Сейчас ваша корзина пуста!
Повышение качества и конкурентоспособности высокопрочной арматуры диаметром 10,0 мм для железобетонных шпал на основе разработки рациональных режимов холодной деформации и термической обработки
Цикл статей:
Глава 1 – Повышение качества и конкурентоспособности высокопрочной арматуры диаметром 10,0 мм для железобетонных шпал на основе разработки рациональных режимов холодной деформации и термической обработки
Глава 2 – Моделирование напряженного состояния при волочении заготовки н^ размер под профилирование
Введение
В основных направлениях экономического и социального развития России на 2005 – 2015 годы предусмотрено дальнейшее расширение промышленного, гражданского и железнодорожного строительства. В настоящее время за счет строительства новых дорог осваивается относительно небольшая часть ежегодного прироста грузооборота на железнодорожном транспорте. Существенно более высокие объемы прироста грузооборота осваиваются за счет увеличения производительности действующих магистралей. Основными путями интенсификации перевозок служат повышение скоростей движения поездов и их веса, что связано с резким ростом силового воздействия подвижного состава на путь. Его состояние на сегодня не вполне отвечает более сложным условиям эксплуатации. В связи с этим компанией ОАО «Российские железные дороги» в 1996г. принята двухуровневая программа технического перевооружения отечественных железных дорог. Первый этап направлен на повышение скорости движения и модернизации существующих дорог, затем начнется строительство специализированных высокоскоростных магистралей. Разработано четыре основных направления строительства. Это Москва-Санкт-Петербург, Москва-Красное-Минск-Брест-Варшава-Берлин, Москва-Юг, Москва-Нижний Новгород-Екатеринбург. Одной из актуальных проблем при реализации намеченной программы является развитие производства современных комплектующих для строения пути и, в частности, железобетонных шпал. Сегодня технологии изготовления железобетонных шпал ориентированы на существенное сокращение металлоемкости конструкций, снижение трудоемкости и энергоемкости производства, использовании схем укрупненного армирования и прогрессивной технологии предщ- пряжения «на бетон» при формировании комплекса ее служебных свойств. Одновременно более жесткие требования предъявляются к качеству армирующего материала В целях развития отечественного производства железобетонных шпал для высокоскоростных магистралей компания приобрела за рубежом несколько специализированных технологических линий по выпуску данной продукции. Одна из таких линий фирмы ОЬМ1 8рА (Италия) действует на Челябинском заводе железобетонных шпал. Проектная мощность потребления арматуры каждой из линий составляет 300 тонн в месяц. Основным несущим элементом в конструкции шпалы для высокоскоростных магистралей, определяющим ее работоспособность и долговечность, является высокопрочная (<тв>1470 Н/мм ) стержневая арматура периодического профиля диаметром 10,0 мм. Использование арматуры диаметром 10,0 мм обеспечивает экономию металла, высокую технологичность армирования и позволяет увеличить производительность при производстве шпал в 2 раза. В зарубежных технологиях производства высокопрочной шпальной арматуры такого диаметра можно выделить два направления: деформационное упрочнение высокоуглеродистых сталей с последующим отпуском под сильным натяжением и термическое упрочнение кремнистых сталей.
С целью освоения производства и загрузки импортных линий отечественной арматурой на данный вид продукции разработаны ТУ-14-125-704-96, где качестве заготовки предусмотрено использование кремнистых сталей с химическим составом, соответствующим сталям марки 40С2 или 55С2.
Опыт освоения высокопрочной арматуры из кремнистых сталей на металлургических заводах выявил проблемы в достижении требуемых показателей качества арматуры при термическом упрочнении в потоке прокатного стана, большого разброса механических свойств готовой арматуры, отклонения по мерности прутков, низкой рентабельности производства при выпуске малотоннажных партий. Освоение производства арматуры требуемого качества метизными предприятиями на базе деформационного упрочнения лимитируется отсутствием подката с регламентированными показателями механических свойств и способностью к холодному пластическому деформированию. Эти причины привели к фактическому отсутствию арматуры этого класса на рынке, а заводы ЖБШ переориентировались на зарубежных производителей, поставляющих свою продукцию по цене в 1,5 -2 раза выше отечественной. Несмотря на то, что концепция развития металлургии России до 2010г. предусматривает расширение производства импортозамещающих видов металлопродукции, сегодня ни одно отечественное предприятие не освоило производство арматуры, конкурентоспособной с западными аналогами.
Данная работа посвящена вопросам повышения качества и конкурентоспособности высокопрочной арматуры для железобетонных шпал диаметром
10,0 мм с О”_в>1470 Н/мм из кремнистых марок стали 40С2 и 55С2. Эффективным способом решения этой задачи может стать схема производства, состоящая из двух технологических блоков: блока холодной пластической деформации, включающем операции волочения подката на размер под профилирование и нанесения периодического профиля и блока финишного термического упрочнения. Такой подход открывает широкие возможности в управлении качеством продукции за счет реализации преимуществ холодной пластической деформации и термообработки на каждой отдельной стадии производства. Так, на этапе холодной пластической деформации появляется возможность получать арматуру по теоретической массе, обеспечить точность выполнения геометрических показателей качества. На этапе термической обработки сформируется высокопрочное изотропное состояние арматуры. В целом технологический процесс обеспечит гибкость и мобильность при смене сортамента, выпуск малотоннажных партий, многовариантность финишного упрочнения, получение стабильных однородных механических свойств арматуры и повышение конкурентоспособности продукции.
