Сейчас ваша корзина пуста!
Историко-техническии анализ совершенствования стыковых скреплений и соединений сваркой железнодорожных рельсов
Цикл статей:
Глава 1 – Развитие конструкции железнодорожных рельсов, их стыковых соединений и технологий обработки
Глава 2 – Поставка рельсов для строительства железных дорог
Глава 3 – История совершенствования химического состава и способов термической обработки рельсов
Развитие железнодорожного транспорта и совершенствование рельсовой колеи показало, что для повышения плавности хода и продолжительности безремонтной эксплуатации пути необходимо не только улучшение поперечного профиля рельсов, их химического состава и механических свойств, но и увеличение длины рельсов, и уменьшение количества стыков [204; 205]. При строительстве первых железных дорог металлургическая промышленность не имела возможности изготавливать рельсы длиной более одного метра, так как их получали путём литья в песчано-глинистые формы [46; 206]. Использование коротких рельсов приводило к большому количеству стыков между ними, что не позволяло увеличивать скорость движения поездов. В связи с этим остро встал вопрос об увеличении длины рельсов, с одновременным снижением их веса. Данная задача была решена лишь при развитии прокатного производства в XIX в. Инженерами- металлургами были разработаны рельсопрокатные станы и технологии прокатки на них рельсов увеличенной длины. Одновременно, проводились работы по получению металла для изготовления рельсов более высокого качества и с лучшими механическими свойствами. Это позволило отказаться от производства рельсов литьём. С увеличение длины рельсов сократилось количество стыков, что положительно сказалось на эксплуатационных характеристиках, продолжительности безремонтной работы и т.п.
Современные виды и способы соединений рельсов
Болтовые и сварные (неразъёмные) соединения рельсов
В рельсовой колее стык является наиболее слабым и часто повреждаемым местом. Это связано с тем, что колесо, накатываясь на стык, прогибает рельс вниз,
а на принимающем рельсе образуется ступенька, приводящая к удару колеса по нему. В связи с этим уменьшение количества стыков повышает уровень безопасности и комфортность при перевозке грузов и пассажиров [19]. Создание бесстыкового пути даёт возможность не только повысить комфортность и безаварийность, но и одновременно увеличить скорость движения поездов.
Плоские и уголковые рельсы укладывались в путь без скрепления между собой, что могло приводить к их сдвигу и сходу подвижного состава. Впервые соединение рельсов между собой было произведено на грибовидных рельсах1 [86].
Дальнейшее изменение профиля поперечного сечения рельсов потребовало и изменения конструкции накладок. Первоначально заводы России выпускали различные типы рельсов, и для их стыковки требовалось большое количество разных видов накладок. Это затрудняло проведение ремонтных и профилактических работ. Уменьшение номенклатуры рельсов позволило резко сократить количество и разнообразие видов накладок. С переходом на однотипные рельсы, эксплуатируемые и в настоящее время, соединительные накладки остаются практически без изменений.В 1838 г. были предприняты первые попытки создания единой рельсовой нити за счёт использования жёстких соединительных накладок (болтового соединения рельсов) (рисунок 42) [46]. Несмотря на их наличие, из-за зазора между рельсами, ударно-динамическое воздействие на путь в месте стыка остаётся, поэтому стык считается самым напряжённым местом в пути [67]. При длине рельсов 12,5 м около 35 – 50 % затрат труда уходит на выправку пути в зоне стыков. Стыки создают значительное сопротивление движению поездов (около 10 % от основного).
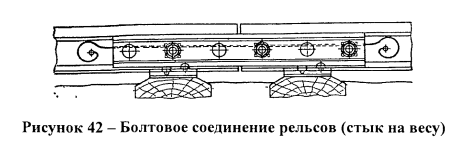
К общим же недостаткам болтового соединения следует отнести:
- высокую шумность от удара колёс по стыкам рельсов;
- низкую скорость движения;
- наличие блуждающих токов;
- на электрифицированных линиях, оборудованных путевой автоматической блокировкой, наличие стыков ухудшает токопроводимость цепей, что вызывает нарушение в работе автоблокировки;
- интенсивный износ ходовых частей подвижного состава и рельсового пути – смятие и выколы головки рельсов в зоне стыка на расстоянии 60 – 80 мм от стыкового зазора, изломы рельсов по болтовым отверстиям, изломы накладок, болтов, подкладок и прикрепителей.
Ослабление конструкции и ухудшение её состояния приводит к увеличению негативного воздействия стыка на путь.
По расположению стыков относительно опор наиболее распространены стыки на весу и стыки на сдвоенных шпалах.
Стык на весу (рисунок 42) зарекомендовал себя как упругий, при нем износ рельсовых концов меньше, чем при других стыках. В России он принят как стандартный, а также широко распространён на железных дорогах многих стран.
Недостаток стыка на весу состоит в том, что из-за большого прогиба рельсовых концов накладки работают на изгиб в более тяжёлых условиях, чем в стыках на сдвоенных шпалах.
Стык на сдвоенных шпалах (рисунок 43) [46] обладает большей сопротивляемостью горизонтальным и вертикальным перемещениям. В России такие стыки используют крайне редко.
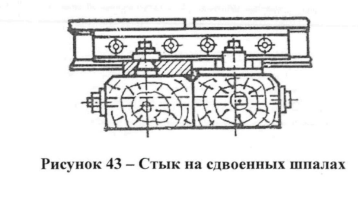
По сравнению со стыками на весу, стыки на сдвоенных шпалах более жёсткие, они требуют дополнительных затрат металла на объединение шпал, а в ряде случаев – применения специальных стыковых скреплений (например, общей подкладки на обе шпалы). Кроме того, такие стыки трудно собирать на звеносбороч- ной базе и подбивать.
В зависимости от взаимного расположения стыков разных рельсовых нитей одного пути различают стыки: по наугольнику, вразбежку и бессистемно расположенные.
При расположении по наугольнику (рисунок 44) стыки обеих рельсовых нитей находятся на одном перпендикуляре к продольной оси пути. Такое размещение принято как стандартное в России и во всех европейских странах.
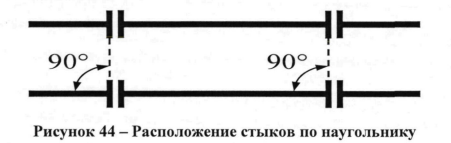
Преимущества такого расположения:
- меньшее число ударов в стыках при проходе подвижного состава, чем при других схемах;
- возможность индустриальной укладки (заготовки рельсошпальной решётки на звеносборочных базах) и разборки пути;
- более лёгкое содержание пути.
Недостаток – необходимость применения укороченных рельсов для укладки в кривых, чтобы обеспечить расположение стыков именно по наугольнику.
Основное преимущество стыков вразбежку в том, что они не требуют применения укороченных рельсов для укладки на внутренних нитях в кривых. К их недостаткам относятся вдвое большее, чем при стыках по наугольнику, количество ударных воздействий колёс, невозможность индустриальной укладки и разборки пути. Стыки вразбежку были распространены в США, но в настоящее время от них практически отказались.
Бессистемно расположенные стыки обладают теми же преимуществами и недостатками, что и стыки вразбежку.
Широкое внедрение клееболтовых стыков усиленной конструкции повышает эффективность бесстыкового пути с рельсовыми плетями длиной более 950 м по сравнению с участками, где ранее эксплуатировались короткие плети. В связи с этим и для таких участков рационально сваривать эксплуатируемые рельсовые плети, ликвидируя уравнительные пролёты с предварительным закреплением рельсовых плетей в оптимальном температурном интервале. Клееболтовые стыки применяют для изоляции блок участков друг от друга. Бесстыковой путь предусматривает отсутствие стыков не только на перегонах, но и на стрелочных переводах. Современные стрелочные переводы (рисунок 45) [53, с. 71; 54, с.86] являются высоко ответственными и достаточно сложными конструкциями в путевом хозяйстве. В настоящее время они выполняются на железобетонных брусьях, и для повышения их работоспособности требуется сварка с рельсами основного пути [53, 54].
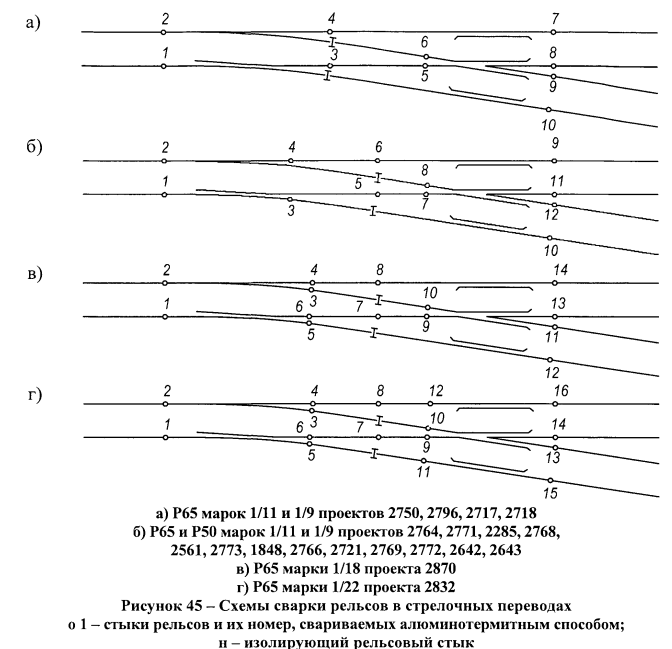
Таким образом, применение жёстких стыковых накладок не позволило полностью решить проблему по созданию бесстыкового пути. Для создания бесстыкового пути необходимо неразъёмное соединение рельсов.
История разработки инновационных технологий для разных способов сварки рельсов
В зависимости от формы энергии, используемой для образования сварного соединения рельсов для железнодорожного транспорта, виды сварки разделяют на термический и термомеханический классы. К первому классу относятся термитная, электродуговая ванным способом и электрошлаковая сварки; ко второму способу – электроконтактная и газопрессовая сварки [207].
Развитие промышленности и железнодорожного транспорта в XIX в. требовали увеличения объёмов производства стали и чугуна, поэтому учёными были предприняты попытки их получения внепечным способом. Наиболее перспективным способом являлось производство железа из руды с помощью химических реакций восстановления.
В 1865 г. основоположником современной физической химии русским учёным H.H. Бекетовым был впервые предложен метод получения металлов из их окислов [208]. Своими исследованиями о вытеснении из соединений одних элементов другими H.H. Бекетов превратил этот метод в научную теорию, заложив основу алюминотермии. Было установлено, что алюминий обладает высокой активностью, соединяясь с кислородом, и что при определённых условиях он легко восстанавливает из окислов другие металлы, в том числе и железо. На этом методе в дальнейшем был разработан способ алюминотермитной сварки массивных деталей между собой.
Большой вклад в создание термитной сварки внёс Г. Гольдшмидт, представитель Гейдельбергской школы химиков (Германия), ученик Р.В. Бунзена [209]. В 1888 г. он получил права на металлургический завод в Эссене, где в 1893 г. осуществил первый промышленный алюминотермический процесс с целью получения корубиса – шлака, по твёрдости соответствующего карборунду.
До успешного эксперимента Г. Гольдшмидта многие исследователи пытались применить алюминий для уменьшения оксидных включений в слитках стали, но процесс алюминотермии был трудно управляемым, смесь вспыхивала мгновенно или совсем не загоралась. Г. Гольдшмидт преодолел эту трудность, применив для холодной шихты запал из пероксида бария. Первый патент учёного (1897 г.) защитил способ производства технически чистых металлов [74].
Получение таким способом металлов было связано с рядом технологических трудностей и оказалось экономически не целесообразным по сравнению с общепринятым печным производством. Однако, в дальнейшем, данный метод получения жидкой стали был успешно применён для сварки крупногабаритных деталей между собой, в том числе и рельсов.
Первый патент, относящийся к соединению рельсов с помощью термитной сварки (рисунок 46) [210], получил Г. Гольдшмидт в 1901 г. Вскоре после этого была организована фирма «Гольдшмидт термит компани», и термитный процесс начали применять не только для сварки рельсов, но и для заварки дефектов отливок, ремонта треснувших рам двигателей, маховиков, штанг и т.п. В 1908 г. Г. Гольдшмидт усовершенствовал технологию сварки рельсов [33].
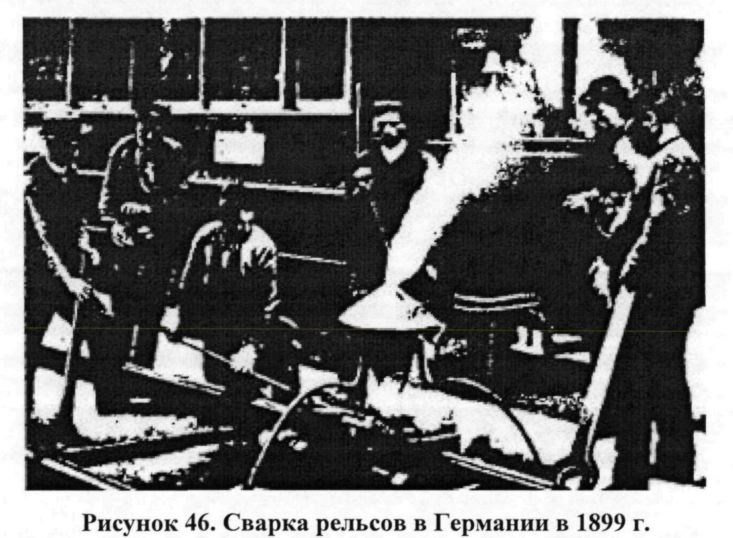
В это же время была предпринята попытка получения бесстыкового пути [204]. Для этой цели на железных дорогах США сварили рельсовую плеть длиной около 3 миль (5 км) [211].
Термитная сварка представляет собой процесс сварки металлических деталей путём заливки в зазор между соединяемыми деталями жидкого металла, требуемого химического состава, получаемого в результате алюминотермической реакции. Такие преимущества термитной сварки, как портативность оборудования и приспособлений, возможность соединять крупные заготовки на месте, и почти сразу же использовать сваренное изделие, были быстро оценены железнодорожниками. Термитом стали сваривать рельсы, поломанные тяги, штоки и др. В 1904 г. только австрийская фирма «Электрик тракшен» выполнила 10 тыс. стыков. Термитная сварка считалась выгодной для соединения деталей с площадью сечения более 5 см . На сварку стыка уходило до 10 мин. В 1904 г. в США термитная сварка была использована для соединения рельсов, деталей корабельных якорей, паровых машин и изготовления перекрытий мостов. Процесс оказался особенно выгодным при сварке соединений, сечение которых превышало 25 см . Непревзойдённые в то время возможности термитной сварки были продемонстрированы при прокладке путей Парижского метрополитена.
Уже в первые два десятилетия XX в. были разработаны и нашли применение три технологические схемы термитной сварки, где сжигание смеси, получение железа и шлака производили в отдельном тигле, расположенном над местом сварки. При этом соединение получали:
- заливкой разделки жидким металлом без дополнительных технологических приёмов;
- заливкой разделки шлаком (иногда и металлом) с последующим сдавливанием деталей и вытеснением его (их) из зазора;
- комбинированным способом.
- термитно-стрелочном заводе по технологии инженера М.А. Карасева и применён
С 1915 г. в России стали применять термит для сварки трамвайных рельсов, и было сварено 126 стыков, в 1918 г. – 151 (рисунок 47)[212]. С 1923 г. стыки трамвайных рельсов столицы начали регулярно соединять с помощью термитной сварки [68].
