен, например, 2ВЗ, то этот путь является путём второго класса, группы В, третьей категории.
Таким образом, повышение скоростей движения, комфорта пассажиров и увеличение нагрузок на ось требовало как улучшения конструкции верхнего строения пути, так и повышения качества металла, из которого изготавливают рельсы, проведения дополнительной термической обработки готовых рельсов, совершенствования их геометрических форм и размеров. Одновременно с этим необходимо было создать специальное рельсопрокатное производство, обеспечивавшее потребность железных дорог и гарантировавшее необходимое качество получаемых рельсов, так как оно напрямую определяло безопасность движения поездов.
Формирование специальных требований к рельсам
Назначение железнодорожных рельсов заключается в создании поверхности с наименьшими сопротивлениями для качения колёс подвижного состава, непосредственном восприятии и упругом перерабатывании и передаче нагрузки от колёс на подрельсовое основание, направлении ходовых частей локомотивов и вагонов. На участках с автоблокировкой рельсовые нити служат одновременно и проводниками сигнального тока, а на участках с электрической тягой – проводниками обратного тягового тока. Для соответствия назначению и надёжной работы железнодорожные рельсы должны обладать рядом свойств. Они должны быть прочными (иметь достаточные моменты инерции и моменты сопротивления, чтобы возникающие в них напряжения изгиба и кручения не превышали допустимых значений); долговечными (рельсовая сталь должна обладать высокой твёрдостью, износостойкостью и вязкостью); иметь высокую контактно-усталостную выносливость. К тому же, должны быть обеспечены прямолинейность в вертикальной и горизонтальной плоскостях, установлены допуски в размерах поперечного профиля, определены химический состав и твёрдость рельсовой стали, оговорены недопустимые дефекты металлургического производства и неметаллические строчечные включения [198 – 202].
Рельсы, предназначенные для сварки или других специальных целей, по требованию потребителя допускается изготовлять длиной не менее 6,0 м без закалки одного или обоих концов. Рельсы после полного остывания могут быть подвергнуты холодной правке на роликоправильных машинах и штемпельных прессах. После холодной правки не допускаются:
- повторная холодная правка рельсов на роликоправильных машинах в одной и той же плоскости;
- падение рельсов с высоты более 1,0 м;
- волнистость и скручивание рельсов; рельс считается скрученным, если при замере его на контрольном стеллаже он имеет по концам зазоры между краем подошвы и стеллажом (по диагонали) более 1/10000 своей длины.
Концы рельсов должны быть отфрезерованы перпендикулярно продольной оси рельса. Перекос торцов не должен быть более 1,0 мм при изменении в любом направлении. Обрубать и ломать дефектные концы рельсов не допускается.
Болтовые отверстия на концах рельсов должны быть просверлены перпендикулярно к вертикальной продольной плоскости рельса. Поверхности болтовых отверстий и торцы рельсов должны быть без рванин, задиров и следов усадки в виде расслоений и трещин. Заусенцы и наплывы металла у болтовых отверстий и на торцах рельсов должны быть удалены зачисткой.
Пробный отрезок рельса для копровых испытаний должен выдержать при температуре от 0 °С до + 40 °С испытание на трёхточечный удар без излома, трещин и выколов подошвы (как в пролёте, так и на опорах). Пробный отрезок рельса для испытания на прочность подошвы должен выдержать без трещин или излома статическую нагрузку до получения стрелы прогиба 4,0 мм на базе 1 м.
Таким образом, жёсткое соответствие требованиям, предъявляемым к рельсам, обеспечивает их надёжность.
Применение упрочняющей термической обработки новых рельсов
Совершенствование нагревательных устройств и всесторонние исследования процессов термической обработки стали позволяют разрабатывать технологиче-
ские процессы, с помощью которых осуществляется поверхностная закалка го¬ловки рельсов:
- с прокатного нагрева;
- с повторного поверхностного нагрева газопламенными горелками;
- с повторного поверхностного нагрева токами высокой частоты;
- с повторного объёмного (печного) нагрева.
Стало возможным выполнять объёмную закалку по всему поперечному сече-нию рельса: - с прокатного нагрева,
- с повторного объёмного (печного) нагрева.
Совершенствование способов термического упрочнения рельсов в 1940-1960- е гг. приведено в таблице 27 [35, с. 107-155].