В развитии этого направления необходимо разработать режимы получения заготовки под профилирование и нанесения периодического профиля, обеспечивающих формирование требуемых геометрических показателей качества арматуры и создание благоприятного уровня напряженного состояния перед финишной термообработкой. Провести исследования закономерностей изменения механических свойств холоднопрофилированной арматуры периодического профиля на этапе термического упрочнения и определить на этой основе результативные режимы обработки, обеспечивающих достижение регламентированных показателей качества продукции. Изучив процессы формирования качества на этапах холодного пластического деформирования и термической обработки, на основе полученных знаний необходимо разработать методику управления качеством высокопрочной арматуры для железобетонных шпал, позволяющую определять рациональные режимы обеспечения заданного уровня качества и повышения конкурентоспособности готовой продукции. Выпустить опытно-промышленные партии высокопрочной арматуры периодического профиля для железобетонных шпал и выполнить оценку качества готовой продукции. Работа является продолжением и развитием исследований по разработке эффективных технологических процессов производства арматуры периодического профиля различного назначения, проводимых в разное время учеными магнитогорской научной школы среди которых Никифоров Б.А., Харитонов В.А., Киреев Е. М., Харитонов Вик. А., Фогель Л.М., Белан А.К., Кор- чунов А.Г., Харитонов A.B.
Состояние, перспективы развития и проблемы производства высокопрочной арматуры периодического профиля для железобетонных шпал
Современные требования к качеству арматуры для железобетонных шпал
Арматура периодического профиля для армирования различных предварительно напряженных железобетонных конструкций, является самым массовым видом высокопрочной стали [1].
Весьма обширна и номенклатура изделий, изготавливаемых с предварительным напряжением: покрытия зданий, пролетные строения и опоры мостов, железобетонные сваи и трубы, железнодорожные шпалы, опоры ЛЭП и мачты освещения, телебашни, защитные оболочки, морские и шельфовые сооружения, плавучие доки, корпуса понтонов и многое другое. В высшей степени убедительной демонстрацией эксплуатационной надежности высокопрочной арматуры является успешное ее использование для производства железнодорожных шпал. В мире в настоящее время их установлено более миллиарда штук. Есть участки железной дороги, где железобетонные шпалы прослужили более 40 лет и не имеют каких-либо существенных повреждений [2]. Динамические нагрузки, ощутимые температурные перепады, увлажнение и высушивание, замораживание и оттаивание, воздействие нефтепродуктов и других агрессивных веществ предъявляют исключительно высокие требования к надежности и долговечности этих изделий.
Сегодня технологии производства железобетонных шпал и производимое для этого оборудование ориентированы на существенное сокращение металлоемкости конструкций, снижение трудоемкости и энергетических затрат. Достичь этого позволяют [3]:
- более жесткие требования к качеству арматуры, в части повышения прочностных характеристик при сохранении и увеличении ее пластичности, технологичности и долговечности;
- переход к схемам укрупненного армирования, за счет использования высокопрочной арматуры диаметром до 10,0 мм;
- применение прогрессивной технологии преднапряжения «на бетон», когда натяжение арматуры в каналах шпал осуществляется непосредственно на бетон с постоянной ее анкеровкой по торцам изделия.
Показатели качества выпускаемой в настоящее время высокопрочной арматуры для железобетонных шпал оцениваются по механическим свойствам, величине потерь напряжения от релаксации, стойкости к коррозионному растрескиванию, уровню сцепления с бетоном. Кроме того, регламентируются металлургическое качество металла, требования к качеству поверхности, предельно допустимые отклонения по овальности и массе погонного метра арматуры.
Структура обеспечения качества высокопрочной арматуры для железобетонных шпал показана на рис.1. По всем этим показателям в последние 10-15 лет зарубежными производителями достигнут значительный прогресс. Так минимальное значение временного сопротивления разрыву ав стержневой арматуры диаметром менее 15,0 мм должно составлять не менее 1100
Н/мм2, для бунтовой проволочной арматуры диаметрами 6,0-10,0 мм ав сол ответственно от 1770 до 1570 Н/мм [4].
Для всех видов арматуры в качестве характеристики пластичности используется относительное удлинение перед разрывом Agt{8п) не менее 3,5 %. Низкие потери от релаксации определяются высоким расчетным пределом упругости, величина которого составляет около 0,8 от условного предела текучести стали.
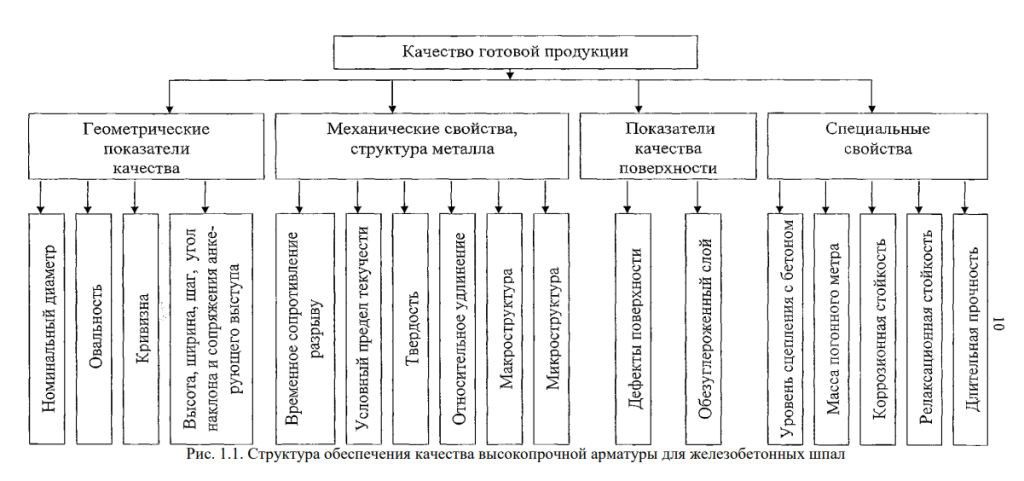
Для оценки уровня сцепления арматуры с бетоном используют критерий Рема [5 ]:

где Бсм – площадь проекции анкеруюгцих выступов на плоскость, нормальную оси арматуры; ён – номинальный диаметр арматуры ; X – шаг анкерую- щих вмятин или выступов. Конкретные показатели качества арматуры устанавливаются в стандартах и технических условиях зависимости от технологии ее производства (табл. 1.1 -1.2).