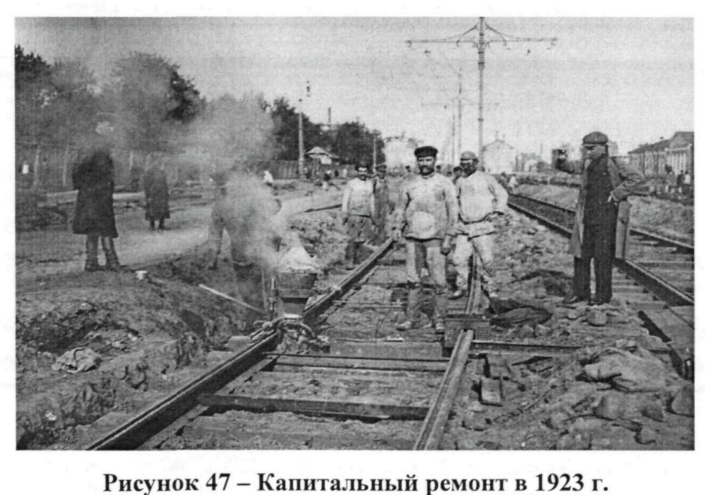
В 1930 г. в СССР наиболее употребляемым был комбинированный способ термитной сварки стыков рельсов трамвайных и железнодорожных путей [214, 215]. При этом жидкий металл сплавляли с подошвой стыкуемых рельсов и нижней частью шейки, а шлаком нагревали головки рельсов и вставленную между ними стальную пластину до «сварочного жара», затем специальным прессом стягивали свариваемые рельсы, в результате чего осуществлялась сварка (рисунок 48).
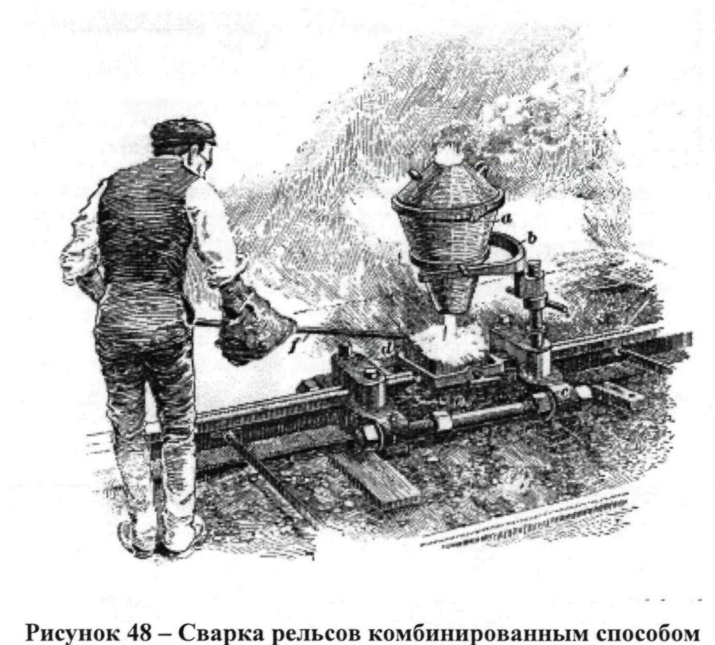
Вплоть до середины 1950-х гг. сварка рельсов на железнодорожном транспорте осуществлялось в основном алюминотермитным способом.
Началом возрождения термитной сварки можно считать применение её в 1963 г. в Германии для ремонта крупных изделий, однако прочность алюмино- термитных стыков составляла на тот период 50-60 % от прочности стыков, сваренных электроконтактным способом. Усовершенствование технологии производства и хранения термитной смеси, разработка новой оснастки, инструментов и приспособлений позволили фирмам Германии, Франции и Чехословакии использовать термитную сварку для получения бесстыкового пути. На основе новых разработок бесстыковой путь начал появляться на железных дорогах других европейских государств [47].
В России вторично термитная сварка для соединения железнодорожных рельсов появилась в 1996 г., когда ЗАО «СНАГА», адаптировав данный метод для отечественных условий, стала активно внедрять его на всей сети железных дорог. В связи с этим было признано целесообразным использовать алюмино- термитный способ для сварки рельсов в пределах стрелочных переводов, уложенных на железобетонных брусьях. Это обеспечивает надёжную токопроводи- мость рельсовых цепей и повышает надёжность автоблокировки. Алюминотер- митная сварка также используется для восстановления лопнувших рельсовых плетей бесстыкового пути.
В период с 2005 г. по настоящее время проводится алюминотермитная сварка рельсов по технологиям фирм ЗАО «СНАГА» и «Электро-Термит» в соответствии с ТУ 0921-127-01124323-2005 «Сварка рельсов алюминотермитная методом промежуточного литья» [197].
Газопрессовая сварка (рисунок 49) использовалась для сварки рельсов в стационарных условиях. Она характеризуется нагревом металла газовым пламенем и осадкой (сдавливанием) или проковкой нагретых деталей. Нагрев производится многопламенными сварочными горелками с большим количеством (до ста и более) небольших сопел, равномерно распределённых по торцевой поверхности, мундштука. Свариваемые поверхности за 1-2 мин частично оплавляются, после чего детали сдавливаются и соединяются. Нагрев ведётся обычно ацетиленокис- лородным пламенем, осадка производится гидравлическим устройством с зажимами для прочного захвата соединяемых деталей [32, с. 330-332].
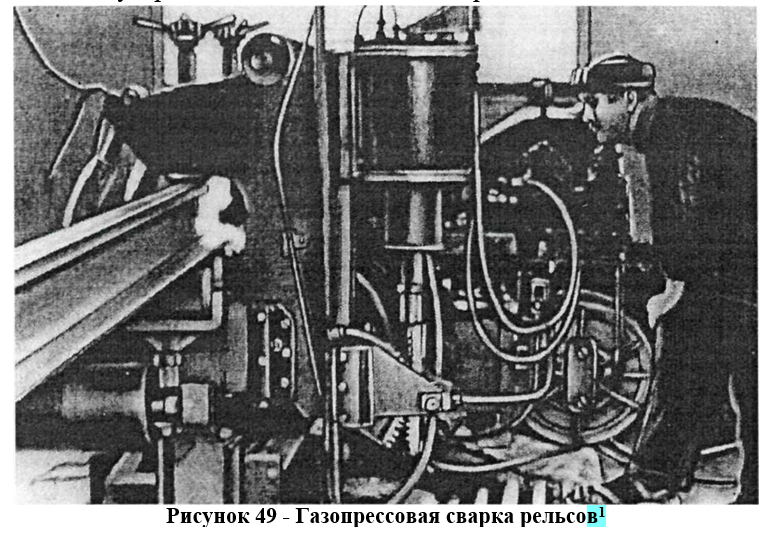
Оборудование для этого способа сварки было разработано во второй полови¬не 1940-х гг. коллективом в составе Т.А. Владимирского, М.С.Никитина, Н.В. Бродовича, A.B. Обухова и А.К. Швылпова [30].
Для газопрессовой сварки характерны защита от окисления, низкая стоимость оборудования, ненужность присадочного металла и однородность сварного соединения.
В основе электродуговой сварки рельсов лежит метод использования тепловой энергии электрической дуги для расплавления металла, открытый в 1802 г. электротехником В.В.Петровым. В 1882 г. русский инженер H.H. Бенардос изобрёл «способ соединения и разъединения металлов непосредственным действием электрического тока», а в дальнейшем – и основные способы дуговой электрической сварки. В 1888 г. Н.Г. Славянов разработал метод дуговой электросварки металлическим электродом, а в 1891 г. получил патент на «Способ и аппараты для электрической отливки металлов», тем самым усовершенствовав способы использования тепла электрической дуги для промышленного нагрева [34, с. 5-6]. Применение в 1907 г. шведским инженером О. Кьельбергом металлических электродов с флюсовым покрытием позволило предохранить металл шва от вредного воздействия воздуха. В 1929 г. советский инженер-изобретатель Д.А. Дульчевский разработал способ автоматической дуговой сварки под флюсом. В 1932 г. коллективом Московского электромеханического института инженеров железнодорожного транспорта под руководством К.К. Хренова был создан способ дуговой электросварки под водой [207, с. 15-16].
Электродуговая сварка рельсов ванным способом (рисунок 50) применяется с середины 1930-х гг. В 1940-е гг. Институтом электросварки под руководством Е.О. Патона было разработано оборудование для автоматической сварки [216, с. 16-17]. Электродуговая сварка характеризуется увеличенными размерами сварочной ванны, удерживаемой в специальной стальной или керамической форме. Расплавление кромок свариваемых изделий происходит за счёт тепла жидкого металла. Стальную форму приваривают встык. Керамические формы делают разъёмными и после сварки удаляют. Электродуговую сварку применяют при сварке стержневых изделий (арматуры, рельсов и т.п.). Её можно вести одним или несколькими электродами, на повышенных режимах, что обеспечивает необходимый нагрев свариваемых элементов для создания большой ванны из жидкого металла. Сварку начинают в нижней части формы, в зазоре между торцами стержней (рельсов). Расплавленный в электрической дуге металл заполняет пространство между свариваемыми деталями. Технология отличается большим удельным расходом электродов (10-15 шт./стык) и меди (70-100 г/стык), низкой производительностью (8-10 стыков в смену) и весьма низким качеством сварки, что не позволило ей найти широкое применение при сварке рельсов [34; 217; 218].
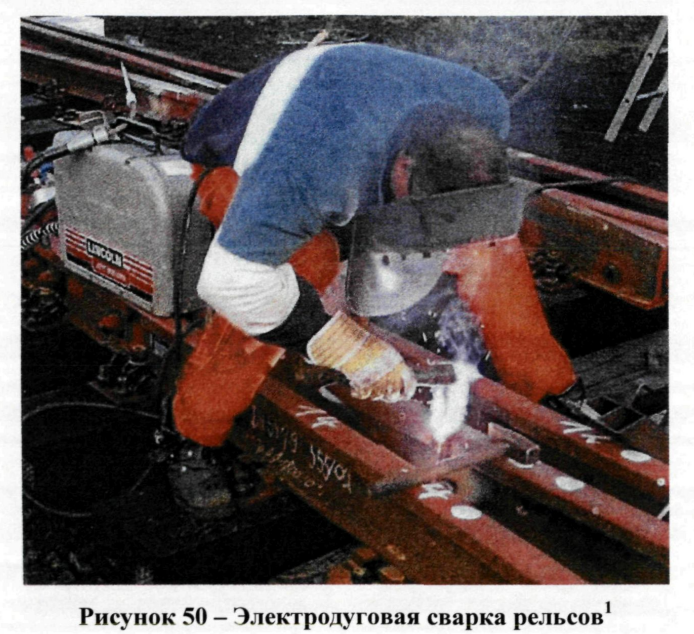
В настоящее время данный вид применяют для сварки трамвайных рельсов, арматуры в строительных конструкциях и т.п.
Электрошлаковая сварка была разработана в 1950-х гг. в Институте электросварки им. Е.О. Патона АН УССР. Впервые электрошлаковую сварку осуществил в 1949 г. Г.З. Волошкевич, который в 1956 г. получил авторское свидетельство на данный способ соединения металлов [207 с. 158]. Попытки разработать технологию сварки рельсов электрошлаковым способом закончились неудачей, т.к. процесс сварки в поперечном сечении оказался ещё более трудоёмким, чем ванный способ рельсов [217].
Процесс получения соединения металлов путём контактной сварки был впервые применён У. Томсоном в Англии в 1856 г. и Э. Томсоном в США – в 1877 г. В этом же году H.H. Бенардос изобрёл контактную точечную сварку, а в 1885 г. получил патент на способ точечной электросварки клещами с угольными электродами, чем положил начало электроконтактной сварке. Появление роликовой, стыковой, рельефной сварок стало возможным благодаря замене угольных электродов на медные [207, с. 213-214].
При электроконтактной сварке (рисунок 51) электрический ток пропускают через место сварки, оказывающее омическое сопротивление прохождению тока. При этом происходит разогрев металла в месте контакта (стыка) за счёт выделения Джоулевого тепла. Разогретые и обычно оплавленные детали сдавливаются или осаживаются, способ отличается высокой степенью механизации, автоматизации и роботизации.
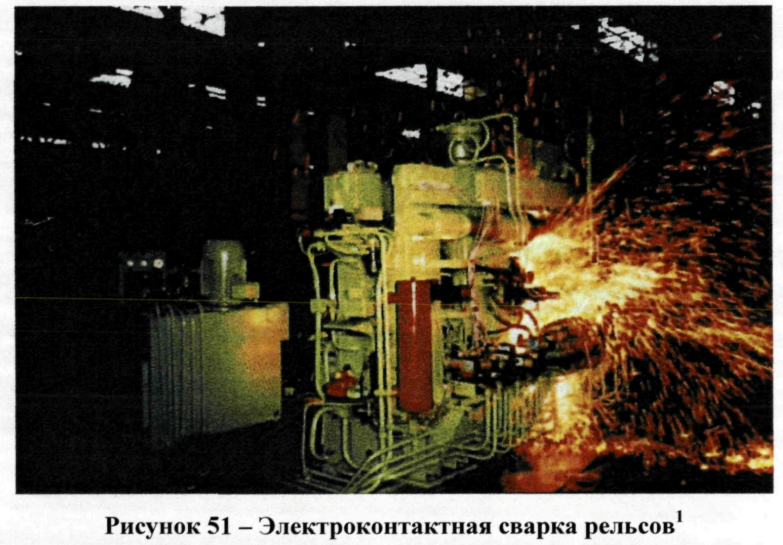
Электроконтактная сварка впервые была успешно применена в 1943 г. на же¬лезных дорогах СССР [219]. Разработка технологии контактных машин для сварки рельсов институтом электросварки им. Е.О. Патона и ВНИИЖТом позволили производить сварку рельсов в плети для бесстыкового пути в стационарных условиях. В дальнейшем была разработана передвижная рельсосварочная машина ПРСМ (рисунок 52)[221], позволяющая сваривать рельсы контактным способом непосредственно при их укладке. Развитие бесстыкового пути железных дорог показало, что не всегда можно или целесообразно использовать рельсосварочную машину. Так, например, при ремонтных работах использование контактной сварки рельсов связано с рядом неудобств: требуются продолжительные окна, расшивка пути, доставка рельсосварочной машины к месту сварки и т.п.
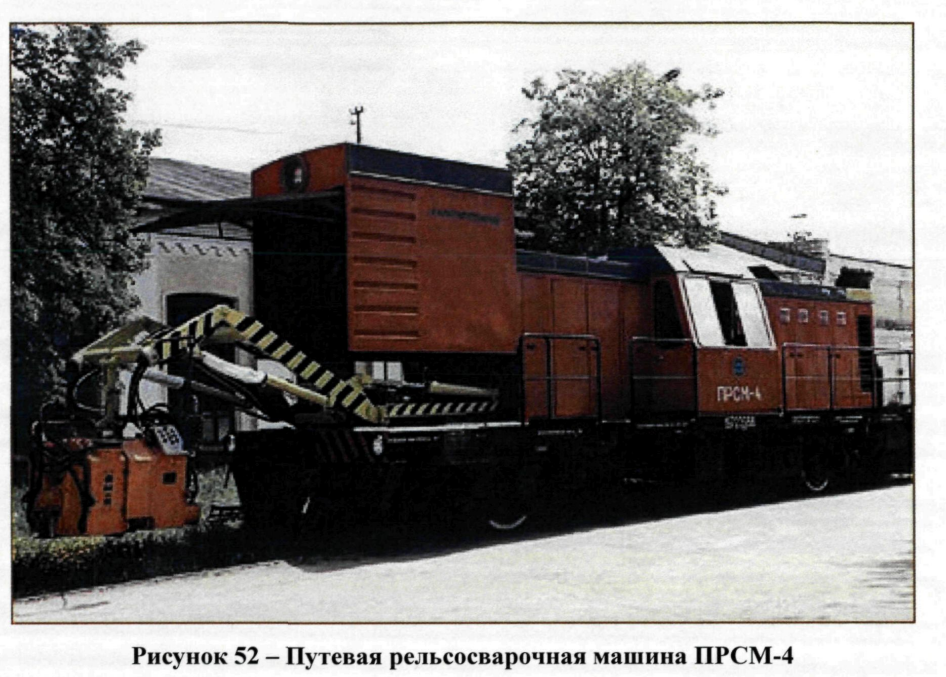
В таблице 29 сопоставляются различные способы сварок по показателям, до¬стигнутым к концу XX в. [31, с. 5]. Учитывая, что алюминотермитная сварка рельсов с 1964 г. не применялась на отечественных железных дорогах, то приведённые для неё данные в таблице 29 являются несколько заниженными. В начале XXI в. в Россию стали поступать рельсы импортного производства, которые при сварке контактным способом стали давать выходы по дефектам сварных стыков (рисунок 53) [220], а при алюминотермитной сварке качество стыков получалось высоким, при строгом соблюдении технологии сварки.