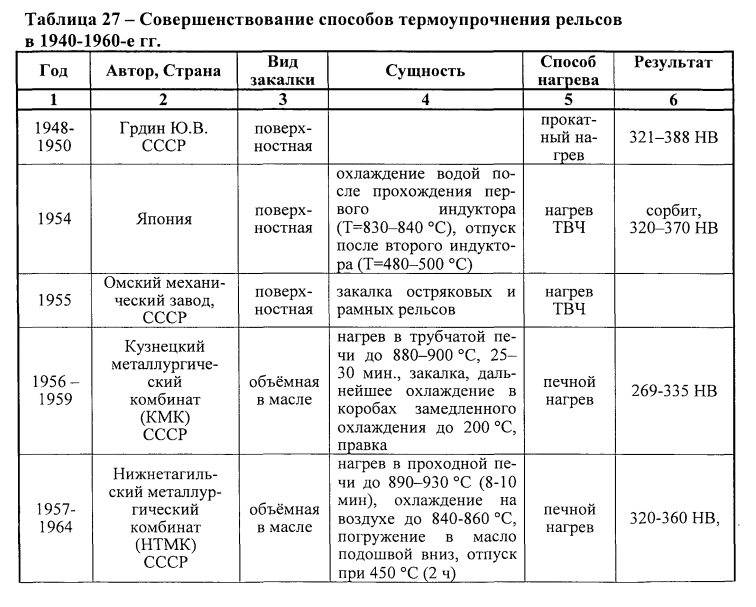
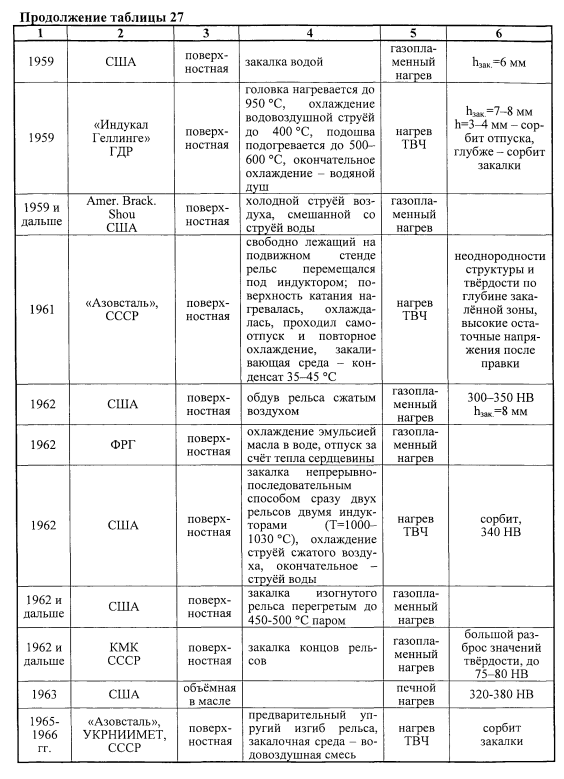
В связи с изменением химического состава рельсовой стали потребовалось внести уточнения в технологические процессы закалки, которые не меняли сущность процесса и значения твёрдости. Уточнение технологических параметров при закалке стало возможным благодаря проведению научных исследований процессов структурообразования рельсовых сталей при различных режимах термической обработки. Были проведены теоретические изыскания и экспериментальное изучение процесса охлаждения различных элементов профиля рельсов при разных способах закалки [36].
В настоящее время в России используются, в основном, объёмно-закалённые рельсы. За рубежом, при термическом упрочнении рельсов, как с прокатного, так и со специального, повторного, нагрева, широко используют экологически чистые окружающие среды (водо-воздушные смеси, сжатый воздух, воду или полимерные среды), с последующим самоотпуском, что позволяет получить свойства, дифференцированные по сечению рельсов [203]. В России разработана технология и специальная установка для термической обработки рельсов с двусторонним охлаждением, обеспечивающая лучшие показатели, по сравнению с существующими методами, по следующим параметрам:
- улучшение геометрических параметров;
- обеспечение дифференцированного уровня свойств по сечению (твёрдая головка, упрочнённая подошва, вязкая шейка);
- повышение сопротивления контактной усталости и износу;
- повышение сопротивления усталостным разрушениям в головке и подошве за счёт создания там сжимающих остаточных напряжений [37].