Нормативно – техническая документация | Диаметр d, мм | Условный предел те- кучестиа 0,2, НУмм2 (не менее) | Временное сопротивление разрыву 2 Gb , Н/мм (не менее) | Относительное удлинение после разрыва 5,% (не менее) |
ISO/DIS 6934 | 6-20 | 835 | 1230 | А&{дп)> 3,5 |
ISO 6934-3/1991 | 6,2-16,0 | 1275-1420 | 1420-1570 | А&{8П)> 3,5 |
EN 10138 | 6-15 | 900 | 1100 | А&{3П)> 3,5 |
ГОСТ 5781-88 ( класс AV -AVI) | 6-40 | 785-980 | 1030-1230 | 7-6 на базе |
ГОСТ 10884-94 ( класс Ат-800-‘”‘■ Ат-1200 ) | • 10-18 – | 800-1200 | 1000-1450 | 8-6 на базе 5ё |
ТУ 14-125-704-96 | 10 | 1325 | 1470 | 6 на базе 10ё |
Нормативно – техническая документация | Диаметр d, мм | Условный предел те- кучестиа Н/мм2 (не менее) | Временное сопротивление разрыву ав , Н/мм2 (не менее) | Относительное удлинение после разрыва 5,% (не менее) |
ЕЙ 10138 | 3-10 | 1600-1300 | 1860-1570 | А&{8П)> 3,5 |
ГОСТ 7348 | 3-8 | — | 1780-1470 | $юо ^4-6 |
ТУ 14-178-231-92 | 5 | 1400-1300 | 1670-1570 | §юо >4 |
ТУ 14-4-1681-91 | 3 | 1400 | 1700 |
Сравнение качественных показателей арматуры, выпускаемой за рубежом, показывает незначительное различие механических свойств горячекатаной и термически упрочненной продукции и более существенное отставание по сортаментному ряду и механическим свойствам проволочной холоднодеформированной арматуры. В Европейских странах в промышленных объемах выпускаются и успешно эксплуатируются на высокоскоростных магистралях железнодорожные шпалы, армированные высокопрочной арматурой диаметром 10,0 мм. Особенностью арматуры для железобетонных шпал, в отличие от других сортов арматурной стали , является высокий уровень её
прочностных свойств ав не менее 1375-1570 Н/мм . В России на высокопрочную арматуру диаметром 10,0 мм для железобетонных шпал разработаны ТУ 14-125-704-96, в которых отражены современные тенденции к показателям качества этой продукции. Применение арматуры такого диаметра и прочности позволяет получать значительную экономию металла при армировании, что особенно актуально ввиду того, что его возврат в черную металлургию в виде лома на сегодняшний день не решен.
Анализ состояния производства высокопрочной арматуры периодического профиля для железобетонных шпал за рубежом и в России
За рубежом высокопрочная арматура для железобетонных шпал диаметром 10,0 мм выпускается с использованием технологий деформационного упрочнения на прямоточных волочильных станах нового поколения с последующей механотермической обработкой и термического упрочнения. При этом западными производителями в формировании потребительских свойств арматуры комплексно задействуются практически все известные механизмы упрочнения и повышения пластичности, начиная от металлургии (микролегирование стали, выплавка ее в электропечах) и горячей контролируемой прокатки, и заканчивая механотермическим упрочнением путем вытяжки и низкотемпературного отпуска.
С конца 60 -х годов большое развитие получили технологии деформационного упрочнения высокопрочной арматуры. Согласно современным воззрениям упрочнение при холодной деформации наступает в результате резкого возрастания числа дислокаций и их взаимного торможения, что приводит к повышению предела текучести стали [6], При этом в качестве основного процесса формоизменения используется волочение в монолитных волоках, прокатка в двух- и многовалковых калибрах или сочетание этих способов [79]. Технология холодной прокатки арматуры периодического профиля в мире за последнее время не претерпела существенных изменений, а усилия изготовителей оборудования были в основном направлены на увеличение числа клетей и производительности станов. На смену одно-, двухклетьевым станам с многовалковыми калибрами пришли современные компактные многоклеть- евые непрерывные станы блочной конструкции с высокой скоростью прокатки, оборудованные твердосплавными валками [7, 10]. В этой индустрии задействованы и имеют приоритеты на международном рынке оборудования и технологий такие мощные фирмы как “KOCH”, “KARL FUHR”, “BAU STAHL GEVEBE” (Германия),” PROPERZI”, “EUROROLLS”, “Р1ТТ1М”(Италия), “ELIN UNION” (Австрия) и другие.
Стремительными темпами в мире развиваются технологии, основанные на деформационном упрочнении в сочетании с финишной механотерми- ческой обработкой-отпуском при температуре 370-420°С под натяжением, разработанной фирмой «SOMERSET WIRE» (Великобритания). Такую арматуру в зарубежной практике называют релаксационно стойкой или с низкими потерями от релаксации, в отечественной – стабилизированной, а метод ее получения -стабилизацией [4,11]. Релаксационная стойкость арматуры повышается при этом в три – четыре раза и очень мало изменяется с течением времени.
Распространению данной технологии на холоднодеформированную арматуру диаметром более 6,0 мм способствовал существенный прогресс в производстве ускоренно-охлажденной высокоуглеродистой катанки диаметрами до 18,0 мм по способу «Stelmor» и появление на западном рынке в конце 90х годов нового поколения прямоточных волочильных машин для сухого волочения на которых реализуется принцип волочения с противонатяжением. Сегодня машины этого класса, а также линии стабилизации предлагают такие фирмы как «Continuus-Properzi», «MFL» , «Team Mechanica» (Италия), «KOCH» (Германия) и др. Новые волочильные машины разработаны с учётом требований эргономики, повышают эффективность и безопасность работы оператора, обладают повышенной скоростью волочения. За счёт горизонтальной компоновки барабанов оператор быстрее заправляет проволоку на барабаны, чем при вертикальных барабанах обычных машин такого класса. Машины снащены горизонтально намоточным устройством, вращение приёмника проволоки осуществляется в одной линии с плоскостью волочения проволоки, это означает что проволока не подвергается никакому скручиванию. Волочение может осуществляться как в волоках обычной конструкции, так и во вращающихся волоках. Линии стабилизации комплектуются профилирующими многовалковыми установками и устройствами механотермической обработки под натяжением. В настоящее время на этой основе этой технологии налажен выпуск продукции по ЕЙ 10138 с периодическим профилем рис. 1.2.