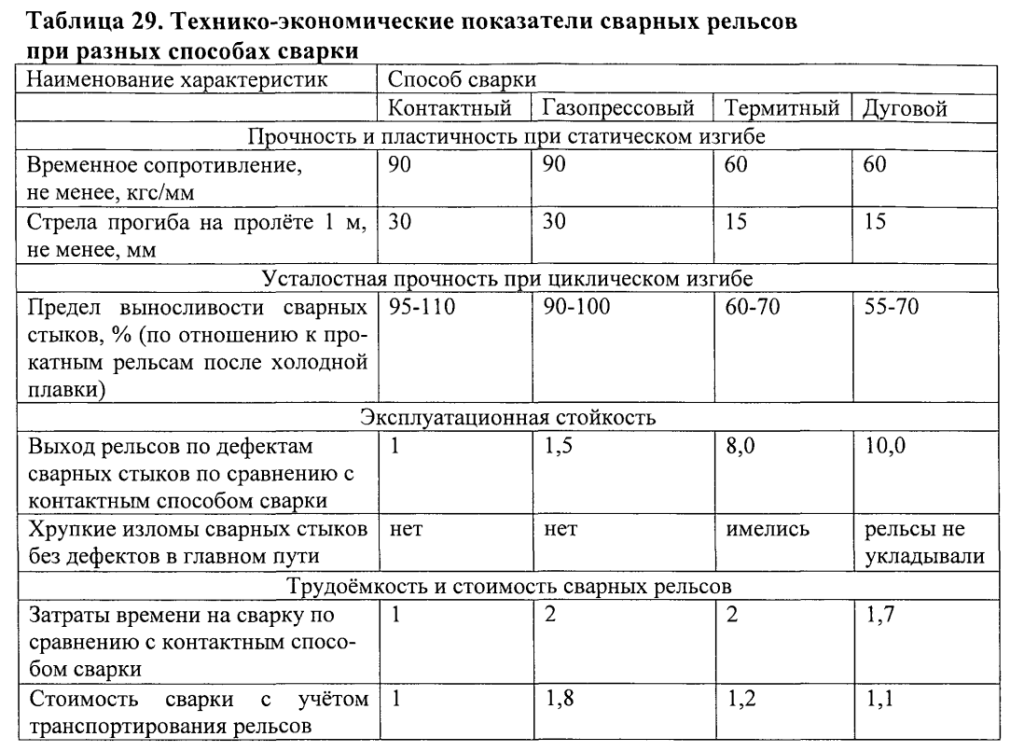
Таким образом, в настоящее время для создания бесстыкового пути на железной дороге используются контактная и алюминотермитная сварка рельсов, а на трамвайных путях – термитная и электродуговая, которую постепенно вытесняет термитная.
Преимущества и недостатки бесстыкового пути и способов его получения в современных условиях
Многолетние исследования и опыт эксплуатации бесстыкового (сварного) пути (рисунок 54), как за рубежом, так и в России, подтвердили высокую эффективность бесстыковой конструкции температурно-напряжённого типа без сезонных разрядок напряжений [24; 26; 222 – 225].
К преимуществам бесстыкового, по сравнению со стыковым, относят:
- снижение динамического воздействия на путь;
- уменьшение износов рельсов и ходовых частей подвижного состава;
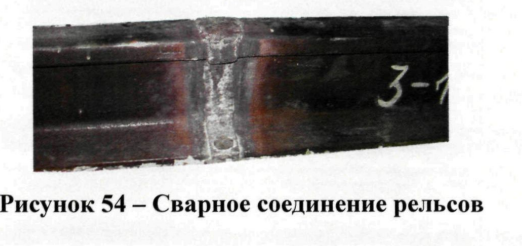
- сокращение выходов из строя рельсов по стыковым дефектам;
- уменьшение сопротивления движению поездов и, соответственно, экономия топлива и электроэнергии на тягу;
- снижение расходов на содержание и ремонт пути и подвижного состава (примерно на 25 – 30 %);
- увеличение срока службы (примерно на 20 %);
- снижение интенсивности бокового износа наружной рельсовой нити в кривых и, соответственно, повреждений рельсов по этой причине;
- сокращение потребности в очистке щебёночного балласта на угольно-рудных маршрутах в 1,5-2,0 раза;
- сокращение расходов металла на стыковые скрепления (до 4,5 т-км);
- уменьшение расходов на ремонт ходовых частей вагонов и локомотивов;
- повышение комфортабельности проезда пассажиров;
- бесстыковая рельсовая цепь позволяет значительно сократить нарушения в работе автоблокировки, так как около 25 % из них происходит из-за неисправностей стыковых соединений. Износ рельсов бесстыкового пути по сравнению со стыковым происходит медленнее, в среднем на 14% на кривых радиусом 600700 м и на 12 % – на прямых, также увеличивается срок службы рельсов или период до капитального ремонта, с одновременным снижением расходов на содержание пути [47; 198; 224; 225].
К недостаткам бесстыкового пути следует отнести:
- большее время, затрачиваемое на оформление стыка;
- большая стоимость работ для выполнения стыка;
- требуется более высокая квалификация рабочих, собирающих стык;
- необходимо дополнительное оборудование для сварки.
Контактная сварка рельсов производится без использования присадочных материалов и без специальной подготовки торцов [35].
До недавнего времени контактная сварка рельсов выполнялась на контактных машинах двумя методами: с предварительным прерывистым подогревом и непрерывным оплавлением. Качество стыков зависит главным образом от степени пластической деформации и нагрева металла свариваемых изделий. В настоящее время разработан метод контактной сварки с нагревом импульсным током [163].
Контактные стыковые машины являются основным оборудованием для сварки рельсов, которая выполняется в стационарных условиях на машинах типов МСГР-500, К-1000 и К190ПК-1, а в пути – с помощью передвижных или самоходных агрегатов, оснащённых контактными головками К-900 и других моделей. Рельсосварочные машины типа МСГР-500 работают методом прерывистого подогрева, а К190ПК-1, К-900, К-900А и К-920 – методом непрерывного оплавления [226].
Преимущества:
- высокое качество сварного соединения;
- механизация и автоматизация работ (в стационарных условиях);
- высокая производительность процесса.
Недостатками являются:
- сложность и высокая цена оборудования;
- необходимость продолжительных окон;
- отсутствие разработанной технологии сварки при пониженных температурах;
- невозможность сварки в зоне стрелочных переводов.
При алюминотермитной сварке используется комплект специального оборудования, общий вес которого не превышает 250 кг.
Преимущества алюминотермитной сварки очевидны:
- удобство, манёвренность и универсальность применяющейся оснастки;
- небольшая продолжительность окон;
- проведение процесса сварки без потребления электроэнергии;
- возможность проведения в полевых условиях;
- высокая производительность;
- возможность сварки стыков рельсов в зоне стрелочных переводов;
- достаточная прочность получаемого сварного соединения.
В то же время недостатками являются:
- отсутствие разработанной технологии сварки при пониженных температурах;
- зависимость от качества термитной смеси.
Как стыковой, так и бесстыковой пути должны выполнять одни и те же задачи, основными из которых являются:
- обеспечение бесперебойной работы железнодорожного транспорта;
- обеспечение безопасности перевозки пассажиров;
- обеспечение сохранности грузов;
- долговечность как самого груза, так и подвижного состава и т.п.
Стыковой и бесстыковой пути находятся при одних и тех же условиях, которые оказывают различное влияние на их работоспособность.
Таким образом, экономически более выгодно для прокладки нового железнодорожного бесстыкового пути использовать контактную сварку, а для ремонта и текущего содержания пути и приварки стрелочных переводов – термитную.
Влияние внешних условий на сохранение работоспособности железнодорожного пути
Природные колебания температур в достаточно широком интервале от – 40 до + 60 °С влияют на эксплуатацию рельсовой колеи. При значительном понижении температуры происходит укорочение рельсов по длине. При таком укорочении зазоры в стыках увеличиваются [47].
В бесстыковом пути полное отсутствие зазоров приводит к возникновению значительных внутренних растягивающих напряжений при отрицательных температурах, что, в конечном итоге, может вызвать разрыв рельса по всей плоскости его поперечного сечения. Такие разрывы очень опасны, т.к. являются одной из
причин схода подвижного состава во время движения, приводящего к крупным авариям и крушениям [227].
При повышении температуры окружающей среды и отсутствии облачности рельсы могут нагреваться до 60 °С. При несоблюдении условий эксплуатации, отсутствие зазоров в рельсовых плетях вызывает возникновение значительных внутренних напряжений сжатия, которые приводят к выбросам рельсошпальной решётки (рисунок 55) [228]. Это вызывает необходимость приостановки движения поездов на данном участке и проведения внепланового ремонта и текущего содержания пути.
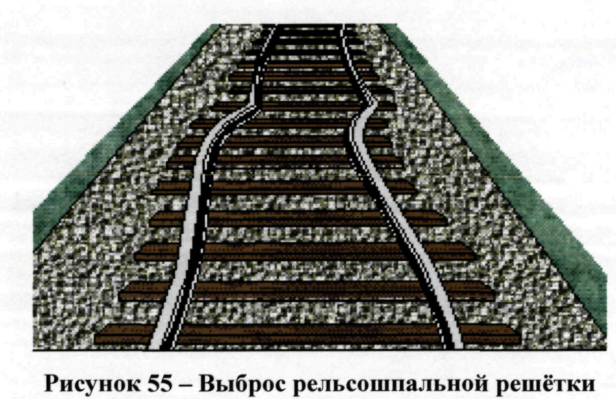
Таким образом, зазоры необходимы в бесстыковом пути, как при повышении, так и при повышении температуры окружающего воздуха. До недавнего времени такие зазоры предусматривались в бесстыковом пути через каждые 800 м [48, 57].
Применение температурно-напряжённого бесстыкового пути позволяет увеличить длину бесстыковой плети до длины перегона, однако требует ужесточения условий эксплуатации.
Описание процесса алюминотермитной сварки
Термит, употребляемый для сварки рельсов, изготавливается из железной окалины – отходов сталепрокатного производства и металлического алюминия. Их размельчают до получения зёрен диаметром от 0,1 до 2,5 мм. Первичный алюминий должен содержать не менее 98-99 % чистого алюминия. Перед размолом окалина должна быть хорошо обожжена с целью удаления из неё влаги и масла.
Пыль из размельчённой окалины и алюминия удаляется воздушным сепаратором. Окалина по своему химическому составу различна. Чем меньше в окалине кремния, тем она лучше для получения сварочного термита. Содержание в окалине кислорода не должно быть ниже 25 %.
Железо с кислородом может образовать три окисла: FeO – закись железа; Fe203 – окись и Fe304 – закись-окись.
При нормальных условиях составляющие термитной смеси не вступают во взаимодействие, но если термитную смесь подогреть до 1100-1200 °С, то между её компонентами начинается химическая реакция. В результате этой реакции металлический алюминий соединяется с кислородом окалины и превращается в окись алюминия, а окалина, отдавая кислород алюминию, превращается в железо. Эта реакция идёт с большим выделением тепла, поэтому если она уже началась, то далее продолжается произвольно, нарастающими темпами и прекратить её невозможно – она неуправляемая. Химическая реакция выражается следующим образом [34, с. 473; 53, с.72; 54, с. 88; 208; 217; 229; 230]:
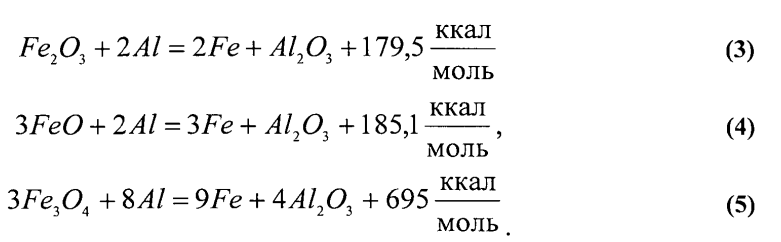
Термитная смесь содержит по весу 23,7 % алюминия и 76,3 % окалины. При сгорании 1,0 кг термитной смеси выделяет 762 ккал тепла, что позволяет получить температуру разогретого металла порядка 2700-3000 °С.
Окалина и алюминий могут содержать различные примеси. Поэтому процент содержания алюминия и окалины в термитной смеси рассчитывается с учётом чистоты алюминия и содержания кислорода в окалине. Практика термитной сварки показала, что окалины в термитной смеси должно быть на 7-8 % больше расчётного содержания. Тогда термитный металл получается плотнее и лучше сваривается с металлом рельса.
Чтобы лучше использовать образующееся при реакции тепло и увеличить выход металла, в термитную смесь для сварки рельсов при изготовлении добавляют мелко измельчённые кусочки стали – отходы гвоздильного производства. При расплавлении сталь увеличивает выход термитного металла и понижает начальную температуру продуктов реакции термита. В зависимости от веса порции термита в термитную смесь добавляют этих отходов (называемых обсечкой) от 12 до 20 % к весу предполагаемого выхода термитного металла. Для улучшения механических свойств металла сварного шва в термитную смесь вводят ферросплавы, в большинстве случаев ферромарганец, ферросилиций, ферромолибден, фер- ротитан, феррованадий. Ферросплавы обуславливают получение термитного металла с механическими свойствами, близкими к металлу свариваемых рельсов.
Для сварки рельсов в настоящее время применяется способ промежуточного литья (рисунок 56) [54, с. 89], при котором из продуктов термитной реакции используется только расплавленный металл 5 без шлака 4 [53, 54].
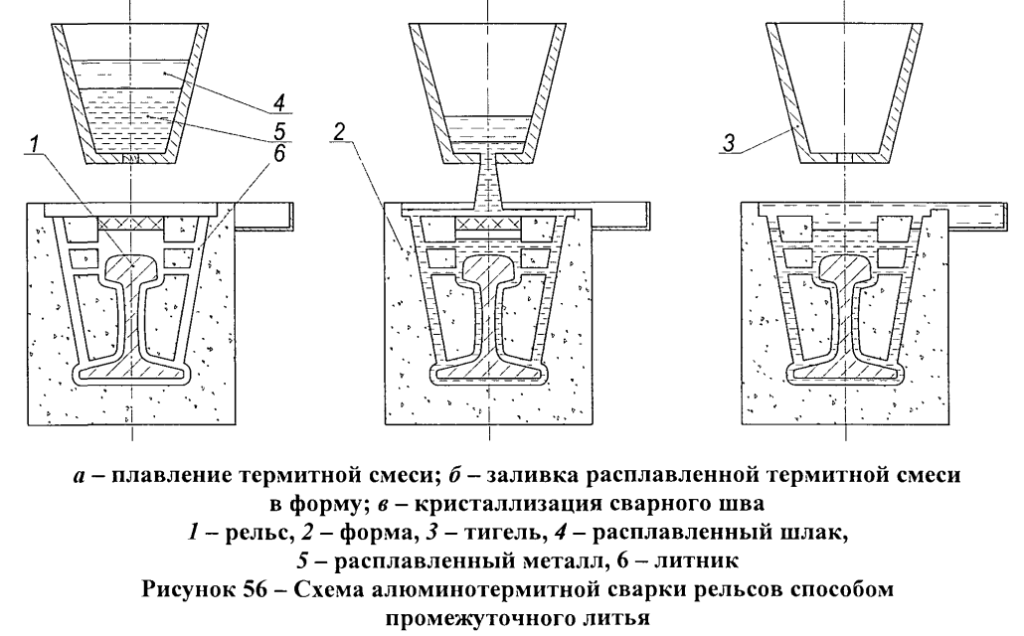
Жидкий металл является одновременно источником тепла и присадочным материалом, соединяющим концы рельсов 1. Свариваемые концы рельсов при этом способе устанавливаются с зазором 25±1 мм и заключаются в соответствующие для данного способа сварки формы 2. Для сжигания термита при сварке способом промежуточного литья применяется конический тигель 3 с выпускным отверстием в дне. Расплавленный металл заливается из тигля в форму и заполняет оставленный между торцами рельсов зазор, начиная с подошвы рельсов, куда попадает через специальный литник 6. Постепенно заполняя зазор и свободное пространство между рельсами и стенками формы, металл вызывает расплавление соприкасающихся с ним стенок рельсов, а, застывая, образует с рельсами одно целое – сварное соединение. Вытекающий из тигля за металлом шлак стекает по жёлобу, оставляя над металлом лишь слой небольшой толщины.