Рельсы, предназначенные для термической обработки, должны соответствовать требованиям, предъявляемым к рельсам первого сорта. Твёрдость на поверхности катания головки закалённых рельсов должна быть в пределах 321 – 401 НВ; твёрдость шейки и подошвы рельсов – не более 388 НВ [158]. Макроструктура закалённого металла головки рельса должна представлять собой сорбит закалки. Механические свойства закалённых рельсов должны соответствовать представленным в таблице 28 [31].
Пробный отрезок рельса должен выдерживать низкотемпературные испытания на удар под копром без излома и признаков разрушения. При неудовлетворительных результатах испытаний на удар под копром рельсы разрешается подвергать высокому отпуску на твёрдость 255 -302 НВ и сдавать их как незакалённые [183, с. 112].
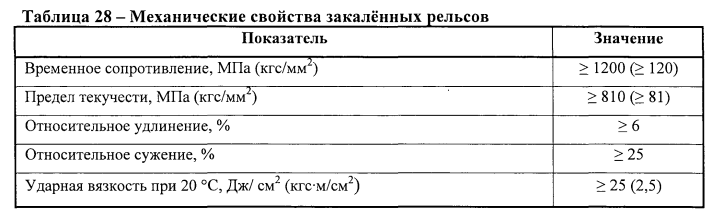
Рельсы, подлежащие сварке между собой, должны быть одного типа и одинаковой группы годности. Новые и старогодные рельсы длиной 25 м должны иметь не более четырёх сваренных стыков, рельсы длиной 12,5 м – не более двух. При износе концов рельсов с болтовыми отверстиями более 2 мм перед сваркой производят их обрезку не менее 600 мм. Вырезают также дефектные места рельсов. При термитной сварке рельсов допускается оставлять ранее сваренные контактным способом стыки. При этом расстояние от места обрезки до существующего (старого) сварного шва должно быть не менее 3 м. Рельсы, сваренные термитным способом, при статическом поперечном изгибе должны иметь показатели прочности и пластичности не ниже регламентированных [191]. Сварка должна производиться при температуре окружающего воздуха не ниже – 5 °С.
Таким образом, совершенствование технологии обработки рельсов обеспечивает соответствие рельсов ужесточаемым условиям эксплуатации.
Выводы
- Эксплуатация первых железных дорог с рельсами, изготовленными из чугуна, и имевшими разные профили поперечного сечения показала, что этот материал обладает высокой хрупкостью, низкой пластичностью и не способен выдерживать высокие нагрузки, действующие на рельсы и приводящие к их разрушению, а разные типы, выпускаемые заводами по заказу дорог, затрудняют их сортировку. Это потребовало сокращения количества типов рельсов и использования для их изготовления более пластичного материала – стали.
- Развитие металлургии, материаловедения показало, что за счёт правильной термической обработки можно значительно повысить прочностные характеристики рельсовой стали. Исходными материалами при выплавке стали являются чугун и стальной лом – для мартеновского процесса, и чугун – для бессемеровского способа. Мартеновская сталь по качеству лучше бессемеровской. Она менее хладноломка, так как имеет меньшее содержание фосфора, даёт более плотный слиток, её химический состав более однороден и содержит меньше примесей.
- На эксплуатационные характеристики рельсов большое влияние оказывают химический состав и технология выплавки. В связи с этим Рельсовой комиссией под руководством JI.O. Николаи было принято решение о разработке технических условий на рельсы, регламентирующих содержание основных элементов химического состава рельсовой стали и её прочностные характеристики. Оптимизация химического состава и повышение прочностных характеристик проводится до настоящего времени, что требует периодической корректировки имеющихся технических условий и стандартов.
- Всесторонний анализ условий эксплуатации различных участков железнодорожного пути, проведённый различными организациями и ведущими специалистами, показал, что на работоспособность пути оказывают большое влияние динамическое воздействие поезда и природно-климатические явления и факторы. В связи с этим принято классифицировать отдельные участки пути по категориям, в зависимости от грузонапряжённости, скоростей движения и виду обращающегося подвижного состава. До конца 2011 г. классы путей утверждались Департаментом пути и сооружений ОАО «РЖД» по представлениям железных дорог.