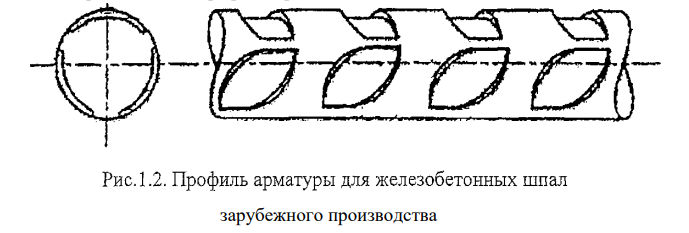
Применение технологии холодной пластической деформации с последующей стабилизацией обеспечивает гибкость при смене сортамента, возможность выполнения заказов в широком диапазоне тоннажности. Однако при этом жесткие требования предъявляются к качеству исходного подката, в части регламентации исходной микроструктуры, обеспечивающей способность к обработке с большими степенями деформации. С увеличением диаметра арматуры проявляется неравномерность пластического течения металла в продольном ‘направлении с локализацией деформации сжатия в периферийных слоях проволоки и действием в центральных ее слоях преимущественно деформаций растяжения. Неравномерность пластического течения приводит к неравномерному формированию структуры деформации, что полностью не устраняется при последующей стабилизации и снижает механические свойства готовой продукции [12,13]. Особое значение имеет снижение деформационного разогрева с целью подавления процессов старения [14].
Самостоятельным направлением в формировании высокопрочного состояния арматуры является упрочнение с отдельного нагрева закалкой с последующим отпуском [15,16].
Получаемая по такой технологии продукция по ISO 6934-3/В22 обладает высокой однородностью свойств и стойкостью к релаксации, что позволяет ей успешно конкурировать со стабилизированной арматурой.
В нашей стране основным процессом изготовлений высокопрочной хо- лоднодеформированной арматуры по ГОСТ 7348 и шпальной арматурной проволоки по ТУ 14-4-1681-91, является деформационное упрочнение патен- тированной заготовки с последующим отпуском в расплаве солей. С исполь- зованиием данной технологии производится арматура диаметрами 3,0-8,Омм [17]. Вопросами повышения качества холоднодеформированной арматуры в рамках этой технологии уделялось значительное внимание [9,18,19]. Однако в большинстве случаев исследования преследовали целью увеличение прочностных характеристик холоднодеформированной арматуры диаметрами 3,05,0 мм, получаемой из катанки диаметрами 5,5 -8,0 мм.
По оценке НИИЖБА из производимых в России видов холоднодеформированной высокопрочной арматуры только проволока диаметром 5,0 мм, выпускаемая «Северсталь-Метиз», близко соответствует требованиям международных стандартов.
Большой вклад в решение вопросов повышения диаметра и показателей качества холоднодеформированной арматуры внесла научная школа -Магнитогорского горно-металлургического института им. Г.И. Носова (сегодня МГТУ) учеными которой были выполнены комплексные теоретические и технологические исследования процесса производства высокопрочной холоднодеформированной арматуры с использованием многовалковых калибров, результаты которых послужили основой для разработки конструкций прокатных станов и промышленных технологий [20-22].
В работе [21] разработан процесс прокатки в многовалковых калибрах- калибрование в монолитной волоке (ПКВ) для производства высокопрочной
арматуры (^>1700 Н/мм2 ) с новым видом периодического профиля диаметром 7,0 мм, эффективность которого при армировании шпал подтверждена специалистами ВНИИжелезобетона [23]. Однако, в настоящее время, по ряду причин, потенциал этих разработок остался во многом невостребованным, а темпы внедрения технологии многовалковой прокатки на предприятиях приостановлены.
Решающим фактором, сдерживающим развитие производства высокопрочной арматуры больших диаметров на основе деформационного упрочнения является отсутствие отечественного подката диаметром более 12,0 мм требуемого качества с регламентированными показателями механических свойств и способностью к холодному пластическому деформированию [85]. Даже при условии закупки импортных волочильных станов и линий стабилизации отечественные метизные предприятия по этой причине не могут наладить выпуск холодно деформированной арматуры диаметром 10,0 мм.
На металлургическом переделе высокопрочная арматура выпускается по ГОСТ 5781 и ГОСТ 10884. Максимально достигнутый уровень механических свойств высокопрочной горячекатаной арматурной стали по ГОСТ 5781, составляет 1230 Н/мм2 и определяется в значительной мере химическим составом сложнолегированных сталей. Прочностные характеристики такой арматуры в основном обеспечиваются легированием стали, для выплавки которой необходимы дефицитные и дорогостоящие легирующие добавки. Ввиду этого прогнозировать освоение отечественной промышленностью горячекатаной арматуры диаметром 10,0 мм с высокими значениями временного сопротивления разрыву для армирования современных железобетонных шпал в ближайшее время затруднительно.
Применение технологии термомеханической обработки с прокатного нагрева, решает вопросы повышения прочности арматурной стали без использования сложного легирования. Однако опыт освоения высокопрочной арматуры по ГОСТ 10884 из высокоуглеродистой стали с содержанием углерода 0,7-0,85 на заводах России и СНГ выявил проблемы высокой трещино- чуствительности этих сталей, большого разброса механических свойств готовой арматуры [24-26].
Обеспечить надежность технологии производства термоупрочненной арматурной стали требуемого класса прочности можно только путем очень точного определения содержания химических элементов в стали и поддержания в узких пределах технологических параметров прокатки и охлаждения [24]. Термоупрочненная с прокатного нагрева арматура, вне зависимости от вида периодического профиля, после охлаждения имеет явно выраженную структурную неравномерность по сечению (рис. 1.3), что значительно понижает эксплуатационные характеристики изделий особенно при циклических нагрузках [27].