Этот слой шлака предохраняет термитный металл от быстрого остывания, чем способствует более свободному выделению газов из жидкого металла и получению более плотного металла.
В середине XX в. стыковая контактная сварка вытеснила алюминотермит- ную. В настоящее время в России алюминотермитная сварка получила своё второе рождение, в первую очередь, при соединении рельсов в районе стрелочных переводов, так как контактные машины по ряду причин не могут быть применены в этих местах. В их числе невозможность подсоединения захватов контактных машин в ряде стыков стрелочного перевода и невозможность в стрелочном переводе сделать петлю из рельсов, требуемую при контактной сварке.
Алюминотермитная сварка рельсов выполняется на всех типах стрелочных переводов, а собранных на железобетонных брусьях в обязательном порядке – по схемам, приведённым на рисунке 45.
Кроме того, этот вид сварки, наряду с электроконтактной, применяется для окончательного восстановления лопнувшей бесстыковой плети или вваривания в неё взамен временной рельсовой рубки рельсовой вставки длиной от 3 м.
Алюминотермитная сварка железнодорожных рельсов должна выполняться в строгом соответствии с техническими условиями ТУ 0921-127-01124323-2005 [197]. Нарушение технологии сварки, использование некачественных сварочных материалов и т.п. приводит к дефектам в сварном соединении и может способствовать его разрушению. В таблице 30 приведены данные на начало 2008 г. по дорогам РФ по выявленным дефектам в сварных соединениях рельсов, сваренных алюминотермитной сваркой, с указанием причин образования дефектов [231, с. XIV-46].
Из приведённых данных видно, что основной причиной образования дефекта в стыке является нарушение технологического процесса сварки, причём общее количество дефектов не превышает 0,1 % от сваренных стыков данным методом, что является очень высоким показателем. Сравнивая технологии фирм ЗАО «СНАГА» и «ЭЛЕКТРОТЕРМИТ» видно, что больший процент брака относится к стыкам, сваренным по технологии фирмы «ЭЛЕКТРОТЕРМИТ». Поэтому руководством ОАО «РЖД» была принята технология ЗАО «СНАГА», как основная на сети железных дорог России.
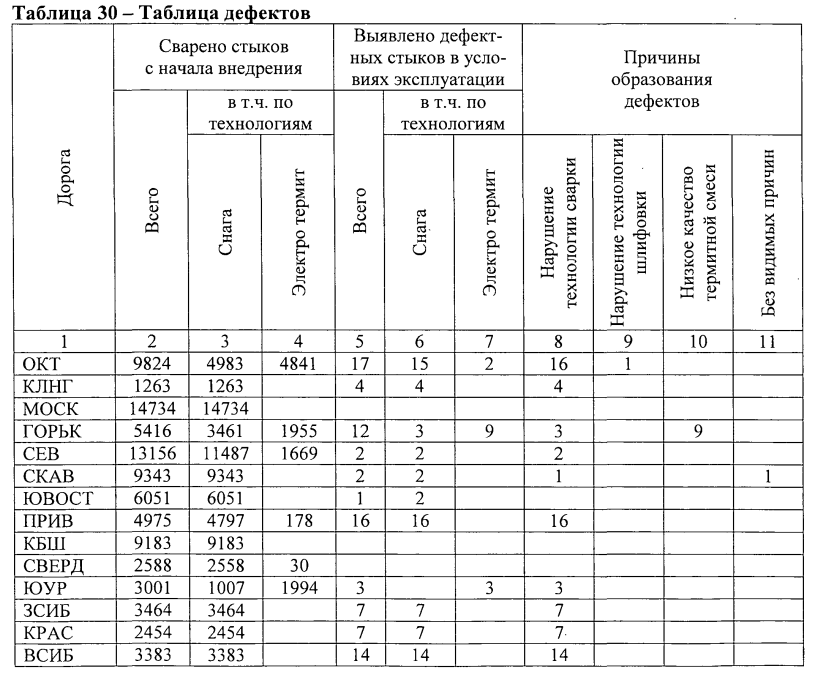

Технология АТСР к настоящему моменту отработана и при её строгом соблюдении брак исключён, но каждое отклонение от заданных параметров может приводить к браку, что, в первую очередь, связано с плохой свариваемостью рельсовой стали. Был проведён (выполнен) ряд работ [56; 58 – 63; 69-71; 232 – 240], направленных на определение влияния технологических параметров, влияющих на качество сварного шва рельсов, сваренных алюминотермитным способом. Такими исследованиями занималась и автор этой работы.
Разработка оборудования и проведение эксперимента по алюминотермитной сварке рельсов
Создание элементов многопламенной горелки для предварительного подогрева концов рельсов и её испытания
К 2004 г. алюминотермитная сварка рельсов приобрела большую популярность в России, поэтому остро встал вопрос о необходимости закупки железными дорогами комплектов оборудования за рубежом для её проведения [50, 51].
Перевод производства в Россию значительно снижал общие расходы на приобретение оборудования. ЗАО «СНАГА» были проведены все подготовительные работы для выпуска оборудования и большинства расходных материалов на предприятиях России. По заказу ЗАО «СНАГА» автором была проведена конструктивно-технологическая проработка, модернизация многопламенной горелки и изготовление опытного образца для предварительного подогрева торцов рельсов перед сваркой.
Было показано, что для выпуска таких горелок целесообразно использовать в качестве сборочной единицы стандартный корпус сварочной горелки, выпускаемой отечественными предприятиями и разработать конструкцию специального наконечника, стыкуемого с ним.
Из выпускаемых отечественной промышленностью разных типов горелок, наиболее подходящей по мощности является горелка ГЗУ-4. Корпус горелки ГЗУ-4 отличается от зарубежного образца посадочными местами и седлом инжектора. Поэтому был заново разработан стыковочный узел корпуса с горелкой, инжектор и инжекторная камера. Для ряда элементов горелки потребовалось проведение уточняющих расчётов, которые были выполнены по известной методике [242, 243].
Горелка для подогрева рельсов состоит из корпуса горелки, специального наконечника и многосоплового мундштука. Конструкция разработанной горелки представлена на рисунке 57.
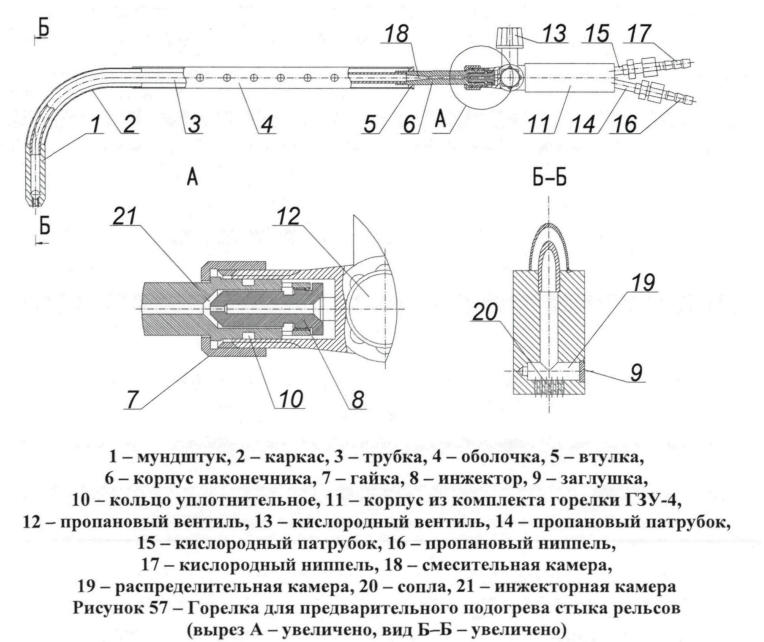
Кислород поступает в горелку по резиновому шлангу, надеваемому на ниппель 17, и патрубку 15, а пропан через ниппель 16 и патрубок 14. Количество поступающего кислорода регулируется вентилем 13, а пропана – вентилем 12, расположенных в корпусе горелки 11. Кислород, пройдя вентиль 13 и инжектор 8, создаёт разрежение в пропановом канале корпуса горелки, благодаря чему пропан засасывается в инжекторную камеру 21 корпуса наконечника 6. В смесительной камере 18 происходит смешение пропана и кислорода, образуется горючая смесь, которая проходит по трубке наконечника 3 в многосопловый мундштук 1. Для получения заданной мощности и размеров газового пламени в конструкции мундштука необходимо иметь 3 ряда сопел (9 + 6 + 9) на базе 24 мм.
Проведённые расчёты позволили определить необходимый диаметр горлового отверстия инжектора и диаметр каждого из сопел мундштука.
Для повышения стойкости мундштука его изготовили из стали 12Х18Н10Т.
Наконечник, многосопловый мундштук и инжектор потребовали ряда конст- – руктивных изменений стандартной горелки, на основании которых был разработан полный комплект чертежей. В него вошли сборочный чертёж, рабочие чертежи всех составляющих горелки, спецификация и технические условия на изготовление опытного образца [50, 51, Приложение Г (справка об участии автора в разработке горелки)].
Организация испытания разработанной горелки и экспериментального определения температур при предварительном подогреве рельсов
Испытания опытного образца горелки проводились на опытном полигоне фирмы ЗАО «СНАГА» при участии автора, представителей фирмы и аттестованных сварщиков термитной сварки. Для данных испытаний были выбраны рельсы Р65. На специальном стенде были закреплены два куска рельсов с зазором 25 мм. Горелка, в соответствии с ТУ 0921-127-01124323-2005 [197] была закреплена на комбинированной стойке (рисунок 58). В соответствии с технологией (Приложение Д), на стык была установлена форма, выполнена обмазка в местах соприкосновения формы с рельсами и проведён предварительный подогрев концов рельсов в течение 8 минут (рисунок 59). Окончание подогрева соответствовало моменту времени, когда торцевые поверхности головок и шеек рельсов достигли температуры близкой к температуре солидус.
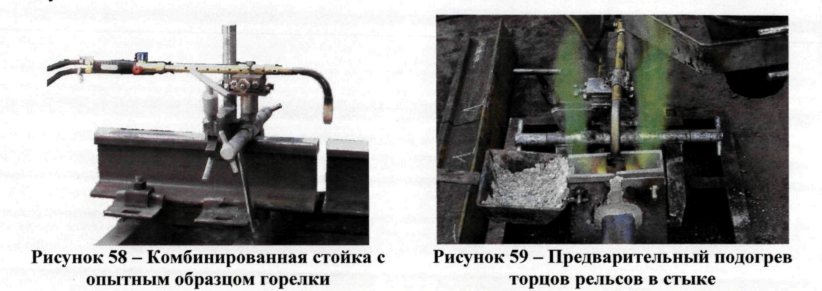
Для анализа характера разогрева торцов рельсов, форма была разрушена и проведён визуальный осмотр характера распределения температур по поверхностям обоих рельсов. Характер распределения температур оказался одинаковым на обоих торцах, что является одним из необходимых условий при проведении прогрева. На рисунке 60 приведены рельсы с разогретыми концами, через некоторый промежуток времени, после разрушения формы.
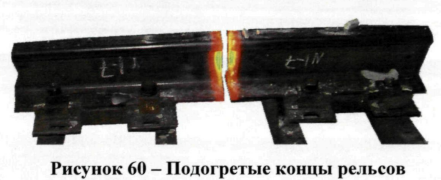
Зона высокотемпературного подогрева торцов свариваемых рельсов составила около 15-20 мм. Технические параметры горелки представлены в Приложении Г. Данная горелка обеспечивает достаточно равномерный подогрев торцов свариваемых рельсов до температуры 1200-1250 °С и имеет возможность плавной регулировки мощности пламени.
После полного охлаждения и зачистки стыка от окалины в одном из рельсов были подготовлены места для замера температур.
В данном эксперименте использовались хромель-алюмелевые термопары (ХА), соединённые с гальванометрами [241]. Температуры определялись в головке, шейке и подошве рельсов на расстоянии 42, 52, 62, 72 и 82 мм от торца рельса, который нагревался газовым пламенем при подогреве (рисунок 61). Из-за необходимости установки на стык рельсов формы расположить термопары ближе к поверхности нагреваемого торца рельса оказалось проблематично.
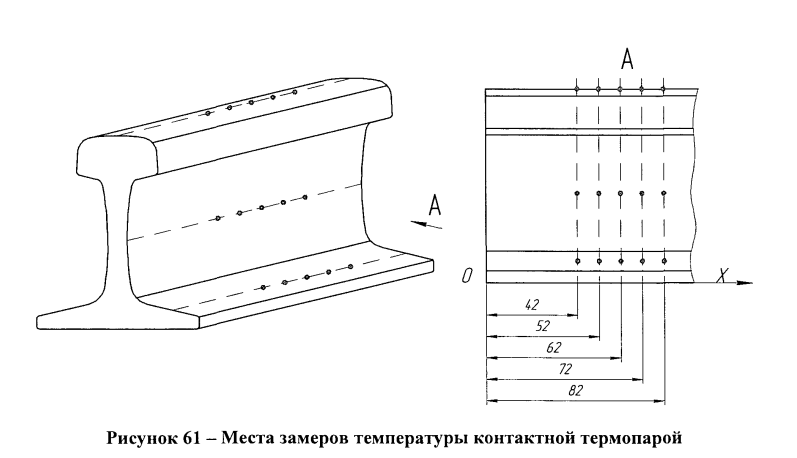
Целью данных экспериментов было определение эффективной мощности разработанной горелки для предварительного подогрева рельсов при алюмино- термитной сварке, чтобы впоследствии можно было проводить численные эксперименты.
На указанных рельсах эксперимент повторялся четыре раза после полного их охлаждения. Полученные результаты экспериментов были обработаны – вычислены средние значения температур в каждой точке. По средним значениям построены термические циклы для каждой точки и распределения температур по длине рельса в головке, шейке и подошве. Полученные данные с помощью программы Microsoft Excel были обработаны с построением линий тренда термических циклов на этапе подогрева в соответствующих сечениях (рисунок 62). Аналогичные термические циклы были получены для других поперечных сечений [70].