Список литературы
- Народное хозяйство РСФСР в 1958 году [Текст] : стат. сб. – М.: Гос- статиздат, 1959. – 508 с.
- Народное хозяйство РСФСР в 1959 году [Текст] : стат. сб. – М.: Гос- статиздат, 1960. – 600 с.
- Народное хозяйство РСФСР [Текст] : стат. сб. – М.: Госстатиздат, 1957. -372 с.
- Народное хозяйство СССР в 1959 году [Текст] : стат. сб. – М.: Госстат-издат, 1960.-896 с.
- Народное хозяйство СССР в 1962 году [Текст] : стат. сб. – М.: Госстат-издат, 1963. – 736 с.
- Народное хозяйство СССР в 1963 году [Текст] : стат. сб. – М.: Госстат-издат, 1964. – 760 с.
- Народное хозяйство СССР в 1965 году [Текст] : стат. сб. – М.: Госстат-издат, 1966. – 912 с.
- Народное хозяйство СССР в 1967 году [Текст] : стат. сб. – М.: Госстат-издат, 1968.- 1008 с.
- Народное хозяйство СССР в 1969 году [Текст] : стат. сб. – М.: Госстат-издат, 1970. – 736 с.
- Народное хозяйство СССР в 1973 году [Текст] : стат. сб. – М.: Стати-стика, 1974. – 880 с.
- Народное хозяйство СССР в 1975 году [Текст] : стат. сб. – М.: Стати-стика, 1976. – 846 с.
- Народное хозяйство СССР в 1977 году [Текст] : стат. сб. / ЦСУ СССР. – М.: Статистика, 1978. – 654с.
- Народное хозяйство СССР в 1979 году [Текст] : стат. сб. / ЦСУ СССР. – М.: Статистика, 1980. – 615 с.
- Народное хозяйство СССР в 1980 году [Текст] : стат. сб. / ЦСУ СССР. – М.: Статистика, 1981.-583 с.
- Народное хозяйство СССР. 1922 – 1982 году [Текст] : юбил. стат. сб. / ЦСУ СССР. – М.: Статистика, 1982. – 624 с.
- Народное хозяйство СССР в 1982 году [Текст] : стат. сб. / ЦСУ СССР. – М.: Статистика, 1983. – 574 с.
- Народное хозяйство СССР в 1983 году [Текст] : стат. сб. / ЦСУ СССР. – М.: Статистика, 1984. – 607 с.
- Народное хозяйство СССР в 1985 году [Текст] : стат. сб. / ЦСУ СССР. – М.: Статистика, 1986. – 655 с.
- Народное хозяйство СССР в 1987 году [Текст] : стат. ежегодник / Гос-комстат СССР. – М.: Финансы и статистика, 1988. – 736 с.
- Народное хозяйство СССР в 1989 году [Текст] : стат. ежегодник / Гос-комстат СССР. – М.: Финансы и статистика, 1990. – 766 с.
- Российская Федерация в 1992 году [Текст] : стат. Ежегодник / Госком¬стат России. – М.: Республиканский информационно-издательский центр, 1993. – 654 с.
- Российский статистический ежегодник. 1994 [Текст] : стат. сб. – М.: Госкомстат России, 1994. – 799 с.
- Российский статистический ежегодник. 1995 [Текст] : стат. сб. – М.: Госкомстат России, 1996. – 976 с.
- Российский статистический ежегодник. 1997 [Текст] : стат. сб. – М.: Госкомстат России, 1997. – 749 с.
- Российский статистический ежегодник. 1999 [Текст] : стат. сб. – М.: Госкомстат России, 1999. – 621 с.
- Российский статистический ежегодник. 2000 [Текст] : стат. сб. – М.: Госкомстат России, 2000. – 642 с.
- Российский статистический ежегодник. 2007 [Текст] : стат. сб. – М.: Госкомстат России, 2007. – 826 с.
- Российский статистический ежегодник. 2008 [Электронный ресурс]: стат. сб. – М.: Росстат, Режим доступа: http://www.gks.ru/bgd/regl/b08__l3/ IssWWW.exe/Stg/d3/l 3-79.htm. (Ссылка актуальна на 20.08.2013)
- Российский статистический ежегодник. 2012 [Текст] : стат. сб. – М.: Росстат, 2012.-786 с.