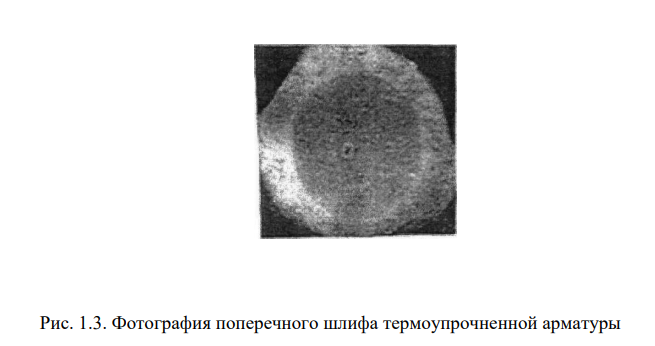
Арматурная сталь периодического профиля размерами до 12,0 мм производится на мелкосортно-проволочных станах, имеющих высокую скорость прокатки. Прокатываемые на них профили отличаются небольшой продольной устойчивостью ввиду малой площади поперечного сечения. При производстве этих профилей значительно увеличиваются простои станов по причине застревания раската между чистовыми клетями и моталками [28,29]. Совместное действие вышеперечисленных факторов обусловило низкую эффективность технологии горячей прокатки при производстве горячекатаной и термоупрочненной арматурной стали периодического профиля мелких сечений. Немаловажно особенностью технологий горячей прокатки на сортовых станах является экономическая нецелесообразность выполнения малотоннажных заказов. В 1996 г. в России были разработаны технические условия ТУ-14-125- 704-96 на арматуру диаметром 10,0 мм для армирования современных железобетонных шпал. Механические свойства арматуры в таблице 1.3.
Механические свойства | Значение (не менее) |
Временное сопротивление разрыву, <тв | 1470 Н/мм2 |
Условный предел текучести, ст0 2 | 1325 Н/мм2 |
Относительное удлинение, 310 | 6% |
Твердость , НКС | 44-48 |
Длительная прочность, 2сгА при 2-106 циклов и | 180 Н/мм2 |
а0 = 0,65 <тв |
В качестве исходной заготовки предусмотрено использование кремнистых сталей с химическим составом, соответствующим сталям марки 40С2 или 55С2.
Применению сталей этой группы в производстве арматуры способствует положительное влияние кремния на фазы, которые определяют структурное состояние металла. Кремний создает в твердом растворе направленные связи, а при повышенных концентрациях обеспечивает упорядоченность распределения атомов в решетке, что, в свою очередь, повышает сопротивление движению дислокаций на стадии микропластической деформации [79]. Кремний в малой степени увеличивает количество остаточного аустенита, но значительно повышает сопротивление малым пластическим деформациям, что оказывает положительное влияние на величину длительной прочности арматуры изготавливаемой из кремнистой стали [30].
Единственным предприятием до недавнего времени выпускающим арматуру из стали 55С2 методом термического упрочнения был «Омутнинский металлургический завод». Однако вышеизложенные причины обусловили низкую эффективность производства и неудовлетворительное качество продукции.
Сегодня ни одно отечественное металлургическое предприятие не освоило производства данного вида продукции, а заводы ЖБШ закупают арматуру импортного производства. В связи с этим актуальным является поиск технических решений по формированию заданного уровня качества и повышение конкурентоспособности высокопрочной арматуры для железобетонных шпал диаметром 10,0 мм .
Обоснование выбора технологических режимов формирования качества арматуры диаметром 10,0 мм для железобетонных шпал
В любом технологическом процессе объектом управления являются показатели качества продукции, установленные нормативно-технической документацией [31]. В достижении нормируемого уровня показателей качества используются различные методы: экономические, организационные, инновационные, технологические, статистические и др. [32]. От грамотного сочетания этих методов зависит эффективность и результативность технологических процессов и конкурентоспособность продукции [33].
На наш взгляд эффективным способом решения задачи освоения арматуры по ТУ-14-125-704-96 диаметром 10,0 мм из кремнистых сталей 40С2 и 55С2 может стать технологическая схема, включающая два технологических блока формирования качества продукции. Первый блок – процесс получения арматуры периодического профиля методами холодной пластической деформации, состоит из операции однократного волочения подката в монолитных волоках на размер под профилирование и профилирования. С учетом формы поперечного сечения арматуры, регламентированной техническими условиями ТУ-14-125-704-96, операция нанесения периодического профиля базируется на двухвалковой схеме профилирования круглой заготовки. Второй технологический блок включает термическое упрочнение закалкой с отпуском профилированной в холодном состоянии арматуры периодического профиля.
Такой подход открывает более широкие возможности в управлении качеством продукции за счет реализации преимуществ холодной пластической деформации и термообработки на каждой отдельной стадии производства. Так на этапе холодного пластического деформирования появляется возможность получать арматуру по теоретической массе, обеспечить точность выполнения геометрических показателей качества. На втором этапе термической обработки сформируется высокопрочное изотропное состояние арматуры.
В целом технологический процесс должен обеспечить выпуск малотоннажных партий арматуры, гибкость и мобильность при смене сортамента, многовариантность финишного упрочнения, получение стабильных однородных механических свойств арматуры и повышение конкурентоспособности продукции.
Чтобы реализовать преимущества предлагаемой технологической схемы необходимо определить размер заготовки под профилирование на основе металлоемкости элементов арматурного профиля, разработать аппарат оценки и управления напряженным состоянием арматуры с учетом специфики кремнистых сталей на стадии холодного пластического деформирования при волочении на размер под профилирование, которое с учетом условий профилирования предопределяет склонность стали к появлению закалочных трещин при последующей термической обработке. Изучение напряженного состояния в процессе волочения и его влияния на качество арматуры, подвергаемой термообработке является необходимым условием проектирования результативных режимов обработки выпуска качественной продукции [83].
Методы исследования процесса волочения, основанные на усреднении продольных напряжений в поперечных сечениях очага деформации и его ограничении плоскими или сферическими поверхностями входа и выхода металла из волоки, обычно исключают возможность расчета распределения напряжений в радиальном направлении и определения действительных размеров очага деформации. Такие методы в основном дают возможность найти напряжение волочения, необходимое при расчетах нагрузок волочильного оборудования и оценки энергосиловых параметров процесса волочения [34]..