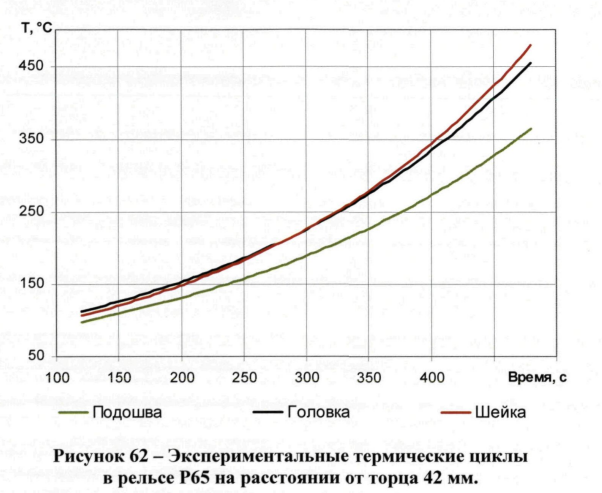
Определение эффективной тепловой мощности пламени горелки при предварительном подогреве
Для проведения численных экспериментов по влиянию технологических параметров на изменение распределения температур и термических циклов в расчётной модели необходимо было задавать эффективную тепловую мощность (ди), которая вводится в рельс при подогреве и может быть определена по зависимости [243, с. 141].

Однако задать к.п.д. горелки с учётом конкретных особенностей данного технологического процесса оказалось затруднительно, т.к. часть тепловой энергии поглощается формой, часть теряется за счёт конвективного и лучистого теплообмена с окружающей средой, значительная часть уносится газовым потоком. Торцы рельсов нагреваются боковыми частями пламени.
В связи с этим, имея экспериментальные значения, было решено провести численный эксперимент по определению температур в ряде точек (см. рисунок 61). Для этого была разработана расчётная модель по определению температур при подогреве торцов рельсов и, меняя в расчётной модели эффективную тепловую мощность, добились соответствия расчётных и экспериментальных значений температур. Вычисленное таким образом значение эффективной тепловой мощности принималось в дальнейших численных экспериментах, как соответствующее действительному вводу тепловой энергии в торцы рельсов.
Распространение теплоты существенно зависит от формы и размеров тела. Обычно формы рассматриваемого тела упрощаются и сводятся к простейшим.
В случае сварки стыка рельсов полученное сварное соединение можно представить в виде трёх полубесконечных стержней, по которым распространяется тепло (рисунок 63).
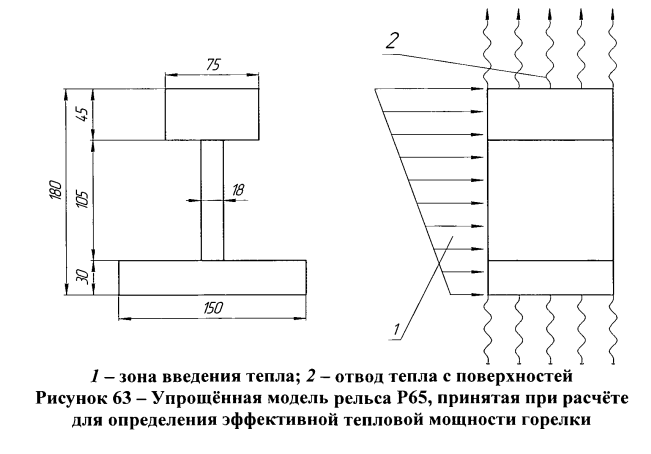
Теплота от мгновенного плоского источника в стержне распространяется в основном в направлении вдоль стержня. Температуру по поперечному сечению стержня можно принять равномерной, а процесс распространения теплоты – линейным, при котором теплофизические коэффициенты не зависят от температуры. Теплоотдача с боковых поверхностей рельсов незначительна, так как на стык и прилегающие участки, непосредственно перед подогревом, устанавливается литейная форма.
Широкое применение для решения задач теплопереноса имеют аналитические и численные методы: метод конечных элементов (МКЭ) и метод конечных разностей (МКР).
Для получения распределения температур для рельса с известными физическими свойствами условия однозначности сводятся к заданию начального и граничного условий.
Начальные условия для уравнения теплопроводности состоят в задании температуры во всех точках М области С в момент /=0, от которого ведётся отсчёт времени.
В случае равномерного распределения температуры в теле начальное условие упрощается:

В задачах теплопроводности используются следующие типы граничных условий. Граничные условия первого рода – определяют закон об изменении температуры точек поверхности тела. Граничные условия второго рода – задаётся плотность теплового потока на поверхности тела как функция координат и времени [244, с. 147-148]:

или мощность источника тепла. Граничные условия третьего рода – задаётся температура окружающей среды и закон конвективного теплообмена между поверхностью тела и окружающей средой.
Для описания процесса теплообмена используется закон Ньютона, согласно которому количество тепла (^2), отдаваемого единицей площади поверхности 5 с температурой Т в единицу времени в окружающую среду с температурой Тс в процессе охлаждения, пропорционально разности температур поверхности тела и окружающей среды [244, с. 148]:

где а – коэффициент полной поверхностной теплоотдачи.
Коэффициент полной поверхностной теплоотдачи характеризует интенсивность теплообмена между поверхностью тела и окружающей средой. Он отражает совместные действия конвекции и излучения, и зависит от ряда факторов [244 – 246].
Применительно к рельсу можно реализовать граничные условия первого или второго рода, а на боковых поверхностях – граничные условия третьего рода.
Одним из основных факторов, определяющих распределение температур в рельсе при подогреве, является вводимая мощность. Для оценки распределения температуры в рельсе была выделена зона, в которую вводилось тепло от пропа- но-кислородной горелки (рисунок 63).
В качестве базового, для последующего анализа влияния мощности теплового источника при подогреве, на распределение температур приняты следующие граничные условия: в рельс вводится тепло различной мощности; происходит конвективный теплообмен с окружающей средой; температура окружающей среды Гс=20 °С.
Расчёт производился с помощью программного комплекса «Поле-аналитик», разработанного на кафедре «Технология сварки, материаловедение, износостойкость деталей машин» (ТСМИ) МИИТ [247]. При расчётном определении температур в узлы расчётной модели, соответствующие торцевой поверхности рельса, вводилась тепловая мощность, соответствующая теплу, выделяемому пламенем горелки при подогреве рельсов. Теплофизические коэффициенты принимались не зависящими от температуры, расчёт выполнялся пошагово. Время нагрева составляло 480 с, что соответствовало времени подогрева рельса при экспериментальном замере температур на натурных образцах.
При анализе температурных полей была выявлена их некоторая неравномерность распределения по сечению рельса.
Проведённое сопоставление результатов расчёта по МКЭ и экспериментальных данных (рисунок 64) показало удовлетворительное их соответствие – расхождение не превышает 12- 15 %, что вполне приемлемо для подобных расчётов. Аналогичные результаты получены и для других точек рельсов, в которых были проведены экспериментальные замеры температур в разные моменты времени при их предварительном подогреве.
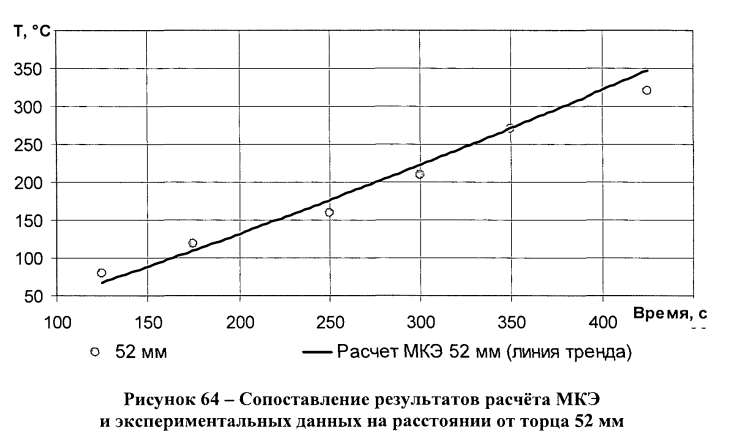
Таким образом, в результате проведённых численных экспериментов, сопоставляемых с результатами натурных экспериментов, была определена эффективная тепловая мощность, соответствующая реальной мощности, вводимой при подогреве в рельс – 5600 Дж/с.
Численный анализ температурных полей и скоростей охлаждения при алюминотермитной сварке рельсов
Рельсы изготавливают из углеродистой спокойной раскисленной стали, которую выплавляют в конверторах, мартеновских и электропечах. Рельсовая сталь может легироваться: ванадием, кремнием, хромом и титаном.
В настоящее время большинство железнодорожных рельсов изготавливается из рельсовой стали марки М76 по ГОСТ Р 51685-2000, для которой стандартом определены следующие пределы содержания основных химических элементов: С – 0,71-0,82 %; Мп – 0,75-1,05 %; Si – 0,25-0,45 %; Р – 0,035 %; S – 0,040 %; AI – 0,025 %.
Наличие в рельсовой стали и металле сварного шва высокого содержания углерода при ускоренном охлаждении может приводить к образованию закалочных структур в отдельных зонах поперечного сечения рельса, снижающих пластичность. Поэтому важно знать скорости охлаждения в различных зонах сварного соединения.
Для проведения численных экспериментов по анализу тепловых процессов при алюминотермитной сварке рельсов была использована программа, разработанная на кафедре ТСМИ МИИТ P.A. Королёвым [234], основанная на методе конечных разностей. Разработанная расчётная модель повторяет форму поперечного сечения железнодорожных рельсов, используемых при проведении эксперимента. Свариваемые рельсы были заменены полубесконечными стержнями с площадью поперечного сечения F и периметром р, соответствующими площади поперечного сечения и периметру свариваемых типов рельсов. Распределение температуры в поперечном сечении стержней на этом этапе расчёта принималось постоянным для каждого поперечного сечения рельса, но переменным по его длине. Теплообмен нагретой части рельса с окружающей средой учитывался с помощью коэффициента поверхностной теплоотдачи и принимался равным [244, с. 151]:

Для расчёта распределения температуры в поперечном сечении свариваемых стержней в расчётную модель второго этапа было введено поперечное сечение, форма которого максимально приближена к форме поперечного профиля желез
нодорожного рельса в зависимости от его типа, регламентированного ГОСТР 51685-2000. На рисунке 65 показана замена реального поперечного профиля железнодорожного рельса типа Р50 (сплошная линия) расчётным профилем поперечного сечения рельса (штриховая линия). При этом обязательным условием является равенство площадей обоих поперечных сечений.
Такой подход при решении задачи теплопроводности для рельса, имеющего постоянное поперечное сечение по длине, позволяет существенно уменьшить количество вводимой информации в расчётную модель и сократить время счёта, а для сечений, в которых необходимо проанализировать неравномерность распределения температур по поперечному сечению, выполняется второй этап расчёта. Такие приёмы часто используются в инженерной практике для решения сложных и громоздких задач [248].
При решении температурной задачи сварки рельсов алюминотермитным способом, совместно с P.A. Королевым была разработана методика с использованием данного подхода [56; 249; 250]. Данная методика подробно рассмотрена в [234].
В расчётах принималось, что свариваются одинаковые рельсы между собой, а, следовательно, тепловые процессы в них протекают симметрично относительно оси сварного шва, поэтому можно рассматривать только половину модели.
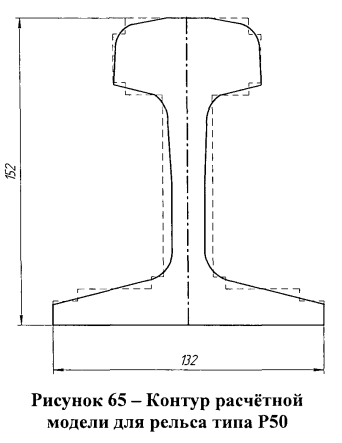
При решении температурной задачи сварки рельсов алюминотермитным способом, совместно с P.A. Королевым была разработана методика с использованием данного подхода [56; 249; 250]. Данная методика подробно рассмотрена в [234].
В расчётах принималось, что свариваются одинаковые рельсы между собой, а, следовательно, тепловые процессы в них протекают симметрично относительно оси сварного шва, поэтому можно рассматривать только половину модели.
В качестве начальных условий первого этапа расчёта температура рельса принималась равной температуре окружающей среды, а на втором этапе – распределению температур, после этапа подогрева и технологической паузы. Граничными условиями первого этапа расчёта являлось граничное условие второго рода (постоянный удельный тепловой поток) – на нагреваемом торце рельса и граничное условие первого рода (изотермическая граница), а на втором этапе – частный случай граничного условия второго рода (адиабатическая граница).
На первом этапе (предварительный подогрев) в рельс с одного торца вводится количество теплоты, зависящее от мощности пламени газовой горелки, с помощью которой выполняется предварительный подогрев [243, с. 140; 244, с. 197]:
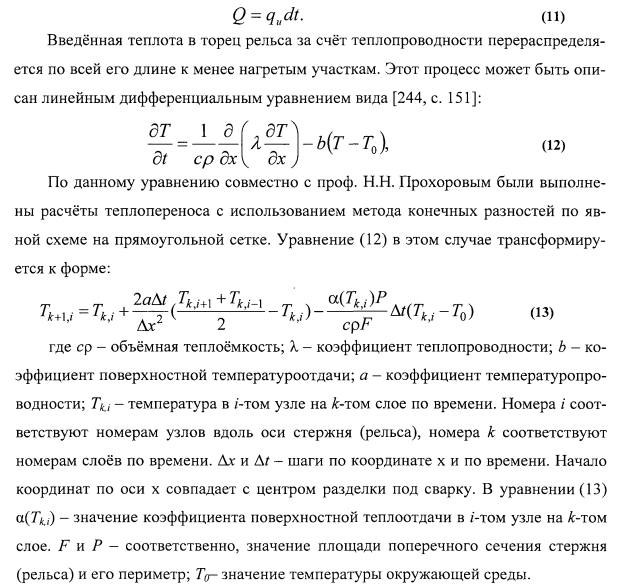
Согласно технологическому процессу после окончания предварительного подогрева наступает «технологическая пауза», в период которой убирают газовую горелку, устанавливают тигель с термитом над формой, поджигают термитную спичку, а от неё термитную смесь в тигле. Заканчивается «технологическая пауза» завершением термитной реакции и выпуском расплавленного термитного металла в литейную форму. В период «технологической паузы» за счёт процессов теплопроводности происходит лишь перераспределение температуры, поэтому в расчётной модели это предусмотрено отсутствием ввода тепла в какие-либо её места.
Затем, наступает этап сварки, на котором тепло вводится однократно вместе с заливкой расплавленного термитного металла в форму. Для расчётной модели это соответствует вводу тепла в узлы сетки расчётной модели и перераспределения температуры в ней за счёт протекания процессов теплопроводности.
Перераспределение температуры в плоскости расчётного поперечного сечения представляет собой процесс, который описывается линейным дифференциальным уравнением вида [244, с. 151]:
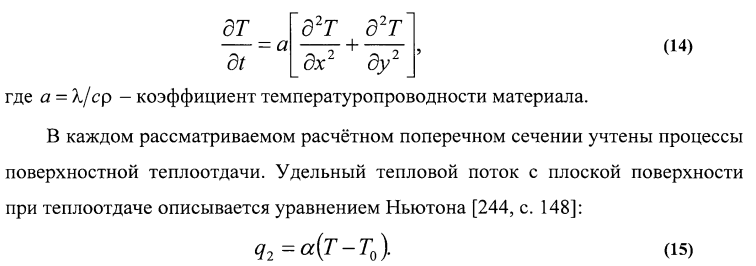
В расчётной модели учтено, что часть рельса находится в форме и теплообмен идёт в этом месте между рельсом и формой. Поэтому было принято допущение, что при подогреве часть рельса, заключённая в форме и сама форма имеют одинаковые температуры.
На этапе сварки, начиная с момента заливки расплавленного термитного металла и до момента разрушения формы, учитывается её влияние, что было замечено на ряде кривых, описывающих термические циклы. Решение задачи теплопроводности с учётом нелинейности теплофизических коэффициентов [234] показало, что на этапе нагрева кривые термических циклов несколько отличаются по значениям температур от термических циклов рассчитанных с постоянными теплофизическими характеристиками материала. На этапе охлаждения эти расхождения температур незначительны – особенно при определении скоростей охлаждения. На основании этих исследований в данной работе теплофизические характеристики материала принимались постоянными, а расчёт проводился по линейному дифференциальному уравнению (12).