- Шур, Е.А. Повреждения рельсов [Текст] / Е.А. Шур. – М.: Интекст, 2012.- 192 с.
- Отчёты ОАО «РЖД» за 2003-2013 гг.
- Транспорт и связь в России [Текст] : стат. сб. – М.: Госкомстат, 1995. – 240 с.
- Транспорт и связь в России [Текст] : стат. сб. – М.: Госкомстат, 2001. – 222 с.
- Транспорт в России. 2007 [Текст] : стат. сб. – М.: Росстат, 2007. – 198 с.
- Исследование рельсового дела в СССР [Текст] / М., 1929. – 250 с.
- Капорцев, Н.В. Альбом чертежей верхнего строения железнодорожного пути [Текст] / Н.В. Капорцев. – М.: Трансжелдориздат, 1960. – 212 с.
- Исследование рельсов и стыковых скреплений [Текст] / под ред. В.Н. Данилова-М.: Трансжелдориздат, 1955. – 192 с.
- Ашпиз, Е.С. Железнодорожный путь: учебник / Е.С. Ашпиз, А.И. Гасанов, Б.Э. Глюзберг и др.; под ред. Е.С. Ашпиза. – М.: ФГБОУ «Учебно- методический центр по образованию на железнодорожном транспорте», 2013. – 544 с.
- ГОСТ Р 51685-2000. Рельсы железнодорожные. Общие технические условия. [Текст]. Введ. 2001-07-01. – М.: ИПК Издательство стандартов, 2001. – 24 с.
- Deutsche Eisenbahnen 1835-1985 [Text] / Autorenkoll. unter Ltg. von Elf-riede Rehbein … – 1. Aufl. Berlin: Transpress. – 1985 – 288 s.
- Каталог продукции [Электронный ресурс] /Нижнетагильский метал-лургический комбинат Режим доступа: http://www.ntmk.ru/ru/production/catalogue. php?iAction=l&prt_id=14&prt type=0 (Ссылка актуальна на 25.08.2011)
- ГОСТ 6368-82. Рельсы железнодорожные узкой колеи типов Р8, Р11, Р18 и Р24. Конструкция и размеры [Текст]. – Взамен ГОСТ 6368-52 ; введ. 1984— 01-01. – М.: Изд-во стандартов, 1989. – 7 c.http://standartgost.ru/rOCT%2Q6368- 82#page-l (Ссылка актуальна на 25.08.2011)
- ГОСТ 4121-96 Рельсы крановые. Технические условия [Текст]. – Вза¬мен ГОСТ 4121-76 ; введ. 2002-07-01. – Минск: Изд-во стандартов, 1989. – 7 c.http://files.stroyinf.ru/Datal/3/3926/ (Ссылка актуальна на 25.08.2011)
- Николин, А.И. Совершенствование процессов сварки и термической обработки рельсов магистральных железных дорог [Текст] : дис. … канд. техн. наук: 05.16.01, 05.03.06 Николин Аркадий Игоревич -М., 2004. – 199 с.
- Рельсовая проблема [Текст] : (к соединённому заседанию коллегии НКПС и Главчермета), 1927. – 84 с.
- Комаров, О.Н. Использование термитных материалов в технологиях получения стальных отливок [Текст] : дис. … канд. техн. наук: 05.16.04 Комаров Олег Николаевич – Комсомольск-на-Амуре, 2006. – 268 с.
- Фефелов, В.Н. Повышение эксплуатационных свойств поверхности ка-тания рельсов за счёт оптимизации режимов шлифования и параметров абразив¬ного инструмента [Текст] : дис. … канд. техн. наук: 05.02.08 Вадим Николаевич Фефелов – Новосибирск,- 2006. – 126 с.
- Ильинский, Д.П. Из истории паровозостроительной и вагоностроитель¬ной промышленности России [Текст] / Д.П. Ильинский, В.П. Иваницкий // По ма-териалам книги «Очерк истории русской паровозостроительной и вагонострои-тельной промышленности». НКПС – 1929. – М., 2007. – 217 с.
- Тарасова, В.Н. Становление рельсопроката в России [Текст] / В.Н. Тарасова, О.Н. Трынкова // Мир транспорта. -2012. – № 5 (43). – С. 144-155.