В настоящей работе для расчета напряженного состояния в очаге деформации при волочении предлагается метод линий скольжения и характеристик. Этот метод, применяемый при решении плоских и осесимметричных задач, ведет свое начало от работ М. Леви, Г. Генки и Л. Прандтля. Собственно метод и его приложение получили свое дальнейшее развитие в работах отечественных ученых: A.A. Ильюшина [35], В.В. Соколовского [36], А.Ф. Томленова [37], К.Н. Шевченко [38], Л.М. Качанова [39], Г.Э. Аркулиса [40] и др.
Используя поле линий скольжения, построенное Р. Хиллом [41] для плоской задачи, Г. Генки принял допущение о возможности его использования при решенииосесимметричной задачи [42] Позже предположение Г. Генки было подтверждено на основании экспериментальных исследований проведенных Т. Иорданом и Е. Томсеном [43], О. Павельский, используя поле линий скольжения такое же, как при протяжке листа, но интегрируя дифференциальные уравнения равновесия для осесимметричной задачи с учетом условия пластичности Мизеса, рассмотрел волочение круглого прутка [44]. Автором получены значения и характер распределения компонент тензора напряжений на входе и выходе из очага деформации. Постоянные интегрирования определялись при использовании краевых условий на входной границе поля линий скольжения весьма трудоемким методом – графически. Упрочнение материала учитывалось средней за проход величиной сопротивления деформации, а силы трения на контакте при построении поля не рассматривались.
Развитие метод получил в работе Х.И. Копыловского [45], посвященной изучению напряженного состояния материала при волочении моно- и биметаллических прутков. Впервые было предложено оценивать опасность появления внутренних дефектов в проволоке наличием в очаге деформации зоны всестороннего растяжения, снижающей пластичность металла. В зависимости от технологических факторов волочения, качества исходной заготовки эта зона инициирует образование дефектов или приводит к «разрыхлению» осевых слоев проволоки. Опытные исследования подтвердили полученный характер распределения напряжений в очаге деформации и возможность появления внутренних дефектов при определенных параметрах процесса волочения.
Современная вычислительная техника и программные процедуры открывают новые возможности при изучении напряженного состояния методом линий скольжения. Большой объём графических построений и математических операций, необходимый при расчете напряженного состояния, может быть быстро вычислен при использовании специально разработанных компьютерных программ. Программные продукты на базе современных информационных технологий легко интегрируются в системы управления качеством продукции, позволяют быстро реагировать на изменения технологических параметров процессов. Для проектирования рациональных режимов холодной пластической деформации с использованием метода линий скольжения необходима разработка программного обеспечения на базе современных языков программирования, позволяющая вычислять напряженное состояние и давать визуальную картину распределения напряжений в очаге деформации.
Технологическая схема холодного профилирования арматуры диаметром 10,0 мм с нанесением двухстороннего периодического профиля с серповидными выступами на поверхность холоднотянутой круглой проволоки ранее не исследовалась. С целью получения научных сведений о закономерностях явлений, происходящих при таком способе профилирования и влияющих на формирование геометрических показателей качества продукции, требуются дополнительные исследования.
Известно, что конечные величины формоизменения можно определить только при известной кинематической схеме течения металла в очаге деформации. В случае операции профилирования, которая является одним из случаев периодической прокатки, кинематические схемы течения металла в очаге деформации очень сложны. Для получения формул, пригодных для практического расчета, необходимо вводить упрощающие допущения с указанием вероятной погрешности, вносимой тем или иным допущением, а получаемые при этом выражения математически сложны и неудобны для практического определения формоизменения [46-48]. Поэтому предпочтение в данном случае можно отдавать экспериментальным методам исследования.
В предлагаемой технологии окончательное формирование требуемых показателей качества арматуры основано на термическом упрочнении мар- тенситным превращением с последующим отпуском. Мартенситное превращение вызывает сильное упрочнение стали благодаря одновременному действию нескольких структурных механизмов, таких как измельчение зерна и фазовый наклеп, приводящий к получению сильно фрагментированной субструктуры, созданной дислокациями, а также образование пересыщенного углеродом а – твердого раствора, в котором в процессе закалки или во время выдержки происходят процессы перераспределения углерода [49].
Окончательные свойства закаленная арматура приобретает в результате отпуска, при котором реализуются потенциальные возможности для повышения сопротивления малым пластическим деформациям и всего комплекса прочностных свойств, создаваемых в процессе закалки с мартенситным превращением. В работах [50-52] указывается, что механические свойства, обработанной по такой технологии проволоки, отличаются высокой однородностью. В работе [30], отмечается, что релаксационная стойкость сталей подвергнутых закалке и отпуску выше, чем после деформационного наклепа и отпуска, при равных значениях временного сопротивления разрыву. Этот эффект объясняется более равномерным распределением дислокаций, образующих более стабильные системы в стали после закалки и отпуска. В отличие от холоднотянутой проволоки и термически упрочненной с прокатного нагрева арматуры закаленно-отпущенная проволока не содержит остаточных зональных напряжений, обладает изотропностью свойств и имеет высокую структурную однородность. Из-за своих структурных особенностей эта проволока по сравнению с холоднотянутой (рис. 1.4, 1.5) обладает повышенной циклической стойкостью в области неограниченной выносливости, а главное имеет лучшую релаксационную стойкость [50,51].
Традиционная технология термической обработки стали по схеме «закалка – отпуск» осуществляется с использованием тепла печного нагрева. Этот вид обработки хорошо зарекомендовал себя в промышленных технологиях упрочнения изделий широкой номенклатуры, обеспечивая надежность и стабильность исполнения технологических режимов, однородность свойств и высокое качество продукции. Данный способ упрочнения может быть использован как один из вариантов финишной термической обработки профилированной в холодном состоянии арматуры из кремнистых сталей. Перспективным приемом промышленной реализации способа термического упрочнения применительно к длинномерным изделиям, к числу которых относится и арматура для шпал, являются поточные технологии индукционной закалки и отпуска. Применение электронагрева вносит существенные отличия в условия протекания фазовых превращений в стали, предопределяя характер получаемых структур и комплекс формируемых при этом свойств изделий.