Для верификации были проведены экспериментальные замеры температур с помощью термопар и пирометра. Пирометр не дал возможность получить значения температур с необходимой точностью [237].
С учётом возможного повреждения средств измерения температуры во время проведения операций монтажа сварочной формы и уплотнения мест сопряжения формы с рельсом, минимально возможное расстояние расположения термопар составило 50 мм от торца рельса.
С точки зрения безопасности, нахождение людей вблизи горелки на этапе подогрева нежелательно, а на этапе сварки нахождение персонала ближе 5 м от места сварки – запрещено, так как горение термитной смеси происходит бурно и сопровождается выбросом искр. Поэтому, разработка методики определения температур была разработана с учётом описанных выше технологических особенностей процесса алюминотермитной сварки рельсов способом промежуточного литья. Схема расположения термопар разрабатывалась с учётом возможности подтверждения или опровержения полученных ранее значений. Расчёт температур в поперечном сечении показал неравномерное распределение температуры. Максимальные значения температуры достигаются в головке рельса, а при переходе к шейке рельса происходит заметное понижение максимальных значений температур. Поэтому, термопары были расположены следующим образом. Вдоль рельса на поверхности катания головки рельса были расположены три термопары. На расстоянии 50 мм, 60 мм и 70 мм от торца рельса. И одна термопара была расположена в средней части шейки рельса на расстоянии 60 мм от торца рельса (рисунок 66). Такое расположение термопар позволило провести измерение температур во время проведения всего процесса сварки как по длине рельса (термопары, расположенные на поверхности катания головки рельса), так и в поперечном сечении
рельса (термопары, расположенные на расстоянии 60 мм от торца рельса, соответственно в шейке и головке рельса).
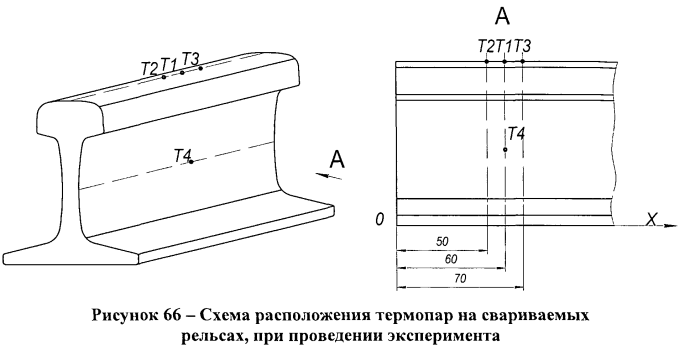
Для проведения экспериментальных исследований из стандартных железно-дорожных рельсов типа Р50, соответствующих требованиям ГОСТ Р 51685-2000 “Рельсы железнодорожные. Общие технические условия”, были изготовлены на-турные образцы, длиной 1 м каждый.
Для размещения и закрепления термопар как на поверхности катания головки рельса, так и в средней части шейки рельса выполнялись отверстия, соответствующие диаметрам термопар, глубиной 5 мм. Закрепление термопар производилось с помощью специальных клиньев. В качестве инструмента для записи получаемых данных использовался ноутбук “Toshiba”, а для анализа и обработки – специальная приставка “Dock Station” . Применение данного оборудования дало возможность производить и регистрировать 154 измерения температуры в секунду с каждой термопары. Измерение температуры производилось на протяжении всего процесса проведения алюминотер- митной сварки как на этапе предварительного подогрева и технологической паузы, так и на этапе сварки, после заливки расплавленной термитной смеси и последующей кристаллизацией и охлаждением сварного соединения. Погрешность измерений составляет ± 15 °С. Краткое описание технологического оборудования и основные операции При проведении эксперимента, предварительный подогрев производился на протяжении 7 мин; технологическая пауза длилась 1 мин; разрушение сварочной формы было произведено через 4 мин после заливки расплавленной термитной смеси. Для исключения повреждения термопар, завершающие операции по доводке полученного сварного соединения не проводились.
В результате проведённых экспериментальных исследований для каждого из технологических этапов, были построены термические циклы (рисунок 67). Окончанию предварительного подогрева газовой горелкой соответствует момент времени 420 с, а завершению технологической паузы – 480 с. Результаты измерений температур, полученные на этапе сварки, приведены для первых 300 с.
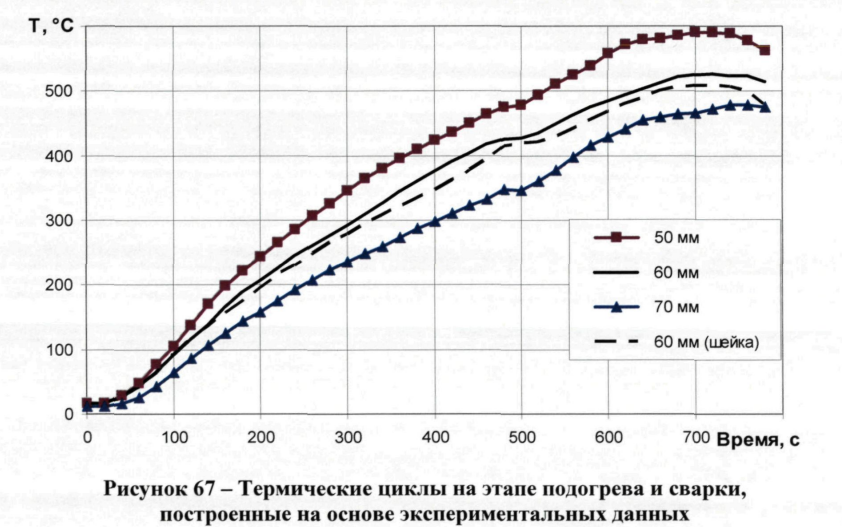
Все кривые имеют одинаковый характер: монотонно возрастают на всем временном промежутке (как во время предварительного подогрева, так и во время технологической паузы). Это объясняется тем, что термопары расположены на расстоянии от нагреваемого торца, нагрев данных точек происходит за счёт тепла перераспределяющегося от торца рельса за счёт процессов теплопроводности. Теплота подходит к данным точкам с некоторым «запозданием по времени» поэтому, хотя предварительный подогрев прекращается в момент времени 420 с и до момента времени 480 с длится технологическая пауза, кривые термических циклов продолжают возрастать.
На этапе сварки температуры во всех точках расположения термопар продолжают увеличиваться. Через 250 с после заливки расплавленного термитного металла начинается постепенное понижение температур во всех точках замера температур, к этому моменту сварочная форма разрушена.
Для сопоставления данных, получаемых при расчёте с использованием разработанных моделей и вычислительных алгоритмов с данными, полученными в результате экспериментальных исследований, были проведены расчёты, моделирующие условия эксперимента [237].
Сопоставление экспериментальных данных и расчётных, полученных с использованием разработанных моделей и алгоритмов, на этапах предварительного подогрева и сварки приведено на рисунке 68.
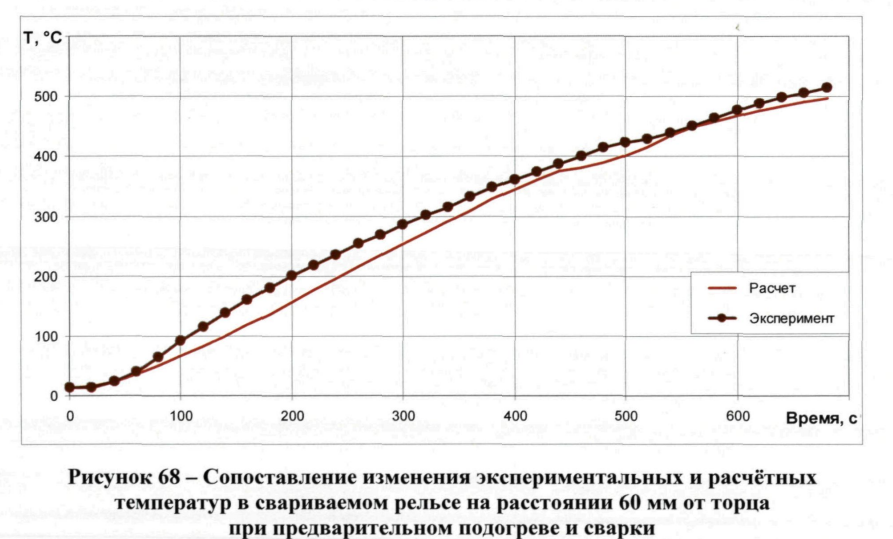
При сопоставлении средних температур, полученных экспериментально со средними температурами, полученными при расчёте с использованием разработанных расчётных моделей и вычислительных алгоритмов, было установлено следующее. На этапе предварительного подогрева максимальное процентное рас-хождение между экспериментальными значениями и значениями, полученными при расчёте температурных полей, термических циклов и скоростей охлаждения составляет 15-16 %.
Особенности распределения температур и скоростей охлаждения по длине рельса при их алюминотермитной сварке
При анализе распределения температур по длине рельса были выполнены различные математические эксперименты отличающихся мощностью источника предварительного подогрева, продолжительностью технологической паузы, температурой окружающей среды и т.п. В качестве примера на рисунке 69 приведены распределения температур для мощности источника предварительного подогрева в 4 и 7 кВт. Изменения температур показаны в виде аксонометрических поверхностей, в периодах предварительного подогрева, перераспределения теплоты залитого термитного металла и последующего охлаждения.
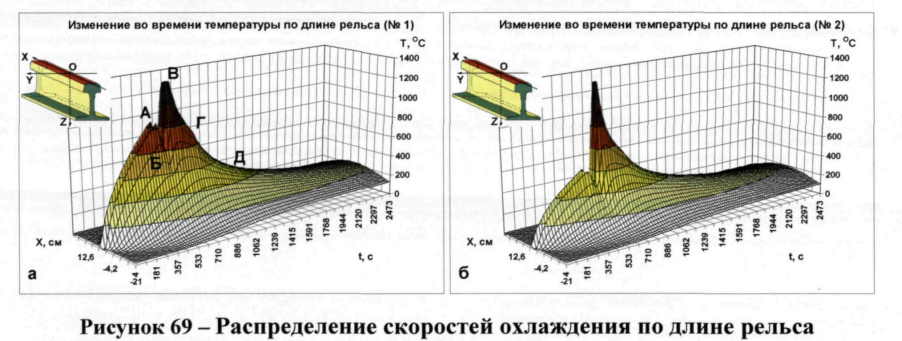
На рисунке 69а показаны перераспределение температур по длине рельса во времени когда мощность источника предварительного подогрева составляет 7 кВт, длительность подогрева – 447 с, длительность технологической паузы – 60 с и длительность существования формы после заливки термитного металла – 250 с. Соответствующие моменты времени на рисунке отмечены буквами А – Д.
Из рисунка 69а видно, что в период действия источника предварительного подогрева, температура на поверхности нагреваемого торца рельса возрастает от 0 до температуры выше 1000 °С (точка А). В зазоре на этапе предварительного подогрева металл отсутствует, поэтому между двумя отмеченными точками А температура воздуха не показана. После окончания предварительного подогрева, во время технологической паузы, происходит неизбежное остывание торцов рельса это явление отражено снижением температуры «от точки А до точки Б». Далее следует заливка термитного металла и происходит соответствующее возрастание температуры до
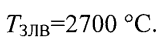
После заливки металла происходит остывание сварного соединения, причём центральная его часть остаётся, защищена керамической формой. Соответствующий фрагмент на рисунке 69а находится в интервале между точками В и Г. В момент, соответствующий точке Г, когда происходит удаление керамической формы, на кривой 71(0, t) наблюдается излом. До точки Г скорость охлаждения (производная dT/dt) оказывается ниже по абсолютной величине, после точки Г эта скорость оказывается выше.
Последующее остывание рельса приводит к тому, что температура на оси шва становится все ниже и распределение её по длине рельса становится все более пологим. Оценка скоростей охлаждения металла С06/5 выполняется при остывании до температуры ниже 550 °С. Соответствующая точка на рисунке 69а отмечена буквой Д.
Аналогичный расчёт поверхности Т(Х, t) выполнен при мощности источника предварительного подогрева 4 кВт. Остальные параметры, характеризующие условия сварки, оставлены без изменения (пример №2). Результаты расчёта температур для примера №2 показаны на рисунке 696. Здесь так же наблюдаются все выше отмеченные эффекты, однако, как это отчётливо видно, температура, обеспеченная предварительным подогревом на торце рельса, оказывается существенно ниже и составляет около 600 °С.
Общий характер изменения во времени распределения мгновенных скоростей охлаждения по длине рельса, применительно к примеру №2, проиллюстрирован в виде аксонометрической поверхности на рисунке 70.
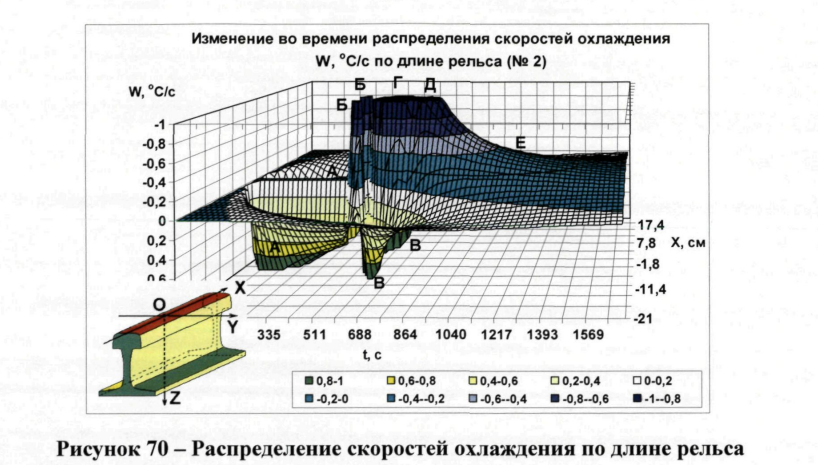
Окончание этапа предварительного подогрева торцов рельсов на рисунке 70 буквой А. После окончания подогрева происходит интенсивное остывание метал¬ла. Соответствующие области на рассматриваемой поверхности отмечены буквами Б. По окончании технологической паузы, после заливки термитного металла он претерпевает нагрев. Этому эффекту соответствуют две области, отмеченные буквой В. На рисунке 70 скорости охлаждения металла ограничены значением – 1 °С/с, а скорости нагрева значением +0,6 °С/с. На самом деле эти скорости зна¬чительно выше и могут при определённых условиях достигать десятков [°С/с]. Периоду остывания рельса соответствуют области отмеченные буквами Д и Е. Следует указать, что благодаря удалению керамической формы, как отмечено выше (см. рисунок 69а, точка Г), происходит скачкообразное изменение скорости остывания металла. На рисунке 70 видно, что в соответствующий момент и близ¬кие интервалы времени, изменение температуры в точках, прилежащих к сварно¬му шву, происходит по кривым не с одним, а несколькими точками перегиба.
Область Е на рисунке 70 соответствует периоду процесса равномерного ос-тывания металла шва и околошовной зоны. Именно в этой области, в дальнейшем, необходимо найти значения скоростей охлаждения соответствующие минимальной устойчивости аустенита.
Перспективы использования алюминотермитной сварки для получения бесстыковых соединений рельсов
На процесс сварки большое влияние оказывают низкие температуры окружающей среды. С понижением температуры увеличивается скорость охлаждения и ускоряется кристаллизация расплавленного металла сварочной ванны, в результате чего частички шлака и выделившиеся газы могут не успевать всплыть, насыщая металл порами и шлаковыми включениями.
Повышенный отвод тепла от нагретого металла и увеличение содержания в нём газов способствуют образованию микротрещин в шве и околошовной зоне. На сварочных материалах возможна конденсация влаги, что также способствует попаданию водорода в металл шва.