- Садчиков, П.И. Первый русский паровоз Черепановых [Текст], [Элек-тронный ресурс] / П.И. Садчиков, Т.Н. Зайцева / Из истории железных дорог // Железнодорожный транспорт, 2009. – №12. – Режим доступа: http://www.zdt- magazine.ru/publik/history/2009/12-09.htm (Ссылка актуальна на 25.08.2011).
- Козырев, H.A. Железнодорожные рельсы из электростали [Текст] / H.A. Козырев, В.В. Павлов, J1.A. Годик, В.П. Дементьев. – Новокузнецк, 2006. – 387 с.
- Афонина, Г.М. Краткие сведения о развитии отечественных железных дорог с 1838 по 2000 гг. [Текст] / Г.М. Афонина // изд. 2-е, доп. – М., 2001. – 232 с.
- Железные дороги [Электронный ресурс] / История создания железных дорог России. – Режим доступа: http://www.rrh.agava.ru/allrails.htm (Ссылка акту-альна на 25.08.2011)
- История железнодорожного транспорта России [Текст] / в 3-х т. – Т. 1. 1836-1917 / под ред. Красковского Е.Я., М.М. Уздина – СПб. : АООТ «Иван Фё-доров», 1994. – 336 с.
- Мительман, М.М.И. История Путиловского завода (1801-1917) [Текст] / М.М.И. Мительман, Б.Д. Глебов, А.Г. Ульянский и др. // 3 изд. – М.: Из¬дательство социально-экономической литературы, 1961. – 720 с.
- Мнения различных авторов о рельсах со стальной головкой [Текст] / СПб., 1874.- 11 с.
- Посьет Константин Николаевич [Электронный ресурс]. – Режим дос¬тупа: http://ru.wikipedia.org/wiki/nocbeT,КонстантинНиколаевич (Ссылка акту¬альна на 25.08.2011)
- Перспективы развития металлургии черных металлов [Текст] // Мате-риалы к пятилетнему плану промышленности ВСНХ СССР на 1928/29 – 1932/33. 3 т. – Ленинград, 1929. – С. 438-461.
- Социалистическое строительство СССР [Текст] : стат. ежегодн. ЦЦУНХУ ГОСПЛАНА СССР. – М.: В/О СОЮЗОРГУЧЕТ, 1935.-690 с.
- Болдырев, М.Н. Состояние рельсов на сети СССР в последнее время [Текст] / М.Н. Болдырев // Исследование рельсового дела в СССР. М.: Транспе¬чать, 1928-С. 15-25.
- Доклад товарища Куйбышева о втором пятилетнем плане развития на-родного хозяйства СССР [Электронный ресурс] / XVII съезд ВКП(б) (Заседание шестнадцатое 3 февраля 1934 г., вечернее). – Режим доступа: http://www.hrono.ru/vkpb_17/16 1 l.html (Ссылка актуальна на 25.08.2011).
- Кемеж, Н.П. Состояние и перспективы поставок рельсов и рельсовых скреплений [Текст] / Н.П. Кемеж, Сборник докладов по материалам заседания НП «Рельсовая комиссия» 26-27 октября 2007 г. Новокузнецк. Улучшение качест¬ва и условий эксплуатации рельсов и рельсовых скреплений. – Екатеринбург, 2008.-С. 20-24.
- По вопросу об изменении технических условий на изготовление и при-ёмку стальных рельсов [Текст] / Журнал инженерного совета министерства путей сообщения № 9 – 1899 г. – СПб., 1901. – 82 с.
- Тарасова, В.Н. Эволюция технических требований к рельсам в Россий-ской Империи – СССР – Российской Федерации (конец XIX – начало XXI в.) [Текст] / В.Н. Тарасова, О.Н. Воронина // Вопросы истории естествознания и тех¬ники. – 2013.-№ 1. – С. 99-114.
- Неразрушающий контроль металлов и изделий [Текст] : под ред. Г.С. Самойловича // Справочник. – М: Машиностроение, 1976. – 456 с.
- Гурвич, А.К. Дефектоскопия рельсов [Текст] : учебник для техн. школ ж.-д. транспорта. / А.К. Гурвич, Б.Л. Довнар, В.Б. Козлов и др. – 4-е изд., перераб. и доп. – М.: Транспорт, 1978. – 440 с.