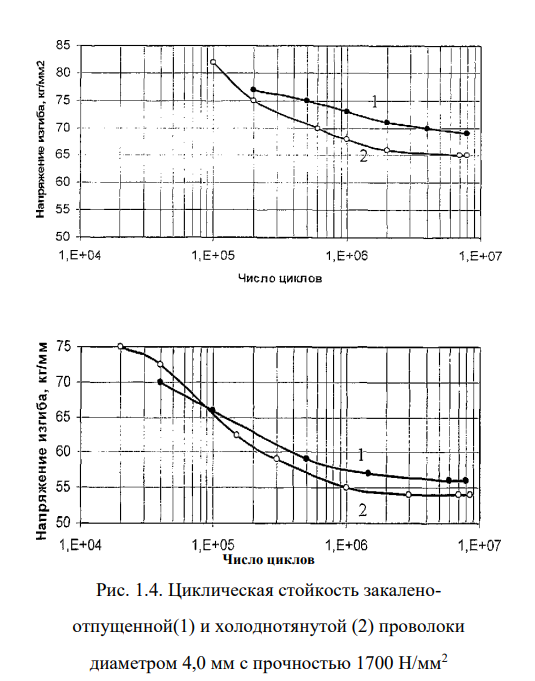
Принципиальное различие между обычным нагревом в печи и внутренним электронагревом ТВЧ заключается в способе подвода энергии к изделию. При обычном нагреве передача тепла осуществляется от поверхности к внутренним слоям путем теплопроводности и лимитируется градиентом температур между нагреваемым объектом и средой, коэффициентом теплопередачи на границе раздела сред и теплопроводностью металла.
Нагрев ТВЧ происходит за счет теплового действия тока, индуктированного в самом изделии, находящемся в области переменного магнитного поля. Коэффициент теплопроводности металла, оказывающий большое влияние на скорость превращения при нагреве внешними источниками тепла, например, в печи при индукционном нагреве не играет решающей роли. Существенной особенностью индукционного нагрева является то, что, изменяя количество подводимой в единицу времени энергии, приходящейся на единицу нагреваемого объема, можно практически получать любые скорости нагрева, вплоть до скоростей, исчисляемых сотнями градусов в секунду. При этом время нагрева в большинстве случаев соответствует секундам или десяткам секунд.
Кратковременность пребывания металла в области повышенных температур не обеспечивает условий для завершения диффузионных процессов при фазовых превращениях. Это вызывает ряд особенностей, которые необходимо учитывать в технологии скоростной закалки и отпуска стали.
Одна из таких особенностей заключается в том, что при повышенных скоростях нагрева процесс образования аустенита завершается при более высоких температурах, чем при обычном печном нагреве. При этом основным фактором, обеспечивающим существенное повышение прочности и пластичности стали, закаленной после скоростного электронагрева, является измельчение зерна аустенита, и соответственно, уменьшение размеров кристаллов мартенсита.
Исследованиями [53] установлено, что при индукционном нагреве можно получать размер зерна аустенита 11-14 балла, в то время как при нагреве в печи он обычно находится в пределах 7-10 балла, т.е. крупнее в 15-30 раз. Чем мельче зерно, тем выше сопротивление стали хрупкому разрушению. Увеличение средней площади зерна аустенита с 40-50 (11-12 балл) до 800 мкм (7-8 балл) снижает хрупкую прочность примерно в 5 раз.
Другим фактором, положительно влияющим на получение высоких свойств стали при электрозакалке, является фиксирование в твердом растворе наибольшего количества углерода при применении резкого охлаждения потоком воды или душем. При таком охлаждении в максимальной степени подавляется частичный распад мартенсита при закалке и концентрация углерода в нем определяется последующим отпуском.
Специфика структурного состояния стали, заложенная электрозакалкой, предопределяет особенности ее поведения и в процессе отпуска.
В первые годы применения высокочастотной термической обработки режимы закалки и отпуска назначались такими же, как и при обычной закалке. Однако сталь, отпущенная по технологии печного отпуска, зачастую обнаруживала пониженные свойства. В связи с этим представляет интерес рассмотреть накопленные за последние годы в литературе сведения, касающиеся особенностей электротермического отпуска.
Действие электронагрева при низком отпуске поверхностно закаленной ТВЧ стали изучалось в работе [54]. Условия сквозного нагрева, являющегося первым и непременным требованием для термической обработки арматурной стали, в значительной мере отличаются от условий поверхностной обработки. Шепеляковский К.З. [55], отмечая особенность глубинной закалки, указывает, что скорость нагрева при такой обработке в 10-30 раз меньше, чем при поверхностной закалке, но и эта скорость в десятки раз превышает скорость нагрева внешними источниками тепла.
Особенности фазовых превращений при скоростном отпуске проволочных материалов, подвергнутых ранее электрозакалке, изучались в работе [56]. В этой работе отмечается, что скоростной нагрев смещает 1-ый и 3-ий эффекты отпуска в область более высоких температур. При этом не удается предотвратить процесс распада мартенсита даже при нагреве со скоростью 104—105 град/сек.
В значительной мере подавляется распад остаточного аустенита, который при обычном отпуске происходит в интервале температур 200-300° С с образованием фаз, аналогичных продуктам отпуска мартенсита. При быстром нагреве остаточный аустенит частично распадается в интервале его минимальной устойчивости. Причем этот распад интенсифицируется объемным эффектом 3-го превращения. Значительное количество остаточного аустенита может быть сохранено до субкритических температур.
Повышение скорости нагрева, как указывается в работе [53], заметно отражается на структурных изменениях при отпуске. Электроотпуск задерживает снятие микроискажений кристаллической решетки, а рекристаллиза- ционные процессы в феррите сопровождаются уменьшением плотности дислокаций.