С понижением температуры сталь становится все более чувствительной к концентраторам напряжений; ими могут быть мельчайшие внутренние и внешние дефекты наплавленного металла, которые в условиях отрицательных температур могут привести к образованию микротрещин. Остаточные сварочные напряжения, особенно в зонах их концентрации, таких, как переходы от наплавленного металла к основному, наплывы, поры, выходящие на поверхность и другие подобные дефекты, оказывают большее влияние на зарождение и образование трещин. Кроме того, сварщики вынуждены выполнять ряд технологических операций голыми руками, что в условиях низких температур может привести к их переохлаждению.
Для определения качества сварного стыка рельсов, сваренного при низкой температуре, были проведены контрольные эксперименты в отапливаемом цехе при температуре воздуха плюс 19 °С и в ангаре, имеющем температуру минус 15 °С, такую же как и у окружающей среды в момент проведения эксперимента [238]. Процесс сварки рельсов Р65 Нижнетагильского завода алюминотермитным способом в данных экспериментах выполнялся согласно существующим техническим условиям [197]. После сборки стыка на специальном стенде, был проведён подогрев формы и концов рельсов газовой горелкой в течение 10 минут до температуры приблизительно 1200 °С. Так как температура окружающей среды была ниже, чем предусмотрена техническими условиями [197], то продолжительность подогрева потребовалось увеличить, а мощность пламени использовать максимальную из рекомендуемых.
После кристаллизации термитного металла форма была разрушена, для удаления прибыльной части сварного шва. При дуговой сварке, в том числе и ванным способом, ответственных конструкций для снижения скорости охлаждения стыки закрывают асбестом, который можно снимать только после остывания шва до 100 °С и ниже. При алюминотермитной сварке прибыльную часть необходимо удалить практически сразу после кристаллизации, иначе потребуется мощное дополнительное оборудование и значительные трудозатраты.
После проведения шлифовки головки рельса его оставили остывать на холодном воздухе. Когда рельс полностью остыл, провели испытание на малогабаритном специализированном прессе МПС-300, предназначенном для испытания сваренных образцов рельсов методом статического изгиба до их полного разрушения с автоматической регистрацией величин разрушающего усилия (прочности) и стрелы прогиба (пластичности) сварного стыка. Испытание проводилось при приложении усилия к головке рельса. Результаты испытаний приведены в таблице 31, из которой видно, что как по прочности, так и по пластичности стык, сваренный при температуре окружающей среды минус 15 °С, не удовлетворяет существующим нормативным требованиям.
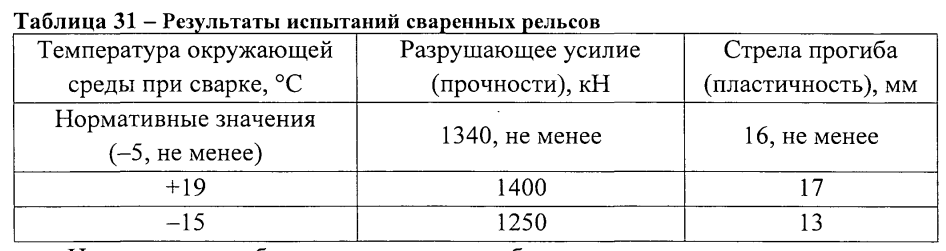
Используя разработанную программу, было проанализировано влияние температуры окружающей среды на скорость охлаждения в диапазоне от +40 до – 40 °С. Результаты расчётов проиллюстрированы на рисунке 71, где показаны средние скорости охлаждения в различных поперечных сечениях рельсов.
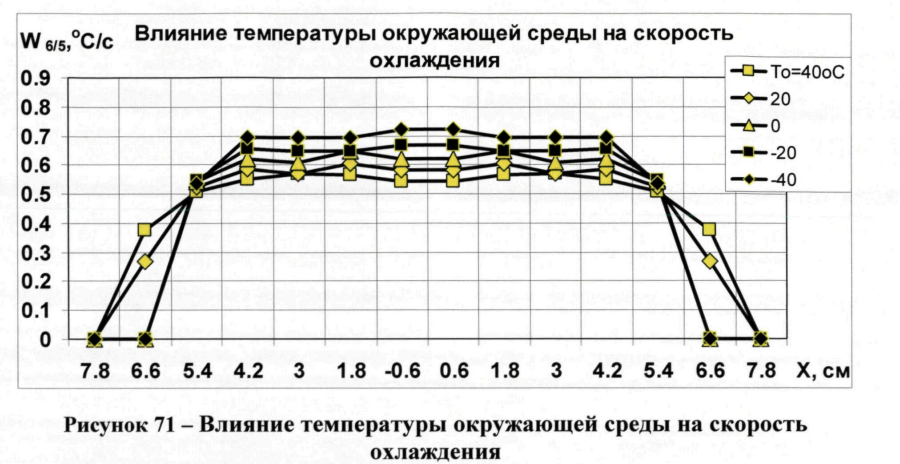
Из приведённых данных видно, что с повышением температуры окружающей среды (Т0) скорости охлаждения металла в интервале температур 600-500 °С (сОб/5) на базе значений X, соответствующих зон термического влияния (ЗТВ), уменьшаются, при этом протяжённость ЗТВ, как и следовало ожидать, увеличивается. В поперечном сечении имеет место неравномерное распределение скоростей охлаждения (рисунок 72): в головке меньше средних, а на периферии подошвы (в пере) – возрастают. Из рисунка 72 видно, что в крайних точках подошвы скорости охлаждения почти в два раза выше, чем в головке рельса, что подтверждает (объясняет) полученные экспериментальные значения снижения разрушающего усилия и стрелы прогиба при испытании рельсов сваренных при отрицательной температуре.
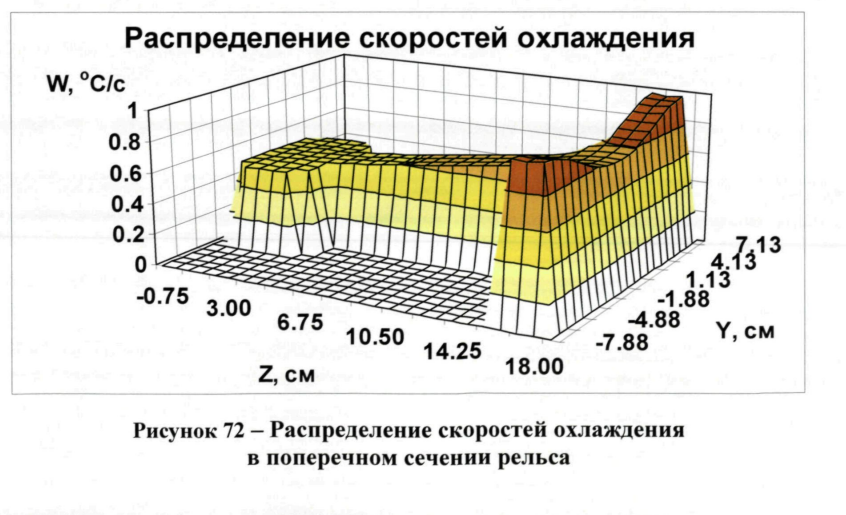
Проведённые исследования показали, что при некотором усложнении технологии сварки рельсов алюминотермитным способом их можно будет сваривать не только при положительных температурах, но и при любых отрицательных. Это даст возможность восстанавливать лопнувшие рельсы в зимний период, не дожидаясь среднесуточных положительных температур окружающей среды, тем самым сократить продолжительность пребывания плети в состоянии временно восстановленной и снизить затраты на её содержание, а также продлить сроки выполнения сварочных работ алюминотермитным способом и в зимний период.
На основании проведённых исследований была подана заявка на предполагаемое изобретение, по которой получен патент РФ . на изобретение №2464141 «Способ алюминотермитной сварки рельсов при отрицательных температурах» [52; 71; 237; 238].
Основные результаты и выводы
- Проведённый анализ рельсовых скреплений показал, что за период существования железных дорог было предложено несколько вариантов соединения рельсов. Наиболее распространённым является болтовое соединение. К его недос-таткам относятся:
• высокая шумность от удара колёс по стыкам рельсов;
• низкая скорость движения поездов;
• наличие блуждающих токов и др. - Неразъёмные (сварные) стыки лишены недостатков, присущих болтовым, и позволяют повысить скорость движения поездов, комфортабельность перевозки пассажиров и грузов, существенно снизить износ рельсов и ходовых частей и т.п. Однако трудозатраты по укладке новых и замене старых рельсов увеличиваются, но окупаются за счёт существенного снижения затрат на ремонт деталей ходовых частей вагонов и локомотивов и восстановление разрушенных торцов рельсов.
- Анализ эксплуатации бесстыкового пути и лабораторные исследования показали, что наилучшими прочностными характеристиками обладают стыки, сваренные контактным способом, однако в ряде случаев рельсы могут быть сва¬рены только алюминотермитным способом (стрелочные переводы, ремонт и т.п.). Таким образом, в настоящее время бесстыковой путь получают с использованием контактной и алюминотермитной сварки, другие виды требуют больших трудоза¬трат и не обеспечивают необходимого качества.
- Проведённый анализ технологии и оборудования, используемого при алюминотермитной сварке рельсов, показал, что единственной технологической операцией, влияющей на получение необходимой структуры и обеспечивающей необходимое качество сварного соединения, является предварительный подогрев, осуществляемый специальной горелкой. В связи с этим основное внимание при данном способе сварки должно уделяться этой технологической операции и строго соблюдаться требования технических условий по подогреву.
- Анализ существующих конструктивных особенностей горелки, используемой для подогрева стыков рельсов при алюминотермитной сварке рельсов, по-зволил разработать её новый вариант, в котором за основу принят стандартный корпус от существующей сварочной горелки отечественного производства. Проведённые испытания опытного образца модернизированной горелки показали, что она позволяет получить одинаковый подогрев двух концов свариваемых рельсов и обеспечивает необходимые условия их подогрева.
- Экспериментально установлено, что глубина высокотемпературной области на момент окончания подогрева составила 15-20 мм, а наиболее интенсивный разогрев происходит в головке и верхней части шейки рельсов.
- Многочисленные натурные испытания сварных образцов рельсов подтвердили, что несоблюдение технологических параметров при выполнении АТСР приводит к хрупким разрушениям по зоне сплавления, начинающимся от периферийных участков подошвы рельса, расположенных в зоне сплавления. Дальнейшее распределение трещин происходит по зоне сплавления с возможным переходом в основной металл рельса или сварной шов.
- Численными экспериментами установлено, что при недостаточном подогреве или низкой температуре окружающей среды температура торцов рельсов резко снижается, что приводит к повышению скоростей охлаждения металла шва и околошовной зоны. Это способствует образованию закалочных структур, по-вышению хрупкости и образованию микротрещин, снижающих прочность стыка рельсов. Так, например, при сварке рельсов при температуре окружающей среды равной – 15 °С скорости охлаждения на периферийных участках подошвы рельса почти в два раза выше, чем в головке.
- Проведённые экспериментальные исследования показали, что с понижением температуры окружающей среды повышается скорость охлаждения металла периферии подошвы рельса, приводящая к образованию хрупких структур, резко снижающих прочностные характеристики. Сваренные по утверждённой технологии образцы рельсов при температуре – 15 °С не выдержали нормативных требований при испытаниях.
- Создание благоприятных условий в процессе сварки и последующем охлаждении сварного стыка с меньшими скоростями охлаждения позволили предложить технологию, обеспечивающую образование равновесных структур, исключающих снижение его прочности и пластичности. На данный способ получен патент РФ на изобретение №2464141 «Способ алюминотермитной сварки рельсов при отрицательных температурах».
Заключение
- В ходе историко-технического анализа выявлено, что периоды, в которые происходили существенные изменения конструкций рельсов, не совпадают с периодами истории развития российских железных дорог. Поэтому для выявления закономерностей в разработке и совершенствовании железнодорожных рельсов автором была впервые разработана периодизация, отражающая изменения состава материала, геометрических параметров конструкции рельсов, что нашло отражение в нормативах стандартов.
- На основании разработанной автором периодизации установлено, что в рамках соответствующих периодов применяли деревянные лежни, в том числе с металлическим покрытием, чугунные и стальные рельсы. В качестве конструкций колейных дорог использовали лежни круглого и прямоугольного сечения; чугунные, в том числе уголковые, грибовидные, широкоподошвенные, двухголовые рельсы, а также стальные рельсы с трапецеидальной формой головки и головкой с вертикальными боковыми гранями. Процесс унификации стандартов был направлен на выработку единых требований к широкоподошвенным рельсам широкой колеи. Приоритет в содержании обозначений условных знаков типизации сместился от веса рельса к его функциональному назначению, с сохранением весовой характеристики.
- Поставка отечественных рельсов, необходимых для обеспечения строительства российских железных дорог, осложнялась в XIX в. из-за конкуренции с зарубежными аналогами, которые были дешевле, но проигрывали по качеству и срокам службы; в XX в. – из-за политических и экономических последствий Октябрьской революции, Гражданской, Первой и Второй мировых войн, распада СССР.За счёт оптимизации химического состава путём легирования и повышения содержания углерода, а также совершенствования термической обработки, в том числе применения двухсторонней закалки, можно повысить прочностные характеристики рельсовой стали, обеспечивающие в данный исторический период требования по перевозкам грузов и скоростям движения поездов.Наиболее повреждаемым местом является стык рельсов. В связи с этим разрабатывались различные виды скреплений рельсов между собой, которые изменялись вместе с ними. Болтовое соединение является наиболее распространённым на железнодорожном транспорте. Однако, неразъёмные (сварные) стыки, которые использовались с начала XX в., позволяют повысить скорость движения поездов, комфортность перевозки пассажиров и грузов, существенно снизить износ рельсов и ходовых частей и т.п.Анализ эксплуатации бесстыкового пути и лабораторные исследования показали, что наилучшими прочностными характеристиками обладают стыки, сваренные контактным или алюминотермитным способом. В конце 1950-х гг. контактная сварка полностью вытеснила алюминотермитную при соединении рельсов. Однако, в конце XX в. с вводом стрелочных переводов на железобетонном основании потребовалось их вваривать в бесстыковой путь, что невозможно сделать контактной сваркой, и было принято решение МПС РФ об использовании алюминотермитной сварки.
- В ходе историко-технического анализа выявлено, что алюминотермитная сварка является впервые применённым способом сварки рельсов. Основной технологической операцией, обеспечивающей качество сварного шва, является предварительный подогрев, при котором используется специальная горелка. В ходе разработки конструкции и технологии изготовления отечественного варианта такой горелки для предварительного подогрева рельсов, а также при проведении её лабораторных и натурных испытаний принимала участие и автор. Лабораторные, натурные и численные эксперименты позволили обосновать необходимость проведения корректировки технологических процессов сварки в зависимости от внешних условий. Установлено, что кроме строгого соблюдения равномерности и продолжительности подогрева торцов рельсов, необходимо учитывать температуру окружающей среды. В результате проведённых исследований был разработан способ алюминотермитной сварки рельсов, дающий возможность проводить её практически при любых погодных условиях и обеспечивать необходимое качество сварного соединения (патент РФ на изобретение № 2464141).
Список литературы
- Исследование рельсовой стали [Текст] / Запросы председателя комис¬сии по исследованию рельсовой стали инженерам отдела по испытанию и освиде-тельствованию заказов М-ва Путей Сообщения, а также Заводоуправлениям и по-лученные на них ответы. – СПб., 1906. – 214 с.
- Манган [Электронный ресурс] : – Режим доступа: http://uk.wikipedia. org/wiki/Mn (Ссылка актуальна на 25.08.2011).
- Скаков, А.И. Качество железнодорожных рельсов [Текст] / А.И. Скаков М.: Металлургиздат, 1955. – 368 с.
- Гуляев, А.П. Металловедение [Текст] : учебник для вузов / А.П. Гуляев // 6-е изд., перераб. и доп. – М.: Металлургия, 1986. – 544 с.
- ГОСТ 24182-80. Рельсы железнодорожные широкой колеи типов Р75, Р65 и Р50 из мартеновской стали. (CT СЭВ 4983-85). Технические условия [Текст]. – Взамен ГОСТ 8160-63 и ГОСТ 6944-63 ; введ. 1981-07-01. – М.: Изд-во стандартов, 1988. – 9 с.
- Технологическая инструкция [Текст] / Технология сварки рельсов алюминотермитным способом // Фирма «Снага». – Словакия, 1997. – 11 с.
- Правила технической эксплуатации железных дорог Российской Феде-рации [Текст] / С изм. и доп., внес, приказами МПС России от 03.07.01 г. № 16, от 27.05.2002 г. № 24: Утв. М-вом путей сообщения Рос. Федерации 26.05.2000 г.: офиц. изд. – М.: Техинформ, 2002. – 189 с.
- Правила технической эксплуатации железных дорог Российской Феде-рации [Текст], [Электронный ресурс] / Приказ Министерства транспорта Россий¬ской Федерации от 21 декабря 2010 г. № 286. Опубликовано 25 декабря 2010 г. на сайте «Российской Газеты». Вступает в силу 29 сентября 2011 г. Зарегистрирован Минюстом России 28 января 2011 г. Регистрационный №19627. // Режим доступа: www.rg.ru/2010/12/25/zheldor-site-dok.html
http://doc.rzd.ru/doc/public/ru7structure 1а=704&1ауег&1с1=5104<Ш=4051 #613 5 (Ссылки актуальны на 25.08.2013). - Стратегия развития железнодорожного транспорта в Российской Феде-рации до 2030 года [Текст] / Утверждена Распоряжением Правительства Россий¬ской Федерации от 17 июня 2008 года. № 877-р. – Текст официально не опубли¬кован.
- Программа инновационного развития ОАО «Российские железные до¬роги на период 2011-2015 гг. [Текст] / Концепция программы одобрена Минэко-номразвития России и утверждена решением Совета директоров ОАО «РЖД» от 29 ноября 2010 г. №26.
- Бельфер, С.М. Путевое хозяйство [Текст] : Учебник для вузов ж.-д. тр- та / С.М. Бельфер, Э.В. Воробьёв, Л.М. Дановский и др. : под ред. И.Б Лехно – М.: Транспорт, 1981.-447 с.
- Сварка рельсов алюминотермитная методом промежуточного литья. Технические условия ТУ 0921-127-01124323-2005 [Текст]. – М.: ВНИИЖТ, 2005. – 16 с.
- Карпущенко, Н.И. Железнодорожный путь [Текст] / Н.И. Карпущенко, С.И. Клинов, H.H. Путря и др. : под ред. Т.Г. Яковлевой – М.: Транспорт, 1999. – 405 с.
- Железнодорожный транспорт [Текст] : Энциклопедия / под. ред. Н.С. Конарева. – М.: Большая Российская энциклопедия, 1994. -559 с.
- Яковлев, В.Ф. Железнодорожный путь: конструкции верхнего строения пути рельсовых дорог [Текст] / В.Ф. Яковлев, JI.A. Андреева – СПб.: Издательство Петербургского гос. ун-та путей сообщения, 2002. – 149 с.
- Крейнис, 3.JI. Железнодорожный путь [Текст] / 3.J1. Крейнис, И.В. Фе-доров – М.: ИГ «Вариант», 1996. – 368 с.
- Крейнис, 3.JL Современные конструкции верхнего строения железно-дорожного пути [Текст] / З.Л. Крейнис – М.: РГОТУПС, 1997. – 78 с.
- Галицын, Г.А. Технология термообработки железнодорожных рельсов и накладок при охлаждении в воде [Текст] / Г.А. Галицын, А.Б. Добужская, Е.А. Муравьёв / Материалы юбилейной рельсовой комиссии. // Сборник докладов – Новокузнецк, 2002. – С. 156-167.
- Ольденборгер, А.И. Сплошной рельсовый путь без зазора в стыке [Текст] / А.И. Ольденборгер // Железнодорожное дело, – СПб., 1904. – № 14-15. – 40 с.
- Першин, С.П. Методы расчёта устойчивости температурно- напряжённого пути и способы её повышения [Текст] : дис. … канд. тех. наук : Першин Сергей Петрович. – М., 1959. – 271 с.
- Евдокимов-Рокотовский, И.И. Рельсовый путь за сто лет [Текст] / И.И. Евдокимов-Рокотовский. – б.м. – б.г., – 20 с.
- Ковалев, H.A. Справочник сварщика [Текст] / H.A. Ковалев – Ростов- на-Дону: Феникс, 2011. – 350 с. ISBN 978-5-222-17065-6.
- Шепелев В.Н. Термитная сварка рельсов [Текст] / В.Н. Шепелев – М.: Транспорт, 1963. – 56 с.
- Hans Goldschmidt [Электронный ресурс] // Режим доступа: http://en.wikipedia.org/wiki/Hans_Goldschmidt (Ссылка актуальна на 25.08.2011).
- Корниенко, A.M. История сварки. XV-середина XX ст. [Электронный ресурс] / A.M. Корниенко, – К, Феникс, – 2004 // «Автогенная обработка». Тер¬митная сварка. История развития. – Режим доступа: http://www.autowelding.rU/publ/l/l/l/9-l-0-58. (Ссылка актуальна на 12.12.2013)
- Новакович, В.И. Становление бесстыкового пути. // Путь и путевое хо-зяйство. – 2003. – № 9. – С. 17-19.
- Набережная Обводного канала. Сварка стыков термитом. (Капиталь¬ный ремонт в 1923 г.) [Электронный ресурс] / Фотографии старого Санкт- Петербурга // Архив ленинградского ТТУ – Режим доступа: http://oldsp.ru/old/photo/view/23379 (Ссылка актуальна на 12.12.2013)
- Малкин, Б.В. Термитная сварка [Текст] / Б.В. Малкин, A.A. Воробьёв – М.: Министерство Коммунального Хозяйства РСФСР, 1963. – 105 с.
- Чистяков, Б.П. Термитная сварка рельсовых стыков на железнодорож¬ных путях в СССР и за границей [Текст] / Б.П. Чистяков // Лекции, прочитанные в Ленинградском институте инженеров путей сообщения на курсах по поднятию квалификации инженеров железнодорожного транспорта в 1928 г. – М.: Транспе¬чать НКПС, 1929.-91 с.
- Рукавцов, К.А. Мой опыт сварки термитом [Текст] / К.А. Рукавцов – М.: Трансжелдогриздат, 1940. – 64 с.
- Проблемы дуговой и контактной электросварки [Текст] // Сборник, по- свящённый памяти Е.О. Патона. – Москва-Киев: Государственное научно- техническое издательство машиностроительной литературы, 1956. – 318 с.
- Сварка в машиностроении [Текст] : справочник в 4-х т. / редкол.: Г. А. Николаев (пред.) и др. //Т. 1. / под ред. H.A. Ольшанского. – М.: Машино¬строение, 1978. – 504 с.
- Болдырев, A.M. Сварочные работы в строительстве и основы техноло¬гии металлов [Текст] : учебник / A.M. Болдырев, A.C. Орлов – М.: Изд-во АСВ, 1994.-432 с.
- Сварка в СССР [Текст] : в 2-х т. / под ред. Г.К. Николаева, К.С. Колес-никова // Т. 1. Развитие сварочной техники и науки о сварке, технологических процессах, сварочных материалах. — М.: Наука, 1981. – 150 с.
- Резанов, В.А. Разработка метода оплавления контактной сварки леги-рованных рельсовых сталей [Текст] : автореф. дис. канд. тех. наук: 05.02.10 / Ре-занов Виктор Александрович, М., – 2013. – 20 с.
- Рельсосварочная машина [Электронный ресурс] : Режим доступа: http://p.www.pz.gov.ua/news/img/prsm4_big.jpg (Ссылка актуальна на 12.12.2013)
- Новакович, В.И. Бесстыковой путь со сверхдлинными рельсовыми пле-тями [Текст] : учеб. пособие для вузов ж.-д. тр-та / В.И. Новакович. – М.: Мар¬шрут, 2005.- 144 с.
- Новакович, В.И. Бесстыковой железнодорожный путь с рельсовыми плетями неограниченной длины [Текст] / В.И. Новакович. – Львов: Вища школа. Изд-во при Львов, ун-те, 1984. – 100 с.
- Севостьянова, Л.Л. Бесстыковой путь в условиях Дальневосточного ре-гиона [Текст] : учеб. пособие / Л.Л. Севостьянова. – Хабаровск: ДВГУПС, 1997. – 101 с.
- Клименко, Л.В. Бесстыковой путь – прогрессивная конструкция желез-нодорожного пути [Текст] / Л.В. Клименко // Соискатель: приложение к журналу «Мир транспорта» МКЖТ МПС РФ, 2004. – № 1 – С. 88-93.
- Номенклатурный справочник каховского завода электросварочного оборудования на 1999 г.
- Авария поезда в Амурской области [Электронный ресурс] / Lenta.ru : Режим доступа: http://lenta.ru/news/2008/07/23/rail/. (Ссылка актуальна на 12.12.2013)
- Выброс пути [Электронный ресурс] // Правила технической эксплуата¬ции железных дорог Российской Федерации : Режим доступа: http://railways.id.ru/doc/norm/pte.htm. (Ссылка актуальна на 12.12.2013)
- Малкин, Б.В. Термитная сварка рельсов [Текст] / Б.В. Малкин, A.A. Воробьёв – М.: Транспорт, 1963. – 272 с.
- Шепелев, В.Н. Термитная сварка рельсов [Текст] / В.Н. Шепелев – М.: Транспорт, 1963. – 55 с.
- Воронин, H.H. Роль сварки в обеспечении безопасности бесстыкового пути [Текст] / H.H. Воронин, H.H. Прохоров // Безопасность движения поездов: труды 9-ой научно-практич. конф.; МИИТ, ОАО «Российские железные дороги», Министерство транспорта Российской Федерации и др. – М.: МИИТ, 2008, – с. XIV-45 -XIV-47.
- Королев, P.A. Расчётное обоснование технологических параметров сварки рельсов алюминотермитным способом [Текст] / P.A. Королев, Ворони¬на О.Н. // Московская конференция Молодых учёных «Научно-технические про¬блемы развития Московского мегаполиса» : тезисы докладов – М.: ИМАШ РАН, 2002, – с. 65-66.
- Королев, P.A. Экспериментальное определение термических циклов при сварке рельсов алюминотермитным способом [Текст] / P.A. Королев, Воро¬нина О.Н. // «Юбилейная XV Международная Интернет-конференция молодых учёных, аспирантов и студентов по современным проблемам машиноведения» : тезисы докладов – М.: ИМАШ РАН, 2003, – с. 58.
- Королев, P.A. Обоснование технологических параметров и обеспечение их контроля при алюминотермитной сварке рельсов [Текст] : дис. … канд. техн. наук: 05.03.06 Королев Роман Александрович – М., 2006. – 201 с.
- Воронин, H.H. Алюминотермитная сварка рельсов [Текст] / H.H. Воронин, H.H. Прохоров, О.Н. Трынкова // Ремонт, инновации, технологии, модернизация. – 2009. – № 6 (44). – С. 27-29.
- Трынкова, О.Н. Применение алюминотермитной сварки на железнодо-рожном транспорте [Текст] / О.Н. Трынкова // «Инновации в науке, образовании и производстве» : труды СПбГТУ № 492. – СПб.: СПбГТУ. – 2004, – с. 201-206.
- Воронин, H.H. Резервы алюминотермитной сварки рельсов [Текст] / H.H. Воронин, H.H. Прохоров, О.Н. Трынкова // Мир транспорта. – 2012. – № 2 (40).-С. 76-82.
- Воронин, H.H. Алюминотермитная сварка рельсов зимой [Текст] / H.H. Воронин, О.Н. Трынкова, О.В. Фомичева // Мир транспорта. – 2012. – № 4 (42). – С. 56-59.
- Воронин, H.H. Кинетика формирования поля скоростей охлаждения металла при температуре минимальной устойчивости аустенита при алюминотер- митной сварке [Текст] : в 4 т. / H.H. Воронин, H.H. Прохоров, О.Н. Трынкова // Вузы-наука-город : труды первой Моск. городской научно-практич. конф. «Вузы- наука-город»; МИИТ. – М.: МИИТ, 2005, – Т. 3-4, – с. IV-124 – IV-128
- Прохоров, H.H. Влияние мощности источника теплоты на характер по-догрева рельса перед алюминотермитной сваркой [Текст] / H.H. Прохоров, H.H. Воронин, О.Н. Трынкова / «Состояние, проблемы и перспективы развития метал-лургии и обработки металлов давлением» : сборник трудов МГВМИ и Союза куз-нецов. – М.: МГВМИ, 2004, – Вып. 4, – с. 153-157.
- ГОСТ Р 8.585-2001 ГСИ. Термопары. Номинальные статические харак-теристики преобразования. [Текст]. – Взамен ГОСТ Р 50431-92, МИ 2559-99 : введ. 2002-07-01. — Госстандарт России: ИПК Издательство стандартов № 2002. М.: Стандартинформ, 2010. – 84 с.
- Рыкалин, H.H. Нагрев металла газовым пламенем [Текст] / H.H. Рыка- лин, М.Х. Шоршоров, А.К. Нинбург // Руководящие материалы – М.: МХП СССР, Главкислорд, ВНИИАвтоген, Госхимиздат, 1954. – Вып. 2. – 118 с.
- Глизманенко, Д.Л. Газовая сварка и резка металлов [Текст] / Д.Л. Глизманенко, Г.Б. Евсеев. -М.: МАШГИЗ. 1961.-448 с.
- В.Н. Волченко, В.Н. Теория сварочных процессов [Текст] : учебник для вузов по спец. «Оборуд. и технология сварочн. пр-ва» / В.Н. Волченко, В.М. Ямпольский, В.А. Винокуров и др.; под ред. В.В. Фролова. – М.: Высшая школа, 1988. – 559 с. ISBN 5-06-001473-8.
- Теория сварочных процессов [Текст] : учебник для вузов / под ред. В.М. Неровного. – М.: МГТУ им. Н.Э. Баумана, 2007. – 752 с. ISBN 978-5-7038¬3020-8
- Петров, Г.Л. Теория сварочных процессов (с основами физической хи-мии) [Текст] : учебник для вузов / Г.Л. Петров, A.C. Тумарев // Изд. 2-е, перераб. – М.: Высшая школа, 1977. – 392 с.
- Петров, С.Ю. Методические указания по использованию программы «Поле-аналитик» [Текст] / С.Ю. Петров, М.: МИИТ, 1996. – 12 с.
- Воронин, H.H. Анализ повреждаемости и оценка работоспособности несущих сварных конструкций грузовых вагонов [Текст] : дис. … докт. техн. наук : 05.22.07, 05.03.06 / Воронин Николай Николаевич, М., – 1994. – 348 с.
- Прохоров, H.H. Анализ перераспределения температур в поперечном сечении рельса путём математического моделирования тепловых процессов при его предварительном нагреве перед выполнением алюминотермитной сварки [Текст] / H.H. Прохоров, H.H. Воронин, P.A. Королев // Состояние, проблемы и перспективы развития металлургии и обработки металлов давлением: сборник на- учн. трудов МГВМИ; М.: МГВМИ, 2005, – Вып. 5, – с. 312-317.
- Воронин, H.H. Обоснование основных технологических параметров алюминотермитной сварки рельсов [Текст] / Воронин H.H., P.A. Королев // Сварка на рубеже веков: тезисы докладов научно-технической конференции 20-21 января 2003; МГТУ им. Н.Э. Баумана. – М.: МГТУ им. Н.Э. Баумана, 2002, – с. 40