Наиболее существенным является влияние быстрого нагрева на процессы коагуляции карбидной фазы. Размеры частиц цементита мало изменяются при электроотпуске в области выше температур третьего превращения, в то время, как печной отпуск сопровождается их значительным ростом. Характерной особенностью структуры электроотпущенной стали является состояние феррито-цементитной смеси, в которой частицы цементита имеют форму тонких пластинок толщиной порядка 0,01 мк с межпластинчатым расстоянием 0,10-0,15 мкм. Такому состоянию структуры соответствует повышенный уровень прочности металла [57].
Отпуск стали с нагревом ТВЧ изучался в работе [56]. Отпуску подвергали ударные образцы из сталей Х4Н, 48Х, 43XH3M, 38ХГС. Скорость нагрева изменялась в пределах от 0,01 до 150 град/с и в диапазоне 800-1000 град/с. Отпуск проводили при непрерывном нагреве до заданной температуры. Во всех случаях преимущества электроотпуска проявлялись тем в большей степени, чем с большей скоростью выполнялся нагрев. Влияние выдержки при отпуске сказывалось тем сильнее, чем при более высокой температуре она назначалась. Отрицательное влияние на свойства стали оказала выдержка в интервале температур 200-500° С.
Индукционное оборудование обладает более широким спектром технических возможностей по сравнению с другими видами термического оборудования. Индукционные установки хорошо вписываются в линии различных агрегатов, позволяя создавать оптимальные технологические маршруты. Применение индукционного нагрева позволит разрабатывать эффективные режимы упрочнения арматуры, сочетающие высокую степень механизации и автоматизации с простотой обслуживания. Индукционный нагрев в сочетании с процессами закалочного охлаждения создает предпосылки для более высокого и стабильного уровня термической обработки, а следовательно и качества готовой продукции [58,59].
Следует заметить, что кремнистые марки стали 40С2 или 55С2, производятся российскими металлургическими предприятиями в массовом объеме. В качестве закалочной среды для получения структуры мартенсита для этих сталей может быть использована вода, что значительно удешевляет операции термообработки и улучшает экологическую обстановку.
Литературные данные дают разрозненную картину поведения изделий из этих сталей при термической обработке «закалка-отпуск», выполнявшемся в разных условиях с применением различного оборудования, образцов и материалов, электрических и технологических характеристик нагрева и пр. Сталь 40С2А не входит в перечень стандартных материалов, используемых в производстве упругих элементов деталей машин. Сведений о формировании механических свойств изделий из этой стали в литературе представлено недостаточно. Кроме того, наличие на поверхности арматуры периодического профиля, полученного методами холодной-пластической деформации, будет вносить ряд особенностей в достижение требуемого качества готовой продукции. Научные данные о термическом упрочнении профилированной в холодном состоянии арматуры периодического профиля из кремнистых марок стали в литературе нами не найдены. В связи с этим требуются отдельные исследования, результатом которых должны стать математические модели формирования механических свойств арматуры периодического профиля из кремнистых марок стали при термической обработке по схеме «закалка- отпуск», и разработка на этой основе результативных режимов термического упрочнения, обеспечивающих требуемое качество готовой продукции.
Изучив процессы формирования качества на этапах холодного пластического деформирования и термической обработки, полученные знания необходимо объединить в методику управления качеством высокопрочной арматуры железобетонных шпал, позволяющую определять рациональные режимы обработки формирования заданного качества готовой продукции.
Цель и задачи исследования
Целью работы является обеспечение заданного уровня качества и повышение конкурентоспособности высокопрочной арматуры периодического профиля диаметром 10,0 мм для железобетонных шпал.
Для достижения поставленной цели в работе необходимо решить следующие задачи:
- разработать режимы холодной пластической деформации заготовки под профилирование на основе моделирования и анализа напряженного состояния в зависимости от технологических параметров процесса волочения, с учетом специфики обеспечения заданного уровня качества готовой продукции при профилировании и финишной термообработке;
- разработать модель управления геометрическими показателями качества арматуры в процессе холодного профилирования круглой холоднотянутой заготовки, на базе которой определить эффективные режимы обработки и калибровки профилирующих валков;
- выполнить исследование процессов формирования качества арматуры периодического профиля из сталей 40С2 и 55С2 на этапе термического упрочнения и разработать результативные режимы финишной термообработки;
- разработать методику управления качеством высокопрочной арматуры для железобетонных шпал диаметром 10,0 мм, на основе которой определить рациональные технологические режимы обработки, обеспечивающие формирование заданного уровня качества и повышение конкурентоспособности готовой продукции;
- выпустить опытно-промышленные партии высокопрочной арматуры периодического профиля для железобетонных шпал.
Список литературы
- A.C. Мадатян. Перспективы развития стальной и неметаллической арматуры железобетонных конструкций // Промышленное и гражданское строительство.- № 9.- 2002.С. 18-21.
- А.И. Звездов. 21 век -век бетона и железобетона// Бетон и железобетон .-№ 1.-2001.С. 4-6.
- К.В. Михайлов. Задачи отечественной строительной науки в области арматуры и предварительно напряженных железобетонных конструкций// Бе¬тон и железобетон .2004- № .- 2 . С. 3-5.
- С.А. Мадатян. Современный уровень требований к напрягаемой арма¬туре// Бетон и железобетон .2005- № 1 . С.8-10.
- И.Н. Тихонов.. В.З. Мешков., Г.Н. Судаков. Эффективная стержневая арматура для железобетонных конструкций// Бетон и железобетон .2002- № .- 4. С-10-15.
- Полухин П.И. Физические основы пластической деформации. М.: Ме¬таллургия, 1980, 546 С.
- Производство арматурной проволоки холодной прокаткой// Метизы.- 2005.-№ 1.С. 18-24.
- Никифоров Б.А Изготовление арматурной проволоки холодной прокаткой за рубежом // Черметинформация. Сер. 9. Метизное производство. – 1979.- Вып 3.-38С.
- Б.А. Никифоров, В.А. Харитонов, E.H. Киреев. Производство высоко¬прочной арматурной проволоки. -УПИ, 1982.-96С.
- Capo Д., Битков В.В. Технология производства холоднокатаной про¬волоки для армирования железобетонных конструкций // Сталь. – 1994. – №8. С.15-18.